
умк_кириенко_1
.pdf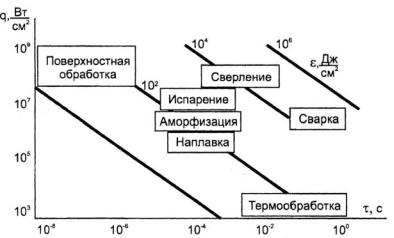
Рис. 13.3. Режимы лазерной обработки при различных видах воздействия лазерного излучения на поверхность:
q– интенсивность излучения, Вт/см2; ε – уровень удельной энергии, Дж/см2;
τ– время воздействия, с
Широкое применение лазеры получили в медицине и биологии. На их основе созданы различные установки и инструменты.
Использование лазера дает значительный эффект. Так, например, с помощью лазерного луча можно выполнять отверстия диаметром 0,03 – 3 мм
иглубиной в несколько миллиметров. При этом производительность лазерной установки составляет около 60 отверстий в минуту. С помощью лазера сваривают интегральные схемы, детали приборов точной механики, миниатюрные детали различных изделий и др. Лазерная сварка позволяет повысить производительность труда в 3 – 5 раз по сравнению с обычным способом сварки. По расчетам специалистов, организация и внедрение в нашей стране централизованного раскроя тканей с использованием лазерных установок позволит получать экономию около 300 млн рублей в год.
Плазма – это частично или полностью ионизированный газ, обладающий практически одинаковой плотностью положительных или отрицательных зарядов. Плазма может быть низкотемпературной (порядка 105 °С)
ивысокотемпературной (106 – 108 °С). Низкотемпературная плазма получила более широкое применение в технологических процессах промышленных производств. В СССР созданы плазмотроны мощностью от 100 Вт до 10000 кВт в устройствах для напыления порошковых металлов и их соединений. Использование их дает значительный эффект. Известно, что лопасти гребных винтов различных судов изготовляют из дорогостоящей легированной стали. Была разработана технология плазменного напыления износостойкого порошка на поверхности лопастей, изготовленных из недорогой стали. Винты, полученные таким образом, относительно дешевы,
аслужат в несколько раз дольше, чем выполненные из легированной стали. На промышленных предприятиях нашей страны применяют плазменно-
261
механическую обработку металлов, суть которой состоит в разупрочнении поверхности заготовок перед резанием. Это дает возможность повысить скорость обработки и увеличить толщину снимаемой стружки. Установлено, что внедрение плазменно-механического метода обработки марганцовистых сталей способствует повышению производительности труда в 4 – 10 раз, а титановых сплавов – в 15 раз.
С помощью плазмотронов можно перерабатывать хлорорганические отходы, которые до сих пор выбрасывались. Из них можно получать новые вещества, необходимые для различных отраслей. Плазменная технология связывается с появлением металлобетонов, где в качестве связующего вещества используют сталь, чугун, алюминий, свинец и т. д. Раньше это было сделать невозможно из-за слабого контактного сцепления между металлом и минеральным наполнителем. Плазменная же технология позволяет производить быстрое поверхностное оплавление частиц горной породы, что обеспечивает хорошую совместную работу металла и минерального наполнителя. Полученный металлобетон прочнее обычного бетона при сжатии в 10 раз, при растяжении – в 100 раз.
При обработке плазмой поверхности кирпичных, бетонных стен или стен, поверхность которых облицована керамической плиткой, образуется стекловидный расплав, который надежно защищает здание от влаги и атмосферных воздействий. Если же на стены здания предварительно нанести растворы солей различных металлов, то их поверхности приобретут соответствующую окраску.
13.5. Химические и электрические способы обработки материалов
При обработке металлов резанием получение деталей необходимых размеров достигается снятием стружки с поверхности обрабатываемой заготовки. Стружка, таким образом, является одним из наиболее распространенных отходов в металлообработке, объем которого составляет примерно 8 млн т в год. При этом по меньшей мере 2 млн т – это отходы переработки высоколегированных и других особо ценных сталей. При обработке на современных металлорежущих станках в стружку зачастую идет до 30 – 40 % металла от общей массы заготовки.
Поэтому все большее внимание уделяется новым способам обработки металлов, основанным на безотходной или малоотходной технологии. Появление новых способов обработки обусловливается также все более широким распространением в машиностроении и других отраслях народного хозяйства высокопрочных, коррозионно-стойких и жаропрочных металлов и сплавов, обработка которых обычными методами затруднена.
К новым методам обработки металлов относятся химические,
электрические, плазменные, лазерные, ультразвуковые, а также гидропластическая обработка металлов.
262
При химической обработке используется химическая энергия. Снятие определенного слой металла осуществляется в химически активной среде (химическое фрезерование). Оно заключается в регулируемом по времени и месту растворении металла в ваннах. Поверхности, не подлежащие обработке, защищают химически стойкими покрытиями (лаки, краски, светочувствительные эмульсии и др.). Постоянство скорости травления поддерживается за счет неизменной концентрации раствора.
Химическими методами обработки получают местные утончения и щели; «вафельные» поверхности; обрабатывают труднодоступные поверхности.
При электрическом методе электрическая энергия преобразуется в тепловую, химическую и другие виды энергии, участвующие непосредственно в процессе удаления заданного слоя. В соответствии с этим электрические методы обработки разделяют на электрохимические, электроэрозионные, электротермические и электромеханические.
Электрохимическая обработка основана на законах анодного растворения металла при электролизе. При прохождении постоянного электрического тока через электролит на поверхности заготовки, включенной в электрическую цепь и являющейся анодом, происходят химические реакции и образуются соединения, которые переходят в раствор или легко удаляются механическим способом. Электрохимическую обработку применяют при полировании, размерной обработке, хонинговании, шлифовании, очистке металлов от оксидов, ржавчины и т. д.
Анодно-механическая обработка сочетает электротермические и электромеханические процессы и занимает промежуточное место между электрохимическим и электроэрозионным методами. Обрабатываемую заготовку подключают к аноду, а инструмент – к катоду. В качестве инструмента используют металлические диски, цилиндры, ленты, проволоку. Обработку ведут в среде электролита. Заготовке и инструменту задают такие же движения, как при обычных методах механической обработки. Электролит подают в зону обработки через сопло.
При пропускании через раствор электролита постоянного электрического тока происходит процесс анодного растворения металла, как при электрохимической обработке. При соприкосновении инструмента-катода с микронеровностями обрабатываемой поверхности заготовки-анода происходит процесс электроэрозии, присущий электроискровой обработке. Продукты электроэрозии и анодного растворения удаляются из зоны обработки при движении инструмента и заготовки.
Электроэрозионная обработка основана на законах эрозии (разрушения) электродов из токопроводящих материалов при пропускании между ними импульсного электрического тока. Она применяется для прошивания полостей и отверстий любой формы, разрезания, шлифования, гра-
263
вирования, затачивания и упрочнения инструмента. В зависимости от параметров и вида импульсов, применяемых для их получения генераторов электроэрозионная обработка разделяется на электроискровую, электроимпульсную и электроконтактную.
При определенном значении разности потенциалов на электродах, одним из которых является обрабатываемая заготовка (анод), а другим – инструмент (катод), между электродами образуется канал проводимости, по которому проходит импульсный искровой (электроискровая обработка) или дуговой (электроимпульсная обработка) разряд. В результате температура на поверхности обрабатываемой заготовки возрастает. При этой температуре мгновенно оплавляется и испаряется элементарный объем металла и на обрабатываемой поверхности заготовки образуется лунка. Удаленный металл застывает в виде мелких гранул.
Следующий импульс тока пробивает межэлектродный промежуток там, где расстояние между электродами наименьшее. При непрерывном подведении к электродам импульсного тока процесс их эрозии продолжается до тех пор, пока не будет удален весь металл, находящийся между электродами на расстоянии, на котором возможен электрический пробой (0,01 – 0,05 мм) при заданном напряжении. Для продолжения процесса необходимо сблизить электроды до указанного расстояния. Электроды сближаются автоматически с помощью следящего устройства того или иного типа.
Электроискровую обработку применяют для изготовления штампов, пресс-форм, фильер, режущего инструмента, деталей двигателей внутреннего сгорания, сеток и для упрочнения поверхностного слоя деталей.
Электроимпульсная обработка используется как предварительная для штампов, турбинных лопаток, поверхностей фасонных отверстий в деталях из жаропрочных сталей. При электроимпульсной обработке скорость съема металла в 8 – 10 раз больше, чем при электроискровой.
Электроконтактная обработка основана на локальном нагреве заготовки в месте контакта с электродом-инструментом и удалении размягченного или расплавленного металла из зоны обработки механическим способом (при относительном перемещении заготовки и инструмента). Метод не обеспечивает высокой точности и качества поверхности деталей, но дает высокую скорость съема металла, поэтому используется при зачистке отливок, отрезании литниковых систем, зачистке проката из специальных сплавов, черновом шлифовании корпусных деталей машин из труднообрабатываемых сплавов и т.п.
Электромеханическая обработка связана преимущественно с ме-
ханическим действием электрического тока. На этом основана, например, электрогидравлическая обработка, использующая действие ударных волн, возникающих в результате импульсного пробоя жидкой среды.
264
Ультразвуковая обработка металлов – разновидность механиче-
ской обработки – основана на разрушении обрабатываемого материала абразивными зернами под ударами инструмента, колеблющегося с ультразвуковой частотой. Источником энергии служат электрозвуковые генераторы тока с частотой 16 – 30 кГц. Рабочий инструмент – пуансон – закрепляют на волноводе генератора тока. Под пуансоном устанавливают заготовку, и в зону обработки поступает суспензия, состоящая из воды и абразивного материала. Процесс обработки заключается в том, что инструмент, колеблющийся с ультразвуковой частотой, ударяет по зернам абразива, лежащим на обрабатываемой поверхности, которые скалывают частицы материала заготовки. Скорость обработки зависит от частоты и амплитуды колебаний, твердости и размеров абразивных частиц. Ультразвуковые колебания инструмента создаются с помощью магнитно-стрикционных вибраторов, преобразующих электрическую энергию в механическую. Ультразвуковая обработка используется для получения твердосплавных вкладышей матриц и пуансонов, вырезания фигурных полостей и отверстий в деталях, гравирования, прошивки отверстий с криволинейными осями, нарезания резьбы, разрезания заготовок на части и других работ.
Точность размеров деталей и шероховатость их поверхностей, обработанных ультразвуковыми методами, зависят от зернистости используемых абразивных материалов и соответствуют получаемым при шлифовании.
13.6. Плазменно-лазерная обработка
Лучевые, или лазерные, методы обработки основаны на использо-
вании сфокусированного луча (электронного, когерентного, ионного) с весьма высокой плотностью энергии. Луч лазера используется как в качестве средства нагрева и размягчения металла впереди резца, так и для выполнения непосредственно процесса резания при прошивке отверстий, фрезеровании и резке листового металла, пластмасс и других материалов.
Процесс резания идет без образования стружки, а испаряющийся за счет высоких температур металл уносится сжатым воздухом. Сейчас лазеры применяют для сварки, наплавки и разрезания в тех случаях, когда к качеству этих операций предъявляются повышенные требования. Например, лазерным лучом путем прожигания или испарения режут сверхтвердые сплавы, сотовые титановые панели в ракетостроении, листовой и панельный алюминий, композиционные материалы, изделия из нейлона и твердую древесину. Высокая плотность энергии в зоне нагрева создает дополнительный эффект очистки металла.
Следует отметить, что пока лазеры имеют сравнительно низкий коэффициент полезного действия из-за преобразования электрической энергии в тепловую, а последней – в механическую.
265
Плазменные методы обработки металлов по праву считаются одними из самых прогрессивных. Огромная температура плазмы, значительная кинетическая энергия ее струи гарантируют высокое качество обработки любых металлов и материалов. Мощность современных плазменных установок достигает 6 МВт.
Использование плазменных и лазерных методов обработки особенно эффективно при изготовлении деталей сложных форм.
13.7. Гидропластическая обработка
Изготовление металлических пустотелых деталей с гладкой поверхностью и малыми допусками (гидравлические силовые цилиндры, плунжеры, корпуса для электродвигателей, вагонные оси, некоторые шестерни) все чаще осуществляется в последнее время не путем снятия стружки, а посредством так называемой гидропластической обработки. Пустотелую цилиндрическую заготовку, нагретую до температуры пластической деформации, укладывают в массивную разъемную матрицу, сделанную по форме изготовляемой детали, и закачивают под давлением воду. Заготовка раздается и принимает форму матрицы. Для изготовления, например, вагонной оси требуется давление 150 МПа. Поэтому рассматриваемый метод не позволяет изготовлять детали значительных размеров, например трубы. Но если сделать так, чтобы вода, попав внутрь заготовок и соприкасаясь с горячим металлом, мгновенно превращалась в пар, ее объем многократно увеличится. За счет этого заготовка будет плотно прижиматься к матрице. Потребуется давление пара лишь 10 – 20 МПа.
Осуществление этой идеи в нашей стране позволило исключить при изготовлении пустотелых деталей сверление и другие виды механической обработки. Достигается и другой эффект – металл детали становится под давлением более плотным и мелкозернистым. Детали, изготовленные таким способом, имеют более высокую долговечность. Новым методом можно изготовлять биметаллические трубы, закладывая в матрицу две заготовки – одна в другую. Возможны и такие оригинальные установки, которые выполняют самые разные операции, от пробивки отверстий в фольге до изготовления полусфер из листового металла значительной толщины.
13.8. Основы мембранной технологии
Мембранная технология – новый принцип организации и осуществления процесса разделения веществ через полупроницаемую перегородку, отличающийся отсутствием поглощения разделяемых компонентов и низкими энергетическими затратами на процесс разделения.
266
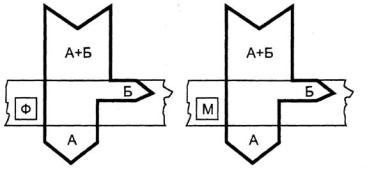
По сравнению с традиционными процессами разделения неоднородных систем мембранная технология выгодно отличается высокой энерго- и ресурсоэкономичностью, простотой аппаратурного оформления, экологической чистотой.
Слово «мембрана» имеет латинское происхождение (membrana) и означает «кожица», «перепонка». В технологии под мембраной мы будем понимать перегородку, обладающую различной проницаемостью по отношению к отдельным компонентам жидких и газовых неоднородных смесей.
При внешнем сходстве процессов фильтрования и мембранного разделения (рис. 13.4) между указанными процессами есть принципиальное отличие.
а б
Рис. 13.4. Схемы мембранного разделения и фильтрования:
а– мембранное разделение;
б– фильтрование
Входе фильтрования хотя бы один из компонентов газовой или жидкой смеси задерживается и фиксируется внутри фильтрующей перегородки. Это приводит к тому, что перегородка постепенно забивается и процесс фильтрования на ней без очистки делается практически невозможным. В отличие от фильтра мембрана не фиксирует в себе ни одного из компонентов разделяемой жидкой или газовой смеси, а только делит первоначальный поток на два, один из которых обогащен по сравнению с исходным каким-то компонентом. Подобный принцип действия мембраны делает ее способной к практически неограниченному сроку службы, без заметного изменения в эффективности разделения смесей.
Взависимости от материала, из которого изготавливают мембраны,
их делят на полимерные, металлические, стеклянные, керамические или композиционные.
По механизму действия различают диффузионные, адсорбционные
и ионообменные мембраны.
267
В зависимости от агрегатного состояния разделяемой смеси, движущей силы процесса разделения, размеров частиц компонентов и механизма разделения различают следующие разновидности мембранных процессов: диффузионное разделение газов; разделение жидкостей методом испарения через мембрану; баромембранные процессы разделения жидких смесей; электродиализ.
Диффузионное разделение газов основано на различной проницаемости мембран для отдельных компонентов газовых смесей. Для осуществления диффузионного разделения газовых смесей используются как сплошные, так и пористые мембраны с размерами пор меньшими, чем длина свободного пробега молекул газов при заданном давлении. Движущей силой процессов диффузии компонентов является разность их концентраций на противоположных поверхностях мембраны.
Диффузионное разделение газов сегодня является наиболее крупномасштабным и экономичным методом, широко используется для получения урана-235, являющегося ядерным топливом. Данный процесс используется для создания аппаратов «искусственное легкое», при производстве водорода, выделении гелия из состава природных и нефтяных газов, является перспективным для выделения кислорода из воздуха, удаления диоксида углерода, воды и других компонентов из газовоздушных смесей в системах жизнеобеспечения людей в замкнутых пространствах, для создания контролируемой атмосферы, обогащенной диоксидом углерода, при хранении овощей и фруктов. Созданы и используются специальные пленки, которые помогают длительное время сохранять качество завернутых в них овощей, фруктов, цветов. В основе такой технологии лежит свойство полимерных мембран разделять воздух на молекулярном уровне: в нем становится меньше кислорода, что резко замедляет процессы гниения.
Разделение жидкостей методом испарения через мембрану основано на различной диффузионной проницаемости мембран для паров веществ. Движущей силой процесса является разность концентраций или давлений. Смесь жидкостей, находящихся в контакте с мембраной, нагревают, а пары, проникающие через мембрану, отводят с помощью вакуумирования или потоком инертного газа. Наиболее широко данный метод применяется при разделении азеотропных смесей, а также смесей веществ, имеющих невысокую термическую стабильность.
Баромембранные процессы разделения жидких смесей на практике осуществляются под избыточным давлением и поэтому объединены в группу баромембранных.
268
Установки, работающие по принципу баромембранного разделения, уже сегодня широко используются для обессоливания морской и соленой воды, очистки сточных вод, извлечения ценных компонентов из разбавленных растворов, в пищевой промышленности – для концентрирования сахарных сиропов, фруктовых и овощных соков, растворимого кофе, получения ультрачистой воды для электронной промышленности, медицины и фармацевтики.
Если мембранный процесс применяют для отделения от идеального раствора крупных коллоидных или взвешенных микрочастиц размером 0,1 – 10 мкм, то его называют микрофильтрацией, или мембранной фильтрацией.
Микрофильтрация нашла широкое применение в микробиологической промышленности при концентрации водных растворов ферментов, белков, нуклеиновых кислот, полисахаридов и других веществ в химической, пищевой и целлюлозно-бумажной промышленности для очистки сточных вод.
Микрофильтрация используется для концентрирования тонких суспензий, осветления растворов, очистки сточных и природных вод при проведении обессоливания морской воды. Мембранное концентрирование различных жидких продуктов с успехом может заменить традиционный процесс – вакуум-выпаривание.
Электродиализ можно определить как перенос ионов через мембрану под действием электрического тока. При наличии мембран, избирательно пропускающих одни ионы и задерживающих другие, можно решать многочисленные задачи выделения ценных компонентов из растворов, обессоливания воды, снижения жесткости, регенерации растворов в гальванических производствах, очистки сточных вод.
Перспективность мембранных методов прежде всего – в их уни-
версальности. Скоро нельзя будет представить ни одной технологической линии в пищевой, медицинской, фармацевтической и ряде других отраслей промышленности, в которой не было бы установок для мембранного синтеза, разделения, концентрирования и очистки продуктов.
13.9. Основы радиационно-химической технологии
За последние два десятилетия сформировалась новая область хими-
ческой технологии – радиационно-химическая технология (РХТ). Ее
269
предшественницей следует считать ядерную технологию, интенсивное развитие которой (с начала 40-х гг. XX в.) стимулировалось необходимостью срочного решения ряда задач, связанных с практическим использованием атомной энергии.
Целью РХТ является разработка методов и устройств для наиболее экономичного осуществления с помощью ионизирующего излучения физических, химических и биологических процессов, позволяющих получать новые материалы или придавать им улучшенные свойства, а также для решения экологических проблем. Выделение этого направления в отдельную область технологии обусловлено прежде всего особенностью действия ионизирующего излучения на вещество.
Радиационно-химические процессы обусловливаются энергией возбужденных атомов, ионов, молекул. Энергия ионизирующего излучения превышает в сотни тысяч раз энергию химических связей. Механизм ра- диационно-химических процессов объясняется особенностями взаимодействия излучений с реагирующими веществами.
В качестве источников ионизирующего излучения используются потоки заряженных частиц большой энергии (электроны, α-, β- частицы, нейтроны, γ-излучение).
Выделим достоинства ионизирующего излучения:
−высокая энергетическая эффективность излучения, приводящая к тому, что по сравнению с традиционными радиационная технология является в целом энергосберегающей;
−высокая проникающая способность излучения. Исходя их этого, излучение наиболее эффективно использовать для обработки блочных материалов и изделий, при стерилизации биомедицинских материалов в упаковке;
−излучение представляет собой легкодозируемое средство обработки материалов и не загрязняет продукцию.
Первоначально ионизирующее излучение использовали для производства уникальных продуктов, а также продуктов улучшенного качества. Причем это было продиктовано ценами на указанные продукты. Имелись случаи экономии сырья и энергии. Однако они были единичными.
Сегодня наблюдается явное смещение интересов в использовании ионизирующих излучений: от получения продуктов с уникальными и улучшенными свойствами к экономии сырья и энергии.
Доказано, что стоимость получения сшитой полиэтиленовой изоляции кабеля при радиационной технологии в 2,2 раза ниже, чем при исполь-
270