
отчет по практиккке
.pdfсоответствующую емкость. Температура продукта в емкости контролируется по месту с помощью прибора, установленного на трубопроводе выхода продукта из емкости, давление в аппарате контролируется по месту по манометру. Из емкостей хранилищ пластификатор ДОФ направляется на станцию взвешивания жидких компонентов – в весовой мерник-дозатор жидких компонентов и далее распределяется на производство, мерник жидких компонентов оборудован мешалкой непрерывного действия предназначенной для гомогенизации компонентов и сливным клапаном. На всасывающих линиях насосов установлены фильтры для исключения попадания в расходные емкости механических включений.
Эпоксидированное соевое масло, поступающее в бочках, завозится на склад жидкого сырья или помещение обогрева для временного хранения, откуда далее насосом перекачивается в расходную емкость для соевого масла которая снабжена рубашкой обогрева, в соотношении 1:1 ДОФ + соевое масло. Из расходной емкости соевое масло также поступает в мерник дозатор. Сыпучие и малые сыпучие компоненты – смола ПВХ СИ-70; мел , стеарат кальция, ТОСС, стеариновая кислота, дифенилолпропан доставляются в мешках и биг-бегах автотранспортом. На складе компоненты хранятся: в мешках по (20÷50) кг на деревянных поддонах по (20÷40) мешков, в биг-бегах на деревянных поддонах в 2 яруса. ПВХС, ТОСС, мел,
стеарат кальция и малые сыпучие компоненты доставляются в отделение дозирования химического сырья, далее мешки вручную грузятся на роликовый стол и распарываются. ПВХС из мешков или биг-бегов засыпается в загрузочную воронку откуда установкой вакуумной подачи сырья транспортируется в расходный силос. ТОСС засыпается в загрузочную воронку, далее шнековым транспортером направляется в силос. Мел засыпается в загрузочную воронку, далее мел шнековым транспортером поступает в силос. Силоса представляют собой вертикальные емкости с коническим днищем, оборудованные перемешивающим устройством, кроме силоса с ПВХС, дозировочным
11

шнеком, а также на выходе имеется пневматический клапан для силоса ПВХС. Объем силосов от 3,0 до 7,0 м3 Контроль заполнения силосов производится с помощью датчиков верхнего и нижнего уровня. При достижении минимального и максимального уровня компонента в силосе срабатывает световая и звуковая сигнализация. Из силосов компоненты автоматически подаются на станцию взвешивания сухих компонентов в весовой мерник-дозатор сыпучих компонентов согласно рецептуры. Малые сыпучие компоненты такие как стеариновая кислота и дифенолпропан в мешках доставляются к расфасовочной камере, их содержимое взвешивается на электронных весах и фасуется в полиэтиленовые мешки на определенные порции. Далее расфасованные компоненты на ручной тележке доставляются к тактовому транспортеру, по которому подаются в горячий смеситель.
Рисунок- 2.1 Отделение дозирования сырья
12
2.2 Приготовление композиции на двухстадийной нагревающей- охлаждающей-смешивающей установке
Смешение – это физический процесс, целью которого является
получение однородной смеси, состоящей компонентов разных фаз. При этом начальное состояние системы характеризуется упорядоченным распределением компонентов, а конечное – неупорядоченным, статистически случайным распределением компонентов. Для реализации процесса смешения смеситель должен обеспечить проведение по меньшей мере двух процессов: измельчения (диспергирования) одного из компонентов, в некоторых случаях сопровождающегося изменением физического состояния компонентов растворением, плавлением, поглощением, статистически случайного распределения ингредиентов по всему объему смеси.
В состав любой смеси обычно входят два или более компонентов. Компонент смеси, концентрация которого выше всех остальных, называется дисперсионной средой. Компоненты смеси, распределяемые в дисперсионной среде, называют диспергируемой фазой. В
многокомпонентных системах смешение рассматривается как процесс последовательного смешения каждого компонента по очереди с ранее приготовленной смесью, играющей роль дисперсионной среды. Приготовление композиции, необходимой для получения гранулированного пластиката на основе поливинилхлорида, осуществляется на
двухстадийной нагревающе-охлаждающей смешивающей установке. Требующееся на одну операцию количество сырья отвешивается на автоматических станциях взвешивания в весовых мерниках-дозаторах: взвешивания жидких компонентов и взвешивания сухих компонентов. Вся образовавшаяся газо-пыльная смесь от станции взвешивания сухих компонентов выбрасывается в атмосферу. Сухие компоненты и смесь пластификаторов из мерников загружаются в нагревающий смеситель в определенном порядке. Дополнительно в смеситель с помощью тактового
13
транспортера с заданным тактом поступают навески малых сыпучих компонентов, предварительно отвешенные в камере расфасовки.
2.3 Получение, охлаждение, упаковка пластиката
Линия для производства кабельного пластиката состоит из:
экструдера типа червячного осциллирующего смесителя, одношнекового экструдера типа червячного прессгранулятора с горячей резкой , охладителя гранулята и транспортной системы гранулята. Двухступенчатый агрегат обеспечивает эффективное смешение сухой композиции, ее желатинизацию, пластикацию и расплав. Система управления экструдера и гранулятора позволяет поддерживать технологические параметры всего процесса в заданном режиме. Имеющаяся система вакуумной дегазации, включающая вакуум-насос, позволяет эффективно удалять летучие вещества, образующиеся из расплавленной композиции. Парогазовая смесь из вакуумнасоса поступает в емкость-сепаратор, где происходит отделение капель воды, уносимой из вакуум-насоса, от газовой фазы. Из емкости-сепаратора воздух, содержащий продукты дегазации, выбрасывается в атмосферу, а отделенная вода направляется в емкость для охлажденной воды.
Полученный расплав транспортируется к головке гранулятора с горячей резкой. Полученные гранулы пластиката с помощью пневмотранспорта передаются на установку охлаждения, состоящую из воздуходувок, циклонов и вибросит. Охлаждение гранул осуществляется в бункерах-циклонах охладителях гранул с помощью воздуха пневмотранспорта, нагнетаемого воздуходувками. Воздух из циклонаохладителя выбрасывается в атмосферу. Охлажденные гранулы поступают на установки просеиваниявибросито для сепарации фракций гранул более 7 мм и менее 2 мм. Далее стандартные гранулы кабельного пластиката через сушильную установку, транспортируются к бункеру-циклону готовой продукции. Партии гранул при пуске экструдера и смене рецептуры собираются в мешок и направляются на переработку в неответственные
14
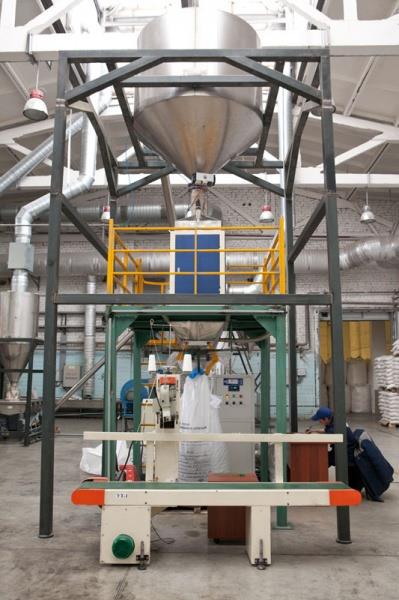
изделия. Воздух из бункеров удаляется в атмосферу.Из бункера готовой продукции гранулы поступают на автоматическую станцию взвешивания. Рисунок- 2.2 Автоматическая станция взвешивания готового пластиката
Где ведется затарка продукта в клапанные мешки и биг-беги. При упаковке гранул кабельного пластиката в биг-беги их одевают на горловину и зажимают с помощью пневмозажимов под весовым дозатором. При упаковке готовой продукции контролируются следующие показатели:
-внешний вид, размер гранул;
-цвет, засоренность гранул (белые, неокрашенные марки);
-масса кабельного пластиката в мешках и контейнерах (биг-бегах).
15
Требования безопасности и производственной санитарии
Поливинилхлоридный пластикат при нормальной температуре вредных продуктов в концентрациях опасных для организма человека, не выделяет и не является взрывоопасным продуктом. При длительном воздействии повышенных температур (170±10°С) возможно выделение хлористого водорода. Предельно допустимая концентрация хлористого водорода в производственных помещениях составляет 5 мг/ м3При воспламенении пластиката во время его изготовления и переработке и хранении пожар следует тушить любыми имеющимися средствами пожаротушения кошма, песок, огнетушитель. Производственные помещения в соответствии с санитарными нормами и правилами должны соответствовать категории В. Пластикат должны изготовлять в помещениях, оборудованных приточно-вытяжной вентиляцией обеспечивающей необходимую чистоту воздуха, в соответствии с санитарными нормами. Выделяющиеся в окружающую среду химические соединения, образующиеся в процессе производства, обладают высокой токсичностью, что может приводить к появлению острых и хронических профессиональных отравлений, профессиональных заболеваний кожи - экзем и дерматитов, а также других профессиональных заболеваний. К производственным вредностям относятся также сопутствующие условия - выделение тепла оборудованием, шум и загрязнение воздуха пылью при смешивании, загрузке сухих компонентов. При производстве пластиката должны соблюдаться меры предосторожности, работающие с вредными веществами должны быть в спецодежде, фартуке, защитных очках и респираторе. Руки должны быть предохранены резиновыми перчатками или защитными мазями типа биологические «перчатки»
16
Заключение
1.В процессе прохождения практики я ознакомился с технологией производства поливинилхлоридного кабельного пластиката.
2.Ознакомился с основным технологическим оборудованием, с
вспомогательными обслуживающими системами, такими как, система подачи сжатого воздуха, система охлаждения технологического водоснабжения. Подробно рассмотрены возможные неполадки технологического оборудования, способы их устранения и по рядок оповещения руководства в случаях нештатных ситуаций.
3. Освоил процесс |
пуска линии по производству кабельного |
пластиката в работу, |
порядок вывода линии на максимальную |
производственную мощность.
4.Ознакомился с порядком проведения контроля выпускаемой продукции на всех стадиях, от стадии дозирования сырья до стадии упаковки пластиката.
17
Список использованной литературы
1.А. М. Кутепов, Т. И. Бондарева, М. Г. Беренгартен. Общая химическая технология. Издательство -М.: ИКЦ "Академкнига", 2007 - 528 с.
2.Кабельный пластикат ГОСТ 5960-72 (Пластикат для изоляции и
защитных оболочек проводов и кабелей) ГОСТ 5960-72 с изм. 1. М.: ИПК издательство стандартов, 2004.- 47 с.
3.В.К. Завгородний. Оборудование для переработки пластмасс. М.: Машиностроение, 1976.- 217 с.
4.Э.Фишер. Экструзия пластических масс. М.: Химия, 1970. - 301 с. .
5.Постоянный технологический регламент производства гранулированного полихлорвинилового кабельного пластиката и компаундов на основе полиолефинов. Уфа.: ООО НПО «УфаНефтеГазпроект», 2008. – 44 с.
18