
АЕПТВМ КП / КП Толкатели заготовок
.pdf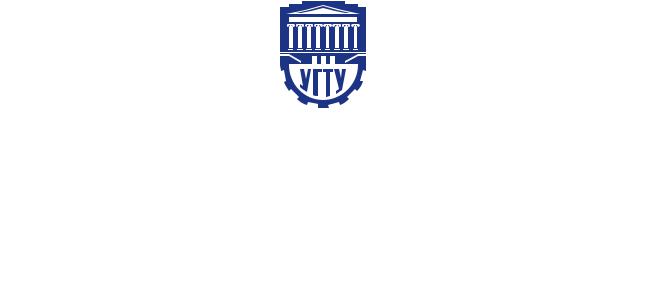
Федеральное агентство по образованию РФ ГОУ ВПО «Уральский государственный технический университет – УПИ»
В.С. Паршин, В.А. Спиридонов, В.Л. Мухоморов
ТОЛКАТЕЛИ ЗАГОТОВОК ДЛЯ МЕТАЛЛУРГИЧЕСКИХ ПЕЧЕЙ
Учебное электронное текстовое издание Подготовлено кафедрой «Металлургические и роторные машины»
Научный редактор доц., канд. техн. наук Б.Н. Губашов Рецензент доц., канд. техн. наук Н.Х. Понетаева
Методические указания к курсовому проекту по дисциплине «Механика» (раздел «Детали машин и основы конструирования») для студентов всех видов обучения специальности 110300 – «Теплофизика, автоматизация и экология промышленных печей». В работе дано описание конструкций реечного, рычажного, винтового и фрикционного толкателей. Показан расчёт основных конструктивных параметров этих устройств с проверочным расчётом на прочность зубчатых передач, винтовых пар, катковых опор, устойчивости штанг на продольный изгиб. Рассмотрены также расчёт и конструирование подшипниковых узлов, расчёт мощности привода и выбор двигателя. На примере рычажного толкателя показано применение кинематического анализа и синтез рычажной системы для оптимизации конструкции.
© ГОУ ВПО УГТУ−УПИ, 2005
Екатеринбург
2005

Паршин В.С., Спиридонов В.А., Мухоморов В.Л. |
Толкатели заготовок для металлургических печей |
1. ЦЕЛЬ И ЗАДАЧИ КУРСОВОГО ПРОЕКТИРОВАНИЯ
Целью курсового проектирования по дисциплине «Механика» (раздел «Детали машин и основы конструирования») является расширение и закрепление знаний, полученных в период лекционного обучения и на практических занятиях, приобретение практических навыков в решении инженерных задач по выбору основных параметров проектируемой машины, по кинематическому анализу и конструктивной разработке отдельных узлов.
В качестве темы курсового проекта студенту задаётся конструктивная разработка одного из вариантов печного толкателя, состоящего из двигателя, передач и рабочего органа. Заданием предусматривается расчёт мощности привода, выбор двигателя, редуктора, муфт, подшипников, расчёт основных деталей на прочность и т. д.
Проект состоит из графической части и пояснительной записки. Графическая часть проекта рассчитана на 1,5…2 листа формата А1. Объём пояснительной записки – 15…20 листов. Проект выполняется в IV учебном семестре и защищается перед комиссией, назначенной заведующим кафедрой, и должен быть предварительно подписан руководителем.
2. ОБЗОР КОНСТРУКЦИЙ ТОЛКАТЕЛЕЙ И ВЫТАЛКИВАТЕЛЕЙ
По способу передачи толкающего усилия различают следующие конструкции толкателей и выталкивателей: реечные, винтовые, рычажные кулачковые, цепные, фрикционные. Для привода толкателей и выталкивателей преимущественно используют электрический привод, но иногда применяют на этих установках гидравлический и пневматический приводы.
Винтовые толкатели имеют по сравнению с реечными меньшие габариты, но применяются обычно только при небольших усилиях проталкивания садки P ≤500 кН вследствие низкого КПД винтовой пары.
Значительно надёжнее и долговечнее реечные толкатели, которые применяют при усилиях проталкивания садки до 2…2,5 МН. Реечные
ГОУ ВПО УГТУ-УПИ – 2005 |
Стр. 2 из 39 |
|

Паршин В.С., Спиридонов В.А., Мухоморов В.Л. |
Толкатели заготовок для металлургических печей |
толкатели имеют обычно более сложный редуктор, поскольку он должен обеспечить большее передаточное число. Основное преимущество реечных редукторов – больший КПД (η=0,85…0,90) и устранение ходовой гайки. Гайка относительно быстро изнашивается (срок службы около 2-х лет). Она сложна в изготовлении, так как имеет большие размеры и требует точной обработки.
Штанги толкателей выполняют коваными, сварными и – для толкателей на малое усилие – из катаных заготовок круглого сечения. Кованые и сварные штанги более сложны в изготовлении: сложнее получается конструкция направляющих. Однако применение штанг толкателя прямоугольного сечения позволяет выполнить зубчатые рейки в виде отдельных деталей, изготовляя их из более прочной стали (40ХН, 40Х), и при износе зубьев заменять, сохраняя тяжёлые и дорогие штанги.
Штанги толкателей из круглого проката проще в изготовлении, но в этом случае зубья приходится нарезать непосредственно на них. Следовательно, марка стали будет хуже, а при износе зубьев штанги необходимо заменять целиком.
Скорость толкания металла толкателями выбирают обычно небольшой: при проталкивании садки 0,1…0,3 м/с. Возвратный ход может быть более быстрым – 0,6…0,8 м/с. Для регулирования скорости в последних конструкциях предусматривают привод толкателей от двигателей постоянного тока.
Рычажные толкатели применяют у печей с боковой загрузкой металла, так как толкающие штанги такого толкателя могут быть введены в
печь при малых размерах окон в торцевой стенке печи.
3. РЕЕЧНЫЙ ТОЛКАТЕЛЬ
Реечный толкатель предназначен для перемещения отдельных блюмов и слябов с рольганга в нагревательную печь и продвижения через неё всего ряда блюмов и слябов. Схема реечного толкателя представлена на рис. 1. Толкающая штанга 1 снабжена толкающими пальцами 2 с пружинными амортизаторами 3. При движении штанги вперёд в опорных катках 4 пальцы упираются в торец штанги и толкают перед собой
ГОУ ВПО УГТУ-УПИ – 2005 |
Стр. 3 из 39 |
|
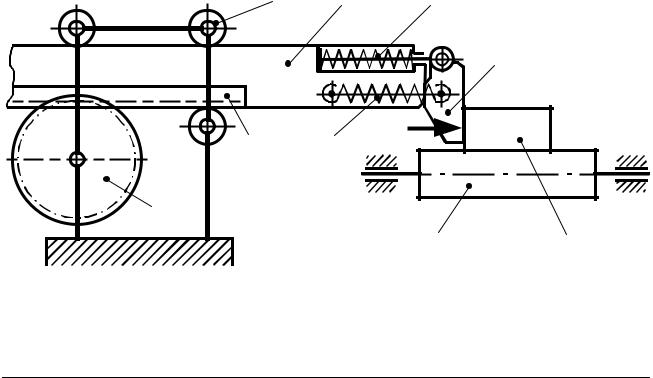
Паршин В.С., Спиридонов В.А., Мухоморов В.Л. |
Толкатели заготовок для металлургических печей |
блюм 5. При движении штанги назад и наличии на рольганге 6 следующего блюма пальцы отклоняются вверх, и головка штанги беспрепятственно возвращается в исходное положение, после чего замыкающая пружина 7 прижимает толкающие пальцы к торцу штанги. С нижней стороны штанги укреплена зубчатая рейка 8, при помощи которой на штангу передаётся толкающее усилие от привода через приводную шестерню 9.
Максимальную мощность привода толкателя определяют по усилию и скорости толкания всего ряда блюмов, кВт
Nmax = |
P V |
|
, |
(3.1) |
|
||||
1000 η |
|
|
||
где P – толкающее усилие, Н; |
|
|
||
V – скорость толкания, м/с ; |
|
|
||
η – коэффициент полезного действия (КПД) всего привода. |
|
|||
КПД подсчитывают по формуле |
|
|
||
i=n |
|
|
||
η=∏ηi , |
|
(3.2) |
i=1
где n – количество механизмов или узлов, находящихся между двигателем и рабочим органом;
ηi – КПД i-го механизма или узла (определяется по таблице 1).
8 |
9 |
4 1 3
2
7 |
P |
|
6 |
5 |
Рис. 1. Схема реечного толкателя
ГОУ ВПО УГТУ-УПИ – 2005 |
Стр. 4 из 39 |
|

Паршин В.С., Спиридонов В.А., Мухоморов В.Л. |
Толкатели заготовок для металлургических печей |
Рабочий ход толкателя условно делится на три участка: a, b и c (рис. 2). На участке a толкатель совершает холостой ход, при котором башмак непосредственно ещё не доходит до слитка. На участке b толкатель продвигает один слиток с усилием P1сл до соприкосновения со всей садкой. И на участке c происходит продвижение всего ряда слитков с усилием PΣсл. Отношение c/b ≈0,1, следовательно, максимальное усилие PΣсл приходится на довольно кратковременный отрезок времени.
Таблица 1 Коэффициенты полезного действия механизмов и узлов
Тип |
Oпоры |
||
передачи |
скольжения |
|
качения |
Подшипники |
0,95…0,99 |
|
0,98…0,99 |
Открытые зубчатые передачи: |
|
|
|
цилиндрические |
0,93…0,95 |
|
0,95…0,96 |
конические |
0,92…0,94 |
|
0,93…0,95 |
Закрытые цилиндрические зубчатые пе- |
0,95…0,97 |
|
0,97…0,99 |
редачи (редукторы на каждую пару) |
|
|
|
Редукторы: |
|
|
|
двухступенчатые |
|
|
0,94…0,96 |
трёхступенчатые |
|
|
0,91…0,94 |
Червячные передачи при: |
|
|
|
однозаходном червяке |
0,50…0,75 |
||
двухзаходном червяке |
0,75…0,80 |
||
трёхзаходном червяке |
0,80…0,85 |
||
самотормозящем червяке |
0,30…0,40 |
||
Зубчатые муфты |
|
0,99 |
|
Передача: |
|
|
|
цепная |
0,90…0,97 |
||
клиноремённая |
0,88…0,92 |
||
плоскоремённая |
0,83…0,95 |
||
фрикционная |
0,90…0,96 |
||
винт-гайка (винт однозаходный) |
0,40…0,50 |
Для выбора мощности двигателя нагрузочную диаграмму удобнее представлять в виде зависимости статического момента от времени Mс =f(t).
ГОУ ВПО УГТУ-УПИ – 2005 |
Стр. 5 из 39 |
|
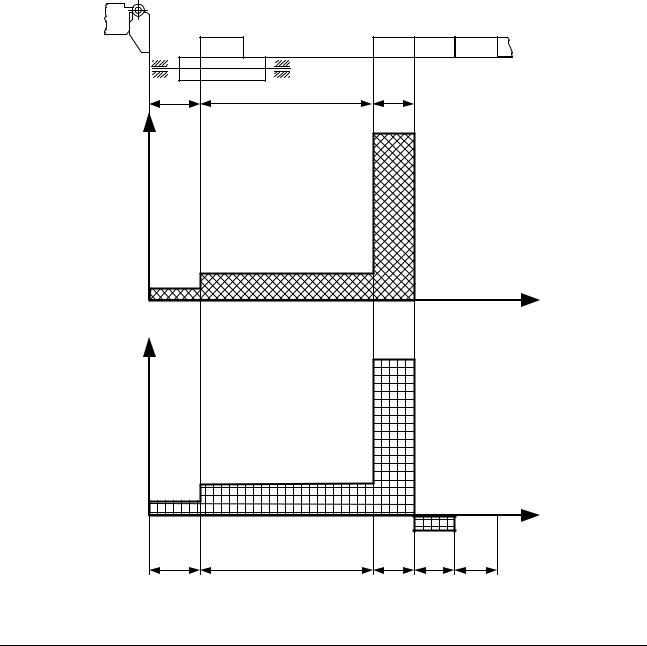
Паршин В.С., Спиридонов В.А., Мухоморов В.Л. |
|
|
Толкатели заготовок для металлургических печей |
|||
На участке a нагрузочной диаграммы статический момент будет ра- |
||||||
вен моменту холостого хода Mс =Mxx, кНм: |
|
|||||
|
|
dц |
|
|
||
|
|
Gш |
|
µц +f |
|
|
|
|
|
|
|||
|
Mxx = |
2 |
|
, |
(3.3) |
|
|
|
|
||||
|
|
|
i ηxx |
|
||
где Gш – вес штанги, кН; |
|
|
|
|
|
|
dц |
– диаметр цапф направляющих роликов в подшипниках качения; |
|||||
µц |
– 0,003…0,005; |
|
|
|
|
|
f – коэффициенттрениякаченияштангиоролики, f= 0,0015…0,002, м; ηxx = 0,5η – КПД механизма на холостом ходу.
a |
b |
c |
|
|
P |
|
PΣсл |
|
|
P1сл |
|
|
|
|
Pxx |
|
|
|
|
|
|
|
|
S |
Мст |
|
|
|
|
|
|
|
|
t |
ta |
tb |
tc |
td |
te |
Рис. 2. Нагрузочная диаграмма толкателя |
ГОУ ВПО УГТУ-УПИ – 2005 |
Стр. 6 из 39 |
|

Паршин В.С., Спиридонов В.А., Мухоморов В.Л. |
Толкатели заготовок для металлургических печей |
На участке b статический момент Mс будет равен, кНм: |
|
Mс =Mxx +Gсл µDш , |
(3.4) |
2 i η |
|
где Gсл – вес слитка, кН;
µ – коэффициент трения между слитками и подом печи (при движении заготовки по чугунным направляющим – µ= 0,2…0,5; по стальным направляющим – µ= 0,4…0,7; по керамическим направляющим – µ= 0,6…1,0; поглиссажнымнаправляющим трубам – µ= 0,3).
На участке c статический момент является максимальным и складывается из момента холостого хода и момента от сталкивания всей садки, кН м:
Mc =Mxx + |
∑Gсл µDш |
. |
(3.5) |
|
2 i η |
||||
|
|
|
После проталкивания всей садки двигатель тормозится, затем разгоняется в противоположную сторону и возвращает толкатель в исходное положение. Следует учесть, что обратная скорость в полтора – два раза выше скорости толкания, в результате чего время возврата будет также ниже. После возврата толкателя возникает пауза до следующего цикла толкания. Таким образом, на нагрузочной диаграмме толкателя появятся ещё два участка: d – возврат толкателя в исходное положение и участок e – пауза до следующего цикла толкания. На участке d статический момент равен моменту холостого хода.
Следует отметить, что при работе толкателя в переходных режимах, когда скорость изменяется, нагрузка на валу двигателя отличается от статической на величину динамических составляющих момента и мощности, зависящих от момента инерции двигателя, который пока не известен. В связи с этим задача может быть решена в два этапа: 1) предварительный выбор двигателя; 2) проверка двигателя по перегрузочной способности и по нагреву.
Для предварительного выбора двигателя по известной нагрузочной диаграмме механизма можно найти средний момент статической нагрузки [12]:
ГОУ ВПО УГТУ-УПИ – 2005 |
Стр. 7 из 39 |
|
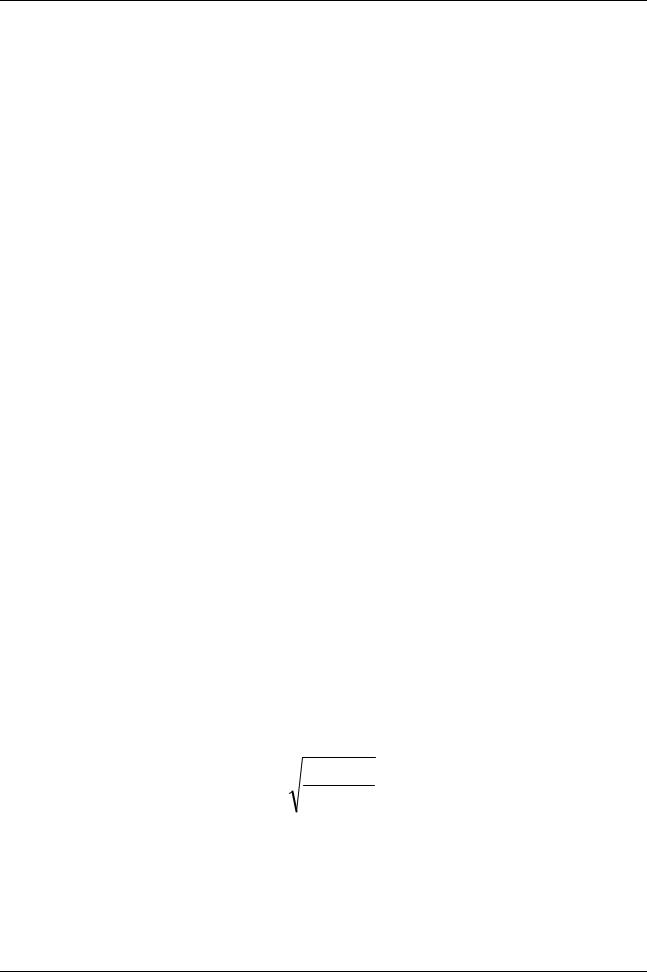
Паршин В.С., Спиридонов В.А., Мухоморов В.Л. Толкатели заготовок для металлургических печей
Mc.ср = |
Ma ta +Mb tb +Mc |
tc +Md td |
. |
(3.6) |
|
ta +tb +tc +td +te |
|||||
|
|
|
|||
Номинальный момент выбираемого двигателя определяют из выра- |
|||||
жения |
|
|
|
|
|
|
Мном = kд Мс.ср , |
|
|
(3.7) |
где kд = 1,2 – коэффициент, учитывающий динамические режимы работы привода.
По полученному значению Мном можно выбрать двигатель по каталогу [3].
Можно также определить номинальную мощность двигателя по
формуле: |
|
|
|
Nном = |
(1,2 −1,4)Nmax |
, |
(3.8) |
|
|||
|
λ |
|
где λ – перегрузочная способность двигателя; для двигателей постоянного тока λ = 2…2,5 .
По найденной мощности из каталога [3] выбираем электродвигатель. Общее передаточное число привода находят из отношения числа оборотов (nд, об/мин) выбранного электродвигателя к числу оборотов
(nш, об/мин) реечной шестерни:
|
60V |
i = пд/пш, |
(3.9) |
|
где nш = |
, V – скорость толкания, м/с, dш – диаметр начальной ок- |
|||
|
||||
|
πdш |
|
ружности шестерни.
Задаваясь числом зубьев шестерни (Z ≥ 20), её модуль определяют из расчёта прочности зубьев на изгиб по формуле, мм:
m = |
P KF YF |
, |
(3.10) |
||
|
[σ |
F |
]Ψ |
|
|
|
|
m |
|
|
где P – окружное усилие шестерни, соответствующее толкающему усилию, Н;
YF – коэффициент, учитывающий форму зуба;
[σF] – допускаемое напряжение изгиба с учётом характера нагружения и срока службы передачи, МПа (Н/мм2);
ГОУ ВПО УГТУ-УПИ – 2005 |
Стр. 8 из 39 |
|
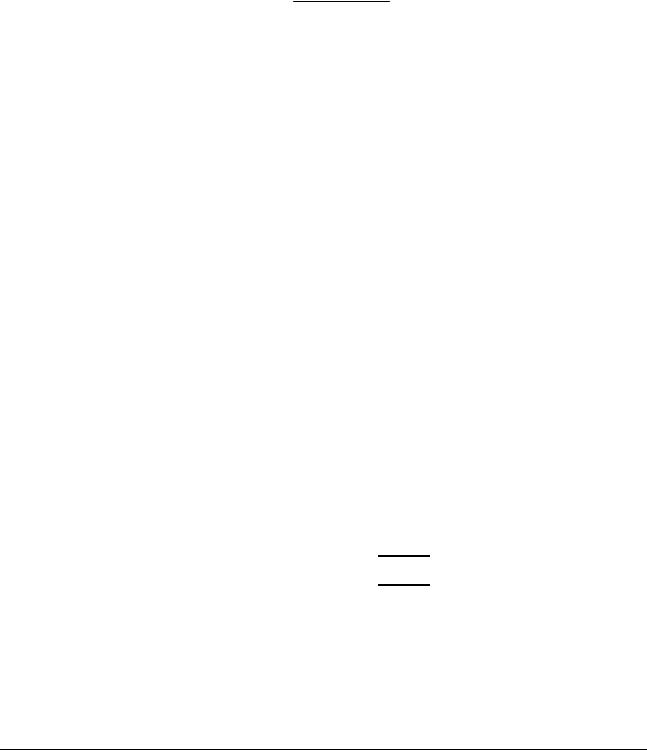
Паршин В.С., Спиридонов В.А., Мухоморов В.Л. |
Толкатели заготовок для металлургических печей |
Ψm = b/m = 10-12 – коэффициент ширины реечного зацепления по модулю зацепления (b – длина зуба рейки, мм).
Коэффициент, учитывающий форму зуба, зависит от числа зубьев и относительного смещения X режущего инструмента. Значения коэффициента ΥF приведены в табл. 2.
Допускаемые напряжения изгиба определяются по формуле:
[σF ] = |
σF0 limb |
, |
(3.11) |
[SF ]' [SF ]" |
где σ0F limb – предел выносливости при отнулевом цикле изгиба, МПа
(табл. 3);
[SF]' – коэффициент, учитывающий нестабильность свойств материала зубчатых колёс (табл. 3) при вероятности неразрушения 99 % (в этом коэффициенте отражена и степень ответственности зубчатой передачи: при вероятности неразрушения большей, чем 99 %, значения [SF]' существенно возрастают);
[SF]" – коэффициент, учитывающий способ получения заготовки зубчатого колеса (для поковок и штамповок [SF]" = 1; для проката
[SF]" = 1,15; для литых заготовок [SF]" = 1,3).
Определённый по формуле (1.5), модуль округляют по ГОСТ 9563–60 и находят диаметр делительной окружности шестерни dш = m Z. Ширину шестерни принимают больше ширины рейки примерно на 5…10 мм.
По общему передаточному числу и мощности привода в каталоге [1] подбирают редуктор.
Таблица 2
Коэффициент формы зуба
Ζ |
|
Коэффициент смещения режущего инструмента |
|
||||||||
–0,5 |
–0,4 |
–0,3 |
–0,2 |
–0,1 |
0 |
+0,1 |
+0,2 |
+0,3 |
+0,4 |
+0,5 |
|
12 |
– |
– |
– |
– |
– |
– |
– |
– |
3,90 |
3,67 |
3,46 |
14 |
– |
– |
– |
– |
– |
– |
4,24 |
4,00 |
3,78 |
3,59 |
3,42 |
17 |
– |
– |
– |
– |
4,50 |
4,27 |
4,03 |
3,83 |
3,67 |
3,53 |
3,40 |
20 |
– |
– |
– |
4,55 |
4,28 |
4,07 |
3,89 |
3,75 |
3,61 |
3,50 |
3,39 |
25 |
– |
4,60 |
4,39 |
4,20 |
4,04 |
3,90 |
3,77 |
3,67 |
3,57 |
3,48 |
3,39 |
30 |
4,60 |
4,32 |
4,15 |
4,05 |
3,90 |
3,80 |
3,70 |
3,62 |
3,55 |
3,47 |
3,40 |
ГОУ ВПО УГТУ-УПИ – 2005 |
Стр. 9 из 39 |
|

Паршин В.С., Спиридонов В.А., Мухоморов В.Л. |
Толкатели заготовок для металлургических печей |
Таблица 3
Значения предела выносливости при отнулевом цикле изгиба σ0F limb и коэффициента нестабильности материала [SF]'
Марка стали |
Термическая или термо- |
σ0F limb, |
[SF]' |
химическая обработка |
МПа |
||
40, 45, 50, 40Х, 40ХФА |
нормализация, улучшение |
1,8НВ |
1,75 |
40Х, 40ХН, 40ХФА |
объёмная закалка |
500…550 |
1,80 |
40ХН, 40ХН2МА |
закалка при нагреве ТВЧ |
700 |
1,75 |
20ХН, 20ХН2М, 12ХН2, 12ХНЗА |
цементация |
700 |
1,55 |
|
|
|
Таблица 4 |
||
|
Твёрдость некоторых сталей |
|
|
||
|
|
|
|
||
Марка |
Диаметр заго- |
Термообработка |
Твёрдость НВ, |
|
|
стали |
товки, мм |
средняя |
|||
|
|||||
40 |
300–800 |
нормализация |
150 |
|
|
45 |
100–800 |
нормализация |
160 |
|
|
40Х |
500–800 |
нормализация |
160 |
|
|
40Х |
св. 160 |
улучшение |
245 |
|
|
40ХФА |
100–500 |
улучшение |
265 |
|
4. ВИНТОВОЙ ТОЛКАТЕЛЬ
Винтовой толкатель подаёт в печь заготовки, продвигает их по ходу печи и выгружает через окно выдачи; применяется для преодолений усилий до 700 кН при ходе башмака до 2,5 м.
Винтовой толкатель (рис. 3) состоит из неподвижной рамы 1, на которой установлены передняя 2 и задняя 3 стойки. К передней стойке прикреплены направляющие втулки 4 для штанг 5, радиальный 6 и упорный 7 подшипники для переднего конца винта 8. При вращении винта перемещаются гайка 10 и связанная с ней траверса 11. Траверса 11 в свою очередь жёстко связана с задними концами штанг 5, которые проходят через направляющие втулки 4 передней стойки, и их передние концы присоединены к общей толкающей головке 12. Такая конструкция обеспечивает работу винта только на растяжение. Винт вращается от привода, состоящего из электродвигателя 13, упругой муфты с электромагнитным
ГОУ ВПО УГТУ-УПИ – 2005 |
Стр. 10 из 39 |
|