
АЕПТВМ КП / КП Толкатели заготовок
.pdf
Паршин В.С., Спиридонов В.А., Мухоморов В.Л. |
Толкатели заготовок для металлургических печей |
тормозом 14 и редуктора 15. Винт соединён с выходным валом редуктора муфтой 16.
13 |
14 |
15 |
16 |
9 |
10 |
8 |
6 |
7 |
12 |
P |
3 |
11 |
5 |
1 |
2 |
4 |
Рис. 3. Схема винтового толкателя
Мощность электродвигателя привода винтового толкателя рассчитывают через усилие и скорость толкания аналогично расчёту, приведённому выше. Определение общего передаточного числа привода и выбор редуктора возможны после расчёта винта и гайки толкателя.
Расчёт винта и гайки толкателя
Основным критерием надёжной работы винтового толкателя является износостойкость резьбы винтовой пары, средний диаметр которой рассчитывают по формуле:
dср = |
2 P |
, |
(4.1) |
Ψ π[p] |
где P – осевая сила, действующая на винт и гайку, Н;
Ψ= H/dср – отношение высоты гайки к среднему диаметру резьбы (принимают для цельных гаек Ψ= 1,2…2,5 и для разъёмных Ψ= 2,5…3,5; большие значения Ψ относят к большим диаметрам);
[p] – допускаемое давление, зависящее от материалов винтовой пары и условий её эксплуатации, МПа (для закалённой стали по бронзе
ГОУ ВПО УГТУ-УПИ – 2005 |
Стр. 11 из 39 |
|

Паршин В.С., Спиридонов В.А., Мухоморов В.Л. Толкатели заготовок для металлургических печей
[p] = 10…13 МПа; для незакалённой стали по бронзе [p] = 8…10 МПа; для незакалённой стали по чугуну [p] = 5…6 МПа).
Для винтовых толкателей принимают при небольших усилиях трапецеидальную резьбу (ГОСТ 9484–81), при больших – упорную (ГОСТ 10177–82) или прямоугольную по следующим соотношениям: рабочая высота профиля резьбы h = 0,1 dср; наружный диаметр резьбы dн = dср + h; внутренний диаметр резьбы dв = dср – h; шаг резьбы S = 2 h.
Если резьба многозаходная с числом заходов Z, то ход резьбы S1 и угол наклона ϕ определяют соответственно по формулам:
S1 = z S, tgϕ = S1/πdср.
Прочность винта толкателя, работающего одновременно на растяжение и кручение, проверяют по формуле наибольших касательных напряжений:
σ= σ2 +4τ2 ≤[σ] , |
(4.2) |
р |
|
где напряжения от растяжения σ= Р/F = 4 P/(πdв2) и напряжение от кручения
τ= Mкр/W = [P tg(ϕ+ ρ)(dср/2)+ Mоп]/W. |
(4.3) |
В этих формулах: P – осевая сила винта; ϕ – угол подъёма винтовой линии; ρ – угол трения (arctg ρ= µ; при слабой смазке для стали по бронзе µ= 0,1 и для стали по чугуну µ= 0,15); dср – средний диаметр нарезки; W = 0,2dв3 – момент сопротивления сечения винта при кручении.
Крутящий момент Mоп от сил трения в подпятнике зависит от его конструкции. Для подпятника скольжения в виде кольцевой пяты момент
равен |
|
|
|
Mоп = |
2 |
Pµ[(R3 −r 3 ) (R2 −r 2 )], |
(4.4) |
|
3 |
|
|
где R и r – наибольший и наименьший радиусы кольцевой пяты.
Для подпятника в виде упорного шарикового подшипника этот момент равен
Mоп = P µ1 d1/2, |
(4.5) |
ГОУ ВПО УГТУ-УПИ – 2005 |
Стр. 12 из 39 |
|

Паршин В.С., Спиридонов В.А., Мухоморов В.Л. Толкатели заготовок для металлургических печей
где µ1 = 0,01…0,03 – коэффициент трения подшипника качения; d1 – диаметр цапфы в упорном подшипнике.
Допускаемое напряжение на растяжение рекомендуют принимать
[σ] = σТ/3, |
(4.6) |
где σТ – предел текучести материала винта. |
|
Число оборотов винта толкателя nв определяется |
отношением |
V (м/мин) кходу резьбы S1 (м), об/мин: |
|
nв = V/S1. |
(4.7) |
Тогда общее передаточное число привода винтового толкателя – |
|
i = nд/nв, |
(4.8) |
где nд – число оборотов выбранного электродвигателя под нагрузкой, об/мин.
5.РЫЧАЖНЫЙ ТОЛКАТЕЛЬ
Вотличие от конструкций толкателей, у которых штанга с большим ходом и движется возвратно-поступательно в результате реверсивного вращения электродвигателя, у рычажного толкателя возвратнопоступательное движение толкающего устройства происходит при непрерывном вращении электродвигателя в одном направлении. Обычно рычажные толкатели рассчитаны на малые и средние толкающие усилия со скоростями движения 2…3 м/миниходомтолкателя впределах 200…600 мм.
Преобразование вращательного движения двигателя в возвратнопоступательное движение толкающего устройства в рычажном толкателе
сэлектрическим приводом происходит следующим образом (рис. 4). Электродвигатель вращает входной вал 1 редуктора 2 с кривошипом 3
на выходном валу 4. Кривошип соединён шатуном 5 с рычагом 6, закреплённым на валу 7.
На этом же валу насажены несколько коротких рычагов 8, к которым одним концом шарнирно присоединены толкающие штанги 9. Штанги проходят через окна печи и другим концом скользят по направляющей плите внутри печи. При движении вперёд штанги проталкивают через на-
ГОУ ВПО УГТУ-УПИ – 2005 |
Стр. 13 из 39 |
|

Паршин В.С., Спиридонов В.А., Мухоморов В.Л. |
Толкатели заготовок для металлургических печей |
гревательную печь весь ряд длинных заготовок на величину хода. При обратном движении штанг между ними и концом ряда заготовок подаётся следующая заготовка, после чего цикл повторяется.
2 |
5 |
9 |
P
1 |
3 |
4 |
6 |
7 |
8 |
Рис. 4. Схема рычажного толкателя
Кинематический расчёт рычажного толкателя сводится к выбору размеров рычажной системы для обеспечения заданного хода толкателя и определению передаточного числа.
Механизм толкателя можно рассматривать как шестизвенный – AB, BC, CDE, AD, EF и F (рис.5). Точки A и D зафиксированы друг относительно друга, поэтому их также следует рассматривать как звено. Точки C, D и E также жёстко зафиксированы друг относительно друга, и поэтому звено CDE рассматривается как единое. Изменяемые углы ϕ3 и ϕ4 отличаются друг от друга на величину ∆ϕ34, являющуюся постоянным параметром для конкретного конструктивного исполнения звена DCE.
B
A |
ϕ1 |
C ∆ϕ34
ϕ2
E
D |
ϕ |
ϕ4 |
|
3 |
ϕ5 F
ГОУ ВПО УГТУ-УПИ – 2005 |
Стр. 14 из 39 |
|

Паршин В.С., Спиридонов В.А., Мухоморов В.Л. |
Толкатели заготовок для металлургических печей |
Рис. 5. Кинематическая схема рычажного толкателя
Механизм толкателя можно условно разделить на четырёхзвенный механизм ABCD и кривошипно-шатунный DEF, синтез которых подробно рассмотрен в литературе [2,5,6,10,11,13].
Начнём синтез рычажного толкателя с рассмотрения механизма DEF, изображённого на рисунке 6а. Имеем: H = D1F2 – D1F1, где
D1F2 = lDE cosϕ42 + lEF cosϕ52 и |
|
D1F1 = lDE cosϕ41 + lEF cosϕ51. |
|
|||
Тогда, учитывая, что lDE/lEF = δ, |
получим: |
|
|
|||
|
|
1 |
|
|
|
|
H =lDE cosϕ42 −cosϕ41 |
+ |
|
|
(cosϕ52 |
−cosϕ51 ) . |
(5.1) |
|
δ |
|||||
|
|
|
|
|
|
|
Выразим cosϕ51 и cosϕ52 через углы ϕ41 и ϕ42. Из полученного выра- |
||||||
жения определяем sinϕ51 и, преобразовывая его, определяем cosϕ51 : |
|
|||||
e +lDE sinϕ41 |
2 |
(5.2) |
||||
cosϕ51 = 1− |
|
|
lEF |
. |
||
|
|
|
|
|
Аналогичное выражение можно записать и для углов ϕ52 и ϕ42.
В кинематической схеме предлагаемой для задания на курсовой проект эксцентриситет равен нулю, поэтому, подставляя (5.2) в (5.1) и учитывая, что e = 0, получим:
lDE = |
|
|
|
|
|
H |
|
|
. (5.3) |
|
cosϕ42 |
−cosϕ41 |
+ |
1 |
( |
1−(δ sinϕ42 )2 − |
1−(δ sinϕ41 )2 ) |
||||
|
|
|||||||||
|
|
|
|
δ |
|
|
|
|
|
Таким образом, задаваясь ходом толкателя H, углами ϕ41, ϕ42 и δ, можно определить длины звеньев DE и EF.
Синтез четырёхзвенного механизма будем осуществлять по минимальному углу давления в начале проталкивания заготовок, углу ϕ31 образованному между крайним положением коромысла DC и горизонтальной прямой, а также коэффициенту λ= lBC/lAB (рис. 6, б). (Угол давления – угол между вектором силы, приложенной к ведомому звену (без учёта трения), и вектором скорости приложения силы.)
ГОУ ВПО УГТУ-УПИ – 2005 |
Стр. 15 из 39 |
|

Паршин В.С., Спиридонов В.А., Мухоморов В.Л. |
Толкатели заготовок для металлургических печей |
Угол давления будет близок к нулю при положении механизма AB1C1D, когда звенья AB и BC образуют между собой угол в 90°. Значит, в этом положении механизма следует начать проталкивать заготовки.
E1 E2
|
|
|
|
|
|
C |
ϕ41 |
ϕ42 |
|
|
|
B |
ϕ2 |
D |
e |
ϕ51 |
|
ϕ52 |
A |
ϕ1 |
|
|
|
|
ϕ3 |
||
D1 |
|
|
H |
|
|
|
|
F1 |
|
F2 |
D |
||
|
а) |
|
|
|
|
б) |
B1 |
C3 |
C1 |
|
|
|
|
|
|
|
|
|
|
|
|
|
|
C2 |
B3 |
A |
B2 |
|
|
M |
|
|
|
|
||
|
|
|
ϕ33 |
|
|
|
|
e |
|
|
|
|
|
|
ϕ32 |
|
|
|
|
|
ϕ |
|
|
|
|
|
|
31 |
|
|
O |
D |
C1′ |
C2′ |
|
|
|
P |
90°-ϕ42 |
в)
P ϕ32-ϕ12
F
C |
|
ϕ42+ϕ52 |
ϕ12-ϕ22 |
|
E |
|
B |
ГОУ ВПО УГТУ-УПИ – 2005 |
Стр. 16 из 39 |
|
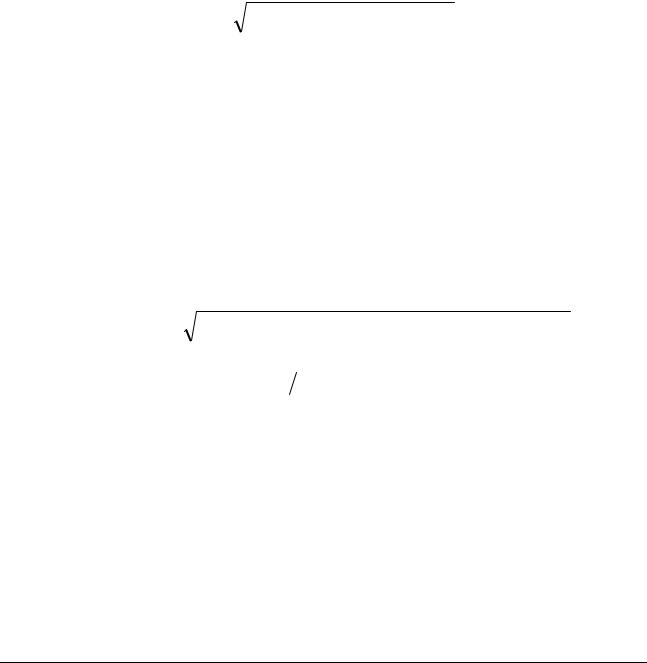
Паршин В.С., Спиридонов В.А., Мухоморов В.Л. |
Толкатели заготовок для металлургических печей |
г) |
д) |
Рис. 6. Схема к синтезу рычажного толкателя
Данная схема обеспечит рабочий ход толкателя, обусловленный углами качания коромысла ϕ31 – ϕ32. При крайнем левом положении механизма коромысло DC составляет угол с горизонталью ϕ33. Таким образом, ход ползуна F, обусловленный углами ∆ϕ= ϕ31 – ϕ32 будет холостым, т. е. на этом участке проталкивания заготовок не будет.
Начнём синтез механизма ABCD. Из ∆AC2M (см. рис. 6, в) имеем
C2M = (AB2 +B2C2 )2 −(OC2' )2 , |
(5.4) |
где
(5.5)
OC2' = lBC – lDC cosϕ31 + lDC cosϕ32 . (5.6)
Из ∆DC1C1' имеем C1C1' = lDC sinϕ31. С другой стороны C1C1' = lAB + e. Длину звена DC определим как lDC = c lDE, где c – коэффициент про-
порциональности, определённый по чертежу прототипа толкателя. Подставляя (5.5) и (5.6) в (5.4) и учитывая, что λ= lBC/lAB, получим
систему уравнений с тремя неизвестными lAB, lBC, e :
lDC sinϕ32 −e = (lAB +lBC )2 −[lBC −lDC (cosϕ31 |
−cosϕ32 )]2 |
|
lDC sinϕ31 =lAB +e |
|
. (5.7) |
|
||
lBC lAB = λ |
|
|
|
|
|
Выразив e и lAB через lBC, получим квадратное уравнение относительно lBC:
2 |
2 |
|
|
|
sinϕ32 −sinϕ31 |
|
|
|
lBC +2lDC |
cosϕ31 |
−cosϕ32 |
− |
|
lBC − |
|
λ |
λ |
||||||
|
|
|
|
|
|||
|
−2lDC2 |
[1−cos(ϕ32 −ϕ31 )]. |
|
(5.8) |
Задавшись значениями λ, ϕ31 и ϕ32, можно определить lBC, а затем lAB.
ГОУ ВПО УГТУ-УПИ – 2005 |
Стр. 17 из 39 |
|

Паршин В.С., Спиридонов В.А., Мухоморов В.Л. |
Толкатели заготовок для металлургических печей |
Таким образом, мы определили длины всех звеньев рычажного толкателя, т. е. осуществили его синтез.
Для выбора двигателя и редуктора необходимо определить передаточное отношение механизма χ, равное отношению линейных скоростей точки B кривошипа и точки F ползуна:
χ= VB |
ωD . |
(5.9) |
ω |
V |
|
D |
F |
|
Для дальнейшего определения передаточного отношения строим с произвольным масштабным коэффициентом µV планы скоростей криво- шипно-ползунного механизма DEF (рис. 6, г) и четырёхзвенного механизма ABCD (рис. 6, д). Пользуясь этими планами скоростей, выразим передаточное отношение механизма χ:
χ = |
PB |
|
PE lDE |
. |
(5.10) |
PC lDC |
|
PF |
|||
|
|
|
|
Отношение PE/PF можно вычислить из косоугольного треугольника PEF по теореме синусов:
PE |
= |
cosϕ5 |
|
. |
(5.11) |
|
PF |
sin(ϕ4 +ϕ5 ) |
|||||
|
|
|
Аналогично можно вычислить отношение PB/PC треугольника PCB:
PB = sin(ϕ3 −ϕ2 ) . PC sin(ϕ1 −ϕ2 )
из косоугольного
(5.12)
Подставляя (5.11) и (5.12) в (5.10), получим:
χ= |
lDC |
|
sin(ϕ3 |
−ϕ2 )cosϕ5 |
. |
(5.13) |
lDE |
|
sin(ϕ1 −ϕ2 )sin(ϕ4 +ϕ5 ) |
||||
|
|
|
|
Как видно из уравнения (5.10), передаточное отношение шестизвенного механизма является величиной переменной, зависящей от угла поворота кривошипа и от соотношений длин звеньев. Следовательно, имея постоянную скорость вращения кривошипа, ползун будет иметь переменную скорость. Задавшись средней скоростью толкания заготовок (скоростью
ГОУ ВПО УГТУ-УПИ – 2005 |
Стр. 18 из 39 |
|

Паршин В.С., Спиридонов В.А., Мухоморов В.Л. |
Толкатели заготовок для металлургических печей |
ползуна VF), можно определить расчетное значение угловой скорости кривошипа ωкр:
ω = χVf . |
(5.14) |
кр lAB
Мощность привода рычажного толкателя определяется по формуле:
N = |
PVF |
. |
(5.15) |
|
|||
|
η |
|
После этого выбирают двигатель по каталогу [1]. Определив Mдв, ωдв конкретного двигателя, можно выбрать редуктор по передаваемой мощности и передаточному числу i = ωдв/ωкр .
6. ФРИКЦИОННЫЙ ВЫТАЛКИВАТЕЛЬ
Фрикционный выталкиватель применяют для выдачи из печи горячих слитков, выталкиваемых штангой в торец. Во фрикционном выталкивателе ход штанги достигает 5 м и более при скоростях движения до 1 м/с. Толкающее усилие редко превышает 5…10 кН. Квадратная штанга 1 движется возвратно-поступательно от двух фрикционных роликов, установленных на подшипниках в передней стойке 2. Необходимое толкающее усилие создаётся в результате того, что верхний ролик прижимает штангу к нижнему ролику при помощи нажимных винтов и пружин 3. Оба ролика вращаются приводом в разных направлениях. Штанга движется по направляющей балке 6, которая одним концом опирается на заднюю стойку 7, а другим – на вертикальную цапфу 5 передней стойки. Это даёт возможность поворачивать штангу в горизонтальной плоскости на небольшой угол для выталкивания из печи перекосившихся слитков.
Для передачи штанге толкающего усилия P фрикционные ролики должны быть прижаты к штанге с усилием N, определяемым по формуле:
/ |
µ, |
(6.1) |
N = βP |
где β – коэффициент запаса сцепления роликов, который рекомендуется принимать в силовых передачах, равным β= 1,25…1,5;
ГОУ ВПО УГТУ-УПИ – 2005 |
Стр. 19 из 39 |
|

Паршин В.С., Спиридонов В.А., Мухоморов В.Л. |
Толкатели заготовок для металлургических печей |
µ – коэффициент трения между роликами и штангой, принимаемый |
|
для трения стали по стали |
или по чугуну без смазки, – равным |
µ= 0,15…0,2 и для трения стали по стали при наличии смазки – равным
µ= 0,04…0,05.
Затем мощность и общее передаточное число привода выталкивателя находят по описанной ранее методике расчёта реечных толкателей.
|
4 |
3 |
|
|
|
2 |
|
|
|
1 |
P |
7 |
6 |
5 |
|
Рис. 7. Схема фрикционного выталкивателя |
|
7. РАСЧЁТ ШТАНГ ТОЛКАТЕЛЕЙ
Как было рассмотрено выше, штанги передают вращательное движение и толкающее усилие P от привода толкателя на рабочий орган (башмак или линейку), непосредственно проталкивающий заготовки в печи.
Штанги проверяют на прочность по максимальному напряжению от совместного действия рабочего усилия сжатия и изгиба. Изгиб, как правило, вызван внецентренным приложением усилия сжатия со стороны толкающей линейки или усилия в зубчатой передаче со стороны привода.
Расчёт выполняют по известной зависимости:
σ |
= |
P |
+ |
M |
≤[σ], |
(7.1) |
|
A |
W |
||||||
max |
|
|
|
|
|||
|
|
|
|
max |
|
|
|
где P – усилие проталкивания |
заготовок; А – поперечное |
сечение |
|||||
штанги; |
|
|
|
|
|
|
ГОУ ВПО УГТУ-УПИ – 2005 |
Стр. 20 из 39 |
|