
METODAAA_33__33__33_0001
.pdf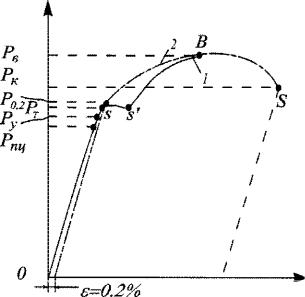
низкоотпущенная |
сталь, чугун и |
др.), характерно хрупкое разрушение |
(рис. 2.5.2, в). |
|
|
Р |
Р |
р |
о |
М О |
Л/ О |
А/ |
а) |
|
б) |
В ) |
Рис. 2.5.2. Диаграммы растяжения: а - диаграмма материала значительной пластичности; б - диаграмма со скачкообразным переходом из упругой в пластическую область; в - диаграмма материала в хрупком состоянии
Для определения механических свойств на диаграмме растяжений отмечаются характерные точки, по которым определяют: предел пропорциональности, предел упругости, предел текучести, временное сопротивление разрыву, истинное сопро тивление разрыву (рис. 2.5.3).
Рис. 2.5.3. Характерные точки на диаграмме растяжений, по которым
рассчитывают характеристики прочности: 1 - диаграмма истинных напряжений; 2 - диаграмма условных напряжений
ЛЦе)
Для упругой области нагружения характерна прямая пропорциональная зави симость между Р и / (участок ОРпц на рис. 2.5.3). Это означает, что изменение длины образца прямо пропорционально нагрузкам. Основной характеристикой прочности в этой области является модуль продольной упругости Е (модуль Юн га), определяемый тангенсом угла наклона, упругой линии диаграммы растяже-
163
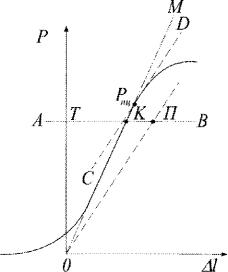
ний P-l. Приближённо величину Е можно рассчитать делением задаваемого при роста напряжения на каждой последовательной ступени нагружения на среднюю величину приращения относительной упругой деформации в той области, где со храняется постоянство этой характеристики. Приращение деформации измеряют тензометрами большой точности и чувствительности. В настоящее время величи ну Е определяют не при растяжении по ГОСТ 1497-84, а различными динамиче скими способами.
Условное наибольшее напряжение, задаваемое с определённым допуском, до которого деформация прямо пропорциональна нагрузке, называется пределом
пропорциональности. |
Зная нагрузку Рщ |
и начальную площадь поперечного се |
|||||
чения образца F0 |
рассчитывают предел |
пропорциональности ощ: |
|||||
|
|
|
|
с, пц |
Рщ/ Fa |
(2.5.1) |
|
|
|
|
|
При |
определении предела |
пропорционально |
|
|
|
|
|
сти допускается некоторая условность, связанная с |
|||
|
|
|
|
трудностью точного определения значения на |
|||
|
|
|
|
грузки, которая соответствует пределу пропор |
|||
|
|
|
|
циональности. |
Величину апц |
определяют непо |
|
|
|
|
|
средственно по показаниям зеркального тензо |
|||
|
|
|
|
метра при последовательном нагружении образца |
|||
|
|
|
|
или графическим методом по машинной диа |
|||
|
|
|
|
грамме растяжения. Графический метод пригоден |
|||
|
|
|
|
только в тех случаях, если масштаб диаграммы по |
|||
|
|
|
|
оси деформации не менее 50:1 и по оси нагрузки - |
|||
|
|
|
|
не более 10 МПа/мм. При определении <5пц гра |
|||
|
|
|
|
фическим методом проводят |
прямую ОМ, совпа |
||
|
|
|
|
дающую с условно прямолинейным участком диа |
|||
|
|
|
|
граммы (рис. 2.5.4). На этой прямой откладывают |
|||
Рис. 2.5.4. Схема |
отрезок КП, равный половине отрезка ТК. Точки 77 |
||||||
графического определения |
и О соединяют прямой и параллельно этой прямой |
||||||
предела пропорциональности |
|
|
|
|
|||
по |
диаграмме^ |
растяжения„ |
проводят касательную CD к кривой растяжения. |
||||
|
|
|
|
Точка касания прямой CD с диаграммой рас- |
|||
|
|
|
|
тяжения и есть |
Р,пц. |
|
|
Условное напряжение, при |
котором остаточное удлинение достигает 0,05 % |
(иногда меньше - 0,005 %) от расчётной длины образца, называется пределом уп ругости. Допуск указывается в обозначении предела упругости (например, ао,о5, ао,о2)- Зная нагрузку Рупр и начальную площадь поперечного сечения образца F0j рассчитывают предел упругости <5упр'.
Pynp/Fo. |
(2.5.2) |
При определении <5упр графическим методом расчёт ведут аналогично случаю с ъщ (рис. 2.5.5).
164
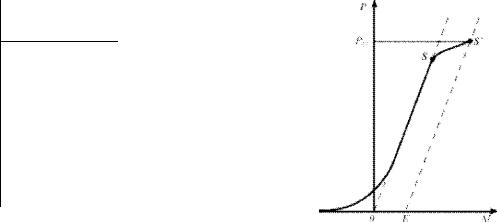
Условное напряжение, при котором деформация образца происходит без за метного увеличения роста нагрузки, называется физическим пределом текуче сти. Положение площадки текучести я - я ' н а диаграмме растяжения определяет нагрузку Рт, знание которой позволяет рассчитать физический предел текучести
GT = PT/F0. |
(2.5.3) |
Условное напряжение, при котором остаточная деформация (удлинение) дос тигает 0,2% от расчётной длины образца, называется условным пределом текуче сти. Его определение целесообразно, когда на диаграмме растяжения нет ярко выраженной площадки текучести, тогда находят нагрузку Род, аналогично приве денной ранее методике (рис. 2.5.6). Зная нагрузку Р 0 д и начальную площадь попе речного сечения образца Fo, рассчитывают условный предел текучести стод:
ст0 д = Р 0 д / ^ 0 . |
(2.5.4) |
Величины а щ , ао,о5, стт, стод, характеризуют сопротивление малым пластиче ским деформациям. Сопротивление значительным пластическим деформациям характеризуются временным сопротивлением. Обычно максимальная нагрузка в этом случае совпадает с началом образования шейки на образце.
/
//
//
//
/#
Рис. 2.5.5. Схема примерного |
Рис. 2.5.6. Схема определения |
определения предела упругости |
условного предела текучести |
по диаграмме растяжения |
по диаграмме растяжения |
Отношение наибольшей нагрузки Рв, отмеченной за время испытания, к пер воначальной площади поперечного сечения образца F 0 , называется временным сопротивлением (или пределом прочности) оВ'-
GB = PB/F0. |
(2.5.5) |
Отношение нагрузки в момент разрыва образца Рк к площади поперечного се чения в шейке образца после разрыва FR называется истинным сопротивлением разрыву SR-'
165
SK=PK/FK. |
(2.5.6) |
Пластические свойства материалов при растяжении оценивают по значениям относительного удлинения 8 и относительного сужения \|/ образцов после разры ва.
Относительным удлинением образца называется отношение приращения расчётной длины образца после разрыва к первоначальной расчётной длине, вы раженной в процентах:
5 = [ ( / * - / о ) / / о ]ЮО%, |
(2.5.7) |
где 1к - длина расчётной части образца после разрыва. Для её определения разру шенные части образца плотно складываются так, чтобы их оси образовывали прямую линию.
Относительным сужением образца называется отношение уменьшения площади поперечного сечения образца к первоначальной площади, выраженное в процентах:
i|/ = Pb -FK)/Fo] 100%, |
(2.5.8) |
где FK~ площадь поперечного сечения после разрыва.
Для определения относительного сужения измеряют минимальный диаметр образца после разрыва в двух взаимно перпендикулярных направлениях. По сред нему арифметическому из полученных значений рассчитывают площадь попереч ного сечения FR.
Определение механических свойств металлов и сплавов имеет важное значе ние и широко используется в промышленности. При сдаче готовой продукции ме таллургических заводов обязательно контролируются: временное сопротивление разрыву (предел прочности) ов, предел текучести ст0,2, относительное удлинение 8, относительное сужение \\f.
Испытание на твёрдость металлических образцов
Из всех видов механических испытаний твёрдость определяют чаще всего. Это объясняется простотой и высокой надёжностью метода измерения твёрдости, а также тем, что испытание можно проводить на самом изделии, не вызывая его по вреждений.
Твёрдостью называется свойство материала оказывать противодействие меха ническому проникновению в него более твёрдого постороннего тела.
По своей физической сущности твёрдость есть характеристика сопротивляе мости материала местному пластическому деформированию. Поэтому показатель твёрдости связан с показателями прочности и пластичности материала и зависит от конкретных условий ведения испытаний.
Твёрдость является вторичной характеристикой прочностных свойств материала и находится в тесной взаимосвязи с ними. Определив твёрдость материала, можно косвенно судить и о его пределе прочности. Однако в
166
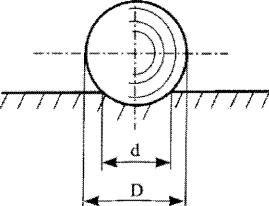
большинстве случаев испытание на твёрдость проводится с целью контроля качества металла и его термообработки.
Основными методами определения твёрдости являются методы внедрения в поверхность образца металла стандартных наконечников из твёрдых недеформирующихся материалов под действием статических нагрузок. В качестве стандарт ных наконечников используются стальной шарик, алмазный конус, пирамида. Сравнение характеристик твёрдости, полученных при различных испытаниях, проводится с помощью эмпирических зависимостей. Значение твёрдости выража ется числами твёрдости в различных шкалах.
В настоящее время применяют, в основном, следующие методы определения твёрдости: метод Бринелля, метод Роквелла и метод Виккерса. В данной работе испытания проводятся по методу Бринелля и методу Роквелла.
При измерении твёрдости любым способом поверхность испытуемого образца или детали должна быть плоской, так как при измерении твёрдости цилиндриче ских образцов наконечник вдавливается глубже, чем при испытании плоских об разцов той же твердости, поэтому твёрдость получается заниженной.
Поверхность образца или изделия должна быть горизонтальной и не иметь та ких дефектов, как окалина, грязь, забоины, различные покрытия. Все поверхност ные дефекты должны быть удалены мелкозернистым наждачным кругом, напиль ником или наждачной бумагой. При нанесении отпечатка на испытуемое изделие или образец расстояние между соседними отпечатками и до края образца должно быть не менее 3 мм.
Определение твёрдости по Бринеллю
Для определения твёрдости по Бринеллю в качестве твёрдого тела, вдавливае мого в испытуемый материал, используют стальной шарик определённого диа метра D, который вдавливают в испытуемый материал с усилием Р. После снятия нагрузки на поверхности материала остается шаровый отпечаток диаметром d (лунка) (рис. 2.5.7). Показателем твёрдости является число твёрдости по Бринел лю, обозначаемое НВ (Н - Hardness, англ. - твёрдость, В - начальная буква на звания метода Brinell).
Р
Рис. 2.5.7. Схема образования отпечатка при испытании
твёрдости по Бринеллю
167
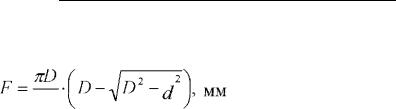
Отношение усилия Р к поверхности полученного отпечатка (шарового сегмен та) F дает число твёрдости НВ:
|
Т Т О _ Р |
, 2 |
. |
(2-5.9) |
||
|
rib - —, |
кг/мм |
|
|
||
|
F |
|
|
|
|
|
Поверхность шарового сегмента: |
|
|
|
|
|
|
|
F = iiDh, |
мм2, |
|
(2.5.10) |
||
где D - диаметр вдавливаемого шарика, мм; h - глубина отпечатка, мм. |
|
|
||||
Выразив h через диаметры шарика D и отпечатка d, получим |
|
|
||||
h = |
D-Jrf-d' |
|
|
|
(2 |
-5.11) |
|
|
|
мм. |
|||
2 |
|
|
|
|
||
|
|
|
|
|
||
Тогда поверхность шарового сегмента |
|
|
|
|
|
|
2 |
|
|
|
|
(2.5.12) |
|
|
|
|
|
|
|
|
а число твердости по Бринеллю будет характеризоваться формулой |
|
|
||||
|
2Р |
|
|
|
|
|
н " ^ Й ^ 7 ) ' к г / м м 2 |
|
( 2 - 5 Л З ) |
В зависимости от толщины испытываемого материала метод испытания твер дости по Бринеллю позволяет применять шарики различного диаметра: 10,5, 5,0 и 2,5 мм.
Нагрузка Р в зависимости от качества испытываемого материала будет соот
ветствовать |
|
P=KD2, |
(2.5.14) |
где К - постоянная для данного материала величина, равная 30, 10 или 2,5.
Для измерения диаметра отпечатка используется либо лупа, либо инструмен тальный микроскоп, дающий увеличение в 10-20 раз. Инструментальный микро скоп снабжен отсчётной линейкой. Устанавливая микроскоп над отпечатком (лункой), проводят её замер, устанавливая диаметр в двух взаимно перпендику лярных направлениях, после чего высчитывают среднее значение (рис. 2.5.8).
Твёрдость по Бринеллю выражается в кгс/мм (значение твёрдости по Бринел лю обычно даётся без указания размерности, например, НВ 360). Для перевода твёрдости в систему СИ пользуются коэффициентом к = 9,81-106, на который ум ножают табличное значение твёрдости: НВСи = НВ-&, Па = НВ-к-10~6 МПа (мегапаскалей).
Методом Бринелля можно испытывать материалы с твердостью не более НВ 450. При более высокой твердости испытываемого материала вдавливаемый ша рик деформируется, и результаты испытания искажаются.
168
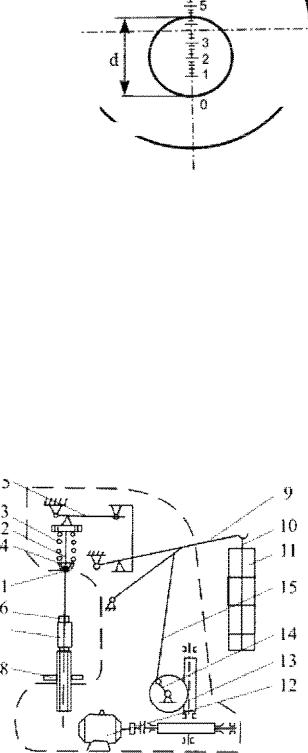
По значениям твердости по Бринеллю можно с некоторым приближением су дить о прочности металла при растяжении, так как между числом твердости НВ и временным сопротивлением разрыву ав (МПа) экспериментально установлены следующие соотношения:
НВ 125... 175, |
с г в * 3 , 5 Н В ; |
более НВ 175, |
<тв ~ 3,4 НВ. |
Испытание на твёрдость по Бринеллю проводят на приборах - твердомерах марки ТБ, в которых нагрузка на наконечник со стальными шариками прилагается через систему рычагов, нагрузка подбирается комбинацией грузов.
Схема специального автоматического пресса (твердомера), применяемого в настоящее время для измерения твердости по Бринеллю, представлена на рис. 2.5.9.
Рис. 2.5.9. Схема автоматического пресса для измерения твёрдости
по Бринеллю
Шарик 1 закреплен на конце шпинделя 2. Пружина 3 прижимает втулку 4 к конусному седлу. Испытуемый образец 6 устанавливается на столик 7 и вращени ем маховика 8 до упора поджимается к шарику 1. При этом пружина 3 сжимается,
169
создавая предварительную нагрузку Р0 = 100 кг (961 Н), необходимую для фикси рования на рабочем столике образца. Основная нагрузка прикладывается к шари ку через систему рычагов.
На длинном рычаге 9 расположена подвеска 10, на которую навешиваются съемные грузы 11. В зависимости от количества этих грузов нагрузка на образец (основная) может устанавливаться в пределах от 187,5 до 3000 кг. Пусковой кнопкой включается электродвигатель 12, который через двухступенчатый червячный редуктор 13 поворачивает кривошип 14, опускает шатун 15, поддерживающий рычаг 9. В результате этого нагрузка от грузов через рычаги 9 и 5 и шпиндель 2 прикладывается к образцу. При этом на прессе загорается контрольная лампочка. Образец находится под действием постоянной нагрузки в течение некоторого заданного, регулируемого контактами, времени. Затем изменяется направление вращения двигателя, шатун 15 поднимается и снимает нагрузку. Вращением маховика 8 опускают столик с образцом и замеряют диаметр отпечатка. Число твердости подсчитывается по формуле или определяется по приложению 5.
Определение твёрдости по Роквеллу
Определение твёрдости по Роквеллу проводится путем вдавливания в испыты ваемый образец алмазного (или из твердого сплава) конуса с углом при вершине 120° или закаленного шарика диаметром 1,588 мм. Шарик используется для менее твёрдых материалов, а конус - для более твёрдых.
Вдавливание шарика или конуса производится под действием двух последова тельно прилагаемых нагрузок - предварительной Ро и основной Pi:
|
|
|
Р=Р0+РЪ |
(2.5.15) |
где Р |
- |
общая нагрузка; Ро - |
предварительная нагрузка, во |
всех случаях равна |
10 кг; |
Pi |
- основная нагрузка; |
при вдавливании стального |
шарика (шкала В) - |
90 кг, при вдавливании алмазного конуса (шкала С) - 140 кг, (шкала А) - 50 кг. Выбор нагрузки (шкалы) зависит от предполагаемой твёрдости испытуемого
материала и от формы вдавливаемого тела.
Твёрдость по Роквеллу определяется глубиной вдавливания шарика или кону са в поверхность испытуемого материала под действием основной нагрузки.
Число твёрдости по Роквеллу HR (R - Rockwell, англ. - первая буква названия метода) - число отвлеченное, выражается в условных единицах и зависит от раз ности глубин h - ho, где ho- глубина внедрения под действием предварительной нагрузки; h - окончательная глубина внедрения после снятия основной нагрузки и сохранения предварительной (рис. 2.5.10).
За единицу твёрдости принята величина, соответствующая осевому перемеще нию наконечника на 0,002 мм.
Таким образом, число твёрдости по Роквеллу (HR) определяется по формуле: HR = 130-/ - при измерении по шкале В;
170
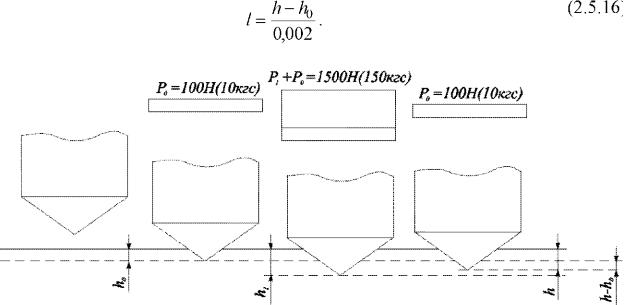
HR = 100-/ - при измерении по шкалам С и А; величина / - определяется по формуле
Рис. 2.5.10. Схема вдавливания наконечника при определении твердости по Роквеллу
В зависимости от того, применяют ли шарик или алмазный конус, и от нагруз ки, при которой проводят испытание (то есть по какой шкале: В, С или А), число твёрдости обозначают HRB, HRC или HRA.
Определение твёрдости по Роквеллу имеет широкое применение, так как этот прибор дает возможность испытывать мягкие, твёрдые, а также тонкие материа лы. Отпечатки от конуса или шарика очень малы, что позволяет испытывать гото вые детали без их порчи; испытание легко выполнимо и занимает мало времени, не требуется никаких измерений, а число твёрдости читается прямо по шкале.
Циферблат индикатора пресса имеет две шкалы - чёрную и красную. При ис пытании твёрдости алмазным конусом, отсчёт производят по чёрной шкале, стальным шариком - по красной.
Схема автоматического твердомера ТК (твердомер конусный), применяемого для измерения твёрдости по Роквеллу, представлена на рис. 2.5.11. Твердомер со стоит из рычажного механизма нагружения с грузами 1 и приводом от электромо тора 2, измерительной системы с индикатором 9 для определения глубины отпе чатка, механизма подъема столика 6 для установки образца и шпиндельной го ловки со сменными наконечниками 7.
Образец укладывают на столик 6 и вращением маховичка 5 поднимают до со прикосновения с наконечником 7. Продолжают вращение до тех пор, пока малая стрелка индикатора не станет против красной точки, а большая - вертикально. При таком положении стрелок пружина 8 сжимается и создает предварительную нагрузку на образец 10 кг. Затем при помощи маховичка 4 циферблат индикатора 9 устанавливается так, чтобы большая стрелка показывала нуль черной шкалы
171
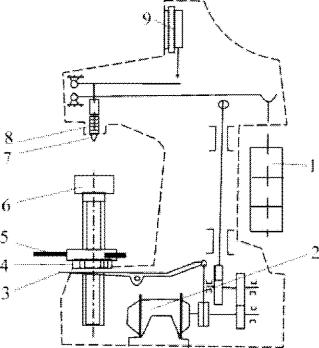
или (при испытании шариком) деление 30 красной. Нажатием клавиши 3 вклю чается механизм нагружения прибора и автоматически осуществляется цикл вдавливания (нагружение нагрузкой Р - выдержка - снятие нагрузки). По окон чанию цикла стрелка индикатора 9 показывает твёрдость по Роквеллу. Вращением маховичка 5 образец отводится от наконечника.
Рис. 2.5.11. Схема автоматическо го пресса для измерения твёрдости
по Роквеллу
Определение твёрдости по Виккерсу
Данный метод используют для определения твёрдости деталей малой толщи ны и тонких поверхностных слоев, имеющих высокую твёрдость. Твёрдость оп ределяется вдавливанием в испытуемую поверхность (шлифованную или даже полированную) четырёхгранной алмазной пирамиды.
Твёрдость по Виккерсу HV (МПа) определяют по формуле
HV = 1,854 (P/d2) 10"6, |
(2.5.17) |
где Р - нагрузка на пирамиду, Н; d - среднее арифметическое значение длин обе их диагоналей отпечатка, измеряемых после снятия нагрузки, м.
При измерении твёрдости применяют следующие нагрузки: 10; 20; 100; 200; 300; 500 Н. Чем тоньше материал, тем меньше должна быть нагрузка. Число твёр дости по Виккерсу определяется по специальным таблицам по измеренной вели чине d. Перевод чисел твёрдости HV в систему СИ аналогичен переводу чисел твёрдости НВ.
Во многом аналогично методу Виккерса и происходит измерение микротвёр дости, с той лишь разницей, что нагрузка составляет 0,05... 5 Н, и требуется более тщательная подготовка образцов.
172