
ОРГ срс Тарасова
.pdf
МИНИСТЕРСТВО ОБРАЗОВАНИЯ И НАУКИ РОССИЙСКОЙ ФЕДЕРАЦИИ ВОЛЖСКИЙ ПОЛИТЕХНИЧЕСКИЙ ИНСТИТУТ (ФИЛИАЛ)
ФЕДЕРАЛЬНОГО ГОСУДАРСТВЕННОГО БЮДЖЕТНОГО ОБРАЗОВАТЕЛЬНОГО УЧРЕЖДЕНИЯ ВЫСШЕГО ПРОФЕССИОНАЛЬНОГО ОБРАЗОВАНИЯ «ВОЛГОГРАДСКИЙ ГОСУДАРСТВЕННЫЙ ТЕХНИЧЕСКИЙ УНИВЕРСИТЕТ»
КАФЕДРА «ТЕХНОЛОГИЯ И ОБОРУДОВАНИЕ МАШИНОСТРОИТЕЛЬНЫХ ПРОИЗВОДСТВ»
Т. С. Тарасова
ВЫБОР И ПРОЕКТИРОВАНИЕ ЗАГОТОВОК.
МЕТОДИЧЕСКИЕ УКАЗАНИЯ К ВЫПОЛНЕНИЮ ОргСРС
Методические указания
Волгоград
2012
УДК.621.91.01
Рецензент:
канд. тех.наук доцент С.В.Семенов
Издается по решению редакционно-издательского совета Волгоградского государственного технического университета
Тарасова, Т. С. Выбор и проектирование заготовок. Методические указания к выполнению ОргСРС [Электронный ресурс]: методическое указание / Т. С. Тарасова // Сборник «Методические указания» Выпуск 2. - Электрон. текстовые дан. (1 файл: 2,82 МБ) - Волжский: ВПИ (филиал) ВолгГТУ, 2012. – Систем. требования: Windows 95 и выше; ПК с процессором 486 +; CD-ROM. – номер гос. регистрации
0321200818.
В методическом указании приводятся краткие теоретические сведения о технологии получения заготовок свободной ковкой.. Рассмотрены методы выбора и расчета припусков на механическую обработку. Приведены нормативные материалы необходимые для расчета и выбора припусков и предельных отклонений на механическую обработку по ГОСТ 7062, ГОСТ 7829, методика и примеры выполнения семестровых заданий.
Предназначены для студентов бакалавриата, обучающихся по направлениям: 150900.62 «Технология оборудования и автоматизация машиностроительных производств», «Конструкторско-технологическое обеспечение машиностроительных производств», 200500 «Метрология, стандартизация и сертификация» всех форм обучения.
© Волгоградский государственный технический университет, 2012
© Волжский политехнический институт, 2012
2
СОДЕРЖАНИЕ |
|
Введение |
4 |
Термины и определения |
5 |
1. Семестровое задание №1 |
|
Проектирование заготовки для заданной детали из заданной марки |
|
стали методом свободной ковки на молоте (ГОСТ 7829) |
6 |
2. Семестровое задание №2
Проектирование заготовки для заданной детали из заданной марки
стали методом свободной ковки на прессе (ГОСТ 7062) |
17 |
3. Семестровое задание №3
Проектирование заготовки для заданной детали из заданной марки
стали методом штамповки (ГОСТ 7505) |
27 |
4. Семестровое задание №4 |
|
Проектирование заготовки для данной детали из заданной марки |
|
материала методом литья в песчаные формы (ГОСТ 26645) |
27 |
5. Семестровое задание №5 |
|
Проектирование заготовки для данной детали из заданной марки |
|
стали методом литья в кокиль (ГОСТ 26645) |
27 |
Список литературы |
28 |
3
ВВЕДЕНИЕ
Важным этапом разработки технологического процесса механической обработки является расчет припусков.
Установление правильных размеров припусков на обработку - ответственная технико-экономическая задача. Назначение чрезмерно больших припусков приводит к непроизводительным потерям материала, превращаемого в стружку, увеличению трудоемкости механической обработки; повышению расхода режущего инструмента и электрической энергии; возрастанию потребности в оборудовании и рабочей силе. При этом затрудняется построение операций на настроенных станках, снижается точность обработки в связи с увеличением отжатий в технологической системе.
Недостаточно большие припуски не обеспечивают удаления дефектных слоев материала и необходимой точности и шероховатости обрабатываемых поверхностей, а также вызывают ужесточение требований к точности исходных заготовок и приводят к удорожанию последних, затрудняют разметку и выверку положения заготовок на станках по методу пробных ходов, увеличивают опасность появления брака.
Вметодических указаниях изложен опытно-статистический метод установления припусков при различных методах получения заготовок.
При изучении специальных дисциплин, таких как «Технология машиностроения», «Технологическая оснастка», «Металлорежущий инструмент», студентам приходится решать вопросы проектирования технологических процессов обработки деталей, конструирования технологической оснастки и режущих инструментов. Решение этих задач невозможно без освоения дисциплины «Выбор и проектирование заготовок».
Методические указания включают три семестровых работы: первая из двух семестровых заданий; вторая - из одного; третья - из двух, охватывающих важнейшие разделы дисциплины и данные из стандартов по различным видам заготовок - поковкам, штамповкам, отливкам.
Вметодических указаниях определены цель, содержание и методика выполнения каждого семестрового задания, приводятся примеры выполнения, необходимые справочные материалы или ссылки на справочную литературу.
Задания выдаются преподавателем. Каждая семестровая работа выполняется на листах формата А4 с титульным листом, страницы нумеруются, приводится список литературы.
4
ТЕРМИНЫ И ОПРЕДЕЛЕНИЯ
1 Припуск – предусмотренное превышение размеров поковки против номинальных размеров детали или предварительно ободранной заготовки, обеспечивающее после обработки резанием требуемые чертежом размеры детали (ободранной заготовки) и чистоту ее поверхности.
2 Напуск – увеличение припуска, упрощающее конфигурацию поковки ввиду невозможности или нерентабельности изготовления поковки по контуру детали.
3 Допуск на кузнечную обработку – разность между наибольшим и наименьшим предельными размерами поковки.
4 Верхнее отклонение на размер – разница между наибольшим предельным и номинальным размерами поковки.
5 Нижнее отклонение на размер – разница между номинальным и нижним предельным размерами поковки.
6 Бурт – неконцевой участок поковки увеличенного поперечного сечения, у которого длина равна или меньше 0,3D или 0,3B, где D – диаметр бурта, B – большая сторона прямоугольника.
7 Уступ – участок поковки с меньшим поперечным сечением, чем смежный с ним участок. Для поковок типа вал величина уступа выражается полуразностью диаметров смежных участков.
8 Выступ – участок поковки с большим поперечным сечением, чем смежный с ним участок.
9 Выемка – участок поковки, диаметр или сторона которого меньше диаметра или сторон двух смежных с ним участков.
10 Фланец – концевой участок вала, увеличенного диаметра или стороны прямоугольника, у которого длина l ≤ 0,3D или l ≤ 0,3 H, где D – диаметр фланца, H – большая сторона прямоугольника.
11Поковка стальная штампованная (поковка) - изделие,
изготовленное горячей объемной штамповкой в соответствии с техническими требованиями ГОСТ 8479.
12Масса поковки - весовой параметр поковки, определяемый исходя из ее формы и плотности стали.
13Радиальное биение - разность наибольшего и наименьшего расстояний от профиля сечения поковки до его оси.
14Допуск радиального биения - наибольшее допускаемое значение радиального биения.
15Масса поковки расчетная - установленная величина,
используемая при назначении припусков и допусков.
16Исходный индекс - условный показатель, учитывающий в обобщенном виде сумму конструктивных характеристик (класс точности, группу стали, степень сложности, конфигурацию поверхности разъема) и массу поковки.
5
Семестровое задание №1
Проектирование заготовки для заданной детали из заданной марки стали методом свободной ковки на молоте (ГОСТ 7829)
1 ЦЕЛЬ РАБОТЫ
Изучить методику назначения припусков и предельных отклонений на механическую обработку, установленных ГОСТ 7829, для поковок изготовляемых из углеродистой и легированной сталей ковкой на молотах.
2 СОДЕРЖАНИЕ РАБОТЫ
1.Освоить методику назначения припусков предельных отклонений на механическую обработку, определения напусков и возможности выполнения на поковках концевых и промежуточных уступов, выемок, фланцев и буртов.
2.Выполнить расчетное задание.
3 ТЕОРЕТИЧЕСКАЯ ЧАСТЬ
3.1 Свободная ковка на молотах
Свободная ковка это процесс пластической деформации, нагретого до определенной температуры металла, происходящий под действием последовательных ударов бойка молота.
При машинной ковке процесс формообразования поковки происходит под ударами падающих частей ковочных молотов (бабы, штока, поршня и бойка).
По виду привода различают молоты паровоздушные, пневматические, механические и гидравлические. В кузнечном производстве в основном применяются паровоздушные (приводятся в действие за счет использования энергии пара или сжатого воздуха) и пневматические (работают за счет энергии разряжения и сжатия воздуха, находящегося между рабочим и компрессорным поршнями) ковочные молоты различных конструкций.
В зависимости от конструкции станин паровоздушные молоты могут иметь массу падающих частей от 1 до 8 т.
Отечественные пневматические молоты выпускаются с массой падающих частей от 50 до 1000 кг.
Ковка не только изменяет форму и размеры обрабатываемого металла, но и способствует улучшению его структуры и механических
6
свойств. Она измельчает и уплотняет зерна, устраняет внутренние раковины и пористости.
Свободная ковка обычно применяется для получения единичных поковок различной формы и размеров, а также при изготовлении небольших партий поковок.
Данный метод является универсальным для изготовления поковок на молотах или прессах. Ковкой получают заготовки для самых разнообразных деталей массой от 10 граммов до 250 тонн, с точностью размеров по 15 - 16-му квалитетам (допуски составляют 3… 30 мм), шероховатостью поверхности до Rz 80 мкм.
В местах сложной конфигурации приходится прибегать к напускам для упрощения формы, что увеличивает объем механической обработки.
Недостатки ковки: низкая производительность; высокая стоимость оборудования; низкая точность и высокая шероховатость поверхности (необходима механическая обработка, следовательно - увеличивается расход металла); высокие затраты энергии, связанные с нагревом заготовки; требуется высококвалифицированная рабочая сила.
Достоинство ковки: это единственный метод получения особо крупных изделий, к которым предъявляются особые требования к качеству внутренней кристаллической структуры, при эксплуатации с высокими механическими нагрузками.
Термины и определения, применяемые в методических указаниях, приведены на странице 5.
3.2 Припуски на механическую обработку резанием, величины предельных отклонений, величины и условия назначения напусков на поковки, изготовляемые ковкой на молотах
Припуски на механическую обработку резанием, величину предельных отклонений на номинальные размеры, а также величину и условия назначения напусков для поковок общего назначения, изготовляемых из углеродистой и легированной прокатной стали или начерно обработанного слитка производят по ГОСТ 7829 для ковки на молотах в единичном и мелкосерийном производстве.
Форма и соотношение размеров основных типов поковок по табл. 1. Припуски назначают на номинальные размеры детали из расчета
механической обработки поковок с двух сторон.
Предельные отклонения устанавливаются на номинальные размеры поковок.
Допускается округлять расчетные номинальные размеры поковки до ближайших целых чисел в большую сторону.
7
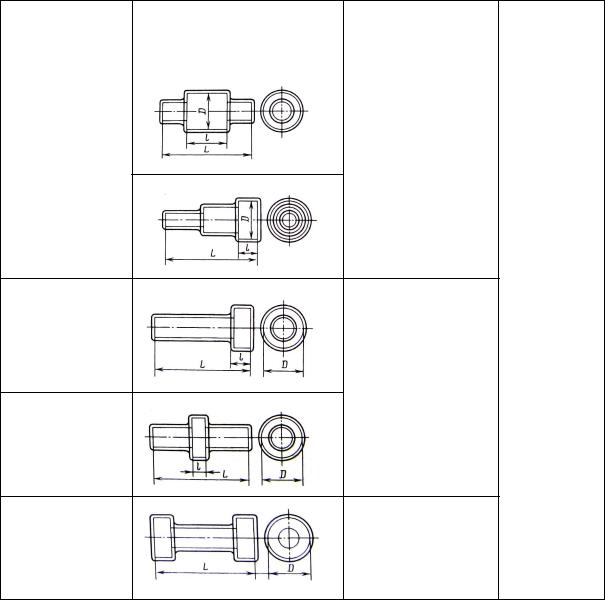
Объем и вес поковок определяется по номинальным размерам с учетом напусков на скосы между уступами, на скос от руба, на сферу и на конусность отверстия.
Таблица 1 - Основные типы поковок
|
|
|
Номер |
Тип поковки |
Эскиз поковки |
Соотношение |
таблиц |
|
|
размеров |
припусков и |
|
|
|
допусков |
Круглого |
|
|
|
сечения с |
|
|
|
уступами |
|
|
|
L > 1,5 D l > 0,3 D
2, 3
Круглого сечения с фланцем
L > 1,5 D l ≤ 0,3 D
Круглого сечения с буртом
Круглого
сечения с L > 1,5 D выемкой
Припуски и предельные отклонения для поковок круглого |
и |
||
квадратного |
сечений с уступами назначаются |
основные |
и |
дополнительные. |
|
|
|
Основные припуски z и предельные отклонения ±T/2 |
на диаметр и |
размер сечения устанавливают в соответствии с рис. 1 и табл. 2.
Длину уступов и выемок на чертеже поковки указывают от единой базы. За базу принимают торец выступа наибольшего сечения, не являющийся торцом поковки.
8
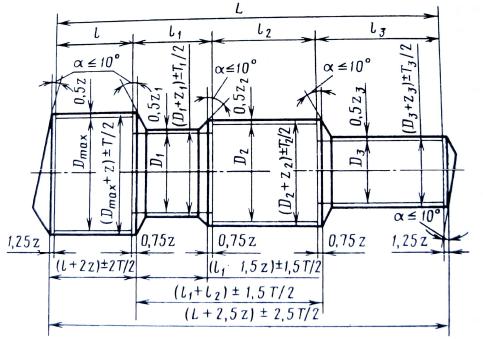
Таблица 2 - Припуски и предельные отклонения поковок, мм
Длина детали, |
|
Диаметр детали D или размер сечения B, H, мм |
|
|||||||||
L |
|
|
|
|
|
|
|
|
|
|
|
|
до |
св. 50 |
св. 70 |
св. 90 |
|
св.120 |
|
св. 160 |
св. 200 |
св. 250 |
св. 300 |
||
мм |
|
|
||||||||||
50 |
до 70 |
до 90 |
до120 |
|
до 160 |
|
до 200 |
до 250 |
до 300 |
до 390 |
||
|
|
|
||||||||||
|
|
|
|
|
|
|
|
|
|
|
|
|
|
|
Припуски (z; z1; z2; z3) и предельные отклонения |
|
|||||||||
|
|
|
|
(±T/2; ±T 1/2; ±T2/2; ±T3/2) |
|
|
||||||
До 250 |
5±2 |
6±2 |
7±2 |
8±3 |
|
9±3 |
|
- |
- |
|
- |
- |
Св. 250 до 500 |
6±2 |
7±2 |
8±2 |
9±3 |
|
10±3 |
|
11±3 |
12±3 |
|
13±4 |
14±4 |
Св. 500 до 800 |
7±2 |
8±2 |
9±3 |
10±3 |
|
11±3 |
|
12±3 |
13±4 |
|
14±4 |
15±4 |
Св. 800 до 1200 |
8±2 |
9±3 |
10±3 |
11±3 |
|
12±3 |
|
13±4 |
14±4 |
|
15±4 |
16±4 |
Св.1200 до 1700 |
- |
10±3 |
11±3 |
21±4 |
|
13±4 |
|
14±4 |
15±4 |
|
16±5 |
17±5 |
Св.1700 до 2300 |
- |
11±3 |
12±3 |
13±4 |
|
14±4 |
|
15±4 |
16±5 |
|
17±5 |
18±5 |
Св. 2300 до 3000 |
- |
- |
13±4 |
14±4 |
|
15±4 |
|
16±5 |
17±5 |
|
18±5 |
19±5 |
Св. 3000 до 4000 |
- |
- |
- |
15±5 |
|
16±5 |
|
17±5 |
18±5 |
|
19±5 |
20±6 |
Св. 4000 до 5000 |
- |
- |
- |
16±5 |
|
17±5 |
|
18±5 |
19±5 |
|
20±6 |
21±6 |
Св. 5000 до 6000 |
- |
- |
- |
- |
|
18±5 |
|
19±5 |
20±6 |
|
21±6 |
22±6 |
Дополнительный припуск S назначают по табл. 3 на диаметры (размеры) всех сечений детали, кроме основного, в зависимости от разности диаметров (размеров) наибольшего и рассматриваемого сечений детали, с назначенными на нее основными припусками.
-
Рисунок 1- Поковка вала с уступами и выемками
Основное сечение определяют в следующем порядке:
- если поковка имеет ступень с необрабатываемой поверхностью, то за основное сечение принимают ступень с необрабатываемой поверхностью;
9
- если у поковки нет ступеней с необрабатываемой поверхностью, то для определения основного сечения рассчитывают площади продольных сечений ступеней D'1 . l'1 ; D'2 . l'2 ; D'3 . l'3 ; … и сравнивают их с площадью продольного сечения выступа с наибольшим диаметром D'max . l' ;
Таблица 3 - Дополнительный припуск S на диаметры (размеры) всех сечений, кроме основного, мм
Разность |
|
|
|
|
|
|
|
|
|
|
|
|
|
|
|
|
|
диаметров |
До |
Св. 40 |
Св. 80 |
Св.100 |
|
Св.120 |
Св.140 |
Св.160 |
Св. |
||||||||
наибольшего и |
40 |
до 80 |
до100 |
до 120 |
|
до 140 |
до 160 |
до 180 |
180 |
||||||||
рассматриваемого |
|
|
|
|
|
|
|
|
|
|
|
|
|
|
|
|
|
сечений, мм |
|
|
|
|
|
|
|
|
|
|
|
|
|
|
|
|
|
Дополнительный |
|
|
|
|
|
|
|
|
|
|
|
|
|
|
|
|
|
припуск на |
|
|
|
|
|
|
|
|
|
|
|
|
|
|
|
|
|
диаметр S1, S2, S3 |
3 |
4 |
|
5 |
|
|
6 |
|
|
|
7 |
|
8 |
9 |
|
10 |
|
|
- если все полученные значения D'1. l'1 ; D'2 |
. l'2 ; D'3 |
. l'3 ; … |
меньше, чем |
|||||||||||||
D'max |
. l' , то за основное сечение принимают выступ с наибольшим |
||||||||||||||||
диаметром; |
|
|
|
|
|
|
|
|
|
|
|
|
|
|
|
|
|
|
- если есть значения D'1. l'1 ; D'2 |
. l'2 ; D'3 |
. l'3 ; … |
большие, чем D'max . l' , то |
|||||||||||||
для |
тех значений D'1 |
. l'1 ; D'2 |
. l'2 ; |
D'3 |
. l'3 |
; … |
|
которые больше D'max |
. l' , |
||||||||
рассчитывают величины: |
|
|
. l'1 - D'max . l' ); |
|
|
|
|
|
|
|
|||||||
|
|
|
A1 = S1(D'1 |
|
|
|
|
|
|
|
|||||||
|
|
|
A2 = S2(D'2 |
. l'2 - D'max . l' ) и т.д. |
|
|
|
|
|
иза основное сечение принимают сечение, для которого величина А имеет наибольшее значение;
-если за основное сечение принят не выступ наибольшего диаметра
D'max , то дополнительный припуск переносят с основного сечения на выступ наибольшего диаметра.
Выполнимость на поковках концевых и промежуточных уступов, выемок, фланцев и буртов (рис. 2) проверяют после назначения основных
идополнительных припусков в соответствии с табл. 4.
Таблица 4 - Минимальная выполнимая высота уступа
Диаметр (D'1; D'2; D'3), мм |
До100 |
Св.100 |
Св.180 |
Св.250 |
|
|
до 180 |
до 250 |
|
Минимальная выполнимая высота уступа |
|
|
|
|
(h'1; h'2; h'3), мм |
4 |
5 |
6 |
7 |
Концевые и промежуточные уступы (рис. 2, а) выполняют, если их высоты h'1; h'2; h'3; … не менее значений, приведенных в табл. 4, и если их
10