
Методичка
.pdf4. Перечень тем практических занятий
|
Таблица 2 |
|
|
Тема дисциплины |
Наименование практического занятия |
|
|
1 |
2 |
|
|
Тема 2. Основные |
Работа 1. Анализ технических условий на |
положения теории |
изделие |
технических систем |
|
|
|
Тема 3. Разработка изделий |
Работа 2. Составление схемы сборки и анализ |
и основы теории |
технологичности |
оптимизации |
Работа 4. Процессы сборки различных |
|
соединений |
|
|
Тема 4. Разработка |
Работа 5. Составление технологического |
технического задания |
процесса сборки |
|
|
Тема 5. Проектная и |
Работа 3. Анализ и расчет сборочных |
рабочая конструкторская |
размерных цепей |
документация |
Работа 7. Разработка инструкции приемочного |
|
контроля и программы испытаний изделия |
|
|
Тема 7. Методы |
Работа 6. Проектирование приспособлений для |
проектирования |
сборки |
|
|
4.1.Методические указания по выполнению практических работ
Тема 2. Основные положения теории технических систем
Практическая работа № 1
АНАЛИЗ ТЕХНИЧЕСКИХ УСЛОВИЙ НА ИЗДЕЛИЕ
Цель:
Ознакомление с устройством, назначением, функциональными возможностями и условиями эксплуатации изделия.
Выявление технических характеристик, возможных неисправностей и методов их устранения.
11
Составление рекомендации по техническому уходу и правил
безопасной эксплуатации за изделием.
Содержание работы
1.Ознакомиться с чертежом изделия, разобраться в устройстве и работе изделия, составить спецификацию, сформулировать служебное назначение.
2.Исходя из назначения изделия, определить его технические характеристики.
3.Установить технические требования на функционирование, сборку,
контроль и приемочные испытания изделия.
Методические указания
Разбираясь с устройством и работой изделия, необходимо установить полноту представленных материалов: достаточно ли имеется видов, разрезов и сечений на чертежах, данных по зубчатым передачам, размеров и посадок в сопряжениях деталей, насколько полно представлены технические условия.
При необходимости выполнить дополнительные разрезы, сечения,
проставить размеры, посадки, параметры зубчатых передач.
Под служебным назначением машины понимают кратко и четко сформулированную задачу, для решения которой предназначена машина.
Анализ служебного назначения следует начинать с ожидаемых результатов действия машины. В их состав могут входить показатели производительности, мощности, развиваемого усилия, грузоподъемности и т.п.
Формулировка служебного назначения должна включать перечень условий, в которых предстоит работать машине.
Техническая характеристика изделия состоит из перечня наиболее важных параметров изделия, вытекающих из его служебного назначения, с
указанием диапазона их изменения и допустимых отклонений. В описание
12
устройства машины входит перечисление основных элементов и их взаимного расположения (например, редуктор цилиндрический состоит из разъемного корпуса, в котором на подшипниках качения монтируется быстроходный вал с муфтой и тихоходный вал с червячным колесом). Также кратко описывается работа изделия.
Технический уход за изделием состоит из периодических осмотров внешнего вида машины, проверки уровня масла в системе смазки,
периодической замены масла, периодических проверок величин зазоров в зацеплениях и люфтов подвижных деталей, подтяжки крепежных болтов.
Из возможных неисправностей указывают на те, что возникают в процессе эксплуатации: тугой ход, повышенный шум, нагрев, вибрации, а
также возможные их причины и способы устранения.
Технические условия требований, предъявляемых к изделию в процессе сборки и приемочного контроля (окраска машины и отдельных ее частей,
применяемая смазка, боковой зазор в зубчатых передачах, радиальное биение быстроходного вала, и т.п.).
Содержание отчета
1. Назначение изделия, его функциональные возможности и условия нормальной эксплуатации.
2.Техническая характеристика изделия.
3.Устройство и работа изделия, правила безопасной эксплуатации.
4.Рекомендации по техническому уходу за изделием.
5.Возможные неисправности и методы их устранения.
6.Технические условия на сборку (последовательность), регулировку зазоров, контроль параметров и приемочные испытания (длительность в час).
Контрольные вопросы
1.Что понимается под служебным назначением изделия?
2.Что может входить в состав технических требований па сборку и приемку изделия?
3.Какие возможны неисправности в работе передаточных механизмов?
13
4.В чем состоит технический уход за изделием в период эксплуатации?
5.Что понимается под технической характеристикой изделия?
Практическая работа № 2
СОСТАВЛЕНИЕ СХЕМЫ СБОРКИ И АНАЛИЗ ТЕХНОЛОГИЧНОСТИ
Цель:
Разработка технологических схем общей и узловой сборки изделия.
Качественная и количественная оценка технологичности сборки изделия
и отдельных соединений.
Содержание работы
1.Анализ структуры изделия и выделение сборочных единиц.
2.Определение последовательности сборки изделия и составление технологических схем сборки.
3.Качественный и количественный анализ технологичности сборки изделия.
Методические указания
Эффективность сборки часто определяется тем, из какого количества самостоятельных узлов собирается изделие. Поэтому целесообразно перед началом проектирования процесса сборки выделить из состава изделия те сборочные единицы, которые можно будет собирать самостоятельно и в готовом виде включать в состав изделия. К сборочным единицам не относятся мелкие (3–5 деталей) узлы в виде, например, рукоятки в сборе.
Последовательность сборки определяется, как правило, конструкцией изделия. Сначала устанавливают последовательность сборки составных частей изделия, а затем переходят к общей сборке. Общая сборка начинается с основной, базовой детали (корпус, рама, станина), к которой последовательно присоединяются все остальные элементы (с.е. и детали прямого вхождения).
14
Последовательность общей сборки изделия и узловых сборок в наглядной форме представляются технологическими схемами сборки (см. приложение
1).
На схеме сборки каждый элемент изделия (деталь, узел) изображается прямоугольником, разделенным на три части. В верхней части прямоугольника указывается наименование элемента, в левой нижней части
– числовой индекс по спецификации, а в правой нижней – количество этих элементов, устанавливаемых одновременно. Перед числовым индексом сборочной единицы ставят буквы "Сб" (сборка).
Схема строится в порядке выполнения сборки, которая начинается с базовой детали. По номеру этой детали ставят числовой индекс с.е. Процесс общей сборки изображается на схеме горизонтальной линией. Ее проводят слева направо от базового элемента к собранному изделию. Сверху над этой линией располагают условные изображения деталей прямого вхождения в изделие, а снизу все узлы (с.е.) в последовательности их присоединения к базовой детали. При одновременном присоединении двух–трех элементов линии от их условного изображения подводятся к одной точке на схеме.
На технологические схемы наносят краткие надписи, поясняющие характер выполняемых технологических операций (запрессовать, клепать,
проверить зазор, отрегулировать длину хода и т.п.), когда они не ясны из сборочных чертежей. Кроме того, на схемах выполняются краткие пояснительные надписи по выполнению дополнительных работ, например,
разборку составных частей при выполнении пригонки деталей.
Качественная оценка технологичности собираемого изделия на уровне
"хорошо – плохо" должна включать:
1)анализ возможности расчленения изделия на самостоятельные сборочные единицы;
2)оценку удобства сборки и доступность мест соединения не только ручным, но и механизированным инструментом,
15
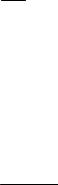
3)возможность сборки из предварительно собранных узлов, возможность параллельной сборки нескольких узлов,
4)оценку возможности применения механизированных инструментов,
5)анализ возможности регулирования положения деталей,
6)наличие направляющих фасок на собираемых деталях;
7)наличие окон для доступа к деталям внутри корпуса и т.п.
Процесс сборки значительно облегчается наличием монтажных зазоров,
позволяющих свободно проходить деталям через отверстия и окна в корпусах, вводить собираемые детали, сборочные единицы снаружи, а не изнутри корпуса.
Из количественных оценок технологичности целесообразно определить коэффициент сборности изделия:
Ксб Дсб
Д
где Дсб – суммарное число деталей, входящих в сборочные единицы (узлы); Д
– общее число деталей в изделии (без учета мелких крепежных деталей).
Уровень стандартизации конструкции изделия может быть оценен коэффициентом стандартизации:
Кст Ест Дст ,
ЕД
где Ест – число стандартных сборочных единиц (подшипников, масленок,
муфт); Дст – число стандартных деталей прямого вхождения (рым-болты,
шпонки, без мелких крепежных деталей); Е – общее число сборочных единиц в изделии; Д – общее число деталей прямого вхождения.
Коэффициент унификации резьбы:
К |
ур |
|
|
К рi |
, |
|
Крi Коi |
||||||
|
|
|
где Крi – количество отверстий с резьбой i-го размера, Коi –количество одинаковых отверстий с однотипной резьбой i-го размера.
16
Содержание отчета
1.Технологические схемы общей и узловой сборки изделия.
2.Качественная и количественная оценка технологичности сборки изделия и отдельных соединений.
Контрольные вопросы
1.Что представляет собой технологическая схема сборки?
2.Для чего составляется технологическая схема сборки?
3.Какие существуют рекомендации по составлению технологических схем сборки?
4.Дайте определение технологичности изделия с точки зрения сборки
его?
5.Как выполняется качественная оценка технологичности изделия?
6.Какие возможны показатели количественной оценки технологичности?
Практическая работа № 3
АНАЛИЗ И РАСЧЕТ СБОРОЧНЫХ РАЗМЕРНЫХ ЦЕПЕЙ
Цель:
Составление схем рассчитываемых размерных цепей, наложенных на
чертеж изделия, и выбор для расчета замыкающих звеньев.
Содержание работы
1.Выбрать из технических условий на сборку изделия два наиболее ответственных требования: зазор в подшипниках, боковой зазор в зубчатой передаче. Установить значение замыкающего звена и допускаемые отклонения.
2.Построить схемы двух размерных цепей: одну – с линейными размерами (регулировка зазора в подшипниках), другую – включающую звенья с пространственными отклонениями (обеспечение бокового зазора в зубчатом зацеплении). Назначить экономичные допуски на размеры.
17
3. Рассчитать погрешность замыкающего звена при экономичных допусках. Определить методы достижения точности замыкающих звеньев
(полной взаимозаменяемости, пригонки или регулировки). 4. Определить параметры компенсирующих звеньев.
Методические указания
Наибольшую трудность представляет поиск и построение размерных цепей. Эту работу начинают с замыкающих звеньев, определяющих эксплуатационные параметры изделия (например, величины радиального биения выходного вала редуктора, величины бокового зазора в цилиндрической зубчатой передаче, величины осевого зазора в паре конических подшипников).
Затем, переходя от сопрягающихся поверхностей одной детали к другой,
ищут наиболее короткий путь, связывающий те две поверхности,
относительное положение которых определяет величину замыкающего звена.
При построении сборочных размерных цепей особое значение имеют отклонения расположения поверхностей или их осей от определенного конструктором заданного расположения (отклонение посадочных шеек вала,
наружной и внутренней поверхностей втулки, погрешность делительной окружности зубчатого колеса и посадочного отверстия и т.п.).
После выявления составляющих звеньев определяют их номинальные значения (измерением по чертежу), а затем назначают допуски на их изготовление по средней экономичной точности (8–10 квалитет). Значения допусков принимают по справочным таблицам «Допуски и посадки».
Метод достижения точности замыкающих звеньев обычно определяется конструкцией. Это может быть метод полной или частичной взаимозаменяемости, метод пригонки или регулировки с помощью подвижного, либо неподвижного компенсатора (для многозвенных цепей).
Чаще всего необходимая точность сборочных размерных цепей с числом звеньев свыше 4 – достигается путем пригонки (мелкосерийное производство) или регулировки (крупносерийное производство). Сопоставив
18
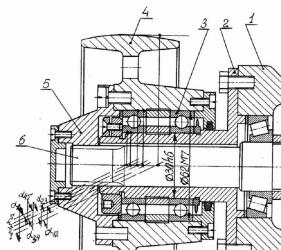
значение требуемой и получающейся величин замыкающего звена,
определяют необходимую величину компенсации или регулирования.
Расчетом проверяют достаточность конструкторских размеров для обеспечения максимально возможной величины компенсации или регулирования (пригонки):
k p т
где р – расчетное значение погрешности замыкающего звена при принятых отклонениях составляющих звеньев;
– требуемое (заданное) по техническим условиям значение погрешности замыкающего звена.
Поскольку наибольшие трудности у студентов возникают при расчете размерных цепей с пространственными отклонениями, рассмотрим простой пример построения и расчета такой цепи (рис. 1).
Рис. 1. Схема конструкции узла ременной передачи
На чертеже представлен узел ременной передачи. На корпусе машины 1
крепится несущая втулка 2, на которой с помощью подшипников 3 вращается приводной шкив 4. Крутящий момент валу 6 передается через шлицевую втулку 5, закрепленную на шкиве. Так как здесь вращается корпус (шкив), то подшипники садятся в шкив с натягом, а на втулку по переходной посадке.
Техническими требованиями ограничивается биение наружной поверхности
19
шкива, например, величиной 0,1 мм. Но между неподвижной деталью
(несущей втулкой) и вращающимся шкивом имеются подшипники.
Соединение этих деталей вносит погрешность в точность вращения шкива.
Построение размерной цепи начинаем с построения осей, определяющих замыкающее звено, т.е. оси 1 наружной поверхности шкива и оси 5
посадочной шейки втулки. Поскольку оси реальных поверхностей на чертеже сливаются в единую ось, для построения размерной цепи каждую ось рисуем отдельно наклонной к теоретической оси под углом 30…45 . Чтобы показать связь поверхности с ее осью, проводим прямую с точками на концах. Теперь,
идя от одной поверхности, например наружной поверхности шкива, надо прийти к оси поверхности посадочной шейки втулки. Итак, шкив садится своим отверстием (ось 2) на наружное кольцо подшипников (ось 3).
Подшипники своим внутренним кольцом (ось 4) садятся на шейку втулки
(ось 5). Размерная цепь замкнута.
Теперь надо задаться экономичными значениями допускаемых погрешностей этих составляющих звеньев:
12 – несоосность наружной поверхности шкива посадочному отверстию
шкива;
23 – погрешность запрессовки подшипников в шкив (определяется характером посадки);
34 – несоосность наружного и внутреннего колец подшипника;
45 – погрешность посадки подшипников на шейку втулки.
Техника расчетов и значения погрешностей подробно излагается в методических пособиях [3–5].
Содержание отчета
1.Обоснование выбора для расчета замыкающих (исходных) звеньев.
2.Схемы рассчитываемых размерных цепей, наложенные на чертеж изделия: линейной и с пространственными отклонениями.
3.Расчеты размерных цепей тем или иным методом; выводы.
20