
16
.pdfNТО−2 = (Нпл × n) / ПГТР - N КР - NТР - NТО−3 |
(4) |
где ПГТО−2 − периодичность текущего ремонта, ч Для тракторов периодичность проведения ТО-2 составляет 500 мото-ч.
Следовательно для К-701 количество ТО-2 составит:
NТО−2 = (2500 × 3) / 500 -1 - 2 - 4 = 8 шт.
Для трактора ДТ-75М количество ТО-2 составит:
NТО−2 |
= (2500 ×9) / 500 - 3 - 8 -11 = 23 шт. |
|
Для трактора МТЗ-82 количество ТО-2 составит: |
|
|
NТО−2 |
= (2500 ×14) / 500 - 5 -12 -18 = 35 шт. |
|
Количество ТО-1 для тракторов: |
|
|
|
NТО−1 = (Нпл × n) / ПГТР - NКР - NТР - NТО−3 - NТО− 2 |
(5) |
где ПГТО−1 − периодичность текущего ремонта, ч Для тракторов периодичность проведения ТО-2 составляет 125 мото-ч.
Следовательно для К-701 количество ТО-1 составит:
NТО−1 = (2500 × 3) /125 -1 - 2 - 4 - 8 = 45 шт.
Для трактора ДТ-75М количество ТО-1 составит:
NТО−1 = (2500 ×9) /125 - 3 - 8 -11 - 23 = 135 шт.
Для трактора МТЗ-82 количество ТО-1 составит:
NТО−1 = (2500×14) /125 - 5 -12 -18 - 35 = 210 шт.
Сезонное техническое обслуживание техники (СТО) проводят 2 раза в год.
Соответственно для К-701 количество СТО составит 6 шт., для трактора ДТ75М – 18 шт. и для трактора МТЗ-82 – 28 шт.
2. Трудоемкость ТО и ремонтов тракторов определяется на основе удель-
ной нормативной трудоемкости одного ремонта или технического обслуживания и их планового количества за год по формуле:
Т = N i ×Tудi |
(6) |
где Ni − количество ремонтов или ТО машин одной марки, шт.; Tудi − удель-
ная трудоемкость одного ремонта или ТО, чел.-ч.
Таблица 1 – Трудоемкость ТО и ремонта тракторов
Наименование |
Вид ремонта |
Кол-во ре- |
Трудоемкость, чел.-ч. |
||
машины, мар- |
|
|
|||
и ТО |
монтов и ТО |
на единицу |
всего |
||
ка, модель |
|||||
|
|
|
|
||
1. Трактор |
КР |
1 |
726 |
726 |
|
К-701 |
ТР |
2 |
185 |
370 |
|
|
СТО |
6 |
29,3 |
176 |
|
|
ТО-3 |
4 |
43,2 |
173 |
|
|
ТО-2 |
8 |
11,6 |
93 |
|
|
ТО-1 |
45 |
2,2 |
99 |
|
|
Итого: |
|
|
1637 |
31
2. Трактор |
КР |
3 |
369 |
1107 |
ДТ-75М |
ТР |
8 |
140 |
1120 |
|
СТО |
18 |
17,1 |
308 |
|
ТО-3 |
11 |
21,4 |
236 |
|
ТО-2 |
23 |
6,4 |
148 |
|
ТО-1 |
135 |
2,7 |
365 |
|
Итого: |
|
|
3284 |
3. Трактор |
КР |
5 |
311 |
1555 |
МТЗ-82 |
ТР |
12 |
85 |
1020 |
|
СТО |
28 |
3,5 |
98 |
|
ТО-3 |
18 |
19,8 |
357 |
|
ТО-2 |
35 |
6,9 |
242 |
|
ТО-1 |
210 |
2,7 |
567 |
|
Итого: |
|
|
3839 |
Общая годовая трудоемкость ремонтных работ для за- |
8760 |
|||
данного |
|
|
|
|
парка машин |
|
|
|
|
3. Согласно заданию, трудоемкость проведения КР относится и выполняется на специализированных ремонтных предприятиях. Она составляет 3388 чел.- ч. Кроме этого 50% трудоемкости проведения ТР тракторов относится и выполняется на станциях технического обслуживания тракторов (СТОТ). Она составляет 745 чел.-ч. Так же 20% ТО-1 проводятся непосредственно в полевых условиях. Трудоемкость его проведения составляет 206 чел.-ч. Соответственно годовая трудоемкость ремонтных работ выполняемых в центральной ремонтной мастерской хозяйства составит:
8760 – 3380 – 745 – 206 = 4429 чел.-ч.
6. По дисциплине «Топливо и смазочные материалы»
Провести расчёт тепловой характеристики топлива и потребление воздуха на
процесс сгорания.
Исходные данные: Содержание элементов в образце рабочего топлива: уг-
лерод – 86 %, водород – 13,5 %, сера – 0,2 %, кислород – 0,3 %
Требуется:
1.Определить теплоту сгорания топлива.
2.Определить теоретическое количество воздуха, необходимое для полного сгорания топлива.
3.Определить теплоту сгорания нормальной рабочей смеси топлива и воздуха.
Решение.
1. Определение теплоты сгорания топлива, его нормальной рабочей смеси. Теплота сгорания смеси рабочего топлива определяется по формуле для подсчёта низшей теплоты сгорания:
QH = QB – 25(9H + W)
Для расчёта низшей теплоты сгорания необходимо определить высшую теп-
32

лоту сгорания по следующей формуле:
QB = 339C + 1256H – 109(O–S)
QB = 339 × 86 + 1256 × 13,5 – 109 × (0,3 – 0,2) = 29154 + 16956 – 10,9 = 46099,1
кДж/кг
QH = 46099,1 – 25( 9 ×13,5 +0 ) = 43061,6 кДж/кг
2. Определение теоретического количества воздуха, необходимого для полного сгорания топлива.
Теоретическое количество воздуха, необходимое для полного сгорания топлива определяется по следующей формуле:
LТ.В. = (2,67С + 8Н + S – О) / 23,2
LТ.В. = (2,67 × 86 + 8 × 13,5 + 0,2 – 0,3) / 23,2 = (229,62+ 108 – 0,1)/23, 2=14,54
кг/кг 3. Определить теплоту сгорания нормальной рабочей смеси топлива и воз-
духа.
Теплоту сгорания нормальной газообразной рабочей смеси топлива и воздуха определяется по следующей формуле:
Qг.с. = QH/ 1+ α × LТ.В.
Для нормальной горючей смеси α=1
Qг.с. = 43061,6 / 1+1 × 14,54 = 43061,6/15,54= 2771,017 кДж/кг
а) по специализации «Эксплуатация сельскохозяйственной техники»
1. Теория и расчет трактора и автомобиля.
Требуется: Определить рабочую скорость движения Vр трактора.
Исходные данные: частота вращения коленчатого вала двигателя nдв = 2000 мин−1 , передаточное отношение трансмиссии на выбранной передаче iтр = 90, буксования на выбранной передаче δ = 7,5%, радиус ведущего колеса (звездочки) rк = 0,67.
Решение:
Для определения рабочей скорости движения трактора необходимо знать теоретическую скорость движения трактора:
Vт = 0,377rк nдв , км/ч
iтр
После необходимо определить значение КПД буксования:
ηδ = 1-δ
Определяем действительную рабочую скорость движения:
Vp=Vт·ηδ, км/ч
2. Проектирование машинно-тракторного парка и инженернотехнического обеспечения.
Организовать работы уборочно-транспортного комплекса на заготовке рассыпного сена на площади 200 га, при урожайности травы 120 ц/га . Хозяй-
33
ство располагает техникой: КПС-5Г, ГВР-6,0, ПК-1,6А, ПФ-0,5, МТЗ-82.2,
ХТЗ-150К.
Определить:
1.Технологическую схему заготовки сена с названиями скомплектованных агрегатов.
2.Производительность и количество агрегатов при соблюдении условия неразрывности технологического процесса уборки сена с поля за 4 дня.
3.Потребность в дизельном топливе при расходе агрегатом 0,8 кг на едини-
цу работы.
Решение:
1. Технологическая схема заготовки будет включать в себя следующие агрегаты:
– скашивание сена в валки с плющением стеблей: КПС-5Г (самоходная ко- силка-плющилка);
– сгребание трав: МТЗ-82.2+ГВР-6.0 (грабли-ворошилки-высушиватели);
– подбор валков с копнением и формированием копны цилиндрической формы: МТЗ-82.2+ПК-1,6А (подборщик-копнитель);
– скирдование копен МТЗ-82.2+ПФ-0,5 (погрузчик-стогометатель).
2. Производительность агрегатов для заготовки рассыпного сена:
Часовая производительность косилки-плющилки самоходной КПС-5Г:
Wч = 0,1× Вр × v p ×τ , га/ч
где B p - рабочая ширина захвата косилки, м; v p - рабочая скорость движе-
ния косилки, км/ч; Примем v p = 11 км/ч (из технологической скорости ска-
шивания трав); τ − коэффициент использования времени смены; Примем
τ = 0,85 .
B p = Bк × β , м
где Bк - конструктивная ширина захвата косилки, м; Bк = 5 м (справочные данные); β − коэффициент использования конструктивной ширины захвата;
β = 1,05 .
|
|
|
B p = 5 ×1,05 = 5,25 м. |
|
||||
|
Wч |
|
= 0,1× 5,25 ×11× 0,85 = 4,9 га/ч. |
|
||||
Зададим продолжительность времени смены на скашивании Тсм |
= 7 ч. |
|||||||
Тогда, сменная производительность косилки определится: |
|
|||||||
|
Wсм |
= Wч ×Тсм |
= 4,9 × 7 = 34,3 га/см. |
|
||||
Потребное количество косилок: |
|
|
|
|
||||
|
|
|
n = |
|
F |
|
, шт |
|
|
|
|
|
|
|
|
||
|
|
|
|
|
|
|
||
|
|
|
Wсм × |
Д р |
|
|||
где F − площадь поля, га; |
|
F = 200га (по условию задачи); Д р |
- количество |
|||||
рабочих дней; Д р = 4 дня |
|
|
|
|
|
|
|
|
200 |
|
= 1,45 » 2 Принимаем 2 косилки. |
|
|||||
n = |
|
|
||||||
34,43 × 4 |
|
34

Часовая производительность при сгребании трав агрегатом МТЗ-82.2+ГВР- 6.0:
Конструктивная ширина захвата ГВР-6.0: Bк = 6 м; β =1,15 ; Соответственно, рабочая ширина захвата агрегата определится:
B p = 6 ×1,15 = 6,9 м.
Рабочая скорость при скашивании: v p = 10 км/ч.
Wч = 0,1× 6,9 ×11× 0,85 = 6,45 га/ч.
Сменная производительность МТЗ-82.2+ГВР-6.0:
Wсм = 6,45 × 7 = 45,15 га/см.
Потребное количество агрегатов для сгребания:
n = |
200 |
= 1,10 » 2 . Принимаем 2 агрегата МТЗ-82.2+ГВР-6.0. |
45,15 × 4 |
Часовая производительность при подборе валков с копнением и образованием копен агрегатом МТЗ-82.2+ПК-1,6:
Конструктивная ширина захвата ПК-1,6:
Bê = 1,6 м;
β = 1,0 ;
Соответственно, рабочая ширина захвата агрегата определится:
B p |
= 1,6 ×1,0 = 1,6 м. |
|||
Рабочая скорость при скашивании: |
||||
v p |
= 8 км/ч. |
|
|
|
|
|
|
|
Wч = 0,1×1,6 ×11× 0,85 = 1,5 га/ч. |
Сменная производительность МТЗ-82.2+ПК-1,6: |
||||
|
|
|
|
Wсм = 1,5 × 7 = 10,5 га/см. |
Потребное количество агрегатов для копнения: |
||||
|
n = |
200 |
|
= 4,76 » 5 . Принимаем 5 агрегатов МТЗ-82.2+ПК-1,6. |
|
|
4 |
||
|
10,5 × |
|
Часовая производительность погрузчика МТЗ-82.2+ПФ-0,5 составляет 30 т/ч (справочные данные).
Сменная производительность погрузчика составит:
Wсм = 30 × 7 = 210 т/см.
Определим количество погрузчиков при урожайности сена q = 120 ц/га = 12 т/га.
Объем работ в тоннах:
Q = q × F , т
Q = 12 × 200 = 2400 т;
Тогда, потребное количество агрегатов для погрузки составит: n = = 2,85 » 3 . Примем 3 агрегата МТЗ-82.2+ПФ-0,5
Запишем условие поточности агрегатов для заготовки сена:
∑WсмКПС−5 Г ³ ∑WсмГВР−6,0 ³ ∑WсмПК−1,6 ³ ∑WсмПФ−0,5
2 × 34,43 ³ 2 × 45,15 ³ 5 ×10,5 × (12т) ³ 3 × 210(630т)
35

68,86 ³ 90,3 ³ 52,5(630т) ³ 630т
Условие поточности выполняется.
3. Потребность в дизельном топливе определится:
|
Q = q × F |
где Q - потребность |
в дизельном топливе на весь объем работы, кг; |
q −удельный расход |
топлива, кг/га; q = 0,8 кг/га (по условию задачи); |
F − объем выполненной работы, га. F = 200га. При скашивании КПС-5Г:
Q = 8 × 200 = 1600 кг;
При ворошении МТЗ-82.2+ГВР-6.0:
Q = 8 × 200 = 1600 кг;
При копнении: МТЗ-82.2.+ПК-1,6:
Q = 8 × 200 = 1600 кг;
При скирдовании: МТЗ-82.2+ПФ-0,5:
Q = 8 × 200 = 1600 кг.
Общий: Qобщ = 1600 +1600 +1600 +1600 = 6400 кг.
3. Ремонт машин и оборудования.
Определить рациональный способ восстановления детали с выбором оборудования, режимов и материалов, разработать маршрутную технологию
восстановления детали.
Исходные данные: Эскиз детали с указанием дефекта (Таблица 1).
Материал Сталь 4ОХН ГОСТ 4543-71, масса 1,37 кг, твердость 174...217 НВ.
Таблица 1 – Исходные данные для решения задачи
Контролируемый
Размеры, мм
дефект
Эскиз детали
|
Диаметр |
||
№ Наименование |
|
|
Длина |
|
По чертежу |
Допустимый |
|
Износ поверх- |
|
|
|
3 |
ности под ша- |
25+0,015 |
24,96 |
30 |
|
рикоподшип- |
+0,002 |
|
|
|
ник |
|
|
|
Ось промежуточной шестерни (701601355) шасси трактора Т-4А
Требуется:
1.Дать конструкторско-технологическую характеристику детали
2.Выбрать возможные способы устранения дефекта.
36
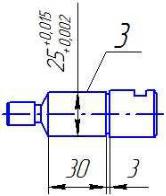
3.Определить рациональный способ устранения дефекта (на основании критерия применимости и справочных данных).
4.Подобрать оборудование и режимы для рационального способа восстановления (на основании справочных данных).
5.Подобрать материалы для рационального способа восстановления.
6.Разработать маршрутную технологию восстановления детали. Подобрать необходимое оборудование.
7.Сделать вывод.
Решение:
1. Конструкторско-технологическая характеристика детали
Материал – Сталь 40ХН Твердость 174…217 НВ
Рис. 1. Эскиз оси промежуточной шестерни шасси трактора Т-4А (70-1601355)
В нашем случае дефектом является износ наружной, посадочной поверхности под шарикоподшипник. При разработке технологического процесса его ремонта необходимо учитывать оснащение данного предприятия и его технологические возможности. Химический состав и механические свойства данной марки стали приведены в таблицах 4.2 и 4.3 соответственно.
Таблица 1. Химический состав стали 4ОХН ГОСТ 4543-71
С,% |
|
Сr, % |
Ni, % |
|
Si, % |
|
Mn, % |
Р,% |
|
S,% |
Сu, % |
||||
|
|
|
|
|
|
|
|
||||||||
|
не более |
|
|
||||||||||||
|
|
|
|
|
|
|
|
|
|
|
|
|
|
||
|
|
|
|
|
|
|
|
|
|
|
|
|
|
|
|
0,36... 0,44 |
0,45... 0,75 |
1,0... |
0,17... |
|
0,5... |
|
0,035 |
0,035 |
0,3 |
||||||
1,40 |
0,37 |
|
0,8 |
|
|||||||||||
|
|
|
|
|
|
|
|
|
|
|
|
||||
|
|
|
|
|
|
|
|
|
|
|
|
|
|
||
Таблица 2. Механические свойства стали 40ХН |
|
|
|
|
|
||||||||||
|
|
σ в , |
|
σ и , |
|
КСU, |
|
Ψ, % |
|
НВ |
|
|
|||
|
|
MПа |
|
МПа |
|
Дж\см2 |
|
|
|
|
|||||
|
|
|
|
|
|
|
|
|
|
|
|
|
|||
|
|
590 |
|
345 |
|
49 |
|
|
38 |
|
174...217 |
|
|||
|
|
|
|
|
|
|
|
|
|
|
|
|
|
|
|
2, 3. Анализ и выбор способа восстановления
Учитывая конструкторско-технологические особенности данной дета-
37

ли, её габаритные размеры, форму, материал, твердость, шероховатость, точность изготовления, условия работы, и т.п., можно сделать вывод о том, что изношенную поверхность под шарикоподшипник оси промежуточной шестерни можно восстановить следующими способами: осталивание, электроконтактная приварка стальной ленты, нанесение полимерных материалов. Окончательный выбор рационального способа восстановления производится по критерию применимости, в результате сравнения возможностей выше перечисленных способов.
Из всех вышеперечисленных способов восстановления поверхности под шарикоподшипник оси промежуточной шестерни в данных условиях, т.е. для центральной ремонтной мастерской хозяйства, наиболее рациональным будет выбрать способ электроконтактной приварки стальной ленты. Данный способ является технологически простым, доступным и относительно дешевым. Для этого способа характерны высокая производительность, минимальные потери присадочного материала и припуск на последующую механическую обработку за счет возможности регулирования толщины приваренного слоя.
4, 5, 6. Разработка маршрутной технологии
Схема технологического процесса восстановления оси промежуточной шестерни на рис. 2.
Очистка
Дефектация
Шлифование
Электроконтактная
наплавка
Токарная
Шлифование
Контроль
Рис. 2. Схема технологического процесса восстановления оси промежуточной шестерни
При поступлении детали в ремонт её необходимо подвергнуть очистке,
38
которая производится в моечной машине ОМ-3600 ГОСНИТИ с применением моющего средства «Лобомид-101» (концентрация 10 г/л, температура 7585° С). Деталь загружают в машину и очищают поверхность до полного удаления масла, грязи и продуктов износа.
Далее ось поступает на дефектацию, где её визуально осматривают, проверяют поверхность на наличие трещин, замеряют поверхность, подлежащую восстановлению. При наличии кольцевых трещин ось выбраковывается.
Перед приваркой ленты ось необходимо подвергнуть шлифованию на круглошлифовальном станке для удаления следов износа и придания правильной геометрической формы.
Затем ось устанавливают на установку 011-1-02Н для приварки ленты из стали 65Г на поверхность под шарикоподшипник.
После приварки ленты ось обтачивают на токарно-винторезном станке 1К62 для удаления наплывов ленты на установленном участке ленты.
Затем ось шлифуют на круглошлифовальном станке до диаметра 25++0,0150,002
мм, на длине 30 мм.
Заключительной операцией является - контроль. Контролируют диаметр 25++00,,015002 скобами 8111-02496Д, 8111-02498Д и микрометром МК25-1.
005 Моечная (А)
Содержание (О): загрузить деталь в моечную машину, промыть до удаления следов масла и грязи.
Оборудование (Б): машина моечная ОМ-3600 ГОСНИТИ.
Материалы (М): моющее средство «Лабомид-101» концентрация 10 г\л, ветошь ГОСТ 5354-79.
Выбор режимов нормирования работ. t = 75…85°C
Тн = Тшх+Тпз\n, мин;
Тн - технологическая норма времени на операцию, мин; Тшт - штучно-калькуляционное время, мин;
Тпз - время на подготовительно-заключительные работы, мин; n - количество деталей в партии, шт (n = 1);
Тшт=10...12 мин; Тпз = 4 мин.
Тн = (10... 12) + 4\1 = 14...16 мин; принимаем Тн = 15 мин.
010 Дефектация (А)
Оборудование (Б): стол дефектовщика ОРГ-1468-01-090А Содержание (0): визуально осмотреть ось, при наличии трещин ось выбраковывается; провести замер поверхности под шарикоподшипник. Оснастка (Т): микрометр МК 25-1 ГОСТ 6507-88.
Нормирование работ:
Тшт = 8 мин; Тпз = 2 мин; табл. 2.35.
Тн = 8 + 2/1 = 10 мин.
39
015 Шлифование (А):
Оборудование (Б): кругло-шлифовальный станок 1Б151.
Материал (М): охлаждающая жидкость: эмульсия "Аминил Б", концентрация 10 г/л.
Содержание (О): установить ось в центрах станка, шлифовать поверхность под шарикоподшипники до выведения следов износа и придания правильной геометрической формы.
Оснастка (Т): круг шлифовальный ПП 900x40x305; 14А40ПСМ27К1А 35м\с, индикатор ИЧ 10 кл1, микрометр МК50-1 ГОСТ 6507-88. Выбор режимов и нормирование работ:
-окружная скорость шлифовального круга: 35 м\с;
-число оборотов: 150 об\мин;
-подача поперечная: 0,01...0,05 мм\об;
-расход охлаждающей жидкости: 0,3 л\мин. стр151[9].
Тшт = 5,8 мин; Тпз = 5 мин;
Тн = 5,8 + 5 = 10,8 мин.
020 Электро-контактная наплавка (А): Оборудование (Б): установка 011-1-02Н
Материал (М): металлическая лента, сталь 65Г ГОСТ 2283-80. Содержание (О): наплавить ленту на поверхность под шарикоподшип-
ник до диаметра 25,5 мм на длине 30 мм.
Оснастка (Т): штангенциркуль ШЦ-1-125-0,1 ГОСТ 166-88. Выбор режимов и нормирование работ:
-частота вращения детали: 5об\мин;
-подача сварочных клещей: 3 мм\об;
-усилие сжатия электродов: 150 кг\с;
-амплитуда импульса сварочного тока: 10,8 мс;
-количество сварочных точек на 1см сварочного шва: 6...7.
025 Токарная (А).
Оборудование (Б): токарно-винторезный станок 1К62.
Материал (М): охлаждающая жидкость, эмульсия "Аминил Б", концентрация 10 г/л.
Содержание (О): установить ось в центрах станка, обточить наплывы в месте приварки ленты до диаметра 25,1 мм на длине 30 мм, обточить фаску
1x45°. Оснастка (Т): резец 2103-0007 Т-15КВ МН 577-64, резец 2660-0005
Т15К6 МН 623-64, микрометр МК25-1 ГОСТ 6507-88, штангенциркуль ШЦ- 1-125- 0,1 ГОСТ 166-88.
Выбор режимов и нормирование работ:
-число оборотов: 630 об\мин;
-подача: 0,3 мм\об;
-расход охлаждающей жидкости: 0,5 л\мин.
40