
Tehnologiya_konstruktsionnyh_materialov
.pdf
Ультразвуковая сварка Ультразвуковая сварка - сварка давлением, осуществляемая при воз-
действии ультразвуковых колебаний. Сущность процесса ультразвуковой сварки (УЗС) состоит в приложении высокочастотных колебаний (16…20
КГц) к свариваемым заготовкам. В заготовках возникают касательные на-
пряжения, вызывающие пластическую деформацию материала свариваемых поверхностей. В месте соединения развивается повышенная температура (0,4…0,6Тплавления), зависящая от свойств свариваемых материалов. Эта температура способствует возникновению пластического состояния сваривае-
мых материалов и их соединению. В месте сварки образуются совместные кристаллы, обеспечивающие прочность сварного соединения. Одновременно,
под действием ультразвука разрушаются окисные пленки на поверхностях заготовок, что облегчает получение соединения.
Типовая схема УЗС (рис. 5.19, а) состоит из электромеханического Рис. 5.19 Ультразвуковая
сварка:
а - типовая схема; б – при-
меры сварки;
1 – неподвижная опора; 2 –
регулируемая опора; 3 – кор-
пус установки; 4 - акустиче-
ская развязка; 5 – магистраль охлаждения; 6 – акустиче-
ский узел; 7 – кожух; 8 -
электромеханический преоб-
разователь; 9 – ультразвуковой генератор; 10 - концентратор колебательной скорости; 11 - сварочный наконечник; 12, 13 – свариваемые заготовки; 14 -
кривая упругих колебаний.
преобразователя 8, волноводного звена - трансформатора или иначе концен-
тратора колебательной скорости 10, акустической развязки системы от кор-
171
пуса машины 4, излучателя ультразвука - сварочного наконечника 11 и опор
1, 2, на которых располагаются свариваемые заготовки 12 и 13. Электромеха-
нические преобразователи выполняют из магнитострикционных или электро-
стрикционных материалов (никель, пермендюр, титанит бария). Под воздей-
ствием переменного электромагнитного поля в преобразователе возникают механические напряжения, которые вызывают упругие деформации материа-
ла. Таким образом, преобразователь является источником механических ко-
лебаний. Волноводное звено служит для передачи энергии к сварочному на-
конечнику. Это звено должно обеспечить необходимое увеличение амплиту-
ды колебаний сварочного наконечника по сравнению с амплитудой исходных волн преобразователя.
При вводе механических колебаний в свариваемые металлы заготовки начинают вибрировать с ультразвуковой частотой. Форма колебаний опреде-
ляется геометрическими размерами изделия. В наиболее простом и распро-
страненном случае (сварка листа прямоугольной формы) в свариваемом из-
делии устанавливается стоячая волна с характерным чередованием узлов и пучностей плоской волны изгибных колебаний. Уровень напряжений, возни-
кающих в пучностях, определяется мощностью энергии, вводимой в зону сварки.
УЗС позволяет соединять металлы без снятия поверхностных пленок и расплавления (особенно: чистый алюминий, медь, серебро). УЗС сваривают:
металлическую фольгу со стеклом и керамикой (металл - стекло; отношение толщин 1/1 000 и больше); большинство известных термопластичных поли-
меров. Для ряда полимеров УЗС является единственно возможным надежным способом соединения. Для УЗС характерны: малая энергоемкость; возмож-
ность питания нескольких сварочных головок от одного генератора и воз-
можность выноса их на значительное расстояние; простота автоматизации процесса работы колебательной системы; гигиеничность процесса.
172

Технологическое оборудование для ультразвуковой сварки состоит из следующих узлов: источника питания, аппаратуры управления сварочным циклом, механической колебательной системы и привода давления.
УЗС применяют в приборостроении, радиоэлектронике, авиационной промышленности.
Сварка трением Сварка трением – сварка с применением давления, при которой нагрев
осуществляется трением, вызванным относительным перемещением свари-
ваемых частей или инструмента.
Простейшая и наиболее распространенная схема сварки приведена на рис. 5.20, а. Две детали, подлежащие сварке, устанавливают соосно в зажи-
мах машины; одна из них - неподвижна, а другая приводится во вращение вокруг их общей оси. На сопряженных торцовых поверхностях деталей, при-
жатых одна к другой осевым усилием Р, воз-
никают Рис. 5.20. Сварка трени-
ем:
а - схема; б – примеры сварки; в – участок свар-
ки трением задних мос-
тов; Р – осевое усилие.
силы трения. Работа, за-
трачиваемая при относи-
тельном вращении сва-
риваемых заготовок на преодоление этих сил трения, преобразуется в тепло,
которое выделяется на поверхностях трения и нагревает прилегающие к ним тонкие слои металла до температур, необходимых для образования сварного соединения (при сварке, черных металлов температуры в стыке достигают
173
1000…1 300° С). Таким образом, в стыке, действует внутренний источник тепловой энергии, вызывающий быстрый локальный нагрев небольших объ-
емов металла. В процессе трения пластичный металл стыка выдавливается в радиальном направлении под воздействием осевого усилия и тангенциальных сил, возникающих в стыке при вращении одной детали относительно другой.
Выдавленный металл «грат» - имеет характерную для сварки трением форму сдвоенного правильного кольца, расположенного по обе стороны плоскости стыка. При выдавливании пластичного металла, хрупкие окисные пленки,
покрывавшие торцовые поверхности соединяемых заготовок до начала свар-
ки, разрушаются, а их обломки, а также продукты сгорания адсорбированных жировых пленок и другие инородные включения вместе с металлом удаляют-
ся из стыка в грат. Нагрев прекращается путем быстрого (практически мгно-
венного) прекращения относительного вращения. При этом в контакт оказы-
ваются введенными очищенные торцовые поверхности соединяемых деталей,
металл которых доведен до состояния повышенной пластичности. Для полу-
чения прочного соединения достаточно такой, подготовленный к сварке ме-
талл, подвергнуть сильному сжатию - проковать. Это достигается с помощью продолжающего еще некоторое время действовать осевого усилия. Таким образом, прочность образующегося сварного соединения непосредственно связана с величиной пластического деформирования торцов свариваемых де-
талей и с режимом проковки.
Сварка трением широко применяется при изготовлении: в автомобиле-
строении - деталей рулевого управления, карданных валов легковых и грузо-
вых автомобилей, полуосей, задних мостов автомобилей (рис. 5.20, в), клапа-
нов двигателей внутреннего сгорания, цилиндров гидравлических систем и др.; в тракторостроении - деталей рулевого управления, планетарных пере-
дач, валов отбора мощности, катков, траков, роторов турбо нагнетателей ди-
зельного двигателя и др.; в электропромышленности - деталей высоковольт-
ной аппаратуры, выводов бумаго-масляных конденсаторов, кислотных акку-
муляторов и анодов игнитронов, поршней пневматических цилиндров сва-
174
рочных машин и др.; в инструментальном производстве - при массовом изго-
товлении концевого режущего инструмента (фрезы, сверла, метчики).
5.6.Электромеханические виды сварки
Кэлектромеханическим видам сварки относятся все способы контакт-
ной сварки.
Контактная сварка Контактная сварка – сварка с применением давления, при которой
используется тепло, выделяющееся в контакте свариваемых частей при про-
хождении электрического тока. Для осуществления контактной сварки крат-
ковременно нагревают место соединения электрическим током с последую-
щей осадкой разогретых заготовок. В процессе осадки пластически деформи-
руются внешние слои заготовок, и формируется сварное соединение. Коли-
чество выделяемой теплоты определяется законом Джоуля – Ленца: Q=I2R∑t,
где: Q –количество теплоты, выделяемое при прохождении электрического тока по сварочной цепи, в Дж,; I- сварочный ток; R∑- полное омическое со-
противление сварочной цепи; t – время прохождения тока по сварочной цепи.
Полное сопротивление сварочной цепи складывается из: суммарного сопро-
тивления тел заготовок и электрической подводки (Rзаг + Rэл) и сопротивле-
ния сварочного стыка (Rс). Наличие выступов и впадин микронеровностей и различного вида пленок на поверхностях сварочного стыка определяет по-
вышенное электрическое сопротивление. При этом: (Rзаг + Rэл)<< Rс. Поэто-
му, при прохождении по сварочной цепи электрического тока максимальное количество теплоты выделяется в месте сварочного контакта заготовок. В ре-
зультате высокой плотности тока в зоне контакта металл разогревается до термопластического состояния или до оплавления. При непрерывном сдав-
ливании нагретых заготовок металл в зоне контакта пластически деформиру-
ется, разрушаются и удаляются к периферии стыка оксидные пленки, проис-
ходи сближение поверхностей до расстояний меньших межатомных – обра-
зуется сварное соединение.
175
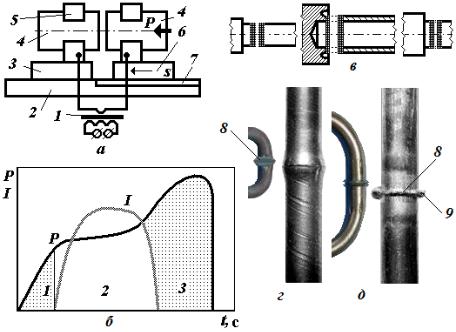
Различают контактную сварку: стыковую (СКС), точечную (ТКС),
рельефную (РКС) и шовную (ШКС).
Стыковая контактная сварка – контактная сварка, при которой со-
единение свариваемых частей происходит по поверхностям стыкуемых тор-
цов. Схема установки для СКС показана на рис. 5.21, а. На станине 2 уста-
новлены две плиты: неподвижная 3 и подвижная 6, перемещаемая по направ-
ляющим 7. Заготовки 4 устанавливаются в зажимах 5. Сварочный ток пода-
ется от трансформатора 1. При перемещении плиты 7, заготовки сжимаются проковочным усилием Р. СКС соединяют круглые и не круглые стержни
(одинакового или различных диаметров), круглые или некруглые стержни к плоской заготовке, плоские или кольцевые заготовки. Проковка заготовок сопровождается уменьшением их линейных размеров.
Рис. 5.21 Контакт-
ная стыковая свар-
ка:
а – схема; б – цик-
лограмма сварки; в
– торцы заготовок;
г - примеры сварки сопротивлением; д
– примеры сварки оплавлением; 1 -
трансформатор; 2 –
станина; 3 – не-
подвижная плита; 4 – свариваемые заготовки; 5 - зажимы; 6 – подвижная плита; 7 – направляющие; 8 – сварной шов; 9 – грат; Р – сила сжатия I – ток; t
–время.
Взависимости от степени разогрева торцов заготовок различают: свар-
ку сопротивлением и оплавлением. СКС сопротивлением – стыковая кон-
тактная сварка, при которой нагрев металла осуществляется без оплавления
176
стыкуемых торцов. Для правильного формирования сварного шва необходи-
мо протекание процесса сварки в определенной последовательности.
Совместное графическое изображение тока и давления, называют цик-
лограммой сварки (рис. 5.21, б). Процесс сварки идет в три этапа: предвари-
тельный прижим заготовок; разогрев торцов; проковка (прижим заготовок и выдержка). Перед сваркой заготовки необходимо очистить от оксидных пле-
нок, их торцы должны по форме соответствовать друг другу (рис. 5.21, в).
Торцы должны иметь простой периметр (круг, квадрат, прямоугольник с ма-
лым соотношением сторон) и быть плотно прижаты друг другу предвари-
тельной механической обработкой. Соединения, сваренные стыковой сваркой сопротивлением, характеризуются плавным очертанием (рис. 5.21, г). Свар-
кой сопротивлением соединяют заготовки из низкоуглеродистых, низколеги-
рованных конструкционных сталей; алюминиевых сплавов; сечением до 200 мм2.
СКС оплавлением – стыковая контактная сварка, при которой нагрев металла сопровождается оплавлением стыкуемых торцов. СКС оплавлением имеет две разновидности: сварка с непрерывным и прерывистым оплавлени-
ем. При непрерывном оплавлении заготовки устанавливают в электродах машины с набольшим зазором по торцам. После подключения источника то-
ка, заготовки сближают. Вначале соприкосновение заготовок происходит по небольшим площадкам, через которые протекает ток высокой плотности.
Между торцами заготовок появляются перемычки из жидкого металла. Од-
новременно возрастает сварочный ток и развивается температура до 8 000оС.
Под воздействием высокой температуры перемычки испаряются. Под дейст-
вием магнитного поля, часть металла в виде искр (капель) и паров выбрасы-
вается из стыка. Вместе с металлом из стыка выбрасываются и загрязнения
(оксидные пленки), которые находились на торцах. По мере сближения заго-
товок число контактов (оплавляемых выступов) увеличивается. После равно-
мерного оплавления всей поверхности свариваемого стыка, отключают сва-
рочный ток и осаживают заготовки. При этом жидкий металл и часть пласти-
177
чески деформированного металла из стыка, выдавливается наружу, образуя грат 9 (рис. 5.21, д). При прерывистом оплавлении, заготовки под током при-
водят в кратковременное соприкосновение и вновь разводят на небольшое расстояние. При смыкании заготовок происходит прерывистое оплавление торцов, заготовки укорачиваются на заданную величину и одновременно равномерно разогреваются по сечению. Число смыканий может быть от двух до нескольких десятков, в зависимости от размеров сечения заготовок. После равномерного оплавления всей поверхности свариваемого стыка, отключают сварочный ток и осаживают заготовки. В процессе сварки оплавлением вы-
равниваются неровности стыка, удаляются из стыка все оксиды и загрязне-
ния. Поэтому не требуется особой предварительной подготовки торцов.
Сварка позволяет соединять заготовки из разнородных металлов (быстроре-
жущая и углеродистая стали; медь и алюминий …) сечением сложной фор-
мы.
Контактная стыковая сварка широко применяется: для получения из проката длинных изделий или заготовок, поступающих в дальнейшую пере-
работку (сварка трубчатых змеевиков поверхностей нагрева котлов; сварка на трассе стыков труб газопроводов; сварка концов рулонов стальной ленты для пропуска через линии непрерывного волочения; сварка железнодорож-
ных рельсов в длинные плети, улучшающие условия прохождения по ним подвижного состава); для изготовления деталей замкнутой формы (звеньев цепей; ободов автомобильных колес; колец жесткости для реактивных двига-
телей; зубчатых венцов; оконных переплетов из легких сплавов); для эконо-
мического образования сложных деталей из простых катаных, кованых,
штампованных или механически обработанных заготовок, часто прошедших перед сваркой окончательную термическую обработку (кожух карданного вала автомобиля, можно сваривать из трубы и двух поковок; тягу самолета,
сваривают из трубы и двух штампованных проушин); для экономии легиро-
ванных сталей (рабочая часть сверла из быстрорежущей стали сваривается с хвостовиком из низкоуглеродистой стали; заготовку клапана двигателя внут-
178
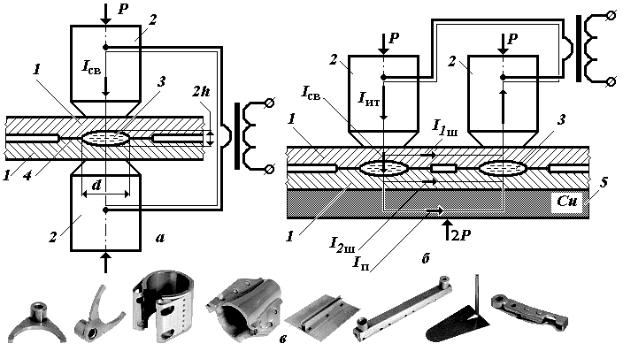
реннего сгорания, получают сваркой стержня из жаропрочной стали, обра-
зующего после высадки головку клапана, и хвостовика из конструкционной стали); для уменьшения отходов (сварка прутков арматуры железобетона в бесконечную плеть с отрезкой от нее стержней заданной длины; сварка ко-
ротких угольников, швеллеров).
Точечная контактная сварка (ТКС) – контактная сварка, при которой сварное соединение получается между торцами электродов, передающих усилие сжатия.
Перед началом сварки контактные поверхности зачищают и обезжиривают. Заготовки 1 устанавливают между нижним и верхним электродами 2 сварочной машины (рис. 5.22, а). Далее заготовки сжимают и подают ток.
Рис. 5.22. Точечная контактная сварка:
а – двухсторонняя; б – односторонняя; в – образцы сварки;
1 – свариваемые заготовки; 2 – электроды; 3 - жидкая точка; 4 – уплот-
няющий поясок; 5 - подкладка; Iит – ток источника тока; Iсв – сварочный ток;
I1ш – ток шунтирования в верхней заготовке, I2ш – ток шунтирования между сварными точками; Iп – ток шунтирования в подкладке; h – величина про-
плавления; d – диаметр жидкой точки.
179
Прогрев осуществляют до появления жидкой точки 3 между контакт-
ными поверхностями. После этого производят проковку. Для соединения за-
готовок одновременно в двух точках применяют одностороннюю сварку
(рис. 5.22, б). Для этого, заготовки устанавливают на медную плиту - под-
кладку 5 и прижимают электродами, расположенными с одной стороны заго-
товок. При односторонней сварке необходимо учитывать шунтирование тока:
в верхней заготовке (I1ш), между сварными точками (I2ш) и в медной пластине (Icu). 2Iсв=I1ш-I2ш-ICu; где: Iит –ток источника тока; Iсв- сварочный ток, необходимый для получения одной сварной точки.
ТКС всегда начинается с предварительного сжатия деталей для обеспе-
чения хорошего контакта. Если при включении тока усилие Р0 , развиваемое электродами недостаточно, то контактные сопротивления велики и на них почти мгновенно выделяется очень много тепла: металл в контактах плавится и быстро выбрасывается в виде искр; происходит так называемый начальный выплеск. При малом усилии, возможен, прожег деталей, и обгорание элек-
тродов. Нагрев при точечной сварке характеризуется малой продолжительно-
стью (от тысячных долей секунды до нескольких секунд) и значительной не-
равномерностью. Наиболее интенсивно нагревается центральный столбик, в
пределах которого плотность тока наибольшая. Окружающий металл нагре-
вается протекающим в нем током малой плотности и за счёт теплопередачи
(скорость нагрева значительно меньше). В начале нагрева ток имеет наи-
большую плотность в области, прилегающей к контакту между свариваемы-
ми деталями, а в дальнейшем интенсивное тепловыделение поддерживается здесь из-за роста удельного сопротивления при нагреве. Поэтому наиболее быстро нагревается центральная зона точки – её чечевицеобразное ядро 3.
Образованию ядра такой формы способствует интенсивный отвод тепла в охлаждаемые электроды. При нагреве до некоторой критической температу-
ры в контакте между деталями под действием силы Р начинают образовы-
ваться общие зёрна – начинается сварка без расплавления. Дальнейший на-
грев ведёт к расплавлению ядра, образующего после кристаллизации прочное
180