
Tehnologiya_konstruktsionnyh_materialov
.pdf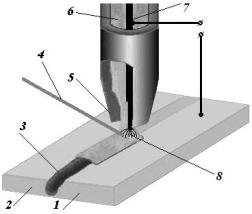
нейных швов только в полуавтоматическом режиме; выполнение сварки главным образом в нижнем положении.
ДСФ выполняют неподвижными подвесными сварочными головками;
передвижными сварочными автоматами (сварочными тракторами) и шланго-
выми сварочными полуавтоматами. Основные элементы сварочной машины показаны на рис. 5.8, б. Сварочная проволока 10, намотанная в кассету11, по-
дается роликовым механизмом в зону сварки. Дуга зажигается между заго-
товкой и сварочной проволокой за счет подачи высокочастотного импульса тока. Источник питания обеспечивает постоянное напряжение сварки и вы-
сокочастотное импульсное напряжение зажигания дуги.
Дуговая сварка в защитном газе – дуговая сварка, при которой дуга и расплавляемый металл, а в некоторых случаях и остывающий шов, находятся в защитном газе, подаваемом в зону сварки с помощью специальных уст-
ройств. В качестве защитных газов используют инертные газы (аргон, гелий)
и активные газы (углекислый газ, азот, водород …), иногда применяют смесь двух и более газов (Ar + O2; Ar + H2; Ar + N2; Ar + CO2). Чаще всего приме-
няют: аргон, углекислый газ; смесь аргона или углекислого газа с кислоро-
дом. Дуговая сварка в защитном газе может выполняться в любом пространственном по-
ложении. Схема дуговой сварки в защитных газах приведена на рис. 5.9. Прямая дуга 8 го-
рит между электродом (электродной проволо-
кой) 7
Рис. 5.9. Схема дуговой сварки в защитных газах:
1, 2 – заготовки; 3 – сварной шов; 4 – присадочный пруток;
5 – сопло; 6 – защитный газ; 7 - электродная проволока; 8 - дуга.
и заготовками 1, 2.Питание дуги осуществляется источником сварочного то-
ка через токопроводящий мундштук. Защитный газ 6 подается в зону сварки по специальному шлангу через кольцевой канал сопла 5. Сварку производят
151
плавящимся (сварочной проволокой) или неплавящимся электродом. В по-
следнем случае в зону сварки необходимо подавать присадочный пруток 4.
При использовании плавящегося электрода, сварочная проволока, на-
мотанная на кассету, подается в зону сварки роликовым механизмом. Прово-
лока при этом методе играет двойную роль – она является и токопроводящим электродом, и служит присадочным материалом. Использование механиче-
ской подачи присадочной проволоки позволяет создавать сварочные полуав-
томаты (перемещение головки производится вручную), или сварочные авто-
маты (снабжены механизмом перемещений сварочной головки).
Аргонодуговую сварку применяют для соединения: цветных (алюми-
ний, медь, магний), тугоплавких (титан, ниобий, цирконий) металлов и их сплавов; легированных и высоколегированных сплавов.
Сварку неплавящимся электродом применяют при соединении загото-
вок толщиной от 0,8 до 6 мм. При толщине заготовок до 3 мм возможна свар-
ка без применения присадочного материала (с расплавлением только мате-
риала заготовок). При необходимости получение выпуклого шва или толщи-
не заготовок более трех мм применение присадочного прутка (проволоки)
обязательно.
Для сварки листовых заготовок толщиной 0,2…1,5 мм применяют ав-
томатическую сварку в импульсном режиме. Между электродом и заготов-
ками постоянно горит маломощная (дежурная) дуга, которая обеспечивает ионизацию сварочного промежутка. На дежурную дугу накладывают мощ-
ные импульсы дуги заданной частоты и длительности. Импульсный режим позволяет точно дозировать тепловложения и снизить минимальную толщи-
ну свариваемого металла.
Сварку неплавящимся электродом ведут на постоянном токе прямой полярности. Дуга горит устойчиво при напряжении 10…15 В и минимальном токе 10 А, что обеспечивает возможность сваривать заготовки от 0,8 мм. При применении обратной полярности возрастает напряжение дуги и уменьшает-
ся устойчивость ее горения. Однако дуга обратной полярности позволяет
152
очищать свариваемые поверхности заготовок от окисных и оксидных пленок
(сварка алюминиевых и магниевых сплавов). Это явление получило название
«катодное распыление» и может быть объяснено тем, что поверхности заго-
товок бомбардируются тяжелыми положительными ионами аргона, которые механически разрушают пленки. Совместить устойчивость дуги (прямая по-
лярность) с катодным распылением (обратная полярность) позволяет приме-
нение переменного тока. Для питания дуги переменным током используют специальные источники, включающие в себя дополнительный стабилизатор горения дуги. Стабилизатор подает дополнительное напряжение в сварочную цепь в полупериод обратной полярности. Иногда применяют преобразовате-
ли, изменяющие полупериоды переменного тока по фазе и амплитуде.
Сварку в среде углекислого газа применяют при изготовлении различ-
ных конструкций из углеродистых и низколегированных сталей. Сварку вы-
полняют только плавящимся электродом на повышенных плотностях посто-
янного тока обратной полярности, горелками с механической подачей сва-
рочной проволоки.
Под действием высокой температуры дуги углекислый газ диссоцииру-
ет на окись углерода им свободный кислород: 2СО2 = 2СО+О2. Выделяю-
щийся кислород окисляет: железо (образуется растворимая в жидком металле закись железа) и легирующие элементы, входящие состав свариваемой стали.
При взаимодействии с углеродом, закись железа образует нерастворимую в металле окись углерода. В результате, металл сварного шва получается по-
ристым с низкими механическими свойствами. Для предотвращения порис-
тости сварного шва применяют электродную проволоку с повышенным со-
держанием раскисляющих примесей (марганец и кремний) марок Св–08ГС;
Св–10Г2С и тому подобное.
Электрошлаковая сварка Электрошлаковая сварка (ЭШС) - сварка плавлением, при которой для
нагрева используется тепло, выделяющееся при прохождении электрического тока через расплавленный шлак. При ЭШС основным источником тепла слу-
153
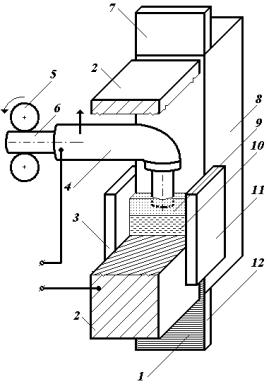
жит расплавленный шлак, разогретый сварочным током, проходящим от электрода к заготовкам. Дуга при сварке отсутствует.
Схема установки для ЭШС приведена на рис. 5.10. В начале процесса Рис. 5.10. Схема установки для электро-
шлаковой сварки:
1 – сварной шов; 2, 8– заготовки; 3, 11 –
медные охлаждаемые ползуны; 4 – мунд-
штук; 5 – механизм подачи электрода; 6 –
электрод;
7 – выходная планка; 9 – шлаковая ванна;
10 –сварочная ванна; 12 - вводная планка;
стрелками указаны: направления вращения роликов механизма подачи электрода и на-
правление сварки.
сварки возбуждается электрическая дуга между сварочным электродом 6 и вводной
планкой 12. При расплавлении флюса, в пространстве между кромками заго-
товок 2 и 8 и медными водоохлажаемыми формирующими устройствами
(ползунами) 3 и 11 образуется шлаковая ванна 9. После накопления доста-
точного количества жидкого шлака дуга шунтируется шлаком и гаснет, а по-
дача электрода и подвод тока через мундштук 6 продолжаются. Шлаковая ванна является расплавленным электролитом. Поэтому, при прохождении то-
ка через расплавленный шлак в нем выделяется теплота, достаточная для поддержания высокой температуры шлаковой ванны (2 000оС), расплавле-
ния кромок заготовок и сварочной проволоки. Непрерывная подача свароч-
ной проволоки обеспечивает подвод тока и пополнение сварочной ванны 10
жидким металлом. По мере заполнения зазора между заготовками, мундштук и ползуны перемещаются вверх, оставляя после себя, сварной шов 1. На на-
чальном участке сварного шва образуется непровар кромок. На конечном участке сварного шва образуются: усадочная раковина и посторонние вклю-
154
чения. Поэтому сварку начинают на вводной планке, а заканчивают – на вы-
ходной планке 12. По окончании сварки, планки срезают газовой резкой. Ме-
талл кромок заготовок расплавляется одновременно по всему периметру шлаковой ванны, что позволяет вести сварку металла большой толщины за один проход.
По сравнению с ДСФ, ЭШС позволяет: повысить производительность сварки за счет: непрерывности процесса сварки; выполнения сварного шва за один проход при большой толщине заготовок; увеличения сварочного тока в
1,5…2 раза. Улучшить макроструктуру сварного шва за счет отсутствия мно-
гослойности и большей однородности однослойного шва. Снизить затраты на сварку вследствие: повышения производительности; упрощения процесса подготовки кромок заготовок; уменьшения сечения сварного шва; уменьше-
ния расхода сварочной проволоки, флюса и электроэнергии. К недостаткам ЭШС можно отнести: Большие вертикальные габариты установок. Крупно-
зернистую структуру сварного шва и околошовной зоны, получаемые вслед-
ствие замедленного нагрева и охлаждения сварного шва. После сварки необ-
ходимо провести отжиг и нормализацию готовой детали для измельчения зерна металла сварного соединения.
ЭШС широко применяется в машиностроении для изготовления кова-
но-сварных или лито-сварных конструкций (станины и детали мощных прес-
сов, станков, коленчатые валы судовых двигателей, роторы и валы гидротур-
бин).
Диффузионная сварка Диффузионная сварка - сварка давлением, осуществляемая за счет вза-
имной диффузии атомов в тонких поверхностных слоях контактирующих частей.
Отличительной особенностью диффузионной сварки является применение относительно высоких температур нагрева (0,5…0,7 Тплавления) и сравнительно низких удельных сжимающих давлений (0,5…0,7 МПа) при изо-
термической выдержке от нескольких минут до нескольких часов. Диффузи-
155
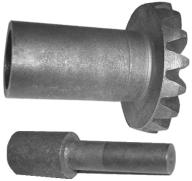
онную сварку выполняют в вакууме (сварка химически активных металлов)
или в атмосфере защитных или инертных газов.
Свариваемые заготовки устанавливают внутри охлаждаемой камеры, в
камере создается вакуум (10-3…10-5 Па) (или нагнетаются защитные или инертные газы). Нагрев заготовок производится с помощью нагревателя или индуктора ТВЧ. Процесс сварки идет в две стадии. На первой стадии заго-
товки нагреваются, и прикладывается давление. Происходит пластическое деформирование микровыступов и разрушение тонких пленок на контакти-
рующих поверхностях заготовок. На второй стадии заготовки выдерживают-
ся под давлением. Под действием диффузии, образуется объемная зона вза-
имного соединения. С целью ускорения процесса (сварка тугоплавких метал-
лов и сплавов) в камеру может быть введен электронный луч, позволяющий нагревать заготовки с более высокой скоростью. Для получения качественно-
го соединения, свариваемые поверхности заготовок необходимо предвари-
тельно очищать от окисных пленок и загрязнений.
Диффузионная сварка позволяет: соединять ме-
таллы, сплавы и керамические материалы в различ-
ных сочетаниях и соединять заготовки с большой разницей по толщине (рис. 5.11). Как правило, полу-
ченные соединения не нуждаются в последующей механической обработке.
Рис. 5.11. Примеры диффузионной сварки.
Плазменная сварка Плазменная сварка - сварка плавлением, при которой нагрев произво-
дится сжатой дугой. Источником теплоты при плазменной сварке является
плазменная струя – направленный поток ионизированных частиц газа, с тем-
пературой до 20 000оС. Сжатая дуга - это столб дуги, помещенный в узкий канал, который ограничивает его расширение. Устройства для получения сжатой дуги называют плазматронами.
156
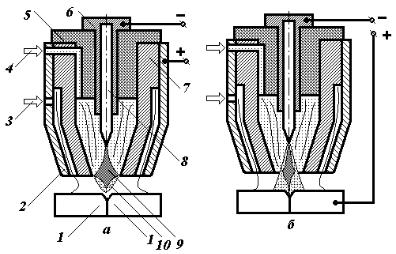
Плазму получают, пропуская поток плазмообразующего газа через столб сжатой электрической дуги 9 (рис. 5.12). Столб электрической дуги 9,
горящий между электродом 8 и плазмообразующим соплом 7, помещают в узкий канал с охлаждаемыми стенками, и через него продувают плазмообра-
зующий газ. В качестве плазмообразующего газа обычно используют аргон.
Рис. 5.12. Схемы плазматро-
нов:
а - косвенного действия; б –
прямого действия: 1 – свари-
ваемые заготовки; 2 – защит-
ное сопло; 3 – подача защитно-
го газа; 4 – подача плазмообра-
зующего газа; 5 -изолятор; 6 –
электрододержатель; 7 – плаз-
мообразующее сопло; 8 - электрод; 9 - электрическая дуга; 10 - плазменная дуга.
Для получения более мощной дуги используют водород или азот. Столб дуги сжимается, что приводит к повышению в нем плотности энергии и темпера-
туры. Частые столкновения частиц газа приводят к их высокой ионизации.
Загорается плазменная дуга 10. Нагретый в дуге газ, сталкиваясь с поверхно-
стями свариваемых заготовок 1, нагревает и оплавляет их. Под давлением га-
за расплавленный металл заготовок раздвигается, энергия дуги передается непосредственно твердому металлу дна сварочной ванны.
Меняя расход газа и диаметр канала сопла, можно изменять давление струи плазмы, а также плотность теплового потока, передаваемого от дуги к заготовкам. Это основное технологическое преимущество сжатой дуги, по-
зволяющее регулировать размеры и форму сварочной ванны. В сжатой дуге достигается высокая плотность теплового потока, особенно при малой мощ-
ности дуги. Это позволяет получать узкие швы с малой шириной зоны тер-
мического влияния и увеличивать скорость сварки. Так как плазмообразую-
157
щий газ передает детали значительную долю общей полезной мощности, а
нагрев газа сильно зависит от всех параметров режима, то эффективный КПД сжатой дуги можно изменять в пределах 30…80%. Другим преимуществом сжатой дуги является повышение ее пространственной устойчивости.
Уменьшается блуждание активного пятна по поверхности детали из-за ста-
билизирующего действия плазмообразующего газа. Это улучшает формиро-
вание шва.
Различают плазматроны косвенного (рис. 5.12, а) и прямого (рис. 5.12,
б) действия. В плазматронах косвенного действия дуга горит между электро-
дом и соплом. Эти плазматроны применяют при обработке неэлектропровод-
ных материалов и при пайке. Для сварки и резки чаще применяют плазма-
троны прямого действия. В них дуга горит между электродом и свариваемы-
ми заготовками. В этих плазматронах сжатую дугу зажигают в две стадии.
После подачи в плазматрон газа зажигают вспомогательную (дежурную) дугу между электродом и соплом плазматрона искровым разрядом от осциллятора или, замыкая промежуток электрод - сопло графитовым стержнем. Дежур-
ную дугу питают от отдельного маломощного источника или от основного источника через ограничивающее сопротивление, чтобы ограничить ее ток и уменьшить износ сопла. Под действием газа дежурная дуга образует струю плазмы небольшой мощности. При ее соприкосновении с деталью зажигается рабочая дуга.
При плазменной сварке применяют сварочный ток силой 3...400 А, на-
пряжение дуги 25...35 В, средняя скорость сварки составляет 15...50 м/ч.
Сжатой дугой сваривают детали толщиной 0,01...16 мм, отношение глубины проплавления к ширине шва составляет от 1:3 до 3:1 при толщине сваривае-
мых кромок 3...12 мм.
Плазменную дугу используют для сварки металлов (высоколегирован-
ной стали, сплавов титана, никеля, молибдена, вольфрама) и неметаллов;
резки всех материалов; пайки; наплавки; напыления.
158
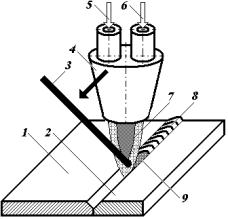
Плазменная резка производится высокоскоростной плазменной дугой.
В отличие от плазменных сварочных головок, плазменный резак снабжен до-
полнительными каналами для подачи в зону резания защитного газа (защит-
ное сопло 2). Резка производится при величине тока 55…150А и напряжении
110…120 В. В современных установках для плазменной резки, оснащенных числовым программным управлением, можно разрезать практически любые конструкционные материалы. В частности, можно разрезать низколегирован-
ные стали толщиной до 20 мм с точностью до 0,25 мм и скоростью реза до
1,12 м/мин.
5.3. Химические способы сварки
Химические способы включают в себя термитную и газовую сварку.
Газовая сварка Газовая сварка - сварка плавлением, при которой для нагрева исполь-
зуется тепло пламени смеси горючих газов с кислородом, сжигаемых с по-
мощью горелки.
Схема газовой сварки (ГС) показана на рис.5.13. Кромки заготовок 1и 2
Рис. 5.13. Схема газовой сварки:
1, 2 – свариваемые заготовки; 3 – присадочный пруток; 4 – газовая горелка; 5 – подача кисло-
рода; 6 – подача горючего газа; газовое 7 –
пламя; 8 – сварной шов; 9 - ванна жидкого металла; стрелкой указано пере-
мещение горелки.
подвергаются местному нагреву до оплавления сосредоточенным пламенем
6. Образовавшаяся ванна жидкого металла 9 контактирует с кромками обоих листов. При перемещении горелки 4 в направлении стрелки под пламенем металл будет расплавляться, а позади, в связи с охлаждением, – затвердевать,
образуя, сварной шов 8. Для увеличения рабочего сечения шва и повышения прочности сварного соединения, кромки под сварку делают со скосом (раз-
159
делка кромок). Полученный объем заполняют дополнительным расплавлен-
ным металлом, используя присадочный пруток 3.
ГС не требует сложного и дорогого оборудования, а также источника электроэнергии. Изменяя тепловую мощность пламени, его положение отно-
сительно места сварки и скорость сварки, можно в широких пределах регу-
лировать скорость нагрева и охлаждения свариваемого металла. При помощи ГС можно сваривать почти все металлы, применяемые в технике. Такие ме-
таллы, как чугун, медь, латунь, свинец легче поддаются газовой сварке, чем дуговой.
В ГС используются горючие газы: ацетилен, водород, метан, пропан и пары керосина. Основным горючим газом является ацетилен. Ацетилен -
бесцветный газ, с резким запахом, ядовит, взрывоопасен. Ацетилен получают из природного газа термоокислительным пиролизом метана с кислородом
(используется для снаряжения ацетиленовых баллонов) или в специальных ацетиленовых генераторах при взаимодействии карбида кальция с водой:
CaC2+2H2O=C2H2+Ca(OH)+ Q. Наиболее безопасно использовать ацетилен,
поставляемый в баллонах. Ацетилен поставляется в баллонах белого цвета с красной надписью «ацетилен». Ацетиленовые баллоны, для уменьшения взрывоопасности, заполнены пористым наполнителем (гранулированный ак-
тивированный уголь размером зерна 1…3,5 мм) и ацетоном. При давлении
1,5 МПа в одном литре ацетона растворяется до 368 л ацетилена. Макси-
мальное давление в ацетиленовых баллонах – 1.9 МПа.
Кислород поставляется в баллонах голубого цвета с черной надписью
«кислород». При давлении 15 МПа, в баллоне помещается 600 л газообразно-
го кислорода. Так как масла и жиры в атмосфере сжатого кислорода способ-
ны самовоспламеняться, то вся кислородная аппаратура не должна контакти-
ровать с этими веществами. В противном случае возможен взрыв с воронкой глубиной до 5 метров.
Для уменьшения сетевого или баллонного давления газа и обеспечения постоянного рабочего давления в газовых магистралях применяются газовые
160