
Tehnologiya_konstruktsionnyh_materialov
.pdfВыбивка отливок осуществляется на вибрационных выбивных решет-
ках, где под действием вибрации происходит разрушение формовочной сме-
си.
Выбивка стержней осуществляется на вибрационно–пневматических или гидравлических устройствах.
Обрубка отливок производится для удаления с отливки литников, при-
былей, выпоров и заливов. Она осуществляется пневматическими зубилами,
дисковыми и ленточными пилами и газовой резкой.
Очистка отливок от пригара, остатков формовочной и стержневой сме-
си производится чаще всего в дробеметных или гидропескоструйных каме-
рах.
3.3. Изготовление отливок специальными способами литья
Отливки, получаемые в разовых песчаных формах, во многих случаях не удовлетворяют требованиям современной техники, так как имеют недос-
таточно высокую точность размеров и качество поверхности. Применение специальных способов литья позволяет получать отливки повышенной точ-
ности, с малой шероховатостью поверхности, минимальными припусками на механическую обработку.
Литье по выплавляемым моделям
Прообраз процесса литья по выплавляемым моделям – метод восковой формовки известен свыше 4 000 лет, когда он применялся как метод художе-
ственного литья. Промышленное развитие он получил лишь в прошлом сто-
летии.
Сущность литья по выплавляемым моделям заключается в использова-
нии модели из легкоплавкого материала (воска, парафина, стеарина) и специ-
альных облицовочных материалов, которые наносят на модель для получе-
ния литейной формы.
61
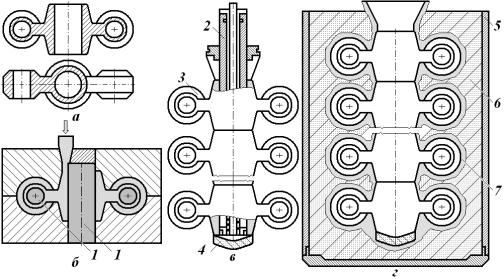
Технология изготовления отливок по выплавляемым моделям имеет большое количество вариантов во всех основных операциях, а также в рецеп-
турах модельных и формовочных материалов.
Упрощенная схема литья по выплавляемым моделям для получения стальной отливки приведена на рис. 3.15.
В металлическую разъемную пресс-форму (рис. 3.15, б), внутренняя поверхность которой выполнена с большой точностью, запрессовывают под небольшим давлением расплавленный легкоплавкий модельный состав
(смесь парафина, стеарина, воска или других компонентов), который после охлаждения и извлечения из формы образует модели 3 с элементами литни-
ковой системы, имеющие точные размеры и высокое качество поверхности.
Полученные модели собираются в блоки с общей литниковой системой (рис.
3.15, в).
Рис. 3.15.
Схема изго-
товления от-
ливок литьем по выплав-
ляемым мо-
делям:
а – отливка;
б – изготов-
ление модели; в – блок моделей; г – неразъемная форма; 1 – стержни; 2 – ме-
таллический штырь; 3 – модель; 4 – колпачок; 5 – опока; 6 – наполнитель; 7 –
огнеупорная оболочка.
На блоки наносится несколько слоев огнеупорного облицовочного ма-
териала (методом погружения блока моделей в раствор с промежуточной сушкой и обсыпкой кварцевым песком каждого слоя). После сушки блоков и выплавления модельного состава образуется огнеупорная оболочка - форма
62
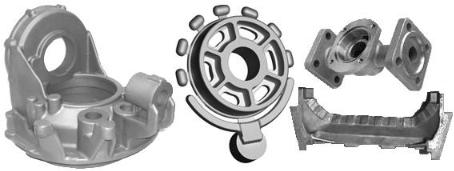
7, которую помещают в опоку 5, засыпают наполнителем 6 для повышения ее прочности, прокаливают и заливают металлом (рис. 3.15, г).
После затвердевания металла формы выбивают, отливки отрезают от стояка и очищают от остатков формы.
Литье по выплавляемым моделям широко применяется для изготовле-
ния отливок из черных и цветных металлов (рис. 3.16) во многих отраслях промышленности. Несмотря на то, что данный способ литья трудоемкий и дорогой, его применение оправдывается при получении точных отливок без последующей механической обработки, при изготовлении деталей со слож-
ной и трудоемкой механической обработкой, при использовании труднооб-
рабатываемых и тугоплавких сплавов.
Рис. 3.16. Примеры отливок по вы-
плавляемым моде-
лям.
Этим спосо-
бом изготавливают рабочие колеса и лопатки авиационных, газовых и паровых турбин, сложные детали приборов, детали стрелкового оружия, режущий инструмент, различ-
ные детали автомобилей (шаровые пальцы, коромысла клапанов, вилки ко-
робок передач), и многое другое.
Литье в оболочковые формы
Способ литья в оболочковые формы основан на использовании в соста-
ве формовочных смесей специальных связующих (термореактивных смол),
способных при нагреве плавиться, а затем при повышении температуры не-
обратимо твердеть, образуя с песком прочную оболочку.
Металлической плитой, нагретой до температуры 200 … 250ºС, накры-
вают поворотный бункер 3 с формовочной смесью 4, состоящей из сухого кварцевого песка и порошка термореактивной смолы (рис. 3.17).
63
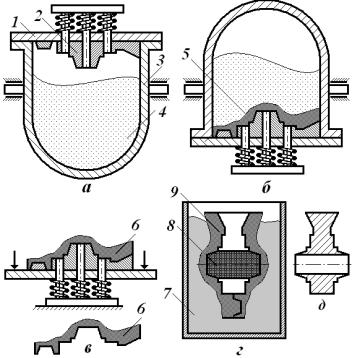
При повороте бункера на 180ºС смола, находящаяся в слое смеси, при-
легающем к нагретой плите, оплавляется и связывает частицы песка. На мо-
дели образуется полутвердая оболочка 5 толщиной 5 … 15 мм (толщина обо-
лочки зависит от времени контакта нагретой плиты с формовочной смесью).
Бункер возвращают в исходное положение, а плиту вместе с оболочкой сни-
мают с бункера и помещают на 2 … 3 мин в печь, где при температуре 280 …350ºС происходит окончательное затвердевание оболочки.
Полученную оболочку 6 снимают с модельной плиты - это половина литейной формы. С помощью второй модельной плиты получают другую по-
ловину формы. Полуформы собирают, устанавливая в них при необходимо-
сти стержни, и форму заливают расплавленным металлом.
Рис. 3.17 .Принципиальная схе-
ма изготовления оболочковых форм:
а – исходное положение; б –
получение оболочки; в – съем оболочки; г – форма в сборе; д –
отливка; 1 – модельная плита; 2
– модель; 3 – поворотный бун-
кер; 4 – формовочная смесь; 5 –
оболочка; 6 – полуформа, 7 –
наполнитель; 8 – стержень; 9 –
форма в сборе.
После заливки металла и затвердевания отливки оболочковая форма легко разрушается.
Основными преимуществами литья в оболочковые формы по сравне-
нию с литьем в песчаные формы являются более высокая точность размеров и качество поверхности отливок, высокая газопроницаемость форм, умень-
шение трудоемкости изготовления форм.
64
К недостаткам метода следует отнести применение дорогостоящих ма-
териалов, ограниченность размеров и массы отливок, трудность регенерации песка, невысокие санитарно – гигиенические условия труда.
Оболочковые формы широко используются при изготовлении мелких и средних отливок из сплавов цветных металлов и ответственных чугунных отливок: ребристых цилиндров, коленчатых и распределительных валов и других деталей.
3.4. Литье в многоразовые формы
Наряду с разовыми формами в литейном производстве применяются постоянные формы – кокили, которые изготавливают из чугуна, стали, а ино-
гда из цветных сплавов.
Литье в кокиль
При литье в кокиль отливки получают путем заливки расплавленного металла в металлические многократно используемые формы, конструкции которых разнообразны: неразъемные и разъемные (с вертикальной, горизон-
тальной и комбинированной плоскостями разъема). Они могут быть одноме-
стными и многоместными. Число плоскостей разъема и их расположение за-
висят от конфигурации литой детали и положения отливки при заливке.
Внутренние полости в отливках при литье в кокиль могут выполняться как разовыми песчаными, так и постоянными металлическими стержнями, в том числе и разъемными.
На рис. 3.18 приведена конструкция кокиля для получения литого алюминиевого поршня. Кокиль имеет вертикальный разъем и состоит из двух половин 1, 6 и нижней плиты 8. Для получения отверстий в поршне исполь-
зуются металлические стержни. Причем, если боковые стержни под поршне-
вые пальцы 7, будут затем извлекаться из отливки без особых затруднений,
то извлечь центральный стержень можно только, если он разъемный. После охлаждения отливки сначала извлекается центральная клиновая часть 4, а за-
тем боковые 3 и 5.
65
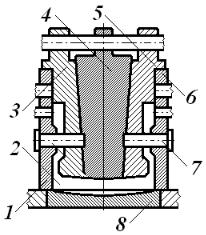
Технология литья в кокиль имеет ряд особенностей. Формирование от-
ливки происходит в условиях интенсивного отвода тепла от отливки к метал-
лической форме, обладающей повышенной теплопроводностью. В результате быстрого затвердевания структура металла становится мелкозернистой и плотной, а, следовательно, отливки получаются с повышенными механиче-
скими свойствами.
Рис. 3.18. Конструкция кокиля для литья алюми-
ниевого поршня:
1, 6 – половинки кокиля; 2 - внутренняя полость кокиля; 3, 4, 5 - металлический разъемный стер-
жень; 7 - боковой стержень; 8 – нижняя плита.
На поверхности чугунных отливок в резуль-
тате быстрого охлаждения возможно образование слоя цементита (FeзC) – отбела, затрудняющего
механическую обработку отливок. Образование отбела можно предотвратить использованием облицованных кокилей, имеющих внутреннее теплоизоля-
ционное покрытие, которое предотвращает отбеливание чугуна и разгар ко-
киля.
Кокиль практически не податлив и интенсивно препятствует усадке от-
ливки, что способствует возникновению в отливках внутренних напряжений,
которые в большинстве случаев снимаются последующей термической обра-
боткой.
Литьем в кокиль можно получать отливки практически из всех сплавов массой от нескольких килограммом до нескольких тонн. Наибольшее рас-
пространение получило литье в кокиль алюминиевых и магниевых сплавов,
обладающих сравнительно невысокой температурой плавления и хорошими технологическими свойствами. Этим методом получают головки блоков ав-
томобилей, поршни, корпуса масляных насосов и другие детали.
Литье в кокиль по сравнению с литьем в песчаные формы имеет ряд преимуществ: повышенные механические свойства отливок, более высокие
66
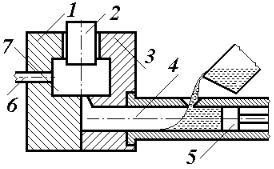
точность размеров и качество поверхности, улучшенные технико-
экономические показатели и санитарно-гигиенические условия труда.
Основными недостатками литья в кокиль являются низкая стойкость и большая стоимость формы, пониженная заполняемость кокиля, трудность или невозможность получения тонкостенных отливок, возможность получе-
ния отбела в отливках из чугуна.
Литье под давлением
Сущность процесса литья под давлением состоит в том, что фасонные отливки получают в металлических разъемных пресс-формах, принудительно заполняемых расплавленным металлом. Это позволяет получать сложные по конфигурации отливки, точных размеров, имеющих высокое качество по-
верхности, с четкими конструктивными рельефами и готовыми отверстиями.
Внутренние полости и отверстия в отливках формируют с помощью металлических стержней, применение песчаных стержней исключается, так как струя металла, подаваемая в форму под давлением (100 МПа и более),
может разрушить песчаный стержень.
Литье под давлением осуществляется на специальных машинах порш-
невого и компрессорного действия, из которых наиболее широко применя-
ются машины поршневого типа с холодной камерой прессования.
Принципиальная схема получения отливки на такой машине с горизон-
тальной камерой сжатия приведена на рис. 3.19. Пресс-форма состоит из двух Рис. 3.19. Схема литья под давлением:
1 – подвижная половина пресс-формы; 2 -
стержень, 3 - неподвижная половина пресс-формы; 4 - камера сжатия;5 - пор-
шень; 6 – выталкиватель: 7 - полость пресс-формы.
частей: подвижной 1 и неподвижной 3, которые с большим усилием прижи-
маются друг к другу. Для удобства извлечения стержни обычно располага-
ются в подвижной половине. В камеру сжатия 4 заливают жидкий металл,
67
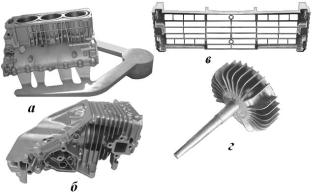
который поршнем 5 запрессовывается в полость пресс-формы 7. После за-
твердевания металла пресс-форма раскрывается, выталкиватель 6 удаляют отливку, пресс-форму закрывают и процесс повторяется.
Струя металла подается в полость прессформы под большим давлени-
ем и скоростью, в результате чего из полости формы не успевают удалиться газы и воздух. Это приводит к образованию пор под литейной корочкой, что исключает последующую высокотемпературную термообработку.
Основные достоинства литья под давлением – высокие точность разме-
ров и качество поверхности получаемых отливок, возможность получения тонкостенных отливок и высокая производительность процесса литья, а ос-
новные недостатки – газовая пористость отливок, ограниченные габаритные размеры, низкая стойкость пресс-форм при повышении температуры заливки.
Литье под давлением применяется для получения точных тонкостен-
ных отливок из сплавов цветных металлов в серийном и массовом производ-
ствах в электротехнической промышленности, точном приборостроении, в
автомобильной промышленности (блоки цилиндров, корпуса карбюраторов,
крышки генераторов, барабаны стеклоподъемников, решетки и другие детали
(рис. 3.20).
Рис. 3.20. Автомобильные детали,
полученные литьем под давлением:
а, б – блоки цилиндров; в - решетка радиатора; г – крыльчатка насоса.
Повышенная плотность и гер-
метичность крупных тонкостенных корпусных заготовок из легкоплав-
ких сплавов получается при применении литья под низким давлением.
Для получения отливок, не имеющих газовой и воздушной пористости применяется также жидкая штамповка. В металлическую прессформу 1
(рис. 3.21), состоящую из матрицы и подвижного пуансона 3, заливают пор-
цию
68
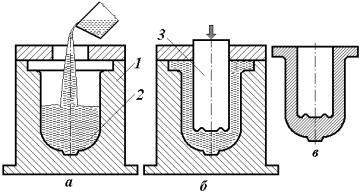
жидкого металла 2. Пуансон медленно входит в металл и производит его выдавливание в полость формы. Металл, соприкасаясь со стенками формы,
охлаждается, затвердевает и подвергается небольшой пластической дефор-
мации, что приводит к получению детали с повышенной плотностью и по-
вышенными механическими свойствами.
Рис. 3.21. Схема штамповки заготовок из жидкого металла:
а – заливка металла; б – вы-
давливание металла в полость формы; в – отливка: 1 - пресс-
форма; 2 -жидкий металл; 3 - подвижной пуансон.
Центробежное литье
Сущность способа заключается в том, что расплавленный металл зали-
вают во вращающуюся форму. Под действием центробежной силы металл равномерно распределяется по внутренней поверхности формы, заполняет все полости и затвердевает, образуя отливку.
Центробежные силы создают условия для направленного затвердева-
ния металла, от стенок формы, способствуя повышению плотности отливки.
При этом легкие неметаллические включения оттесняются к внутренней по-
верхности, скапливаются там и затем удаляются при механической обработ-
ке.
В зависимости от положения оси вращения формы центробежные ма-
шины делятся на машины с горизонтальной, вертикальной (рис. 3.22), а ино-
гда и наклонной осью вращения.
При использовании машины с вертикальной осью вращения отливка может получиться с параболической внутренней поверхностью, так как
помимо центробежных сил на металл действует и сила тяжести. На этих ма-
шинах получают отливки небольшой высоты (короткие втулки, кольца и дру-
гие заготовки).
69
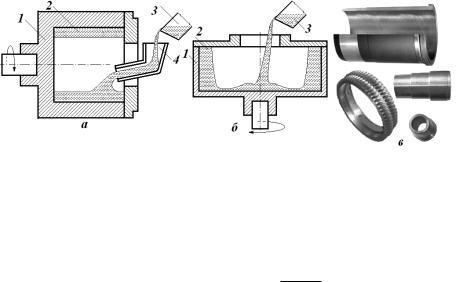
Качество получаемых отливок зависит от скорости вращения формы.
При малой частоте вращения формы отливки получаются с пониженной плотностью, металл плохо очищается от неметаллических включений, а при очень быстром вращении увеличивается ликвация, нарушается нормальный процесс затвердевания отливки.
Рис. 3.22. Схемы центробежного ли-
тья
а - на машине с го-
ризонтальной осью вращения; б – на машине с вертикальной осью вращения; в – примеры отли-
вок; 1 – форма; 2 – жидкий металл; 3 - ковш; 4 - заливочный желоб.
На практике расчет частоты вращения формы обычно определяют по
формуле Л.С. Константинова: n 5520 ; где n - частота вращения формы,
r
мин-1; ρ - плотность сплава, т/м3; r - внутренний радиус формы, см.
Основные преимущества центробежного способа литья заключаются в получении отливок высокого качества (плотная, мелкозернистая структура),
отсутствие стержней для оформления цилиндрических отверстий, экономия металла на литниках и прибылях.
Наряду с достоинствами центробежному способу присущи и недостат-
ки. К ним следует отнести ликвацию сплавов под действием центробежных сил и повышенные припуски на механическую обработку для внутренних размеров.
Центробежное литье применяют для получения отливок, имеющих форму тел вращения (цилиндров, втулок, венцов, гильз цилиндров) и для фа-
сонных отливок сложной конфигурации.
Помимо перечисленных методов литья в настоящее время применяют-
ся и другие методы: непрерывное литье, электрошлаковое литье, литье под низким давлением, регулируемым давлением, вакуумным всасыванием и
70