
Kontrolnye_semestrovye_zadanija_po_discipline
.pdf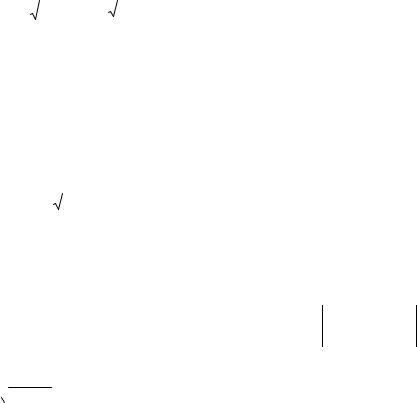
выбирается из конструктивных соображений.
Если в штампе применяются два диагонально расположенных направляющих узла, то минимальный диаметр dНП (мм) направляющей колонки можно определить по формуле
dНП = 0,5 × |
F ПЛ |
+ 70 × 8 |
P |
, |
|
где: FПЛ – |
площадь опорной поверхности плиты, (см2); |
||||
Р – полное расчетное усилие, (кН). |
|
||||
Полученное значение dНП округляется до ближайшего значения из номинального ряда по |
|||||
ГОСТ 13120–83: 12, 14, 16, 16, 20, 22, 25, 28, 32, 36, |
40, 45, 50, 56, 63 и т.д. |
||||
При заднем расположении колонок диаметр dНП |
должен быть увеличен до следующего |
стандартного значения, а при установке трех или четырех направляющих узлов соответственно уменьшен до следующего стандартного значения.
Форма и размеры матрицы определяются штампуемой деталью. Толщину НМ (мм) матрицы определяют по эмпирической формуле
НМ = s + KM × |
a + b + 7 |
, |
|
|
|
|
|
|
|||
где: a и b – размеры рабочей зоны матрицы, мм; |
|
|
|
|
|||||||
|
s – толщина штампуемого материала, мм; |
|
|
|
|
||||||
|
KM – |
коэффициент, зависящий от свойств штампуемого материала. |
|
|
|||||||
Значения коэффициента KM приведены в таблице 14. |
|
Таблица 14 |
|||||||||
|
|
|
|
|
|
|
|
|
|
||
|
sВ, МПа |
|
До 120 |
120…200 |
200…300 |
300…500 |
500…1000 |
|
св. 1000 |
||
|
KM |
|
0,5 |
|
0,6 |
0,8 |
1,0 |
1,5 |
|
2,0 |
Дополнительно достаточность толщины НМ (мм) матрицы проверяется по эмпирической формуле
НМ = 3 100 × Р ,
где Р – требуемое технологическое усилие штамповки, кН.
После этого из двух значений выбирается большее и округляется до ближайшего значения из следующего ряда чисел: 8, 10, 12, 16, 20, 25, 28, 32, 36, 40, 45, 50, 56, 63, 71, 80.
Пуансон проверяется на смятие опорной поверхностью головки поверхности плиты. Напряжение смятия sСМ (МПа) поверхности головки
sСМ = P / FГОЛ,
где: P – технологическое усилие, воспринимаемое пуансоном, Н; FГОЛ – площадь поверхности его головки, мм2.
Если sСМ>100 МПа, то пуансон следует упирать головкой в стальную закаленную подкладную плиту.
Буферные устройства являются необходимым элементом большинства штампов, их применяют для обеспечения необходимого усилия для прижима или выталкивания. Расчет буферного резинового устройства выполняют в следующей последовательности. Исходными данными для расчета являются усилия в начале Р1 и в конце Р2 операции, а также требуемый ход hВФ буфера.
Определяется предварительное сжатие буфера
|
= |
hБФ |
. |
|
1 |
|
|||
|
Р |
−1 |
||
|
|
2 |
||
|
|
Р1 |
||
|
|
|
|
Требуемые усилия Р1 и Р2 определяют исходя их характеристики выполняемой операции. Наибольшее допускаемое сжатие буфера
D2 = y × НВФ,
где: y = 0,3 – относительное обжатие буфера на 30%; НВФ – высота буфера в свободном состоянии.
Полное сжатие буфера D определяется из выражения
D = D1 + hВФ = hВФ × Р2 / (Р2 - Р1).
Требуемая полезная площадь FВФ (мм2) определяется из условия, что при y = 0,3 развиваемое резиной удельное усилие составляет 1,7 Н/мм2.
FВФ = Р2 × h /1,7,
где h – коэффициент, зависящий от твердости резины, h = 0,75…1,5. Если буфер сжимается не на 30%, то усилие, развиваемое буфером
РВФ= 5,7 × FВФ ×DВФ / НВФ × h,
относительное сжатие
y = ×DВФ / НВФ.
Полезная площадь буфера FВФ, требуемая для обеспечения РВФ
FВФ = РВФ × НВФ × h/5,7×DВФ.
При размещении резинового буфера необходимо учитывать его выпучивание, при этом для цилиндрического буфера D3ВФ=1,3 DВФ.
При проведении расчетов необходимо выдерживать условие НВФ £0,3 DВФ.
При использовании полиуретанового буфера методика расчета остается такой же, однако удельное усилие в среднем 4 Н/мм2 и h = 1,2…0,85.
6. РАЗРАБОТКА СБОРОЧНОГО ЧЕРТЕЖА ШТАМПА Сборочный чертеж выполняется на листе стандартного формата с соблюдением
требований ЕСКД и обычно в масштабе 1:1. Спецификация является приложением к расчетно– пояснительной записке.
Вконструкции штампа, имеющего рабочие элементы из твердых сплавов или твердосплавные вставки, должны быть применены шариковые направляющие узлы, обеспечивающие надежность работы штампа.
Пуансоны и матрицы должны опираться на закаленные подкладные плиты, если давление, передаваемое опорными поверхностями пуансонов и матриц на плиты, превышает допускаемое напряжение на их смятие.
Конструкции съемников и прижимов должны обеспечить повторную заточку режущих кромок без снятия пакета. Возможность неправильной сборки верхней и нижней частей штампов должна быть полностью исключена.
Рабочие детали штампов сложной конфигурации выполняются секционными. Длина секций определяется технологическими возможностями изготовителя (но не более 300 мм). Крепление секций должно исключать возможность их смещения. Секции крепят штифтами, врезкой в плиты, собирают в обоймы и т.п. В местах стыка секций зазор не допускается.
Длина посадочной части под штифты в деталях, имеющих толщину более двух диаметров штифтов, должна быть не более двух диаметров. Диаметр остальной части отверстия следует выполнять не менее чем на 1мм больше диаметра штифта.
Вдеталях, фиксируемых с помощью цилиндрических штифтов, где отверстия под штифты не являются сквозными, необходимо предусматривать резьбовые отверстия для их выпрессовки с помощью винтов.
Неуказанные литейные радиусы в зависимости от габаритных размеров заготовок деталей штампов должны быть в пределах от 2 до 40 мм. Неуказанные формовочные уклоны назначаются изготовителем. Допускается вместо литейных уклонов применять фаски.
Отклонение высоты штампа в закрытом состоянии от размера, указанного на чертеже, не
должно превышать: ± 3,0 мм для штампов с закрытой высотой до 250 мм; ± 5,0 мм – с закрытой высотой свыше 250 до 630 мм; ± 10,0 мм – с закрытой высотой свыше 630 мм. Если штамп крепится к прессу при помощи хвостовика, то хвостовик следует размещать так, чтобы его ось совпадала с центром давления штампа, т.е. с точкой, к которой приложена равнодействующая всех сил, действующих в направлении, параллельном оси хвостовика. Если штамп крепится без хвостовика, его установка на пресс должна быть выполнена таким образом, чтобы центр давления штампа совпадал с вертикальной осью пресса.
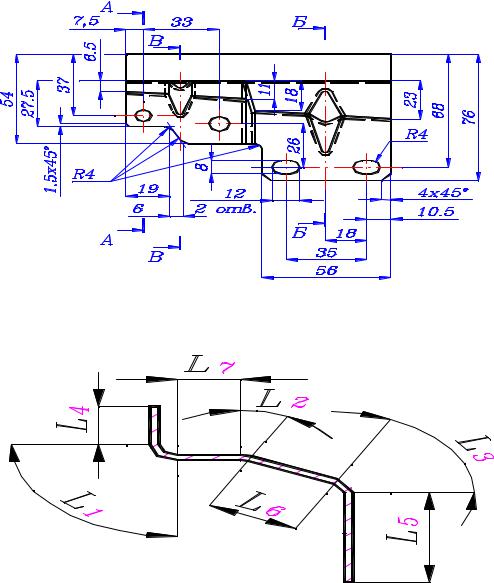
Направляющие узлы следует располагать симметрично относительно центра давления штампа.
7. ПРИМЕР ВЫПОЛНЕНИЯ КОНТРОЛЬНОЙ РАБОТЫ
7.1. ОПРЕДЕЛЕНИЕ РАЗМЕРОВ ИСХОДНОЙ ЗАГОТОВКИ Чертеж типовой детали “ кронштейн крепления крыла” приведен в приложении 5.
Необходимо определить форму и размеры исходной заготовки. Вид детали в плане представлен на рис. 1.
Рис. 1. Вид детали в плане Разобьем контур заготовки в поперечном сечении на прямолинейные и криволинейные
участки. Расчетная схема представлена на рис. 2.
Рис. 2. Расчетная схема определения ширины заготовки
Определим ширину заготовки.
Внутренний радиус гиба r = 3 мм, толщина заготовки s = 1,5 мм, тогда
r / s = 2,
радиус нейтральной линии ρ = 3,67 мм.
Для криволинейного участка
L = π* ρ * αг / 180,
где αг – угол закругления между двумя радиусами, проведенными в точки начала и конца закругления перпендикулярно к прямым участкам детали.
При αг = 90 град длина криволинейного участка

L 1 = 5,8 мм.
Для наклонной полки αг = 32,6°.
L 2 = L 3 = 2,1 мм.
Длины прямолинейных участков:
L 4 |
= (16 – 1,5 – 3) = 11,5 мм, |
||
L 5 |
= 76 |
– 16 – 23 = 37 |
мм, |
L 6 |
= (362 + 232)0,5 – 2 |
. 3 . tg (32,6°) = 39 мм, |
|
L 7 |
= 6 – |
3 – 1,5 = 1,5 |
мм, |
Длину развертки Lг определяют как сумму длин прямых и закругленных по условной нейтральной линии участков
Lг = Σ Lп i + Σ (π *ρi *αг i / 180).
Ширина заготовки
B1 = 5,8 + 2 . 2,1 + 11,5 + 37 + 39 + 1,5 = 99 мм.
При изготовлении необходимо получить как правую, так и левую детали (левая – зеркальное отражение правой). Для того чтобы центр давления штампов переходов располагался по оси симметрии заготовки, обрабатываем сразу обе детали, а на последнем переходе их разрезаем. Зададим ширину перемычки между полуфабрикатами деталей равной 10 мм. Тогда ширина исходной заготовки
B2 = 99 . 2 + 10 = 208 мм.
Припуск на обрезку наружной полки 3 мм. Ширина вырубленной заготовки
B3 = 4,5 . 2 + 205 = 214 мм.
В качестве исходной заготовки выбираем полосу. Величина перемычек между заготовкой и краем полосы 4,5 мм.
Ширина полосы
BП = 4,5 . 2 + 214 = 223 мм.
Аналогично определяем длину заготовки. На рис. 3 изображен фронтальный вид детали.
Рис. 3. Фронтальный вид детали
Внутренний радиус гиба r = 2,5 мм, толщина заготовки s = 1,5 мм, тогда
r / s = 1,67,
радиус нейтральной линии
ρ = 3,67 мм.
Для наклонной полки αг = 62,7°.
L 8 = L 9 = 4 мм.
Длины прямолинейных участков:
L 10 = 52 мм,
L 11 = 59 мм,
L 12 = 3 мм.
Длина заготовки
L = 52 + 2 . 4 + 3 + 59 = 122 мм.
Для базирования заготовки при установке ее в штампы соответствующих переходов вводим два технологических отверстия диаметром 12,2 мм.
После анализа чертежа детали и теоретической развертки предлагаем следующую схему обработки: деталь можно получить за четыре перехода, на первом переходе – операция 10, производим вырубку из полосы внешнего контура заготовки и пробивку двух технологических отверстий; на втором переходе – операция 20, выполняем операции гибки полок и формовку ребер жесткости; на третьем переходе – операция 30, выполняем пробивку отверстий и обрезку припуска по ширине детали; на четвертом переходе – операция 40, выполняем разрезку полуфабриката на две детали – левую и правую.
Для выбора основного технологического оборудования необходимо определить технологические усилия по каждой операции.
7.2. ОПРЕДЕЛЕНИЕ НЕОБХОДИМЫХ ТЕХНОЛОГИЧЕСКИХ УСИЛИЙ Технологическое усилие P(H) разделительных операций в штампах с металлическими рабочими деталями, у которых соответствующие режущие кромки пуансона и матрицы параллельны между собой, вычисляются по формуле
P = L * s * σср,
где L – периметр контура вырубки, пробивки или отрезки, мм; s – толщина штампуемого материала, мм; σср – сопротивление срезу, МПа.
Материал заготовки – сталь 08 кп ГОСТ 4041–71.
σср = 250 Мпа.
Определяем длину периметра вырубки наружного контура заготовки
L k = 120 + 2 * 47,2 + 2 * 119 + 2 * 65,2 +84 = 666,8 мм.
Длина периметра пробиваемого отверстия диаметром 12,2 мм
L отв = 116,84 мм.
Суммарная длина реза
L = L k + 2 * L отв = 666,8 + 2 * 116,84 = 900,5 мм.
Определяем усилие операции вырубки и пробивки
P1 = 900,5 * 1,5 * 250 = 337679,6 H = 338 кН.
Для повышения качества вырубки применяем прижимные устройства. Усилие Pпр , которое должен обеспечить прижим, Н
Pпр = L * s * qпр,
где qпр (Н/мм 2) – удельное усилие.
Принимаем qпр = 15 Н/мм2, тогда усилие прижима
Pпр = 1,5 * 15 * 900,5 = 20261 Н = 20,3 кН.
При оснащении штампа выталкивающими устройствами, усилие выталкивания (противодавление) должно составлять
Pпд = 0,1 * P1 .
Pпд = 0,1 * 338 = 33,8 kH.
Выбираем схему штампа, в которой прижим выполняет одновременно роль съемника, в этом случае учитываем максимальное усилие
Pпд = 33,8 kH.
Усилие проталкивания детали или отхода через матрицу определяется по формуле
Pп = к пр * P1 .
Усилие снятия детали или отхода с пуансона определяется как
P сн = к сн * P1 .
Принимаем коэффициенты
k сн = 0,04 и kпр =0,03.
Усилие проталкивания
Pп = 0,03 * 338 = 10,1 кН.
Усилие снятия
Pсн = 0,04 * 338 = 13,5 кН.
Суммарное усилие штамповки
Pобщ = P1 + Pпр + Pпд + Pп + Pсн.
Pобщ = 338 + 20,3 + 33,8 + 10,1 + 13,5 = 415,7 кН.
Необходимое усилие пресса вычисляют по формуле
Pпресса = 1,25 * Pобщ.
Pпресса= 1,25 * 415,7 = 520 кН.
При выборе пресса для выполнения технологической операции необходимо проверить запас энергии, которой он должен обладать. Для этого вычисляется работа деформирования А (Дж), необходимая для выполнения операции
A = Pср * h р,
где Pср – усредненное усилие штамповки, кН; h р – рабочий ход пуансона, мм.
Рабочий ход пуансона при выполнении разделительных операций в штампах с параллельными режущими кромками матрицы и пунсона равен толщине материала s. Принимаем усредненное усилие Pср = 0,7 * Pобщ
Pср = 0,7 * 415,7 = 291 кН.
Работа деформирования А (Дж), необходимая для выполнения операции
A = Pср * h р,
A = 291 * 1,5 = 436,5 Дж.
Таким образом, пресс необходимый для выполнения разделительных операций должен обеспечить усилие не менее 520 кН, обладать запасом энергии не менее 436,5 Дж и иметь подштамповую плиту с длиной не менее 480 мм.
Для выполнения операции 10 выбираем пресс КИ2128А с номинальным усилием 630 кН. Определим усилие, необходимое для выполнения операции 020 – формовка заготовки, при этом происходит гибка полок и формовка ребер жесткости.
Для определения необходимого усилия при выполнении операций гибки необходимо определить изгибающий момент.
Изгибающий момент при гибке заготовки единичной длины с учетом влияния упрочнения
M = β {σто (R – r) 2 / 4 +П [0.25(R2 + r2) ln (R/r)0.5 – 0.125 (R 2 – r 2)]},
где β = 1,15 (для плоской деформации) – коэффициент, учитывающий влияние среднего по величине главного напряжения; σто – экстраполированный предел текучести; П – средний модуль упрочнения; R и r – соответственно наружный и внутренний радиусы гиба.
Экстраполированный предел текучести
σто = σв (1 – 2 Ψв) / (1 – Ψв)2,
где σв – предел прочности штампуемого материала, Мпа; Ψв – относительное уменьшение площади поперечного образца в момент начала образования шейки
Ψв = εв / (1 + εв),
где εв – относительное удлинение материала при растяжении образца в момент начала образования шейки, определяемое как
εв = 0,8 * δ10,
где δ10 – относительное удлинение при разрыве образца. Средний модуль упрочнения определяется по формуле
П = σв / (1 – Ψв) 2.
Определяем необходимые механические характеристики. Для стали 08 кп :
σв = 380 МПа, δ10 = 30 %. εв = 0,8 * 0,3 = 0,24,
Ψв = 0,24 / 1,24 = 0,194, П = 380 / (1 – 0,194) 2 = 395 МПа,
σто = 380 * (1 – 2 * 0,194) / (1 – 0,194) 2 = 358 МПа.
Изгибающий момент при гибке заготовки единичной длины
М = 1,15 * {358 * 0,25* 1,5 2 +
+ 395 * [0,25 * (4,5 2 + 3 2) * ln (4,5 / 3) 0,5 – 0,125 * (4,5 2 – 3 2) ] } = 266,2 H м.
Суммарная длина линий гиба Lг1 = 720 мм. Изгибающий момент, необходимый для гибки
M1 = 266,2 * 0,72 = 192 H м.
Плечо гиба
Lp = rм + rп + s + c* s,
где с = 0,1 – коэффициент, учитывающий зазор между матрицей и пуансоном; rм = 3 мм – радиус матрицы, rп = 3 мм – радиус пуансона.
Минимальное плечо гиба Lp = 1,65 мм.
При выполнении одноугловой гибки, зажатой одним концом, необходимое усилие Рг = М1 / Lp,
Рг = 192 / 1,65 * 10 –3 = 116,2 kH.
Определяем усилие РР, необходимое для штамповки ребер жесткости
РР = L * s * k * σв,
где L = 4 * 0,066 = 0,264 м – суммарная длина ребер жесткости, s – толщина заготовки, к =1 – коэффициент, зависящий от глубины и ширины ребра.
РР = 0,264 * 0,0015 * 380 * 106 = 150500 Н =150,5 кН.
Общее усилие формовки заготовки Pобщ
Pобщ = Рг + РР,
Pобщ = 116,2 + 150,5 = 266,7 кН.
Для обеспечения высокого качества гибки необходимо предусмотреть в конструкции штампа прижим, усилие которого составляет 25 – 30 % от Pобщ, т.е. усилие прижима составит
Рпр = 0,3 * 266,7 = 80 кН.
Необходимое суммарное усилие
Pсум = Pобщ + Рпр,
Pсум = 266,7 + 80 = 346,7 кН.
Необходимое усилие пресса в этом случае
Pпресса= 1,25 * 346,7 = 434 кН.
Определим усилие, необходимое для выполнения операции 30.
На данном переходе проводим пробивку двух отверстий диаметром 7 мм, двух отверстий диаметром 9 мм и четырех пазов шириной 8 мм и длиной 12 мм.
Усилие пробивки и обрезки
P = L * s * σср.
Суммарная длина L 1 контура пробивки
L 1 = 2 * 3,14 * (7 + 9) + 2 * 3,14 * 8 + 8 * 4 = 183 мм.
Суммарная длина L 2 линий обрезки
L 2 = 116 * 2 = 232 мм.
Общая длина L линии реза
L = 232 + 183 = 415 мм.
Усилие пробивки и обрезки
P = 415 * 1,5 * 250 = 155,6 кН.
Усилие Pпр , которое должен обеспечить прижим, Н
Pпр = L * s * qпр,
где qпр = 15 Н/мм2 – удельное усилие прижима, тогда усилие прижима
Pпр = 1,5 * 15 * 415 = 9337,5 Н = 9,3 кН.
При оснащении штампа выталкивающими устройствами, усилие выталкивания (противодавление)
Pпд = 0,1 * P1 .
Pпд = 0,1 * 155,6 = 15,6 kH.
Выбираем схему штампа, в которой прижим выполняет одновременно роль съемника, в этом случае учитываем максимальное усилие Pпд = 15,6 kH.
Усилие проталкивания детали или отхода через матрицу Pп = к пр * P . Усилие снятия детали или отхода с пуансона P сн = к сн * P , Принимаем коэффициенты k сн = 0,04 и kпр =0,03.
Усилие проталкивания Pп = 0,03 * 155,6 = 4,7 кН.
Усилие снятия Pсн = 0,04 * 155,6 = 6,2 кН.
Суммарное усилие штамповки Pобщ = P + Pпр + Pпд + Pп + Pсн.
Pобщ = 155,6 + 9,3 + 15,6 + 4,7 + 6,2 = 191,4 кН.
Необходимое усилие пресса Pпресса = 1,25 * Pобщ.
Pпресса= 1,25 * 191,4 = 239,3 кН.
Определяем усилие, необходимое для выполнения операции 40, при этом происходит разрезка полуфабриката на две детали.
Длина реза L
L = 2 * (56 + 34 + 12,1) = 204,2 мм.
Усилие пробивки и обрезки
P = 204,2 * 1,5 * 250 = 76,6 кН.
Усилие Pпр , которое должен обеспечить прижим, Н
Pпр = L * s * qпр,
где qпр = 15 Н/мм2 – удельное усилие прижима, тогда усилие прижима
Pпр = 1,5 * 15 * 204,2 = 4594,5Н = 4,6 кН.
При оснащении штампа выталкивающими устройствами, усилие выталкивания (противодавление)
Pпд = 0,1 * P .
Pпд = 0,1 * 76,6 = 7,7 kH.
Выбираем схему штампа, в которой прижим выполняет одновременно роль съемника, в этом случае учитываем максимальное усилие Pпд = 7,7 kH.
Усилие проталкивания детали или отхода через матрицу Pп = к пр * P . Усилие снятия детали или отхода с пуансона P сн = к сн * P , Принимаем коэффициенты k сн = 0,04 и kпр =0,03.
Усилие проталкивания Pп = 0,03 * 76,6 = 2,3 кН.
Усилие снятия Pсн = 0,04 * 76,6 = 3,1 кН.
Суммарное усилие штамповки
Pобщ = P + Pпр + Pпд + Pп + Pсн.
Pобщ = 76,6 + 7,7 + 4,6 + 2,3 + 3,1 = 94,3 кН.
Необходимое усилие пресса
Pпресса = 1,25 * Pобщ.
Pпресса= 1,25 * 94,3 = 118 кН.
В итоге получаем:
-усилие пресса для выполнения операции 10 Pпресса= 520 кН;
-усилие пресса для выполнения операции 20 Pпресса= 350 кН;
-усилие пресса для выполнения операции 30 Pпресса= 240 кН;
-усилие пресса для выполнения операции 40 Pпресса= 120 кН.
Необходимый ход пресса для выполнения указанных операций должен быть не менее 100 мм, а длина стола пресса должна быть не менее 400 мм.
На основании этих данных выбираем пресс однокривошипный открытый простого действия модели КИ 2128А. Пресс предназначен для выполнения операций холодной штамповки: вырубки, пробивки, гибки, неглубокой вытяжки. Прессы однокривошипные простого действия, открытые с механизированной регулировкой закрытой высоты, ненаклоняемые являются представителями гаммы однокривошипных прессов и относятся к типу быстроходных.
В конструкции прессов предусмотрено использование их в составе роботизированных
технологических комплексов и линий. |
|
|
|
|
||
Частично механизация процесса наладки пресса при смене штампа позволяет сократить |
||||||
вспомогательное время, повысить безопасность труда оператора и наладчика, улучшить |
||||||
условия труда путем сокращения доли ручного труда. |
|
|
||||
Режимы работы пресса: одиночный, автоматический и наладочные ходы. |
||||||
Привод односторонний, одноступенчатый. |
|
|
|
|||
Муфта– тормоз – жесткосблокированная, |
многодисковая, фрикционная с пневматическим |
|||||
включением, смонтирована на маховике. |
|
|
|
|
||
Ползун |
снабжен |
предохранителем |
от |
перегрузки |
и |
пневматическими |
уравновешивателями. |
|
|
|
|
|
|
Смазка прессов централизованная, импульсная, жидкая от насоса с электрическим |
||||||
приводом, индивидуальная. |
|
|
|
|
||
Управление прессом электропневматическое, двурукое от кнопок или педалей. |
||||||
Электроблокировка обеспечивает надежную работу и безопасное обслуживание пресса. |
||||||
Основные технические характеристики пресса: |
|
|
|
|||
номинальное усилие пресса, кН .................................................................................. |
|
|
|
630 |
||
ход ползуна регулируемый, мм |
|
|
|
|
||
наименьший ..................................................................................................................... |
|
|
|
|
10 |
|
наибольший.................................................................................................................... |
|
|
|
|
100 |
|
число ходов ползуна в минуту ..................................................................................... |
|
|
|
125 |
||
размеры стола, мм: |
|
|
|
|
|
|
слева – |
направо .............................................................................................................. |
|
|
|
|
710 |
спереди – назад .............................................................................................................. |
|
|
|
|
480 |
|
размеры отверстия в столе, мм |
|
|
|
|
||
слева – |
направо ............................................................................................................. |
|
|
|
|
360 |
спереди – назад ............................................................................................................. |
|
|
|
|
240 |
|
диаметр........................................................................................................................... |
|
|
|
|
300 |
|
расстояние от оси ползуна до станины (вылет), мм................................................... |
|
|
260 |
|||
наибольшее расстояние между столом и ползуном |
|
|
|
|||
в его нижнем положении при наибольшем ходе, мм................................................. |
|
|
340 |
|||
расстояние в свету между стойками станины, мм ..................................................... |
|
|
340 |
|||
регулировка расстояния между столом и ползуном, мм ............................................. |
|
80 |
||||
толщина подштамповой плиты, мм .............................................................................. |
|
|
|
85 |
||
размеры ползуна, мм |
|
|
|
|
|
|
слева – |
направо .............................................................................................................. |
|
|
|
|
370 |
спереди – назад .............................................................................................................. |
|
|
|
|
310 |
|
размеры отверстия в ползуне под хвостовик, мм |
|
|
|
|||
диаметр....................................................................................................................... |
|
|
|
|
50 Н9 |
|
глубина ............................................................................................................................. |
|
|
|
|
75 |
|
наибольший ход выталкивателя в ползуне, мм............................................................ |
|
|
50 |
|||
наибольшее число ходов ползуна в минуту в одиночном режиме,............................ 45 |
||||||
высота стола над уровнем пола, мм............................................................................. |
|
|
|
840 |
||
расход сжатого воздуха за одно включение пресса, л |
|
1,6 |
||||
габаритные размеры пресса, мм |
|
|
|
|
||
слева – |
направо ............................................................................................................ |
|
|
|
|
1500 |
продолжительность включения ........................................................................ |
|
|
|
ПВ = 40% |
||
форма исполнения..................................................................................................... |
|
|
|
|
М101 |
|
класс вибрации................................................................................................................ |
|
|
|
|
С1 |
|
7.3. РАЗРАБОТКА СБОРОЧНОГО ЧЕРТЕЖА ШТАМПА |
|
|
||||
Для выполнения первого перехода штамповки разработан штамп для формовки. Штамп |
||||||
состоит из нижней и верхней плит, запрессованных в верхнюю плиту направляющих |
||||||
колонок направляющих втулок запрессованных в нижнюю плиту. Нижний пакет штампа, |
который крепится к столу пресса, образован секциями матрицы вставленными в матрицедержатель. Секции матрицы и матрицедержатель при помощи винтов и штифтов крепится к нижней плите штампа. Для формовки ребер жесткости в секции матрицы врезаны ребра и закреплены при помощи винтов. Под секции матриц установлена пластина. Для повышения качества получаемого полуфабриката в нижний пакет штампа встроен выталкиватель, выполняющий одновременно и роль прижима. Выталкиватель через толкатели связан с пневмоподушкой, встроенной в стол пресс. Ход толкателей 52 мм. В выталкивателе встроены подпружиненные съемники с магнитами, предназначенные для подъема заготовки после штамповки над зеркалом матрицы на 8 мм и для удержания заготовки, установленной схватом манипулятора. Верхний пакет штампа при помощи хвостовика центрируется по отверстию в ползуне пресса и крепится к нему винтами. Верхний пакет образован пуансоном, который через подкладную плиту на винтах и штифтов крепится к верхней плите штампа. В пунсон встроены подпружиненные отлипатели и фиксаторы, предназначенные для базирования заготовки в штампе. Отлипатели совместно с выталкивателем обеспечивают сохранение ориентации заготовки после штамповки. Для облегчения наладки штампа и предохранения рабочих поверхностей штампа предусмотрены дистанцеры.
Для выполнения второго перехода разработан штамп для обрезки и пробивки. Штамп состоит из нижней и верхней плит, запрессованных в верхнюю плиту направляющих колонок, направляющих втулок, запрессованных в нижнюю плиту. Нижний пакет штампа, который крепится к столу пресса, образован секциями матрицы, установленными при помощи винтов и штифтов на нижней плите штампа. В нижнюю плиту встроены колонки и подъемники со встроенными магнитами, предназначенными для удержания заготовки после установки ее на рабочую позицию схватом манипулятора и подъема ее после пробивки. Ход колонок составляет 54 мм. Колонки и съемники связаны с пневмоподушкой, встроенной в стол пресса. В нижней плите выполнены пазы для удаления отходов и закрыты крышками. На нижней плите установлены лотки для удаления обрезанных отходов и установлены на кронштейнах штуцеры и пневмосдувы . Верхний пакет штампа при помощи хвостовика центрируется по отверстию в ползуне пресса и крепится к нему винтами. Верхний пакет образован пробивными пуансонами, обрезными пуансонами, которые через пунсонодержатель при помощи винтов и штифтов крепятся к верхней плите штампа. Между обрезными пуансонами с возможностью перемещения от буфера установлен съемник, ход которого ограничен скобами. Под головки пунсонов установлена подкладная плита. В пунсон встроены подпружиненные отлипатели и фиксаторы, предназначенные для базирования заготовки в штампе. Отлипатели совместно с подъемниками обеспечивают сохранение ориентации заготовки после штамповки. Для облегчения наладки штампа и предохранения рабочих поверхностей штампа предусмотрены дистанцеры и упоры.
Для выполнения третьего перехода разработан штамп для разрезки. Штамп состоит из нижней и верхней плит, запрессованных в верхнюю плиту направляющих колонок, направляющих втулок, запрессованных в нижнюю плиту. Нижний пакет штампа, который крепится к столу пресса, образован секциями матрицы, установленными при помощи винтов и штифтов в матрицедержателе, который при помощи винтов и штифтов установлен на нижней плите штампа. В секции матрицы встроены подпружиненные подъемники со встроенными магнитами, предназначенными для удержания заготовки после установки ее на рабочую позицию схватом манипулятора и подъема ее после пробивки. Ход подъемников составляет 7,8 мм. В нижней плите выполнены пазы для удаления отходов и закрыты крышками. На нижней плите установлен на кронштейне штуцер с гайкой и пневмосдув. Верхний пакет штампа при помощи хвостовика центрируется по отверстию в ползуне пресса и крепится к нему винтами. Верхний пакет образован пуансоном, который при помощи винтов поз и штифтов крепятся к верхней плите штампа. На пуансоне с возможностью перемещения от буфера установлен прижим,