
Основы производственного менеджмента_ в 2-х ч. . Ч.2 _для бакалавров , обучающихся по направлению подготовки 080200
.pdf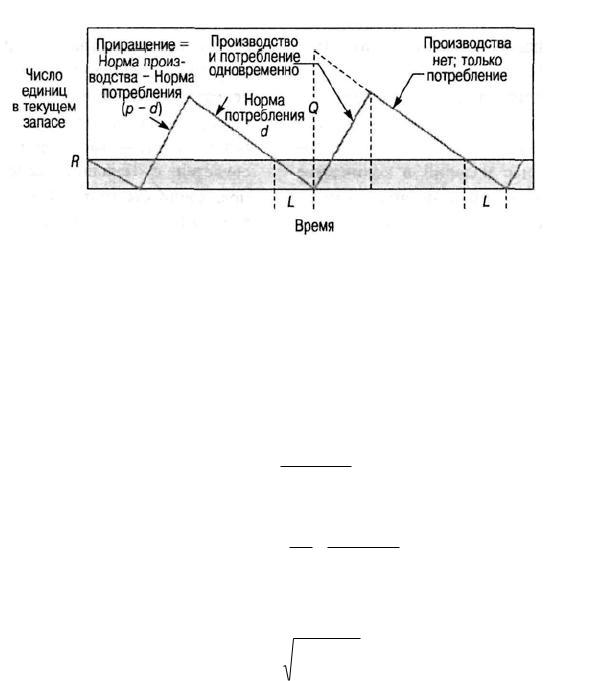
Рис. 8.5. Модель производственного запаса (задела)
Общий результат производства или пополнения запаса представляет величину заказа Q, т.е. Q = pt и t = Q/p.
Поэтому по формуле максимальный уровень запаса Z равен:
Z = (p – d) Q/p .
Отсюда годовые затраты хранения запаса Тн определяются по формуле:
T ( p d )HQ . |
|
H |
2 p |
|
Тогда с учетом (8.1) можно получить выражение для суммарных затрат:
TC DC DS ( p d )HQ . Q 2 p
собой
(8.6)
(8.7)
(8.8)
Выполняя дифференцирование по Q и приравнивая это выражение к нулю, получим, что оптимальный объем пополнения запасов (величина заказа) равен:
Qopt |
2DS p |
. |
(8.9) |
|
|
||||
H ( p d ) |
||||
|
|
|
Естественно, что производительность должна превышать дневную потребность. Рассмотрим пример на определение оптимального размера производства пар-
тии продукции.
Исходные предпосылки. Пусть продукт X – это типичное изделие в товарноматериальном запасе фирмы. Окончательная сборка этого изделия выполняется на ежедневно работающей сборочной линии. Один компонент изделия X (назовем его X1) изготавливается в другом подразделении. Выпуская компоненты X1, это подразделение обеспечивает производительность, составляющую 50 изделий в день, т.е. дневная норма производства р = 50 изделий. Потребность в компоненте X1 на сборочной
60
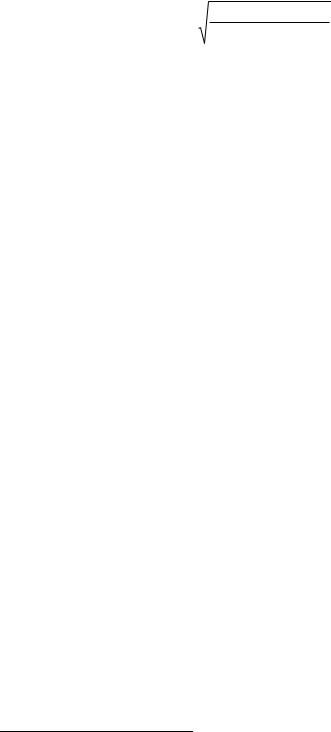
линии равна 20 штук в день, т.е. ежедневная норма потребления d = 20 изделий. Го-
довая потребность |
D = 5000 изделий. Затраты на пуско-наладочные работы |
S = 2200 руб. Годовые издержки хранения Н = 25 руб. на одно изделие. Время |
|
упреждения заказа |
L = 7 дней. |
Каким будет оптимальный размер производства партии для компонента X1? Решение. Оптимальный размер производства партии компонентов вычисляется в соответствии с выражением (8.9):
2 5000 2200 50
Q 541 ,6 шт. 542 шт.
opt |
25 (50 |
20) |
|
Точка очередного заказа вычисляется в соответствии с выражением (8.4):
R 20 7 140 шт.
Отсюда следует, что заказ на 542 штуки компонента X1 необходимо размещать в момент, когда текущий запас снижается до 140 штук. Учитывая, что норма производства компонента X1 составляет 50 изделий в день, выполнение этого заказа займет 10,8 дней и обеспечит двадцатисемидневный запас (542/20 = 27). В период, когда компонент X1 не выпускается (27 - 10,8 = 16,2 дней), подразделение может выполнять другие заказы.
8.6. Модель со ступенчатой (переменной) ценой
На практике может использоваться еще один тип моделей, получаемый расши-
рением параметров модели EOQ – модель со ступенчатой (переменной) ценой
(Price-Break Models)5. Другие названия этой модели – «модель с дисконтированием по размеру партии поставки», «однопродуктовая модель с разрывами цен».
В рассмотренных ранее моделях запасов предполагалось, что стоимость изделий остается постоянной при любом объеме заказа. На практике отпускная цена изделия часто зависит от объема заказа, причем зависимость цены от размера закупки обычно не прямо пропорциональная, а ступенчатая, т.е. чем больше размер заказа, тем меньше цена одного изделия у фирмы-поставщика, поскольку для увеличения объемов продаж многие фирмы предлагают своим покупателям скидки или дисконтирование по количеству. Количественный дисконт (скидка) – это снижение цены единицы (Р) в случае, когда товар покупается в достаточно больших количествах.
Суть модели со ступенчатой (переменной) ценой состоит в учете скидки (дисконта) с цены закупаемого ресурса при увеличении объема партии.
5 Adam E.E., Ebert J.R. Production and Operations Management: Concepts, Models and Behavior.- N. Y.: Prentice Hall Englewood Cliffs, 1990.
61
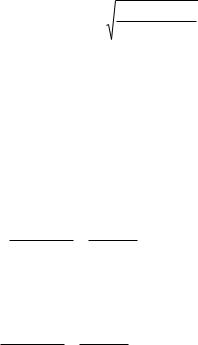
При использовании этой модели, оптимальный объем заказа определяется по минимуму общих затрат на создание запасов. Для этого нужно рассчитать экономичный размер заказа EOQ для каждого ценового диапазона. Для всех возможных значений объема заказа (все EOQ и размеры закупок Q, при которых происходит скачок цены) рассчитывают все элементы затрат и общие затраты на создание запасов. При этом нужно учитывать, что не все значения EOQ, определенные по формуле (8.3), имеют смысл, так как могут находиться в диапазонах цен, отличных от тех, по которым они рассчитаны. Затем методом прямого перебора отыскивается лучший вариант, минимизирующий суммарные затраты на поставку, хранение и покупку ресурса с учетом скидки, действующей на интервале.
Рассмотрим пример.
Исходые предпосылки. Предприятие-поставщик установило следующие цены на свои комплектующие изделия с учетом системы оптовых скидок: до 699 изделий – 150 руб. за одно изделие; от 700 до 1999 изделий – 142 руб. за одно изделие; 2000 изделий и более – 135 руб./изделие. Затраты на заказ у предприятия-потребителя изделий составляют 360 руб., текущие затраты на их хранение – 30 руб./год за изделие – практически не зависят от цены изделия, годовая потребность – 8000 изделий. Требуется определить размер оптимальной партии закупки изделий с учетом скидок.
Решение. Рассчитаем размер оптимальной партии поставки в соответствии с (8.3):
Q 2 8000 360 = 438 шт.
opt |
30 |
|
Оптимальная партия попадает в первый ценовой интервал. Это значит, что меньшие суммарные затраты могут быть только на границах – в начале второго или третьего ценовых интервалов. Проверим эти точки, для чего рассчитаем в них суммарные затраты на заказ, приобретение и хранение изделий.
Рассчитаем суммарные затраты по формуле (8.1). При закупке материала оптимальными партиями по 438 шт. затраты равны:
TC 8000 150 8000 360 438 30 = 1200000 + 5878 +6570 = 1212448 руб.
438 2
Суммарные затраты при закупке по 700 шт. по 142 руб., т.е. на нижней границе второго ценового интервала, составят
TC 8000 142 8000 360 700 30 = 1136000 + 4114 +10500 = 1150614 руб.
700 2
62
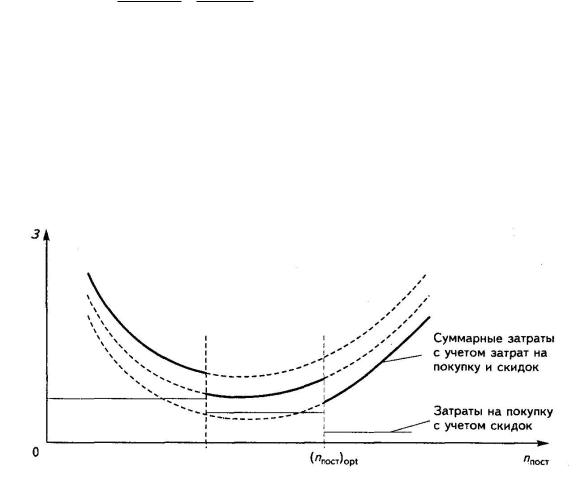
При закупке по 2000 шт. по 135 руб. (нижняя граница третьего интервала) затраты равны:
TC 8000 135 8000 360 2000 30 = 1080000 + 4114 +10500 = 1094614 (руб.)
2000 2
Таким образом, при закупках изделий оптимальной партией, расчет величины которой был выполнен по формуле (8.3), затраты оказываются выше, чем при закупках партиями большего размера, ввиду того, что скидки оказывают существенное влияние на общую сумму затрат. Расчет показывает, что из двух граничных точек следует выбрать минимальный размер партии на втором интервале,
т.е. Qopt = 2000 шт.
На рисунке 8.6 проиллюстрирована рассмотренная модель с тремя уровнями цены.
Рис. 8.6. Зависимости суммарных затрат на создание запасов в модели с тремя уровнями цены
Каждая из трех кривых, отображающих зависимости затрат от объема заказа, имеет свой диапазон реальных значений. В результате из трех кривых получается единственная (выделена жирной линией), которая соответствует всем допустимым значениям объема закупок.
Можно ввести еще одно уточнение в модель. Обычно затраты на хранение единицы ресурса зависят от его цены, т.е. h = ic, где i – коэффициент, показывающий отношение затрат на хранение единицы ресурса к его цене. Учитывая то, что цена в этой модели различна на разных интервалах, путем корректировки параметров модели можно получить более точное решение задачи.
Один из практических выводов для моделей со ступенчатыми ценами состоит в том, что ценовые скидки для крупных закупок часто делают экономически оправданным заказ изделий в количествах, превышающих оптимальную величину Qopt .
63

8.7. Управление запасами на основе «вытягивающих» и «выталкивающих» внутрипроизводственных логистических систем
Известны разные подходы к пополнению запасов, основанные на управлении материальными потоками в рамках внутрипроизводственных логистических систем. Выбор подхода зависит от условий работы организации, ее структуры и целей.
Концепция вытягивающей системы (Pull system)6. Эта система предполагает получение изделий с предыдущего участка по мере необходимости. Центральная система управления не задействована в обмене материальными потоками между различными участками предприятия, не устанавливает для них текущих производственных заданий. На промышленных предприятиях план имеет только линия окончательной сборки, откуда информация о необходимости производить требуемые детали поступает на предыдущие участки.
«Вытягивание» означает, что потребность в ресурсе, хранящемся на складе, считается случайной величиной, а складской запас между двумя смежными производственными звеньями играет роль автоматического регулятора движения между ними материального потока. По мере убывания ресурса со склада принятая модель управления запасом по установленному закону обеспечивает периодическое пополнение этого запаса.
Этот подход не требует централизованного вмешательства в выполнение складом своих регулирующих функций. Модель и относительно постоянные параметры управления закладываются на длительный срок операционным менеджментом, а текущие параметры управления могут корректироваться на основе прогнозирования величины спроса. Процедура «вытягивания» является основой одной из концепций оперативного планирования и управления производством, носящей название
«точно -в -срок».7
Вытягивающая система способствует сокращению производственных запасов при одновременном увеличении гибкости производства. Имеет она и недостатки: вытягивание часто искажает последовательность уровней в сети; каждое отдельное размещение осуществляется независимо от требований, определяющих другие размещения; осуществляемые размещения игнорируют интересы поставщика.
6Hallett D. (перевод. Казарина В.) Pull Scheduling Systems Overview. Pull Scheduling, New York, 2009. pp.1-25. http://pullscheduling.com/eBooks.aspx
7Метод «точно-в-срок» JIT (Just-in-time) изобретен в 1954 г. в корпорации «Тойота» на основе экономических ограничений, господствовавших тогда в Японии.
64

Альтернативой является выталкивающая система (Push system)8, в которой заявки поступают от мест, располагаемых в верхней части потока, но прежде они оцениваются поставщиками. Оценка включает рассмотрение не только потребности каждого отдельного места, делающего заявку, но и всей системы потребностей, а также величину запаса на складе поставщика, так как метод предполагает, что изготовление изделий начинается на одном конце производственной линии, проходит через последовательный ряд технологических операций и заканчивается обработкой на другом конце производственной цепочки.
Управление запасом, основанное на «выталкивании», требует точного знания параметров интенсивности материального потока, проходящего через склад, и предполагает централизованное регулирование его работы. Такая система объединяет информацию как от потребляющей позиции, так и подающей. Это позволяет улучшить распределение через сеть хранилищ или централизованный склад поставщика, но в этом случае на поставщика возлагаются функции контроля не только за состоянием запасов, но и за ходом распределения (потреблением запасов). Система используется преимущественно крупными компаниями, выступающими одновременно в роли и поставщика, и дистрибьютора своей продукции.
Материальный поток «выталкивается» получателю по команде, поступающей на передающее звено из центральной системы управления производством. При этом по завершении обработки на одном участке изделие передается на следующий независимо от того, готов этот участок принять изделие на обработку или нет. Каждый участок имеет производственный план. Однако создать «жесткий» технологический процесс, все параметры которого были бы наперед точно рассчитаны, невозможно. Поэтому на предприятиях всегда должен быть определенный производственный запас, который играет роль буфера и увеличивает гибкость системы. Толкающие системы являются основой систем MRP9, о которых сказано ниже.
8Фролов Е. Современные концепции управления в производственной логистике. Часть 1. «Выталкивающие» и «вытягивающие» системы планирования / САПР и графика. 2010, № 11. http://www.sapr.ru/article.aspx?id=21815&iid=996
9MRP (Material Requirement Planning) — система планирования потребностей в материалах, одна из наиболее популярных в мире логистических концепций. / Гаврилов Д. А. Управление производством на базе стандарта MRP II, 2-е изд. — СПб.: Питер, 2005, 416 с.
65

8.8. Зависимый и независимый спрос в управлении запасами
Повышению эффективности управления запасами способствуют следующие факторы:
широкое использование автоматизированных систем управления запасами;
развитие экономико-математического моделирования;
повышение надежности и оперативности получения данных с помощью современных информационных систем;
развитие методов прогнозирования;
рост квалификации персонала, занимающегося управлением запасами;
развитие корпоративных информационных систем (например, MRP II, ERP);
развитие систем управления качеством, что приводит к снижению потребности
взапасах для исправления бракованной продукции;
сокращение продолжительности цикла производства.
Модели запасов, которые были рассмотрены в разделе восемь выше, примени-
мы для условий так называемого независимого спроса (independent demand)10. Независимый спрос в теории управления запасами, планировании производства – это спрос на изделия, не входящие в комплект по отношению к какому-либо предмету более «высокого уровня», изготавливаемому или хранимому на данном предприятии (хозяйствующем субъекте). Например, спрос на такие товары, как телевизоры, обычно не зависит от спроса на такие товары, как радиоприемники. Предметы с независимым спросом – это, чаще всего, готовые изделия. Обычно готовый продукт продают (или отгружают) заказчику, в производстве какого-либо другого изделия он не участвует.
Но во многих случаях спрос на единицу запаса зависит от спроса на другие единицы, т.е. является зависимым. Зависимый спрос (dependent demand) в теории управления запасами - это спрос на некоторый вид продукции, если он может быть исчислен на основе потребности в изготовлении или пополнении запаса на продукцию более «высокого уровня». Например, известно, что для изготовления автомобиля требуется 4 колеса. Если автомобильная компания планирует выпускать 100 автомобилей в день, то ей понадобятся 400 колес и шин (плюс запасные). Необходимое количество колес и шин зависит от объема выпускаемой продукции. В то же время по-
требность в автомобилях независима от производителя.
Предметы, характеризующиеся зависимым спросом, как правило, представляют собой узлы и комплектующие, использующиеся в производстве конечного продукта.
10 Яндекс. Словари›Словари по экономике и финансам. Глоссарий.ру http://slovari.yandex.ru
66
Основой для планирования потребности в запасах в случае зависимого спроса является спрос на конечные изделия, и компьютер автоматически может определить потребность в каждом из требуемых компонентов. Обычно, когда спрос на различные единицы зависим, соотношения между ними известны и постоянны.
С концептуальной точки зрения, определение зависимой потребности представляет собой относительно простую вычислительную задачу. Необходимое количество изделий с зависимой потребностью можно вычислить довольно просто, основываясь на количестве этих изделий в каждом изделии более высокого уровня. В результате по мере продвижения все дальше вниз по технологической последовательности создания конечного продукта он обрастает новыми элементами зависимого спроса.
Для планирования запасов в условиях зависимого спроса применяются так называемые логистические концепции управления движением материальных ценностей [2]. Примером систем планирования зависимого спроса, которые используются в производственной сфере, является планирование производственных потребностей
(системы типа MRP), в распределительной сфере – планирование потребностей при распределении (системы типа DRP). Более развитые системы второго поколения MRPII/DRPII позволяют осуществлять планирование не только потребностей, но и ресурсов, необходимых для удовлетворения этих потребностей.
Названные системы планирования были разработаны в начале 60-х годов в США, в частности, в работах О.Уайта, который при развитии систем автоматизации промышленных предприятий предлагал рассматривать в комплексе производственные, снабженческие и сбытовые подразделения. В публикациях О.Уайта [6] были сформулированы алгоритмы планирования, сегодня известные как MRP — планиро-
вание потребностей в материалах — в конце 60-х годов, и MRP II — планирование ресурсов производства — в конце 70-х — начале 80-х гг.
Системы планирования материальных потребностей (Material Requirements
Planning – MRP) действуют почти во всех производственных фирмах – даже тех, которые считаются мелкими. Причина в том, что MRP предоставляет логичный, весьма доступный для понимания подход к проблеме определения количества деталей, компонентов и материалов, необходимых для производства каждого конечного продукта. С помощью MRP можно также составить календарный план, в котором будет точно указано, когда заказать или изготовить каждый из необходимых материалов, компонентов и деталей.
67

В первых MRP-системах планировались только материалы. Однако по мере наращивания вычислительной мощи компьютеров и расширения приложений увеличивался и диапазон возможностей MRP. Вскоре эти системы начали использоваться для учета не только материалов, но и ресурсов и получили название MRP II (Manufacturing Resource Planning – Планирование производственных ресурсов). Полная MRP-программа включала около 20 модулей, контролирующих работу всей системы: выдачу заказов, календарное планирование, управление запасами, финансы, бухгалтерский учет, кредиторскую задолженность и т.д. В наши дни MRP оказывает влияние на все производство и включает планирование поставок «точно-в-срок» (JIТ11, «канбан») и интегрированную производственную систему (Computer-Integrated Manufacturing – CIM)12.
Вопросы для самопроверки
1.Какие главные вопросы решаются в производственном менеджменте применительно к управлению запасами?
2.Каковы требования к эффективному управлению запасами?
3.Каковы цели создания запасов?
4.Назовите причины создания и поддержания материальных запасов.
5.В чем заключается различие между незавершенным производством, резервным запасом и сезонным запасом?
6.На какие основные виды подразделяются производственные запасы?
7.Назовите разновидности запасов в соответствии с выполняемыми ими функциями.
8.Что такое резервный запас и для чего он нужен?
9.Каковы функции запасов?
10.Какие виды расходов связаны с материальными запасами?
11.Что включают в себя затраты запаса и от чего зависит их величина?
12.Каким образом расходы влияют на величину запасов?
13.Какие существуют системы управления запасами?
14.Какова область применения различных систем управления запасами?
15.Кратко опишите метод АВС применительно к контролю запасов.
16.Каково назначение и содержание метода АВС-анализа применительно к запасам?
11«Точно вовремя» для рабочих. Группа разработчиков издательства Productivity Press. - М. :ИКСИ, 2007.
12APICS dictionary//edit. Cox J. F., etc. American Production and Inventory Control Society, 1992. P. 54.
68
17.Почему необходимо классифицировать элементы запаса на группы, как это делается в процессе АВС-анализа?
18.В чем суть применения циклов расчета?
19.В чем преимущества использования системы цикловых расчетов?
20.На какие основные вопросы должно давать ответ правило принятия решений по управлению запасами?
21.При каких условиях менеджер предприятия должен отдать предпочтение модели фиксированного объема, а не модели фиксированного периода?
22.Какие недостатки присущи использованию системы заказов с фиксированным периодом?
23.Какие модели запасов вам известны и какова область их применения?
24.Какие допущения принимаются для затрат на пуско-наладочные работы, затрат на размещение заказа и затрат на доставку?
25.Что означает «экономичный размер запаса»?
26.Какие выводы можно сделать на основе анализа формулы Уилсона?
27.Что такое «точка заказа» и как ее определить?
28.Как в развитие базовой модели EOQ учесть скорость пополнения запаса?
29.В какой модели учитывается и скорость потребления, и скорость пополнения запаса?
30.Как определить оптимальную величину заказа при использовании ступенчатых цен?
31.В чем заключается различие между независимым и зависимым спросом?
32.Дайте определение зависимому спросу.
33.Какие методы управления запасами применяются при зависимом спросе?
34.В чем отличие систем планирования MRP и MRP II?
Список литературы
1.Производственный менеджмент: Учебник / Под ред. В.А.Козловского. – М.:
ИНФРА-М, 2006. – 574 с.
2.Чейз Ричард Б., Джейкобз Ф.Роберт, Аквилано Николас Дж. Производственный и операционный менеджмент. – М.: Вильямс, 2007. – 1184 с.
3.Ильенкова С.Д., Бандурин А.В., Горбовцов Г.Я. Производственный менеджмент: Учебник для вузов. - М.: ЮНИТИ-ДАНА, 2001. – 583 с.
4.Козловский В.А., Кобзев В.В. Производственный и операционный менеджмент: Учебное пособие / Под общей ред. проф. В.В. Кобзева. - СПб.: Изд-во СПбГПУ,
2002. – 196 с.
69