
лекции ДМ
.pdfЛекция № 1
ВВЕДЕНИЕ
Машиностроение занимает важное место в современном обществе. Развитие машиностроения идёт по пути роста единичной мощности и производительности машин и агрегатов за счет увеличения скорости и КПД, а также повышения экономичности и улучшения технологичности в эксплуатации, на основе стандартизации деталей и узлов.
Задачей курса деталей машин является изложение научно обоснованных методов и норм расчёта и проектирования деталей общего назначения. Задачей проектирования машины является разработка документации, необходимой для ее изготовления, испытаний и эксплуатации. При этом качественные характеристики машины закладываются при её проектировании.
Понятие машины, узла, детали
Машиной называется устройство, содержащее согласованно движущиеся части и предназначенное для облегчения или замены труда человека и повышения его производительности.
Все разнообразие машин принято разделять на классы:
−технологические машины или машины-орудия труда (станки, оборудование предприятий и т. д.);
−транспортирующие машины (автомобили, самолеты и т. п.);
−логические машины (ЭВМ и т. п.);
−кибернетические машины (роботы и т. п.).
Большинство машин состоит из узлов.
Узлом называется законченная сборочная единица, составные части которой соединяются между собой только сборочными операциями (т.е. без изменения размеров и формы).
В свою очередь узлы состоят из отдельных деталей.
Деталью называется изделие, изготовленное из однородного по наименованию и марке материала без применения сборочных операций (т.е. без свинчивания, напрессовки и т. п.). Например, болт, вал и т. д.
Все детали условно разделяются на детали общего назначения и детали специального назначения.
Кдеталям общего назначения относятся детали, встречающиеся во всех или почти во всех машинах. Например, болты, гайки, валы, подшипники и т. п.
Кдеталям специального назначения относятся детали, встречающи-
еся только в машинах определенного типа. Например, диски и лопатки
1
газотурбинных двигателей, поршни и поршневые кольца двигателей внутреннего сгорания и т.п.
Курс «Детали машин» посвящен расчёту деталей общего назначения.
Классификация деталей общего назначения:
1.Соединительные детали и соединения (необходимы для соединения отдельных деталей в один механизм);
2.Детали для передачи вращательного движения (оси, муфты, валы);
3.Детали для поддержания в пространстве вращающихся частей машины (опоры, корпуса).
Принципы расчёта деталей машин по основным критериям работоспособности
При проектировании к машине в целом и к ее деталям предъявляются самые разнообразные требования. Основными из них являются: проч-
ность, жесткость, виброустойчивость, теплостойкость, износостойкость, экономичность, надежность, технологичность, безопасность в эксплуатации, эстетические требования, требования эргономики и мно-
гие другие. Часть требований противоречат друг другу. Например, требования прочности и минимального веса авиационных изделий. В этой связи для обеспечения выполнения всех требований необходимы многовариантные расчёты и оптимизация конструкций.
Требования, без обеспечения которых недопустима эксплуатация машины, называются критериями работоспособности. К ним относятся первые пять из перечисленных выше требований.
Обеспечение всей совокупности требований определяет надежность машины, ее эксплуатационные характеристики и конкурентоспособность.
Прочностью называется способность детали воспринимать заданные нагрузки без преждевременного разрушения или недопустимо больших остаточных деформаций. Это один из главных критериев. Расчёты на прочность проводят по номинальным допускаемым напряжениям, по допускаемым коэффициентам безопасности и по вероятности безотказной работы.
Расчёт на прочность состоит:
1.Предварительный расчёт (приближённые параметры);
2.Проверочный расчёт (определение прочности в опасных местах).
Условие прочности: σр < [σ], где σр – расчётное напряжение, [σ] – допускаемое напряжение.
Одним из наиболее общих требований является условие равнопрочности. Очевидно, что нет необходимости конструировать отдельные эле-
2
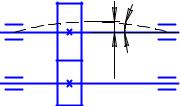
менты с излишними запасами несущей способности, которые не могут быть реализованы в связи с выходом из строя других элементов.
Жёсткость – это способность детали сопротивляться изменению формы под действием силы.
θ |
Проверочный расчёт состоит в определении упругих |
δ |
деформаций: |
∆ℓ ≤ [∆ℓ] – удлинение; ∆δ ≤ [∆δ] – прогиб; Рис. 1.1 θ ≤ [θ] – поворот при изгибе; φ ≤ [φ] – закручивание.
Виброустойчивость. Критерием виброустойчивости называется способность детали работать при высоких скоростях вращения без возникновения резонансных колебаний. Вибрация вызывает дополнительные переменные напряжения и приводит к усталостному разрушению деталей. Особенно опасными являются резонансные колебания. Условие отсутствия резонанса – несовпадение частот возбуждающих нагрузок с собственными частотами (λсобст ≠ λвозб). Это условие достигается конструктивными мероприятиями.
Теплостойкость. Любая работа вызывает тепловыделение. Это приводит к снижению несущей способности детали, снижению защитной способности масляного слоя, разделяющего трущиеся поверхности детали, изменению зазора в соединениях, изменению свойств поверхностей, снижению точности машин. Критерием теплостойкости называется способность детали сохранять эксплуатационные характеристики при повышенных температурах. Температурный расчет сводится к ограничению температуры t° ≤ [t°].
Износостойкость. Износ – процесс постепенного уменьшения размеров детали в результате трения. Как следствие износа – уменьшение прочности и увеличение динамических нагрузок, нарушение герметичности. До 80 % всех отказов в машинах происходит вследствие изнашивания их деталей.
Виды изнашивания: абразивный износ, износ при заедании, износ при коррозии, и т. д. Оценка сопротивлений по изнашиванию проводится
по условиям: р ≤ [р]; рV ≤ [рV]; tраб ≤ [tраб], где р – давление; рV – мощность трения; tраб – рабочая температура. Важнейшей характеристикой процесса изнашивания является интенсивность изнашивания. Интенсивность изнашивания зависит от свойств трущихся поверхностей, а также режима работы – нагрузки, скорости скольжения, условий смазывания.
Вкачестве критериев износостойкости принимаются:
р≤ [p] – при небольших скоростях скольжения;
pV ≤ [pV] – при повышенных скоростях скольжения и смешанном режиме трения;
3
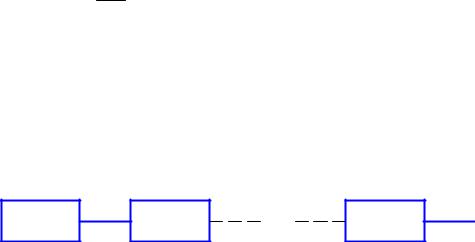
h ≥ [h] – при гидродинамическом режиме трения,
где р – давление; рV – мощность трения; h – толщина смазочного слоя. В наиболее ответственных деталях машин износостойкость обеспечивается надлежащей смазкой (антифрикция) и герметизацией областей
трения.
Надёжность и долговечность деталей машин
Надёжность – свойство выполнять свои функции, сохраняя свои характеристики. Она определяется безотказностью, долговечностью, ремонтопригодностью и сохранностью.
Безотказность – свойства изделий сохранять работоспособность в течение заданной наработки без вынужденных перерывов.
Долговечность – свойства изделий длительно сохранять работоспособность.
Ремонтопригодность – способность изделия к обнаружению и устранению отказов.
Сохраняемость – свойства изделия сохранять эксплуатационные показатели при хранении и транспортировке.
Имеем N0 изделий для испытаний в течении t часов. Пусть Nот – количество изделий, отказавших при испытании, а Nр – количество работа-
ющих изделий, тогда относительное число отказов Q(t) = Nот . Nр
Если N0 велико, то Q(t) – вероятность отказа.
Количественная характеристика надежности – вероятность безот-
казной работы P(t) = Np = N0 − Nот =1−Q(t). N0 N0
Если машина состоит из большого числа узлов, соединенных последовательно (рис. 1.2), а отказ одного приведёт к отказу машины, то по теории вероятности вероятность безотказной работы есть произведение вероятностей безотказной работы отдельных элементов:
n |
|
|
Pст(t) = ∏Pi (t) = P1 P2 ...Pi; |
|
|
1 |
|
|
P1(t) |
P2(t) |
Pi(t) |
Рис. 1.2
Пусть система состоит из параллельных деталей (рис. 1.3). Вероятность безотказной работы такой системы можно записать в виде
4
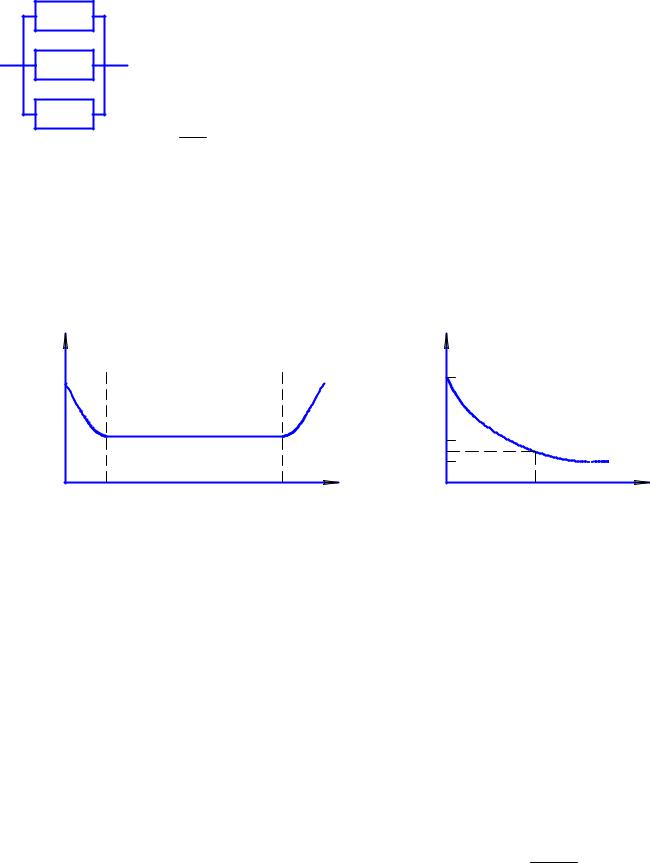
Pст(t) =1−(1− P1) (1− P2)....(1− Pi ) . |
|
|
|||
1 |
Таким образом, надёжность сложной системы всегда |
||||
меньше надёжности самого ненадёжного элемента. Чем |
|||||
2 |
больше элементов имеет система, тем меньше её надёж- |
||||
ность. |
|
|
|
||
i |
Важной характеристикой является интенсивность отказов: |
||||
λ = |
1 – интенсивность отказов, |
|
|||
Рис. 1.3 |
|
||||
|
tср |
|
|
|
|
где tср – средняя наработка за один отказ. |
|
|
|||
В период нормальной эксплуатации машины (область II рис. 1.4) от- |
|||||
казы от износа (область III) еще не проявляются и надежность характери- |
|||||
зуется внезапными отказами. Они носят случайный характер и определя- |
|||||
ются выражением |
P(t) = eλt , |
уменьшаясь с наработкой по экспоненци- |
|||
альному закону (рис. 1.5). |
|
Р |
|
||
λ |
|
|
|
|
|
I |
|
II |
III |
1 |
|
|
|
|
|
0,4 |
|
th |
|
t0 |
t |
0,2 |
t |
|
1/λ |
||||
|
Рис. 1.4 |
|
Рис. 1.5 |
|
|
Надёжность P(t) уменьшается с увеличением t. |
|
Основные пути повышения надёжности машин
1.Улучшение конструкции изделия.
2.Повышение качества производства.
3.Обоснованное уменьшение напряжённости детали.
4.Правильный выбор системы смазки.
5.Резервирование:
а) постоянно параллельное;
Qст(t) = Q1(t) Q2(t) Q3(t) , если Q1 = Q2 = Q3, то Qст(t) = Q13
б) резервирование замещением.
Если надежность переключателя 100 %, то Qст(t) = ∏Qni (!t) ;
Резервирование применяется тогда, когда исчерпаны другие средства, существенно повышает надежность системы, но усложняет её.
5

|
|
|
|
|
|
|
|
|
|
Лекция № 2 |
|
|
|
Выбор допускаемых напряжений |
|||||||||
при статических и переменных нагрузках |
|||||||||||
|
|
|
Все основные расчёты делятся на проектировочные и |
||||||||
d |
проверочные. Например, для стержня (рис. 2.1) |
||||||||||
d ≥ |
4 F |
|
|
– проектировочный расчет, |
|||||||
|
|
|
|||||||||
|
|
|
π[σ] |
|
|
|
|
|
|||
F |
σр = |
F |
|
= |
|
4 F |
≤[σ] – проверочный расчет. |
||||
Рис. 2.1 |
A |
πd2 |
|||||||||
|
|
|
|
|
|||||||
Допускаемые напряжение – это максимальные значения рабочих |
|||||||||||
напряжений, которые могут быть допущены при условии обеспечения |
|||||||||||
надёжности детали в процессе её работы: |
|||||||||||
[σ] = |
σlim D ; |
[τ] = |
|
τlim D ; |
|||||||
|
S |
|
|
|
|
|
S |
|
|
||
где σlim D (τlim D) – предельное нормальное (касательное) напряжение дета- |
|||||||||||
ли, S – коэффициент безопасности. |
|||||||||||
Предельные напряжения – это такие напряжения, при действии ко- |
|||||||||||
торых деталь выходит из строя: |
|||||||||||
σlim D = |
σlim εμ kп |
kp |
, |
|
|||||||
|
k |
|
|
|
|
|
|||||
|
|
|
|
|
|
|
|
|
|
||
где σlim – предельное напряжение для лабораторного образца; |
|||||||||||
εμ – масштабный фактор; |
|
|
|||||||||
kп – коэффициент качества поверхности; kр – коэффициент режима; |
|||||||||||
F |
|
|
|
k = |
|
σmax |
– коэффициент концентрации напряжения. |
||||
|
|
|
|
|
σH |
||||||
|
|
|
|
|
|
|
|
|
|||
|
|
н |
Фактические напряжения σmax в зоне концентрации у |
||||||||
max |
|
σ |
|||||||||
|
дна выточки (рис. 2.2) будут значительно больше, чем |
||||||||||
σ |
|
|
|
σH |
= F |
; где h и δ – ширина и толщина пластины. |
|||||
h |
|
|
|
||||||||
H |
|
|
|
|
|
|
|
δh |
|
||
|
|
|
|
|
|
|
С увеличением абсолютных размеров сечений |
||||
F |
|
|
детали в большей степени проявляется негативное |
||||||||
|
|
влияние неоднородности механических свойств ме- |
|||||||||
Рис. 2.2 |
|
|
талла и структурных дефектов, способствующих раз- |
||||||||
|
|
витию усталостных трещин. Наряду с этим увеличе- |
|||||||||
|
|
|
|
||||||||
ние размеров сечения снижает градиент напряжений и положительный |
|||||||||||
эффект возможного упрочняющего воздействия от обработки. Поэтому с |
|||||||||||
увеличением абсолютных размеров сечения деталей происходит сниже- |
|||||||||||
|
|
|
|
|
|
|
|
|
|
6 |
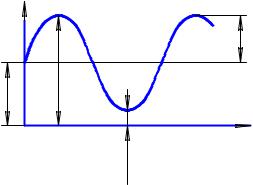
ние их прочности и механических характеристик, получаемых при статических и усталостных испытаниях, учитываемое коэффициентами влияния абсолютных размеров – масштабными факторами:
εσ = |
σ−1d |
; |
ετ = |
τ−1d |
; |
|
|
||||
|
σ−1 |
|
τ−1 |
σ-1d (τ-1d) – предел выносливости образца диаметра d;
σ-1 (τ-1) – предел выносливости пробного образца d = 7…10 мм.
При статических нагрузках состояние рабочих поверхностей оказывает незначительное влияние на их прочность. При циклических нагрузках разрушение деталей связано с развитием усталостных трещин, возникающих обычно в поверхностном слое. Развитию усталостных трещин способствуют возникшие в результате механической обработки микронеровности, являющиеся также концентраторами напряжений. Влияние их учитывается коэффициентами качества поверхности:
kпσ = |
σ−1d ; kпτ = |
τ−1d , |
|
σ−1 |
τ−1 |
где σ-1 и τ-1 – предел выносливости полированных образцов;
σ-1d и τ-1d – предел выносливости образцов с заданной обработкой.
Циклы нагружения
Детали машин обычно подвергаются действию напряжений, циклически меняющихся во времени. При этом возникают микроскопические трещины, приводящие к усталостной поломке деталей. В общем виде кривая, характеризующая изменение напряжений во времени, показана на (рис. 2.3). Большое значение для работы детали имеют верхние σmax и
нижние σmin пределы,
σ
ср |
max |
σ |
σ |
σ min
Рис. 2.3
σ a
t
σcp = σmax + σmin |
– среднее или условно |
2 |
|
постоянное напряжение, |
|
σa = σmax −σmin |
– амплитудное напряже- |
2 |
|
ние.
Важным параметром является коэффици-
ент асимметрии цикла R = σmin .
σmax
7

Втехнике встречается три основных случая нагружения:
1.Статическое нагружение (рис. 2.4).
σ |
|
Обозначение [I] – первый род нагрузки. |
||||||||||
|
σmax = σmin = σср; σа = 0; R = +1; |
|
||||||||||
|
|
|
||||||||||
|
|
Для хрупких материалов принимают |
||||||||||
|
|
σlim = σв ; τlim = τв , |
|
|
|
|
|
|||||
|
|
где σв и τв – пределы прочности при растя- |
||||||||||
Рис. 2.4 |
t |
жении и сдвиге. |
|
|
|
|
|
|||||
|
Для пластичных материалов применяют |
|||||||||||
|
|
σlim = σт ; τlim = τт , |
|
|
|
|
|
|||||
|
|
где σт и τт – пределы текучести. |
|
|||||||||
2. Отнулевой (пульсирующий цикл) (рис. 2.5). |
|
|
|
|
|
|||||||
σ |
|
Обозначение [II] – второй род нагрузки. |
||||||||||
|
|
σ |
|
|
= 0; σ |
≠ 0; σ |
cp |
= σ |
a |
= σmax ; R = 0. |
||
|
|
min |
|
max |
|
|
|
2 |
||||
|
|
|
|
|
|
|
|
|
|
|
|
|
|
|
σlim = σ0 – предел усталости при отнулевом |
||||||||||
|
t |
цикле. |
|
|
|
|
|
|
||||
Рис. 2.5 |
|
|
|
|
|
|
|
|
|
|
|
|
|
|
|
|
|
|
|
|
|
|
|
|
|
3. Знакопеременный симметричный цикл (рис. 2.6). |
|
|
|
|
||||||||
σ |
|
Обозначение [III] – третий род нагрузки. |
||||||||||
|
σmax = σmin |
= σa ; σср = 0. R = -1; |
||||||||||
|
|
|||||||||||
|
t |
σlim = σ-1 – предел усталости при симмет- |
||||||||||
|
ричном цикле. |
|
|
|
|
|
||||||
Рис. 2.6 |
|
σ |
0 |
= |
2σ−1 , где ψσ |
– коэффициент чув- |
||||||
|
|
|
|
1+ ψσ |
|
|
|
|
|
|
||
ствительности материала к асимметрии цикла. |
|
|
|
|
|
|||||||
Коэффициент ψσ = |
2σ−1 −σ0 |
зависит от материала и его термообра- |
||||||||||
|
σ0 |
|
|
|
|
|
|
|
|
|
|
ботки.
Для нормализованных и улучшенных сталей при σв > 800 МПа прини-
мают ψσ = 0,3…0,4 и ψτ = 0,4…0,5.
8
Определение коэффициента запаса прочности
Коэффициент запаса прочности (безопасности)
S = σlim >1, где σр – расчётное напряжение.
σp
В настоящее время применяют три метода определения необходимого запаса прочности. Один из них – табличный, при котором по заранее составленным таблицам определяются допускаемые напряжения в зависимости от материала детали, характера напряжений и цикла их изменения. Такие таблицы удобны в практической работе, но они должны готовиться для каждой отрасли машиностроения и учитывать применяемые в этой отрасли материалы и требования безопасности в эксплуатации.
Более прогрессивным является дифференциальный метод выбора допускаемого запаса или метод Одинга. В этом случае требуемый запас прочности определяется как произведение трех коэффициентов:
[S]=S1S2 S3.
Здесь: S1 = 1…1,5 – коэффициент, учитывающий точность расчетной схемы и достоверность значений нагрузок; S2 = 1,2…2,5 – коэффициент, учитывающий однородность механических свойств материалов и стабильность технологии; S3 = 1…1,5 – коэффициент, учитывающий требования безопасности.
Значения указанных коэффициентов устанавливаются на основе опыта эксплуатации машин в данной отрасли.
Наиболее современным является вероятностный метод выбора допускаемого запаса прочности. В этом случае учитывается, что механические свойства материалов и напряжения, возникающие в работающей детали, являются случайными величинами.
Каждая случайная величина характеризуется графиком плотности распределения значений. Характеристиками функции плотности распределения являются: медианное значение xm и среднее квадратичное отклонение случайной величины xmq .
При расчетах на прочность используется в основном нормальный закон распределения случайной величины (функция Лапласа).
При расчетах на прочность рассматриваются две случайные величины – напряжения σ, зависящие от действующих нагрузок, и предельные напряжения σlim, зависящие от разброса механических свойств материала.
В качестве запаса прочности принимается отношение:
S = σm lim .
σm
9
ПЕРЕДАЧИ.
Основные понятия. Классификация механических передач
Любая машина состоит из трёх основных элементов – двигателя, передаточного механизма, исполнительного механизма.
Устройства для передачи энергии и движения от одного агрегата другому или от одной части машины к другой называются передачами. Применение передач вызывается необходимостью согласования скоростей движения двигателей и исполнительных органов машины.
Передачи подразделяются: механические, электрические, пневматические, гидравлические, бомбинированные. В курсе «Детали машин» изучаются только механические передачи.
Введение передач обусловлено следующими причинами:
1.Требуемые скорости исполнительного механизма, как правило, не совпадают с оптимальными скоростями двигателя;
2.Скорость движения исполнительного механизма необходимо регулировать, что не всегда возможно сделать двигателем;
3.Двигатели обычно выполняются для равномерного вращательного движения, а исполнительные механизмы могут требовать иной вид движения.
Передачи по принципу работы разделяются:
−передачи трением с непосредственным контактом тел (фрикционные) и с гибкой связью (ременные),
−передачи зацеплением с непосредственным контактом (зубчатые и червячные) и с гибкой связью (цепные).
По характеру изменения скорости:
−понижающие (редуктора) и повышающие (мультипликаторы),
−регулируемые и нерегулируемые.
Регулируемые разделяются на:
−со ступенчатым регулированием,
−с бесступенчатым (плавным) регулированием.
Устройство, содержащее одну или несколько зубчатых или червячных передач, установленное в жёстком корпусе и предназначенное для понижения частоты вращения и увеличения крутящего момента, называ-
ется редуктором.
10