
metod416
.pdfкель, П – фосфор, С – кремний, Т – титан, Ф – ванадий, Х – хром, Ц – цирконий).
Цифра после дефиса указывает подгруппу плотности материала:
1– пористость 25-16 %, плотность γ = 6,0-6,6 г/см3;
2– пористость 15-10 %, γ = 6,7-7,1 г/см3;
3– пористость 9-2 %;
4– пористость не более 2 %.
В таблице 23.3 приведена классификация порошковых изделий и область их применения.
Таблица 23.3 – Классификация порошковых материалов, состав и области применения
Тип порошко- |
Некоторые |
Исходные |
|
|
марки |
Назначение |
|||
вого материала |
материалы |
|||
материалов |
|
|||
|
|
|
||
Антифрикци- |
ЖГр1,5; ЖГр2; |
Порошки железа и |
Подшипники |
|
онные |
ЖГр3; ЖГрLД3 |
графита, легирующие |
скольжения |
|
добавки |
||||
|
|
4 % Fe; 7 % С; |
Применяется |
|
Фрикционные |
МК5 |
8 % Pb; 9 % Sn; |
в тормозных |
|
|
|
0-2 % Ni,ост.Cu |
дисках |
|
Плотные |
СП70-2; |
Порошки железа, |
Детали |
|
конструкцион- |
||||
СП45Х2Н3-2 |
хрома, никеля и др. |
машин |
||
ные |
||||
|
|
|
||
Пористые |
1Х18Н9; |
Порошки нержавею- |
|
|
щей стали, бронзы, |
Фильтры |
|||
проницаемые |
Х20Н80 |
|||
сплавов титана и др. |
|
|||
|
|
|
||
|
|
Порошки вольфрама, |
Проволока, |
|
|
|
электроды |
||
Тугоплавкие |
W; Mо |
молибдена, ванадия, |
ламп, детали |
|
|
|
титана, тантала |
приборов, |
|
|
|
|
детали машин |
|
|
Магнитотвердые |
Порошки меди, |
Контакты, |
|
Электро- |
ММК-1 |
алюминия, железа, |
сердечники |
|
серебра, золота, |
||||
технические |
(12 % Аl; |
эл. машин, |
||
кремния, кобальта, |
||||
|
29 % Ni; ост.Fe) |
магниты |
||
|
окислов металлов |
|||
Твердые |
ВК6; ВК8; |
Карбиды вольфрама, |
Режущий |
|
карбиды титана, связ- |
инструмент, |
|||
сплавы |
Т15К6 |
|||
ка кобальт, никель |
волоки, буры. |
|||
|
|
|||
|
|
|
|
271

Среди перечисленных в таблице 23.3 материалов наибольшее распространение получили изделия из порошков на основе железа и меди. Некоторые из свойств приведены в таблице 23.4.
Таблица 23.4 - Составы и свойства некоторых порошковых конструкционных материалов
|
|
Хим.соста |
Предел |
Относи- |
|
|
|
|
|
|
в, % |
|
прочно- |
|
Ударная |
||
Обозна- |
|
|
|
сти при |
тельное |
Твердость |
вязкость, |
|
|
|
другие |
||||||
чение |
|
|
растяж. |
удли- |
НВ |
2 |
, |
|
материала |
|
угле- |
эле- |
нение, |
кДж/м |
|||
|
|
род |
менты |
σв, МПа |
% |
|
не менее |
|
|
|
|
не менее |
|
|
|
||
|
|
|
|
|
|
|
|
|
Материалы на основе железа |
|
|
|
|
||||
СП10-2 |
0,2 |
- |
120 |
8 |
70-80 |
200 |
|
|
СП10-4 |
0,2 |
- |
150 |
18 |
90-130 |
700 |
|
|
СП70-2 |
0,5-0,8 |
- |
200 |
8 |
70-90 |
300 |
|
|
СП70-4 |
0,5-0,6 |
- |
360 |
16 |
110-150 |
600 |
|
|
СП70Д3-2 |
0,3-0,6 |
2-3Cu |
260 |
3 |
80-100 |
200 |
|
|
СП70Д3-4 |
0,3-0,6 |
2-3Cu |
450 |
8 |
120-160 |
450 |
|
|
Материалы на основе меди |
|
|
|
|
||||
БрПО10-2 |
|
|
9,5- |
100 |
8 |
60-80 |
80 |
|
|
|
|
10,5 Sn |
|
|
|
|
|
БрПО10-3 |
|
|
9,5- |
200 |
12 |
80-90 |
120 |
|
|
|
|
10,5 Sn |
|
|
|
|
|
БрЛП68-2 |
|
|
31- |
80 |
8 |
40-50 |
150 |
|
|
|
|
33 Zn |
|
|
|
|
|
23.3 Порядок выполнения работы
23.3.1Спрессовать на гидравлическом прессе образцы из железного и медного порошков при удельных давлениях прессования 150, 300, 500, 700 МПа по 3 образца.
23.3.2Определить объёмную величину и массу упругого последействия. Посчитать их относительную плотность (θ, %) и пористость (П, %) образцов П = 100 – θ.
Относительная плотность определяется отношением плотности спрессованного или спеченного порошкового изделия к плотности компактного металла или сплава
θ= γ 100 ,
γk
272
где γ – плотность спрессованного или спеченного изделия.
γ k – плотность того же изделия в беспористом состоянии (плотность компактного).
23.3.3Построить диаграмму уплотняемости железного порошка.
23.3.4Произвести спекание образцов.
23.3.5Определить твердость спеченных образцов.
23.3.6Выводы.
23.4 Содержание отчёта
23.4.1Цель работы.
23.4.2Краткая характеристика основных процессов порошковой метал-
лургии.
23.4.3Описание экспериментальной работы с построением диаграммы уплотняемости, заполнить таблицу.
Характеристика порошка |
|
|
Усилие прессования, кН |
Давление прессования, МПа |
|
3 |
Величина |
, |
|
|
|
Высота прессовки, м |
Плотность прессовки, кг/м |
упругого |
|||||
|
2 |
бок 2 |
|||||||
|
последей- |
||||||||
Масса навескикг, |
Площадь сечения образца, F,м |
ствия, % |
Боковое давление, Р кН · м |
||||||
δh |
δД |
||||||||
|
|
||||||||
|
|
|
|
|
|
|
|
|
|
23.4.4 Выводы.
23.5 Контрольные вопросы
23.5.1Что такое порошковая металлургия?
23.5.2Каковы достоинства и недостатки порошковой металлургии? Какие вы знаете порошковые антифрикционные и фрикционные материалы?
23.5.3Какие бывают порошковые материалы?
23.5.4Маркировка порошковых конструкционных материалов.
23.5.5Что такое пористость?
23.5.6Как влияет пористость на механические свойства?
23.5.7В чем отличие в деформации компактной стали и порошкового
материала?
23.5.8Что такое упругое последействие?
23.5.9С чем связано боковое давление?
23.5.10Для чего применяют спекание?
23.5.11Какие дополнительные процессы проводят после спекания порошковых заготовок?
23.5.12Опишите свойства, технологию обработки и применения конструкционных порошковых материалов.
273

Приложение А
Характеристика групп сложности спечённых изделий
Группа |
Характеристика основных |
ли |
Дета- |
Вид спечённых |
||
слож- |
признаков деталей |
|
|
деталей |
||
ности |
|
|
|
|
|
|
1 |
Детали достаточно простой гео- |
Цилиндры, |
|
|
||
метрической формы с постоянным |
плоские |
|
|
|||
|
сечением по высоте |
крышки |
|
|
||
|
|
|
и другие |
|
|
|
|
|
|
|
|
||
|
Детали, форма которых аналогич- |
Втулки, |
|
|
||
I |
на деталям группы I, но имеющие |
кольца, |
|
|
||
одно или несколько отверстий или |
гайки |
|
|
|||
I |
пазов при отношении высоты де- |
|
|
|
|
|
|
тали к минимальной толщине |
|
|
|
|
|
|
стенки не более 10 |
|
|
|
|
|
I |
Детали группы II, но при отноше- |
То же |
|
|||
нии высоты детали к минималь- |
|
|||||
II |
ной толщине стенки более 10 |
|
|
|
|
|
|
|
|
|
|
||
I |
Детали группы III, но с перехода- |
Втулки |
|
|
||
ми по сечению (срезы, кольцевые |
с |
буртика- |
|
|||
V |
выемки, глухие отверстия и др.) |
ми, |
фланцы |
|
||
|
|
|
и другие |
|
|
|
|
|
|
|
|
|
|
V |
Детали группы IV, но при отно- |
|
Уд- |
|
|
|
|
шении высоты детали к мини- |
линённые |
|
|
||
|
мальной толщине стенки более 8 |
втулки |
с |
|
||
|
|
|
буртиками, |
|
||
|
|
|
рычаги |
|
|
|
|
|
|
|
|
||
V |
Детали с несколькими переходами |
Шестерни, |
|
|
||
I |
по высоте или сечению, а также |
звёздочки |
с |
|
||
|
ограниченные |
непараллельными |
буртиком, |
|
|
|
|
плоскостями |
или криволинейны- |
детали с |
|
|
|
|
ми поверхностями |
выступами |
|
|
||
|
|
|
|
|
|
|
274
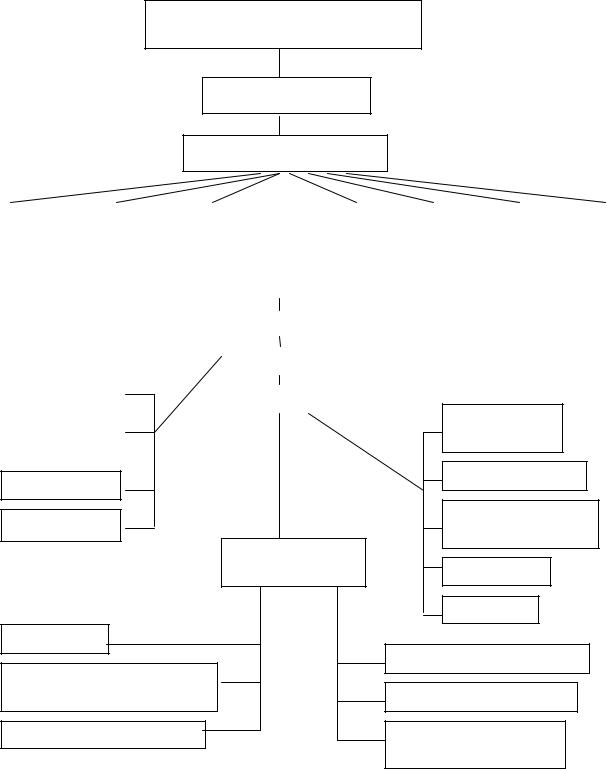
Приложение Б
Поэтапная технологическая схема изготовления порошковых конструкционных деталей путем прессования в закрытых пресс-формах.
Технология изготовления порошковых материалов и изделий
Входной контроль
Подготовка порошков
|
|
|
|
|
|
|
|
|
|
|
|
|
|
|
Восста- |
|
|
Отжиг |
|
Измель- |
|
|
|
Класси- |
|||||
новление |
|
|
|
чение |
|
|
|
фикация |
||||||
|
|
|
|
|
|
|
|
|||||||
|
|
|
|
|
|
|
|
|
|
|
|
|
|
|
|
|
|
|
|
|
|
|
|
|
|
|
|
||
|
|
|
|
|
|
|
|
Смешивание |
|
|
|
|||
|
|
|
|
|
|
|
|
|
|
|
||||
|
|
|
|
|
|
|
|
|
|
|
||||
|
|
|
|
|
|
|
|
Контроль смеси |
|
|||||
|
|
|
|
|
|
|
|
|
|
|
|
|||
|
|
|
|
|
|
|
|
|
|
|
|
|||
|
|
|
|
|
|
|
|
Прессование |
|
|
|
|||
|
Дозирование |
|
|
|
|
|
|
|||||||
|
|
|
|
|
|
|
|
|
|
|
||||
|
|
|
|
|
|
|
|
|
||||||
|
смеси |
|
|
|
|
Спекание |
|
|
|
|||||
|
|
|
|
|
|
|
|
|
|
|
|
|||
|
|
|
|
|
|
|
|
|
|
|
|
|||
|
|
|
|
|
|
|
|
|
|
|
||||
|
Уплотнение |
|
|
|
|
|
|
|
|
|
|
|||
|
|
|
|
|
|
|
|
|
|
|
|
|
|
|
Выпрессовка
Контроль
Дополнительная
обработка
Калибровка
Пропитка маслом, жидкими металлами, пластмассами
Гальваническая обработка
Про- |
|
Грану- |
|
Суш- |
тирка |
|
ляция |
|
ка |
|
|
|
|
|
Подготовка к спеканию
Загрузка впечь
Нагрев и изотермическая выдержка
Охлаждение
Контроль
Механическая обработка
Термическая обработка
Химико-термическая обработка
275
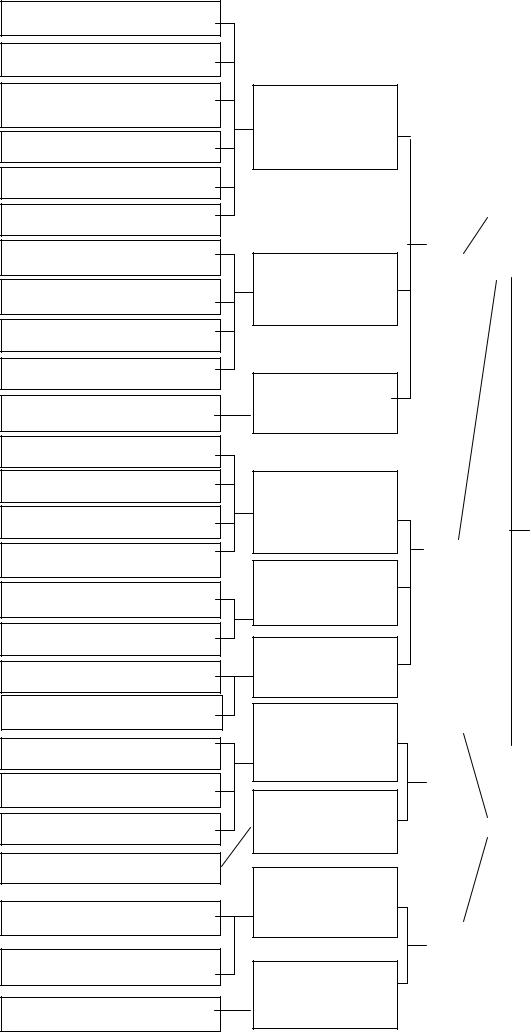
Прессование в закрытой пресс-форме
Пакетное прессование
Прессование в закрытой пресс-форме приложением вибраций
Изостатическое прессование
Центробежное формование
Электростатическое формование
Взрывное прессование
Ударное прессование
Электромагнитное прессование
Электрогидродинамическое прессование
Шликерное литье
Прессование в закрытых пресс-формах
Пакетное прессование
Изостатическое прессование
Центробежное формование
Штамповка
Взрывное прессование
Вибрационное прессование
Химическое формование
Прокатка
Экструзия
Прессование скошенным пуансоном
Ударное выдавливание
Прокатка
Экструзия
277
Ударное выдавливание
С постепенно возрастающим давлением
С мгновенно возрастающим давлением
Без приложения давления
Спостоянно или постепенно возрастающим давлением
Смгновенно возрастающим давлением
Без приложения давления
Спостепенно возрастающим давлением
Смгновенно возрастающим давлением
Спостепенно возрастающим давлением
Смгновенно возрастающим давлением
|
|
|
|
|
|
|
|
методы Технологические |
|
|
|
|
|
|
Прерывистое |
|
|
|
|
|
Холодное |
|
|
|
|
||||
|
|
|
|
|
|||||
|
|
|
|
|
|
|
|
конструкционных порошковых прессования |
|
|
|
|
|
|
|
порошковых )формование( Прессование назначения конструкционного изделий |
В Приложение |
||
|
Горячее |
|
|
|
|
||||
|
|
|
|
|
|
|
|||
|
|
|
|
|
|
|
|
|
|
|
Холодное |
|
|
|
деталей |
|
|||
|
|
|
Непрерывное |
|
|
|
|||
|
|
|
|
|
|
|
|
||
|
Горячее |
|
|
|
|
|
|
||
|
|
|
|
|
|
||||
|
|
|
|
|
|
|
|
|
|
24 Лабораторная работа № 24
Изучение технологии изготовления изделий из пластмасс методом прессования
24.1 Цель работы
Изучить один из наиболее распространенных в промышленности способов изготовления изделий из пластмасс, ознакомиться с конструкцией пресс-формы и особенностями ее эксплуатации.
24.2 Основные сведения
Пластические массы (пластмассы) - это материалы на основе природных или синтетических высокомолекулярных соединений (полимеров), способные под влиянием нагревания и давления формоваться в изделия сложной конфигурации, а затем устойчиво сохранять приданную форму. Пластмассы являются важнейшим конструкционным материалом современной техники. Изделия из пластмасс характеризуются малой плотностью, относительно высокой механической прочностью, устойчивостью к атмосферным воздействиям, стойкостью к агрессивным средам, к резким сменам температур, высокими диэлектрическими и хорошими теплоизоляционными свойствами.
Взависимости от поведения при нагревании различают термопластичные (термопласты) и термореактивные пластмассы (реактопласты).
Термопласты (полиэтилен, капрон, винипласт, полистирол, фторопласт, органическое стекло и др.) при нагревании размягчаются, переходят в вязкотекучее состояние, а при охлаждении вновь затвердевают.
Переход термопластов в вязкотекучее состояние и обратно может происходить неоднократно без изменения их химического состава, что и определяет выбор способа переработки термопластов.
Реактопласты (текстолиты, фенопласты, пресс-материалы, стеклопластики и др.) при нагревании легко переходят в вязкотекучее состояние, но с увеличением продолжительности действия повышенных температур в результате химической реакции переходят в твердое состояние. При повторном нагреве отвердевшие реактопласты теряют способность перехода в вязкотекучее состояние.
Взависимости от числа компонентов все пластмассы подразделяют на простые и композиционные. Простые (полиэтилен, полистирол, полиуретан, фторопласт и др.) состоят из одного компонента - синтетической смолы; композиционные (фенопласты, аминопласты и др.) – из нескольких составляющих, каждая из которых выполняет определенную функциональную роль. Так, смола является связующим звеном для других составляющих. Содержание связующего в пластмассах достигает 30 – 70 %. К другим состав-
278
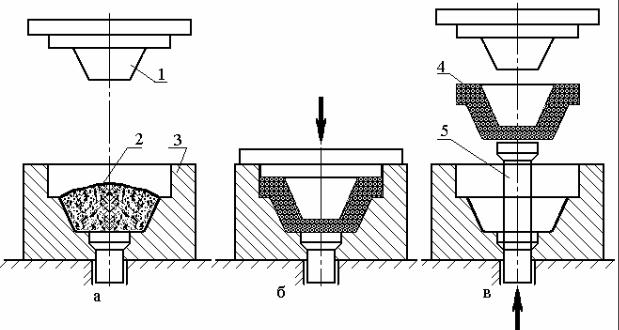
ляющим относятся наполнители (ткань, бумага, графит, асбест и т.д.); пластификаторы (дибутилфталат, камфара, касторовое масло и т.д.); катализаторы (известь, магнезия, уротропин и т.д.); смазывающие вещества (стеарин, олеиновая кислота и др.); красители (сурик, муминигрозин и др.).
Пластмассы перерабатывают в детали, как в твердом состоянии (разделительная штамповка, обработка резанием, сварка, склеивание), так и в высокоэластичном (пневмо- и вакуумформовка, штамповка и др.) и вязкотекучем состояниях.
При переработке в высокоэластичном и вязкотекучем состоянии необходимо совместное действие тепла и давления. Наибольшее распространение получили такие методы переработки пластмасс в вязкотекучем состоянии, как прессование, литье под давлением, экструзия и др. Различают следующие технологические схемы прессования: прямое (компрессионное), литьевое, пакетное (многоярусное) и профильное прессование.
Прямое (компрессионное) прессование заключается в непосредственном приложении к пресс-материалу, находящемуся в нагретой пресс-форме, внешнего давления (рисунок 24.1).
а – загрузка сырья; б – прессование; в – извлечение детали 1 – пуансон; 2 – сырьё; 3 – матрица пресс-формы; 4 – деталь; 5 – выталкиватель;
Рисунок 24.1 – Схема прямого (компрессионного) прессования
При этой схеме прессования сырьё 2 закладывается в полость матрицы пресс-формы 3, при замыкании которой усилие от пресса передается материалу через пуансон 1. Под действием давления и тепла материал переходит
279
ввязкотекучее состояние и заполняет формообразующую полость прессформы. В процессе выдержки при температуре отверждения отформованный материал переходит в твердое неплавкое состояние, после чего пресс-форма раскрывается и деталь 4 извлекается из нее с помощью выталкивателя 5.
Время выдержки под прессом зависит от вида сырья и толщины изготовляемого изделия и выбирают из расчета 100 – 200 с на 1 мм толщины стенки. Это время, идущее в основном на подогрев материала для перехода его в вязкотекучее состояние, может быть на 40 – 60 % сокращено путем предварительного подогрева пресс-материала до 90 – 120 °С, например, в термошкафе. Отверждение является результатом реакции поликонденсации реактопласта, сопровождающейся выделением летучих составляющих полимера и паров влаги. Поэтому для удаления газов выполняют операцию подпрессовки, т.е. после определенной выдержки пресс переключают на обратный ход, обеспечивая подъем пуансона на 5 - 10 мм и выдержку его в таком положении в течение 2 - 3 секунд. После этого пресс-форма снова смыкается и процесс формообразования завершается. При изготовлении крупных толстостенных деталей из материалов с повышенной влажностью подпрессовку осуществляют дважды. Технологические параметры прессования (давление, температура нагрева, время выдержки и др.) зависят от вида перерабатываемого материала.
Для переработки реактопластов рекомендуется задавать давление прессования p = 15 - 80 МПа, а температуру пресс-формы t = 135 – 175 °С в зависимости от рецептуры перерабатываемого материала и геометрии прессуемого изделия. Схема прямого (компрессионного) прессования применяется для изготовления изделий несложной конфигурации из реактопластов с волокнистым или порошковым наполнителем, а также из некоторых термопластов, дозирование загружаемого в пресс-форму сырья осуществляется по объему, массе или поштучно (числом таблеток).
Для изготовления деталей сложной конфигурации с тонкими стенками, углублениями и глубокими отверстиями, оформляемыми с помощью стержней, вставок и знаков, применяют схему литьевого прессования. Эта схема позволяет устанавливать тонкую и сложную арматуру, остающуюся в теле изделия. В отличие от прямого прессования литьевое имеет более высокую производительность.
Основным отличием схемы литьевого прессования (рисунок 24.2) является то, что сырье загружается не в формообразующую часть пресс-формы, а
вотдельную литьевую камеру 2, в которой под действием теплоты становится вязкотекучим и с помощью литьевого плунжера 1 через литниковый канал 3 выдавливается в оформляющую кольцевую полость 4 пресс-формы, образованную стержнем 5 и её цилиндрической поверхностью. По завершении процесса отверждения готовая деталь (не имеющая облоя) извлекается из пресс-формы.
Недостатком литьевого прессования является существенные (до 40 %) отходы материала, неизбежно остающиеся в литьевой камере.
280