
книги / Эксплуатация оборудования для бурения скважин и нефтегазодобычи
..pdfГлава 14
ЭКСПЛУАТАЦИЯ ПОДЪЕМНОГО КОМПЛЕКСА БУРОВОЙ УСТАНОВКИ
14.1.ТЕХНИЧЕСКОЕ ОБСЛУЖИВАНИЕ
ИРЕМОНТ БУРОВОЙ ЛЕБЕДКИ
Техническое обслуживание буровой лебедки (рис. 14.1) начинают с предпусковой подготовки. На первом этапе производят проверку правильности монтажа и сборки основных узлов. Центровку валов и их соосность проверяют с помощью специальных приспособлений. Производят контроль правильно сти монтажа вращающихся деталей, соединенных с элементами других агрегатов. Цепные колеса и шкивы, работающие в паре, должны быть установлены в одной плоскости.
Правильно смонтированные узлы и отдельные детали лебедки должны быть закреплены соответствующими крепежными дета лями. Особое внимание должно быть обращено на надежное кре пление талевого каната к барабану лебедки. Болты необходимо затянуть до отказа и законтрить. На барабане должно быть 8 - 10 витков талевого каната при нахождении крюка на полу бу ровой.
Перед пуском в работу буровой лебедки производят регули ровку ленточного тормоза (рис. 14.2). Проверяют также надеж ность крепления колодок к ленте тормоза.
Тормозные колодки должны равномерно прилегать к тормоз ным шкивам. В заторможенном состоянии рукоятка управления лебедкой должна отстоять от пола буровой на 80-90 см. Ход ру коятки при торможении от вертикали не должен превышать 60° Состояние гидротормоза определяется герметичностью всех со единений. Герметичность шинно-пневматических муфт и их со единений контролируют при подаче сжатого воздуха в пневмати ческую систему управления.
Пуск в работу буровой лебедки без надежно закрепленных защитных кожухов не допускается.
В процессе эксплуатации буровой лебедки необходимо систе матически контролировать зазор между колодками и тормозным шкивом. При отсутствии воздуха в баллоне пневмомуфты зазор должен быть равномерный в пределах 2-3 мм.
Максимально допустимый износ колодок не должен превы шать 12 мм. При превышении допустимого износа колодки
1
9 |
2 |
3 |
4 |
5 |
6 |
7 |
8 |
Рис. 14.1. Лебедка буровая типа ЛБУ:
1 - рама; 2 - регулятор подачи долота; 3, 10 - механизм включения; 4 - тихо ходный вал; 5 ~ механизм переключения скоростей; 6 - механизм включения зубчатой муфты; 7 - коробка передач; 8 - насосный агрегат системы смазки; 9 - электромагнитный тормоз; 11, 14 - быстроходная и тихоходная передачи; 12 - подъемный вал; 13 ~ узлы ленточного тормоза; 15 ~ командоаппарат с датчиком глубины; 16 - воздухопровод
должны быть заменены на новые. Регулировку зазоров между колодками и тормозными шкивами производят с помощью регу лировочных тяг тормозных лент.
В ходе эксплуатации буровой лебедки необходимо регулярно проверять цепные передачи. Вытянутые цепи укорачивают за счет удаления звеньев цепи. Удлинение цепи обнаруживается по резким ударам и рывкам при работе передачи. Допустимое про висание цепи составляет 0,02 от межцентрового расстояния меж ду звездочками.
В ходе спускоподъемных операций с включенным гидродина-
482
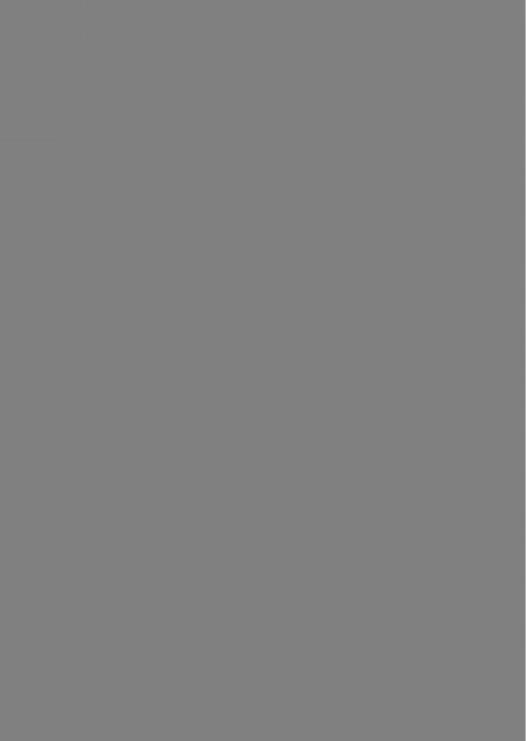
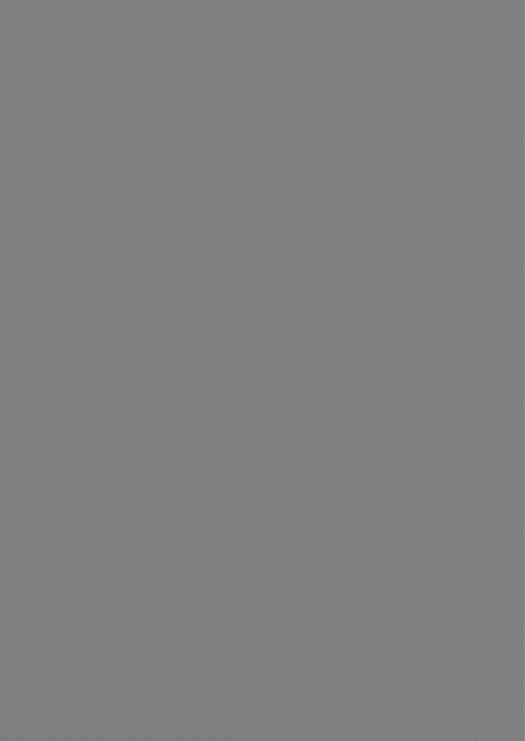
жение исправного крюка вниз свидетельствует о том, что колод ки тормоза не отходят от тормозных шкивов или задевают о ре борды шкивов.
При эксплуатации буровой лебедки регулярно смазывают трущиеся поверхности согласно инструкции по эксплуатации. Приемку и сдачу каждой вахты бригадой производят путем внешнего осмотра всех узлов и креплений. Не реже одного раза в неделю проверяют все сопряжения на износ и производят их ре гулировку. Выявленные дефекты устраняют до начала работы и делают запись в вахтовом журнале.
Замене при текущем ремонте буровой лебедки в полевых ус ловиях подлежат быстроизнашивающие узлы и детали. Наибо лее интенсивному износу подвержены тормозные колодки и шкивы барабана, антифрикционные втулки, шинно-пневмати ческие муфты. Достаточно часто требуют ремонта цепные колеса, подшипники, кулачковые муфты. При ремонте лебедки должны выполняться все требования, предъявляемые к ответственным подъемным механизмам. Детали, устанавливаемые взамен вы шедших из строя, должны быть изготовлены в соответствии с техническими условиями завода-изготовителя. При текущем ре монте производят частичную разборку лебедки.
Буровую лебедку типа ЛБУ разбирают в следующей последо вательности. Снимают верхние, нижние и боковые щиты лебед ки; разбирают систему воздухопровода и пульт управления ле бедки; разбирают и снимают тормозную систему; отвинчивают болты крепления подшипников подъемного вала специальными торцовыми ключами длиной 1000 мм. Чтобы безопаснее снять вал с рамы лебедки, оставляют по одному болту в каждом под шипнике. Затем при помощи подъемного крана вал зацепляют штропом, дают натяжку с таким расчетом, чтобы вал был прижат к раме лебедки, и только после этого отвинчивают последние болты, и вал снимают с рамы. Перед снятием валов необходимо предварительно снять цепи. После снятия валов и тормозной системы приступают к их разборке. Для разборки валы укла дывают на козлы. Демонтаж подшипников, муфт и цепных ко лес с валов производят известными слесарно-механическими ме тодами, используя съемники и прессы.
Тормозные шкивы снимают с бочки барабана одновременны ми ударами кувалды с двух сторон, затем при помощи пресса выпрессовывают из барабана вал.
Биение валов определяют по рейсмусу. Предельно допусти мый прогиб валов 0,3 мм на 1 м длины и 0,8-0,9 мм на всю дли ну вала. По фактическому размеру посадочных поверхностей ва ла подбирают подшипник с тем, чтобы обеспечить заданный на-
тяг. В случае износа посадочную поверхность наплавляют или металлизируют, а затем протачивают для получения первона чальных размеров. Новые подшипники запрессовывают с их предварительным нагревом до 90 °С. Изношенные подшипники гидродинамического тормоза заменяют аналогично подшипникам лебедки. Большие радиальные люфты свободно сидящих на ва лах лебедки цепных колес являются результатом износа под шипников скольжения. После демонтажа цепных колес втулки выпрессовывают. Новые втулки подшипников скольжения за прессовывают с предварительным нагревом колеса до 350 °С. Стопорение втулок осуществляют двумя-тремя винтами, затем новые втулки пришабривают по валу. Рекомендуется изношен ные цепные колеса заменять новыми. В этом случае ремонт со стоит в демонтаже изношенных цепных колес с помощью прес сов или специальных приспособлений. Новое колесо сажают на вал, предварительно нагревая его до 300 °С. При малых износах зубьев их восстанавливают наплавкой с последующей механиче ской обработкой.
Износ бандажей, кроме уменьшения толщины стенок обода, приводит к образованию на их рабочей поверхности кольцевых канавок, волнистости, поперечных трещин, выкрашиваний и дру гих дефектов. Ремонт тормозных шкивов заключается в удалении указанных дефектов путем обточки бандажей непосредственно на лебедке при помощи суппорта токарного станка, укрепленного на раме лебедки. Толщина тормозного шкива должна быть не менее 50 % от номинальной. Отдельные раковины и выкрашивания устраняют наплавкой с последующей зачисткой сварного шва. Иногда бандажи протачивают прямо на буровой; если это невоз можно, их заменяют. Для этого после снятия щитов ограждения ходовой конец каната отсоединяют от барабана лебедки, пропус кают через ролик, установленный на основании вышки, и при крепляют к трактору. При помощи штропа и талевой системы вал поднимают после отвинчивания гаек и снятия болтов под шипников. Для безопасной работы во время отвинчивания гаек, а также для плавной подачи вала к центру буровой используют второй трактор с тросом, пропущенным через промежуточный вал и прикрепленным к подъемному валу.
Подъемный вал укладывают на брусья, уложенные на ротор. Для быстрой замены изношенные бандажи срезают при помощи газовой резки.
Капитальный ремонт предусматривает полное восстановление ресурса буровой лебедки, поэтому качество ремонта должно со ответствовать техническим требованиям отраслевых нормалей. После установки валов на раму лебедки необходимо проверить
486
их параллельность и расстояние между ними, а также совпадение плоскостей сопряженных цепных колес. При этом допускаются следующие отклонения: непараллельность валов - не более 2 мм; торцовое и радиальное биения цепных колес должно быть не более 0,5 мм.
Подъемный вал после установки на него барабана и тормоз ных шкивов проходит статическую балансировку. В случае дис баланса к торцу барабана приваривают стальные планки расчет ной массы.
При сборке подшипника на валу необходимо, чтобы торцовый зазор по наружному кольцу был в пределах 0,2-0,3 мм. Зазор регулируется прокладками под крышки корпуса подшипника. Осевой люфт звездочек, установленных на валу на подшипниках, должен быть не более 1,5-2,5 мм.
Долговечность подшипников гидродинамического тормоза за висит от надежности уплотнения. Если из дренажного отверстия в крышке происходит значительная утечка жидкости, то необхо димо с помощью отжимных болтов выпрессовать стаканы из крышек и изношенные манжеты заменить новыми. Повышенное осевое перемещение ротора гидродинамического тормоза свиде тельствует об износе текстолитовых шайб, которые должны быть заменены новыми.
При установке стаканов на место нужно следить за тем, чтобы внутренние кромки колец не погнулись. Гидродинамический тормоз разбирается в следующей последовательности. Снимают кулачковую муфту, крышки, затем из крышек корпуса гидроди намического тормоза извлекают стаканы. После этого снимают боковые крышки корпуса статора гидродинамического тормоза и извлекают из корпуса ротор. Затем с помощью винтового съем ника снимают с вала внутренние обоймы роликовых подшипни ков. Далее с помощью гидравлического пресса снимают с вала колесо, для чего ввинчивают тяги в резьбовые отверстия ступи цы колеса. Если при осмотре внутренней полости гидродинами ческого тормоза будут обнаружены трещины в наклонных реб рах, то такие ребра в зависимости от размера трещин необходимо удалить частично или полностью. Заваривать или крепить ребра внутри тормоза не разрешается во избежание разрушения во время работы.
Ротор гидродинамического тормоза после сборки должен быть статически отбалансирован. При сборке внутреннюю обойму ро ликоподшипника устанавливают с предварительным подогревом ее в масле до 80-100 °С. Наружная обойма должна входить в расточку стакана. Зазор 2-2,5 мм между лопатками ротора и торцом крышки получают с помощью регулировочных прокла
док. Зазор между ступицей ротора и текстолитовой шайбой дол жен быть равен 1,0-1,5 мм.
Особое внимание при сборке необходимо обращать на взаим ное расположение ребер ротора и крышек статора. Неправиль ная установка ротора на вал или перемена местами крышек при ведут к быстрому нарушению работоспособности гидродинамиче ского тормоза. Собранный гидродинамический тормоз опрессовывают водой под давлением 0,2-0,3 МПа в течение 5 мин. При этом допускается просачивание через сальник отдельных капель.
14.2.ТЕХНИЧЕСКОЕ ОБСЛУЖИВАНИЕ
ИРЕМОНТ ТАЛЕВОЙ СИСТЕМЫ
Талевая система включает кронблок, талевый блок,
крюк.
Безопасная и безаварийная работа по спуску и подъему бу рильных или обсадных труб обеспечивается правильным и сис тематическим уходом за всеми элементами подъемного комплек са буровой установки. Поэтому техническое обслуживание тале вой системы требует особого и повседневного внимания.
Пуск в работу талевой системы необходимо производить по сле проверки нормальной работы всех подвижных элементов та левого и кронблока. Канатные шкивы должны вращаться плавно, без заеданий и заклинивания на полном обороте. Для этого в подшипниках и шарнирах должна быть смазка. Крюк в стакане должен проворачиваться полностью без заеданий. Проверке под вергают защелки, обеспечивающие надежное крепление штропов элеватора и серьги вертлюга.
Перед пуском в работу производят проверку крепления бол товых соединений в талевом и кронблоке. Кожухи при этом должны легко откидываться и закрепляться. Все замечания должны быть устранены перед началом работы.
При наружном осмотре проверяют состояние щек, штропов и других деталей. В случае обнаружения вмятин, трещин неис правные детали талевой системы должны быть заменены. В про цессе эксплуатации талевой системы перед началом каждой вах ты необходимо проверять надежность крепления всех узлов. Все шкивы должны вращаться свободно без заклиниваний и шума. Канатные шкивы не должны задевать своими ребордами за ко жух. Износ канатных шкивов не должен превышать установлен ной нормы.
Подшипники шкивов и шарнирные соединения должны сма зываться в соответствии с инструкцией по эксплуатации. Нагрев
подшипников не должен превышать 70 °С. При загрязнении ка натов необходимо промыть их керосином с помощью ручного насоса.
При выявлении дефектов в талевой системе следует прекра тить работу и произвести ремонт или замену неисправных дета лей. Производить работы при неисправной талевой системы за прещается.
В процессе работы могут быть замечены неисправности, свя занные с шумом в подшипниках шкива; при этом могут греться подшипники. Это, как правило, связано с большим износом подшипников или отсутствием смазки.
Заедание защелок крюка обычно связано с поломками пру жин. В этом случае необходимо заменить пружину или весь фиксатор.
Талевый канат воспринимает статические и динамические на грузки в процессе спускоподъемных операций. Он подвержен действию нагрузок непосредственно и в процессе бурения. По этому износ каната происходит в результате действия различных факторов.
Ходовой конец каната изнашивается в результате трения ме жу витками барабана при намотке на барабан лебедки и сматы вании. Трение также возникает при контакте каната с ребордами барабана при переходе с одного ряда канавки на другой и с ка навками роликов талевого блока и кронблока. При этом трение усугубляется в результате попадания песка на талевый канат и загрязнения смазки. При прорезании верхними витками на мотки нижних витков происходит скоблящее действие прядей по отношению друг к другу.
Усталостное разрушение каната происходит в результате пе региба на роликах и обратного перегиба на барабане лебедки при спускоподъемных операциях. На неподвижном конце усталостное разрушение происходит в процессе бурения из-за переменных нагрузок и вибрации каната.
Степень износа стального каната определяется числом обор ванных проволок на шаге свивки. Отбраковке подлежит канат, в котором оборвано 10 % от общего числа проволок. Ввиду того, что канат изнашивается неравномерно по длине, производится его отбраковка по интервалам путем перепуска на устройстве для закрепления неподвижного конца. Для этого должен быть резерв длины каната на бухте за устройством для крепления. Для сква жины глубиной 2000 м необходимо иметь канат длиной 12001500 м.
Первый перепуск установленного нового каната производится после отработки его ходового конца до износа 20-25 %, а перво-
го ряда намотки на 100 %. Перепуск производится на длину вы рубки ходового конца. По мере дальнейшей отработки ходового конца делается перепуск на 45-60 м. В месте вырубки с обеих сторон на концах делают тугие перевязки из мягкой проволоки. Данные о перепуске и вырубке заносятся в журнал учета ТО и Р оборудования. Талевый канат необходимо осматривать ежеднев но и после перегрузок при аварийных работах.
После установки нового стального каната необходимо его приработать при небольших нагрузках. Необходимо следить за правильной навивкой каната на барабан лебедки, что удлиняет срок его службы. Канат быстро выходит из строя, если витки на барабане не доходят до реборды барабана или у одной реборды наматывается виток на виток. Такая навивка происходит при неправильной установке лебедки, когда ось подъемного вала ба рабана не горизонтальна и не параллельна оси кронблока. По этому необходимо устранить дефект монтажа лебедки.
В начальный период эксплуатации заводская смазка обес печивает нормальную работу каната, но в процессе эксплуата ции смазка выжимается наружу и быстро теряется, поэтому в процессе эксплуатации канат должен смазываться. Наружная смазка предохраняет канат не только от истирания, но и от кор розии.
Смазку в любое время года наносят в подогретом состоянии с помощью кисти во время сматывания каната с барабана. Марка смазочного материала указывается в инструкции по эксплуата ции. При бурении до 500 м смазку производят через два-три рейса, а после 1500 м перед каждым спуском и подъемом.
Изношенный канат используют для такелажных работ. При необходимости порванные канаты сращивают.
Перегрузка осей кронблока при прихватах колонны буриль ных труб и ловильных работах может вызвать их изгиб, что при водит к биению блоков и интенсивному износу подшипников. Такие кронблоки ремонтируют.
При разборке кронблока (рис. 14.4) необходимо: открыть и снять кожух; отсоединить от рамы вспомогательный ролик; ос вободить опоры; снять ось в сборе; отогнуть лепестки стопорной шайбы и отвинтить гайку; удалить штифт; снять с оси опоры, втулку, блоки с роликоподшипниками, а также дистанционные кольца; выпрессовать роликоподшипники из ступиц блоков и вынуть пружинные стопорные кольца; вывинтить масленки из оси; очистить все детали кронблока от грязи и промыть; выявить дефекты деталей и составить дефектовочную ведомость. Для об легчения выпрессовки подшипников ступицы блоков нагревают газовыми горелками до 90-100 °С. При ремонте кронблока заме-
490