
книги / Технология строительной керамики
..pdfСхема подготовки глины по замкнутому циклу приведена на рисрис. 151. Влажность глины после сушки 9— 11%. Тонкость помола глиняного порошка должна соответствовать содержанию зерен раз мером 1— 0,5 мм — 15— 25% и менее 0,5 мм — 75— 85% . Лучшие ре зультаты по сравнению с помолом в дезинтеграторах получают при использовании для помола шахтных мельниц типа ММТ-1000/950/980 мШ
и ММТ-1300/950/740 мШ и других типов. |
|
|
|
|
|
|
||||||
Подготовка |
шамота заключается |
в |
обжиге |
глины, |
измельчении |
|||||||
ее и боя труб |
при просеивании. Брикеты из |
глины делают на |
пресс- |
|||||||||
|
|
|
|
|
вальцах |
или |
ленточных |
|||||
|
|
|
|
|
прессах. Тип |
печи опреде |
||||||
|
|
|
|
|
ляет способ подготовки гли |
|||||||
|
|
|
|
|
ны к обжигу (брикет, «чече |
|||||||
|
|
|
|
|
вица», валюшка |
или |
глина |
|||||
|
|
|
|
|
россыпью). |
|
|
|
|
|||
|
|
|
|
|
|
Брикет, |
«чечевица» (без |
|||||
|
|
|
|
|
глиняной крошки) обжига |
|||||||
|
|
|
|
|
ется в шахтной печи. Заг |
|||||||
|
|
|
|
|
ружают брикет в печь пе |
|||||||
|
|
|
|
|
риодически — через |
10— |
||||||
|
|
|
|
|
12 мин. Температура обж и |
|||||||
|
|
|
|
|
га |
1150— 1200° |
С. |
После |
||||
|
|
|
|
|
выгрузки шамот сортируют, |
|||||||
|
|
|
|
|
недожег возвращают на пов |
|||||||
|
|
|
|
|
торный обжиг. Съем шамота |
|||||||
Рис. 151. Схема подготовки глины по замкнутому |
с 1 м3 печного объема 0,03— |
|||||||||||
0,04 т/ч. Обжиг во вращаю |
||||||||||||
циклу: |
|
|
|
|
||||||||
|
|
|
|
щейся печи объемом до 40 м3 |
||||||||
/ — суш ильны й |
барабан ; 2 — конвейер; |
3 — элект |
||||||||||
ром агнит; 4, € |
— элеваторы ; 5, 8, 9 |
— бункеры ; |
более |
производителен, так |
||||||||
7 — снто-бурат; |
1 0 , 12 — секторны е питатели; 11 |
— |
как съем с |
1 |
м3 печи |
повы |
||||||
м олотковая мельница; 13 — ш нековый питатель; 14 — |
цен тр обеж н о -р отор н ая мельница. |
шается до 0,08— 0,09 т/ч. |
|
Основными недостатками вращающихся печей являются относи тельно большой удельный расход топлива, повышенный выход мелких фракций и значительный пылеунос (10— 15%). В барабане печи пере дача тепла конвекцией малоэффективна, с отходящими газами уно сится более 30% поступающего в печь тепла, т. е. подготовительный процесс (сушка сырья) происходит, примерно, на участке 3/4 длины печи, а обжиг и частичное охлаждение — на участке 1/4 длины печи. Пыль и мелкие фракции образуются главным образом в период уда ления механически и химически связанной воды (до 700° С).
С целью повышения прочности брикета в сыром виде рекомендуется вводить в массу (при влажности 26— 28%) жидкое стекло (0,1% по N azO) и кубовый остаток дистилляции жирных кислот (0,3% ) с содер жащей магний добавкой (0,5% талька или талькомагнезита по MgO). Кубовый остаток повышает прочность влажного брикета (в резуль тате ионного обмена), а магнезиальная добавка интенсифицирует муллитизацию каолинового брикета в области более высоких температур.
Эффективность использования вращающихся печей повышают установкой теплообменников для предварительной подсушки сырья,
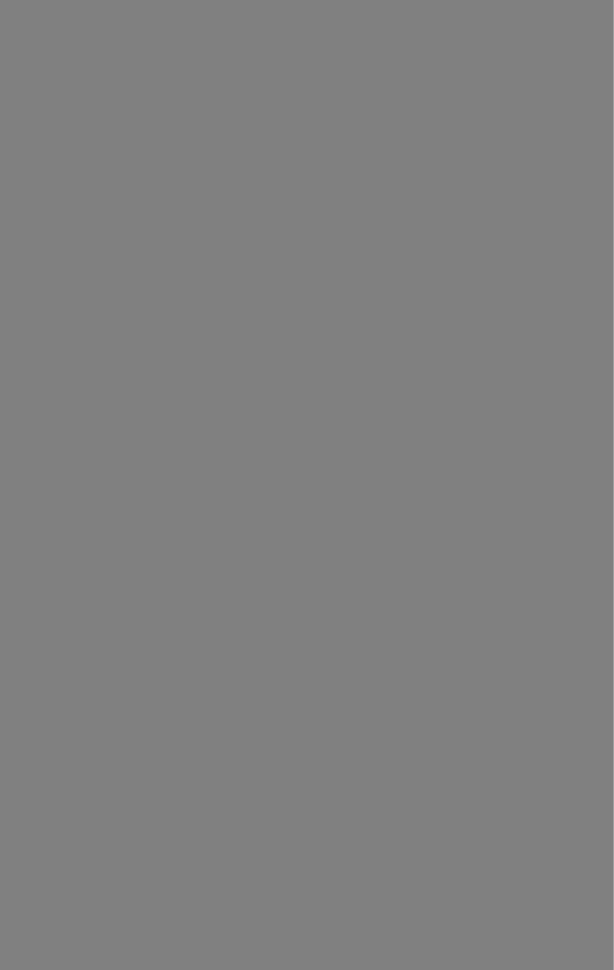
поступает непосредственно на формование. Расход массы на. 1 т труб около 1,5 т.
В США предложен способ и установка гранулирования глинистого сырья, применяемого для изостатического прессования тонкостенных труб. Глину измельчают сухим способом до микронных и субмикрон ных размеров и увлажняют в лопастном смесителе до влажности 5— 10%. Из смесителя глина винтовым шнеком, смонтированным на од ном валу с лопастями смесителя, подается в цилиндрическую камеру
Таблица 46. |
Характеристика |
прессов |
|
|
|
|
||
|
|
|
|
|
|
Т ипы п р ессо в |
|
|
|
Показатель |
СМ-88 |
С М -303 |
P U R -3 5 0 |
P U R -4 5 0 |
SR K F -45D |
||
|
|
|
|
(Г Д Р ) |
(ГДР) |
(Ф Р Г ) |
||
|
|
1 |
|
|
|
|
|
|
Производительность |
(шт./ч) |
|
|
|
|
|
||
при длине |
1 |
м и диаметре, мм |
|
|
130 |
150 |
160 |
|
150 |
|
|
|
130 |
150 |
|||
250 |
|
|
|
80 |
90 |
90 |
90 |
72 |
300 |
|
|
|
65 |
75 |
75 |
90 |
90 |
600 |
|
|
|
— |
25 |
30 |
30 |
40 |
Мощность - электродвигателя, |
|
|
39 |
50 |
75 |
|||
'кВт |
|
|
|
30 |
115 |
|||
Диаметр, цилиндра, |
мм |
394 |
590 |
350 |
450 |
450 |
||
Число оборотов шнека, об/мин |
23,8 |
24,5 |
25 |
25 |
25 |
|||
Величина вакуума, |
МПа |
97,3 |
97,3 |
— |
— |
— |
||
Габариты |
пресса, мм |
|
|
3700 |
4700 |
4000 |
||
длина |
|
|
|
4000 |
4250 |
|||
ширина |
|
|
|
2700 |
3500 |
3700 |
4300 |
3100 |
высота |
|
|
|
8600 |
10 000 |
8300 |
9300 |
9200 |
Масса, т |
|
|
|
8,4 |
10,0 |
6,5 |
10,7 |
17,2 |
уплотнения. Диаметр переднего винта равен диаметру цилиндра, и поэтому на тонкий слой материала воздействует поперечное срезы вающее усилие, обеспечивающее параллельную ориентацию чешуй чатых частичек глины. С противоположной стороны камеры на мате риал воздействует регулируемое давление, обеспечивая оптимальную плотность материала и радиальную ориентацию чешуек глины в плос кости, поперечной к направлению давления. Уплотненный материал на выходе из цилиндра разрезается диском на сегменты без нарушения ориентации частичек и затем соответственно на гранулы. Использо вание гранулированного материала до минимума сокращает количе ство трещин и других дефектов, а при соотношении внешнего диаметра трубы к толщине стенок, равном 13 : 1, в 1,5— 2 раза увеличивается механическая прочность труб.
Формование. Пластическое формование труб осуществляют на шнековых вертикальных и реже горизонтальных прессах. Краткая технологическая характеристика прессов приведена в табл. 46.
Вертикальные прессы бывают безвакуумные (СМ-390) и вакуумные (СМ-88, СМ-306) (рис. 152). На раме 1 смонтирован корпус пресса 6 , в котором вращается вал 2 со шнеком, приводимый в движение элект-
Подъемный стол уравновешивается грузами 1 2 , которые закреплены на тросах, переброшенных через блоки 1 3 . По мере увеличения длины
и массы формуемой трубы стол опускается вниз. Тормозится стол ав томатически при помощи электромагнитов. В момент окончания фор мования труба отрезается стальной струной 7. При выходе из пресса на конец ствола трубы наносится нарезка. Кроме того, на трубах боль шого диаметра делается надрез конца трубы на глубину 3/4 толщины стенки.
В прессах более совершенных конструкций подъемный стол рабо тает при помощи электропневмоцилиндров, что обеспечивает плавную
|
|
|
6 |
г |
|
|
Рис. |
153. Схема процесса формования трубы; |
|
|
|
||
а — ф ормование |
раструба; б |
— ф орм ован ие ствола; |
в — отр ез трубы ; |
г |
— |
|
отбор |
трубы; / |
— подвиж ной |
стол; 2 — подставка; |
3 *— м ундш тук; 4 |
— ко |
|
локол; |
5 — раструб трубы ; 6 |
— р езак ; |
|
|
|
|
работу пресса и |
высокую производительность — до 550— 600 |
труб в |
||||
час. Съем труб у таких прессов производится автоматически. |
|
|||||
Вакуумируется масса в |
вакуумной камере высотой 350— 500 мм, |
располагающейся на верхней части корпуса пресса. Давление 90,67— 100 кПа. Ж ивое сечение перфорированной решетки должно быть равным сечению формуемого изделия или на 3— 5% больше его. Форма отверстия овальная. При формовании труб большего размера вакууми рование массы позволяет использовать мелкий шамот (1— 3 мм) вместо крупного (4— 5 мм) при образовании достаточно плотной и гладкой поверхности труб. Механическая прочность труб из вакуумированных масс повышается на 15— 40% , а водопоглощение снижается на 1— 1,5% . При формовании труб диаметром 300— 600 мм иногда прессы (КЭМА) имеют две вакуумные камеры для двойного вакуумирования массы. Обе камеры подключаются к одному насосу.
После того, как формование раструба |
закончено, |
масса выходит |
из мундштука, стол пресса непрерывно |
опускается |
с подставкой |
(рис. 153), образуя тело трубы. Организация производства безраструбных труб почти на 50% сокращает время на формование труб, снижает продолжительность и потери труб при сушке и обжиге.
Отклонения по толщине стенки ствола и раструба трубы допус каются не более ± 3 мм, по длине ± 2 0 мм, по кривизне ствола — 8 мм.
Для достижения постоянства размеров прессы оборудуют устрой ствами, обеспечивающими получение труб заданной длины и позво ляющими изменять длину труб по мере надобности (рис. 154).
В цилиндре 3 горизонтального трубного пресса на валу 1 вра щается шнек 2 . На одной оси со шнековым валом установлено при способление 2 2 с резательным устройством, приводимое в действие зубчатой передачей от электродвигателя 4 . В начале цикла формо
вания трубы головка 9 штока 1 7 расположена внутри мундштука 5 и на трубе оформляется раструб 8 . Далее труба 7, выдавливаемая го ризонтально из мундштука 5, поддерживается головкой 9 , которая
отводится назад при продвижении трубы, выходящей из мундштука 5. Труба режется на отрезки определенной длины резательным устрой ством 6 , когда отключающий узел 1 2 замыкается выключателем 1 0 , закрепленном на штоке 1 7 .
Выключатель 1 0 имеет контакты, отключающие привод шнекового
питателя, в результате чего поступление трубной массы прекращается. Далее контакты замыкают выключатель, управляющий резательным устройством 6 , выключатель для быстрого отвода штока 1 7 устрой ством 1 5 и удаления головки 9 от раструба 8 . Готовая труба определен ной длины остается на амортизаторах 2 0 ленточного транспортера 1 8 . При замыкании другого выключателя шток 1 7 возвращается к мунд штуку, транспортер 1 8 с амортизаторами 2 1 передвигается по роликам 1 6 до позиции 1 9 и цикл начинается снова. Отключающий элемент 1 2 закреплен на раме 1 1 , н а которой он движется горизонтально до по ложения, соответствующего длине трубы. Положение элемента 1 2 при изменении длины трубы регулируется вручную вращением колеса 1 3 , установленного на рабочей платформе 1 4 .
При формовании труб на полуавтоматических прессах операции нарезки и оправки концов ствола и раструба производятся механиз
мами, установленными на прессе. В |
других |
случаях оправку и на |
||
резку наносят после подвялки труб |
вручную |
или |
механизированно, |
|
с |
помощью передвижных станков с механическим |
приводом, станков |
||
с |
горизонтальными вращающимися дисками и др. |
|
Отформованные трубы подвешивают с помощью штанг на цепной конвейер и направляют на сушку.
Производство труб на конвейерных линиях СМ-452, СМ-901 и дру гих имеет много преимуществ по сравнению с агрегатным способом. Поточная линия (конвейер СМ-452) производства канализационных труб диаметром 350—700 мм и 150— 300 мм включает формование труб пластическим способом, отбор труб от пресса, оправку, суш ку, глазу рование.
Производительность конвейера 3000 т в год, потребляемая мощ ность 140 кВт, количество обслуживающих рабочих 6 человек.
В последние годы разработаны автоматизированные заводы мощ ностью 30 тыс. т труб в год диаметром 150— 500 мм при длине 1500 мм.
К недостаткам формования труб на вертикальных прессах следует отнести: высокую трудоемкость, невозможность формования труб уве личенной длины, необходимость формования труб из масс с влаж ностью 18—21% .
Новые трубные прессы позволяют формовать трубы диаметром 100— 600 мм при длине от 1 до 2 м из массы влажностью 14— 16% с содержанием до 30% шамота. В прессах использованы износостой кие сплавы для шнека, ножей, футеровки и др. Вакуумная камера оборудована ультразвуковой контрольной аппаратурой. Отбор труб от пресса автоматизирован. Производительность пресса 550— 600 труб в час.
ВНИИСтроммаш разработано оборудование для горизонталь ного формования труб. При организации производства труб (диа метром 150— 300 мм, длиной 1 и 1,2 м) горизонтальным способом из масс с пониженной влажностью (12— 14%) эксплуатационные расходы уменьшаются в 2,3 раза, трудоемкость изготовления труб в 1,7; капи тальные затраты в 1,8; произведенные площади в 1,7; повышается ка чество изделий; устраняется сушка, как отдельная операция, соз даются лучшие условия для автоматизации производства. Высокая производительность горизонтальных шнековых процессов (в 2— 4 раза больше вертикальных) и ликвидация отдельных операций резко по вышают съемы с производственных площадей при меньших трудовых затратах.
При горизонтальном формовании безраструбных труб процесс не прерывный, так как по мере выхода трубы из пресса она разрезается проволочным резаком на куски нужной длины. Концы труб закруг ляются на участке оправки и слегка расширяются для монтажа (после обжига) гибких резиновых соединений.
Технология полусухого прессования, разработанная НИИСтройкерамики, предусматривает прессование труб из масс влажностью 8— 10%, того ж е состава, что и для пластического формования, через резиновую оболочку, помещенную в металлическую пресс-форму (гид ростатическое прессование).
Прочность свежесформованных труб не ниже 1,18 МПа. Длитель ность формования зависит от размера труб и составляет 120— 80 с, что обеспечивает производительность около 15 т/ч. Гидростатическим способом изготавливают трубы диаметром 1,5— 2 м и длиной до 2 м.
Сушка. Йскусственная сушка |
труб осуществляется в камерных, |
|
туннельных |
и\конвейерных сушилках. |
|
К а м е р |
н ы е с у ш и л к и |
реже используются для сушки труб, |
чем туннельные) Трубы в камере устанавливаются в два яруса — внизу большего, а вверху меньшего диаметра. Теплоносителем в камерных сушилках является воздух, подогреваемый в калориферах или заби раемый из зоны охлаждения печей. Подъем температуры ведется мед ленно — за первые 12 ч до 30° С при относительной влажности тепло носителя 80— 90% , за вторые 12 ч до 50° С при относительной влаж ности 50— 60% и такрй сохра
няется до конца сушки. Про |
Таблица |
47. Влажность |
труб при переходе |
|||||||
должительность |
сушки |
в |
ка |
из одной |
зоны сушки в другую, |
% |
|
|||
мерных сушилках от 60— 70 ч |
|
|
Влажность труб, |
%, |
||||||
в зависимости |
от |
диаметра |
|
|
||||||
|
|
в ее частях |
|
|||||||
труб. |
|
|
|
|
Температурные |
|
|
|
||
Т у н н е л ь н ы е |
с у |
участки |
пле |
СТВОЛ конец |
||||||
|
|
чико |
||||||||
ш и л к и имеют длину от 32 |
|
|
|
|
||||||
|
|
|
|
|
||||||
до 47 м и бывают двух-, трех- |
75—80° С |
10,3 |
11,5 |
12,5 |
||||||
и четырехпутные. |
Трубы |
в |
||||||||
85—100° С |
6,1 |
6,9 |
7,1 |
|||||||
туннельные сушилки подают |
||||||||||
115— 135° С |
3,9 |
4 |
3,7 |
|||||||
ся на обычных или монорель |
На выходе из сушила |
2,6 |
2,3 |
1,9 |
||||||
совых вагонетках |
по |
4— 16 |
|
|
|
|
|
труб в зависимости от диамет ра. Температура теплоносителя, поступающего в туннель со стороны
выгрузки, 90— 140° С, отбираемого — 35—40° С при относительной влажности около 90% . Плотность загрузки туннельных сушилок до 60 кг на 1 м3 внутреннего объема. Время проталкивания вагонеток 30— 60 мин. Продолжительность сушки 14— 22 ч для труб диаметром 150— 250 мм и 28—40 ч для труб большего размера.
Таблица 48. |
Составы глазурей |
|
|
|
|
||
|
|
|
|
Состав, |
% |
|
|
Материал |
|
|
|
|
|
|
|
|
|
1 |
2 |
3 |
4 |
5 |
6 |
Легкоплавкая |
глина |
44 |
46 |
48 |
25 |
40 |
50 |
Полевой шпат или пег |
|
30 |
30 |
30 |
25 |
20 |
|
матит |
|
— |
|||||
Мел |
|
— |
12 |
12 |
9 |
10 |
15 |
Гипс |
|
16,5 |
— |
_ |
|
— |
— - |
Перлит |
|
30 |
— |
— |
— |
— |
— |
Бой стекла |
|
— |
— |
— |
23 |
25 |
— |
Железная руда |
|
— |
— |
— |
5 |
— |
— |
Марганцевая руда |
9,5 |
12 |
10 |
8 |
“““ |
15 |
Значительные перепады температур между верхом и низом садки (до 40— 50° С) удлиняют время сушки, приводят к повышенному рас
ходу тепла |
(до 8,4 М Дж/(кг 0 С) на испарение влаги) и неравномер |
ной сушке |
труб (табл. 47). |
Рециркуляция теплоносителя частично устраняет этот недостаток.
Влажность после сушки от 3 до 5% |
в зависимости от диаметра труб. |
В к о н в е й е р н ы х с у ш и л к а х (типа |
СМ-982, СМ-410А и др.) сушка |
труб, подвешенных на тарелях к цепи конвейера, протекает при не прерывном их перемещении по параллельно расположенным зигзаго образно соединенным туннелям. Шаг тарелей 0,64— 0,96 м. Подвеши вая трубы на разной высоте (рис. 155), повышают емкость конвейера на 22— 30% . Скорость движения цепи конвейера 0,64— 1,3 м/мин.
Относительная влажность теплоносителя в подвялочной части кон вейера 65—80% . Трубы сушатся горячим воздухом, полученным от
|
калорифера» |
температура теплоно |
||||||||
|
сителя 80— 140° С. Давление на от |
|||||||||
|
косе из зоны подвяливания 0,76— |
|||||||||
|
0,98 |
кПа, |
из |
|
зоны |
сушки — |
||||
|
0,1— 0,3 |
кПа. |
В |
зависимости |
от |
|||||
|
диаметра |
труб |
продолжительность |
|||||||
|
сушки их колеблется от 20 до 40 ч. |
|||||||||
|
Влажность |
высушенных труб |
2— |
|||||||
|
3% . Расход топлива на сушку — |
|||||||||
|
30— 35 кг на 1 т труб. |
|
|
|
||||||
|
Глазурование |
труб |
производят |
|||||||
|
глиняными |
сырыми |
глазурями |
|||||||
|
(табл. 48) и реже соляной глазурью . |
|||||||||
|
Приготовляют |
глазурь |
(кроме |
|||||||
|
соляной) совместным помолом в ша |
|||||||||
|
ровой мельнице предварительно из |
|||||||||
|
мельченных |
компонентов. |
Темпе |
|||||||
|
ратура |
разлива |
глазурей |
1080— |
||||||
Рис. 155. Совмещенная подвеска труб: |
1180° С. Соотношение массы мате |
|||||||||
риала, воды и мелющих тел состав |
||||||||||
1 — труба; 2 — подвеска. |
||||||||||
ляет |
1 |
1 : 1 . |
Продолжительность |
|||||||
|
помола 14— 40 ч. Загружают компоненты в мельницу в два приема — сначала крупнозернистые твердые компоненты (пегматит, марганцевая руда и др.) и глину от 5 до 50%, а после размола в продолжении 22— 24 ч добавляют остальные материалы. Совместный помол продолжается не менее 4 ч. Тонкость помола глазури характеризуется остатком на сите 10 000 отв/см2 не более 2% . Перед подачей на глазурование в ме шалку добавляют воду из расчета доведения плотности глазури до 1,36— 1,45 г/см3 (влажность .глазури 49— 52% ).
Глазуруют трубы, погруж ая' их в глазурь, поливом глазурыо, пульверизацией, а также соляной глазурыо. Глазуровать горячие трубы (свыше 40° С) нельзя.
Г л а з у р о в а н и е п о г р у ж е н и е м (окунанием) осуще ствляется при помощи тельфера, опускающего трубы в бассейн с гла зурыо, или на специальных глазуровочных машинах, работающих по прицепу перекатки или протягивания труб через бассейн с глазурыо. После глазурования трубы выдерживают на решетке калорифера для закрепления глазури. Расход глазури'околр 2— 3% массы трубы.
П о л и в о м трубы г л а з у р у ю т в такой последовательности.