
книги / Технология строительной керамики
..pdfные (1— 2% влаги) плитки размером 150 X 150 X 10 мм пульвериза цией с помощью металлических трафаретов, устанавливаемых на плит ку, движущуюся на цепном конвейере. Плотность глазури 1,56— 1,58 г/см3. Цвет плиток коричневый, глазури — белый.
Для изготовления порфировидных плиток используют глинистое сырье разной естественной окраски. Из порошка глин готовят гранулы, используя вальцы, протирочное сито и вибросито для отделения гра нул от остатка порошка. Далее гранулы поступают на смесительный транспортер и в бункер над прессом. Прессование плиток из гранул осуществляют как из порошка. Влажность порошка глин 5—7%. Зазор между валками вальцев 3— 4 мм. Для получения порфировид ного рисунка используют 35% крупных гранул (1—2 мм) и 65% мелких.
При изготовлении мраморовидных плиток используют обычные цветные порошки, полученные в распылительных сушилках. Основная масса составляет 85%, а лицевой (мраморовидный) слой — 15% — состоит из порошка, полностью проходящего через сито 4900 отв/см2.
Декорировать плитки также можно шелкографическим способом. В Италии освоено производство рельефно-орнаментированных пли ток по следующей технологии. Плитка глазуруется по всей площади. На специальной зачистной машине глазурь снимается с выступающей
поверхности рельефа. Далее плитка поступает в обжиг на 4 —5 ч.
В ФРГ |
изготовляются глазурованные |
плитки для полов (100 х |
X 100 мм) |
с предварительным нанесением |
слоя цветного ангоба (бе |
лого, желтого, зеленого, голубого, серого и черного). Плитки глазу руют прозрачной глазурью поливом, высушивают в течение 18—23 мин
при 150— 165° С и обжигают в электрической |
роликовой |
четырехка |
нальной печи при 1180° С. Время обжига 3 ч |
45 мин. |
|
В США предложено обрабатывать плитки для полов в расплавлен |
||
ной сере (145— 150° С) путем погружения. В результате |
повышается |
прочность почти в 3 раза, морозостойкость, модуль упругости, сопро тивление истиранию и термостойкость. Снижается водопоглощение. Сера может быть заменена парафином, смолой и другими материалами с низкой температурой плавления. Если плитка должна иметь повы шенную шероховатость поверхности (например, пол в душевых, пла вательных бассейнах и др.), предложено (патент ФРГ) в слое глазури применять корундовый порошок с размером зерен 40—200 мк (но не более 300 мк) в количестве 5—25% в пересчете на общую сухую массу компонентов глазури и корундового порошка. В поверхностном слое максимальное количество зерен корунда не должно быть покрыто плен кой глазури. Для этого в процессе обжига обеспечивают получение такой вязкости глазури, которая препятствовала бы осаждению зерен корунда. При глазуровании плитки сначала на нее наносят первый слой в виде спеченного ангоба, затем слой глазури, содержащей зерна корунда, причем оба эти слоя обжигаются одновременно. Количество шероховатых зерен корунда составляют 3—25 шт. на 1 мм2. Слой глазури подвергают различным способам структурирования. Износ плиток в процессе эксплуатации менее заметен на глазурной поверх ности с различными цветовыми оттенками, чем на блестящей однотонной
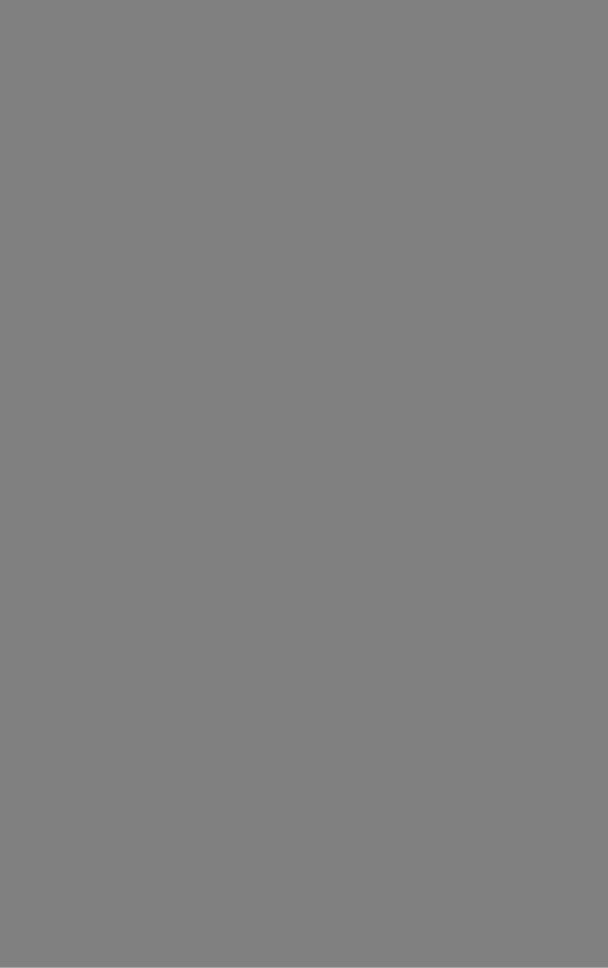
95— 100 м2 при комбинированной садке. Плотность садки на 1 м3 печ ного объема 20—22 м2.
При бескапсельном обжиге плиток производительность печей уве личивается на 15— 20%, расход топлива снижается на 5—8%, в 6— 8 раз снижается расход огнеупорного припаса (оборачиваемость шамот ных этажерок в б—8 раз выше капселей), уменьшаются отходы пли ток в связи с переходом от вертикальной к горизонтальной ставке, уменьшается пятнистость плиток, механические повреждения и дру гие дефекты обжига. В целях защиты плиток от прямого воздействия
острого |
пламени |
на вагонетки устанав |
|
|||||
ливают |
экраны |
из |
огнеупорных |
плит. |
|
|||
Обжигают |
плитки |
при |
1180— 1250° С |
|
||||
(белые) |
и 1150— 1180° С (цветные). |
|
||||||
Туннельные печи конструкции Гипро- |
|
|||||||
стройматериалов имеют размер рабочего |
|
|||||||
канала 1,4 X 1,3 м, длину 88 м. Объем |
|
|||||||
рабочего канала |
160 м3. Печь имеет вход |
|
||||||
ную и выходную камеры. Входная ка |
|
|||||||
мера оборудована |
шторой |
и шибером. |
|
|||||
В печь |
вмещается одновременно 44 ва |
|
||||||
гонетки. Печь делится на зоны: подогрев |
|
|||||||
(1— 12 позиции), обжиг (13— 23 позиции), |
Рис. 121. Кривые обжига плиток |
|||||||
охлаждение |
(24—44 позиции). Зона об |
|||||||
в печах: |
||||||||
жига имеет 30 горелок (по 15 с |
|
|||||||
каждой 1 — щелевых; 2 — туннельных. |
||||||||
стороны). Во время обжига поддержива |
|
|||||||
ют давление |
газа в пределах 1,47—3,92 МПа, воздуха 0,98— 1,18МПа, |
на горелке — 2,16—2,55 МПа. Газовая среда — окислительная. Дав ление в печи на позиции 15— 16 нуль, а на позиции 42 от 1 9 ,6 2 до
24,53 Па. Давление у дымососа 0,39—0,44 МПа, воздуха, отбираемого на сушку, от 0,1 до 0,5—0,6 МПа.
Режимы толкания вагонеток такие: замедленный — от 22 до 27 вагонеток в сутки (через 65—53 мин); нормальный — от 24 до 28 ва гонеток в сутки (через 60—51 мин); ускоренный — от 25 до 29 ва гонеток в сутки (через 58—50 мин). Общая продолжительность обжига 40—44 ч. Съем плиток с 1 м8 туннельных печей составляет 340—380 м2
в месяц. Расход условного топлива 7—9 кг/м2 плиток; Начиная |
с тем |
|
пературы свечения, обжиг |
плиток проводят в окислительной |
среде, |
а конец — в нейтральной. |
Кривые обжига плиток приведены на |
рис. 121.
При скоростном однократном обжиге плиток для предотвращения взрываемости их начальная температура в печи не должна превышать 200° С, а скорость подъема температуры в интервале 500—900° С долж на находиться в пределах 50—80° С/мин. Чтобы исключить образо вание черной сердцевины внутри плитки и вздутие плитки, при 700— 1050° С должна быть выдержка 18—23 мин.
При скоростном режиме обжига плиток в щелевых печах макси мальная температура обжига должна быть в пределах 1100— 1200° С. Выдержка при максимальной температуре обжига не менее 4—5 мин. Длительность скоростного обжига плиток в роликовых щелевых
печах составляет 35— 42 мин, а полный цикл производства от склада сырья до получения готовых плиток (при шликерном способе приго товления порошка) около 4 ч вместо 80— 100 ч при обычном способе производства.
По проекту ПКБ НИИСтройкерамики на керамических комбинатах эксплуатируются конвейерные линии со щелевыми печами производи тельностью 200 и 400 тыс. м2 плиток в год.
На линии осуществляются операции: прессование, прием плиток от прессов, раскладка их на шесть рядов и подача в сушилку; сушка плиток в четырехсекционной газовой сушилке в течение 32 мин и об жиг в роликовой газовой печи в течение 42 мин.
Размеры линии, м: длина 80; ширина 4,5; высота 3,3; общая масса линии 61,5 т.
Институтом НИИСтройкерамика также разработан проект двухъ ярусной конвейерной линии мощностью до 800 тыс. м2 в год. В этой линии для обжига плиток предусмотрена роликовая печь, представ ляющая собой туннель, перегороженный посредине в горизонтальной плоскости стенкой, образованной арочным сводом нижнего яруса и подом верхнего яруса. Роликовый под печи приводится в движение вертикальным редуктором, обеспечивающим самостоятельную работу каждого яруса. Горелки типа В-21/1,3 производительностью 1,3 нм3/ч расположены по всей длине зон подогрева и обжига в обоих каналах печи под роликовым подом и над ним. Продолжительность обжига при
1100° С и |
охлаждения |
52 |
мин. |
|
|
Размеры печи |
64,68 |
X 2,39 м, |
ширина рабочего канала печи |
||
1160 мм, |
высота |
рабочего |
канала |
одного яруса 590 мм. Топливо — |
природный газ с теплотворной способностью 9,86 кВт, удельный рас ход условного топлива 2,5 кг/м2, удельный расход электроэнергии 0,74 кВт • ч/м2.
Институтами Гипростройматериалы и Гипростром такой же мощ ности созданы трехъярусные поточно-конвейерные линии.
Роликовые печи экономичны в эксплуатации, так как расход топ лива на обжиг плиток почти в два раза ниже, чем в туннельных печах.
Сортировка и упаковка плиток. Для сортировки плиток созданы автоматы типа КММ 2720-1-1 и СМ-801. Автомат СМ-801 состоит из механизма для контроля плиток по толщине и кривизне поверхности, механизма для сортировки плиток по длине (ширине) и аппаратного
шкафа. Плитки, имеющие кривизну |
более ± 3 |
мм, отбраковываются. |
|||||||
Производительность автомата 3000 |
плиток |
в |
час. |
|
|
|
|||
|
Д ля |
упаковки плиток используется автомат |
СМ-860 |
производи |
|||||
тельностью до 9000 плиток в час. |
|
|
|
|
|
|
|
||
|
Упаковывают плитки по 20 шт. в пачку. Упаковка плиток автома |
||||||||
том |
снижает трудовые затраты в 4— 4,5 раза |
и |
стоимость |
упаковки |
|||||
в 3 |
раза. Упакованные плитки поступают |
на |
склад готовой |
про |
|||||
дукции. |
|
|
|
|
|
|
|
|
|
Способы крепления плиток. Крепят плитки к |
поверхности |
стены |
|||||||
чаще всего на цементном растворе марки |
50 |
состава |
1 |
5— 1 : 6 |
|||||
(цемент |
и песок). Можно крепить |
плитки |
на битумно-силикатных, |
известково-битумных и синтетических мастиках. Составы мастик сле дующие: битумно-силикатная мастика состоит (мае. ч) из глинобитумиой пасты (битум — 36%, глина — 24, вода — 40%) — 1; жид кого стекла — 0,75, мела 1,5—2,5; известково-битумная мастика (мае. ч) — из битума (БН-111) — 1, известкового теста 100%-ной влаж ности — 0,8, воды — 0,6.
Синтетические мастики готовят на основе цементного раствора с карбоксилметилцеллюлозной (КМЦ) или поливинилацетатной (ПВА) эмульсии.
Г л а в а VII
П
ЛЕГКИЕ ЗАПОЛНИТЕЛИ
Пористые заполнители делятся по их природе, применению, размеру и форме зерен, объемной насыпной массе и прочности. По природе они бывают естественные и искусственные. Последние, в свою очередь, делятся на заполнители, получаемые вспучиванием горных пород и минералов (глин, глинистых сланцев, трепелов, перлита, вермикули-
Таблица |
44. Классификация заполнителей |
|
|
|
|
||
Тип |
заполнителя |
Характер термической |
|
Осиооное |
сырье |
|
|
обработки |
|
|
|||||
|
|
|
|
|
|
||
Керамзит |
и его разновид |
Обжиг со вспучиванием |
Глинистые и песчано-глинистые |
||||
ности (шунгизит, зольный |
|
|
породы |
(глины, |
суглинки, |
гли |
|
гравий, глинозольный ке |
|
|
нистые |
сланцы, аргилит, алевро |
|||
рамзит, вспученные аргил |
|
|
лит), шунгитосодержашие |
слан |
|||
лит и трепел) |
|
|
цы, трепелы, золошлаковые сме |
||||
Термолит |
Обжиг без |
вспучива |
си, зола-унос ТЭС |
|
|||
Кремнистые опаловые породы |
|||||||
Аглопорит |
ния |
|
|
|
|
|
|
Спекание с |
поризацией |
Песчано-глинистые породы, тре |
|||||
|
|
при обжиге |
|
пелы и другие алюмосиликатные |
|||
|
|
|
|
материалы, зола |
ТЭС, отходы |
||
|
|
|
|
углеобогащения |
|
|
Шлаковая пемза
Гранулированный шлак
Перлит вспученный
Вермикулит вспученный
Поризация расплава
Быстрое охлаждение расплава
Обжиг со вспучиванием Вулканические водосодержащие породы (перлитобсидиан и дру гие водосодержащие вулканиче ские стекла)
Природные гидратированные слюды
та, шунгизита и др.), и заполнители, получаемые из отходов про мышленности (зола, шлак и др.).
Все искусственные пористые заполнители разделяют на 7 классов (табл. 44).
Требования к керамзигу. Гравий керамзитовый (керамзит) представ ляет собой пористый материал ячеистого строения, с закрытыми оплав
ленными |
(неостеклованными) мелкими |
порами. Получают из глин |
|||
и глинистых пород ускоренным обжигом |
при 1050— 1250° С. |
||||
Керамзит имеет окатанную шаровидную или эллиптическую форму, |
|||||
размером |
в |
поперечнике |
от |
5 до 40 мм. Его свойства определяются |
|
структурой |
(см. схему |
2). |
|
|
|
|
|
Схема 2. Факторы, |
определяющие структуру керамзита |
В соответствии с ГОСТ 9759—76 керамзит в зависимости от объем ной массы разделяют на 12 марок: «150», «200», «250», «300», «350»,
«400», |
«450», |
«500», |
«550», |
«600», «700», |
«800»; песок — на |
5 марок: |
«500», |
«600», |
«800», |
«1000» |
и «1200». По |
пределу прочности |
при сжа |
тии керамзит разделяют на два класса: А и Б. При марках гравия «150—700» прочность для класса А установлена 0,39—5,88 МПа, для класса Б — 0,29—3,92 МПа.
Марка керамзита по морозостойкости — не менее 15 циклов по переменного замораживания и оттаивания, а потеря массы не должна превышать 8%. Коэффициент формы (отношение наибольшего размера зерна к наименьшему) не более 1,5, а содержание зерен с коэффициен том формы 2,5 и более не должен превышать 20%. Водопоглощен не керамзита в течение 1 ч 15—25% в зависимости от объемной массы. Плотность керамзита 2,3—2,7 г/см3. Коэффициент теплопроводности 0,05—0,2 Вт/(м °С). Наличие свободного кварца (10—40%) ухуд шает теплофизические свойства керамзита.
Размер пор — от нескольких микрон до 1 мм составляет до 98%, размер крупных пор 3—5 мм. Общая пористость до 70%. Масса ке рамзита — полностью спекшаяся, поры не сообщаются между собой
(до 90% замкнутых пор), в результате чего гравий имеет низкую влагоемкость.
Гравий имеет плотную, шероховатую оболочку. Он атмосферо- и огнестоек, долговечен. Огнеупорность керамзита (обычного) от 1140 до 1250° С, жаростойкого до 1400° С.
Гигроскопическая влажность керамзита не должна превышать 2% . Максимально допустимая величина коэффициента уплотнения гравия (при транспортировании) — 1,15.
В зависимости от свойств керамзит применяют для изготовления керамзитобетона и конструктивного железобетона (64%), для тепло изоляционных засыпок (25%) и других целей (11%). Расширяется использование керамзита для легких бетонов (ГОСТ 9757—73).
Обладая относительно высокой прочностью при малой объемной массе, керамзит позволяет получать на его основе легкие бетоны с высоким коэффициентом конструктивного качества (0,25 против 0,18 при той же прочности для обычного бетона).
Сырьевые материалы. Сырьем для производства керамзитового гравия служат легкоплавкие глинистые породы (глины, суглинки, аргилиты, глинистые сланцы, трепелы, диатомиты и др.) различного возраста и генезиса, обладающие способностью при быстром обжиге вспучиваться в природном виде или с добавками, образуя материал ячеистой структуры.
Советский Союз располагает огромными запасами керамзитового (природного) сырья в центральной части европейской территории
СССР, в районе Среднего Поволжья, на Северном Кавказе, в Восточ ной Сибири, Казахстане. Только кремнистых пород (опоки, трепела, диатомиты и др.) зарегистрировано более 850 месторождений.
Лучше других вспучиваются глинистые породы морского, озер ного и озерно-болотного происхождения с преимущественным содер жанием глинистых минералов группы монтмориллонита, гидрослюды, вермикулита и гидрохлорида. Породы, представленные минералами типа каолинита и галлуазита, не вспучиваются без добавок при обыч ных температурах обжига. Плохо вспучиваются или совсем не вспу чиваются глины с малым содержанием щелочей, переотложенные и выветренные глины, суглинки и сланцы, лессы и глинистые породы, содержащие оксид кальция более 5— 6%.
Породы, глинистая часть которых сложена гидрослюдой и квар цем, гидрослюдой, кварцем и каолинитом, занимают промежуточное место между хорошо вспучивающимся (без добавок) сырьем (рис. 122). Большое влияние на вспучиваемость глин оказывают сопутствую щие минералы: слюда, полевой шпат, различные железосодержащие минералы и соединения, а также органические вещества.
Вспучиваемость глинистого сырья определяется коэффициентом, выражающим отношение объема вспученной массы к объему абсолют но сухого сырца. Коэффициент вспучивания всегда выше коэффициен та выхода керамзита. По величине коэффициента вспучивания разли
чают |
глинистое сырье |
хорошей |
вспучиваемости (К |
в > 4,5, уоб < |
||
< 400 |
.-кг/м3), |
слабой |
(/(„ < |
2,5, |
уоб *= 7 50 — 1250 |
г/м3), средней |
(К в ~ |
2,5—4,5, |
уоб — 450—700 |
кг/м3). |
|
Сырье, дающее при обжиге коэффициент вспучивания менее 2 и остеклованную поверхность, нельзя использовать в производстве ке рамзита без добавочных материалов.
Хорошо вспучиваются глинистые материалы, имеющие примерно
следующий |
химический состав, |
%: S i02 — 50—65, А120 3 — 10—25, |
|
Fe20 3 -f- FeO — 3,5— 10, СаО — до 3, MgO— до |
4; Na20 + K 20 — 3,5, |
||
свободного кремнезема — до 25. |
Потери при |
прокаливании 7— 10%. |
|
Желательной |
примесью в сырье |
являются тонкодисперсные органи- |
Рис. 122. Области расположения керамзи тового сырья:
/ — опок; II — диатомитов и трепелов; I I I —
вы соковспучиваю щ нхся |
глин; I V — среди е- |
вспучиваю щ ихся глин; |
V — слабовспучнваю - |
щ ихся суглинков. |
|
Рис. 123. Поля вспучивания в трой ной системе:
1 — области хорошей естественной вспучиваемости; 2 — область примене ния порообразователей.
ческие вещества в пределах 1—3%. По химическому составу можно определить вспучиваемость глин (рис. 123).
Оптимальные соотношения между отдельными флюсующими ок сидами находятся в следующих пределах:
Минералы |
Величина |
Оптималь |
|
соотноше |
ная |
|
ния |
область |
Fe20 3 : СаО |
2— 5 |
4— 7 |
Fe,03 : (К20 + Na20) |
1,2— 2,0 |
1,5— 1,9 |
(СаО + MgO) ■ (К20 + NaaO) |
0 ,4 - 1 ,5 |
0 ,7 - 1 ,0 |
Оксиды алюминия и железа повышают прочность керамзита, ок сид кремния — снижает. Вводят оксиды железа и алюминия в тонко дисперсном, состоянии "в виде огнеупорной глины и пиритных огарков. Общее содержание оксидов железа в сырье не должно превышать 10%, так как при большом его количестве прочность керамзита и его дол говечность снижаются.
Лучшим качеством обладают глины, содержащие минимальное количество пылеватых (5—50 мкм) и песчаных (свыше 50 мкм) части чек при отсутствии крупных (более 0,2 мм) включений карбонатов. Ориентировочное содержание частичек величиной 0,005 мм и менее должно быть не ниже 20%.
.массу в их ввода способы и добавок Классификация .3 Схема
|
Н е ф т ь |
|
3 -1 |
Вулканический |
пепел |
|
|||||
|
М |
а |
з |
у |
т |
|
D— |
Т р е п е л |
|
||
|
Дизельное топпибо |
|
|
||||||||
|
|
|
|
|
|||||||
|
К е р о с и н |
|
|
П е р л и т |
|
||||||
|
Л и г р о и н |
|
У - |
Сульдх/дные затрадтV - |
|
||||||
|
|
|
|
|
|
|
|
||||
Сульфитно-спиртовая борда \- |
|
|
|
||||||||
|
Пиролизная |
см ола" = Н |
О б с и д и а н |
|
|||||||
|
. .Болотная |
руда |
|
|
|
|
|||||
|
Пиритные |
огарки |
|— |
О р га н и ч е с к и е |
|
||||||
|
Ж елезная |
руда |
(— |
|
|
|
|||||
|
Г у м б р и н |
|
|— |
Ж е л е з и с т ы е |
|
||||||
| |
>1 н т р а ц е н |
|— |
Ор г ано-минеральные |
|
|||||||
1 |
У |
г |
о |
л |
ь |
|
|— |
|
|||
|
|
|
|
||||||||
1 |
Т |
о |
р |
ф |
|
|
|— |
Опрыскивание глины жидкими |
|||
| |
О |
п |
и |
л |
к |
и |
|— |
||||
| |
|
З |
о |
л |
ы |
|
|
добавками |
|
||
|
|
|
Опрыскивание поверхности |
гра- |
|||||||
| |
Ч е р н |
о |
з |
е м |
Н |
||||||
нул жидкими добавками |
|
||||||||||
|
|
|
|
|
|
|
|
Шихтовка твердых добавок |
|||
|
|
|
|
|
|
|
|
с гомогенизацией массы |
|
||
|
Порошок |
огнеупорной глины |
Опудридание сырца порошками |
||||||||
|
Огнеупорная зола ТЭЦ |
— |
Обволакивание гранул в печи |
||||||||
|
Песок кварцевый природный |
Опувривание |
гранул |
|
|||||||
|
с горячего конца печи |
|
|||||||||
|
|
|
|
|
|
|
|
|
|||
Молотый кварцевый песок |
|
Обработка гранул |
|
||||||||
|
в шламе глины |
|
|||||||||
|
|
|
|
|
|
|
|
|
|||
|
Длинноплавкие |
железистые >— |
|
|
|
||||||
|
|
|
глины |
|
|
Обволакивающие гранул |
|
||||
|
Порошок |
полевого |
шпата |
|
|
||||||
|
|
|
|
|
|||||||
|
Антрацит (кокс) |
|
ленные в массе |
|
|||||||
|
|
|
|
|
|
|
|
|
|||
|
Длинноплавкие глины |
|
Окисление поверхности1 ) |
|
|||||||
|
|
вспучивания зерен |
|
||||||||
|
Железосодержащие руды |
Совместно железистые |
|
||||||||
|
и отходы промышленности |
|
|||||||||
|
Точкоизмельченный |
|
и органические____ |
|
|||||||
|
|
Железистые |
|
|
|||||||
|
полевой |
шпат |
|
|
1 1 |
||||||
|
|
|
|
|
|
|
|
|
|
||
|
|
|
|
|
|
|
|
Органические |
- |
- |
|
|
В о з д у х |
|
|
Органо-минеральные _ |
|
s*
ао
о
сь
Z
е
о
3:
с:
X)
з*
о
-с сь
0
3
Оэ
Q
*Ъ
В
1
Сч
о
о
*
с
о
с:
со
О
О
Q>
3
о» CD
Q
£
Со
с
3
8 § i'g
I I
и
sшаs § з
*1
11
Обогащенный кислородом |
Щелочные и щелочно - |
в о з д у х |
земельные . |