
книги / Технология производства и методы обеспечения качества зубчатых колес и передач
..pdfТехнология изготовления зубчатых колес для микроэлектромеханических систем |
361 |
Таблица 9.2
Геометрические параметры эвольпентного и циклоидального зацеплений [7]
|
Эвольвент!юс |
|
Циклоидальноезацепление |
|
|||
Номер |
зацепление |
Номер |
|
Радиус окружности, мкм |
|
||
|
|
|
|||||
варианта |
|
варианта |
головка зуба |
ножказуба |
|||
Профильный угол |
|||||||
шестерня |
колесо |
шестерня |
колесо |
||||
|
|
|
|||||
1 |
20° |
3 |
40 |
40 |
40 |
40 |
|
2 |
14,5е |
4 |
40 |
20 |
20 |
40 |
|
|
|
|
|
|
|
Таблица 93 |
|
|
Результаты испытаний приводов радиусом 100 и 150 мкм [7] |
|
|||||
Радиус |
|
Тип |
Минимальное |
|
Частота иммульсоп, |
|
|
микроэлектроприоо- |
зацепления |
напряжение |
необходимая для поддержания непрерывного |
||||
ла, мкм |
|
по табл. 9.1 |
возбуждения, В |
|
вращения |
|
|
|
|
1 |
50 |
|
Каждые 5 минут |
|
|
100 |
|
2 |
68 |
|
Каждые 2 минуты |
|
|
|
3 |
116 |
|
1-2 раза в минуту |
|
||
|
|
|
|
||||
|
|
4 |
52 |
|
Каждые 2 минуты |
|
|
|
|
1 |
75 |
|
Каждые 2 минуты |
|
|
150 |
|
2 |
60 |
|
Каждые 3 минуты |
|
|
|
3 |
76 |
|
Каждые 30 секунд |
|
||
|
|
|
|
||||
|
|
4 |
77 |
|
Каждые 20 секунд |
|
Для повышения качества и дальнейшей миниатюризации изделий перспективным яв ляется реализация в микротехнологнях новых физических эффектов и расширение переч ня используемых материалов [29]. Существуют размерные ограничения, свойственные планарным процессам, однако использование в производстве электронно-лучевых, ион но-лучевых и рентгеновских методов позволяет создавать изделия с характерными разме рами вплоть до 10-25 нм. В свою очередь, прочностные характеристики зубчатых колес и ресурс передач могут быть существенно повышены объемной модификацией материала на наномасштабном уровне.
9.4. Пример использования лазерной технологии для изготовления миниатюрных зубчатых колес
В виде примера рассмотрим получение миниатюрных зубчатых колес на основе тех нологий выжигания и быстрого прототипирования из фотополнмеров с применением вы сокоэнергетического воздействия лазерного излучения [23].
Для получения прототипов и формообразующего инструмента, необходимого при из готовлении сверхминиатюрных зубчатых колес, определяются конструктивный, техноло гический производственный инварианты. Можно отметить, что наивысшая эффектнв-
362 |
Г л а в а 9 |
ность получения опытных образцов на стадии освоения новых для машиностроения тех нологических процессов [24], например, стереолитограф ии [25], достигается при использовании быстрого прототипирования (Rapid Prototyping).
Вкачестве конструктивного инварианта зубчатого колеса целесообразно взять пло ский элемент (слой). Предпочтительным технологическим инвариантом является опера ция выжигания материала заготовки с помощью излучения высокой интенсивности либо послойного выращивания изделия посредством фотополимеризации жидкой фазы.
Вобоих случаях представляется эффективным применение лазерного источника све та и использование в качестве производственного инварианта лазерной установки на ос нове оптического генератора. Помимо вышеназванных технологических преимуществ, ис пользование лазерной техники является эффективным средством обеспечения точности зубчатых колес с модулем зацепления, не превышающим десятые доли миллиметра.
Тем самым на одной установке могут изготавливаться как формообразующий инстру мент (матрица), так и непосредственно сложнопрофильные изделия, какими являются зубчатые колеса.
Стереолитография, ориентированная па фотополимеры, отверждающиеся под дейст вием УФ-излучения, ограничена высокой стоимостью и малым ресурсом лазеров ультра фиолетового излучения. Более предпочтительным является использование лазеров види мого и инфракрасного излучения, что оказывается возможным при наличии подходящих фотополимерных соединений [30].
Технологический процесс получения сверхминиатюрных зубчатых колес включает следующие последовательные этапы.
1.Получение исходной информации о геометрии зубчатого колеса.
2.САПР поверхности изделия.
3.Разработка компьютерной модели эвольвентиого профиля и переходной кривой зу ба, например, при помощи набора кривых различного радиуса.
4.Проектирование технологической модели. Изготовление прототипа изделия.
При реализации заключительного этапа важную роль играет качество маски, как эле мента формообразующего инструмента. Неизменяемая (жесткая) маска представляет со бой обычную матрицу и может быть изготовлена, например, из металла электроэрозионным методом при помощи проволочного электрода. Маска устанавливается на пути па раллельного пучка световых лучей, осуществляя его модуляцию. Затем производится пропорциональное уменьшение проецируемого контура при помощи сменных фокуси рующих объективов. Недостатком жесткой маски является невозможность быстрого уст ранения погрешностей, возникающих в результате неточностей оптической системы (люфты, тепловые деформации и т. д.).
Эти погрешности могут быть устранены при помощи динамических масок (рис. 9.14). В этом случае маска, изготовленная из низкомодульного материала, подвергается дефор мации для изменения в определенных пределах внешнего и внутреннего контура проеци руемого изображения.
Для испытаний могут быть использованы миниатюрные имитаторы зубчатого колеса в виде цилиндрических колец высотой Н, внешним D и внутренним d диаметром соответ ственно. Как показано на рис. 9.14, маска из непрозрачного эластомера, допускающего значительные обратимые деформации при сравнительно малых нагрузках, устанавлива ется между двумя стеклянными полированными пластинами. Нагружение пластин про изводится таким образом, чтобы обеспечить плоскопараллельное сжатие маски.
В связи с тем, что вопрос точности эвольвентиого зацепления играет весьма важную роль, представляет интерес анализ основных факторов, обусловливающих погрешность
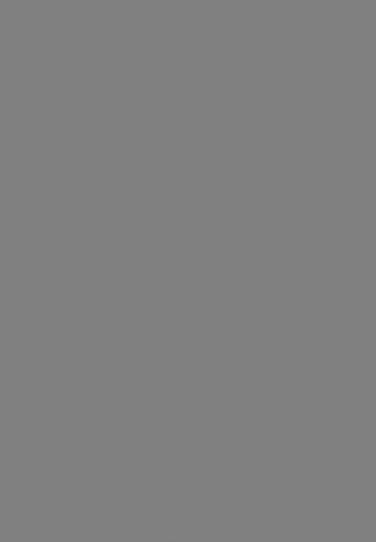

Технология изготовления зубчатых колес для микроэлектромеханических систем |
365 |
Литература
1.Madou М. Fundamentals of Microfabrication. CRC Press. New York, 1997.
2.Климом Д. M., Василис» A. A., Лучипии В. В., Мальце» П. П. Персисктииы развития микроснстсмной техники » XXI веке/ / Мпкросистсмиая техника, 1999,№ 3-6.
3.Peterson К. Silicon as a Mechanical Material / / Proc, of the IEEE, 1982,70, № 5,420-456.
4.Stadlcr F. A. Spitzcnlcistungcn in dcr Klassischcn Mikrobcarbcitung —cine Fragc der Gcistcshaltung// Tagungsband Micro-Engineering96, Stuttgart, 1996.
5.Hagcmann B. Entwicklung von Pcrmanentmagnct-Mikromotoren mit Luftspaltwicklung / / Theses, University of Hannover, Germany, 1999.
6.Корлякон A. M., Лучиннн В. В., Мальцев П. П. Микроэлсктромеханнчсская структура на основе композиции «карбид кремния-нитрид алюминия» / / Микроэлектроника, 1999, № 3,201-212.
7.Lcglcr J. Lcistungsverbalten von Hochfibcrsctzcndcn Strirnradgctricben und Râdcrkcttcn dcr
Gcratetcchnik, Theses, TU Dresden, 1989.
8. Thiirigcn C., Ehrfeld W., Hagcmann B„ Lehr H., Michel F. Development, Fabrication and Testing of a Multi-Stage Micro Gear System / / Tribology Issues and Opportunities in MEMS. Edited by
B.Bushan. Kluwer Academic Publishers. Dordrecht (Boston) 1998,397-402.
9.Ehrfeld W., Lehr H. Deep X-Ray Lithography for the Production of Three-dimensional Microstructurcs from Metals, Polymers and Ceramics / / Radiat., Phys. and Chemistry, 1995 (45) 3,349-365.
10.Лучинин В. В., Таиров 10. М. Особенности матсриалонсдчсского и технологического базиса мик росистем / / Мпкросистсмиая техника, 1999, № 1,7-11.
11.Michel F., Ehrfeld W. Microfabrication Technologies for High Performance Microactuators / / Tribology Issues and Opportunities in MEMS. Edited by B. Bushan. Kluwer Academic Publishers. Dordrecht (Boston) 1998,53-72.
12.Gruber H. P., Wolf A. Komponcntcn fur pSystcmc durch die pEDM / / Proc, of Microcngincering, 24-26.09.97, Stuttgart, 1997.
13.Weber L„ Ehrfeld W., Freimuth H., et al. Micro molding — a Powerful Tool for the Large Scale Production of Precise Microstructurcs / / Proceedings of Micromachining and Microfabrication Process Technology 2,14-15.10.96, Austin, Texas, 1996,156-167.
14.Wolf A., Ehrfeld W., Lehr H., et al. Combining LIGA and Electro Discharge Machining for the Generation of Complex Microstructurcs in Hard Materials. / / Proc. of 9-IPES/UME4 26-30.05.97, Braunschweig, Germany, Vol. 2,1997,657-660.
15.Friedrich C., Vasilc M. Development ofthe Micromilling Process for High Aspect Ratio Microstructurcs, J. MEMS 1996 (5) 1,33-38.
16.Coanc P., Friedrich C. Fabrication of Composite X-Ray Masks by Micromilling// Microlithography and Metrology in Micromachining II, SPIE. 2880,1996,130-141.
17.Vasilc M., Friedrich C., Kikkcri B., McElhannon R. Micron-Scale Machining: Tool Fabrication and Initial R esu lts// Precision Engineering 1997 (119) 2 /3 ,180-186.
18. Paul E„ Evans C., Mangamclli A.. Polvani R. Chemical Aspects of Tool Wear in Single Point Diamond T u rn in g // Precision Engineering, 1996 (18) 1,4-19.
19.Bier W„ Keller W., Linder G., Schubert K., Seidel D. Manufacturing and Testing of Compact Heat Exchangers with High Volumetric Heat Transfer Coefficients / / Microstructurcs, Sensors and Actuators, ASME DSC. Vol. 19.1990.
20.Friedrich C., Kang S. Micro Heat Exchangers Fabricated by Diamond Machining / / Precision Engineering 1994 (16) 1,56-59.
21.Friedrich C., Kithiganahalli B. Deflection Compensation Model for the Machining of Microshafts / / Proceedings of ASPE Annual Conference, Cincinnati, 1994,461-464.
22.Snicgovski J. J. Tribological Issues of Polysilicon Surface-Micromachining / / Tribology Issues and Opportunities in MEMS. Edited by B. Bushan. Kluwer Academic Publishers. Dordrecht (Boston) 199S, 325-340.
23.Deng K„ Collins R. J., Sukenik C. N. Perfomance impact of monolayer coating of polysilicon micromotors / / J . Elcctrochem. Soc., 142 (4): 1278,1995.
366 |
Г л а в а 9 |
24.Krause W. Konstruktionsclcmcntc tier Fcinwcrktcchnik, Carl Hanscr Verlag, München, Wien, 1993.
25.Stark K. G, Mehregany M., Phillips S. M. Analysis of Gear Tooth Performance on Mechanically-Coup led, Outer-Rotor Polycilicon Micromotors //T ribology Issues and Opportunities in MEMS. Edited by B. Bushan. Kluwer Academic Publishers. Dordrecht (Boston) 1998,403-406.
26.Shiglcy J. E. Kinematic Analysis of Mechanisms. McGraw-Hill, Inc., New York, 1969.
27.Mehregany M., Senturia S. D., Lang J. H. Measurement of Wear in Polysilicon Micromotors / / IEEE Trans, on Electron Devices, ED-39, Sept. 1992,2060-2069.
28.Броулай И., Мерей Дж. Физические основы микротехпологин / Пер. с англ. - М.: Мир, 1985.
29.Плескачевский Ю. М. Перспективы применения новых материалов в электротехнической про мышленности / Проблемы современного материаловедения. Труды 4 сессии Научного совета но новым материалам МААН, 6.07.99, Киев, 1999,46-52.
30.Толочко Н. К., Хлопков 10. В., Спиридонов Э. П., Линсвич А. В. Материалы и источники излуче ния для стереолитографии (Обзор) / / Материалы, технологии, инструменты, 2000, № 3,35-38.
31.Шилько С. В., Старжинский В. Е. Разработка технологии изготовления зубчатых колее для мнкроэлсктромеханичсских систем / / Современные информационные технологии. Проблемы исследо вания, проектирования и производства зубчатых передач. Ижевск, 2001.
ЧАСТЬ III
МЕТОДЫ ОБЕСПЕЧЕНИЯ КАЧЕСТВА ЗУБЧАТЫХ КОЛЕС
И ПЕРЕДАЧ

Глава 10
ПОГРЕШНОСТИ МЕХАНИЧЕСКОЙ ОБРАБОТКИ ЗУБЬЕВ ЦИЛИНДРИЧЕСКИХ ЗУБЧАТЫХ КОЛЕС И ПУТИ ИХ УМЕНЬШЕНИЯ
10.1. Основные факторы, влияющие на точность зубообработки
На точность зубообработки цилиндрических зубчатых колес, как и на точность меха нической обработки вообще, влияют следующие основные факторы:
1.Точность изготовления элементов технологической системы (ТС) — станка, при способления, инструмента, заготовки.
2.Точность настройки станка и установки инструмента и заготовки.
3.Упругие деформации элементов ТС из-за нестабильности сил резания и нежесткости этих элементов.
4.Износ, тепловые деформации элементов ТС в процессе обработки, перераспределе ние внутренних напряжений в заготовке на различных операциях и др.
Выделяют геометрическую, кинематическую и динамическую составляющие точно сти станков. Геометрическая точность станка определяется точностью размеров, формы и взаимного положения элементов станка в статическом состоянии. Кинематическая и ди намическая точность станка проявляются при его эксплуатации. Первая определяется точностью взаимного наложения всех элементов ТС в течение всего времени обработки детали, вторая — колебаниями значений показателей кинематической точности станка из-за нежесткости его элементов и периодического изменения действующих на них сил. Кинематическая и динамическая точность станка оказывают особенно большое влияние на точность зубообработки при обработке зубьев по методу обката.
Точность формы, размеров и расположения боковых поверхностен зубьев определя ется точностью и постоянством взаимных положений производящего контура и изделия в каждый момент времени. Погрешности взаимного положения каждой сопряженной точки производящего и обрабатываемого контуров складываются из: а) погрешностей относи тельного положения инструмента и заготовки в пространстве, создаваемых неточностями изготовления и настройки станка и оснастки, а также неточными движениями обкатки;
б) погрешностей самого профиля производящего контура (инструмента). Кинематическая точность станка не имеет значения в станках, работающих по методу
свободного обката (шевинговальных, зубохошшговальных, зубообкатных, зубопрнтирочных и др.), поскольку движение обкатки на этих станках происходит в результате непо средственного зацепления инструмента и изделия.
370 |
Г л а в а 10 |
При изготовлении зубчатых колес по способу копирования профиля первостепенное значение приобретают погрешности самого инструмента и базирования инструмента и за готовки на станке, геометрическая точность и жесткость станка. При изготовлении зубча тых колес по способу обката возрастает значение кинематической и динамической точно сти станка.
10.2. Характер и классификация погрешностей зубообработки
Все процессы формообразования и отделки зубьев цилиндрических зубчатых колес являются прерывистыми и периодическими по причинам прерывистости расположения зубьев колеса на его венце, ограниченного числа зубьев инструмента, характера взаимо действия колеса и инструмента при обработке зубьев. Синусоидально изменяющиеся ошибки зубообработки возникают также по причинам гармонических ошибок вращаю щихся элементов ТС, зубообрабатывающего станка (зубчатых колес, валов, заготовки, ин струмента и др.) и погрешностей зубьев заготовки, возникших на предыдущих операциях.
Практика показывает, что в реальных зубчатых колесах заметно проявляется ограни ченное число гармонических колебаний, вызванных: а) погрешностями установки колеса при зубообразовании; б) биением в зубообрабатывающем станке делительного колеса; в) биением червяка делительной передачи станка; г) биением зуборезного инструмента; г) осевым биением ходового винта (табл. 10.1).
Эти неточности соответственно обнаруживаются: а) по радиальному биению зубчато го венца; б) по накопленной погрешности окружного шага, измеряемого от базы при зубообработке; в) по продольным полосам, наблюдаемым на косозубых колесах, или цикличе ским погрешностям соответствующей частоты; г) по синусоидально изменяющимся по грешностям профиля; д) по волнистости боковой поверхности зубьев косозубых колес (см., например, работы [1-7]).
Другие периодические погрешности в нормальных условиях оказывают малое влия ние и проявляются лишь в случае, когда их величины значительно превышают техниче ски допустимые нормы. Влияние же всех случайных ошибок, не имеющих периодическо го характера изменения, составляет единицы процентов от общей погрешности колеса и с достаточной точностью может рассматриваться отдельно [1].
Периоды колебаний составляющих периодической ошибки колеса связаны между со бой соотношением [1]:
Г, = 2Т2= З73 = ... = iTb
где 7] — период основного колебания, равный 2пп\ п — число оборотов колеса при зубонарезании; Т2, Т3..... 7} — периоды составляющих ошибки колеса.
Рассмотрение ошибок колеса в виде периодической функции позволяет по-новому подойти к решению ряда практических задач. Наиболее существенными из них являют ся: нахождение ошибок изделия по частным синусоидальным колебаниям, действую щим в процессе изготовления зубчатых колес; отыскание правильных методов измере ния общей периодической ошибки колеса и разложение ее при технологическом анализе на ряд отдельных гармонических составляющих для определения периода, амплитуды и начальной фазы с целью обнаружения первоисточников общей периодической ошибки колеса; нахождение связей между периодической ошибкой и проявлением ее при работе данного зубчатого колеса в передаче в виде шума, вибраций, динамических нагрузок.