
книги / Технология производства и методы обеспечения качества зубчатых колес и передач
..pdfМатериалы, методы и технология изготовления зубчатых колес из пластмасс 311
Рис. 8 .2 1 . Схема отлиоки зубчатого колеса с |
Рис. 8 .22 . Схема отливки зубчато |
|
го колеса с четырехточечным рас |
||
различным расположением впускных литников: |
||
положением впускных литников |
||
а — трехточечный литник диаметром 1 мм на |
диаметром 1 мм на торцевой по |
|
диаметре 13 мм через каждые 120°; б — четы |
верхности удлиненной ступицы |
|
рехточечный литник диаметром 1 мм через каж |
(m = 0,5MM,z = 60) |
|
дые 90е (т = 0,5 мм, z =40) |
||
|
Анализ вида отливок зубчатых колес показывает [38J, что при трехточечном впуске (рис. 8.21, а) вершины зубьев отливки, находящихся вблизи литниковых впусков, заполня ются неравномерно, наблюдается некоторое временное запаздывание, образуется перепад давления, результатом является анизотропия усадки по диаметру вершин зубьев. При четырехточечиом впуске (см. рис. 8.21, б, рис. 8.22) вершины зубьев заполняются расплавом син хронно, отмечены сбалансированность давления по периферии зубчатого венца и равномер ность скорости охлаждения отливки. В результате точность зубчатых колес повышается.
Центрирующие элементы. Центрирование полуформ относительно осей ТПА обеспе чивают центрирующие фланцы Fw75, Fw80, Fw85. Фланцы типа Fwl5 — круглые из стали 1.1730 (Сталь 45) диаметрами: 090, 125, 160, 175, 200 мм, выполненные с точностью /8. Fw80 и Fw85 — ступенчатые фланцы. Меньший диаметр — 090/8 для установки в плиту крепления АР.2 в цековку 0907/7x4, а больший диаметр — для монтажа полуформы на плиту ТПА. Fw85 — монолитный фланец, a Fw8Q имеет по центру коническое отверстие 036, с углом при вершине 90°.
Для центрирования полуформ друг относительно друга используется комплект эле ментов: направляющая колонка 7М 6, направляющая втулка ТМ 8 и центрирующая втул ка 7а/19. Дополнительное центрирование формообразующих деталей форм друг относи тельно друга обеспечивают конические пары FwAO с регулировочными шайбами fw41 и FwA2. Если же более жесткое центрирование необходимо обеспечить не только в послед ний момент смыкания полуформ, по и в процессе смыкания, то используют призматиче ские пары FwA5 из стали 1.7131 со специальным износостойким патентованным покрыти ем Lamcoat.
Толкатели Aw (по-английски Ejectorpins, по-немецки Auswerferstifte) — подвижные де тали системы выталкивания форм, обеспечивающие извлечение отливки после или во вре мя раскрытия полуформ. В каталоге представлены пять типов нормализованных цилиндри ческих толкателей: простые цилиндрические с цилиндрической Лг«215 н конической Ли>220 головками, ступенчатые Aw 252, плоские Aw262 и трубчатые HI272 (табл. 8.18). В литерату ре [39,40] даны рекомендации по установке толкателей в плитах. Посадка tf7/g6 обеспечи вает безоблойную работу толкателей при литье любых пластмасс.
312 |
|
Глава 8 |
|
|
|
Таблица 8.18 |
|
|
Типы цилиндрических толкателей |
||
Типы |
Обозначение, |
Техническая характеристика |
|
толкателем |
стандарт |
||
|
|||
Ла/215 |
Ejectorpin. DIN 1530 |
С гладким цилиндрическим стержнем и цилиндрической го |
|
|
|
ловкой |
|
Aw220 |
Ejectorpin. DIN 1530 |
С гладким цилиндрическим стержнем и конической головкой |
|
C-Aw252 |
Shouldered ejectorpin, |
С цилиндрическим ступенчатым стержнем и цилиндрической |
|
|
Step pin DIN 1530 |
голоикой |
|
F-Aw262 |
Flat ejectorpin, blade |
Со ступенчатым стержнем, несущая часть —цилиндрическая, |
|
|
ejectorpin. DIN 1530 |
рабочая —прямоугольная |
|
Aw212 |
Ejectorsleeve |
С гладким цилиндрическим стержнем трубчатого сечения и |
|
|
|
цилиндрической головкой |
Элементы системы охлаждения (термостатирования). Для обеспечения циркуляции термостатирующей жидкости (вода, масло) в канале формообразующей детали (пуансон, матрица, вставка) рекомендуется использовать перегородки Wb700 {Baffle ribs), применяе мые в каналах 0 6 ,8 ,1 0 ,1 2 ,1 4 мм из стеклонаполненного полиамида ПА 66-GF35, толщи ной 1 или 1,5 мм. Они легко монтируются и демонтируются в пресс-форме и герметизиру ются за счет разжима уплотнительных колец специальной латунной втулкой. Более ин тенсивный теплообмен обеспечивает фонтанирующая трубка Т2000 {Compact components fo r core heating and cooling). Теплоагент поступает внутрь трубки и, фонтанируя из торца, двигается с наружной стороны ее. Трубки выпускаются следующих диаметров: 00,8; 1,25; 1,65; 2,40; 2,95; 3,00; 3,30; 4,00; 5,00; 5,45; 6,00; 7,95 мм с длинами 160 или 300 мм. Зазор ме жду трубкой и стенкой отверстия должен составлять от 0,1 до 1 мм. Наиболее эффектив ными элементами системы термостатирования являются специальные турбулизаторы А Т {Turbo-spirals fo r cooling), устанавливаемые в глухие каналы с зазором 0,5 мм на сторону. Турбулизатор представляет собой трубку с внутренним диаметром: 4, 6, 8, 10, 12, 17, 20 или 23 мм, у которой снаружи находятся ребра в виде волнистой спирали с наружным диаметром 12, 14, 16, 24, 32, 36-38 мм соответственно и длиной от 100 до 225 мм.
Подсоединение форм к системе термостатирования производится посредством быстро съемных соединений, состоящих из муфты и ниппеля. Муфты и ниппели имеют исполне ние с запорным клапаном М 1 0 /5 Ш и без него M kiOO /Stil. Муфта присоединяется к пресс-форме и отсоединяется практически мгновенно; штуцер монтируется в цековку на плите пресс-формы, поэтому не подвергается механическому воздействию при монтаже/демонтаже пресс-формы и хранении, а, значит, герметичность соединения не нарушается.
Работа системы выталкивания в две стадии обеспечивается агрегатами двойного вы талкивания Л»1800 и /то1850. Механизм /0/1800 обеспечивает на первой стадии движение обеих ступеней, а затем первая ступень останавливается, а вторая продолжает движение. Механизм /а/1850 обеспечивает сначала движение первой ступени, а затем второй.
Вывинчивание резьбовых знаков из пресс-формы производится м еханизмом винт -гайка: винты многозаходные WzlOOO с левой «Z.» и правой «7?» резьбой и гайки под них из латуни Wzl020 или металлопластиковые WzlOlO; вал-ш естерни Wz1030 и зубча тые колеса И£1040 для передачи вращения от гайки на вал-шестерни.
Для извлечения знаков под углом к плоскости разъема применяют гидроцилиндры
#Z160, НР70, HP8Q или механизм привода наклонных знаков SD /CI, оформляющих не большие поднутрения на наружной поверхности отливки.
Материалы, методы и технология изготовления зубчатых колес из пластмасс 313
Принудительный возврат системы выталкивания в исходное положение обеспечи вает шариковый затвор /401950/1951. Муфта Fre>1950 завинчивается в форму вместо штатного хвостовика, а упор Frol951 - в гидровыталкиватель ТПА.
В каталоге [37] представлен широкий выбор пружин: витые пружины типа Wz8029 и Wz8030 четырех серий (зеленые, синие, красные, желтые) повышенной жесткости из про волоки прямоугольного сечения из специальных пружинных сталей; тарельчатые пру жины Wz8050 с размерами от 8,0 х 3,2 х 0,4 до 80 х 36 х 3 мм; полиуретановые пружины Wz8010 с размерами от 16 х 12 до 100 х 100 мм.
Более подробную информацию об унифицированных деталях литьевых форм чита тель найдет в информационном материале [37] инженерной фирмы АБ-Универсал.
8.5.4. Оптимизация допусков и посадок сопрягаемых деталей литьевых форм
При выборе конструкции литьевой формы для изготовления зубчатых колес следует иметь в виду, что минимальное биение колеса можно получить, применяя одноместную форму, в которой матрица и центральный знак расположены в одной полуформе. Количе ство сопрягаемых деталей в цепи «центральный знак-матрица» должно быть минималь ным. Поэтому при конструировании формы для литья зубчатых колес не следует использо вать промежуточные втулки, обоймы, трубчатые толкатели и т. п. Стержневые толкатели можно применять при отливке прямозубого колеса, если его диаметр позволяет разместить толкатели. В противном случае применяют трубчатые толкатели. На рис. 8.23, а представ-
|
|
а |
|
|
|
|
|
|
б |
|
|
|
|
|
в |
|
|
|
3 |
1 |
5 |
4 |
2 |
6 |
4 |
1 |
3 |
2 |
7 |
8 |
9 |
1 |
3 |
10 |
4 |
2 |
7 |
Рис. 8 .23 . Варианты сопряжения центрального знака и зубчатой матрицы: а — нерекомендуе мый; б, а — предпочтительные ( 1 — центральный знак; 2 — зубчатая матрица; 3 — толкатель; 4 — плита; 5 — втулка; 6 — обойма матрицы; 7 — кольцо крепления; 8 — опорная плита; 9 — толка тель; 10 — промежуточный стакан)
314 |
Глава 8 |
лены нерекомендуемый, а на рис. 8.23, б, в — предпочтительные варианты конструкции со пряжения центрального знака и зубчатой матрицы.
Допуски на радиальное биение посадочных мест матрицы и центрального знака назна чают по 3-5 квалитетам точности (ГОСТ 25346-88). Для подвижных соединений в размер ной цепи «центральный знак-матрица» применяют посадки с зазором H 6/h5; Н7/И6, а для неподвижных - И6/к5; Н7Д6; Н6/Ь5; И7/Ь6. В табл. 8.19 приведены варианты назначения посадок сопряжений (рис. 8.23, а). В табл. 8.20 для каждого варианта приведены результаты расчета достигаемой точности по радиальному биению зубчатого венца отливаемых зубча тых колес модулей 0,1-1,5 мм при диаметре делительной окружности 12-80 мм; точность матрицы соответствует 6-й степени точности по ГОСТ 9178-81 или ГОСТ 1643-81. В зави симости от длины размерной цепи и сочетания назначаемых посадок достижимая точность отливаемых зубчатых колес колеблется от 7-й до 11-й степени; иаилучший результат реали зуется при использовании варианта со стержневым толкателем.
Таблица 8.19
Варианты посадок, применяемых в сопряжениях размерной цепи «центральный знак-матрица»
|
|
|
|
Вариантыпосадки «огвсрстис-иад» |
|
|||
Сопрягаемыелетали |
|
|
Рис. 8.23, а |
|
|
Рис. 8.23, б |
||
|
|
|
1 |
2 |
3 |
4 |
5 |
6 |
Центральный знак-корпус |
|
H6/h5 |
Н6Д5 |
H7/h6 |
H6/h5 |
H7/h6 |
Н6Д6 |
|
Корпус-матрица |
|
|
H6/h5 |
Н5Д5 |
Н7Д6 |
Н6Д5 |
Н7Д6 |
Н6Д5 |
Центральный знак-трубчатый толкатель H6/li5 |
H6/li5 |
H7/h6 |
|
|
|
|||
Втулка-толкатсль |
|
|
H7/s6 |
H7/s6 |
H7/s6 |
|
|
|
Втулка-корпус |
|
|
|
|
|
|
|
|
|
|
|
|
|
|
|
Таблица 8.20 |
|
Достигаемая степень точности зубчатых колес по радиальному биению венца |
||||||||
|
|
|
Достигаемая степень точности колеса |
|
||||
Модуль, |
Вариант |
|
при значениях делительного диаметра d, мм |
|
||||
TH, MM |
но табл. 8.19 |
|
свыше 12 |
свыше 20 |
свыше 32 |
свыше 50 |
||
|
|
до 12 |
||||||
|
|
|
до 20 |
до 32 |
до 50 |
до 80 |
||
|
|
|
|
|||||
От 0,1 до 0,5 |
4 |
7 |
|
7 |
7 |
7 |
|
7 |
|
5 |
7 |
|
7 |
7 |
8 |
|
8 |
|
6 |
9 |
|
9 |
9 |
9 |
|
9 |
|
1 |
9 |
|
10 |
10 |
10 |
|
10 |
|
2 |
10 |
|
10 |
10 |
10 |
|
10 |
|
4,5 |
7 |
|
7 |
7 |
7 |
|
7 |
Свыше 0,5 до 1 |
6 |
8 |
|
8 |
8 |
8 |
|
8 |
Свыше 1,0 до 1,5 |
1 |
8 |
|
9 |
9 |
9 |
|
9 |
2 |
9 |
|
9 |
9 |
9 |
|
9 |
|
|
3 |
10 |
|
10 |
10 |
10 |
|
11 |
|
4,5 |
7 |
|
7 |
7 |
7 |
|
7 |
|
6 |
7 |
|
7 |
7 |
8 |
|
8 |
|
1 |
7 |
|
8 |
8 |
8 |
|
8 |
|
2 |
8 |
|
8 |
9 |
9 |
|
9 |
|
3 |
9 |
|
9 |
10 |
10 |
|
ю _ |
Материалы, методы и технология изготовления зубчатых колес из пластмасс 315
8 .5 .5 . Ко нструкции литьевых форм для зубчатых колес
При изготовлении прецизионных литых изделий, особенно зубчатых колес, полость детали образуется в отдельной матрице формы. Это обеспечивает ряд преимуществ. Пре жде всего такая матрица лучше обрабатывается и полируется. При повреждении или из носе ее легче заменить. Возможна также замена матриц при изготовлении незначительно различающихся деталей. Упрощается проблема вентилирования, так как вентиляционные (газоотводящие) каналы можно располагать в плоскостях разъема формы. Предпочти тельными для изготовления зубчатых колес являются одногнездные формы, обеспечи вающие лучшую воспроизводимость размерных параметров изделия.
Однако на практике часто применяются многогнездные формы, что обусловлено эконо мическими и технологическими факторами. Естественно, для каждой детали или изделия следует производить новый расчет и принимать решение об оптимальной гнездности формы.
Многогнездные формы следует проектировать как трехплитные, а одиогнездные — как двухплитные. При многогнездиых формах расположение отдельных полостей фа сонной заготовки особенно важно для обеспечения высокой точности деталей. Для пре цизионных деталей должно применяться только звездчатое или симметричное, но не по следовательное расположение гнезд, так как в последнем случае невозможно обеспечить одинаковую длину разводящих каналов.
При конструировании форм для косозубых колес необходимо учитывать, что при вы талкивании отливка, двигаясь по зубьям матрицы как по направляющим, поворачивается на некоторый угол, определяемый углом наклона зубьев и шириной зубчатого венца, что требует применения поворотного толкателя.
На рис. 8.24 показан вариант литьевой формы для косозубого зубчатого колеса с глад ким посадочным отверстием, в которой поворот толкателя обеспечивается за счет нсполь-
8 7 4 3 2 5 1 6
t>|<]
Рис. 8.24 . Литьевая форма с поворотным толкателем для косоэубого цилиндрического колеса
3 1 6 Г л а в а 8
зования подшипника качения. Стержневой толкатель 1 опирается на обойму с шариками 2, которые расположены на кольце упорного подшипника 3, установленного в расточке плиты толкателей 4. В зависимости от усилия выталкивания можно устанавливать ради альные, радиально-упорные или упорные подшипники. Возврат толкателя 1 в исходное положение после извлечения отливки 6 из оформляющей полости производится крепеж ной плитой 7, взаимодействующей с фланцем толкателя, под действием возвратных пру жин 8. Свободное вращение толкателя обеспечивается зазором а между крепежной пли той и фланцем толкателя, которой назначается 0,1-0,3 мм.
При изготовлении косозубого зубчатого колеса со шпоночным или шлицевым поса дочным отверстием возможность поворота при выталкивании отливки должен иметь и центральный знак. Один из вариантов такой конструкции представлен на рис. 8.25. Цен тральный знак 1 имеет бурт, которым он опирается на упорный подшипник 2, установлен ный в расточке плиты толкателей 3. При выталкивании отливки между буртом централь ного знака 1 и плитой основания 4 за счет выборки зазора а образуется свободное про странство, которое обеспечивает поворот центрального знака. При изготовлении зубчатого колеса с металлическим диском и полимерным зубчатым венцом трубчатый толкатель 5 может выполняться неподвижным.
Литьевая форма с компенсирующим элементом и приводной пружиной большой мощности [41] (рис. 8.26) содержит матрицу 3, которая расположена в корпусе 4, установ ленном на основании 1, подпружиненном относительно основания пуансона 5 (торец ко торого расположен в оформляющей полости 6), и промежуточную плиту 7, установлен ную таким образом, что она может взаимодействовать с пуансоном 5; ползуны 8, опираю щиеся на промежуточную плиту 7 размещенными в них подпружиненными сухарями 9; толкатели 10, взаимодействующие с передней плитой. Пуансон 5 расположен на цен тральном знаке 11 и имеет упор 12, взаимодействующий с сухарями 9, и демпфирующие элементы 13, расположенные на толкателях 14, проходящих через пуансон 5. Наличие
4 3 2 1 5
Рис. 8 .2 5 . Литьевая форма с поворотным центральным знаком для литья косозубых колес с поса дочным отверстием, имеющим шпоночную канавку
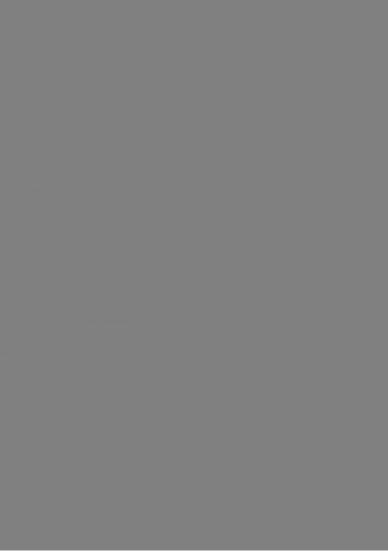
318 |
Г л а в а 8 |
|
Рис. 8 .2 7 . Литьевая форма с подвижной подпружиненной матрицей
ной возможностью перемещения и подпружиненными относительно нее компенсирующи ми элементами 7, снабженными ограниченными буртами 8; промежуточную подвижную плиту 9, жестко связанную с компенсирующими элементами 10 и подпружиненную относи тельно матрицы 5 в направлении оформляющей плиты 2; центральный знак 11, закреплен ный в основании 1. Оформляющая плита 2 и центральный знак 11 выполнены соответст венно с выступами 12 и продольными ребрами 13, сопряженными с продольными пазами 14 на внутренней поверхности матрицы 5. Такое конструктивное решение позволяет повы сить качество изделия за счет использования компенсирующих элементов 7 и 10, переме щающих подвижный знак 15 и матрицу 5 относительно выступов 12 на оформляющей пли те 2; для подпрессовки при охлаждении полимерного материала со стороны торцовых по верхностей изделия. При подаче расплава полимерного материала в оформляющую полость 18 под действием давления расплава подвижный знак 15 перемещается влево, передвигая компенсирующие элементы 7 до упора ограничительными буртами 8 в плиту 6 выталкива ния, а матрицу 5 — до упора в выступ на корпусе 4. При охлаждении расплава и снижении давления в оформляющей полости 18 подвижный знак 15и матрица 5 под действием усилий сжатия пружин возвращаются в исходное положение, матрица 5 упирается в оформляющую плиту 2, а промежуточная подвижная плита 9 прижимается к матрице 5 и через прокладки
16фиксирует положение подвижного знака 15. Готовое изделие выталкивается подвижным знаком 15 после раскрытия формы при перемещении вправо плиты 6.

320 Г л а в а 8
Метод элсктроэрозиоипой обработки. Суть метода электроэрозионной обработки за ключается в том, что слой материала снимают с помощью электрического разряда, возни кающего между специальным электродом и обрабатываемой поверхностью в среде диэлектрической жидкости. Преимуществами метода являются его универсальность, воз можность обработки высокотвердых материалов с высокой точностью, высокая произ водительность. Применение электроэрозии позволяет ускорить процесс получения осна стки при обеспечении высокого качества, особенно для прецизионных деталей сложной формы.
Общие требования к станкам для электроэрозионной обработки — возможность на дежного крепления обрабатываемой заготовки, обеспечение прецизионного взаимного пе редвижения электрода и заготовки, чистоты диэлектрической жидкости и ее подачи в зо ну обработки, передачи импульсов электрического тока от генератора в рабочую зону. Об рабатываемые заготовки выполняются из электропроводного материала, не вступающего в химическую реакцию с водой, водородом и кислородом.
Зазор между обрабатываемой поверхностью и электродом при электроэрозионной об работке составляет около 10 мкм. В процессе обработки он заполняется частицами снято го материала, уменьшающими его первоначальную величину. Для поддержания постоян ного зазора конструкция оборудования должна обеспечивать возможность оперативного контроля за величиной зазора и его регулирования.
Качество обработки во многом зависит от конструкции зажимных приспособлений и точности перемещений заготовки и проволоки электродов в различных направлениях. Со временное оборудование позволяет обеспечить отклонение от требуемых направлений пе редвижения не более 10 мкм.
Производительность процесса элекгроэрозии зависит от разрядного тока, длительности электрического импульса и глубины реза. Повышение производительности электроэрозии и выбор параметров технологического процесса тесно связаны с точностью обработки и вели чиной шероховатости обрабатываемой поверхности. При большей продолжительности элек трического импульса и величины разрядного тока производительность процесса возрастает, однако при этом повышается и шероховатость поверхности. В зависимости от предъявляе мых требований к точности детали можно выбрать режимы, обеспечивающие различные по грешности. Так, при использовании проволоки-электрода диаметром 0,25 мм на станке AGIECUT100D получены результаты, приведенные в табл. 8.21.
Достижимые классы точности и величины шероховатости при электроэрозионной об работке, зависящие от поставленной цели, возможностей оборудования и квалификации персонала, приведены в табл. 8.22.
Современные электроэрозионные станки швейцарской фирмы AG IE марки AGIECUT, работающие с проволочным электродом, обеспечиваются системой ЧПУ, которая позво ляет осуществлять оперативный диалог с управляющей системой и программирование технологического цикла с контролем всех параметров.
|
|
|
|
Таблица 8.21 |
|
Достижимая точность и шероховатость поверхности |
|
|
|||
|
при различных режимах резания |
|
|
||
Параметр |
|
Режим резания |
|
|
|
быстрое |
|
|
тонкое |
|
|
|
качсстисшюе |
прецизионное |
|
||
Точность, мкм |
±30 |
±15 |
±10 |
±6 |
|
Шероховатость Ra , мкм |
1,8 |
1,7 |
1.4 |
0,5 |
_ |