
книги из ГПНТБ / Скуридин, А. В. Склеивание и сращивание деталей стандартных домов и столярных изделий
.pdf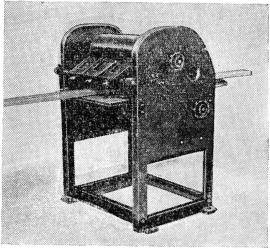
нанесения клея распылением более экономичен, производителен, может тонко регулироваться, но сложен. Более доступно и пред почтительно нанесение клея клеевыми вальцами.
Рис. 9. Схема размещения оборудования в отделении клееных деталей:
1 — место для заготовок; 2 — клеевые вальцы; 3 — столы для сухой сборки; 4—Л'ресс-вагснеткн; 5 — механические ключи; 6 — траверсная тележка;
7 — камера прогрева
Рис. 10. Клеевые вальцы
Клеевые вальцы. Наилучшую намазку дают вальцы с верхним намазывающим валиком и механической подачей (рйс. 10). Основанием их служат две чугунные рамы, соединенные между собой горизонтальными связями. На кронштейне, укрепленном на правой раме, установлен электродвигатель с редуктором. От редуктора вращение получает нижний подающий валик и через шестерни и цепную передачу — большой верхний валик диамет
19
ром 300 мм, который при вращении набирает на себя клей и пере дает его на соприкасающийся с ним маленький валик, получающий вращение от большого через цепную передачу. Маленький валик наносит клей на склеиваемые детали. Толщину слоя клея регули руют специальными скребками, установленными за большим ва
ликом. Ванна для клея и 'верхние вальцы съемные. |
Это удобно |
|
для промывки их, что весьма ценно при работе |
со |
смоляными |
клеями. |
|
|
Техническая характеристика клеевых вальцов |
|
|
Ширина, мм.................................................................................... |
|
500 |
Наибольшее расстояние междувальцами, мм . |
|
50 |
Мощность электродвигателя, кет........................................... |
|
0,6 |
Число оборотов в минуту.................................................... |
1410 |
|
Вес, кг..................................................................... |
|
300 |
Клей рекомендуется наносить на одну из склеиваемых поверх ностей ровным слоем. Толщина клеевого слоя не более 0,3 мм. Расход клея составляет 300—400 г на 1 м2 намазываемой поверх ности. Конструкция вальцов разработана Научно-исследователь ским институтом организации, механизации и технической помо щи строительству (Индустройпроект).
Клеевые вальцы, также как клеемешалка и кисти, при изго товлении клееных деталей очень сильно загрязняются клеями, по этому по окончании смены их нужно очистить и промыть. Если применяли формальдегидные клеи, то оборудование промывают сначала 10%-ным раствором щелочи (едкий натр и др.), а затем водой; казеиновый и казеино-цементный клеи смываются горячей водой.
Склеивание деталей смолами лучше всего производить при температуре воздуха в помещении не ниже 16°, казеиновыми и ка зеино-цементными клеями — при температуре не ниже 12°, мезд ровыми и костными клеями — при температуре не ниже 16°.
Влажность воздуха в цехе должна соответствовать равновес ной влажности древесины.
Склеивание производят по заранее разработанной технологии рабочие, прошедшие специальное обучение. При этом необходимо проводить межоперационный контроль за качеством и влажностью древесины, качеством обработки, размером склеиваемых загото вок, вязкостью клея, его расходом, качеством нанесения клея, удельным давлением, технологическими выдержками, температу рой и влажностью воздуха в клеильном цехе и т. д.
Заготовки, намазанные клеем, выдерживают в течение 10— 15 мин. (открытая пропитка), затем собирают, снова выдержива ют в собранном виде (закрытая пропитка) и запрессовывают' в пресс-вагонетке. При склеивании .в пресс-вагонетке в связи с не большим сроком выдержки собранной детали перед запрессовкой необходимо заранее тщательно продумать организацию работ, обеспечивающую минимальные сроки сборки склеиваемых дета лей, а также производить предварительную сухую сборку.
20

Пресс-вагонетка (рис. 11 и 12) предназначена для склеи вания брусков разных изделий под давлением. Конструкция ее разработана ИндуСтройпроектом. Пресс-вагонетка представляет собой ряд винтовых вайм из швеллеров, закрепленных на ваго нетке, передвигающейся по узкой колее.
Рис. II. Пресс-вагонетка с механическим ключом
Чтобы облегчить загрузку изделий на вагонетку, наружные вер тикальные тяги ее делают откидньими. Боковой прижим склеива емых деталей осуществляется откидными струбцинами, установ ленными по две с каждой стороны вагонетки, а также при помо щи вертикальных деревянных брусков и упоров.
Детали укладывают рядами под болты пресс-вагонетки. Каж дый ряд тщательно 'выравнивают в вертикальной плоскости, при чем первый прижимается к ее стойкам, а последующие ряды — к прокладкам между ними.
'После того как в вагонетку уложат шесть рядов склеиваемых брусков, завинчивают вертикальные прижимные и боковые винты. При этом следят, чтобы ось винта совпадала с осью пакета. Меж ду верхней заготовкой склеиваемого пакета и зажимными винта ми прокладывают деревянный брусок для передачи равномерно го давления по всей поверхности прессуемых заготовок. Верти кальные винты обеспечивают удельное давление на склеиваемые детали до 8—9 кг/см2.
Емкость вагонетки в зависимости от |
изделия достигает 1,5 м\ |
В ней 'можно' склеивать (как на пласть, |
так и на ребро) бруски и |
доски длиной до 2,5 м. Склеивая бруски на ребро, нужно обяза тельно применять прокладки и боковые упоры. При небольших допусках на обработку необходимо тщательно следить за вырав-
21
Рис. 12. Схема шреос-вагонетки

киванием склеиваемых деталей в вертикальной плоскости. Для этого должен быть обеспечен хороший боковой прижим каждой пачки.
Склеивая профильные детали, хороший результат можно полу чить, применив прокладки необходимой формы.
При склеивании узких деталей рекомендуется устанавливать с каждой стороны вагонетки по ряду дополнительных прижимных винтов (14 шт.). Это повысит ее производительность.
Винты пресс-вагонет.ки завинчиваются либо вручную, либо при помощи специального приспособления — механического ключа. При завинчивании винтов вручную передаваемое им удельное давление неравномерно. Это удлиняет время склеивания, а также затрудняет процесс прессования. Лучшие результаты получаются, когда для этой цели используют механический ключ, разработан ный Индустройпроектом и испытанный ЦНИИСКом и Гипростандартдомом при проведении экспериментальных работ.
Рис. 13. Механический ключ
Механический ключ (рис. 13) состоит из неподвижной стойки, на которой монтируют консоли из шарнирных рычагов. На них установлен электродвигатель с редуктором, приводящий в дви жение шпиндель, на конце которого закреплен винтовой ключ. Электродвигатель соединен с редуктором специальной муфтой пре дельного момента, которая может быть отрегулирована на пере дачу необходимого давления. Предельный момент, передаваемый муфтой, может быть до 2 тыс. кг ■ см.
Поднимают и опускают шпиндель специальной рукояткой, на которой расположены две кнопки управления — «завинчивание» и «отвинчивание». Для завинчивания головку ключа устанавли-
23
вают на головку винта и кнопкой включают электродвигатель с редуктором.
Механическим ключом завинчивают винты от середины к кра ям или от одного края до другого. Завинчивать винты ют краев к
•середине не рекомендуется. Чтобы ускорить этот процесс, сле дует в период распрессовки отвинчивать винты на величину, кото рая необходима для последующей запрессовки.
С помощью ключа можно завинчивать винты в радиусе до 2 м. Это дает возможность завинчивать все вертикальные винты прессвагонетки из одного положения. Приспособление обслуживает один рабочий.
При холодном способе склеивания npetec-вагонетку с заготов ками выдерживают в цехе при температуре 16—18° 12—16 час.
Чтобы ускорить процесс склеивания, пресс-вагонетку с заготов ками закатывают в камеру прогрева.
Рекомендуются камеры периодического действия, паровые, с принудительной циркуляцией воздуха. На схеме (рис. 14) видно, что камера имеет две секции, в каждую из которых загружается по одной пресС-вагонетке с запрессованными заготовками.
В верхней части камеры (надстройке) высотой 1,1 м разме щаются вентиляционное оборудование, система отопления и ув лажнительное устройство. Осевой вентилятор ЦАГИ серии В-16 № 8 установлен на одном валу с электродвигателем. Для обеспе чения взрывобезопасности с внутренней стороны обечайки закреп ляется прокладка из алюминия с соблюдением установленных зазоров между лопастями и обечайкой. Взрывобезопасный электро двигатель типа МА-142-1/4 (5,5 кет, 1445 об!мин) выносится за пределы камеры и устанавливается на кронштейнах.
Циркуляция воздуха в камере вертикальная вдоль прокладок. Воздух подается вентилятором через конфузор и пластинчатый ка лорифер в штабель первой секции сверху вниз. Затем через два перепускных окна (250X1170 мм), расположенных внизу перего родки, проходит во вторую секцию и снизу вверх идет через вто рой штабель. Возвращается циркулирующий воздух к всасыва ющему отверстию вентилятора через отверстие (2000X1000 мм) в плите междуэтажного перекрытия и снова засасывается вентиля тором.
Объем циркулирующего воздуха 18 тыс. м3/час. Скорость дви жения его через материал 2 м/сек. Воздухообмен в камере регули руется вытяжной трубой и двумя окнами для притока воздуха.
Так как в камере прогрева скопляются пары ацетона и кероси на, то непрерывный воздухообмен должен обеспечить взрывобезопасность с большим резервом (1/13 часть нижнего предела, ко торый равен 68 г/м3).
Система отопления камеры состоит из одного пластинчатого калорифера ПНМ-6 поверхностью нагрева 34,8 ж2, труб паровой и конденсационной магистралей, паровых вентилей и конденсацион-
24
|
Рис. 14. |
Схема |
камеры |
прогрева: |
электродвигатель 6 |
муфта, |
|
1 — секция прогрева; 2 — пресс-вагонетка; 3— верхняя |
часть |
камеры; |
4 — кронштейн; 5 |
||||
7 — шарикоподшипник; 8 — вал; |
9 — окно для свежего воздуха; |
10 — осевой вентилятор; 11 |
конфузор, |
вентиль |
|||
прямоугольный отвод; 13 — пластинчатый калорифер; |
14 — отверстие для воздуха^ 15 |
перепускное окно, / |
|||||
отопления; 17 — вентиль увлажнения; 18 — конденсационный |
горшок; |
19 — паровой вентиль; 20 |
вытяжной зонт, |
||||
отверстие для |
свежего воздуха; 22 — наслонная |
дверь; 23 — вытяжная труба |
|
|
него горшка № 1. Мощность калорифера рассчитана с резервом на 50%.
При увеличении объема выпуска клееных заготовок количе ство секций также следует увеличить (максимально до 8—10). При этом повышается концентрация паров ацетона и керосина, возра стает температурный перепад до 2° и сопротивление по 7 к&!м2 на каждую секцию.
В связи с этим нужно увеличить диаметр вытяжной трубы, размер окна для притока свежего воздуха, угол установки лопа стей вентилятора, заменить электродвигатель более мощным, а также установить дополнительное количество ребристых труб для промежуточного подогрева воздуха в камере.
Склеиваемые детали выдерживают в камере прогрева при тем
пературе 50—60° в течение 30 |
мин. при |
толщине материала до |
30 мм и 60 мин. при толщине |
материала |
31 —100 мм. Повышая |
температуру прогрева до 70—90°, сроки выдержки в камере со кращаются. Детали шириной до 180 мм выдерживают в течение 1—1,2 часа.
Годовая производительность камеры прогрева при двухсмен ной работе в среднем составляет 2 тыс. м3 склеиваемых заготовок. Максимальный расход пара 166 кг/час; удельный расход — 306 кг на 1 м3; расход электроэнергии — 7 квтч на 1 м3 заготовок.
Вагонетки со склеенными заготовками выкатывают из камеры и выдерживают в цехе, пока детали не остынут до 15—20°, при чем охлаждаются они под давлением.
Последующая обработка склеенных деталей производится пос ле полной полимеризации клея в швах в общем технологическом потоке.
СРАЩИВАНИЕ ДЕТАЛЕЙ СТАНДАРТНЫХ ДОМОВ И СТОЛЯРНЫХ ИЗДЕЛИЙ
Короткомерные отходы, получаемые при раскрое пиломатериа лов, целесообразно, сращивая по длине, использовать для изго товления деталей стандартных домов и столярных изделий. Сра щивание деталей менее трудоемко по сравнению со склеиванием заготовок. Поэтому деловые отходы длиной 400—500 мм рекомен дуется в первую очередь направлять на изготовление заготовок путем сращивания по длине.
Наиболее старым и распространенным способом сращивания заготовок по длине является' соединение их «на ус». В этом слу
чае длина уса должна быть не |
менее |
Юб, где б — толщина |
сое |
диняемой заготовки. |
на ус, |
'применяется способ |
сра |
Кроме соединения заготовок |
щивания их при помощи зубчатого шипа (рис. 15) с углом скоса шипей не более 4°. Соединение на зубчатый шип имеет значитель ные преимущества' по сравнению с соединением на ус, так как при этом значительно уменьшаются отходы древесины. Зубчатое соединение заготовок по длине обеспечивает их достаточную проч-
26

ность, так как величина склеиваемой площади при этом такая же, как и при соединении на ус.
Опыт Прилукского ДОКа по изготовлению столярных изделий путем сращивания из маломерных отходов позволяет рекомен довать этот способ для внедрения на всех деревообрабатывающих предприятиях.
а б
Рис. 15. Заготовки, полученные |
при |
сращивании на зубчатый тип. |
а — вид сбоку; |
б |
— вид спереди |
27
