
книги из ГПНТБ / Конкин, А. А. Углеродные и другие жаростойкие волокнистые материалы
.pdf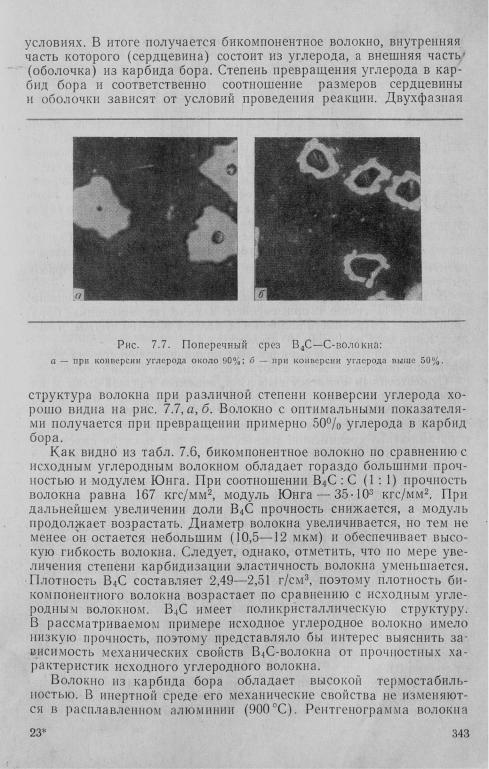
Т а б л и ц а 7.7. Условия синтеза SiC-волокна [62]
|
|
Мольное |
|
|
|
|
Исходное соединение |
соотноше |
Газ-носитель |
^Темпе |
Качественная характеристика |
||
ние Si и С |
ратура, |
отложения на подложке |
||||
|
|
в газовой |
|
°С |
|
|
|
|
фазе |
|
|
|
|
S iC l4 + |
С 7Н 8 |
2 :1 |
Н 2 |
1370 |
П ор ош к ообра зн ое, |
ры хл ое |
|
|
3 :1 |
Н 2 |
1430 |
У сы |
|
S iC l4 + |
СН С 13 |
1:1 |
Н 2 |
1480 |
Р ы х л о е |
|
|
|
2 ,5 :1 |
Н 2 |
1650 |
К р исталли ческое |
|
|
|
2 ,5 :1 |
н2 |
1370 |
» |
|
|
|
2 ,5 :1 |
Н 2 |
1510 |
» |
|
S iC l4 + |
(С Н 3) 2С О |
3 :1 |
Н 2 |
1430 |
О чен ь гладкое |
|
|
|
3 :1 |
н2 |
1540 |
» |
|
C H ?S iC !3 |
1:1 |
Н2“Ь^-г(4* 1) |
1100 |
Б у гр и стое |
|
|
|
|
1:1 |
Н 2 -f* А г ( 3 : 1) |
1150 |
Г л ад к ое |
|
|
|
1:1 |
н2+ А г ( 3 : 1) |
1230 |
М ел к об угр и стое |
|
не изменяется при нагревании до 2200 °С и, |
следовательно, |
фазо |
вые превращения в этих условиях не происходят.
Волокно из карбида бора на подложке из углеродного волокна получено [61] также с применением в качестве источника бора карборана-10. Прочность волокна составляла 80— 180 кгс/мм2 и мо дуль Юнга был равен 50 - 103 кгс/мм2.
Волокно из карбида кремния, как правило, получается на воль фрамовой подложке. Хоух с сотр. [62] описали такой способ.
Существенным является выбор компонентов газовой фазы и их термическая стабильность, определяющая однородность и свойства волокна. Изучено большое число карбидообразующих соединений. Чаще всего применяются смеси, состоящие из соединений кремния и органических соединений. Важно, чтобы при распаде смеси не получался углерод, который, осаждаясь на волокне, снижает его качество.
В табл. 7.7 приведены соединения и смеси, использованные при получении SiC-волокна. Из исследованных композиций наиболее удачной оказалась смесь SiCl4+ (СН3) 2СО при мольном соотноше нии кремния и углерода (без учета атомов углерода, соединенных с кислородом) от 2,5 : 1 до 3 : 1. Оптимальная температура процесса находится в пределах 1400— 1550 °С. Удовлетворительные резуль таты получены также при использовании метилтрихлорсилана. Тер модинамический анализ указывает на важную роль водорода, при меняемого в качестве газа-носителя; в его отсутствии образование SiC невозможно [63].
Важнейшим параметром процесса является скорость движения нити-подложки, определяющая производительность аппарата. По литературным данным [60, 64], скорость движения нити составля ет только 0,6 м/мин.
SiC-Волокно, полученное в оптимальных условиях, имеет кри сталлическую p-форму, аналогичную алмазу. Кристаллическая ре шетка построена из чередующихся атомов Si и С, каждый из кото-
344
рых входит в состав тетраэдра. Плотность волокна 3,21 г/см3. SiC-Волокна являются бикомпонентными (двухфазными) волокна ми; содержание SiC в волокне составляет 90—97 объемн. %. В сердцевине волокна сохраняется вольфрамовая нить, масса ко торой невелика по сравнению с общей массой материала.
Волокна, полученные описанным способом, имеют небольшую
прочность (95— 126 кге/мм2), но довольно высокий модуль |
Юнга |
|
(42 •103 кгс/мм2). Низкая прочность объясняется, |
видимо, |
несо |
вершенством процесса и большой дефектностью волокна. |
|
|
В патенте [65] описаны усовершенствованный |
способ и аппа |
ратура для получения SiC-волокна. Волокно получалось осажде нием из газовой фазы карбида кремния на вольфрамовую подлож ку. Источником кремния служил CH3SiCl3, газом-носителем — водород. Движение смеси газов было параллельным перемещению нити. Температура процесса составляла 1200— 1300°С; колебание температуры по длине нити не превышало 30 °С. Для получения волокна использовался двухкамерный аппарат горизонтального ти па. В первой камере в среде водорода нить очищалась от жиров и при 800— 1200 °С удалялся адсорбированный кислород. Во второй камере SiC осаждался на подложке. Камера была снабжена теп ловым экраном. Может быть несколько реакционных камер, при чем длина каждой из них зависит от их общего числа. Скорость движения волокна изменялась от нескольких сантиметров до де сятка метров в минуту. Диаметр SiC-волокна составлял 100—• 200 мкм, оно имело очень хорошую поверхность и высокие меха нические показатели (прочность 250—350 кгс/мм2, модуль Юнга 45-103 кгс/мм2). В патенте приводится схема аппарата.
Согласно патенту [66] прочность SiC-волокна повышается на 20—30% при обработке его после выхода из реакционной камеры 5%-ным раствором КОН при 20—25 °С в течение 2 мин. Прочность волокна, составлявшая до обработки 220—240 кгс/мм2, после об работки повысилась до 260—320 кгс/мм2. Модуль Юнга остался без изменения и был равен 45 •103 кгс/мм2. Для уменьшения колебаний температуры нити реакционную камеру снабжают тепловым экра ном и печью с тепловым градиентом, расположенными вокруг аппа рата со стороны выхода из него волокна. При наличии такого устрой ства колебания температуры по длине нити снижаются до ±15°С .
Заметное улучшение качества осадка SiC и прочности SiC-во- локна достигается введением в газовую смесь галоидных соедине ний бора в соотношении Si: В (6: 1). При этом получается волок но, состоящее из смеси карбида кремния и бора; оно представля ет собой модифицированное SiC-волокно.
Достигнутые механические показатели SiC-волокон, надо пола гать, не являются пределом, и в будущем могут быть найдены условия, позволяющие улучшить свойства этих волокон.
К положительным свойствам SiC-волокон относятся: высокие термостойкость, химическая стойкость, в том числе к окислителям, хорошая адгезия к связующим, относительно невысокая плотность.
345
7.5.2. Получение карбидных волокон методом пропитки химических волокон и последующей карбидизацией
Этот метод, как указывалось ранее, основан на наполнении хи мических волокон карбидообразующими элементами и последую щей термической обработке. Карбидообразующий элемент должен находиться в волокнистом материале либо в виде окисла, либо в виде соединения, способного превращаться в окисел при низко температурной обработке. При последующей высокотемпературной обработке происходит науглероживание окисла за счет углерода волокна до образования карбида. Возможны два способа введе ния карбидообразующих элементов в волокно. По одному из них карбидообразующие соединения вводятся в прядильный раствор; при формовании получают волокно с равномерно распределенны ми в нем добавками. Применение этого метода рассмотрено выше на примере получения SiC-волокна и смешанного углерод-кремне- земного волокна. По второму варианту готовое химическое волок но пропитывается растворами карбидообразующих элементов, обычно водными растворами солей, хотя, конечно, не исключено использование органических растворителей. Волокно должно об ладать сродством к растворителю с тем, чтобы было достаточно сорбированной соли для последующего получения карбида. В слу чае применения водных растворов солей с pH не менее 7 наиболее приемлемым является вискозное волокно. При использовании в ка честве исходного материала полиакрилонитрильного или углерод ного волокон можно для пропитки применять растворы солей или расплавы солей с кислой реакцией.
Метод получения карбидных волокон термообработкой хими ческих волокон, наполненных карбидообразующими элементами, находится в стадии разработки и пока еще, видимо, не получил практического применения, хотя подобные процессы запатентованы в ряде стран [67—72]. Преимуществом метода является простота введения карбидообразующих элементов в волокно. Концентрация пропиточного раствора должна быть не менее 2,5—3 моль/л; при меньших концентрациях растворов не достигается соотношение С : Me (углерод : металл), необходимое для образования карбида. Для повышения эффективности пропитки волокно подвергают пред варительному набуханию.
Например, вискозное волокно вначале обрабатывают водой, а затем водным раствором соли. Для синтетических волокон при меняют органические растворители.
Температурно-временные режимы в зависимости от состава и структуры волокна, а также природы соли, могут изменяться в широких пределах. Соли тугоплавких металлов, жидкие в обычных условиях, можно применять вместе с разбавителями (бензол, то луол, гексан и др.), замедляющими гидролиз солей и способствую щими рассеиванию тепла, предотвращая тем самым деструкцию целлюлозы. Твердые соли тугоплавких металлов применяются как
34 6
в виде водных растворов, так и растворов в органических раствори телях (четыреххлористый углерод, нитробензол и др.).
Для предотвращения слипания элементарных волокон при по следующей термообработке избыток раствора удаляется и волокно сушится при 70 °С.
Термическая обработка волокна проводится в две стадии. Пер вая стадия — карбонизация — при применении вискозного волокна осуществляется при температуре выше 250°С в инертной среде. Для сохранения скелета углеродного волокна и предотвращения кристаллизации карбидообразующих соединений карбонизация проводится длительное время. На второй стадии термообработки протекает реакция взаимодействия углерода с окислом металла с образованием карбида. Науглероживание металла в зависимости от его природы происходит в интервале 1000— 2000 °С. Скорость нагрева достаточно большая и составляет примерно 1000°С/ч. Свойства карбидного волокна зависят от зернистой структуры кар бида, которая в свою очередь определяется конечной температурой и продолжительностью термообработки. Чем тоньше зернистая структура, тем выше качество волокна.
Состав готового волокна определяется условиями карбонизации (содержанием углерода) и содержанием металла, введенного в во локно. Регулировать содержание углерода в волокне, а следова тельно, соотношение С : Me, можно изменением условий карбони зации. Если необходимо уменьшить выход углерода, то карбони зацию следует проводить в среде инертного газа, содержащего кислород воздуха. Чем меньше в волокне карбидообразующего металла, тем жестче должны быть условия карбонизации для по лучения стехиометрического соотношения С : Me, соответствующего составу карбида.
По этому способу можно получать чисто карбидные и смешан ные углерод-карбидные волокна [73].
Следует отметить, что при получении карбидных волокон этим способом образование карбидов происходит при более низких тем пературах по сравнению с другими известными методами их полу чения, что объясняется повышенной реакционной способностью окислов металлов, обусловленной в свою очередь исключительно высокой степенью дисперсности окислов.
7.6. БОРНИТРИДНОЕ ВОЛОКНО
Нитрид бора, полученный в' середине XIX века, не находил ши рокого практического применения, несмотря на такие цепные свой
ства, как |
высокая прочность, хемостойкость |
и термостойкость, |
а также |
прекрасные электроизоляционные |
свойства. Примерно |
10 лет назад были предприняты попытки получения борнитридного волокна (один из путей практического применения нитрида бора). В 1965 г. фирма «Carborundum» (США) сообщила о выпуске жа
347
ростойкого борнитридного |
волокна диаметром 5—7 мкм [2; 74]. |
По прочности (190 кгс/мм2) |
это волокно не уступает другим жаро |
стойким волокнам. Несколько необычным для этого волокна ока залось сочетание высокой прочности с низким модулем упругости
(2800— 8437 кгс/мм2) ; разрывное |
удлинение волокна |
составляет |
||
1- 2% . |
|
метода |
получения |
борнитрид |
В литературе описаны два |
||||
ного волокна. Один из методов |
[75] основан на пропитке вискозно |
|||
го волокна раствором бората |
алюминия, |
карбонизации его при |
||
350 °С и последующей термической обработке сначала в токе NH3 |
||||
при 1000°С, а затем в вакууме при 1300 °С. |
|
|
Другой способ получения борнитридного волокна предусмат ривает использование в качестве предматериала волокна из окиси бора [76]. Сущность способа заключается в многостадийной обра ботке аммиаком волокна из окиси бора. В процессе обработки про исходит постепенное азотирование окиси бора с образованием ни трида бора. К основным параметрам, определяющим условия по лучения и свойства борнитридного волокна, относятся диаметр ис ходного волокна, концентрация аммиака, продолжительность и температура реакции.
Суммарная реакция превращения В20 3 в BN выражается урав нением
В20 3 + 2NH3 ------>- 2BN + ЗН20
В действительности реакция протекает значительно сложнее и со провождается образованием различных промежуточных продуктов, точный стехиометрический состав которых установить не удалось. По данным авторов работы [76], изменение массы, а также анализ твердого остатка и газообразных продуктов реакции свидетельст вуют о протекании реакции по меньшей мере в три стадии. На пер вой стадии при температуре выше 200°С образуется комплексное соединение:
/ > 200°с
иВ20 3 + NH3 |
>• (B20 3)rtNH3 |
Значение п зависит от условий проведения реакции, но, как пра вило, оно больше трех. Это комплексное соединение имеет более высокую температуру плавления по сравнению с В20 3, благодаря чему при последующей, более высокой температуре обработки со храняется форма волокна. Вторая стадия обработки проводится при 350 °С; на этой стадии происходит дальнейшее обогащение ма териала азотом и образование циклического соединения с включе нием в цикл бора и азота
n h 3
(B20 3)„NH3 ^ > 35Qoq (BN)*- (В20 3)^•(NH3)2 + «Н20
В зависимости от продолжительности реакции, концентрации ам миака и скорости подъема температуры значения х, у, z меняются.
348
Течение реакции определяется скоростью диффузии аммиака внутрь волокна и диаметром волокна, поэтому подъем температуры во времени строго регулируется.
При температуре выше 600 °С возникают трехмерные структу ры, фиксируемые рентгеновским методом, а при температуре выше
1800 °С происходит превращение промежуточного соединения в ни трид бора по реакции
t > 1800°с
(BN )*•(ВгОз)^•(ЫН3)г ----------- > nBN + m(B20 3)-H 20 + Ш Н3
Диффузия аммиака внутрь волокна и степень превращения В20з в BN зависят от диаметра исходного В2Оз-волокна. Из данных табл. 7.8 видно, что содержание азота в волокне уменьшается с увеличением диаметра В20 3-волокна; снижение особенно заметно при диаметре волокна более 20 мкм. При диаметре 34 мкм даже при большой продолжительности процесса степень азотирования остается низкой. Для получения борнитридного волокна целесооб
разно применять |
исходное В20 3-волокно малого диаметра. |
|
||||||
Кристаллическая структура нитрида бора аналогична графиту, |
||||||||
но имеются и существенные различия. |
Так же как у графита, |
кри- |
||||||
Т а б л и ц а 7.8. |
Влияние диаметра В20 3-волокна |
и продолжительности |
||||||
|
|
реакции на степень азотирования |
|
|
||||
|
|
|
(температура 700°С) |
|
|
|
||
Продолжи |
Диаметр |
Содер- |
Продолжи |
Диаметр |
Содер- |
Продолжи |
Диаметр |
Содер- |
тельность, |
жание |
тельность |
жание |
тельность |
жание |
|||
реакции, |
волокна, |
азота, |
реакции, |
волокна, |
азота, |
реакции, |
волокна, |
азота, |
ч |
мкм |
% |
ч |
мкм |
% |
ч |
мкм |
% |
|
6,3 |
44 |
|
6,3 |
49 |
|
6,3 |
51 |
0,5 |
10,8 |
42 |
2,0 |
10,8 |
47 |
14,0 |
10,8 |
50 |
17,5 |
34 |
17,5 |
41 |
17,5 |
45 |
|||
|
34,0 |
22 |
|
34,0 |
30 |
|
34,0 |
32 |
349
Т а б л и ц а 7.9. Свойства некоторых нитридов
|
Температура |
Плотность, |
Коэффициент |
Коэффициент |
Удельное объем |
Нитрид |
линейного |
теплопровод |
ное электрическое |
||
плавления, |
г/см3 |
расширения |
ности, |
сопротивление, |
|
|
°C |
|
а-106, 1/сС |
ккал/(см-с-°С) |
мкОм-см |
HfN |
3298 |
14,0 |
___ |
— |
Проводник |
|
|
|
|
||
ZrN |
2968 |
7,32 |
6—7 |
0,040 |
13,6 |
TiN |
2918 |
5,43 |
— |
0,070 |
21,7 |
BN |
2983 |
2,27 |
0,05— 10 |
0,04— 0,12 |
10е |
Si3N4 |
1899* |
3,44 |
2,47 |
0,045 |
143-10э |
* Температура сублимации.
сталлическая ячейка нитрида бора состоит из гексагональных (ше стизвенных) циклов, в углах которых поочередно расположены ато мы бора и азота, образуя паркетоподобные плоскости (рис. 7.8). В нитриде бора каждый цикл одной плоскости лежит строго под таким же циклом другой плоскости, в то время как в графите по ловина атомов каждого слоя расположена между центрами шести гранников двух соседних слоев (см. гл. 1); полное соответствие в расположении атомов углерода в графите наблюдается через од ну плоскость. Расстояние между соседними плоскостями у обеих структур одинаково и равно 3,34 А; расстояние между атомами уг лерода в шестиграннике графита равно 1,41 А, а между атомами В и N в нитриде бора — 1,45 А.
Волокно из нитрида бора обладает своеобразной физической структурой. Для него, так же как для волокнистой формы углеро да, характерна турбостратная структура. Особенность этой струк туры в отличие от трехмерной гексагональной ячейки (см. рис. 7.8) состоит в отсутствии какой-либо взаимной ориентации плоскостей друг относительно друга в направлении, перпендикулярном оси с. Таким образом, с точки зрения кристаллографии турбостратную структуру нитрида бора можно рассматривать как двухмерные кристаллиты, поскольку отсутствует ближний порядок в трех из мерениях. Нитрид бора в виде массивных образцов, так же как во локно, может иметь турбостратную структуру, но свойства нитрида бора в виде массивных образцов и волокна различные. Нитрид бо ра при температуре выше 2000 °С под действием воды распадается на элементы. Волокно из нитрида бора устойчиво к кипящей воде и в инертной атмосфере не разрушается при температуре до 2500 °С. Эти различия в свойствах, а также данные рентгенострук турного анализа и дифракции электронов привели авторов рабо ты [77] к выводу, что в борнитридном волокне наряду с турбостратной структурой содержатся трехмерные кристаллические образования с параметрами решетки: а — 1,455 А, с = 3,34 А. Следовательно, борнитридное волокно состоит из набора турбостратных и кристаллических форм BN.
35 0
Турбостратную структуру можно рассматривать как промежу точное состояние между кристаллическим и аморфным фазовым со стоянием вещества. Размеры организованных в турбостратной фор ме структурных единиц оказывают существенное влияние на физи ко-механические свойства волокна.
В борнитридном волокне существует большой набор надмолеку лярных структур, размеры которых колеблются от 20—30 А до не скольких тысяч А [78], но преимущественные размеры кристалли тов: Lc= 84 A, La = 148 А, межплоскостное расстояние равно 3,40 А.
Кроме нитридов бора известны другие нитриды, обладающие высокими термическими характеристиками. В табл. 7.9 приведены физические константы некоторых нитридов. Не исключено, что в будущем эти нитриды будут использованы для получения жаро стойких волокон. Примером может служить Si3N4 из которого уже получено волокно хорошего качества.
7.7. БОРНОЕ ВОЛОКНО
Бор представляет собой твердое жесткое хрупкое вещество, трудно поддающееся обработке обычными методами, такими, как штамповка, прокатка, горячее прессование, спекание и др. Каза лось бы, материал с такими свойствами непригоден для получения волокна. Тем не менее на основе бора получено высококачествен ное жаростойкое волокно; это волокно относится к перспективным материалам, предназначенным для создания конструктивных пла стиков с высокими механическими показателями [79].
Непрерывное борное волокно получают методом осаждения бо ра из газовой фазы на вольфрамовую нить-подложку. В качестве исходных компонентов применяются галогениды бора, преимущест венно ВС1з, и водород. При высокой температуре происходит вос становление бора по реакции
2ВС13 + ЗН2 ------ |
v 2В + 6НС1 |
Образующийся элементарный бор осаждается на подложку. Аппа ратурное оформление процесса получения борного волокна анало гично описанному для SiC-волокна (см. рис. 7.6).
Основными параметрами процесса являются состав смеси ис ходных компонентов, температура и продолжительность. По дан ным Талли и др. [2], соотношение ВС13 и Н2 существенно не ска зывается на качестве волокна. Наиболееважным параметром яв ляется температура. При низких температурах (980°С) реакция протекает медленно, при высоких температурах (1260— 1315°С) осаждается крупнозернистый бор; это отрицательно сказывается на свойствах волокна. Видимо, процесс проводится при температурах 980— 1260°С, но истинные значения температур не приводятся. Химические процессы и осаждение бора протекают с большой ско ростью, поэтому продолжительность пребывания волокна в камере
351
составляет 1—2 мин. При заданной продолжительности процесса производительность аппарата определяется длиной его реакцион ного пространства.
В патенте [80] предлагается использовать двухкамерный верти кальный аппарат. Способ и аппаратура обеспечивают значительное увеличение скорости процесса и соответственно снижение стоимо сти волокна без ухудшения его свойств.
Установлено, что температура подложки по длине неравномерна и проходит через максимум, положение которого зависит от соста ва реакционной смеси, скорости движения подложки, разности по тенциалов (приложенного к ней напряжения)' и направления дви жения газовой смеси. Наличие температурного градиента связано также с изменением сопротивления в результате осаждения бора па подложку и изменения скорости реакции. Кроме того, увеличе ние диаметра нити влияет на теплопотери за счет радиации, кон векции и других факторов. Наибольшая скорость реакции наблю дается на участках с наиболее высокой температурой проволоки, хотя температура не является единственным фактором, определяю щим скорость реакции. Противоточное направление газового пото ка (по отношению к движению проволоки) приводит к локализации максимальной температуры проволоки.
Введение газовой смеси с обоих концов нижней части реактора, обеспечивающее более равномерное распределение температуры вдоль подложки, привело к трехкратному увеличению скорости
процесса и получению волокна, |
однородного |
по |
свойствам. |
При |
|||||||
длине нижней части |
аппарата |
66 |
см |
и |
верхней |
части |
аппарата |
||||
122 см волокно диаметром |
100 |
мкм |
|
получается со |
скоростью |
||||||
210 м/ч. Температура процесса 1300°С. Состав газовой |
смеси (по |
||||||||||
объему), |
подаваемой в |
верхнюю |
часть |
нижней |
камеры,— |
||||||
ВС13:Н 2 = |
0,25—0,5, |
а в нижнюю |
часть той же |
камеры — 0,5—3. |
|||||||
Полученное таким |
способом |
волокно |
имело |
прочность |
около |
||||||
320 кгс/мм2. |
|
|
|
|
|
|
|
|
|
|
Помимо вольфрамовой нити-подложки исследовались другие подложки: молибденовая, алюминиевая, танталовая; алюминиевая, покрытая вольфрамом; вольфрамовая, покрытая кремнием, а так же стеклянное волокно, покрытое медью. Осаждение бора на танталовую и молибденовую подложку протекало нормально. Ско рость осаждения бора на танталовую подложку примерно такая же, как для вольфрамовой, а для молибденовой несколько мень шая.
Из-за высокой стоимости вольфрамовой нити пытаются заме нить ее углеродной нитью. По данным патента [81] при нанесении бора из газовой фазы на углеродную подложку в начале процесса наблюдалось равномерное покрытие нити; затем покрытие приоб ретало бамбукоподобный вид с периодически повторяющимися утолщениями по окружности; это были участки с более плотным слоем бора. Утолщения возникают вследствие наличия на нити участков с более высокой температурой, обусловленных неоднород-
352