
3549
.pdfуглами и .
Например, фирма «Сандвик Коромант» изготавливает резцы с положением СМП, у которых фактические задние
углы 80 и 1 60 . При выборе рекомендуемых других углов и 1 положение пластины и углов установки и необходимо рассчитать по формулам, приведенным в [2, 5 и 6]. Рассчитанные значения углов и необходимы для фрезерования (шлифования) паза под пластины в корпусах резцов при их изготовлении.
150
Контрольные вопросы к разделу 3
1.Укажите, по каким признакам классифицируются резцы?
2.Назовите основные части резцов.
3.Перечислите важнейшие углы и их обозначения у резцов. 4.Какие типы резцов, предназначенных для металлообработки, кроме проходных, вы знаете?
5.Назовите основные преимущества резцов с СМП по сравнению с напайными резцами.
6.Укажите недостатки РИ с СМП по сравнению с обычными. 7.Назовите схемы крепления СМП в инструментах по ИСО. 8.Назовите основные виды износа СМП при резании.
9.Какие основные инструментальные материалы применяются в СМП?
10.Какие основные виды изнашивания Вы знаете?
11.Какой вид износа у твердосплавных СМП получили наибольшее распространение?
12.Назовите основные ведущие фирмы, поставляющие инструмент в нашу страну.
13.Назовите обозначение основных групп обрабатываемых материалов по ИСО.
14.Какие основные преимущества резцов с СМП из керамики и СТМ?
15.Перечистите, какими единичными показателями оцениваются системы крепления?
16.Перечислите основные формы СМП и их обозначение по ИСО.
17.Сколько цифр кода применяется в системе кодирования пластин?
18.Какую величину периода стойкости у СМП из твердого сплава рекомендует иметь фирма «Коромант»?
19.Укажите, сколько цифр в коде применяется при кодировании резцов в системе ИСО.
20.Какие величины необходимы для расчета оптимальной величины подачи S?
151
Раздел 4. ФАСОННЫЕ РЕЗЦЫ
4.1. Типы фасонных резцов
Фасонные резцы (ФР) широко применяют в серийном, крупносерийном и массовом производствах при обработке фасонных деталей на автоматах, полуавтоматах и других станках. Различают призматические, круглые и тангенциальные резцы; из быстрорежущей стали или оснащенные твердосплавными пластинами. Точно изготовленные фасонные резцы при правильной установке их на станках обеспечивают высокую производительность, точность формы и размеров обрабатываемых деталей по IТ8 - IТ12 и поверхность с Rа = 63 ... 2,5 мкм.
Фасонные резцы можно классифицировать по следующим признакам (рис. 27):
форма: круглые (а, г, е, ж, и) и призматические
(б, в, д, з)
вид обрабатываемой поверхности: наружные (а- в, д-и) и внутренние (г);
направление подачи относительно заготовки: радиальные (а, б) и тангенциальные (в),
расположение резца относительно детали: с параллельным расположением осей или базы крепления (а-г)
ис повернутым расположением осей или базы крепления под углом μ (д, е);
расположение передней поверхности: без наклона (а- е, и) и с наклоном под углом λ.(ж, з);
форма образующих фасонных поверхностей: кольцевые (а, г, е, ж) и винтовые (и).
По сравнению со стержневыми токарными резцами фасонные резцы обладают следующими достоинствами: большая производительность, высокая точность профиля и размеров детали, длительный срок службы, простота заточки и
152

переточки, не требуют высококвалифицированных рабочих. Недостатками фасонных резцов являются: сложность изготовления, необходимость точной установки, высокая стоимость, разные условия резания и износа по длине режущих кромок.
Призматические резцы применяют для обработки наружных поверхностей. По сравнению с круглыми резцами они обладают повышенной жесткостью и надежностью крепления, высокой точностью обработки, лучшим теплоотводом, простотой установки на станках.
Круглые (дисковые) резцы применяют для обработки наружных и внутренних поверхностей, так как они более технологичны по сравнению с призматическими резцами, но сложнее в установке, обеспечивают большее количество переточек и имеют повышенный срок службы.
Рис. 27. Типы фасонных резцов: Д - деталь; К - круглые резцы; П - призматические резцы; 1-2 - режущие кромки; Dг -
главное движение; Ds - движение подачи
153
Радиальные фасонные резцы имеют подачу, направленную по радиусу, а тангенциальные - подачу, направленную по касательной к поверхности детали. В производстве наибольшее распространение получили фасонные резцы с радиальной подачей, так как они проще в эксплуатации и настройке. Многообразие типов фасонных резцов обусловлено особенностями профилей обрабатываемых деталей и условиями их работы. При обработке простых и сложных профилей широко применяются круглые и призматические резцы с осью или базой крепления, параллельной оси детали (см. рис. 27, а, 6, г). При обработке деталей, имеющих участки с углом профиля 900 (см. рис. 27, д, е), на участке a' - b' рекомендуется применять резцы с осью или базой крепления, наклоненной под углом μ = 10 ... 20° к оси детали. В этом случае на участке a' - b' образуются передние и задний углы, а резцы имеют значительно меньший износ по сравнению с обычными резцами.
Для получения на профиле детали точного конического участка рекомендуется применять фасонные резцы с наклоном передней поверхности под углом λ (рис. 27, ж, з). Это приводит к тому, что режущая кромка резца (1-2) будет расположена на оси детали и погрешность детали на этом участке будет минимальной.
Круглые фасонные резцы с винтовой задней поверхностью (см. рис. 27, и), хотя и улучшают условия работы на участке по сравнению с обычными круглыми резцами, но не нашли широкого распространения из-за сложности изготовления.
Перед проектированием фасонных резцов изучают чертеж детали и определяют возможность ее обработки по всему профилю фасонным резцом выбранной конструкции на применяемом оборудовании.
154
4.2.Методы проектирования резцов
Вработах [2,3 и 5] приведена подробная методика проектирования фасонных резцов. Приведём укрупнено следующие этапы и последовательности расчёта ФР:
1.Выбор типа фасонного резца (круглый или призматический);
2.Выбор углов γ и α в зависимости от выбранного материала резца и
обрабатываемого материала [2,5] в расчётной точке детали с минимальным диаметром (см рис. 28);
Обозначение характерных точек профиля детали (1-6) и резца (1р - 6р), а при необходимости выбор дополнительных режущих кромок резца (при подрезке, обработка фаски и др.); Выбор рекомендуемых режимов резания (скорость V (м/мин) и поперечной подачи s (мм/об) [1,5]). Число оборотов
на шпинделе станка рассчитывается по формуле
п = 1000· V /πdo (об/мин), do - диаметр заготовки;
5.Разработка расчётной схемы и расчёт размеров резца по профилю производится в зависимости от заданных размеров детали по формулам, приведённым в [2,3];
6.Определение передних и задних нормальных углов в любой характерной точке резца «х» про изводится по формулам:
tgγNX ≈ tgγх· sinφ и tgαNX ≈ tgαх· sinφ,
где: γх и αх - соответственно передний и задний углы в продольной плоскости в любой выбранной точке x, рассчитываются по формулам;
φ - угол в плане в точке детали х.
Знание этих углов необходимо при анализе условия работы режущих кромок и расчёта периода стойкости;
7.Расчёт исполнительных размеров и допусков на размеры резцов и калибров.
155
Исполнительные размеры и допуски на размеры ФР во многом определяют размерную стойкость и срок службы резцов. При этом надо обязательно учитывать охватывающие или входящие размеры, условия работы и износ при эксплуатации. Высотные и линейные размеры калибров для контроля профиля резца при изготовлении рассчитываются из размеров резца и принятых допусков. Величины допусков выбираются по рекомендациям [2,3]. Размеры, полученные при расчёте, проставляются на рабочих чертежах резца и калибра;
8.Расчёт количества переточек и срока службы ФР в производстве по формам в [2];
9.Расчёт суммарной силы резания и требуемой мощности при резании;
10.Определение необходимого количества ФР для изготовления заданных программой деталей;
11.Расчёт экономической эффективности (А) от применения ФР по сравнению с обработкой обычными резцами с учётом технологической себестоимости затрат на инструмент. После расчёта величины А решается вопрос какой инструмент рекомендуется применять для изготовления фасонной детали в производстве.
4.3.Расчет погрешности обработки деталей фасонными
резцами
Расчёт погрешности обработки является одним из важных вопросов технологической операции. Это особенно важно в автоматизированном производстве, где широко применяется многоинструментальная и многошпиндельния обработка. В этом случае погрешность на про филе фасонных резцов передаётся на профиль изготовленной детали.
В производстве наибольшее распространение получили фасонные резцы, у которых базовая (одна или несколько) точка режущей кромки расположена на линии центров детали.
156
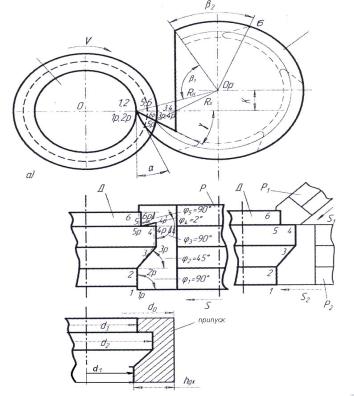
При обработке такими резцами деталей, имеющих конические (1 – 2) и торцовые (1 – 2 – 3) участки - (рис. 29), возникают погрешности. Это связано с тем, что из-за наличия угла режущие кромки резцов, обрабатывающие эти участки, не лежат на линии центров детали.
Рис. 28. Расчетная схема параметров круглого фасонного резца для наружной обработки
Теоретически для исключения погрешности на коническом и торцовом участках необходимо профиль резца в сечении А – А изготавливать по сложным кривым 2 – го порядка. Например, участок профиля фасонных резцов lр – 2р должен быть изготовлен по гиперболе, а участок профиля 1р –
157
2р – 5р должен быть частью эллипса.
По приведенным выше формулам можно рассчитать высоту профиля характерных точек резца, а затем по их координатам определить уравнения этих кривых. Однако изготовление резцов с таким сложным профилем связано с большими трудностями. Поэтому на практике для облегчения изготовления резцов на участке lр – 2р профиль изготавливают по прямой с углом σр, а на участке 1р – 2р – Зр по дуге окружности радиусом rp с координатами х0 и у0. Это приводит к образованию на профиле резца в точке хр погрешности хр, которая при обработке переносится на деталь с образованием на профиле в точке х погрешности х.
– А – сечение, перпендикулярное задней поверхности фасонного резца
При этом если профиль резца имеет погрешность в выпуклую сторону, то на детали погрешность будет в вогнутую сторону, и наоборот.
Теоретические исследования, выполненные на кафедре ИСАП СамГТУ, позволили получить формулы для расчёта погрешности в любой точке детали х после обработки фасонными призматическими и круглыми резцами [1,5].
4.4. Износ поверхности фасонных резцов
При работе фасонные резцы изнашиваются по задним и передним поверхностям с образованием площадок износа. Превалирующим является износ по задним поверхностям, от которого зависят размер припуска при переточках, общее количество переточек и срок службы инструмента. Кроме того, износ влияет также на точность обработки и период размерной стойкости резцов. Износ по задним поверхностям имеет немонотонный характер (рис. 30), что объясняется разными путями и скоростями резания участков лезвия, а также разными задними углами и силами резания.
158
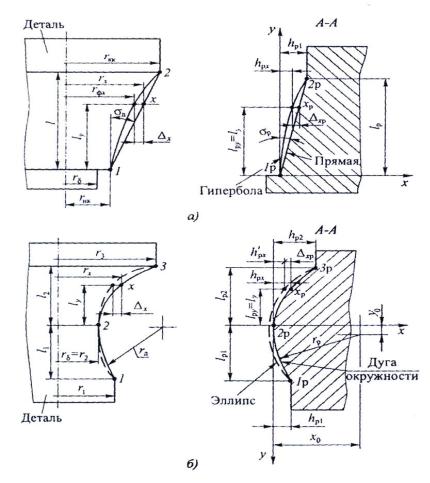
Рис. 29. Схема для расчета погрешностей обработки: а
– на коничеком участке детали; б – на торцовом участке детали; А
Опыт показывает, что наибольший износ имеют обычно участки, имеющие минимальные углы αNX и φх = О(участок 4- 5) и максимальные пути резания (участок 3-4), а наименьший износ - участки сφх = 90° минимальными путями (участок 1- 2 и 5-6). Большое влияние на износ оказывает также
159