
3436
.pdf
ны по отдельным частям, а затем склеены. Недостатком технологии является довольно высокая стоимость расходных материалов. Тем не менее, такая технология имеет и преимущества - быстрота получения модели и высокое качество модельного материала с точки зрения собственно технологии литья по выплавляемым моделям: формовки, вытапливания модели и др.
Рис. 7.7. Оболочковая форма и отливка корпуса турбины, полученные по восковой синтез-модели
Особенностью данной технологии является также наличие поддерживающих структур. Поддержки строятся для удержания вытупающих элементов в процессе построения модели. В качестве материала для поддержек используется восковой полимер с низкой температурой плавления, который после построения модели удаляется горячей водой. Современные машины имеют возможность работы на двух модельных материалах – литейном воске и акриловом фотополимере.
При селективном лазерном спекании модели создаются из порошковых материалов за счет эффекта спекания при помощи энергии лазерного луча. В данном случае, в отличие от SLA-процесса, лазерный луч является не источником светового, а – теплового излучения. Воздействуя на тонкий слой порошка, лазерный луч спекает его частицы и формирует твер-
120

дую массу, в соответствии с заданной геометрией детали. В качестве материалов используются: полиамид, полистирол, песок и порошки различных металлов и сплавов. Существенным преимуществом SLS-процесса является отсутствие технологических поддержек при построении модели.
В процессах SLA и MJM при построении нависающих элементов детали используются специальные поддержки, предохраняющие только что построенные тонкие слои модели от разрушения. В SLS-процессе в таких поддержках нет необходимости, поскольку построение ведется в однородной массе порошка. После построения модель извлекается из массива порошка и очищается от его сотатков (рис. 7.8).
PSL (Plastic Sheet Lamination) – построение модели пу-
тем послойного склеивания ПВХ-пленки на 3D-принтерах,
работающих по технологии PSL - Plastic Sheet Lamination. Та-
кие устройства иногда называются LOM-машинами, от
Laminated Object Manufacturing – послойное склеивание пле-
ночных материалов (полимерной пленки или ламинированной бумаги) с последующим формированием (вырезанием) модели с помощью лазерного луча или режущего инструмента. В частности, 3D-принтеры Solido SD 300 относятся к категории самых дешевых RP-машин для быстрого прототипирования.
Рис. 7.8. Модели, полученные SLS
121
Модельным материалом служит полихлорвиниловая пленка толщиной 0,15 мм пяти цветов: полупрозрачная янтарная, красная, синяя, кремовая, черная. Формирование модели производится путем последовательного склеивания слоев пленки и вырезания контура модели с помощью специального лезвия, закрепленного на подвижной головке.
Модель строится на специальной магнитной подложке, устанавливаемой на подвижной вверх-вниз платформе. Клеевой состав наносится на всю поверхность слоя пленки, а в те места, где после построения необходимо обеспечить легкое удаление пленки, наносится защита от клея. То есть тело модели формируется за счет последовательного склеивания пленки, а пустоты остаются не склеенными, чтобы обеспечить легкое удаление излишков из этих пустот в процессе последующей обработки. Защита от клея наносится с помощью специальных карандашей типа фломастеров с различным диаметром стержня (1, 3 и 6 мм). В зависимости от размеров полости модели, которую необходимо сформировать, используется соответствующего размера фломастер.
Модели из ПВХ-пленки могут использоваться в качестве мастер-моделей при литье в силиконовые формы полиуретановых смол, а также восковых моделей для последующего литья металлов по выплавляемым моделям. Точность построения на 3D-принтере в пределах 0,1-0,12 мм на длине 150
ммпо всем координатам.
7.4.Аддитивные технологии при синтезе литейных форм
Литейные формы - это отдельный раздел аддитивных технологий. Особенно широкое развитие получило направление непосредственного выращивания песчаных форм для литья металлов, а также выращивание металлических изделий, в частности, пресс-форм для литья пластмасс. В этих случаях в полной мере происходит практическое воплощение концепции «безбумажных технологий», так как производство изде-
122
лия вообще не нуждается в сопровождении посредством традиционной бумажной документации в виде конструкторскотехнологической документации [8].
Это позволяет изменить традиционный подход обеспечению работ исполнителями. Конструктор и технолог работают не последовательно, а параллельно и поочередно. В ряде случаев конструктор-разработчик выполняет функцию технолога, создавая параллельно с CAD-моделью детали CADмодели технологической оснастки для литья детали.
Для производства песчаных литейных форм используется две разновидности AF-технологии:
послойное спекание плакированного песка лазерным
лучом;
послойное нанесение связующего состава или Inkjetтехнология.
Первая технология - это разновидность упомянутой выше SLS-технологии, с тем отличием, что в качестве модельного материала используется литейный силикатный или циркониевый песок, предварительно плакированный полимером.
После спекания получается так называемая предварительная непрочная «грин-модель», которая требует весьма аккуратного обращения при очистке. Для обеспечения этого процесса, очищенные места сразу же обрабатывают газовой горелкой, создавая более прочную корку. После очистки фрагменты формы помещают в прокалочкую печь и окончательно при температуре до 350 °С укрепляют весь объем формы.
Вторая технология аналогична MJM-технологии, отличаясь тем, что на рабочую платформу впрыскивается не Основной рабочий материал, а связующий состав. Конструкционный литейный песок в последствии подается и разравнивается на рабочей платформе послойно с шагом 0,2-0,4 мм аналогично тому, как это происходит в SLS-системах. При этом дополнительной термической обработки формы не требуется.
123

Независимо от метода построения собственно формы, алгоритм действий конструктора или технолога практически одинаков. Последовательность операций выглядит следующим образом:
создается CAD-модель изделия (см. рис. 7.9);
назначаются припуски на обрабатываемые механически поверхности;
в соответствии с технологическими рекомендациями проектируется литниковая система, которая сочленяется с основной CAD-моделью;
Рис. 7.9. CAD-модели блока цилиндров и фрагментов песчаной формы для его отливки
создается модель песчаного блока, которая обычно имеет форму параллелепипеда, а затем туда будет помещена технологическая CAD-модель;
блок разделяется на части в соответствии с размерами рабочей зоны AF-машины;
выполняются негативные отпечатки технологической модели в песчаном блоке или его фрагментах; аналогично методом вычитания формируются модели стержней;
на завершающем этапе проектирования формируются stl-файлы формы.
Следующий этап –технологический цикл AF-машины, которая формообразует фрагменты формы.
124

После завершения построения фрагменты песчаной форма собирают в одно целое: состыковывают, герметизируют швы, устанавливают технологические холодильники и т. д.
Далее проводится заливка металла, остывание, извлечение и предварительная зачистная обработка отливки (рис. 7.10).
Рис. 7.10. Сборка формы и отливка (чугун)
7.5. Аддитивные технологии порошковой металлургии
Технология spray forming объединяет в себя и литейные знания, поскольку имеет место плавка металла, и технологии распыливания металла, а это один из этапов порошковой металлургии, и вопросы металлографии из общего металловедения. При том в итоге получается заготовку как бы при литье в изложницу. Однако такая заготовка формируется с использованием механизма послойного синтеза, что и объединяет технологию spray forming с AF-технологиями.
Spray forming – это новая технология получения заготовок из конструкционных и специальных сплавов посредством распыливания (атомизации) металла. Основа технологии состоим в послойном напылении металла на подложку и «выращивании» заготовки в виде болванки для последующей механообработки. Металл плавится в плавильной камере, а потом с помощью специального сопла распыливается потоком инерт-
125
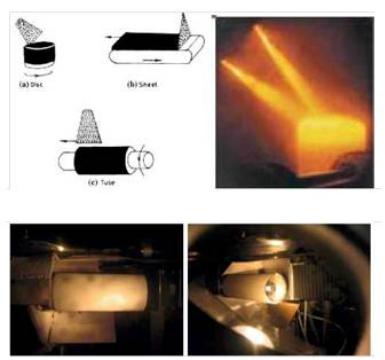
ного газа. При этом частички металла (размером от 10 до 100 мкм) осаждаются на подложку, формируя таким образом заготовку (рис. 7.11).
В отличие от литой заготовки, полученной обычной заливкой металла в изложницу, болванка, полученная методом spray forming, имеет изотропию физико-механических свойств и структуры материала.
Рис. 7.11. Основные схемы технологии Spray forming для получения цилиндрической заготовки
Технология «Spray forming» создана в первую очередь для изготовления деталей высоконагруженных агрегатов аэ-
126
рокосмического назначения из специальных сплавов с повышенными требованиями к эксплутационным свойствам в экстремальных условиях работы. Однако она нашла широкое применение и в серийном общемашиностроительном производстве, например, для изготовления гильз цилиндров автомобильных двигателей из сплавов группы AL-Si.
Такая технология успешно применяется и для заготовок из сплавов, склонных к кристаллизационной ликвации, например, медносодержащих сплавов, применяющихся для получения чистых сверхпроводников группы CuSn, высокопрочных инструментальных материалов типа CuMnNi, CuAlFe для добывающих отраслей промышленности.
Равномерная распределенность химического состава по массиву заготовки и однородность микроструктуры являются главными преимуществами данной технологии. Существенными недостатками являются: большие потери материала (до 20% при атомизации и осаждении металла на подложку) и относительную сложность управления процессом, требующим сложных профессиональных знаний от исполнителей.
Негативные особенности технологии: пористость в микроструктуре материала, образующихся в следствие захвата молекул газа в процессе атомизации и осаждении частиц металла с неполным спеканием друг с другом при кристаллизации. Микропористость металла устраняют посредством горячего изостатического прессования (ГИП) и последующей обработкой пластическим деформированием (прокаткой, ковкой, штамповкой и т.д.).
Основание с подложкой, на которой формируется заготовка совершает различное движение:
-возвратно-поступательное, когда нужно получить заготовку в виде ленты;
-вращательное относительно оси потока распыляемого металла - для получения цилиндрической заготовки-болванки
127
- вращательное относительно оси, перпендикулярной оси потока распыленный частиц - для получения заготовки в виде втулки, кольца или трубы.
Таким образом, технология spay forming открывает широкие возможности для создания материалов с переменными по сечению физико-химическими свойствами (так называемых - градиентных), которые могут быть получены путем послойного нанесения различных, в том числе – разнородных, материалов через два или несколько распылительных сопел.
По мере развития и технического совершенства машин может для быстрого прототипирования представляется интересным практическое использование технологии Spray forming для получения изделия напылением металла на керамическую модель-реплику.
Сущность процесса состоит в следующем. С CADмодели на прототипирующией SLA-установке, выращивается стереолитографическая мастер-модель. По ней изготавливается силиконовая или RIM-форма, в которую вливают жидкую керамику, получая керамическую модель-реплику. Эту мо- дель-реплику устанавливают в Sprayforming-машину, где уже на керамическую модель послойно напыляют расплавленный металл.
Таким образом получают как бы «слепок» с керамической модели-реплики. Последующей механической обработкой удаляют литейный облой и выполняют размеры посадочных поверхностей, чтобы получить окончательно готовое изделие. Максимальный эффект достижим по этой технологии при изготовлении пресс-форм и другой не менее сложной технологической оснастки.
Например, компания RSP Tooling является разработчиком способа изготовления сложной инструментальной оснастки с использованием технологии Spray forming. Машина RSP (рис. 7.12) представляет собой сочетание плавильной машины и устройства для распыливания (атомайзера).
128

Инструментальные сплавы различных групп плавятся в атмосфере инертных газов. Расплав под давлением направляется к распылительному соплу, где с помощью струи азота проводят дисперсное разделение жидкого металла на капельки и быстрое отверждение разбрызганных частиц. До 70% частиц добираются до керамической модели-изложницы уже в твердом состоянии, остальные – долетают в полужидком состоянии. Остающейся тепловой энергии вполне достаточно, чтобы сварить между собой практически все частицы металла.
Рис. 7.12. Машина RSP для изготовления инструментальной оснастки
Металлографические исследования выявили, что такой металл имеет более однородную и мелкозернистую структуру, чем в традиционной отливке. Частицы металла равнораспределенно прилипают к керамической форме, образуя заданный объем заготовки. Стол установки, на котором находится кера-
129