
3307
.pdf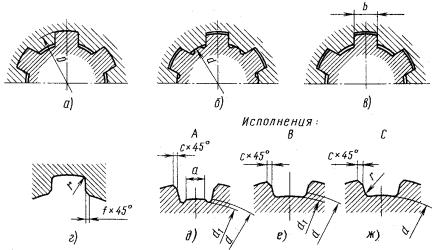
Прямобочные (ГОСТ 1139-80) шлицевое соединение наиболее распространено. Соединение выполняется с центрированием ступицы: по боковым сторонам зубьев в, по наружному диаметру D, по внутреннему диаметру d (рис. 7.7)
Центрирование по “ в ” (рис. 7.7, а) не обеспечивает точной соосности ступицы и вала. Поэтому его рекомендуют при передачи больших моментов. Центрирование по “D” и “d” применяется, когда требуется точность совпадения осей соединяемых деталей (рис. 7.7, б,в).
Рис. 7.7 Виды центрирования прямобочных зубчатых соединений:
а– по боковым граням; б – по наружному диаметру;
в– внутреннему диаметру; г – форма сечения ступицы; д, е – форма сечений вала исполнений б, в
Эвольвентное шлицевое соединение (ГОСТ 6033-80) различают с центрированием ступицы по боковым сторонам “S” (рис. 7.8, а) и по наружному диаметру “D” (рис. 7.8, б). Центрирование по “S” наиболее распространено.
70
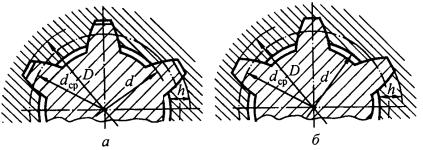
Рис. 7.8 Эвольвентное зубчатое зацепление:
а – центрирование по боковым граням; б – центрирование по наружному диаметру
Достоинства эвольвентных шлицевых соединений:
а – более высокая прочность зубьев, вследствие их утолщения к основанию;
б – высокая технологичность и более низкая стоимость изготовления шлицевых валов.
Вследствие высокой стоимости протяжек для изготовления шлицев в ступицах малых и средних размеров – эвольвентные шлицевые соединения применяются реже прямобочных.
Таблицы 7.4 Примеры обозначения шлицевых соединений
Обозначение |
Способ центрирования |
|
|
Прямобочные шлицевые соединения |
|
|
|
D – 8×36×40H8h7×7F10h9 |
по внешнему диаметру |
|
|
d – 8×36H7e8×40H12a11×7D9f8 |
по внутреннему диаметру |
|
|
b – 8×36×40H12a11×7D9h8 |
по ширине шлиц |
|
|
Эвольвентные шлицевые соединения |
|
|
|
50×2×9H9g |
по эвольвенте |
|
|
50×H7g6×2 |
по внешнему диаметру |
|
|
71 |
|
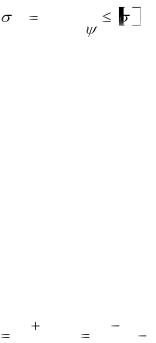
Треугольное зубчатое соединение применяется только в качестве неподвижного при передаче небольших моментов. Центрирование такого соединения осуществляется только по боковым граням. Применяются также конические шлицевые соединения (конусность 1 : 16).
Число Z и размеры шлицев принимаются в зависимости от диаметра вала по соответствующему ГОСТ. Длина зубьев определяется длиной ступицы, а если ступица подвижная – величиной хода еѐ перемещения.
Расчѐт шлицевых соединений производится обычно как проверочный.
Шлицевые соединения рассчитываются на смятие по формуле:
|
|
2М |
; |
|
см |
|
|
см |
|
d c |
|
|||
|
Zh |
|
где: ζсм – расчѐтное напряжение смятия на рабочих поверхностях шлицев;
М– передаваемый момент;
dc – средний диаметр шлицевого соединения; Z – число шлиц;
h – высота поверхности контакта шлицев, принимаемая равной длине ступицы;
ψ – коэффициент, учитывающий неравномерность распределения нагрузки между шлицами, принимаемый равным
0,7…0,8;
[ζ]см – допускаемое напряжение смятия для рабочих поверхностей шлицев.
Размеры dc и h определяют из выражений: прямозубных шлицев:
d |
|
D d |
; h |
D d |
2q ; |
|
c |
2 |
2 |
||||
|
|
|
||||
|
|
|
|
Для шлицев эвольвентного профиля с центрированием по
S: dc = dд = mz и h = m = dд/z;
72
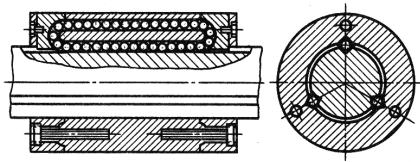
где: dд – диаметр делительной окружности; m – модуль закрепления;
для шлицев эвольвентного профиля с центрированием по D : dc = dд = mz и h = 0,9m = 0,9 dд/z;
для шлицев треугольного профиля:
dc = dд = mz и h = [D – da];
Допускаемое напряжение на смятие [ζ]см для шлицевого соединения при среднем режиме работы можно принимать: для неподвижного с термической обработкой шлицев [ζ]см = 100…140 МПа и без термической обработки [ζ]см = 60…100 МПа.
При лѐгком режиме работы значение этих напряжений можно увеличить на 20…40%, а при тяжелом режиме их необходимо снизить на 30…50%.
В последнее время начали применять шариковые шлицевые соединения (рис. 7.9), требующие очень малых усилий для перемещения ступиц. При перемещении последних под нагрузкой несущая способность шариковых шлицевых соединений в несколько раз больше, чем обыкновенных шлицевых соединений. Так как шариковые шлицевые соединения по конструкции сложнее и дороже обыкновенных, то применение их ограничено.
Рис. 7.9 Шариковое шлицевое соединение
73
Допускаемый момент (Нм) для шарикового шлицевого соединения (твердость вала и ступицы не менее 60 НRС):
Т = 0,016 Zшл ℓ d Dср ,
где Zшл – число рабочих выступов (шлиц); ℓ – рабочая длина соединения, мм;
d, Dср – диаметры шариков и окружности расположения центров шариков, мм.
ЛЕКЦИЯ 8.
СОЕДИНЕНИЯ С НАТЯГОМ
Учебные вопросы
1.Общие сведения
2.Расчет цилиндрических соединений с натягом
8.1. Общие сведения
Соединения с натягом относятся к группе неразъѐмных соединений и представляют собой напряжѐнные соединения, в которых натяг создаѐтся необходимой разностью посадочных размеров сопрягаемых деталей, а сами детали удерживаются в проектном положении за счѐт сил упругости.
Соединения с натягом можно разделить на две группы:
-соединение деталей по цилиндрическим или коническим поверхностям (здесь отсутствуют какие-либо специальные соединительные детали);
-соединения деталей по плоскости с помощью стяжных колец или планок.
Основное применение в машиностроении имеют соединения первой группы (по цилиндрическим поверхностям).
Общим достоинством соединений с натягом является возможность их выполнения для очень больших нагрузок и хорошая работа при ударном нагружении. Взаимное смещение
74
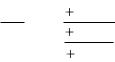
деталей в соединениях с натягом предотвращается силами трения на поверхности контакта.
Характерной особенностью соединений с натягом является то, что они могут воспринимать произвольно направленные силы и моменты, а соединения по цилиндрическим и коническим поверхностям дополнительно обеспечивают хорошее центрирование и не требует специальных крепѐжных деталей.
К недостаткам соединений с натягом необходимо отне-
сти:
-сложность сборки и разработки (особенно внутри неразъѐмного корпуса), возможность ослабления посадки и повреждения посадочной поверхности при разборке;
-большое рассеивание прочности соединения в связи с рассеиванием посадочных размеров в предела допуска.
8.2. Расчет цилиндрических соединений с натягом
Этот тип соединений очень широко применяется при значительных (особенно динамических) нагрузках и отсутствии необходимости в частой сборке и разборке. Шлицевые и особенно шпоночные соединения при динамическом нагружении быстро обминаются.
Примеры соединений: колѐсные центры на ось и бандажи железнодорожных колѐс, венцы зубчатых и червячных колѐс, диски турбин, роторы электродвигателей, гребные винты кораблей, подшипники качения, штампы и т.д.
Характер соединения определяется натягом, который определяется стандартной посадкой.
Например: H 7 Ф40 0.025
S6 0.059
0.043
Минимальный натяг Nmin = 18 мкм Максимальный натяг Nmax = 59 мкм
75

По способу сборки соединения с натягом разделяют на собираемые запрессовкой и соединения, собираемые способом температурного деформирования одной из сопрягаемых деталей.
Нужно отметить, что прочность соединения деталей, собираемых способом температурного деформирования при том же натяге, более чем 1,5 раза превышает прочность соединения запрессовкой. Это обусловлено тем, что при запрессовке происходит частичное сглаживание шероховатостей деталей на сопрягаемых поверхностях.
Применение нагрева или охлаждения для сборки особенно удобно для деталей с большой длиной (валы, оси) при этом температура нагрева должна быть ниже температуры низкого отпуска. До 1500С нагрев мелких деталей осуществляется в масле, а также в электрической или газовой печи.
Охлаждение применяют преимущественно для небольших деталей при их установке в массивные корпуса с помощью твѐрдой углекислоты (сухой лѐд – 790С) или в жидком воздухе (температура1900С) в последнем случае нужно быть особенно осторожным и обеспечить тщательное обезжиривание деталей.
Необходимая величина натяга соединения определяется потребным давлением p на посадочной поверхности, которое должно быть таким, чтобы силы трения оказались больше внешних сдвигающих сил (рис. 8.1).
При нагружении соединения осевой силой А:
A N |
f |
P d p |
f |
; |
|
k |
k |
||||
|
|
|
где: N - сила нормального давления на сопрягаемые поверхности;
d, ℓp – диаметр и длина посадочной поверхности; f – коэффициент трения (см. табл. 1);
k – коэффициент запаса сцепления (k ≈ 1,5…2).
76
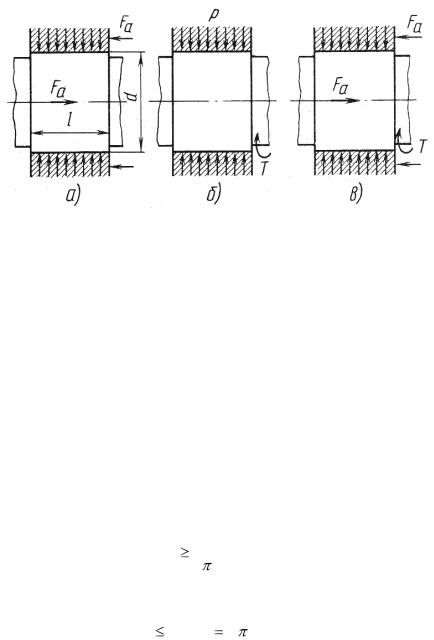
Рис. 8.1 Расчетные схемы соединений с натягом
Таблица 8.1
Усредненные значения коэффициента трения при расчете посадок с натягом
Способ |
|
|
|
|
|
Алюми- |
|
|
|
|
|
|
|
|
|
|
ниевые |
|
|
|
|
сварки |
|
|
|
|
|
|
|
|
Пласт- |
|
Сталь |
Чугун |
|
|
и маг- |
|
Латунь |
||||
соеди- |
|
|
|
массы |
||||||
|
|
|
|
|
|
ниевые |
|
|
||
нения |
|
|
|
|
|
|
|
|
|
|
|
|
|
|
|
|
сплавы |
|
|
|
|
|
|
|
|
|
|
|
|
|
|
|
Меха- |
0,06– |
0,07– |
|
|
0,02– |
|
0,05– |
|
||
ниче- |
|
|
|
0,6–0,5 |
||||||
0,13 |
0,12 |
|
|
0,06 |
|
0,10 |
||||
ский |
|
|
|
|
||||||
|
|
|
|
|
|
|
|
|
|
|
Тепло- |
0,14– |
0,07– |
|
|
0,05– |
|
0,05– |
– |
||
вой |
0,16 |
0,09 |
|
|
006 |
|
0.14 |
|||
|
|
|
|
|||||||
Откуда посадочное давление p равно: |
|
|
||||||||
|
|
P |
|
AK |
|
(1) |
||||
|
|
|
|
|
|
|
|
|
||
|
|
|
f |
d |
|
|||||
|
|
|
|
|
|
При нагружении соединения крутящим моментом Mk:
M |
|
N |
f |
|
d |
P d |
|
f d |
; |
|||
k |
|
|
p |
|
|
|
||||||
k 2 |
k 2 |
|||||||||||
|
|
|
|
|||||||||
|
|
|
|
|
|
|||||||
|
|
77 |
|
|
|
|
|
|
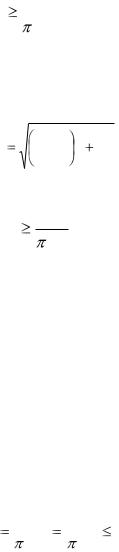
откуда:
P |
2M k K |
|
(2) |
|||
d 2 |
p |
f |
||||
|
|
|||||
|
|
|
|
|
||
При одновременном нагружении |
соединения крутящим |
моментом M k и осевой силой A расчѐт ведут по равнодействующей осевой и окружной силе:
|
2M k |
2 |
|
T |
A2 ; |
||
d |
|||
|
|
по формуле:
T K
P (3) f d
В соединениях с натягом нагрузка по длине распределяется резко неравномерно и у торца ступицы со стороны передачи крутящего момента возникают острые пики напряжений.
Несущая способность соединения может быть существенно повышена оксидированием, а также гальваническими покрытиями хромом и никелем. Большой эффект даѐт введение в соединение порошка корунда (при сборке температурным деформированием); в этом случае коэффициент трения покоя возрастает больше чем в 2 раза.
При нагружении соединения изгибающим моментом M на равномерную эпюру давлений от посадки накладывается эпюра давлений, характерная для изгиба (рис. 8.2).
Наиболее давление в соединении от изгиба:
P |
4 M |
12M |
P , |
|||
|
|
|
|
|
||
|
|
|
|
d 2 |
||
1 2w |
|
|
где: 4πмножитель, учитывающий серпообразный характер эпюры давлений по окружности цапфы;
78
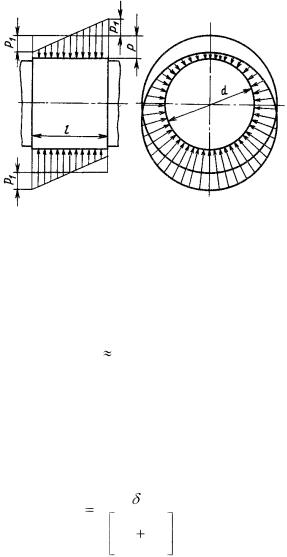
W = d ℓ26 – момент сопротивления изгибу диаметрального сечения цапфы.
Рис. 8.2 Эпюра давлений в соединении при нагружении изгибающим моментом
Изгибающий момент может достигать такой величины, когда давление на посадочной поверхности снижается до 0,25P (т.е. P1 ≈ 0,25P). Исходя из этого условия допустимый момент изгиба не должен превышать величины:
M 0,2Pd 2 |
(4) |
Как видно из выражения (4), допустимый изгибающий момент пропорционален квадрату длины цапфы. Поэтому при нагружении соединения значительным изгибающим моментом необходимо увеличивать еѐ длину.
Посадочное давление р связано с натягом δ зависимостью Ляме.
p |
|
|
|
(5) |
||
|
|
|
||||
|
d |
c1 |
|
c2 |
|
|
|
E1 |
|
E2 |
где
79