
Расчет и конструкирование станков. Старов В.Н
.pdfСТАРОВ В.Н.
РАСЧЕТ
ИКОНСТРУИРОВАНИЕ
СТАНКОВ
Часть 1
Министерство образования Российской Федерации Воронежский государственный технический университет
СТАРОВ В.Н.
РАСЧЕТ И КОНСТРУИРОВАНИЕ
СТАНКОВ
Часть 1
Пособие для студентов специальностей 120200 - Металлорежущие станки и инструменты
120100 -Технология машиностроения всех форм обучения
Воронеж - 2003
Составитель Старов В.Н.
УДК 621..9.06 : 658.06 : 658.512.011
Старов В.Н. РАСЧЕТ И КОНСТРУИРОВАНИЕ СТАНКОВ/ Часть 1. Пособие для студентов специальностей 120200 -
Металлорежущие станки и инструменты. 120100 -Технология машиностроения; всех форм обучения./Воронеж. гос. техн. ун-т. Сост.В.Н.Старов. Воронеж, 2003. 160с.
Пособие составлено на материалах работ авторов |
Г.Н Васильева |
(Автоматизация проектирования металлорежущих |
станков); Пуша |
В.Э., Пигерт Р, Сосонкин В.Е. (Автоматические станочные систем) Врагова Ю.Д.(Анализ компоновки металлорежущих станков. В нем также изложено видением автора на современные требования к методическому обеспечению качества проектирования станочного оборудования, предъявляемого к конструкторско-расчетным работам студентов технических специальностей. в частности специальностей 120100 и 120200 при изучении дисциплин: Металлорежущие станки; Расчет и конструирование станков и других.
Ил. 108. Табл. 6. Библиогр: 7 назв.
Реценззент
Ответственный за выпуск зав. кафедрой проф. В.М. Пачевский
Электронная версия ( на магнитном носителе)
ОГЛАВЛЕНИЕ
Глава 1 ОБЩИЕ ОСНОВЫ ПРОЕКТИРОВАНИЯ МЕТАЛЛОРЕЖУЩИХ СТАНКОВ
1.1ПРЕДСТАВЛЕНИЕ ПРОЦЕССА ПРОЕКТИРОВАНИЯ МЕТАЛЛОРЕЖУЩЕГО СТАНКА КАК ОБЪЕКТА НАПРАВЛЕННЫХ ДЕЙСТВИЙ………………………………
1.2СИСТЕМНЫЙ ПОДХОД В ПРОЕКТИРОВАНИИ СТАНОЧНОГО ОБОРУДОВАНИЯ………………………….
1.3УРОВНИ АВТОМАТИЗАЦИИ,ИСПОЛЬЗУЕМЫЕ ПРИ ПРОЕКТИРОВАНИИ СТАНКОВ……………………………...
1.4ОБЩИЙ ПОДХОД К РЕАЛИЗАЦИИ МЕТОДОВ МАТЕМАТИЧЕСКОГО МОДЕЛИРОРВАНИЯ ПРИ СОЗДАНИИ ОБОРУДОВАНИЯ………………………...
Глава 2 АВТОМАТИЗИРОВАННЫЕ НЖЕНЕРНЫЕ РАСЧЕТЫ СТАНОЧНЫХ ДЕТАЛЕЙ И УЗЛОВ
2.1МАТЕМАТИЧЕСКИЕ ОСНОВЫ ИНЖЕНЕРНЫХ РАСЧЕТОВ НА ЭВМ…………………………………………..
2.2ИНЖЕНЕРНЫЕ МЕТОДИКИ РАСЧЕТА ДЕТАЛЕЙ
ИУЗЛОВ СТАНКОВ…………………………………………
2.3АВТОМАТИЗИРОВАННЫЙ РАСЧЕТ ДЕТАЛЕЙ
И УЗЛОВ СТАНКОВ ПО УНИВЕРСАЛЬНЫМ МАТЕМАТИЧЕСКИМ МОДЕЛЯМ ……………………………
Г лава 3 ОСНОВНЫЕ ОБЪЕКТЫ СТАНОЧНОГО
ОБОРУДОВАНИЯ
3.1. ОСНОВНЫЕ ПАРАМЕТРЫ И ХАРАКТЕРИСТИКИ СТАНКА…………………………………………………………….
3.2.НЕСУЩАЯ СИСТЕМА СТАНКА………………………..
3.3.НАПРАВЛЯЮЩИЕ…………………………………………..
3.4.ГЛАВНЫЙ ПРИВОД И ШПИНДЕЛЬНЫЕ УЗЛЫ
3.5.ПРИВОД ПОДАЧ И ТЯГОВЫЕ УСТРОЙСТВА……..
ЛИТЕРАТУРА
3
Глава 1 ОБЩИЕ ОСНОВЫ ПРОЕКТИРОВАНИЯ
МЕТАЛЛОРЕЖУЩИХ СТАНКОВ
1.1 ПРЕДСТАВЛЕНИЕ ПРОЦЕССА ПРОЕКТИРОВАНИЯ МЕТАЛЛОРЕЖУЩЕГО СТАНКА КАК ОБЪЕКТА
НАПРАВЛЕННЫХ ДЕЙСТВИЙ
Процесс проектирования заключается в реализации принятой концепции станкостроения, создании работоспособной эффективной станочной системы и разработке конструкторской документации, необходимой для изготовления станка в производственных условиях, причем в заданных масштабах. Согласно традиций, заложенных, в том числе, в государственных стандартах, есть стадии разработки конструкторской документации, которые включают: техническое задание, техническое предложение, эскизный проект, технический проект и разработку рабочей документации. Кроме того, в большинстве случаев для коррекции рабочей документации необходимо изготовление и испытание опытного образца, изготовление установочной серии. Несколько иная идея заложена в проектировании оборудования при использовании компьютерных технологий, где основой информации об объекте является определенные совокупности
в форме электронных |
носителей. |
Однако и в этом случае основой для |
|
проектирования всех |
подсистем |
станка |
является технологический |
процесс изготовления |
и сборки |
изделия. |
Причем в техническом |
задании формулируются основные характеристики проектируемого
станка, обеспечивающие получение |
на нем |
деталей заданного |
качества, точности; указываются |
условия |
эксплуатации, область |
применения и другие сведения, определяющие исходные данные проектирования. Базой для назначения технических характеристик проектируемого оборудования являются результаты научноисследовательских работ, технические и технологические изыскания, включающие экспериментальные исследования работоспособности их узлов, а также процесса обработки (формообразования) детали, патентный поиск и анализ имеющихся образцов и многое другое.
Основным содержанием этапа работ, выполняемых в рамках технического предложения, является выбор принципиальной схемы обработки на станке и анализ рациональных компоновочных вариантов станка. Окончательные решения по оптимальному варианту станка принимают на основе технико-экономического анализа. Схема обработки, кроме исходных данных для анализа компоновок станка, формирует требования к функционированию основных узлов оборудования. Объем работ, выполняемых на этапе технического предложения, зависит от конкретности и обоснованности технического задания.
Этап эскизного проекта содержит компоновочные, схемные и конструктивные принципиальные решения проектируемого станка. Основой для принятых решений являются расчеты систем станка и его узлов с учетом показателей качества, которые определяют, исходя из требований стандартов ИСО к станку или производству в целом.
На этапе технического проектирования должны быть получены окончательные компоновочные, конструктивные и схемные решения и их детальная проработка. Разрабатывают сборочные чертежи всех узлов и спецификации к ним, уточняют расчеты, используя оптимизационные модели, проверяют правильность компоновки и сборки, формируют окончательные значения технических характеристик станка.
Этап рабочего проектирования завершает процесс подготовки конструкторской документации. Она содержит описательную и графическую часть. Чертежи включают общие виды узлов, их деталировку и схемы, включая кинематические, гидравлические, пневматические и электрические. Описательную часть в основном составляет паспорт станка, (описание работы основных узлов и систем, а также инструкции по эксплуатации, наладке, транспортированию и установке). В процессе подготовки рабочего проекта должны быть максимально учтены требования ЕСКД, стандартизации, унификации и нормализации, а также требования технологичности конструкции.
В дальнейшем правильность полученных конструктивных решений оценивается при испытаниях опытного образца. По результатам испытаний производят корректировку рабочей документации.
4
Если рассмотреть весь процесс создания станка, то после отработки рабочей документации разрабатывают технологию изготовления станка в соответствии с заданной серийностью и запускают станок в серию.
Как считает автор работы /1/, характерным признаком процесса проектирования является его неопределенность. Рассмотрим эти соображения Известно, что все этапы проектирования последовательно уменьшают неопределенность проектной задачи. При этом основными принципами, обеспечивающими решение проектной задачи, являются последовательность и итерационность. Последовательность заключаете в строгой очередности выполнения этапов проектирования станка, а итерационность — в корректировке предыдущих этапов проектирования исходя из результатов, полученных на последующих этапах. На рис. 1 итерационность процесса проектирования обозначена обратными связями, которые направлены от последующих этапов создания станка е предыдущим.
Принято, что для автоматизации этапов процесса разработки станка с использованием ЭВМ следует использовать или построить следующие системы.
Во-первых, это собственно система автоматизированного проектирования, известная как САПР. Объектами систем автоматизированного проектирования (САПР) являются этапы технического предложения, эскизного, технического и рабочего проектирования. Второе. Автоматизированные системы научных исследований (АСНИ), которые включают в себя системы обеспечения поисковых работ (в виде банков данных), а также системы обеспечения научного эксперимента, и другие подсистемы, охватывающие этап формирования технического задания.
На следующем этапе могут быть использованы автоматизированные системы технологической подготовки производства (АСТПП).
Автоматизированные системы управления технологическими процессами (АСУТП), которые разрабатывают на базе оборудования с числовым программным управлением (ЧПУ), предназначены для реализации производственных программ. Основу их могут составлять гибкие производственные системы (ГПС) или гибкие
автоматизированные производственные системы (ГАП). Есть также интегрированные системы САПР, предназначенные для автоматизации процесса проектирования станочного оборудования или его отдельных узлов, которые объединяют в качестве подсистемы САПР, АСТПП и АСУТП. Примеров таких систем много, например, проектирование и производство шпиндельных коробок агрегатных станков, вырубных штампов и другие.
Важное место занимают автоматизированные системы контроля и измерения (АСКИО).
Высшим уровнем автоматизации процесса создания станка являются комплексно-автоматизированные системы типа: АСНИ — САПР — АСТПП — АСУТП. Формирование технического и математического обеспечения систем автоматизации процесса проектирования в целом или отдельных его этапов требует анализа вида проектных работ.
Вид проектных работ определяется уровнем проектирования и методикой проектирования. По уровню проектирования различают
функциональное и конструкторское проектирование, в зависимости от методики проектирования — аналитическое и эмпирическое
проектирование, рис.2.
Эти виды работ необходимо рассматривать в комплексе, так как качество выполнения одних проектных работ определяет трудоемкость и эффективность последующих проектных работ. Функциональное проектирование включает в себя концептуальное проектирование и схемотехническое. Эти виды работ являются наиболее ответственными, поскольку они выполняются на ранних стадиях проектирования.
Концептуальное проектирование предполагает поиск принципа функционирования отдельных станочных узлов и станка в целом, который определяет тип устройств, выполняющих
5
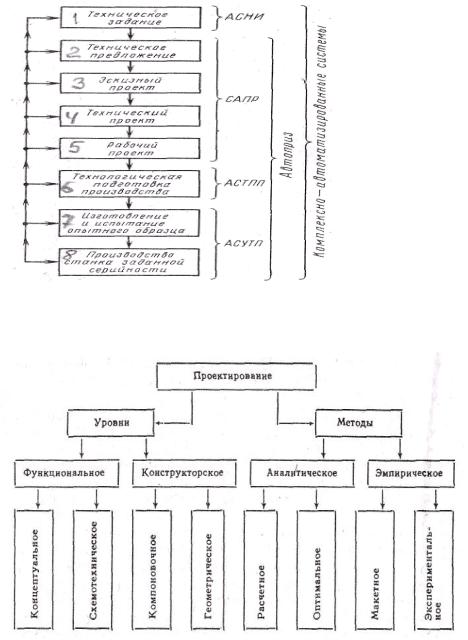
Рис. 1. Системы автоматизации этапов создания станка /1/
Рис. 2. Виды проектирования
отдельные функции станка (главное движение, движение подачи, вспомогательные движения и т. д.). Принцип функционирования должен обеспечивать выполнение характеристик, заложенных в техническом задании. В некоторых случаях необходима разработка принципиально новых технических решений, чтобы достичь требуемых характеристик. Например, привод главного движения металлорежущего станка может быть гидравлического или электрического типа. По способу регулирования частоты вращения шпинделя — ступенчатый и бесступенчатый. Ступенчатый привод проектируют на основе одноили многоскоростного двигателя, шестеренкой коробки скоростей или ступенчато-шкивной передачи.
Привод бесступенчатого регулирования включает в себя либо нерегулируемый двигатель и вариатор, либо регулируемый двигатель. Выбор типа устройств, реализующих те или иные функции станка, осуществляется на базе исходных данных, содержащихся в техническом задании (технические параметры станка, требования надежности и долговечности, габаритные размеры, эксплуатационные требования, ориентировочная стоимость и т. д.).
При схемотехническом проектировании разрабатываются принципиальные и функциональные схемы: электрические, электронные, кинематические, гидравлические, пневматические и т. д. Конструкторские виды работ, включающие компоновочные и геометрическое проектирование, занимают наибольший объем в процессе разработки машин, и их выполняют по результатам функционального проектирования.
Компоновочное (топологическое) проектирование в основном заключается в разработке компоновки систем станков, отдельного станка или его узлов. Процесс компоновки связан с размещением конструктивных элементов в пространстве с учетом их функционального назначения и ограничений.
Расчетами в процессе компоновки, кроме компактности конструкции, оценивается также эффективность компоновочного решения для обеспечения процесса функционирования станка или станочной системы. Большое значение при выборе конструкции и размещения
6
элементов имеют требования художественного конструирования, |
проектирования, при которой рассчитывают оптимальные параметры |
|||||
эргономики и условий эксплуатации. |
конструкции, получила название оптимального проектирования. |
|
||||
Эффективное конструктивное решение достигается лишь при |
Расчетное проектирование выполняют по апробированным |
|||||
разработке нескольких вариантов конструкции, их всестороннем |
аналитическим зависимостям. Для удобства некоторые зависимости |
|||||
анализе и выборе наиболее рационального из них. Обычно этот вариант |
представлены в виде таблиц, графиков или номограмм. Иногда |
|||||
не является наилучшим во всех отношениях, а обладает либо средними |
приходится задаваться конструктивными параметрами, тогда их |
|||||
значениями всех характеристик (в случае компромиссного решения), |
правильность оценивают при проверочных расчетах. Расчетные |
|||||
либо высокими значениями наиболее важных характеристик. |
методики |
отрабатывают |
с |
помощью |
теоретических |
и |
Кроме требования обеспечения заданного уровня параметров |
экспериментальных исследований, а также на основе анализа опыта |
|||||
функционирования станочного узла, приходится учитывать и |
эксплуатации. |
|
|
|
|
|
разнообразные требования, относящиеся к эксплуатации станка и |
Расчетное проектирование является преобладающим при не- |
|||||
процессу его изготовления. Показатели эффективности процесса |
автоматизированном проектировании и базируется на методиках |
|||||
изготовления станка будут определяться: технологичностью отдельных |
расчета, которые изложены в справочниках и справочных пособиях для |
|||||
деталей и технологичностью процесса сборки узлов, максимальной |
конструктора-машиностроителя, в специальной литературе по расчету |
|||||
стандартизацией деталей и узлов, подбором материала деталей, их |
и конструированию станков, в руководящих материалах и т. д. В |
|||||
термообработкой и назначенными посадками в местах сопряжения |
качестве примера можно назвать инженерные методики расчета |
|||||
деталей и т.д. |
различных станочных передач: ременных, винтовых, зубчатых и т. д. |
|
||||
Требование снижения затрат на эксплуатационные расходы |
Основным недостатком расчетного проектирования является |
|||||
обеспечивается соответствующей ремонтопригодностью узлов, |
получение лишь допустимых конструктивных параметров, причем |
|||||
условиями настройки их параметров. |
иногда эти решения получают в виде области значений параметров и |
|||||
Основой для создания конструкций станочных узлов является |
выбор конкретных значений определяется опытом и интуицией |
|||||
конструктивная преемственность, т. е. использование предше- |
проектировщика. Методики расчетного проектирования имеют |
|||||
ствующего опыта. Каждый современный станок в той или иной степени |
ограниченную область применения, так как их создают для типовых |
|||||
является результатом работы конструкторов нескольких поколений. |
конструкций. Если конструктивная схема меняется или не |
|||||
Основной объем работ, выполняемых при геометрическом |
выполняются определенные ограничения, то необходима уже другая |
|||||
проектировании, заключается в подготовке конструкторской до- |
расчетная методика. |
|
|
|
|
|
кументации. При выполнении чертежных работ необходимо |
Оптимальное проектирование применяют при необходимости |
|||||
придерживаться требований ЕСКД для обеспечения легкого чтения |
выбора конструктивного решения из нескольких вариантов. |
|||||
конструкторской документации. |
Особенностью этого вида проектирования является формирование |
|||||
При аналитическом проектировании проектные параметры |
критериев для оценки качества проектных решений. Основными |
|||||
вычисляют с помощью математических выражений, полученных на |
критериями качества являются надежность, производительность и |
|||||
основе научных исследований, опыта проектирования и эксплуатации |
экономичность конструкции. В большинстве случаев значения |
|||||
оборудования. |
критериев не дают предпочтения одному варианту и отбирается два или |
|||||
Расчетное проектирование позволяет получать рациональные |
более конкурирующих варианта, у которых эти значения являются |
|||||
конструкторские решения, т. е. решения, допустимые с точки зрения |
наиболее |
высокими. Иногда |
окончательный |
выбор конструктивного |
||
выполнения всех условий и ограничений на конструкцию. Методика |
|
|
|
|
|
|
7
решения возможен только после экспериментального исследования опытного образца станка.
Неопределенности, возникающие при выборе конструкции из конкурирующих вариантов, а также значительные затруднения возникающие при формировании критериев, не позволяют точно оценивать качество конструктивных вариантов; при этом возможны большие затраты времени на вычисления значений критериев. Поэтому иногда используют относительную систему оценок для поиска конкурирующих вариантов, а затем окончательный вариант выбирают по одному или двум наиболее важным критериям. Если удается получить критерии в аналитическом виде как функции конструктивных параметров, то выбор этих параметров может осуществляться путем нахождения их значений, обеспечивающих наилучшее качество конструкции, т. е, оптимума критериев качества. На практике обычно удается получить значения параметров конструкции, близкие к оптимальным в силу многокритериальности задачи оптимизации, приближенности критериев, отсутствия методов поиска экстремума или значительной трудоемкости методов поиска, а иногда из-за невозможности реализовать оптимальные параметры станка. Следовательно, при оптимальном проектировании может осуществляться не только выбор наилучшей конструктивной схемы узла станка, но и выбор оптимальных параметров конструкции. Вследствие многокритериальности задачи выбора конструктивного варианта и его параметров, правильность принимаемого решения во многом определяется интуицией и опытом проектировщика.
При макетном проектировании изготовляют макет, который представляет собой физическую модель исследуемого узла или станка в целом. Эта модель, как правило, реализует одну или несколько характеристик станка или процесса, происходящего в станке. Макет может быть наглядной объемной моделью станка, воспроизводящей компоновку станка в масштабе, или, например, тепловой моделью станины станка для анализа тепловых деформаций.
Реализуемая характеристика или процесс в макете должны иметь физическую природу оригинала. По результатам испытаний макета, который подобен реальной конструкции, делают заключение о целесообразности того или иного конструктивного решения. Широко
применяют макетирование при отработке компоновочных решений металлорежущих станков с точки зрения технической эстетики и эргономики. Макетирование используют и при оценке конструктивных вариантов деталей несущей системы станка. В этом случае макет, например станины станка, выполняют из оргстекла или другого легкообрабатываемого материала.
Эффективно макетное проектирование при поиске конструктивных решений систем управления оборудованием. Оно позволяет подобрать основные элементы системы и отладить их взаимодействие. Достоверность рекомендаций, полученных при макетировании, зависит от правильности расчета значений коэффициентов подобия, с помощью которых результаты исследования макета переносятся на реальную конструкцию. Ограниченные возможности макетирования в основном проявляются при имитации процесса обработки на станке, а также при варьировании конструктивных параметров макета.
Экспериментальное проектирование заключается в отработке конструкции на стенде, имитирующем конструкцию основных узлов станка и условия его работы. Уменьшение стоимости экспериментального стенда достигается за счет изготовления лишь тех узлов, работоспособность которых вызывает сомнение. Изменяя конструктивные элементы стенда, добиваются такого запаса работоспособности этих узлов, который может гарантировать требуемые характеристики проектируемого станка.
Корректировка конструкторской документации на последних этапах проектирования производится по результатам экспериментального исследования опытного образца. Окончательное заключение о качестве проекта и необходимых конструктивных изменениях может дать только производственный эксперимент, т. е. наблюдение за работой станка в производственных условиях. Кроме затрат на изготовление объекта испытаний и проведение эксперимента, нужно учитывать затраты на обработку результатов эксперимента, которые являются основой для оценки работоспособности конструкции и определения направлений ее улучшения.
Достоинством этого вида проектирования является максимальная достоверность принимаемых конструкторских решений, что, в свою очередь, обеспечивает сокращение временных и материальных затрат
8
на доводку станка. Основные недостатки — более низкие, чем при макетировании, возможности экспериментальной установки в части варьирования конструктивных решений и значительная стоимость. Экспериментальное проектирование необходимо особенно при разработке станков, использующих новые технологические процессы обработки или новые конструкторские решения.
Каждый вид проектирования включает эвристические (творческие) и алгоритмические (рутинные) операции. Алгоритмические операции можно реализовать на ЭВМ. Это деление достаточно условно, так как изучение механизма творческой деятельности конструктора уже в настоящее время позволяет алгоритмизировать операции, ранее относившиеся к эвристическим.
Основным признаком, определяющим долю творческой деятельности в процессе, проектирования, является неопределенность проекта. На начальных этапах проектирования, когда неопределенность проектных параметров наибольшая, объем эвристических операций максимален. По мере уточнения проектных решений увеличивается доля алгоритмических операций.
Творческая отдача конструктора проявляется в основном при выборе физического принципа действия отдельных узлов станка (концептуальное проектирование), при формировании принципиальных и функциональных схем станка и его узлов (схемотехническое проектирование), а также при компоновке станка и станочных узлов (компоновочное проектирование). Для достижения заданных характеристик в некоторых случаях конструкторские решения выполняются на уровне изобретений.
Работы, связанные с теоретическими или экспериментальными исследованиями конструкций (аналитическое и эмпирическое проектирование), в большом объеме содержат алгоритмизируемые процедуры вычислительного характера.
Основой формирования проектных гипотез обычно служит базовая модель, т. е. действующий образец конструкции станка или его отдельного узла. Разработку нового конструктивного образца, который отвечает требованиям технического задания, выполняют с учетом результатов эксплуатации и испытаний базовой модели. Степень переработки узлов определяется отличием требуемых технических
характеристик нового станка от характеристик действующего образца, изменением условий эксплуатации, введением новых конструкторских и технологических решений. Переработке подвергаются те узлы или детали, которые ограничивают повышение качества проектируемого станка до требуемого уровня.
Метод проб и ошибок часто используют и в инженерных расчетах станочных деталей и узлов, например, задаются каким-либо значением неизвестного конструктивного параметра, а затем в результате вычисления других конструктивных параметров оценивают приемлемость принятого значения первого проектного параметра. Эту процедуру приходится повторять несколько раз, пока не будет найдена совокупность значений конструктивных параметров, соответствующих ограничениям на параметры и качественным показателям конструкции
Повышение эффективности поиска новых конструктивных решений методом проб и ошибок обеспечивается применением некоторых эвристических приемов, сформулированных для изобретательской деятельности, таких, например, как инверсия, аналогия, метод «мозгового штурма».
Инверсия предполагает изменение на обратные функций, форм и расположения деталей конструкции. Иногда выгодно поменять детали ролями, т.е. ведомую деталь сделать ведущей, неподвижную — подвижной, направляющую — направляемой, охватывающую — охватываемой, внутреннюю — внешней, верхнюю — нижней.
Изменение расположения может касаться и конструктивных элементов, например, крепежных, уплотнительных, пружинных, подшипниковых и кулачковых: шпонку с вала перенести на ступицу зубчатого колеса, уплотнение — с вала на фланец, подшипники с вала
— на колесо, пружину сжатия заменить пружиной растяжения. Возможно инвертирование форм деталей: выпуклую поверхность заменить на вогнутую, наружный конус — на внутренний. В результате инвертирования конструкция по сравнению с исходной получает новые характеристики, как эксплуатационные, так и технологические.
Аналогия опирается на подобие конструкций в природе и технике. Широко применяется аналогия в роботостроении при разработке как механических устройств робота, так и его «органов чувств».
9
Конструктивные аналоги могут быть заимствованы из других областей техники.
Метод «мозгового штурма» — это метод коллективного генерирования технических решений. Группа специалистов состоит из специалистов смежных, а иногда даже далеких областей науки и техники. Для специалистов отдельной области науки и техники возможен определенный «кризис идей», связанный с некоторым «избытком информации» и ограничивающим направления совершенствования конструкции. Специалисты из одних областей науки и техники могут переносить идеи в другие области. Необходимым условием является отсутствие критики высказываемых идей, чтобы не сковывать творческую инициативу членов группы. После формирования достаточно большого числа решений их анализируют специалисты, которые могут развить наиболее плодотворные технические решения.
Множество рассматриваемых вариантов конструкции значительно сокращается при наличии унифицированных узлов и деталей. Применение принципа агрегатирования при проектировании автоматических линий из унифицированных узлов и деталей позволяет в несколько раз снизить время проектирования по сравнению со средними сроками проектирования тех же автоматических линий из оригинальных сборочных единиц. Нужное конструктивное решение иногда находят в результате патентного исследования.
Автоматизация проектирования и управления производством с помощью ЭВМ позволяет избежать неудобств метода проб и ошибок, метода с набором эвристических приемов, так как описанные
процедуры трудно формализуемы, а |
компьютерные программы |
||||
ориентированы на это. |
|
|
|
||
Таким |
образом, |
методической |
основой |
успешного |
|
проектирования |
является автоматизированное |
проектирование, |
имеющее совершенно иной подход, чем традиционное проектирование, методы которого отходят в прошлое. При этом вся идеология должна быть совершенно иной, чем та, которая применяется при неавтоматизированном проектировании. Эффективное использование ЭВМ обеспечивают системные методы проектирования, которые в той
или иной степени реализуют системный подход к объектам, процессам
исредствам проектирования.
1.2СИСТЕМНЫЙ ПОДХОД В ПРОЕКТИРОВАНИИ СТАНОЧНОГО ОБОРУДОВАНИЯ
Из определения технической системы, которую определяют как совокупность элементов с указанием связей между ними и цели функционирования, следует, что кроме физической природы элементов на характеристики системы влияет и совокупность связей между элементами. Кроме того, изменение цели функционирования может вызвать коренное изменение набора элементов и межэлементных связей. Последние два свойства существенно меняют методологию исследования систем по отношению к методологии исследования отдельных элементов. Различают системы простые и сложные. Сложная система характеризуется большим числом элементов и большим числом связей. Элементы в сложной системе находятся в иерархическом взаимодействии.
Для описания систем используют информационные модели, где каждый элемент системы представлен в виде блока, имеющего входной и выходной сигналы.
Альтернативой системному подходу является физический подход, который характеризуется следующей последовательностью действий: выбор объекта исследования (построение физической модели), эксперимент, разработка математической зависимости. При физическом подходе для изучения реального объекта его разбивают на отдельные части. После исследования каждой из частей закономерности поведения объекта в целом реализуются путем обобщения результатов экспериментального исследования отдельных частей.
Скорей всего, физический подход эффективен при изучении простых систем, в частности, их вещественно-энергетических свойств. Однако он неприемлем при исследовании сложных систем, в которых определяющими являются не вещественно-энергетические, а структурно-поведенческие свойства. Если исследование простой
10
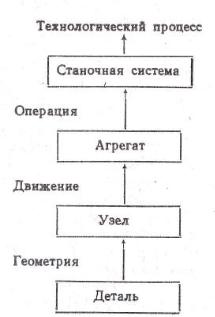
системы можно производить раздельным исследованием ее составных частей, то сложная система требует целостного рассмотрения на всех этапах исследования.
Системный подход включает следующие процедуры: представление объекта в виде системы; указание взаимосвязей (сильных и слабых) между подсистемами; математическое моделирование как подсистем, так и взаимосвязей (и если возможно ,то системы в целом); оценка качества системы и другие. Эти процедуры формируют методологию, коренным образом отличающуюся от методологии физических исследований. Прежде всего, это отказ от изучения целого по частям, переход к математическому моделированию из-за невозможности постановки физического эксперимента и введение для оценки качества системы понятия целевой функции. Теория систем знаменует новый этап развития науки, как науки о сложных системах, в противоположность методологии физических исследований, как теории простых систем.
Рассмотрение станка как объекта проектирования показывает, что он является сложной системой. Прежде всего процесс проектирования имеет дело с несуществующим объектом, т. е. с абстрактным образом несуществующей машины, на котором невозможно поставить физический эксперимент.
Современный станок, а тем боле, станочная система включает в себя гидравлические, электрические, электронные, механические узлы, содержащие десятки тысяч деталей. Эти узлы и отдельные детали находятся в сложной взаимосвязи под действием процессов малой, средней и большой скорости. Совокупность элементов и связей еще более расширяется при проектировании станочных систем, когда каждый станок, узел, деталь имеют несколько исполнений по каждому и десятка и более вариационных признаков. Автоматическая линия для обработки ступенчатых валов имеет сотни тысяч вариантов только компоновочных решений при наличии восьми вариационных признаков.
Обычный металлорежущий станок представляет собой сложную четырехуровневую иерархическую систему вида: станочная система, агрегат, узел, деталь (рис. 3). Станочная система является элементом старшего уровня, детали станка составляют элементы
младшего уровня. Основной характеристикой деталей является их геометрия, выходным параметром узла служит движение, агрегат характеризуется выполнением определенной операции, а станочная система обеспечивает реализацию некоторого технологического процесса.
Необходимо отметить, что деление станочной системы на четыре уровня является приближенным, и могут быть предусмотрены дополнительные подуровни. Так, например, подуровнем станочной системы является уровень станочного модуля. Затем узлы станка могут быть разбиты на другие подузлы (механизмы), которые в свою очередь включают функционально обособленные устройства следующего подуровня и т.д..
Рассмотрим представление станочного модуля, реализованного в виде робототехнического комплекса (РТК) как иерархической системы. Робототехнический комплекс (рис. 4) состоит из двух токарных станков с ЧПУ 1, промышленного робота 2 и загрузочно-разгрузочного устройства 3 (УЗР).
Рис 3. Иерархические уровни станочной системы
11