
2843.Разработка калийных месторождений практикум
..pdf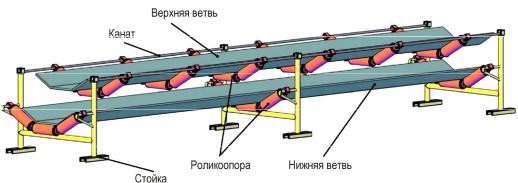
Рис. 2.18. Средняя часть конвейера с канатным ставом
Жесткий став представляет собой рамную конструкцию, на которой устанавливаются роликоопоры верхней и нижней ветви.
Канатный став состоит из двух параллельно натянутых канатов, на которые навешиваются роликоопоры верхней ветви. Сами канаты укладываются в скобы на стойках. Роликоопоры нижней ветви навешиваются на кронштейны, приваренные к стойкам.
Преимущества канатных ставов по сравнению с жесткими ставами заключаются в меньшей металлоемкости, способности выполаживать ленту на перегибах трасы с помощью телескопических стоек, возможности установки различного числа роликоопор на единицу длины конвейера.
Роликоопоры верхней ветви независимо от типа става состоят из трех роликов, боковые ролики наклонены под углом 30–35°, тем самым ленте придается форма желоба. Роликоопоры нижней ветви могут состоять из трех, двух или одного ролика. Грузонесущей является верхняя ветвь транспортерной ленты, нижняя ветвь ленты является холостой (порожней).
Еще одной и очень важной составляющей любого ленточного конвейера является конвейерная лента, выполняющая функции грузонесущего
итягового органа. На рудниках Верхнекамья применяются прорезиненные конвейерные ленты с тканевой основой. Тканевые прокладки толщиной 0,2–0,3 мм изготовляются из высокопрочных хлопчатобумажных тканей
исинтетических материалов (капрона, лавсана, вискозы), которые воспринимают тяговую нагрузку. Число прокладок в поперечном сечении одной ленты изменяется от 3 до 12. От механических воздействий и проникновения влаги прокладки предохраняются резиновыми обкладками толщиной с рабочей стороны от 3 до 10 мм и с нерабочей стороны – 2 мм.
61
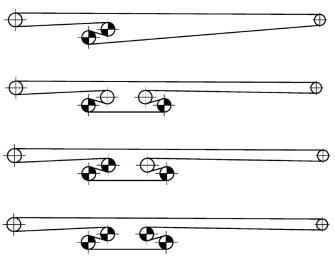
В табл. 2.6 приведены основные технические характеристики ленточных конвейеров.
На рис. 2.19 показаны схемы обводки барабанов ленточных конвейе-
ров.
|
|
|
|
|
|
|
Таблица 2.6 |
||
Основные технические характеристики ленточных конвейеров |
|||||||||
|
|
|
|
|
|
|
|
|
|
Показатели |
Ед. |
|
|
Тип конвейера |
|
|
|||
1Л80, |
Л1000КУ, |
|
|
|
|||||
изм. |
1Л120 |
2Л120В |
|||||||
|
1Л80У-02 |
КЛ-600 |
|||||||
|
|
|
|
|
|||||
Скорость движения |
м/с |
2,0 |
2,6 |
|
3,15 |
2,5 |
3,15 |
3,15 |
|
ленты |
|
||||||||
|
|
|
|
|
|
|
|
||
Ширина ленты |
мм |
800 |
1000 |
1200 |
1200 |
||||
Максимальная произ- |
т/ч |
420 |
650 |
|
800 |
1260 |
1590 |
1590 |
|
водительность |
|
||||||||
|
|
|
|
|
|
|
|
||
Приемная способность |
м3/мин |
8,2 |
16,8 |
|
20,3 |
24,8 |
31,2 |
31,2 |
|
Количество электро- |
шт. |
1 |
|
2 |
2–3 |
4 |
|||
двигателей |
|
||||||||
|
|
|
|
|
|
|
|
||
Суммарная мощность |
кВт |
55 |
150, 264 |
500, 630, |
1000 |
||||
привода |
|
|
|
|
|
750, 945 |
|
а
б
в
г
Рис. 2.19. Схемы обводки барабанов ленточных конвейеров: а – 1Л80, 1Л80У-02, Л1000КУ, КЛ-600;
б – 1Л120 с двумя приводными барабанами; в – 1Л120 с тремя приводными барабанами; г – 2Л120В
62
Конвейеры типа Л1000КУ, КЛ-600 с шириной ленты 1000 мм и канатным ставом применяются преимущественно в качестве участкового конвейерного транспорта. Кроме того, эти конвейеры используются в качестве проходческих комплексов подземного транспорта. Конвейеры Л1000КУ производятся на Александровском машиностроительном заводе, а КЛ-600 – Западно-Уральским машиностроительным концерном. Данные конвейеры не имеют принципиальных отличий друг от друга, основные технические характеристики этих конвейеров аналогичны.
Конвейеры типа 1Л120, 2Л120В с шириной ленты 1200 мм, жестким ставом применяются в схемах магистрального конвейерного транспорта. Конвейеры 1Л120 и 2Л120В выпускаются Александровским машиностроительным заводом.
Конвейеры типа 1Л80 и 1Л80У-02 производства Александровского машиностроительного завода применяются только в схемах проходческих комплексов подземного транспорта.
В качестве аппаратуры автоматизации конвейерных линий рудников принята система АСУК-ДЭП, выполненная на базе контроллеров ДЕКОНТ-Ех. Предусматривается дистанционное автоматизированное управление конвейерными линиями с пульта управления, находящегося в диспетчерской рудника.
Схема управления обеспечивает выполнение следующих операций:
−автоматический последовательный пуск конвейеров линии;
−пуск с пульта управления как всей, так и части конвейерной линии;
−пуск с места любого конвейера при осмотре, ремонте и опробовании;
−контроль времени пуска каждого конвейера;
−автоматическая остановка конвейера при аварийном режиме с отключением всех конвейеров, подающих груз на аварийный;
−остановка конвейерной линии с пульта управления и из любой точки конвейерной линии.
Схемой управления предусмотрены следующие виды защит и блокировок:
−отключение конвейера при разрыве рабочего органа;
−нулевая защита при исчезновении напряжения;
−отключение линии при коротком замыкании;
−невозможность пуска конвейера без предупредительного сигнала;
−отключение двигателя при пуске, если он не достиг номинальных оборотов в течение заданного времени;
63
−невозможность повторного автоматизированного пуска после аварийного отключения;
−блокировка конвейерной линии магистрального направления с конвейерными линиями ответвлений.
Кроме того, схема управления обеспечивает:
−предупредительный звуковой сигнал по линии при пуске и остановке конвейерной линии;
−прерывистую звуковую сигнализацию при аварийной остановке любого конвейера;
−световую сигнализацию у привода конвейера о состоянии конвейера;
−контроль «заштыбовки»;
−контроль времени пуска каждого конвейера;
−двустороннюю телефонную или громкоговорящую связь между пунктами разгрузки и загрузки линии, а также между пунктами установки приводов конвейеров и диспетчером рудника.
Новые и реконструируемые магистральные конвейерные линий оснащаются устройствами плавного пуска на основе тиристорных преобразователей частоты тока производства фирмы Bartec. Приводы магистральных ленточных конвейеров оснащаются коническо-цилиндрическими редукторами производства фирмы Flender.
Применение частотных преобразователей тока позволяет:
−выровнять моменты приводных двигателей конвейера;
−устранить избыточные моменты в двигателе;
−минимизировать динамические загрузки во всем приводном устройстве машины, а также во время начала движения и самого движения;
−уменьшить количество выделяемого приводом тепла;
−обнаружить причины аварии привода;
−предохранить электрические двигатели приводов от возможных перегрузок и повреждений.
Применение коническо-цилиндрических редукторов позволяет уменьшить габариты приводной станции конвейера, что в подземных условиях, связанных со стесненностью, является большим преимуществом.
Вследствие установки данного оборудования на конвейеры уменьшаются эксплуатационные затраты, увеличивается срок службы конвейерной ленты и приводных блоков.
Скребковый конвейер состоит из приводной станции, концевой головки, линейных рештаков, тяговой цепи со скребками, переходной сек-
64
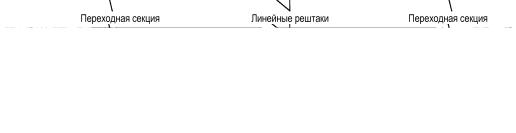
ции. Внешний вид скребкового конвейера типа СП301М показан на рис. 2.20.
Принцип действия скребковых конвейеров основан на перемещении руды волочением по неподвижному грузонесущему органу (рештачный став) с помощью тяговых цепей, приводимых в движение от приводной станции. Загрузку конвейера можно производить в любой точке по всей длине.
Рис. 2.20. Скребковый конвейер СП301М
Скребковые конвейеры применяются для транспортирования карналлитовой руды на руднике СКРУ-1.
Технические характеристики конвейера СП301М:
–производительность 800 т/ч;
–скорость движения тягового органа 1 м/с;
–напряжение питания электродвигателей 1140/660 В;
–энерговооруженность 2×110 кВт;
–тяговый орган две цепи;
–калибр цепи 24×86-(C или D)-13×2;
–расстояние между осями цепей 600 мм.
Электровозный транспорт применяется для доставки карналлитовой руды на руднике СКРУ-1 в рудничных вагонетках с глухим кузовом УВГ-4,5А.
Перемещение вагонеток по горным выработкам осуществляется с помощью рудничного контактного электровоза К14М. Питание электровоза осуществляется по внешней электросети через тяговые подстанции и контактную сеть.
Электровозным транспортом карналлитовая руда доставляется от погрузочного комплекса до опрокидывателя ствола № 1. По главным отка-
65
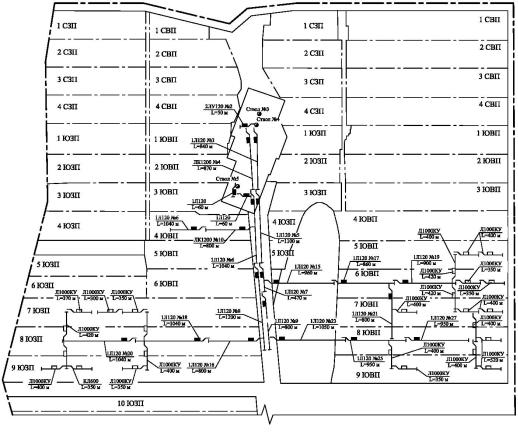
точным выработкам и на вспомогательных путях проложены пути из рельс Р-33 с шириной колеи 750 мм.
В качестве примера на рис. 2.21 и 2.22 представлены схемы конвейерного транспорта рудников СКРУ-2 и СКРУ-3 соответственно.
Условные обозначения: Магистральные конвейеры
Участковые конвейеры
Рис. 2.21. Схема конвейерного транспорта рудника СКРУ-2
Транспортирование сильвинитовой руды от очистных камер до общешахтных бункеров стволов № 4 и № 5 рудника СКРУ-2 осуществляется с помощью ленточных конвейеров с шириной ленты 1000 и 1200 мм.
Из очистных камер пластов Вс, АБ и Красный-II руда самоходными вагонами 5ВС-15М, ВС-30 либо В-15К доставляется до рудоспускных
66
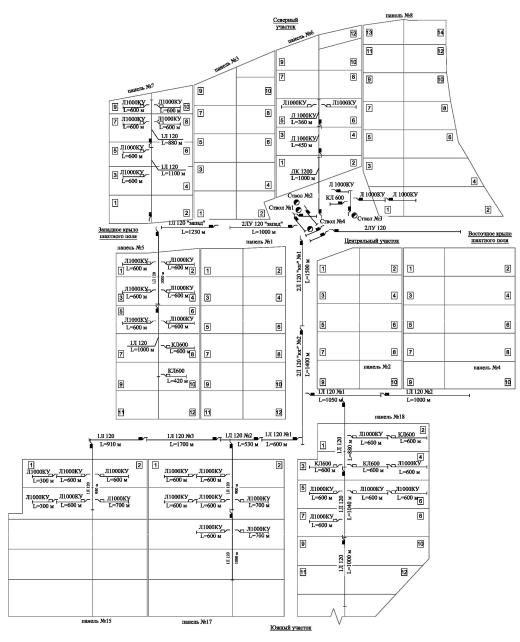
Условные обозначения: Магистральные конвейеры
Участковые конвейеры
Рис. 2.22. Схема конвейерного транспорта рудника СКРУ-3
67
скважин, служащих для перепуска руды на конвейеры типа Л1000КУ или КЛ600, установленных в панельных конвейерных штреках. Далее сильвинитовая руда перегружается на блоковые (межпанельные) конвейеры Л1000КУ, с которых перегружается на конвейеры 1Л-120, установленные в панельных групповых конвейерных штреках. Затем сильвинитовая руда транспортируется до главных южных конвейерных штреков № 1 и № 2. Далее сильвинитовая руда конвейерным транспортом главных южных конвейерных штреков № 1, № 2 доставляется до общешахтных бункеров стволов № 4 и № 5. Панельные, блоковые и групповые конвейерные штреки пройдены в подстилающей каменной соли.
Для транспортирования сильвинитовой руды к стволу № 5 с конвейеров № 5 и № 6 главных южных конвейерных штреков № 1, № 2 через распределительные устройства осуществляется разгрузка на два передаточных конвейера 1Л-120, а также на магистральные конвейеры № 3 и № 4. Передаточными конвейерами сильвинитовая руда транспортируется до общешахтного бункера ствола № 5.
Транспортировка руды на горных участках СКРУ-3 осуществляется конвейерами типа Л1000КУ, КЛ600. Блоковым конвейером руда транспортируется до блокового бункера-накопителя либо до рудоспускной скважины, затем через разгрузочное устройство из бункера или рудоспускной скважины поступает на панельные конвейеры. Панельными конвейерами руда доставляется до панельных бункеров. В качестве панельных конвейеров на горных участках используются конвейеры типа 1Л120.
Из панельных бункеров-накопителей через разгрузочные устройства руда перегружается на магистральные конвейеры. В качестве главного магистрального конвейерного транспорта в руднике применяются конвейеры типа 2ЛУ120, 2Л120, 1Л120.
Руда, транспортируемая с любого участка шахтного поля, может быть разгружена в восточный или западный общешахтный бункер ствола № 1.
Транспортирование сильвинитовой руды от добычных участков до общешахтных бункеров ствола № 2-бис рудника СКРУ-1 осуществляется конвейерным транспортом.
В панели сильвинитовая руда из очистных камер самоходными вагонами доставляется до рудоспусков в выемочных штреках. По рудоспускам руда перегружается на ленточные конвейеры КЛ-600 или Л1000КУ, установленные в панельном конвейерном штреке. Панельные ленточные конвейеры доставляют руду до магистральных конвейеров главного направле-
68
ния, которыми руда транспортируется до приемных бункеров ствола № 2-бис. В качестве магистральных конвейеров на руднике используются конвейеры типа 1Л120, ЛК-1200, 1ЛУ120, 1ЛБ1200, Л1000КУ.
Вспомогательный транспорт служит для доставки людей, оборудования и материалов от ствола до рабочего места или склада.
Для доставки людей на горные участки используются автомашины «Минка-26», «Курьер», «Крот», УАЗ.
Для доставки материалов и оборудования на горные участки применяются тракторы «Крот» (маслозаправщик), Т-16, ТДТ-55, МТЗ-82, ПД-5, ПД-8В, 1ВОМА.
На руднике СКРУ-1 доставка грузов на горные участки и службы, где проложены рельсовые пути, осуществляется электровозным транспортом. В эксплуатации находятся электровозы К-14М. Оборудование и материалы доставляются в рудничных вагонетках ВГ-1,2, ВШ-143 и на специальных платформах до участковых разгрузочных площадок.
Впределах панелей, блоков оборудование и материалы доставляются
кместу производства работ тракторами, малогабаритные грузы доставляются машиной «Минка-26» и шахтным автобусом «Крот».
Все машины с ДВС оборудованы установками пожаротушения типа «Пион».
2.8. Проветривание калийных рудников
Схемы проветривания рудников. На Верхнекамском месторождении применяются две схемы проветривания – центральная и фланговая. Центральная схема характеризуется тем, что воздухоподающие и вентиляционные стволы находятся на одной промплощадке и чаще всего расположены в центре шахтного поля. Данная схема применена на рудниках СКРУ-2, СКРУ-3, БКПРУ-2 и БКПРУ-4.
Фланговая схема характеризуется тем, что воздухоподающие и вентиляционные стволы отнесены друг от друга. Чаще всего воздухоподающие стволы находятся в центральной части, вентиляционные – отнесены к границам шахтного поля (рудники СКРУ-1 и бывший БКПРУ-1).
Пример центральной схемы проветривания показан на рис. 2.23, а. В данной схеме два воздухоподающих ствола и один вентиляционный, на котором установлена главная вентиляторная установка. Стволы расположены в центре шахтного поля. Главные подготовительные выработки
69
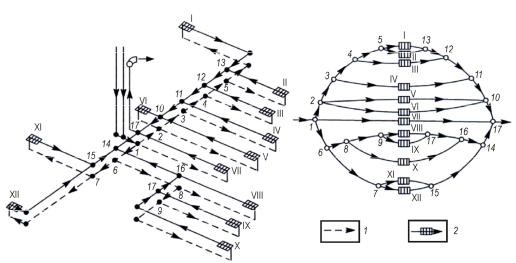
(транспортные и вентиляционные) ориентированы в меридиональном направлении, т.е. на север и на юг, образуя северное и южное крылья рудника.
В другом случае главные подготовительные выработки могут ориентироваться в широтном направлении, т.е. на запад или восток, образуя западное и восточное крылья. Такую схему подготовки имеют рудники СКРУ-2 и СКРУ-3.
Характерной особенностью центральной схемы проветривания является то, что все основные выработки образуют параллельное соединение (рис. 2.23, б), которое является наиболее надежным по регулированию и устойчивым по распределению воздушных потоков.
а |
б |
Рис. 2.23. Центральная |
схема проветривания рудника: а – принципиальная; |
б – упрощенная; 1 – полевые штреки; 2 – пластовые штреки и районы ведения очистных работ
Несколько своеобразной является схема проветривания рудника СКРУ-1 (рис. 2.24). Воздух подается в рудник по двум стволам, находящимся в центральной части шахтного поля, и удаляется по стволу № 2-бис, отнесенному в сторону восточной границы шахтного поля. Чтобы избежать диагонального соединения выработок, в меридиональном направлении от ствола № 2-бис были пройдены главные транспортные и вентиляционные выработки, в которых направленность основных воздушных потоков принята противоположной. Однако проходка в западной части
70