
2843.Разработка калийных месторождений практикум
..pdf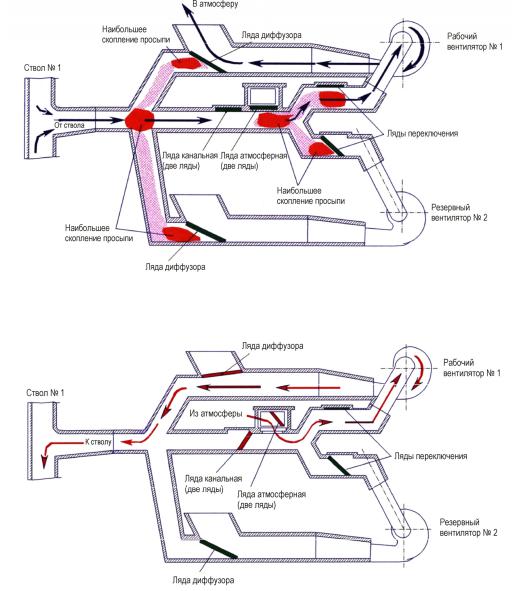
ляционных каналов образуются наросты, что увеличивает аэродинамическое сопротивление вентиляционных каналов и диффузора. Это приводит к увеличению потребляемой мощности на проветривание рудника.
На рис. 2.11 и 2.12 приведены схемы расположения и работы вентиляторной установки ВРЦД-4,5С1 на скиповом стволе при разных режимах.
Рис. 2.11. Схема работы вентиляторной установки с вентиляторами ВРЦД-4,5С1 на всасывание (СКРУ-3)
Рис. 2.12. Схема работы вентиляторной установки с вентиляторами ВРЦД-4,5С1 на нагнетание (СКРУ-3)
51
Налипание пыли на вращающиеся элементы вентиляторов приводит
кповышению вибрации и, как следствие, более частому переключению
срабочего вентилятора на резервный.
2.5. Системы разработки, применяемые при освоении ВКМКС
Промышленными пластами на Верхнекамском месторождении калий- но-магниевых солей являются сильвинитовые АБ и Красный-II и карналлитовый пласт В, представленный на отдельных участках месторождения сильвинитом. Число отрабатываемых пластов определяется условиями залегания пород, необходимостью охраны поверхностных зданий и сооружений от влияния горных работ и мощностью водозащитной толщи (ВЗТ).
На Верхнекамских рудниках получила применение камерная система разработки с оставлением междукамерных целиков. Данная система разработки имеет следующие варианты:
–с оставлением податливых целиков;
–с оставлением «жестких» целиков.
Главным образом на рудниках применяется система разработки с оставлением «жестких» междукамерных целиков, что обусловлено горногеологическими и горнотехническими условиями, а также свойствами пород северной части месторождения. Система с оставлением «жестких» целиков имеет более высокие потери и применяется там, где недостаточна мощность ВЗТ, и при отработке участков месторождений, расположенных вдоль тектонических нарушений. Исключение составляет отработка сильвинитовых пластов на шахтном поле БКПРУ-2, где поддержание кровли осуществляется на податливых целиках.
Основные принципиальные схемы камерной системы разработки сильвинитовых пластов Верхнекамского месторождения приведены на рис. 2.13, 2.14.
Камерная система разработки характеризуется множеством различных параметров, зависящих от горно-геологических и горнотехнических условий залегания пластов, а также от типа транспортных средств, обеспечивающих доставку руды от забоя до выемочного штрека и способствующих его эффективному использованию.
Основными параметрами технологии очистной выемки являются ширина и высота очистной камеры, размеры междукамерного и междуходового целика и длина камеры.
52
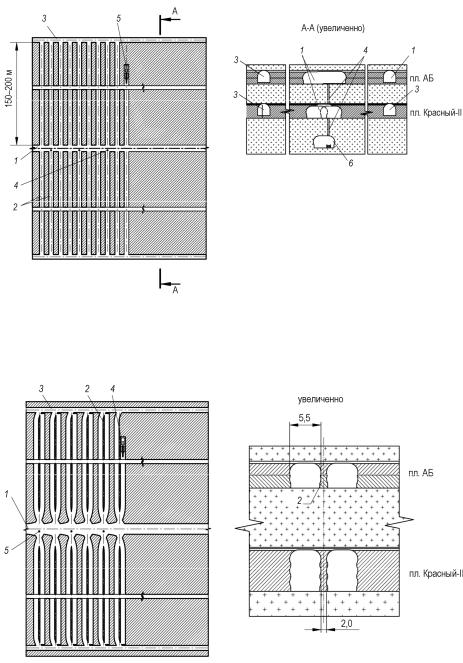
Рис. 2.13. Схема ведения добычных работ на руднике СКРУ-3: 1 – выемочный штрек; 2 – очистная камера; 3 – вентиляционный штрек; 4 – рудоспускная скважина; 5 – комбайновый комплекс; 6 – блоковый конвейерный штрек
а |
б |
Рис. 2.14. Схема ведения очистных работ с оставлением в камере межходового целика на руднике СКРУ-1: а – схема ведения работ в плане, б – сечение очистной камеры; 1 – выемочный штрек, 2 – междуходовой целик, 3 – вентиляционный штрек, 4 – комбайн, 5 – рудоспускная скважина
53
Ширину камеры главным образом определяет устойчивость вмещающих пород, а при комбайновой выемке – и размеры исполнительного органа комбайна. Ширина камеры может быть образована несколькими ходами комбайна. Поддержание кровли камер и подготовительных выработок осуществляется анкерной крепью. Высота камер определяется вынимаемой мощностью пластов. Исключение составляет высота камер по пласту В карналлитового состава, принимаемая в зависимости от мощности ВЗТ, но не более 10 м.
Ширина междукамерного целика зависит от параметров камеры состава и свойств вмещающих пород, глубины разработки, мощности водозащитной толщи. Ширина междукамерных целиков на отрабатываемых площадях Верхнекамского месторождения в силу широкого диапазона горно-геологических и горнотехнических условий изменяется от 3,0 до 18,0 м и в каждом конкретном случае определяется расчетом.
Отработка карналлитового пласта В ведется на СКРУ-1 камерами в четыре хода комбайна «Урал-20Р» по высоте и в три хода по ширине, при этом ширина камеры оставляет 9,0 м, ширина междукамерного целика
18,0 м.
Длина камеры является наиболее постоянным параметром, который обоснован эффективным использованием применяемых транспортнодоставочных средств от забоя. На рудниках ОАО «Уралкалий» длина камеры составляет 150–300 м.
При расчете параметров системы разработки необходимо соблюдать требования, предъявляемые к условиям отработки шахтного поля рудника. Согласно «Указаниям по защите рудников от затопления…» должны быть обеспечены следующие условия:
– безопасность ведения горных работ и защита рудника от затопле-
ния;
–оптимальная полнота извлечения полезного ископаемого из недр
итехнико-экономическая эффективность параметров системы разработки;
–охрана подрабатываемых инженерных и природных объектов на земной поверхности;
–соблюдение соосности камер при отработке сближенных пластов
сопережающей отработкой верхнего пласта не менее чем на 50 м;
–исключение массового обрушения пород в очистных камерах;
–безопасное выполнение закладочных работ в заданные сроки.
54
Выработанное пространство сильвинитовых пластов, а также пласта В карналлитового состава закладывается отходами от обогащения и породой от проходки подготовительных выработок. Необходимость закладки выработанного пространства рудника обусловлена следующими факторами:
−обеспечение охраны окружающей среды;
−уменьшение величины оседания земной поверхности и повышение степени надежности водозащитной толщи.
Осуществление закладки выработанного пространства отходами обогащения является в первую очередь целевым природоохранным мероприятием, которое позволяет сократить объем складирования отходов на поверхности и, следовательно, уменьшить опасность загрязнения окружающей среды.
Применение гидравлической закладки выработанного пространства отходами сильвинитовой обогатительной фабрики, получаемыми в резуль-
тате переработки сильвинитовой руды на руднике СКРУ-3, позволило в 2009 г. разместить 1,85 млн т солевых отходов, в том числе 40 тыс. т шламов.
2.6. Технология и механизация очистных работ
На рудниках Верхнекамского месторождения калийно-магниевых солей отработку сильвинитовых пластов АБ, Красный-II и карналлитового Вк, представленного на некоторых участках сильвинитом Вс, осуществляют комбайновым способом с применением камерной системы разработки.
Весь объем добычи сильвинитовой и карналлитовой руды осуществляют с использованием проходческо-очистных комбайновых комплексов.
Комбайновую технологию характеризует простота производственного цикла. Комбайны обеспечивают отделение руды от массива и осуществляют погрузку ее в транспортные средства.
На очистных и горно-подготовительных работах по пластам АБ, Красный-II и Вс применяют проходческо-очистные комбайны типа «Урал10А(Р)», «Урал-61», ПК-8, «Урал-20Р(А)», «Мариэтта MF-320» в комплек-
се с самоходными вагонами 5ВС-15М, В-15К, ВС-30 и бункер-перегружа- телями БП-14, БП-15, БПС-25, БПС-22.
Для приема руды от комбайнов, временного ее накопления и перегрузки в самоходные вагоны применяют бункер-перегружатели БП-14, БП-15, БПС-25, БПС-22. Применение бункер-перегружателей позволяет
55

значительно сократить время простоев комбайнов в ожидании вагонов
впериод доставки руды и сократить время простоев самоходных вагонов
впериод их загрузки, что повышает производительность комбайновых комплексов.
Доставка руды от комбайнов до участковых конвейеров осуществляется самоходными вагонами на пневмошинном ходу с электрическим приводом типа 5ВС-15М, В-15К, ВС-30. Подача руды на конвейер производится через рудоспускные скважины, пробуренные между выемочным и конвейерным штреками.
При ведении горно-подготовительных работ разгрузка самоходного вагона производится непосредственно на конвейер с использованием разгрузочной платформы (рис. 2.15).
Рис. 2.15. Разгрузка самоходного вагона на конвейер с использованием разгрузочной платформы
Приемные воронки скважин располагают на выемочном штреке. Расстояние между скважинами выбирают исходя из условия, что пробег самоходного вагона по выемочному штреку не должен превышать 20–30 м, а расстояние между скважинами 50–60 м. Диаметр рудоспускной скважины составляет 500 мм. Приемная часть скважины (рис. 2.16), на которую укладывают металлическую решетку с ячейкой 220(250)×220(250) мм2, выполнена с расширением.
В процессе ведения работ имеют место случаи зависания руды в скважинах. Зависание руды является серьезной проблемой, поскольку нарушает течение технологического процесса и представляет опасность для рабочих, занятых на их чистке. В этой связи представляет интерес применение дробилок-питателей, например типа 7MFBH-48A, для приема руды из самоходного вагона и дозированной подачи ее в скважину, что позволит избежать «заштыбовывания» скважин негабаритными кусками руды.
56
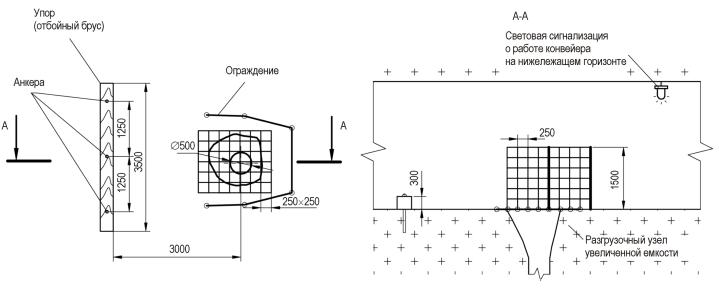
57
Рис. 2.16. Устройство приемного узла рудоспускной скважины
Выпускную часть скважины оборудуют коническим устройством, которое в случае большого потока руды, поступающей на конвейер, может быть заужено для уменьшения потока поступления руды на конвейер. При помощи таких мероприятий уменьшается вероятность перезаполнения
идаже заваливания конвейера рудой.
Вслучае применения нескольких комбайновых комплексов на одном выемочном блоке регулировку осуществляют зауживанием выпускного отверстия на скважине, причем самый дальний комплекс, работающий на блоке, разгружается в скважину с бóльшим выпускным отверстием. Если очистные работы ведут по двум пластам и более, то при разгрузке с верхнего пласта перепуск руды через нижерасположенные выработки осуществляют при помощи перепускных труб.
Вкачестве средства борьбы с запыленностью воздуха в месте разгрузки самоходного вагона используют «ширмы», изготавливаемые из конвейерной ленты. Неэксплуатируемые рудоспускные скважины герметично перекрываются для снижения внутрирудничных утечек.
На СКРУ-1 отработку пласта В карналлитового состава производят комбайнами «Урал-10А», «Урал-20А» и «Урал-400С». Для транспортировки руды по выемочным штрекам используют скребковые конвейеры типа СП-301. Дальнейшую транспортировку руды до погрузочных пунктов осуществляют ленточными конвейерами.
Погрузку карналлитовой руды в рудничные вагонетки производят с помощью механизированного погрузочного пункта ППК-4. Для перестановки составов в процессе погрузки используют маневровые лебедки ЛШВ-01, ЛВД-22. Откатку карналлитовой руды производят в вагонетках УВГ-4 (УВГ-4,5), транспортировку составов к стволам, подвозку материалов и оборудования производят электровозами типа 14Кр-2, Кр-14.
Для проходки вертикальных выработок используют сбоечно-буровые машины БГА-2М, БСК-2РП, СБУ-250.
Для механизации такелажных работ на рудниках используют:
–ручные тали, тельферы, кран-балки, лебедки грузоподъемные ЛУРВ-10, ЛГ-15;
–подъемно-погрузочные лебедки ЛМГ-5, ЛГРУ-10, которые используют при погрузке и разгрузке различных материалов и оборудования из вагонеток, транспортных платформ, монтажа и демонтажа горно-шахтного оборудования и механизмов;
58
–трелевочные тракторы ТДТ-55, колесные тракторы МТЗ-80,82, ВОМА, Т-16М – для перевозки грузов в пределах горных участков и главных транспортных выработок;
–для пожаротушения применяют МТ-403 и Т39224 на базе автомобиля «Крот»;
–для осушения транспортных штреков, квершлагов, камер служебного назначения и нарезки рассолоотводных канавок на участках гидрозакладки используют машину для нарезки компенсационных щелей «Урал-50».
Проветривание очистных камер осуществляют при помощи вентиляторов местного проветривания СВМ-6 или ВМЭ-6У.
Горно-подготовительные и очистные выработки крепят анкерами. Обязательному креплению, преимущественно винтовыми анкерами, подлежат сопряжения очистных камер с подготовительными выработками, панельные выемочные и вентиляционные штреки.
2.7. Рудничный транспорт
Совокупность транспортных машин и комплексов, расположенных в горных выработках, образует комплексную систему подземного транспорта.
Взависимости от места расположения различают участковые и магистральные транспортные комплексы. Участковым транспортом осуществляется доставка руды от забоя до магистральных выработок. Магистральным транспортом осуществляется доставка руды по выработкам главных направлений до общешахтных бункеров. Магистральный транспорт имеет, как правило, несколько точек загрузки.
Взависимости от назначения комплексы подземного транспорта рудника разделяют на основные, предназначенные для полезного ископаемого; вспомогательные – для оборудования, материалов и для перемещения людей; проходческие – для перемещения полезного ископаемого, пустой породы или горной массы от подготовительных забоев до пункта перегрузки на основные или вспомогательные средства транспорта.
Вкачестве основного транспорта в рудниках ОАО «Уралкалий» используется конвейерный и электровозный транспорт, в качестве вспомогательного – автотракторная техника и электровозный транспорт.
Конвейерный транспорт. Транспортирование руды от очистных камер до общешахтных бункеров осуществляется с помощью конвейерных линий. Этот вид транспорта является основным и единственным для
59
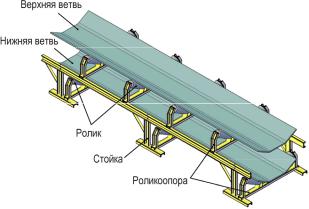
транспортирования сильвинитовой руды на Верхнекамском месторождении калийных солей. Транспортирование карналлитовой руды осуществляется с применением скребковых и ленточных конвейеров, а также в вагонетках с помощью электровозного транспорта.
Конвейерный транспорт играет особую роль на калийных рудниках, так как ни один из других видов транспорта на сегодняшний день не может обеспечить непрерывность и высокую, постоянную производительность доставки руды независимо от длины транспортирования. Конвейерный транспорт не требует больших затрат при эксплуатации, достаточно прост в обслуживании.
На Верхнекамском месторождении калийных солей применяются два вида конвейеров: ленточные и скребковые.
Ленточный конвейер представляет собой конструкцию, состоящую из опорных стоек, приводной и натяжной станций, загрузочного устройства, промежуточных опорных роликов и кольцевой бесконечной ленты, по которой непосредственно перемещаются грузы. Кроме того, на ленточном конвейере устанавливаются устройства для очистки ленты, центрирующие ход ленты роликоопоры.
Передача движения ленте осуществляется фрикционным способом от приводных барабанов. Необходимое натяжение ленты создается натяжным барабаном при помощи натяжного устройства. Загрузка конвейера осуществляется через загрузочное устройство, которое формирует поток руды на ленте.
На рис. 2.17 и 2.18 показаны средние части конвейеров с жестким и канатным ставом соответственно.
Рис. 2.17. Средняя часть конвейера с жестким ставом
60