
- •ПРЕДИСЛОВИЕ
- •ВВЕДЕНИЕ
- •1. КЛАССИФИКАЦИЯ И ОСНОВНЫЕ ЭЛЕМЕНТЫ НАГРЕВАТЕЛЬНЫХ УСТРОЙСТВ
- •4. ПЕЧИ-ВАННЫ
- •5. НАГРЕВАТЕЛЬНЫЕ УСТАНОВКИ
- •5.9.1. Расчет непосредственного электронагрева
- •5.9.2. Расчет индукционного нагрева
- •6. ОБОРУДОВАНИЕ ДЛЯ ОХЛАЖДЕНИЯ
- •8.1.2. Удаление окисляющих газов из контролируемых атмосфер
- •8.1.4. Управление составом атмосферы
- •8.3.1. Травление окалины
- •8.3.4. Гидропескоочистка
- •9. ЦЕХОВЫЙ КОНТРОЛЬ
- •КАЧЕСТВА ТЕРМООБРАБОТКИ
- •10. УСТРОЙСТВО КОММУНИКАЦИЙ ТЕРМИЧЕСКОГО ЦЕХА
- •12. ЭКСПЛУАТАЦИЯ ОБОРУДОВАНИЯ ТЕРМИЧЕСКИХ ЦЕХОВ
- •ОГЛАВЛЕНИЕ
Та б л и ц а 5.10. Время нагрева т. в. ч. шеек коленчатого вала автомобиля
|
большая коренная |
Шейка |
шатунная |
хвосто вика |
Параметр |
малая коренная |
|||
|
|
|
|
Диаметр шейки, см |
5,5 |
5,5 |
5,0 |
5,5 |
|
Ширина |
закален |
7,0 |
3,2 |
|
|
ного слоя, см |
3,8 |
4,0 |
|||
Глубина |
закален |
4 |
4 |
|
|
ного слоя, мм |
4 |
4 |
|||
Время нагрева, с |
5,5 |
2,5 |
2,7 |
3,0 |
При непрерывно-последовательном нагреве и высоте индуктора /ЦНд20 мм =2 см необходимо обеспечить такую скорость его движения:
20 : 7,4=2,7 мм/с.
Пример 3. Определить мощность установки ддя сквозного индукционного нагрева заготов
ки, имеющей d = 70 мм, |
/= 200 мм, массу 6 кг, |
до температуры 1200 °С |
при производительнос |
ти 700 кг/ч. Наиболее подходящая частота рав
на 2500 |
Гц, минимальное время нагрева т = |
= 120 с |
(рис. 5.31), поэтому индуктор необхо |
димо рассчитать на одновременную садку: |
|
|
700-120 |
|
заготовкам. |
|
6-3600 |
При |
толщине футеровки 20 мм и зазоре |
5 мм диаметр индуктора с/ИнД= ^ + 2 5 - 2 = 7 0 + + 25 -2= 120 мм. Длина катушки индуктора бе
рется больше длины нагреваемых деталей на величину диаметра индуктора /ипд=4/+аинд— = 4-200+ 120= 920 мм.
Тепло, необходимое для нагрева заготовок,
Q M = Get (^м. к |
to) |
= 6*4 X |
х 0,70(1200 — 20) = |
19824 кДж. |
|
Принимая термический |
к. п. д. индуктора 0,8, |
потребное количество тепла с учетом тепловых потерь
QT = |
<2м: Т1т = |
19 824:0,8 = |
|
= 24 780 кДж. |
|
Потери тепла |
через футеровку точнее можно |
|
подсчитать по формуле (5.12). |
||
При времени нагрева |
120 с и электрическом |
к. п. д. “Пэл=0,8 получим мощность, подводимую к индуктору,
QT |
24780 |
А /и н д ---- |
= 260 кВт. |
т<Пэл |
120- 0,8 |
При необходимости уменьшить мощность уста новки следует увеличить время нагрева.
Пример 4. Определить время нагрева гиль зы внутренним диаметром 160 мм, высотой 400 мм, массой 12 кг т. п. ч. (50 Гц) до темпе
ратуры |
1000 °С в установке с железным сердеч |
|||
ником |
мощностью 35 кВт. |
|
||
Мощность установки на индукторе |
||||
|
А/ИНД = |
G e t (/м . к — to) |
||
|
Т П тП э л |
|||
откуда |
|
|||
Get (/м . к — to) |
Г2 -0,68 (1000— 20) |
|||
|
||||
х ------------------- |
~~= |
35-0,7-0,8 |
||
|
А/индТ] гЛэл |
|||
|
= 4110 с = |
7 мин. |
6.ОБОРУДОВАНИЕ ДЛЯ ОХЛАЖДЕНИЯ
Оборудование для охлаждения, как и нагревательные устройства, относит ся к основному оборудованию, так как оно необходимо для непосредственного выполнения операций термообработки (закалки, сорбитизации).
Простейшими устройствами для ох лаждения деталей являются закалочные баки, которые по условиям" работы ‘тэжтпГ'разделить на баки периодичес кого и непрерывного действия. Для уменьшения коробления деталей при закалке применяют закалочные прес сы, закалочные и гибочно-закалочные машины, в которых детали охлаждают ся в зажатом состоянии. Последнее позволяет обеспечивать равномерное охлаждение. Закалочные жидкости охлаждают в маслоохладительных ус тановках. При необходимости глубоко го охлаждения деталей (до — 30 °С и ниже) применяют установки для обра
ботки холодом. |
v |
Оборудование для охлаждения по |
|
ка не стандартизовано, однако |
можно |
предложить следующую его индекса цию, которая состоит из ряда букв м цифр.
В индексе баков первая буква Б означает бак, вторая буква О — охладительный, третья буква указывает Способ механизации: К — кон вейерный; П — с подъемным столом; С — со
скиповым подъемником; Т — с поворотной траверсбй; Ч — с качающимся столом; Б — бара банный; Ш — с передвижением деталей толка телем и подъемниками. За буквами через де_ фис следуют цифры, указывающие основные размеры транспортного механизма (ленты кон вейера, подъемного, поворотного или качаклце_ гося стола, барабана и т. п. в дециметрах). Иц.
деке |
бака |
БОП-6.7. читается так: |
бак |
охлади. |
|
тельный |
с подъемным |
столом |
размерами |
||
6X 7 |
дм; |
индекс БСЖ-6 200 |
обозначает |
следу^. |
щее: бак охладительный с конвейером шириной 6 дм и рабочей длиной (горизонтальный учкс. ток ленты конвейера) 200 дм.
В индексе немеханизированных баков третья цифра указывает тип бака: Г — гори зонтальный прямоугольного сечения; В — вев1 тикальный круглого сечения. После третьей буквы через дефис даются внутренние размерЬ1 бака в дециметрах. Например, индекс БОВ-16.50 читается так: бак охладительный вертикальный, диаметром 16 дм, высотой
50 дм.
В индексе закалочных прессов и машин пер |
Большое |
значение |
имеет |
способ |
||||||||||||||||||
вая буква указывает тип охладительной маши |
подвода в бак холодной жидкости и от |
|||||||||||||||||||||
ны: |
П — пресс, |
М — машина. |
Вторая |
буква |
||||||||||||||||||
соответствует способу охлаждения: Ш — охла |
вода |
нагретой. |
Холодную |
|
жидкость |
|||||||||||||||||
ждение в штампах; Р — охлаждение в роликах. |
следует подводить снизу бака, а нагре |
|||||||||||||||||||||
Третья буква показывает назначение пресса |
тую отводить сверху (в соответствии с |
|||||||||||||||||||||
(машины): |
3 — закалочный; |
Г — гибочно-за |
ее естественным движением). Если хо |
|||||||||||||||||||
калочный. Четвертая |
буква — способ механи |
|||||||||||||||||||||
лодная жидкость поступает сверху, она |
||||||||||||||||||||||
зации: |
К — карусельный, |
Б — барабанный, |
||||||||||||||||||||
А — агрегатный. Цифры, стоящие |
через |
дефис |
сразу стремится на дно бака и |
обра |
||||||||||||||||||
после букв, указывают |
предельный |
диаметр |
зует около деталей относительные хо |
|||||||||||||||||||
или |
длину |
изделия |
(для |
листов — ширину) |
в |
лодные струи, |
что вызывает |
неравно |
||||||||||||||
дециметрах. Индекс ПШЗ-60 читается так: за |
||||||||||||||||||||||
калочный пресс, охлаждение изделий в штам |
мерность охлаждения |
и |
коробление |
|||||||||||||||||||
пах, максимальный диаметр детали 60 дм; ин |
деталей. Нагретая жидкость отводится |
|||||||||||||||||||||
декс MP3-160 означает следующее: закалочная |
сверху по всему периметру бака. Ввер |
|||||||||||||||||||||
машина |
с |
охлаждением |
изделий |
в |
роликах; |
ху бака устанавливают |
сливной |
кар |
||||||||||||||
максимальная длина |
изделия |
равна |
160 |
дм. |
||||||||||||||||||
ман, |
из которого |
жидкость |
по |
трубе |
||||||||||||||||||
|
|
|
|
|
|
|
|
|
|
|
|
|||||||||||
|
|
|
6.1. |
|
КОНСТРУКЦИИ |
|
|
течет в сливной бак. В карман |
посту |
|||||||||||||
|
|
|
ЗАКАЛОЧНЫХ БАКОВ |
|
|
|
пает также жидкость, вытесняемая по |
|||||||||||||||
|
|
И МАСЛООХЛАДИТЕЛЬНЫХ |
|
|
груженной в бак деталью. Для удале |
|||||||||||||||||
|
|
|
|
УСТАНОВОК |
|
|
|
|
|
ния скапливающейся в баке |
окалины |
|||||||||||
|
|
|
|
|
|
|
|
|
|
|
|
и извлечения закаленных деталей его |
||||||||||
|
З а к а л о ч н ы е б а к и п е р и о д и |
снабжают подъемным дном или корзи |
||||||||||||||||||||
ч е с к о г о д е й с т в и я устанавливают |
ной. В небольших по объему баках |
|||||||||||||||||||||
у камерных печей, они свариваются из |
спускное дно |
|
поднимается |
|
лебедкой. |
|||||||||||||||||
листовой стали. Толщина стенок малых |
При закалке крупных деталей оно мо |
|||||||||||||||||||||
баков 3—5 мм, а больших 8—12 мм. |
жет |
служить |
амортизатором, |
предо |
||||||||||||||||||
Стенки |
|
бака |
усиливаются |
ребрами |
храняющим |
бак от повреждения |
сор |
|||||||||||||||
из уголков. Приток холодной воды из |
вавшимися деталями. |
с |
закалочной |
|||||||||||||||||||
водопровода и удаление нагретой поз |
Конструкция |
бака |
||||||||||||||||||||
воляют |
|
поддерживать |
необходимую |
жидкостью, |
охлаждаемой |
|
вне |
бака, |
||||||||||||||
температуру водяной |
ванны. При |
ис/ |
представлена на рис. 6. 1, а. Холодная |
|||||||||||||||||||
пользовании |
в |
качестве |
закалочной |
жидкость подводится снизу к центру |
||||||||||||||||||
жидкости масла приходится прибегать |
бака, а при большом его диаметре |
|||||||||||||||||||||
к его искусственному охлаждению, ко |
жидкость поступает по змеевику с от |
|||||||||||||||||||||
торое |
может быть |
местным |
и цент |
верстиями. Чтобы окалина не |
засоря |
|||||||||||||||||
ральным. В первом случае |
масло |
ох |
ла отверстия, их делают сбоку змееви |
|||||||||||||||||||
лаждается в баке при помощи змееви |
ка, а центральную подводящую трубу |
|||||||||||||||||||||
ка с циркулирующей |
в нем холодной |
закрывают колпачком. Масляные баки |
||||||||||||||||||||
водой, во втором — вне |
бака |
в |
цент |
на случай пожара должны иметь^сры- |
||||||||||||||||||
ральной |
маслоохладительной |
установ |
щку и аварийный спуск масла. Управ |
|||||||||||||||||||
ке, обслуживающей несколько баков. |
ление запирающей заслонкой |
аварий- |
Рис. 6.2. Вертикальный закалочный бак с многоярусным подводом холодной жидкости
ного спуска следует вывести на рабо |
ке необходимый для охлаждения змее-' |
|||||
чую площадку. |
вик |
невозможно |
разместить в баке. |
|||
При небольшом количестве баков |
В этом случае целесообразно |
исполь |
||||
и малой напряженности работы приме |
зовать |
централизованное |
охлаждение |
|||
няют местное охлаждение закалочной |
жидкости. |
иногда |
приходится |
|||
жидкости. Наиболее целесообразно в |
Для |
закалки |
||||
этом случае использовать охлаждае |
использовать две закалочные |
жидкос |
||||
мые водой змеевики 1 (рис. 6. 1, б), |
ти — воду и масло. В этом случае удоб |
|||||
расположенные по внутренним стенкам |
но применять сдвоенные баки с отделе |
|||||
бака, и индивидуальные маслоохлади |
ниями для воды и масла. |
|
|
|||
тели пластинчатого типа 2 (рис. 6. 1,в). |
Часто в баках закалочную жид |
|||||
Баки с двойными стенками, между |
кость |
|
подогревают и перемешиватот |
|||
которыми циркулирует охлаждающая |
при |
помощи механических |
мешалЪТГ |
|||
вода, неэффективны, так как их тепло |
или сжатого воздуха. Последний нель |
|||||
передающая поверхность незначитель |
зя вводить во время закалки, так как |
|||||
на и скорость охлаждающей воды не |
пузырьки воздуха |
могут |
адсорбиро |
|||
велика. При высокой тепловой нагруз |
ваться на детали и способствовать об- |
|
|
|
|
|
|
катки для усиления охлаждения в баке |
|||||||
|
|
|
|
|
|
устраивают приспособление, состоящее |
|||||||
|
|
|
|
|
|
из верхней кольцевой трубы, от которой |
|||||||
|
|
|
|
|
|
отходят |
8—12 |
вертикальных |
трубок |
||||
|
|
|
|
|
|
длиной 3—4 м с отверстиями диамет |
|||||||
|
|
|
|
|
|
ром 5 мм через каждые |
100 мм. При |
||||||
|
|
|
|
|
|
подаче воды в кольцевую трубу поверх |
|||||||
|
|
|
|
|
|
ность валка |
подвергается энергичной |
||||||
|
|
|
|
|
|
струйной |
закалке. Струйное |
охлажде |
|||||
|
|
|
|
|
|
ние применяется и в малых баках при |
|||||||
Рис. 6.3. Бак со струйным душевым устройст |
закалке штампов. На рис. 6. 3 изобра |
||||||||||||
|
вом для закалки штампов |
жен закалочный бак с двумя струйны |
|||||||||||
разованию мягких пятен. Для отсоса |
ми устройствами: левое |
1 выполнено в |
|||||||||||
виде четырех параллельных трубок с |
|||||||||||||
паров масла над малыми батга-шгуста— |
отверстиями, а правое 3 — в виде трех |
||||||||||||
н-а^лтгнагкгмвытяжные колпаки, а при |
отдельных сопел. Подлежащий |
закал |
|||||||||||
загрузке и выгрузке деталей |
из бака |
ке штамп укладывается в бак фигурой |
|||||||||||
краном или |
электроталью |
рекоменду |
вниз на решетку 2. Поступающие под |
||||||||||
ется |
устраивать |
бортовые |
отсосы. |
давлением струи жидкости, сбивая па |
|||||||||
В глубоких вертикальных баках для |
ровую рубашку, способствуют быстро |
||||||||||||
поддержания |
равномерной |
температу |
му и равномерному охлаждению дета |
||||||||||
ры жидкости |
ее выводят |
с |
помощью |
ли. |
|
|
|
|
|
|
|
||
сопел, расположенных в несколько ря |
Загрузку и разгрузку деталей в зака |
||||||||||||
дов по высоте бака |
(рис. 6.2). В масля |
лочных баках следует механизировать. |
|||||||||||
ном баке диаметром 4 и высотой 10 м |
Простую механизацию можно осу |
||||||||||||
холодная жидкость поступает по цен |
ществить, |
применяя |
пневматические |
||||||||||
тральной трубе 1 и четырем рядам |
или гидравлические |
подъемники (рис. |
|||||||||||
сопел 2. Нагретая жидкость отводится |
6. 4). В баке с пневматическим |
||||||||||||
•через |
сливной карман 5 по |
трубе 4. |
подъемником (рис. 6. 4, а) |
нагретые |
|||||||||
Труба 3 служит для подачи пара или |
детали выдаются из печи на стол / за |
||||||||||||
сжатого воздуха. Предусмотрен также |
калочного бака |
7. Стол |
подвешен на |
||||||||||
аварийный спуск 6 масла. |
|
|
раме 2 из четырех тяг к штоку подъем |
||||||||||
При закалке валков холодной про |
ника 4. |
Рычаг золотника 3, |
поворачи- |
Рис. 6.4. Закалочные баки с пневматическим или гидравлическим подъемником
|
|
|
|
|
дочки 5 приводятся в переменное вра |
|||||||||
|
|
|
|
|
щение, и вал совершает колебательное |
|||||||||
|
|
|
|
|
движение в закалочной жидкости, од |
|||||||||
|
|
|
|
|
новременно вращаясь вокруг своей оси. |
|||||||||
|
|
|
|
|
Вращение вала способствует его равно |
|||||||||
|
|
|
|
|
мерному охлаждению и резкому умень |
|||||||||
|
|
|
|
|
шению |
коробления. |
Холодная |
жид |
||||||
|
|
|
|
|
кость подводится через отверстия тру |
|||||||||
|
|
|
|
|
бы 8 в низ бака, а нагретая — сливает |
|||||||||
|
|
|
|
|
ся через внутренний карман 1. |
|
|
|||||||
|
|
|
|
|
М е х а н и з и р о в а н н ы е з а к а |
|||||||||
|
|
|
|
|
л о ч н ы е б а к и н е п р е р ы в н о г о |
|||||||||
|
|
|
|
|
д е й с т в и я |
могут |
иметь |
различнее |
||||||
|
|
|
|
|
транспортные |
средства: конвейер, |
по |
|||||||
|
|
|
|
|
воротную траверсу, |
качающийся |
стод, |
|||||||
|
|
|
|
|
подъемники и толкатели, скиповое уст |
|||||||||
|
|
|
|
|
ройство, вращающийся барабан и др. |
|||||||||
|
|
|
|
|
(Наиболее часто применяются зака |
|||||||||
|
|
|
|
|
лочные баки с горизонтальным |
плас |
||||||||
|
|
|
|
|
тинчатым конвейером |
(рис. 6.6). В ба |
||||||||
|
|
|
|
|
ке для закалки легких деталей (рис. 6. |
|||||||||
|
|
|
|
|
6, а) они транспортируются пластинча |
|||||||||
|
|
|
|
|
тым конвейером, ролики которого дви |
|||||||||
|
|
|
|
|
жутся по |
направляющим |
уголкам 7, |
|||||||
|
|
|
|
|
прикрепленным к стенкам бака швед- |
|||||||||
ваясь, выпускает сжатый воздух из |
лерами 9. Конвейер приводится в дви |
|||||||||||||
жение двумя цепями из специальных |
||||||||||||||
подъемника, и стол опускается в масло. |
звеньев 4, натянутых |
на |
двух |
парах |
||||||||||
Для центрирования стола к нему |
при |
цепных звездочек 1 и 8. Он имеет гори |
||||||||||||
варены втулки 6, которые скользят по |
зонтальный участок, на который пада |
|||||||||||||
направляющим штангам 5. Охлаждаю |
ют нагретые |
детали, |
и |
наклонный — |
||||||||||
щая жидкость подается в низ бака по |
для их выдачи из бака. Угол наклона |
|||||||||||||
трубам 8. По окончании закалки стол |
часто делается равным |
35—40° |
|
Для |
||||||||||
поднимается тем же подъемником 4. |
экономии места его можно взять боль |
|||||||||||||
На рис. 6. 5, б показан бак для закал |
шим, но, чтобы избежать сползания |
|||||||||||||
ки деталей в горячем масле с гидрав |
деталей, на нем необходимо устраивать |
|||||||||||||
лическим подъемником. Изделия |
вы |
поперечные ребра. Верхняя пара звез |
||||||||||||
даются на стол 2, который погружает |
дочек |
8 — ведущая. |
|
Горизонтальный |
||||||||||
ся в бак 1 с помощью тяг 3 подъемни |
участок при натяжении |
полотна |
|
кон |
||||||||||
ка 4. В правой стороне бака находятся |
вейера создается верхними направляю |
|||||||||||||
насос 7 с электродвигателем 5 и U-об- |
щими уголками 6. Холодная жидкость |
|||||||||||||
разный трубчатый нагреватель 6. |
|
подводится около желоба 5, по которо |
||||||||||||
Заслуживает |
внимания |
простое |
му детали падают из печи в бак. Для |
|||||||||||
приспособление для закалки |
валов и |
усиления циркуляции в передней |
тор |
|||||||||||
труб в горизонтальном положении при |
цевой стенке бака установлен пропел |
|||||||||||||
вращении их на цепях во время охлаж |
лерный насос 3, он |
отсасывает |
масло |
|||||||||||
дения |
(рис. 6. 5). Бак длиной 8, шири |
по каналу 2 из нижней части бака. |
раз |
|||||||||||
ной 1 и глубиной 1,6 м имеет шесть пар |
Выпускают конвейерные баки |
|||||||||||||
роликов 2 и 4, укрепленных |
на крон |
личных размеров. В табл 6. 1 приведе |
||||||||||||
штейнах в верхней части боковых сте |
на техническая характеристика |
зака |
||||||||||||
нок бака. Через ролики перекинуты ка |
лочных баков. Мощность привода кон |
|||||||||||||
либрованные цепи, которые одним кон |
вейера составляет 1,5—2,0 кВт, насоса |
|||||||||||||
цом закрепляются к стенке бака, а дру |
1—1,5 |
кВт. |
Длина |
|
горизонтального |
|||||||||
гим — огибают |
шесть звездочек |
5 и |
участка конвейера определяется |
необ |
||||||||||
через ролики противовеса 7 крепятся к |
ходимым |
временем |
охлаждения |
дета |
||||||||||
наружной стенке бака. Звездочки за |
лей и скоростью движения л ен ты ^ |
|||||||||||||
креплены на оси 6, Приводимой во вра |
В процессе закалки тяжелых дата- |
|||||||||||||
щение. Нагретый вал 3 помещают на |
лей они при падении со |
значительной |
||||||||||||
цепи |
(положение I) и погружают в |
силой ударяются о полотно конвейера. |
||||||||||||
бак |
(положение II). Через ось |
звез-4 |
В таком баке используют устройство, с |
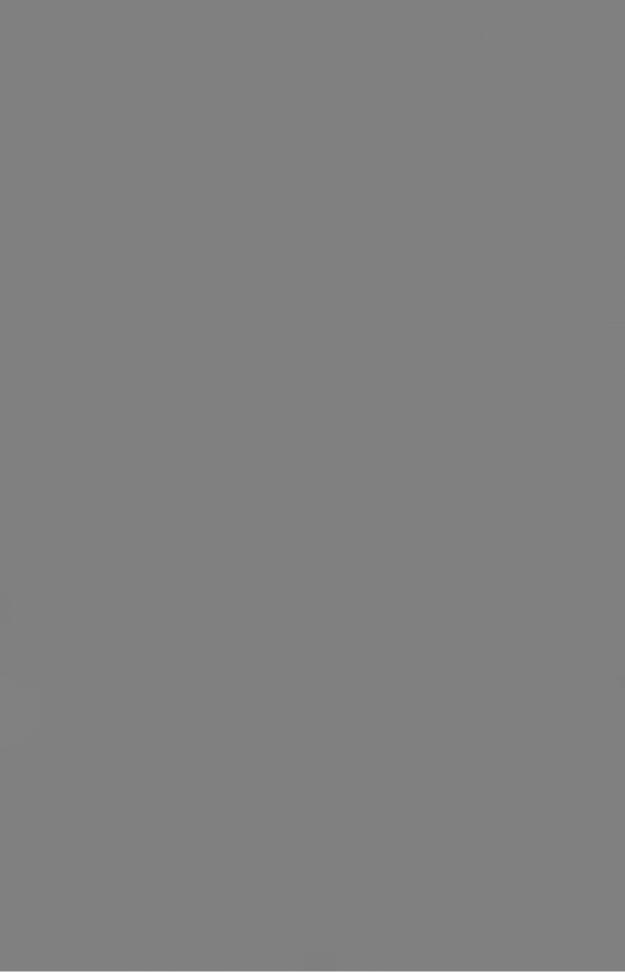


Рис. 6.10. Закалочные баки, используемые в П-образных агрегатах
ка открывается с помощью приспособ ления, состоящего из четырех стоек 4, укрепленных на столике 3. При движе нии траверсы вверх стойки поднимают крышку, а при обратном движении тра версы крышка опускается и закрывает отверстие выдачи.
В баке цементировочной печи авто завода им. Лихачева (рис. 6. 10, б) из делия закаливаются и передаются с помощью двух платформ 1 и 4 гидрав лическими подъемниками 2 и 3 и вин товым толкателем 6. Поддон с изделия ми выдается из печи на платформу 1. Опускаясь в бак 5, платформа устанав ливает поддон на направляющие, по которым он передвигается винтовым толкателем 6 на платформу 4. Послед няя, поднимаясь из бака, доставляет поддон с изделиями на вторую парал лельную линию.
Упростить передачу поддонов с из делиями после закалки во второй ряд позволяет бак с рычажным механиз мом (рис. 6. И). Две пары рычагов 2 шарнирно закрепляются на столике 1 с помощью пальцев в подшипниках 8 бака. С одной стороны на концы паль цев неподвижно насаживаются две одинаковые шестерни 3, приводимые во вращение через третью шестерню
4 и рейку 5 от гидравлического цилин дра 6. Масса столика уравновешивает ся грузами 7, закрепленными на конце рычагов 2. Начальным его положением является самое нижнее (в этом Поло жении изделия закаливаются). Оно фиксируется под действием тяжести поддонов с изделиями. Герметизация бака достигается гидравлическими затворами. Правое выдающее отвер стие бака закрывается крышкой, кото рая может открываться вертикальны ми стойками (см. рис. 6. 10, а), укреп ленными на столике.
Упрощенная конструкция бака ти па качели показана на рис. 6. 12. Плат форма 2 свободно закрепляется на двух рычагах 3, приводимых во враще ние осью 4 с помощью шестерни 5 и рейки 6, которая является продолже нием штока гидравлического цилиндра 7. На конце штока подвешен гру3 дг уравновешивающий массу платф0р1 мы. Горизонтальное положение послед ней обеспечивается балансиром is с грузом 12. Жесткое движение баланси ра 13 осуществляется двумя роликами 11, которые двигаются по направляю щим 10, закрепленным на стенках ба ка 8. Герметизация бака достигается тамбурами 1 и 15 и перегородкой 14.
|
Iй! |
|
|
|
.......................| |
~ |
| |
|
|
||
|
1Г^г------ |
|
|
|
|
||||||
|
1 |
^ |
|
|
|
|
|
|
|
|
|
|
tzd1 |
2 |
^ 1 |
1 |
|
|
|цЕ |
|
|
||
|
Т З -------- |
|
|
i P j i |
|
|
|
||||
|
|
|
|
|
- .- _ - L — |
|
|||||
|
Цемент ационная |
|
|
|
Г |
Моечная |
|
||||
|
1 |
В |
7 |
\ машина^_ _ _ _} |
|||||||
|
I |
печь |
|
||||||||
|
|
|
|
|
|
|
|
||||
|
|
|
|
|
|
|
|
|
|
|
|
Рис. 6.1:1. Закалочный бак с рычажным механизмом |
(типа качели) |
|
|||||||||
На рис. |
6. 13 показан закалочный |
|
лизованного |
охлаждения |
закалочной |
||||||
бак с двумя скиповыми подъемниками. |
|
жидкости при значительном числе ба |
|||||||||
Поддон с деталями из |
печи |
|
выдается |
|
ков и большой расчетной поверхности |
||||||
на гребенчатую подставку 3, которая, |
|
змеевиков, |
которые нельзя разместить |
||||||||
скользя по наклонной плоскости 2, по |
|
в баке. Схема установки |
изображена |
||||||||
гружается в бак с помощью цепной пе |
|
на рис. 6. 14. Нагретое масло из слив |
|||||||||
редачи 1. В нижнем положении первая |
|
ных карманов закалочных баков 1 по |
|||||||||
подставка |
проходит через |
промежут |
|
ступает самотеком в общий сливной |
|||||||
ки между ребрами второй 4 и поднима |
|
бак 5, из которого через приемный кла |
|||||||||
ется с помощью цепной передачи 6 по |
|
пан с сеткой и фильтры 4 подается на |
|||||||||
наклонной плоскости 5, вынимая под |
|
сосом 3 в |
охладительные |
колонки 2. |
|||||||
дон с закаленными деталями из бака. |
|
Охлажденное |
масло подводится вниз |
||||||||
М а с л о о х л а д и т е л ь н ы е |
ус |
|
закалочных баков 1. |
|
|||||||
т а н о в к и |
применяются для |
центра |
|
Наиболее распространенные типы |

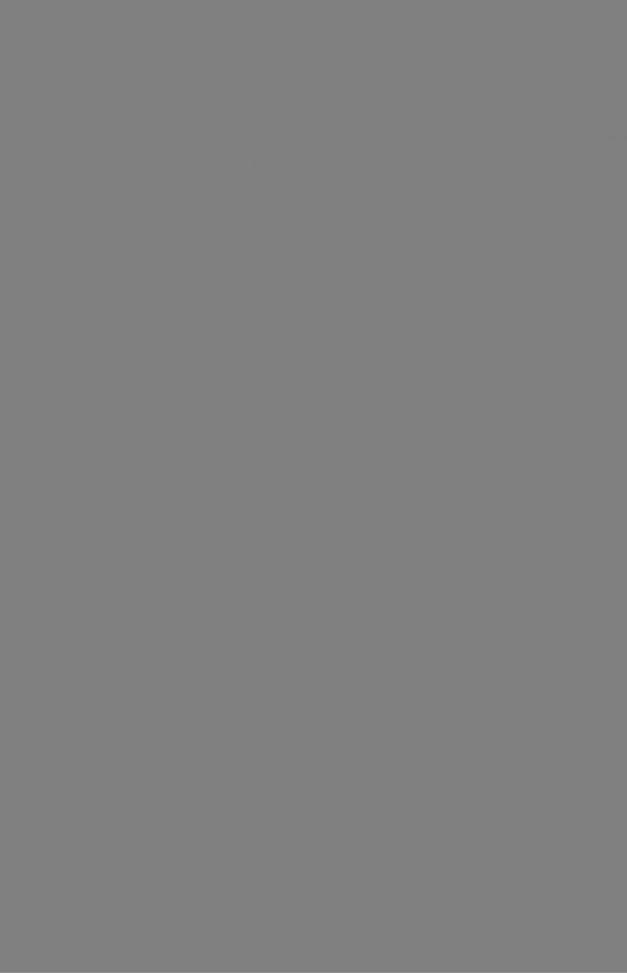
Т а б л и ц а 6.2. Техническая |
характеристика |
|||||||
|
трубчатых маслоохладителей |
|
||||||
Внешние |
|
£ |
Диаметр |
Наружныйдиаметр ммтрубок, |
Поверхностьохлажде м*ния, |
Количествомасла л/мин |
||
Диаметр |
Высота |
|
водыдля |
закалоч?дляжидкоЗной сти |
||||
размеры |
|
|
подводящих |
|
|
|
||
холодиль |
|
|
и отводящих |
|
|
|
||
ника, мм |
|
|
труб, мм |
|
|
|
||
|
|
|
и, |
|
|
|
|
|
|
|
|
« |
|
|
|
|
|
|
|
• |
03 |
|
|
|
|
|
|
|
|
XJ |
|
|
|
|
|
|
|
|
и |
|
|
|
|
|
|
|
|
еа |
|
|
|
|
|
130 |
1100 |
|
75 |
25 |
25 |
14 |
0,6 |
18 |
200 |
1800 |
|
270 |
50 |
50 |
14 |
3 |
90 |
У?50 |
2600 |
|
460 |
60 |
90 |
14 |
12 |
300 |
400 |
2600 |
|
860 |
120 |
120 |
14 |
25 |
700 |
650 |
2500 |
|
2350 |
150 |
150 |
16 |
60 |
1800 |
|
|
|
■В У* |
|
|
|
|
|
П р и м е ч а н и е . |
Температура воды |
20 °С, |
мас |
|||||
ло охлаждается |
с 55 до 30 °С, рабочее давление воды |
|||||||
и масла |
0,5 МПа. |
|
|
|
|
|
числа труб по высоте и ширине холо дильника. Секции, расположенные по ширине, соединяются сборными труба ми 2 для масла и 3 для воды. Масло движется навстречу воде. К. п. д. уста новки достаточно высокий, так как ма сло, имеющее меньший коэффициент теплоотдачи, движется тонким слоем, омывая трубы с водой и одновременно теряя тепло через поверхность наруж ной трубы в окружающее пространст во. Однако для чистки такого масло охладителя его необходимо полностью разбирать.
Характеристика трубчатых масло охладителей приведена в табл. 6. 2.
Фильтры применяются для очис1жи охлаждаемой жидкости от грязи, ока лины и других примесей и представ ляют собой цилиндры со вставленными в них сетчатыми корзинами. Удобнее использовать несколько рядов сеток с постепенно уменьшающимися ячейка ми. Чтобы не останавливать работу во время чистки сеток, применяют два фильтра. Сливные баки располагают ся. ниже уровня земли. Часто сливной бак служит также и для спуска масла на случай пожара. При большом коли честве закалочных баков в цехе вме стимость сливного бака делается срав нительно небольшой, а аварийный бак устраивается отдельно в земле за пре делами цеха. На рис. 6. 16 показана центральная маслоохладительная ус тановка, включающая восемь охлади тельных колонбк 1 с поверхностью ох лаждения 100X8=800 м 2, буферный сливной бак 2 объемом 14 м3 и четыре
насоса 3 шестеренчатого типа, обслу живающие вертикальный бак 5.
Охладительные колонки переклю чают на последовательное или парал лельное соединение с помощью кранов 4. Движение масла показано сплошны
ми стрелками, |
воды— штриховыми. |
Рассматриваемая |
маслоохладительная |
установка может быть размещена в цехе непосредственно у закалочных баков. Иногда целесообразно устанав ливать ее в пространстве между колон нами цеха. В современных больших маслоохладительных установках тре буемая температура охлаждения мас ла поддерживается автоматически (и з
меняется количество пропускаемой охлаждающей воды).
6.2.РАСЧЕТЫ ЗАКАЛОЧНЫХ БАКОВ
ИМАСЛООХЛАДИТЕЛЬНЫХ
УСТАНОВОК |
|
Расчет з а к а л о ч н е г о б а к а |
пе |
р и о д и ч е с к о г о д е й с т в и я |
сво |
дится к нахожд'ению полезного объема бака по уравнению теплового баланса. При этом считается, что все выделен ное во время охлаждения металла теп ло идет на нагрев закалочной жидкос ти. Установив наибольшую массу од новременно закаливаемых деталей и предельно допустимые температуры нагрева охлаждающей жидкости, рас считывают необходимый объем зака лочной жидкости, т. е. минимальный полезный объем бака. Уравнение теп лового баланса имеет следующий вид:
Откуда
Г * |
н—Citu. к) |
(6.1) |
к — ^ж. и) |
Здесь G — масса одновременно Зака ливаемых деталей, кг; сi и Сч— Сред ние теплоемкости металла от 0° д0
*м.н и ^м.ю кДж/(кг-К); *м.н — началь ная температура нагрева металла, °Q .
ttd-.K— конечная температура металла' после охлаждения, °С; Уж — объем за калочной жидкости, л; ст— Теплоем кость закалочной жидкости, кДж/(л\/ ХК); *ж.к — конечная температура Жи_ дкости после закалки, °С; ^ж.н —-на чальная температура закалочной Жи_ дкости,°С.
При закалке в воде начальная тем пература воды в водопроводе летом /ж.н принимается равной 15—20 °Q а
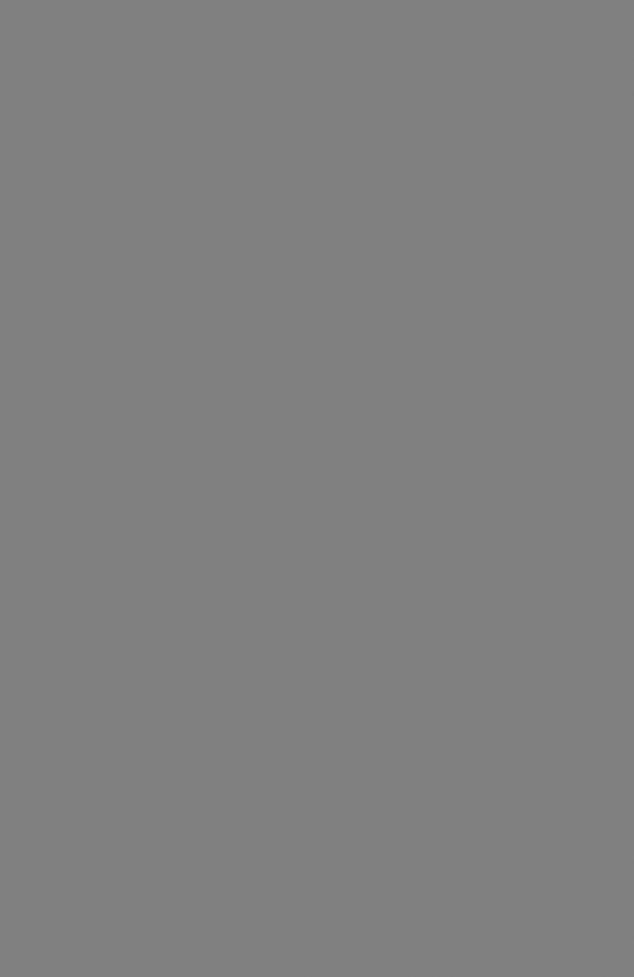
9000 (0,7 1. • 850 — 0,50 • 1 SO* |
r л ллл |
|
2,1 (8 5 - 4 0 ) |
|
|
Сж |
50 000-0,9 |
(на практи- |
Отношение — = |
--------------- = 5 |
|
<7М |
9000 |
|
ке оно равно 5 —7).
При длине детали б м высоту бака прини маем равной 8 м, тогда площадь его попереч ного сечения должна составлять 50 : 8 = 6 ,2 м2, что соответствует диаметру 2,8 м.
Размеры сливного кармана бака определя
ются суммированием |
|
|
|
||||
GM/ Y* = |
9000 : 7800 |
= |
1,15 м3 |
|
|||
— объем |
масла, |
вытесненного |
металлом, и |
||||
|
А Уж = |
|
Y40 — 7эо |
|
|||
|
|
Уж |
|
|
|
||
|
|
|
|
790 |
|
|
|
|
= |
900 — 870 |
1,72 м3 |
|
|||
|
5 0 ------------------= |
|
|||||
|
|
|
|
870 |
|
|
|
— прирост |
объема |
масла в результате |
нагрева. |
||||
Объем сливного |
|
кармана |
составляет |
1,15+ |
|||
+ 1,72=2,87 |
м3. |
|
|
|
|
|
|
Если |
принять |
ширину |
кармана |
равной |
350 мм (наружный диаметр 3550 мм, внутрен ний 2800 мм), то при объеме 2,87 м3 его глу бина
Укар
А = ----------------- ------------ =
JL (D 2 — D2 )
2.87-4
л 0,80 м, или 800 мм.
3,14(3,552 — 2,82)
Перед закалкой следующей садки жидкость должна быть охлаждена до начальной температуры t m .u. Естест венное охлаждение в результате теп лоотдачи через стенки бака и зеркало ванны происходит очень медленно. В баках, углубленных в землю, темпе ратура снижается от 60 до 20 °С со скоростью 1—2°/ч, а в надземных ба ках со скоростью 3—5°/ч. При закал ке в воде холодная вода поступает из водопровода, а при закалке в масле оно подается из центральной масло охладительной установки. Если такая установка отсутствует, в масляный бак вводят змеевик, охлаждаемый водой. Скорость движения воды принимается равной ее скорости в водопроводе vB= = 0,5 —1,0 м/с, а скорость подачи мас ла УМао = 1,0—2,0 м/с. Масло и вода из бака сливаются самотеком со ско ростью 0,2—0,3 м/с.
Расчет змеевика закалочного бака сводится к нахождению необходимой теплопередающей поверхности между маслом и охлаждающей водой и раз меров змеевика. Поверхность змееви-
ка определяется из условий теплопе редачи через стенку:
|
|
Q = |
O-Ftcp, |
|
(®;2 ) |
||
где |
Q — количество |
тепла, |
которое |
||||
надо передать от масла |
к воде за |
1 ц9 |
|||||
кВт; |
сй=80—120 |
кВт/(м2-К )— сред-’ |
|||||
ний |
коэффициент |
теплопередачи |
от |
||||
масла к воде |
через |
стенку |
змеевика; |
||||
F — теплопередающая |
поверхность, |
||||||
змеевика, м2; |
|
|
|
|
|
|
|
|
tiK. н + t Ж. К |
tn. н + |
^в. к |
|
|||
|
Т е р = |
2 |
|
|
2 |
* |
|
тСр — средняя |
разность |
температур |
между маслом и охлаждающей водой; ^к.ш <ж.к — начальная и конечная тем пературы нагрева масла, t B.н, ^в.к начальная и конечная температуры воды.
П ри м ер 2. Определить необходимые разме ры змеевика для условий предыдущего при мера.
Размеры бака были равны: внутренний ди аметр 2,8 м и высота 8 м. Наименьшее время меж ду операциями закалки 6 ч. Среднее коли чество тепла, которое должно быть передано от масла к воде в час, составляет:
п — Qм _ |
^ м ( С 1 ^ м . Н |
а |
С2*М . к ) _ |
Чм |
: |
|
9000 (0,71- 850—0,50 *150)
= 792 800 кДж./ч.
6
При охлаждении масла от 40 °С макси мальная температура нагрева воды может быть принята не выше 35 °С. Начальная темпе ратура воды принимается равной 20 °С (тем пература воды в водопроводе летом).
Следовательно, потребуется пропустить такое количество воды:
,, |
_ |
|
<2м |
|
_ |
792 800 |
_ |
” |
|
|
|
|
|
4 ,2 ( 3 5 - 2 0 ) |
|
= |
12 584 |
л/ч « |
12,6 |
м3/ч = 0,0035 м3/с. |
|||
При |
скорости |
воды v tt= |
1 м/с поперечное се |
||||
чение змеевика должно |
быть равно 0,0035: 1 = |
||||||
= 0,0035 |
м2, откуда внутренний диаметр трубы |
||||||
змеевика |
d nn = 21 |
мм, |
а наружный |
диаметр, |
|||
взятый по сортаменту трубы, d nар = 24 мм. |
|||||||
Среднюю разность температур меж ду мас |
|||||||
лом и водой |
можно |
определить как среднее |
|||||
арифметическое: |
|
|
|
|
|||
|
|
|
t)K. Н + |
^Ж. К |
^В. II + / В. к |
|
|
|
|
8 0 + 4 0 |
|
3 5 + 2 0 |
|
||
|
|
~2 |
_ |
2 |
32 °С. |
||
|
|
|
|
||||
Коэффициент |
|
теплопередачи |
а = |
||||
= 100 |
В т/(м 2-К ). Тогда |
по |
формуле |
(6.2) на |
ходим теплопередающую поверхность змее вика:
F = |
Qм |
792 800 |
Ct/cp |
6 8 ,8 М2.. |
|
|
100 *32-3,6' |
При наружном диаметре 24 мм поверх
ность ОДНОГО ПОГОННОГО Метра |
Трубы JtfifHap = |
||
=3,14-0,24.1 «0,075 м2. |
|
L — |
|
Необходимая |
длина |
змеевика |
|
= 68,8:0,075=917 |
м. Змеевик |
размещается |
на |
внутренней стенке бака, поэтому средний диа метр витка змеевика меньше диаметра бака на 0 ,1 м, т. е. равен 2,7 м, а его длина ГШ= 3,14х Х 2,7=8,5 м. Змеевик должен иметь 9 1 7 :8 ,5 = = 108 витков.
При размещении змеевика в баке на высо те 7,5 м шаг змеевика равен 7500 : 108=70 мм, т. е. просвет между его соседними витками со ставит 70—24= 46 мм. Змеевик можно изгото вить так: необходимо взять трубу диаметром
24 мм, длиной |
917 м, загнуть ее по |
среднему |
диаметру 2,7 |
м и разместить в баке |
с шагом |
70 мм. |
|
|
Объем |
з а к а л о ч н о г о |
б а к а |
н е п р е р ы в н о г о д е й с т в и я , оп ределенный из условий теплового ба ланса, получается небольшим и в нем нельзя разместить конвейер, поэтому размеры бака находятся конструктив-) но. Ширина бака берется в зависимос ти от^ полезной ширины печи^ обслу живаемой баком, или ширины ленты конвейера печи; длина горизонтально го участка конвейера определяется по необходимому времени пребывания деталей в Охлаждающей среде и ско рости движе'ния конвейера бака. Пос ледняя должна быть в два-три "раза больше скорости движения конвейера печи или средней скорости движения деталей в4печи v^ = 2—3 аПч, чтобы в закалочном баке не нагромождались детали. Время пребывания деталей в охлаждающей среде т рассчитывается. Длина горизонтального участка кон
вейера _Lrop—Щт. Длину бака опреде ляем с учетом размеров конвейера. Затем вычисляется количество тепла, вносимого в бак охлаждаемым метал лом за 1 ч, и необходимые размеры охлаждающего змеевика или размеры трубы для подачи холодной жидкости и отвода нагретой.
Пример. Требуется найти размеры конвей ерного бака для закалки в масле 400 кг метал ла в час*. Необходимое время охлаждения дета лей 1 мин, а средняя скорость их движения в пеЧИ Упеч= 0,3 м/мин.
Берем ширину конвейера бака на 100 мм больше ширины лотка печи, выдающего нагре тые детали в бак. Минимальная длина горизон тального участка конвейера бака (от места па дения деталей щ конвейер) Lr0p= (0,3X3) 1,0=
= 0,9 м.
Угол наклонной части конвейера принима ем равным 30°. Находим размеры бака, учиты вая длину горизонтальной и наклонной частей конвейера и высоту жидкости над закаливае мыми деталями (200—400 мм). В данном слу чае высота бака равна 1,5 м, а длина 4,0 м.
Определяем количество тепла, выделяемого в 1 ч закаливаемым металлом, имеющим перво начальную температуру 850 °С:
Q M = G ( c н .к ) =±=
=400(0,71 • 850 — 0,50 • 150) =
=211 400 кДж/ч.
При охлаждении змеевиком его. теплопере дающая поверхность вычисляется по формуле
|
|
<3м |
211 400 |
- = 18 М2 . |
|||
|
|
atср |
100.32-3,6 |
||||
Потребное количество |
охлаждающей воды |
||||||
у |
_ |
QM |
|
_ |
211*400. |
||
|
В |
св('в .к - |
|
4,2(35 “ |
20) |
||
= 3360 кг/ч = 3,36 |
м3/ч = |
0,0009 !м 7с. |
|||||
При скорости воды |
в змеевике ув =. If м/с. внут |
||||||
ренний |
его диаметр |
с?вн = 34 мм, |
а., наружный |
||||
^нар = 40 мм. Поверхность длины |
1 |
м змеевика |
|||||
f= 1 |
д^нар = 3,14-0,04 = 0,125 |
м2, |
е^о длина |
||||
L = 18:0,125 = 144 м. |
|
|
|
|
|
||
|
Размещаем змеевик гна двух |
боковых стен |
ках бака, имеющих высоту 1 ,5 ,. длину =4 ,м каж дая. Длина одного витка, змеевика составляет 1,5X 2 = 3 м. Количество Шагов'равно 144:3=* = 48. При общей длине Стенок* 8 м размер ша га составляет 8000:48= 167 мм, т.. е. зазор между соседними трубками равен около 42 мм, что вполне приемлемо. Если здз.ор будет меньше диаметра трубы; змеевики' размещают еще и на дне бака'или используют централи зованную маслоохладительную установку.
Для случая охлаждения закалочной жидко сти в центральной маслоох^адитеЛьнрй уста новке определяются сечения подводящих и от водящих труб. Количество масла, которое на до сменить при его нагреве от 30 до .60 °G,
у |
_ |
QM |
. |
. _ |
.. |
.2 1 1 |
400 |
_ |
“аС |
|
См(<„.к-'м .н> |
2,1(60 у- 30) |
|||||
= |
3360 у/ч = 3,36 |
м3/ч = |
0,001 |
м3/с. |
||||
Масло |
в |
змеевик |
подается |
под |
давлением, |
|||
и его скорость у в подаодящей |
трубе |
можно |
принять равной 1 м/с. Масло из бака отводит ся самотеком, поэтому в отводящей трубе а = = 0,25 м/с. При указанных скоростях необхо димые диаметры подводящей и отводящей труб будут соответственно равны, 36 и 72 мм..
При среднем |
диаметре |
цепной, |
шестерни |
|||||
£)шес = 550 |
мм и |
скорости |
движения |
ленты |
||||
конвейера |
у0 = 0,3-3 = 0,9 |
м/мин |
частота |
враще |
||||
ния приводного вала |
|
|
|
|
|
|||
|
Уб |
0,9 |
|
= 0,009 |
с- |
|||
jtDn |
3,14-0,55-60 |
|||||||
|
|
|
||||||
Если |
двигатель имеет , частоту |
вращения |
||||||
2 0 с-1, то передаточное |
число |
должно быть |
равно 20 : 0,009«2220. Это может быть достиг
нуто с |
помощью двух шкивов |
(6 = 1 ,5 ), |
чер |
вячного |
редуктора (i2= 25) и храповика |
(6 = |
|
= 60). |
|
|
|
Тепловой расчёт м а с л о о х л а д и - |
|||
т е л ь н о й у с т а н ов д и |
сводится к |
определению необходимой поверхнос ти охлаждения для теплопередачи от масла к охлаждающей воде. При рас чете принимается, что все тепло, вы деляемое охлаждающимся металлом, воспринимается маслом и от него пе редается воде.
Количество масла (если оно не за дано) и воды находится из уравнения теплового баланса маслоохладителя:
QM == УжСт (£ж. н |
tm. к) = |
— КвСВ(^В.к |
^в. н) » |
где QM— количество |
тепла, выделяе |
мого металлом за 1 ч при закалке во всех баках, обслуживаемых маслоох ладительной колонкой, кДж; Vm— расход масла, л/ч; ст— теплоемкость масла, кДж/(л- К ); tmM— начальная температура масла, поступающего в маслоохладительную колонку; tm.K— конечная температура охлаждаемого масла (берется не ниже 30 °С, так как при более низкой температуре повин шается вязкость и снижается закали вающая способность); VB— расход во
ды, л/ч; |
св — теплоемкость воды, |
кДж/(л • К ); |
/в.к — конечная темпера |
тура воды по выходу из колонки, °С; /в.н — начальная температура воды, поступающей в маслоохладительную колонку (принимается равной темпе ратуре воды в водопроводе летом 15— 20 °С).
Пользуясь приведенными данными, можно определить количество масла, пропускаемого через колонку в 1 ч. Необходимое количество воды зави сит от значения /в.к. Существенное уве личение количества пропускаемой во ды не дает должного эффекта. В труб чатом маслоохладителе при отношении количества воды к количеству масла, равному 0,5; 1; 2; 4; и 6, температура последнего падала соответственно на 10; 13; 16; 18 и 19 °С. Максимальный объем пропускаемой воды целесооб разно принимать равным одному—двум объемам масла. При этом температу ра воды в маслоохладителе повысит ся на 10—15 °С.
Определив количество масла и во ды, пропускаемых за 1 ч, и задавшись скоростью их движения, можно найти
поперечные сечения |
для |
поступления |
|
масла и воды: |
|
|
|
/ж |
Уж |
_ |
Ув |
ЗбООс/ж ’ ' в |
|
ЗбООив * |
|
|
|
Скорость движения воды в зависимос
ти от ее напора в водопроводе vB= = 0,5 —1,0 м/с, а нормальная скорость движения масла ам= 1 —2 м/с. Тепло
передающая поверхность |
маслоохла |
дителя F определяется |
по формуле |
( 6.2) : |
|
(ZTc р |
(6.3) |
|
где -а — коэффициент теплопередачи маслоохладителя, Вт/(м2-К); тСр — средняя разность температур в масло охладителе, °С.
Наиболее точно тСр можно опреде лить как среднюю логарифмическую
|
Тнач — Ткон |
(6.4) |
|
Тср — |
Тнач |
||
|
2,3 |
|
|
|
lg |
|
|
|
|
Ткон |
|
Здесь Тнач |
и Ткон — средние разности |
||
температур |
соответственно при |
входе |
|
в маслоохладитель |
и выходе |
из не |
го, °С.
Средняя разность температур за висит от принятого характера движе ния масла и воды:
Тнач = ^ж. R — t B.K
и Ткон == tm. к — ^в. н — при противотоке;
Тнач — ?ж. н — ^в. н
и Ткон — tm. к — ^в. н — при параллельном потоке.
Для случая охлаждения масла от 60 до 30 °С и нагрева воды от 15 до 25 °С по формуле (6.4) получим сле дующие значения средней логарифми ческой разности температур: при про тивотоке
Тнач — tm. н — |
к = |
60 — 25 = |
35 °С; |
|
Ткон == tm. к— tj |
н = |
30— 1 5 = 15°С; |
||
Тср = |
Тнач •” |
Ткон |
|
|
|
|
Тнач |
|
|
|
2,3 |
lg |
|
|
|
Ткон |
|
||
35 — 15 |
= |
24 °С; |
|
|
2,3 |
|
|
||
|
|
lg 2,3 |
||
при паралельном потоке |
|
|||
Тпач == ?ж.н — tB,н = |
60 — 15 = |
45 °С; |
||
Ткон == ^ж.к— |
к == 30 — 25 = |
5 °С; |
Тнач — Ткон
Тср =
Тнач
2,3 lg
Ткон
45 — 5
2,3 lg 9 = 18 °С.
В |
|
результате |
повышения средней |
(поперечное сечение 177* 10—6 и 314Х |
|||||||||||||||||
разности |
температур |
|
в |
маслоохлади |
Х10-6 м2). Необходимое число трубок |
||||||||||||||||
теле |
потребная поверхность |
охлажде |
при пропускании по ним масла можно |
||||||||||||||||||
ния |
|
при |
|
противотоке |
уменьшается. |
найти по формуле |
|
|
|
|
|
||||||||||
Приближенно |
среднюю |
разность |
тем |
|
|
|
|
|
|
|
|
||||||||||
ператур можно вычислить как среднюю |
|
|
|
|
|
|
|
|
|||||||||||||
арифметическую: |
|
|
|
|
|
|
|
|
|
|
|
|
|
|
|
||||||
Тср — |
^Ж.Н+ tж. к |
|
|
^ В . |
Н 4 " |
/ в . и |
|
Оно должно соответствовать конструк |
|||||||||||||
|
|
2 |
|
|
|
|
2 |
|
|
ции маслоохладителя. Чаще всего труб |
|||||||||||
|
|
|
|
|
|
|
|
|
|
|
ки располагаются в шахматном поряд |
||||||||||
|
|
|
|
|
|
|
|
|
|
|
|
|
|||||||||
|
|
604-30 |
|
25 4“ 15 |
|
|
ке, образуя правильные треугольники. |
||||||||||||||
|
|
|
|
2 |
|
|
|
2 |
|
= |
25 °С. |
Число трубок в круглом маслоохлади |
|||||||||
|
|
|
|
|
|
|
|
|
|
|
|
|
теле, состоящем из одной секции, оп |
||||||||
Суммарный коэффициент теплопе |
ределится из уравнения |
|
|
|
|
||||||||||||||||
редачи маслоохладителя |
определяется |
|
ti = . 1 -f- Зх “|- Зх2, |
|
|
|
|||||||||||||||
коэффициентами |
теплопередачи |
через |
|
|
|
|
|||||||||||||||
стенку трубок: |
|
|
|
|
|
|
|
где х — целое |
число; |
п = 7; |
19; |
37 |
|||||||||
|
|
< *= — — |
|
^— |
|
’ |
(6-5) |
и т. д. |
|
|
|
|
|
|
|
||||||
|
|
|
~ |
В круглой маслоохладительной ко |
|||||||||||||||||
|
|
|
|
------ 1 |
|
— 1------ |
|
|
лонне, |
разбитой радиусами |
на |
шесть |
|||||||||
|
|
|
|
|
О ж |
|
Л |
|
С 1в |
|
|
секций, число трубок в секции |
|
|
|||||||
где б — толщина трубки, м; к — коэф |
|
|
|||||||||||||||||||
|
п=(х-\-х2)/2. |
|
|
|
|||||||||||||||||
фициент |
теплопроводности |
материала |
Здесь |
х — целое число; |
п = 6; |
10; |
15; |
||||||||||||||
трубки |
[для |
стали |
>,=40 |
Вт/(м-К), |
|||||||||||||||||
для |
латуни >,= 100 |
Вт/(м-К)]; |
а ж и |
21 и т. д. |
|
|
п, определен |
||||||||||||||
а в — коэффициенты теплопередачи со |
Количество трубок |
||||||||||||||||||||
ответственно от масла к стенке и от |
ное из теплового расчета, принимают |
||||||||||||||||||||
стенки трубки к воде, Вт/(м2-К). |
наиболее близким к значению, кото |
||||||||||||||||||||
Суммарный |
коэффициент теплопе |
рое получается по формулам. Зная |
|||||||||||||||||||
редачи ос2 определяется в основном |
число трубок п и теплопередающую |
||||||||||||||||||||
коэффициентом аж, имеющим наимень-. |
поверхность |
маслоохладителя |
F, |
на |
|||||||||||||||||
шую |
величину. Значения суммарного |
ходим длину трубок: |
|
|
|
|
|
||||||||||||||
коэффициента теплопередачи с учетом |
|
|
I =.F/nnd. |
|
|
|
|
||||||||||||||
загрязнения |
холодильника |
при |
эксп |
|
|
|
|
|
|
||||||||||||
луатации |
могут |
быть |
найдены |
по но |
При |
большой длине |
трубок маслоох |
||||||||||||||
мограмме |
(рис. |
6. |
17) |
в зависимости |
|||||||||||||||||
ладитель можно выполнить в виде ря |
|||||||||||||||||||||
от скорости |
движения |
масла, воды и |
|||||||||||||||||||
де последовательно |
соединенных |
ко |
|||||||||||||||||||
вязкости масла по Энглеру (Э°). В слу |
|||||||||||||||||||||
лонок N (с |
длиной |
трубок |
в |
каждой |
|||||||||||||||||
чае ориентировочных расчетов суммар |
|||||||||||||||||||||
ный коэффициент теплопередачи мож |
из них l'=l:N) или |
использовать сек |
|||||||||||||||||||
ционный маслоохладитель, |
состоящий |
||||||||||||||||||||
но |
принять |
равным |
для масла |
150— |
|||||||||||||||||
из нескольких секций (2; 4; |
6 и т. д.). |
||||||||||||||||||||
200 |
|
Вт/(м2-К), |
для |
раствора |
NaOH |
||||||||||||||||
|
При |
выборе |
стандартного |
маслоохла |
|||||||||||||||||
200—250 Вт/(м2.К). |
|
|
|
|
|||||||||||||||||
|
|
|
|
дителя с известной |
поверхностью |
ох |
|||||||||||||||
По найденной поверхности охлади |
|||||||||||||||||||||
лаждения определяют количество мас |
|||||||||||||||||||||
теля |
определяем |
|
его |
размеры. Для |
|||||||||||||||||
|
лоохладителей и порядок их соедине |
||||||||||||||||||||
трубчатого |
маслоохладителя диаметр |
||||||||||||||||||||
ния |
(последовательное, параллельное |
||||||||||||||||||||
трубки принимается равным 15—20 мм |
|||||||||||||||||||||
или смешанное). |
|
|
|
|
|
||||||||||||||||
|
|
|
|
|
|
|
|
|
|
|
|
|
|
|
|
|
|
6.3. ЗАКАЛОЧНЫЕ ПРЕССЫ И МАШИНЫ
Рис. 6.17. Номограмма для определения сум марного коэффициента теплопередачи в масло охладителях
Закалочные прессы и машины при меняют с целью уменьшения коробле ния и поводки деталей при закалке. Они широко используются на заводах массового производства при охлажде нии дисков, конических шестерен ко лец, плит, коленчатых и кулачковых
Рис. G.18. Пресс для закалки конических шес терен
валиков и др. Некоторые детали, на пример листы рессор, передние оси ав томобилей, диски сцепления, охлаж даются в гибочно-закалочных маши
нах.
З а к а л о ч н ы е п р е с с ы могут быть разнообразными как по конст рукции, так и по размерам. Значитель ное распространение получили прес сы для закалки конических шестерен
(рис. 6. 18). Они состоят из верхнего 15 и нижнего 3 плунжеров, движущих ся под действием сжатого воздуха в своих .цилиндрах. На нижнем конце плунжера 15 укреплен штамп 14 с цент рирующим коническим шпинделем 12. На плунжере 3 смонтирован нижний штамп 9, имеющий в центре сегмент ную втулку 11, а по окружности ци линдр 5.
В состоянии, готовом для работы, оба штампа находятся в верхнем поло жении (как изображено на рисунке). Нагретая шестерня 10 укладывается на нижний штамп. Поворачивается ручка 16 четцрехходового крана. Сжатый воздух поступает в верхний цилиндр, заставляя плунжер 15 вместе с верх ним штампом 14 идти вниз и зажимать шестерню 10. При этом конический шпиндель 12 верхнего штампа входит в отверстие нижней втулки 11, которая раздвигается, центрируя шестерню. Давление нажима втулки регулируется сжатым воздухом, выпускаемым по трубопроводу 17. Плотная посадка шестерни на оправку предотвращает ее коробление при закалке в горизон тальной плоскости. Одновременно верхний штамп 14 с помощью двух опорных колец прижимает шестерню к нижнему штампу 9, препятствуя ее короблению.
Далее верхний плунжер, двигаясь вниз, заставляет опускаться шестер ню, зажатую между двумя штампами, в бак 7. Масло поступает в пресс по трубе 1 под цилиндр 5, а из него через отверстия 4 в бак 7. Нагретое масло отводится в маслоохладитель через трубы 6. При опускании цилиндра 5 отверстия 4 закрываются приливами 2, которые находятся внутри бака 7, а масло под давлением проходит через отверстия 8 нижнего штампа, с высо кой скоростью омывает зубья шестерен и сливается обратно в бак 7 через от верстия 13 верхнего штампа. Равно мерное интенсивное охлаждение зубьев шестерен в зажатом состоянии обес печивает хорошую закалку и умень шает деформацию. После необходимой выдержки шестерни в масле четырехходовый кран 16 поворачивается в об ратную сторону и сжатый воздух нап равляется под плунжеры. Штампы поднимаются в прежнее положение и закалочная шестерня снимается.
Давление верхнего штампа на шес терню регулируется специальным ре-
Рис. 6.19. Машина для закалки кулачковых валиков с вращением в зажатом состоянии
Аукционным клапаном; второй такой же клапан регулирует давление шпинделя 12 на внутреннее отверстие закаливае мой шестерни. Прессы снабжены мас ляными фильтрами, манометрами и предохранительным клапаном. Они работают при давлении воздуха в се ти 0,5—0,6 МПа. Прессы изготовляют для шестерен с наибольшими наруж ными диаметрами 380 и 630 мм. Они имеют соответственно площадь 0,9Х Х0,9 и 1,3X1,3 м2; высоту 2,54 и 2,86 м; массу 2,2 и 3,8 т; количество масла, заполняющего пресс, 320 и 570 л; рас ход сжатого воздуха 0,40—0,55 и 0,60— 0,70 м3/мин; объем сменяемого зака лочного масла 25 и 40 л/мин и сред нюю производительность 40 и 20 шт/ч.
При закалке дисков, колец, плит применяют штампы в виде решетча тых плит. В ряде конструкций зака лочных прессов вместо сжатого возду ха используют воду или масло, пода ваемое под давлением.
При закалке больших плит и лис тов (до 1,5X7,0 м) их зажимают-меж ду двумя плитами с опорными шипами или ребрами. В этом случае применя ют струйное охлаждение. Закалочная жидкость подается через отверстия в
опорных шипах и |
ребрах (см. рис. |
3. 27, б). |
м а ш и н ы при |
З а к а л о ч н ы е |
меняют для охлаждения длинных ци линдрических деталей (коленчатых валов, задних полуосей, кулачковых и карданных валов и др.), причем их не только зажимают, но и вращают в за калочной жидкости, что значительно уменьшает коробление.
На рис. 6. 19 изображена машина для закалки кулачковых валиков. Она имеет неподвижную станину 5, вверху которой размещены двигатель' 6, два пневматических цилиндра 4, а сбоку — два пневматических цилиндра 2 и 8. К поршням пневматических цилинд ров 4 с помощью штоков крепится верхняя подвижная станина 3, несу щая один ряд/роли'щ вЖ К штокам боковых цилиндров 8 подвешивается нижняя подвижная станин.а_(0,_ несу-_ щая на себе два ряда р.одиков 1, на саженных на две оси. Последние при водятся во вращение через ряд цилинд рических и конических передач и под вижный вертикальный шток 7 со шпонкой от двигателя 6. В состоянии, готовом для работы, обе станины на ходятся в верхнем положении. Нагре тый валик укладывается ^а нижние ролики. Сжатый воздух под давлени
ем 0,5—0,7 МПа подается в верхнюю часть цилиндра 4. Верхняя станина 3 опускается, зажимая роликами шейки закаливаемого вала, давит на нижнюю
Рис. 6.20. Боковой вид закалочно-правильной машины для закалки на воздухе коленчатых валов
станину, погружая ее в масло. Одно временно включается двигатель 6, при* водящий во вращение ролики 1 ниж ней станины. Зажатый и вращающий ся между роликами валик погружает ся в закалочную жидкость. По окон чании закалки сжатый воздух направ ляется в нижнюю часть пневмати ческих цилиндров, станины 10 и 3 под нимаются вверх, вынимая из масла закаленный валик.
В последних моделях машин пнев матические цилиндры заменены мас ляными, что позволяет более плавно зажимать вал и обеспечивает надеж ную работу. Машина снабжается мас ляным насосом с двигателем мощнос тью 2 кВт.
Производительность машины в час 50—80 валов длиной от 500 до 1000 мм и диаметром шеек до 50 мм. Бак имеет такие размеры: 2,5Х0>8Х0,9 м. Вы сота машины составляет 2,2 м, масса 4 т. Верхний штамп имеет ход 350 мм, нижний 150 мм. На одну деталь рас ходуется 0,01 м3 сжатого воздуха. За калка чаще производится в растворе каустической соды.
Для закалки на воздухе коленча тых валов из высоколегированных ста лей типа 18Х2Н4ВА применяется зака лочно-правильная машина, боковая проекция которой показана на рис. 6. 20. Нагретый коленчатый вал ко ренными шейками 5 укладывается на ряд параллельных роликов 6 и 7, сидя щих на осях, укрепленных в подшип никах рамы 8. Шейки вала зажима ются параллельными роликами 4 с по мощью пневматических цилиндров 9 через рычаги 2. Ролики 6 и 7 приво дятся во вращение от двигателя 3 через червячный и шестеренный редукторы.. Вал охлаждается в зажатом состоя нии при вращении. Одновременно про исходит и правка вала. После закалки и прекращения подачи сжатого возду ха в цилиндры 9 подвижные ролики 4 под действием груза 1 отводятся и сто рону, освобождая вал. Частота вра щения приводных роликов 1/6 с-1. Мощность двигателя составляет 6 кВт.
Закалочные машины барабанного типа широко используются для закал ки в зажатом состоянии самых разно образных деталей: передних осей ав-

Рис. 6.22. Конструкция гибочно-закалочной машины с радиальным размещением штампов:
а — боковой вид машины; б |
— продольный разрез барабана; в — схема движения штампов; |
г |
— конструкция подвижного штампа |
положение |
V штампы |
раскрываются, |
делитель 1. Производительность |
ма |
|||||||
ось выпадает на направляющую 12 и |
шины составляет 40—50 осей в час. |
||||||||||
задерживается ведущими рычагами 11, |
Гибочно-закалочные машины /ши |
||||||||||
закрепленными на штампе. При даль |
роко применяются в рессорном произ |
||||||||||
нейшем |
движении барабана закален |
водстве для гибки и закалки листов |
|||||||||
ная ось скатывается по направляю |
рессор. |
|
|
|
|||||||
щим 13 |
на |
конвейер |
отпускной печи, |
Барабанная гибочно-закалочная ма |
|||||||
а штампы, перейдя в положение 1, |
шина (рис. 6. 22) представляет собой |
||||||||||
вновь готовы к приемке нагретой оси. |
шестиугольный |
барабан, |
торцевые |
||||||||
Остальные |
пять |
штампов |
работают |
стенки 1 которого имеют по углам |
|||||||
аналогично. Полный цикл работы ма |
радиальные прорези. В углах наруж |
||||||||||
шины продолжается 70—80 с, средняя |
ной поверхности |
барабана закрепле |
|||||||||
производительность |
машины |
равна |
ны неподвижные штампы 2, а подвиж |
||||||||
160—180 осей в час. |
|
|
|
|
ные штампы 3 двигаются в радиаль |
||||||
Иногда при закалке, кроме охлаж |
ных прорезях торцевых стенок. На |
||||||||||
дения в зажатом состоянии, осуществ |
концах подвижных штампов |
насаже |
|||||||||
ляют еще правку растяжением. На |
ны ролики 4, которые соприкасаются |
||||||||||
рис. 6. 21, б изображена барабанная |
с неподвижным копиром 5. Вращаю |
||||||||||
машина для закалки передних осей |
щийся барабан находится в закалоч |
||||||||||
автомобиля с небольшим растяжением. |
ном баке 6, ниже барабана размеща |
||||||||||
По краям каждой боковой поверхности |
ется пластинчатый конвейер 7. При |
||||||||||
пятигранного барабана |
7 |
укреплены |
вращении барабана вокруг оси ролики |
||||||||
гидравлические |
цилиндры |
2, |
которые |
подвижных штампов катятся по не |
|||||||
растягивают оси штоками 3. Предва |
подвижному копиру (рис. 6. 22, в). По |
||||||||||
рительно концы оси зажимаются ку |
падая на участок с большим радиусом |
||||||||||
лачками 4 с помощью штоков гидрав |
копира R, они зажимают штампы, из |
||||||||||
лических цилиндров 9. Подошва оси |
гибая лист. На участке копира с ма |
||||||||||
дополнительно зажимается еще в двух |
лым радиусом г |
(положение |
V, VIл J) |
||||||||
точках |
раздвижными |
кулачками 5, |
штампы разжимаются, выдавая |
лист |
|||||||
приводимыми в |
движение |
гидравли |
рессоры. Нагретый лист рессоры зак |
||||||||
ческими цилиндрами 6. Нагретая пе |
ладывается в открытые штампы |
(по |
|||||||||
редняя ось автомобиля помещается в |
ложение /), которые при движении |
||||||||||
зажимы, |
растягивается |
и погружается |
барабана по часовой стрелке закры |
||||||||
в зажатом состоянии в закалочный |
ваются, изгибая лист и затем погружая |
||||||||||
бак при вращении барабана с помо |
его в зажатом состоянии в масло. При |
||||||||||
щью шестерни 8, укрепленной на валу |
достижении положения V штампы рас |
||||||||||
барабана. Вода к гидравлическим ци |
крываются, лист |
падает на |
конверт) |
||||||||
линдрам подводится через ряд отверс |
и его вынимают из закалочного бака. |
||||||||||
тий, расположенных в приводном валу, |
Для закалки более широкого ассор |
||||||||||
от насоса |
через |
специальный |
распре |
тимента листов |
рессор подвижны^ и |
Рис. 6.23. Боковой вид гибочно-закалочной ма |
|
|
|
|
|
|
||||||||
шины |
с |
размещением |
штампов |
на |
наружных |
|
|
|
|
|
|
|||
|
|
|
гранях барабана |
|
|
|
|
|
|
|
|
|
||
неподвижные формирующие |
штампы |
|
|
|
|
|
|
|||||||
делаются съемными. |
|
|
|
|
|
|
|
|
|
|
||||
На рис. 6. 23 приведена схема дру |
|
|
|
|
|
|
||||||||
гой конструкции барабана гибочно-» |
|
|
|
|
|
|
||||||||
закалочной машины с восьмью парами |
|
|
|
|
|
|
||||||||
штампов. Штампы 1 и 2 размещены |
|
|
|
|
|
|
||||||||
на наружной поверхности барабана. |
|
|
|
|
|
|
||||||||
Подвижный штамп 1 приводится в |
|
|
|
|
|
|
||||||||
движение от копира 4 через |
ролик 5 |
|
|
|
|
|
|
|||||||
и рычаг 6, шарнирно-закрепленный на |
|
|
|
|
|
|
||||||||
оси 3. Гибочно-закалочные машины |
|
|
|
|
|
|
||||||||
позволяют значительно сокращать руч |
|
|
|
|
|
|
||||||||
ные работы по наладке рессор при |
|
|
|
|
|
|
||||||||
сборке. |
|
|
|
|
|
|
|
|
|
|
|
|
|
|
Производительность барабанных ги |
|
|
|
|
|
|
||||||||
бочно-закалочных машин 300—400 лис |
Рис. 6.24. Приспособление для закалки внутрен |
|||||||||||||
тов в час, занимаемая площадь 2,5Х |
ней поверхности цилиндров в зажатом состоя |
|||||||||||||
Х5,0 м. Закалочная машина приво |
|
|
|
нии |
|
|||||||||
дится во вращение от двигателя мощ |
|
Перед закалкой головка 8 приспо |
||||||||||||
ностью 3—4 кВт через зубчатую пере |
|
|||||||||||||
дачу и редуктор. |
|
|
д л я |
з а |
собления вместе с верхним воздушным |
|||||||||
П р и с п о с о б л е н и е |
цилиндром 9 отводится на кронштей |
|||||||||||||
кал; к и |
в н у т р е н н и х |
п о в е р х |
не |
10 в |
сторону. Нагретый |
цилиндр |
||||||||
н о с т е й ц и л и н д р о в |
показано на |
надевается на оправку, поворотная го |
||||||||||||
рис. 6. 24. Нагретый цилиндр устанав |
ловка 8 надвигается на цилиндр и в- |
|||||||||||||
ливается на специальную оправку 5, |
верхнюю часть нижнего 1 и верхнего |
|||||||||||||
представляющую собой полую цилинд |
9 |
пневматических |
цилиндров |
пускает |
||||||||||
рическую |
шестерню |
высотой, |
равной |
ся |
сжатый |
воздух. Верхний |
поршень |
|||||||
высоте |
закаливаемого цилиндра. Оп |
с помощью головки 5 зажимает зака |
||||||||||||
равка |
|
разрезана |
радиально |
на |
ряд |
ливаемую деталь с торцов, а шток ниж |
||||||||
секций, |
которые стянуты |
поршневыми |
него цилиндра 1 равномерно распи |
|||||||||||
кольцами 4, заложенными в прорезях |
рает внутреннюю поверхность цилинд |
|||||||||||||
с торцов тела оправки. Внутри пос |
ра на оправке 5. Через питающую тру |
|||||||||||||
ледней ходит стержень 6, имеющий |
бу 5 и кольцевую щель 2 подается под. |
|||||||||||||
две конусные направляющие. При пус |
давлением |
масло, |
которое |
проходит |
||||||||||
ке сжатого воздуха в верхнюю часть |
/между |
зубьями оправки, охлаждает |
||||||||||||
нижнего воздушного |
цилиндра 1 пор |
внутреннюю поверхность закаливаемо |
||||||||||||
шень тянет стержень вниз и его конус |
го цилиндра и сливается вверху в от |
|||||||||||||
ные |
направляющие |
раздвигают |
оп |
водящую трубу 7. Таким образом осу |
||||||||||
равку. |
|
|
|
|
|
|
|
ществляется |
равномерное охлаждение |
при закалке |
внутренней |
поверхности |
перегрев жидкости и образование па- |
||||||||||||
цилиндра |
в зажатом состоянии. |
|
ровой рубашки. |
|
|
|
|
|
|||||||
|
|
|
|
|
|
|
|
При закалке с нагревом т. в. ч. час |
|||||||
6.4. СПРЕЙЕРНЫЕ УСТАНОВКИ |
|
то применяют индуктор-спрейер, |
с |
||||||||||||
ДЛЯ ОХЛАЖДЕНИЯ ДЕТАЛЕЙ |
|
'помощью которого изделие |
сначала |
||||||||||||
Одним |
из перспективных |
способов |
нагревают, а потом охлаждают. Его |
||||||||||||
используют, |
например, |
при |
закалке |
||||||||||||
охлаждения |
при термической |
обработ |
зубьев шестерен (см. рис. |
5. |
13), |
не |
|||||||||
ке является струйное охлаждение во |
прерывно-последовательном |
нагреве |
|||||||||||||
дой, подаваемой под давлением на |
валов |
(см. рис. 5. |
12), рельсов и др. |
||||||||||||
охлаждаемую поверхность изделия с |
|
Струйное устройство для непрерыв |
|||||||||||||
помощью спрейерных устройств и фор |
но-последовательного охлаждения рель |
||||||||||||||
сунок. При этом достигается более |
сов, нагреваемых т. в. ч., состоит из |
||||||||||||||
интенсивный отвод тепла от нагретых |
пяти |
многосопельных форсунок. Каж |
|||||||||||||
изделий, чем в закалочных баках. Для |
дая форсунка имеет коллектор 3 дли |
||||||||||||||
повышения |
равномерности охлажде |
ной 500 мм с 10 соплами, расстояние |
|||||||||||||
ния изделия вращают. Струйное ох |
между ними равно 50 мм (рис. 6.25, а) . |
||||||||||||||
лаждение |
широко |
применяется |
при |
Вода в сопло 7 подается по внутрен |
|||||||||||
закалке после горячей прокатки лис |
ней |
трубе 4 |
коллектора |
форсунки и |
|||||||||||
тов и нагрева поверхности т. в. ч. при |
распыляется |
воздухом, |
поступающим |
||||||||||||
индивидуальной закалке труб, прутков, |
из |
наружной |
трубы 5 |
через |
ряд |
от |
|||||||||
рельсов; сорбитизации поверхности ка |
верстий 6, расположенных с наклоном |
||||||||||||||
тания колес, бандажей, роликов. |
|
в сторону движения воды. Вода в фор. |
|||||||||||||
В качестве охлаждающей среды ча |
сунку |
подводится |
под |
избыточным |
|||||||||||
сто используют водовоздушную смесь. |
давлением 0,05 МПа по трубе 1 диа |
||||||||||||||
Меняя количество подаваемого возду |
метром 15 мм, а воздух подается под |
||||||||||||||
ха, давление |
воды |
и воздуха, можно |
давлением 0,2 МПа по трубе 2 диа |
||||||||||||
получить различный теплоотвод и, сле |
метром 25 мм. |
|
устройство |
для |
не |
||||||||||
довательно, |
различную |
скорость |
ох |
Водовоздушное |
|||||||||||
лаждения изделий. При водовоздушном |
прерывно-последовательного охлажде |
||||||||||||||
охлаждении поверхность изделия омы |
ния листов толщиной 10—40 мм пока |
||||||||||||||
вается водяной пылью, что исключает |
зано на рис. 6. 25, б. В направлении дви- |
ч |
|
т |
| L |
4. |
|
S3 |
/Ц уж |
Вода ^ I L |
Рис. 6.25. Струйные устройства для охлаждения изделий
жения сверху и снизу листа устанав |
ных дуостанов 1 и системы охлаждаю |
||||||||||||
ливается по шесть-семь коллекторов 1 |
щих форсунок 2. |
|
|
водой, пода |
|||||||||
с шагом 0,5—0,8 м. В каждом из них |
Струйное охлаждение |
||||||||||||
через ~0,2 |
м размещаются |
форсунки. |
ваемой |
под давлением, |
применяется |
||||||||
При ширине листов 3,6 и 1,6 м в кол |
в роликозакалочной |
машине при |
за |
||||||||||
лекторе их помещается соответственно |
калке листов толщиной 5—50 мм и |
||||||||||||
16 и 7 шт. Форсунки располагаются |
шириной до 3,2 м. Закалочная машина |
||||||||||||
от поверхности листа на 0,5 м, верхние |
состоит из 23 пар нижних и верхних |
||||||||||||
устанавливаются под углом 45°. При |
роликов диаметром 300 мм с электро |
||||||||||||
этом длина эффективного охлаждения |
приводом. Между роликами сверху и |
||||||||||||
листа составляет 3—4 м. Воздух под |
снизу по ширине листа коллекторами |
||||||||||||
давлением 0,05—0,6 МПа подается в |
диаметром 66 мм подводится охлаж |
||||||||||||
форсунку по осевому патрубку 4, а |
дающая вода. Каждый коллектор имеет |
||||||||||||
вода по трубе 5 и каналу диаметром |
восемь форсунок с овальным выход |
||||||||||||
8 мм в кольцевую выточку 3 диамет |
ным сечением 6X8 мм, расположен |
||||||||||||
ром 14 мм. Воздух, поступая с высо |
ных от поверхности листа на расстоя |
||||||||||||
кой скоростью, захватывает воду и |
нии ~200 |
мм. Давление |
воды состав |
||||||||||
образует в камере 2 диаметром 11 мм |
ляет 0,6—0,8 МПа. Снизу листа подает |
||||||||||||
дисперсную водовоздушную смесь, нап |
ся большее количество воды. Скорость |
||||||||||||
равленную на поверхность листа. Ско |
движения листа |
0,1 м/с. |
|
|
|
||||||||
рость |
охлаждения |
регулируется |
от |
На рис. 3. 27, б изображен пресс |
|||||||||
0,05 до 0,4 м3/ч при расходе воздуха |
для закалки листов шириной до 2,6 м |
||||||||||||
20—25 м3/ч. |
|
охлаждения реко |
и длиной до 12 м после их нагрева в |
||||||||||
Для |
улучшения |
роликовой печи. Струйное охлаждение |
|||||||||||
мендуется |
водовоздушную |
смесь |
по |
производится через сопла (узел а) |
|||||||||
давать с помощью центробежных фор |
водой под давлением 0,3—0,4 МПа. |
||||||||||||
сунок 2, диаметр выходного отверстия |
Расход |
воды на |
закалку |
составляет |
|||||||||
которых равен 5 мм, а угол рабочего |
25 м3/мин. Сила зажатия листа в прес |
||||||||||||
конуса |
а=60° (рис. 6. 25, в). Форсун |
се 100 т. |
|
|
|
воды охлаж |
|||||||
ки снабжаются шайбой 1, имеющей |
Встречным потоком |
||||||||||||
центральное отверстие диаметром |
3— |
даются прутки диаметром 20—40 мм, |
|||||||||||
3,5 мм и два периферийных отверстия |
двигающиеся со скоростью 3—5 м/с |
||||||||||||
диаметром 2,6—2,8 мм, расположенных |
после |
горячей |
прокатки. |
Установка |
|||||||||
под углом |
16° к оси центрального |
от |
имеет общую длину 72 м и состоит из |
||||||||||
верстия. Такая форсунка, |
находящая |
19 последовательно |
расположенных с |
||||||||||
ся от поверхности листа на расстоянии |
небольшими промежутками |
труб |
диа |
||||||||||
150—250 мм, при давлении подавае |
метром |
100 мм, длиной по 3 м. Избы |
|||||||||||
мой смеси 0,15—0,3 МПа дает' зону |
точное давление воды 0,1—0,3 МПа, |
||||||||||||
орошения 160—260 мм. При давлении |
расход ее составляет 6—7 м3/мин. Для |
||||||||||||
водовоздушной смеси 0,3 МПа ко |
прутков диаметром |
более |
20 мм |
не |
|||||||||
эффициент |
теплоотдачи |
достигает |
обходимо |
применять |
прерывистое |
ох |
|||||||
8000 Вт/(м2-К). |
|
|
|
лаждение. |
При |
обработке |
фасонного |
||||||
На рис. 6. 26 показана установка |
проката используют дифференцирован |
||||||||||||
для закалки и сорбитизации толстых |
ное охлаждение массивных частей про |
||||||||||||
листов, состоящая |
из ряда правиль |
филя. Например, для охлаждения угол- |
ка поток воды следует направлять на |
количество сопел 4, которые направ |
|||||||||||
его внутреннюю часть, а не на весь |
ляют струи воды по касательной к |
|||||||||||
уголок. |
|
|
|
|
ободу |
колеса. |
Использованная |
вода; |
||||
На рис. 6. 27 показаны два устрой |
сливается в |
кольцевой бак 7 и дал^е |
||||||||||
ства для непрерывно-последовательно |
в канализацию оборотной воды. Для |
|||||||||||
го охлаждения труб. Первое устрой |
удобства загрузки колес на закалоч |
|||||||||||
ство |
с водовоздушным |
охлаждением |
ный стол кольцевая коробка с сопла |
|||||||||
(рис. 6. 27, а) представляет собой ме |
ми при помощи пневматического цн- |
|||||||||||
таллический цилиндр 2, в котором ук |
линдра 1 опускается в положение, обоз |
|||||||||||
репляется ряд форсунок 1, наклонен |
наченное штрихами. |
|
|
|||||||||
ных к выходу в сторону движения сме |
Обод железнодорожных колес сор- |
|||||||||||
си. |
Вода |
подается |
в |
центральный |
битизируют |
в |
вертикальном положе |
|||||
канал 3 форсунки, а в кольцевое про |
нии (рис. 6. 28, б). Колесо устанавли |
|||||||||||
странство 4 поступает воздух под дав |
вается |
в бак |
1 |
на |
ролики |
2, 3, 4. р 0_ |
||||||
лением 0,2—0,3 МПа, который на вы |
лик 4 приводится во вращение, и коле |
|||||||||||
ходе сопла 5 распыляет воду. Отрабо |
со под действием трения также начи |
|||||||||||
танная вода отводится в сливной бак. |
нает вращаться. Уровень воды в баке |
|||||||||||
Во втором устройстве с водяным |
поддерживается |
несколько выше |
обо |
|||||||||
охлаждением (рис. 6. 27, б) вода на |
да. При вращении колеса происходит |
|||||||||||
сосом 1 подается в кольцевой канал 2 |
сорбитизация обода, а втулка и диск |
|||||||||||
и, выходя из сопла, омывает охлаж |
охлаждаются |
на воздухе. |
|
|
||||||||
даемую трубу. Отработанная вода сли |
|
|
|
|
|
|
|
|||||
вается в бак 3, из которого по трубо |
|
6.5. |
|
|
ОБОРУДОВАНИЕ |
|
||||||
проводу отсасывается насосом 1. Рас- |
ДЛЯ ГЛУБОКОГО ОХЛАЖДЕНИЯ |
|
||||||||||
'ход |
оборотной <воды |
составляет 5— |
|
(УСТАНОВКИ ДЛЯ ОБРАБОТКИ |
|
|||||||
7 м3/мин. |
|
|
|
|
|
|
ХОЛОДОМ) |
|
|
|||
На рис. 6. 28 показаны две уста |
|
|
|
|
||||||||
|
|
|
|
|
|
|
||||||
новки для сорбитизации колес. Пер |
Глубокое |
охлаждение |
при терми |
|||||||||
вая установка (рис. 6. 28, а) |
представ |
ческой |
обработке |
используется |
для |
|||||||
ляет собой вращающийся горизонталь |
разложения остаточного |
аустенита в |
||||||||||
ный стол. После нагрева колесо 3 ус |
закаленных |
высоколегированных |
ин |
|||||||||
танавливается втулкой в гнездо 2 и |
струментальных и цементируемых ста |
|||||||||||
стол приводится во вращение частотой |
лях с целью повышения твердости и |
|||||||||||
1/2 с-1 от |
электродвигателя |
9 через |
стабилизации |
размеров обрабатывае |
||||||||
пару конических передач 6 и редуктор |
мых деталей. Для этого детали погру. |
|||||||||||
8. Поверхность катания колеса охлаж |
жают в среду с низкой температуру |
|||||||||||
дается водой, подаваемой через коль |
и выдерживают в ней. При охлажде. |
|||||||||||
цевую коробку 5, имеющую |
большое |
нии ниже мартенситной точки Мн оС- |
таточный |
аустенит превращается в |
Обработка холодом должна сразу |
|||||
мартенсит. |
Применение |
очень низких |
следовать за закалкой, так как в боль |
||||
температур |
(—170 °С) |
часто обуслов |
шинстве сталей выдержка при темпе |
||||
ливает потерю вязких свойств металла |
ратуре 20 °С или низкий отпуск перед |
||||||
и образование трещин. Поэтому изде |
обработкой холодом приводит к ста |
||||||
лия следует охлаждать только до тем |
билизации |
содержания |
остаточного |
||||
пературы, при которой распад остаточ |
аустенита. Часто отрицательные |
тем |
|||||
ного аустенита приостанавливается |
пературы используются при испытани |
||||||
(точка Мк). Для значительного числа |
ях механических свойств и определе |
||||||
промышленных сталей точка Мк наб |
нии порога |
^хладноломкости. Иногда |
|||||
людается при температуре от —60 до |
обработку |
холодом |
применяют |
для |
|||
—100 °С. Чтобы уменьшить внутренние |
уменьшения диаметра деталей при их |
||||||
напряжения, после обработки холодом |
сопряжении |
с другими |
деталями |
(на |
|||
необходимо сразу же производить от |
пример, при посадке на вал муфт, на |
||||||
пуск. |
|
|
колеса — бандажей |
и т. п.) |
|
||
v |
|
|
|
|
|
|
|
|
|
|
СО |
Теплоем |
|
|
|
|
|
при0°С кг/м* |
и |
|
|
||
|
|
и |
кость при |
|
|
||
|
|
со |
0°С |
и |
Температура |
||
|
|
5 |
|||||
|
Хими |
« |
0,1МПа, |
при 0,1 МПа, °С |
|||
Хладагент |
СО |
кДж/(кг*К) |
|
|
|||
ческая |
Плотность 0,1иМПа,, |
Я |
|
|
|
|
|
|
формула |
£ |
|
|
|
|
|
|
|
К |
|
|
|
|
|
|
|
|
■5 |
|
|
|
|
|
|
|
►» |
|
|
кипе |
плав |
|
|
|
Я |
ср |
cv |
||
|
|
|
<и |
ния |
ления |
||
|
|
|
ч |
|
|
||
|
|
|
о |
|
|
|
|
Аммиак |
NH3 |
0,77 |
17,0 |
2 ,2 2 |
1,67 |
- 3 3 ,4 |
—77,1 |
Пропан |
С3Н8 |
2 ,0 2 |
44,1 |
1 ,8 8 |
1,64 |
—42,1 |
— 188 |
Фреон 22 |
CHF2C1 |
3,85 |
86,5 |
— |
— |
—40,8 |
— 160 |
Этан |
с2нв |
1,36 |
30,0 |
1,72 |
1,46 |
— 88,5 |
— 184 |
Этилен |
С2Ни |
1,26 |
28,0 |
1,55 |
1 ,2 2 |
— 109 |
- 1 0 4 |
Фреон 13 |
CF3C1 |
4,60 |
104 |
— |
— |
- 8 1 ,5 |
— 181 |
Метан |
СН4 |
0,72 |
16,0 |
2 ,2 2 |
1,67 |
— 162 |
- 1 8 3 |
Жидкий: |
N2 |
|
28,0 |
|
|
— 196 |
|
азот |
1,25 |
1,05 |
0,75 |
- 2 1 0 |
|||
воздух |
02 |
1,29 |
29,0 |
1 ,0 0 |
0,71 |
- 1 9 5 |
— |
кислород |
1,43 |
32,0 |
0,92 |
0,84 |
— 183 |
—219 |
и<Теплота:парения кипенприИИ и МПа,0,1Iккал/кг |
• |
кг/м*сти, |
Темпе С°ратура, |
Давление в |
|
Плотность |
|
||||
|
о |
|
Критиче |
|
|
|
я |
|
|
||
|
•ч |
ская точка |
|
||
|
я |
|
|
|
Область • |
|
* |
|
|
МПа0,1 |
примене |
|
|
|
|
ния |
|
|
|
|
|
|
|
|
|
. |
|
|
|
328 |
683 |
4-132 |
1 1 1 |
Д о |
|
°С |
1 0 2 |
582 |
+ 9 6 |
43 |
- 5 0 |
|
|
— |
— |
+ 9 6 |
50 |
|
|
|
116 |
546 |
+ 3 2 |
48,9 |
До |
о о О |
|
115 |
610 |
+ 9 ,7 |
50,7 |
1 |
||
— |
400 |
+ 2 9 |
39,4 |
|
|
|
1 2 2 |
424 |
- 8 2 |
45,6 |
Д о |
|
°С |
|
|
|
|
- 1 7 0 |
||
48 |
808 |
- 1 4 7 |
33,5 |
Д о |
|
°С |
47 |
861 |
-1 4 1 |
37,2 |
- 1 9 0 |
||
51 |
1140 |
- 1 1 9 |
49,7 |
|
|
|
Для обработки холодом используют |
ется сухим хладагентом. Для достиже |
|||||
установки, работающие |
на |
твердой |
ния |
большей равномерности темпера |
||
углекислоте, жидких хладагентах (кис |
туры внутрь камеры часто вводят |
|||||
лороде, азоте или воздухе), механи |
жидкую среду, температура затверде |
|||||
ческие каскадные холодильные маши |
вания которой ниже температуры воз |
|||||
ны и турбодетандеры. Применяемые |
гонки твердой углекислоты (например, |
|||||
хладагенты приведены в табл. 6.3. |
денатурированный спирт). Детали ох |
|||||
У с т а н о в к и , |
р а б о т а ю щ и е |
лаждаются в 'этой среде. |
|
|||
на т в е р д о й у г л е к и с л о т е , да |
на |
У с т а н о в к и , р а б о т а ю щ и е |
||||
ют температуру охлаждения до —78 °С. |
ж и д к о м х л а д а г е н т е |
(кис |
||||
Такая установка состоит из наружного |
лороде, азоте или воздухе), дают тем |
|||||
кожуха с хорошей теплоизоляцией, в |
пературу до —170 °С. Одна из |
таких |
||||
крышку которого |
вставлен |
медный |
установок изображена на рис. 6. 29. |
|||
сосуд. Последний |
служит |
охлаждаю |
Она состоит из охладительной камеры, |
|||
щей камерой. Пространство между ка |
бака для хранения жидкого хладаген |
|||||
мерой и наружным |
кожухом заполня |
та и щита управления. Охладительная |
ХХЛаЛЛЛ"
f 6 7
|
1 |
1 |
|
|
и |
- |
|
_ , |
| |
HI--- |
|
|
i |
|| |
|
|
1 |
11 |
Чч' |
|
1 |
II |
|
|
1 |
S |
|
|
1 |
|
|
|
1 |
|
а У'V-U? |
---------h - |
|
Ф Ш
н
Рис. 6.29. Установка для обработки холодом, работающая на жидком хладагенте

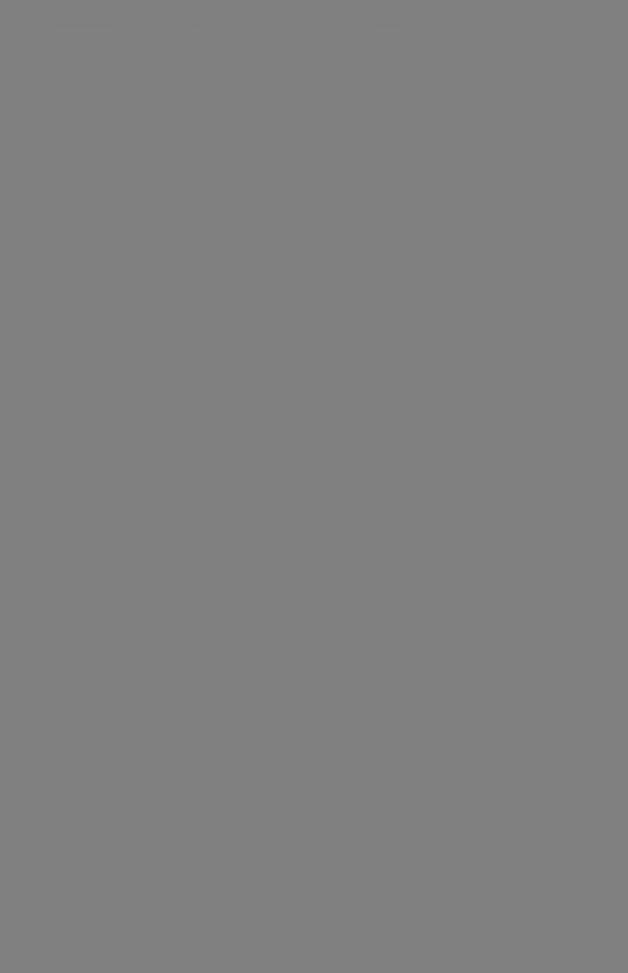
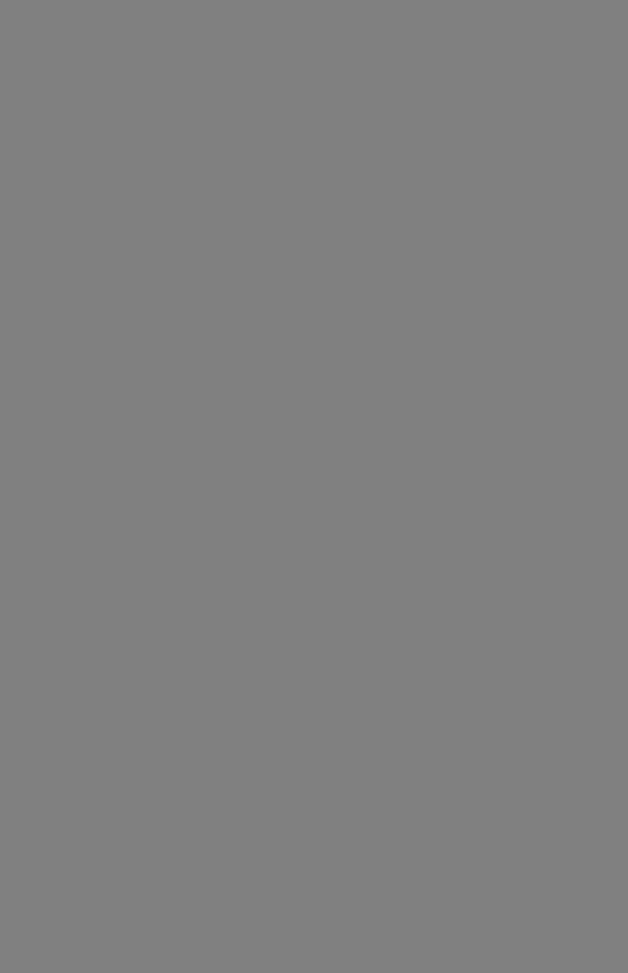
высыпаются на конвейер закалочного бака (см. рис. 3.3, в). При нагреве тя жёлых деталей ленту конвейера от пускной печи следует выполнять из усиленных литых звеньев (см. рис. 3.13, б).
7.3. ПОТОЧНЫЕ ТОЛКАТЕЛЬНЫЕ АГРЕГАТЫ
ДЛЯ ГАЗОВОЙ ЦЕМЕНТАЦИИ (НИТРОЦЕМЕНТАЦИИ)
В состав агрегатов, в зависимости от технологии, входит следующее обо рудование: безмуфельная печь для га зовой цементации (нитроцементации), механизированный закалочный бак или коридор для охлаждения в контроли руемой атмосфере, моечно-сушильная машина, отпускная печь и транспорт ные средства.
Наиболее широко применяются замкнутые агрегаты П-образной или Ш-образной планировкой, в которых поддоны расположены в один или два ряда. В однорядных печах с газовым отоплением радиационные трубы раз мещают вертикально вдоль стенок пе чи. В двухрядных печах их располага ют горизонтально над и под изделиями (см. рис. 1.5,6). При газовом отопле нии чаще используют трубы U-образ- ной формы.
На рис. 7.3 показана схема разме щения оборудования основных типов цементационных толкательных агрега
тов с печами на газовом отоплении конструкции ЗИЛ.
Наиболее компактным является це ментационный агрегат с нагревом вер тикальными радиационными трубами ц непосредственной закалкой после подстуживания (рис. 7.3, а). В первой ли нии агрегата размещаются цементаци онная печь 1, закалочный бак 2 с горя чим маслом и передаточный бак 3 с холодным маслом. Во второй линии -ч-. моечная машина 4, камера сушки сжа тым воздухом 5, отпускная печь 6 и участок с шаговым конвейером для разгрузки и загрузки поддонов.
Для цементации деталей с непо средственной закалкой применяются также однорядный 12-поддонный и двухрядный 48-поддонный агрегаты конструкции ЗИЛ.
Стали, которые нельзя непосредст венно закаливать после цементации, обрабатывают в агрегатах с охлади тельным коридором, имеющим контро лируемую атмосферу. Таким является 18-поддонный агрегат, изображенный на рис. 7.3, б.
Высоколегированные стали цемен тируют с полным циклом термической обработки. В 24-поддонных агрегатах с горизонтальными U-образными ра диационными трубами (рис. 7. 3, г) де тали после цементации в печи 1 ох лаждаются в коридоре 7, нагреваются для закалки в печи 8, охлаждаются в баке 2 и через передаточный конвейер
Рис. 7.3. Размещение рборудования в цеменгационных агрегатах с печами, работающими на газовом отоплении:
^ |
цементационная печь; 2 — закалочный |
бак; 3 |
— передаточный бак с холодным маслом; |
4 — моечная машина; 5 — сушилка сжатым |
воздухом; 6 — отпускная печь; 7 — охладитель |
||
|
ный коридор; 8 — закалочная печь; |
9 — передаточный конвейер |
зж а
Рис. 7.4. Размещение оборудования в цементационных агрегатах с элек трическими печами:
1 — охладительный коридор; 2 — печь для низкого отпуска; 3 — моечно-сушиль ная машина; 4 — закалочный бак; 5 —• печь для цементации; 6 — печь для нагре ва под закалку; 7 — печь для высокого отпуска; 8 — передаточный конвейер
|
|
|
|
|
Число |
поддонов |
|
|
|
|
Расход газа, |
м*/ч |
|
|
|||
|
|
|
|
|
|
в печах |
|
|
|
карбюризатора |
|
|
|
||||
Тип агрегата |
|
|
to S |
|
|
сс |
|
Габариты, |
|
|
|
|
|
|
|
|
|
|
|
|
|
X |
|
|
о |
|
|
|
|
|
|
|
|
|
|
|
|
|
22 |
|
|
аз |
|
|
|
|
|
|
|
|
|
|
|
|
|
;S i m ж |
|
|
т |
|
|
|
|
|
|
|
|
|
|
||
|
|
|
_ ю |
|
|
ч |
|
|
|
|
|
|
|
|
|
|
|
|
|
|
5 ° |
|
|
|
|
|
|
|
|
|
|
|
|
||
|
|
|
|
|
2 в |
о |
|
|
|
|
|
|
|
|
|
|
|
|
|
Се |
2 |
аз |
|
|
|
|
I s |
|
|
|
|
|
|
||
|
|
OI о |
« |
о |
|
|
|
|
|
|
|
|
|
|
|||
|
|
|
|
и |
к |
|
|
|
|
|
|
|
|
|
|
||
|
Электрический нагрев (агрегаты конструкции ЭТО) |
|
|
|
|
|
|||||||||||
СТЦА-•5.60.5/3-П1 |
635 4<)<J 15 |
|
14 |
— |
1 2 |
7,1X15,3X6.0 |
|
135 |
38 |
9 |
— |
4 |
— |
8 6 |
|||
СТЦА' 5.80.5/3-П1 v |
517200 |
|
30 |
|
18 |
5 |
8 |
11,5X17,8X7,1 |
|
140 |
60 |
1 0 |
— |
— |
— |
115 |
|
СТЦА- 10.60.5/3-П2 |
757 300 |
|
2 0 |
|
30 |
— |
15 |
7,8X15,3X6,0 |
|
135 |
60 |
1 0 |
— |
4 |
— |
93 |
|
СТЦА- 10.100.5/3-П2 |
1000 400 |
|
15 |
|
44 |
6 |
1 2 |
7,3X29,7X6,0 |
|
146 |
108 |
1 2 |
— |
4 |
— |
136 |
|
СТЦА- 10.100.5/3-П2 |
600400 |
|
15 |
|
42 |
— |
— |
6,9X22,3X5,2 | |
80 |
81 |
6 |
— |
4 |
— |
8 8 |
||
СТЦА- 10.60.5/7-Л2л/ |
616 400 |
|
15 |
|
28 |
— |
28 |
8,6X33,2X4,9 |
! |
93 |
60 |
1 0 |
40 |
— |
— |
135 |
|
СТЦА- 5.100.5/7-Ш1 |
1100 350 |
|
17 2 2 - 2 |
— |
2 2 |
15,2X22,4X6,0 |
|
123 |
1 2 0 |
30 |
60 |
— |
— |
236 |
|||
СТЦА- 10.100.5/7-Ш2 ,1080 600 |
|
1 0 |
44*2 |
— |
44 |
17,4X22,1X4,7. |
93 |
142 |
1 0 |
56 |
— |
— |
205 |
||||
СТЦА- 5.100.5/3-П1 |
11030,200 |
|
30 |
|
2 2 |
1 0 |
14 |
10,8X33X7,1 |
1130 |
1 0 2 |
1 0 |
48 |
— |
— |
140 |
||
|
|
Газовый нагрев |
(агрегаты конструкции ЗИЛ) |
|
|
|
|
|
|
||||||||
ЗИЛ-12-П1 |
— |
1 2 0 |
|
50 |
|
1 2 |
— |
6 |
5,0X12,6X6,4 |
|
84 |
18 |
1,5 |
— |
1 .0 |
75 |
— |
|
|
|
|
|
|
|
|
|
|
|
|
|
|
||||
ЗИЛ-18-П1 |
— |
2 0 0 |
|
30 |
|
18 |
— |
— |
4,1X16,8X6,2 |
|
82 |
25 |
2 .0 |
— |
1,5 |
85 |
— |
ЗИЛ-21-Г11 |
— |
250 |
|
25 |
|
21 |
— |
9 |
5,0X16,3X6,5 |
|
84 |
60 |
2 .0 |
— |
1 ,0 |
1 2 0 |
— |
ЗИЛ-28-П2 |
— |
400 |
|
15 |
|
28 |
2 2 |
14 |
8,0X20,8X6,4 |
|
1 0 0 |
50 |
2,5 |
— |
— |
130 |
— |
ЗИЛ-48-П2 |
— |
500 |
|
12 |
|
48 |
— |
1 2 |
8,8X19,5X6,0 |
|
90 |
45 |
3,0 |
— |
1,5 |
180 |
— |
ЗИЛ-24-П1 |
— |
300 |
2 0 |
|
24 |
3 |
8 |
11,5X22X3,5 |
|
74 |
70 |
3,0 |
1 2 0 |
— |
150 |
— |
П р и м е ч а н и я : 1. Производительность агрегатов дана при цементации на глубину 0,8—1,2 |
мм, при ни* |
||
троцементации на |
глубину 0,5—0,7 мм производительность |
агрегатов возрастает в 1 ,&—1,6 раза |
конструкции |
2. В агрегатах |
конструкции ЭТО применяются поддоны |
размерами 0,5X0,5 м; а в агрегатах |
ЗИЛ поддоны имеют размеры 0,6x0,4 м. Маса поддона составляет 50 кг, нагрузка на него равна 100—120 м.
9, моечную машину 4 и камеру сушки 5 поступают для отпуска в печь 6. Пос ле отпуска поддоны разгружаются, за полняются новыми деталями и цикл повторяется.
В |
28-поддонном |
агрегате |
(рис. |
7.3, в) |
оригинальным |
является |
совме |
щение высокого отпуска и последую щего нагрева под закалку в печи 8.
Планировка цементационных агре гатов заводов ЭТО с электрическим на гревом показана на рис. 7. 4. Непосред ственная закалка после цементации ис пользуется в двухрядном агрегате СТЦА-10.60.5/3 (рис. 7.4, а).
Стали, которые нельзя непосредст венно закаливать после цементации, обрабатывают в агрегате СТЦА-20.100.
5/10 с охладительным |
коридором |
(рис. 7.4, б). |
стали |
Высоколегированные |
20Х2Н4А и 18Х2Н4ВА после цемента ции подвергают только высокому от пуску или полной термической обработ ке. Агрегат СТЦА-5.100.5/3-П7Л для полной термической обработки показан на рис. 7.4, в. Поддоны загружаются на участке 8, проходят моечно-сушиль ную машину 3 и однорядную электро печь газовой цементации 5 и через ох
ладительный коридор 1 поступают в электропечь 7 для высокого отпуска, затем охлаждаются в камере 1. Затем поддоны с изделиями нагреваются в закалочной печи 6, охлаждаются в ба ке 4, проходят моечно-сушильную ма шину 3, печь низкого отпуска 2 и раз гружаются на участке 8.
Ш-образный агрегат СТЦА-20.100. 5/7, в котором детали после цементации подвергаются только высокому отпус ку, показан на рис. 7.4, г. Агрегат вклю чает две цементационные печи 5 и одну отпускную 7.
Основные характеристики цемента ционных агрегатов приведены в табл. 7.2.
Для повышения производительнос ти цементационной печи целесообраз но увеличивать число рядов поддонов, а не ее длину. На ЗИЛ работает четы рехрядная цементационная печь 20Х Х 4= 80 поддонов. Печь нагревается горизонтальными U-образными радиа ционными трубами, расположенными в два ряда по высоте и в два ряда по ши рине печи. Однако в таком агрегате за трудняются загрузка и выгрузка поД* донов.
При многорядном расположении
824 Vs8
В
Рис. 7.5. Высокопроизводительный аг регат для газовой цементации (нитро цементации) с двухэтажным располо жением оборудования
поддонов целесообразнее применять двухэтажные цементационные агрега ты, замыкая путь поддонов по верти кали. Тогда они будут приводиться в движение только гидравлическими подъемниками и толкателями. На рис. 7.5 приведена схема такого агрегата. Поддон с деталями загружают сверху
втамбур 4, герметичность которого обеспечивается крышкой 5 и подъемной платформой 3 с песочными затворами. От печи тамбур отделяется клиновой задвижкой 6. Поддоны приводятся в движение гидравлическим толкателем 2. Детали, пройдя печь, опускаются на платформе 7 в закалочный бак 9. По сле закалки платформа поднимается на уровень первого ряда агрегата, поддо ны с помощью толкателя 8 продвига ются через моечно-сушильную камеру 10 и отпускную печь 11. После отпуска вытаскиватель 1 подает поддон на платформу 3, которая поднимается в тамбур 4. Конструкция печи значитель но упростится, если после цементации
вагрегате детали проходят только вы сокий отпуск.
7.4. ПОТОЧНЫЕ ЛИНИИ БАРАБАННОГО ТИПА
Для нагрева мелких деталей — ро ликов, шариков, болтов, гаек — приме няют линии с барабанными печами, за калочными баками и моечными маши нами.
На рис. 7.6 изображена типовая линия, состоящая из барабанной зака лочной печи 5, закалочного бака со шне ковым конвейером 4, барабанной моеч ной машины 5 и отпускной печи 7. Де тали скиповым подъемником 1 загру жаются в распределительный бункер 2, из него в реторту закалочной печи. По сле окончания нагрева они попадают через отверстие реторты в лоток зака лочного бака и шнековым конвейером 4 подаются в моечную машину 5. Из реторты моечной машины детали сбра сываются в распределительный бункер, из которого поступают в шнек отпуск ной печи 7. В отпускной печи они на греваются горячим воздухом, подогре ваемым в калорифере 8 и циркулирую щим с помощью центробежного венти лятора 6. Барабан закалочной печи, шнековые конвейеры моечной машины, отпускной печи и закалочного бака вра щаются от электродвигателей 9, 11, 12 через редукторы и цепные передачи.
Щелочный раствор моечной машины циркулирует при помощи насоса 10. Основные характеристики барабанных печей приведены в табл. 3. 8.
В линии с барабанными печами по сле закалочного бака иногда устанав ливают галтовочный барабан для очи стки шариков от окалины и коэрцитиметр для контроля твердости и струк туры. Часто в линии с барабанными закалочными печами для отпуска дета лей (роликов, колец) применяют кон вейерную печь с вентиляторами.
При изготовлении шариков и роли ков из цементируемых сталей для про цесса цементации используют барабан ную печь с непосредственной закалкой. Такая линия СБЦА состоит из бара банной электропечи для цементации (см. рис. 3.38, б), бака со шнековым конвейером, моечной барабанной ма шины и барабанной отпускной электро печи (см. рис. 3.38, а).
7.5. РОТОРНЫЕ ПОТОЧНЫЕ ЛИНИИ
Роторные поточные линии включа ют печи, нагревательные установки, за калочные и моечные машины, конт рольные аппараты карусельного типа. Рабочие роторы линии объединяются в один общий поток транспортными ро торами.
Схема роторной линии для обработ ки тонких колец приведена на рис. 7.7, а. Кольца из круглого бункера-накопи теля 9 поступают в ротор 8 индукцион ного нагрева с двумя позициями. Ро тор поворачивается на 180°, и нагретые кольца передаются транспортным ро тором 7 под пресс закалочной машины 6, имеющей четыре позиции. После ох лаждения колец ротор машины пово рачивается на 90° и транспортный ро тор 5 передает кольца в отпускную печь 4. Ротор 5 имеет две позиции для от мывки колец от масла водным раство ром щелочи. Карусель отпускной печи рассчитана на восемь электрических прессов, поэтому за каждый цикл она поворачивается на 45°. Из электропрес са отпускной печи кольца транспорт ным ротором 3 передаются в контроль ный роторный автомат 2. На двух пози циях транспортного ротора 3 они охла ждаются водой и подсушиваются горячим воздухом. В роторе 2 на одной позиции контролируется твердость, а на второй — коробление колец. Далее кольца направляются в приемный ро-
Рис. 7.6. Поточная линия с барабанными печами для термической обработки мелких деталей

непрерыв |
стальной |
7.8. Поточная линия для |
отжига холоднокатаной |
Рис. |
ного |
очень большую длину. На основании практических данных установлено, что длина ленты в горизонтальной печи должна быть не более 150—200 м, а скорость не выше 100 м/мин. В этом случае производительность печи со ставляет около 10—15 т/ч. При более высоких скоростях движения лента со скальзывает с барабанов.
С целью экономии места протяжные горизонтальные печи делаются с трех рядным движением ленты по высоте печи. Такие печи для отжига широкой ленты достигают в длину 120 м и боль ше.
Однако меньшую площадь занима ют вертикальные (башенные) печи, об ладающие большей герметичностью. Лента в таких печах делает ряд оборо тов, огибая верхние и нижние направ ляющие ролики. Благодаря большому углу охвата роликов лента хорошо цен трируется, что позволяет увеличить скорость ее движения до 600 м/мин. Такие печи экономичны только при больших скоростях движения ленты (свыше 150 м/мин).
Башенные отжигательные печи име ют несколько температурных зон: на грева, выдержки, замедленного и уско ренного охлаждения. Поточная линия, кроме печи, включает разматывающие и наматывающие барабаны, сварочную машину, ножницы, очистные, промыв ные и сушильные устройства, тянущие ролики и башни запаса.
На рис. 7.8 приведена конструкция поточной линии с вертикальными печа ми для непрерывного отжига холодно катаной стальной ленты в контроли руемой атмосфере. В печи осуществлен принцип рекуперации тепла: для подо грева поступившей в печь ленты ис пользуется тепло охлаждающейся лен ты, что позволяет значительно (до 40 %) сократить расход энергии на на грев металла. Холоднокатаная лента
сразматывающих барабанов 1 прохо дит через сварочную установку 2, на правляющий ролик 3, блок 4 (верти кального регулятора ленты), промыв ные ванны 5, 6 и сушильную камеру 7
спомощью тянущих роликов 24 и 23 в вертикальную башню запаса ленты 8. Башня запаса представляет собой ка меру прямоугольного сечения с рядом неподвижно укрепленных (вверху) и
свободных (внизу) роликов, на которых петлеобразно натянута лента. При со кращении длины ленты нижние ролики
подтягиваются к верхним. Из башни запаса лента по траншее попадает в ка меру подогрева 10, где делает девять вертикальных ходов общей длиной 84 м и, подогреваясь от тепла выходящей ленты до температуры 400 °С, поступа ет в зону 9 нагрева и выдержки, дела ет еще четыре оборота, нагреваясь до температуры 680 °С от электрических нагревателей. Затем лента вновь воз вращается в теплообменную камеру 10, охлаждаясь до температуры 450 °С.
Выйдя из печи, лента проходит шесть секций охладительной камеры 11, представляющих собой коробки из листового железа, охлаждаемые водой. Здесь, пройдя путь длиной 69 м, лента охлаждается до температуры 150 °С и попадает для окончательного охлажде ния и промывки в водяной затвор 22. Далее лента пропускается между рези новыми роликами 15 для удаления вла ги, просушивается горячим воздухом в камере 14 и, пройдя уравновешиваю щий ролик 12, тянущими роликами 21 направляется в башню 13 запаса лен ты, из которой выдается тянущими ро ликами 16, проходит вырезку проб пу ансоном 17, счетчик 18 и через направ ляющий ролик 19 наматывается на ба рабан 20.
Производительность агрегата при отжиге ленты толщиной 0,2—0,5 мм и шириной 650—950 мм составляет около 15 т/ч. Скорость движения ленты 100— 150 м/мин. Мощность нагревательной зоны печи 160 кВт. Расход защитного газа около 70 м3/ч. Недостатком агре гата является сложность заправки лен ты при ее обрыве. Для упрощения этой операции в печи должны быть преду смотрены специальные люки.
На рис. 3.41 изображена башенная печь для непрерывного отжига жести производительностью 30 т/ч без реку перации тепла. Общая длина находя щейся в печи ленты 600 м, время пре бывания ленты толщиной 0,25 мм со ставляет около 120 с, а скорость ее дви жения в печи 300 м/мин.
7.7. ПОТОЧНЫЕ ЛИНИИ ДЛЯ СВЕТЛОЙ ЗАКАЛКИ В РАСПЛАВЕ СОЛЕЙ
Светлая закалка в расплавах солей и щелочей позволяет снизить трудоем кость термической обработки, повысить механические свойства деталей, до стичь высокой скорости охлаждения, получить светлую поверхность деталей,
а также исключить вредную для здо ровья рабочих операцию очистки изде лий от окалины. Изотермическая за калка в расплавах щелочей сталей ЗОХГС, 38ХС, 40ХНМ и других повы шает ударную вязкость и пластичность деталей в 1,5—2 раза по сравнению с обычной закалкой и отпуском на ту же твердость. Кроме того, при изотерми ческой закалке значительно уменьша ются коробление и деформация деталей и сокращается цикл операции.
Поточная линия для светлой закал ки состоит из ряда последовательно расположенных ванн (нагрева, охла ждения, промывки, пассивирования), в которых подвески с деталями приво дятся в движение горизонтальным цеп ным конвейером. Перенос подвесок из одной ванны в другую совершается ры чажными или вертикальными цепными перебросами.
На рис. 7.9, а показана поточная ли ния для изотермической закалки бол тов из стали 38ХС и 40Х. Болты на специальных подвесках подогреваются в шахтной печи 8 и переносятся для окончательного нагрева в электродную соляную ванну 7, после чего они прохо дят изотермическую закалку в ванне 6 с расплавом NaOH при температуре 350—400 °С, промываются от щелочи в горячей воде двух ванн 5 и 4 и пассиви руются в ванне 3. Подвески с деталями транспортируются горизонтальным цеп ным конвейером 1 и рычажными пере бросами 2.
Рычажный переброс (рис. 7.9, б) состоит из двух рычагов 5 с захватами 3, насаженными на ось 6, приводимую во вращение цепью 7 с помощью цеп ных шестерен^ и червячного редукто ра 1 от электродвигателя 2. Детали, подвешенные на штанге, двигаясь на цепи горизонтального конвейера 4, за мыкают контакты ограничителей и включают мотор переброса. Рычаги 5 переброса подхватывают штангу за концы и переносят подвеску с деталями в следующую ванну, вновь укладывая штангу на цепи горизонтального кон вейера. Продолжительность выдержки деталей в ваннах определяется скоро стью движения конвейера и длиной ванны.
С увеличением высоты подвески приходится увеличивать размеры ры чажных перебросов, что приводит к не обходимости удлинять поточную ли нию. В этом случае лучше применять

цепные перебросы. Цепной переброс (рис. 7.9, в) состоит из четырех пар колес 4, соединенных цепями Галля 5. Цепи имеют подвески 6, которые под хватывают за концы двигающуюся на горизонтальном цепном конвейере 8 штангу 7 и перебрасывают подвеску с деталями в следующую ванну. Привод цепного переброса осуществляется че рез цепную передачу 3, червячный ре дуктор 2 от электродвигателя 1.
Общая продолжительность процес са светлой закалки болтов в полуавто матической поточной линии составляет 50--55 мин вместо 9—10 ч при обычной закалке в масле с применением пескоочистки и оксидирования. Стоимость обработки болтов снижается в два ра за. Размеры и расположение ванн и ба ков таковы, что их можно выдвигать в сторону и менять местами. Это позво ляет применять различные варианты технологии термической обработки.
Скорость конвейера определяется) продолжительностью нагрева и регули руется вариатором. Автоматическое ре гулирование тепловых режимов ванн осуществляется так, что при падении температуры ниже заданной в одной из ванн электродвигатель выключается и конвейер останавливается. Это преду преждает брак из-за недогрева. Специ альные зонты и местная вытяжная вен тиляция обеспечивают безопасные ус ловия работы. Производительность по луавтоматической линии равна 60 кг/ч.
Поточная линия для ступенчатой закалки деталей включает подогрева тельную печь, электродную ванну я нагрева под закалку, закалочную ще_ лочную ванну из расплава 75 % КОЦ+ +25 % NaOH с температурой 160—- 220°С, соляную ванну для отпуска с температурой 400—500 °С и ванны ддя промывки и пассивирования деталей.
Для предохранения деталей от кор розии в технологическом процессе их обработки применяют операцию окси дирования, которая проводится в горя
чих водных растворах окислителей,но продолжительность такой операции со ставляет 1—3 ч, что усложняет вклю чение ее в поточную линию. При введе нии в щелочную закалочную ванну окислителей (NaN03, NaN02, Na3P o 4)
вцелом ряде случаев процесс закалки
всолях можно совместить с операцией оксидирования. Это сокращает цикл обработки деталей в два-четыре раза и упрощает создание комплексных поточ ных линий.
7.8.ПОТОЧНАЯ ЛИНИЯ
СНАГРЕВАТЕЛЬНЫМИ АППАРАТАМИ
ИПЕЧАМИ
На рис. 7.10 приведена автомати ческая поточная линия для изготовле ния и термической обработки вагонных
Рис. 7.10. Автоматическая поточная линия для изготовления и термической обработки вагон ных пружин с нагревательными аппаратами и печами
пружин с электроконтактным нагревом и отпуском в конвейерной печи.
Прутки со стеллажа 1 по рольгангу поступают в установку 2 для электроконтактного нагрева места реза и раз резаются на заготовки эксцентриковым прессом 3 мощностью 60 т. Заготовки по рольгангу 4 двигаются до упора и автоматически подаются на конвейер 5, с которого поступают в установку 8 электроконтактного нагрева и манипу лятором 10 подаются в ковочные валь цы 9 для оттяжки одного конца. Затем заготовки транспортируются для нагре ва в электроконтактную установку 11, здесь манипулятором 13 в вальцах 12 оттягивается другой конец. После это го заготовки поступают в электрокон тактную установку 14 для общего на грева и передаются в навивочный ста нок-автомат 15. Навитые пружины по лотку 17 сбрасываются на конвейер 16, которым доставляются в закалочную барабанную машину 18. В закалочной машине пружины гидравлическим ци линдром 19 насаживаются на оправку, а после охлаждения снимаются с оправ ки вторым гидравлическим цилиндром 20 и сбрасываются на конвейер 21. По следний выдает пружины из бака, и они направляются в конвейерную печь для отпуска.
От конвейера 5 до навивочного стан ка 15 заготовки движутся с помощью рейнеров. Рейнер 6 перемещается вдоль поточной линии по раме 7, он имеет захваты, управляемые пневматическим цилиндром. Работа рейнеров полностью автоматизирована. После окончания технологической операции на станке го ловки рейнера автоматически захваты вают заготовки, поднимают их и пере носят на следующую операцию. Всего на линии имеется шесть головок. По точная линия позволяет полностью лик видировать ручной труд и увеличить производительность в два-три раза.
Установка для электроконтактного нагрева состоит из трех самостоятель ных, параллельно расположенных электроконтактных4 устройств, смонтиро ванных на одной раме. Температура на грева заготовок контролируется фото пирометром ФЭП-2, который, после того как они будут нагреты до необхо димой температуры, дает сигнал на от ключение напряжения и перемещение в навивочный станок.
Закалочная машина (рис. 7.11) со стоит из восьмипозиционного барабана
8, вращающегося вокруг горизонталь ной оси, и отводящего конвейера 9, ко торый размещается в баке 10. Пружи на поступает по конвейеру 2 к лотку 3f сбрасывается на него и скатывается на позицию загрузки 7 закалочного бара бана. Если температура пружины перед закалкой была ниже требуемой, то на лотке 3 открывается люк 5 и пружина по склизу 12 направляется в контейнер передельного брака. Сигнал для от крытия люка подается фотопиромет ром 4 с помощью исполнительного ме ханизма 11. Другой фотопирометр 1 не пропускает на лоток пружину с по вышенной температурой, пока она не снизится до требуемой.
После того как пружина попадает на опорную призму 15, пневматический цилиндр, расположенный на боковой стороне бака против позиции загруз ки 7, вдвигает оправку 14 внутрь пру жины. Положение последней фиксиру ется в осевом направлении торцевой опорой 13, которая зажимает пружину с помощью рычага при повороте бара бана, На позиции выгрузки другой пневматический цилиндр выталкивает оправку, а при последующем повороте барабана торцевая опора отходит и пружина падает на конвейер 9, кото рый выдает ее из закалочного бака. Конвейер бака имеет верхние привод ные и нижние натяжные звездочки. Последние натягиваются через трос специальным винтом 6. Закалочный ба рабан вращается мальтийским меха низмом через редуктор с помощью электродвигателя мощностью 2 кВт. Конвейер бака приводится в движение от того же электродвигателя через хра повой механизм, собачка которого свя зана с мальтийским механизмом. Бара бан и конвейер бака движутся перио дически.
Поточная линия для изготовления и обработки пружин позволяет снизить стоимость термической обработки в три раза.
7.9. РЕГУЛИРОВАНИЕ СКОРОСТИ ДВИЖЕНИЯ МЕХАНИЗМОВ
Скорость движения непрерывно ра ботающих механизмов регулируется с помощью электродвигателей постоян ного тока; механических регуляторов; реле времени, периодически включаю щего приводные механизмы.
1 |
2 3 4 5 |
6 |
7 |
- |
|
Рис. 7.11. Барабанная машина для закалки пру жин в фиксированном состоянии:
а — общий вид; б — фиксирующее зажимное устрой ство пружины
Электродвигатели постоянного тока позволяют плавно регулировать ско рость в пределах 1 : 4. Частота враще ния двигателя регулируется реостатом путем изменения напряжения в обмот ке ротора или магнитного потока, воз буждаемого в обмотке статора. При от сутствии в цехе постоянного тока ча стота вращения регулируется по систе ме генератор — двигатель. Механизм приводится в действие от специального генератора, вращаемого асинхронным двигателем переменного тока. Частота вращения изменяется реостатами, включенными в обмотку ротора гене ратора и электродвигателя постоянно го тока, в пределах 1 15.
8 |
9 |
10 |
б
При регулировании частоты враще ния с помощью электродвигателей по стоянного тока снижаются к. п. д. и мощность двигателя. Поэтому ближай шей задачей является создание ионно электронного привода с асинхронным электродвигателем переменного тока. В печах термической обработки и в ме ханизированных закалочных баках ши роко применяются методы механиче ского регулирования скорости движе ния механизмов. Некоторые конструк ции устройств для механического регулирования частоты вращения дви гателя приведены на рис. 7.12. Ско рость движения регулируется путем из менения частоты вращения ведомого вала с помощью промежуточной ше стерни 5, сцепленной со ступенчатым шкивом 1 из шестерен, насаженных на
Рис. 7.12. Механическое регулирование частоты вращения и скорости движения механизмов
ведомый вал (рис. 7.12, а). Вал ше стерни 5 связан рукояткой 4 с привод ной шестерней 3 и может перемещаться вдоль ведущего вала 2 на шпонке, пе редавая крутящий момент любой из шестерен шкива. Недостаток данной передачи заключается в ступенчатом регулировании скорости.
Плавное регулирование скорости движения достигается с помощью фрикционных передач. На рис.-7.12, б показан фрикционный вариатор скоро сти с двумя коническими барабанами 1 и 3, между которыми вращается ро лик 2. Сообщив ролику движение вдоль оси, маховичком 4 можно менять число оборотов приводного вала.
На рис. 7.12, в изображена фрикци онная передача, которую легко исполь
зовать в печах карусельного типа. На ведомую ось 1 насаживается диск 2, приводимый во вращение фрикцион ным роликом 4, скользящим на шпонке вдоль приводного вала 3. Число оборо тов ведомого вала регулируется в ре зультате изменения положения фрик ционного ролика.
Из всех фрикционных передач в термических печах наибольшее распро странение получил вариатор с кониче скими дисками (рис. 7.12, г). Он состо ит из двух пар дисков 2 и 4, имеющих форму усеченных конусов, посаженных на шпонки параллельных осей 6 и 7. Диски могут перемещаться на оси с по мощью шарнирно-закрепленных рыча гов 1 и 5 винтом 9 с правой и левой на резкой. При вращении винта махович
ком 8 рычаги сближают одну пару дис ков и одновременно раздвигают на то же расстояние другую пару. Клиновид ный ремень 3 меняет свое относитель ное положение на дисках, в результате чего изменяется передаточное число. Вместо маховичка на винт может наса живаться цепная звездочка, в этом случае управление вариатором осущест вляется калиброванной цепью. Обозна чив через d[ и d2 минимальные диамет ры дисков, а через D{ и D2 — макси мальные, определим передаточные числа:
. |
|
_ |
Л |
*min — |
^ \ * т а х — |
-~ j- . |
|
Общее передаточное число |
|||
|
(max |
D1D2 |
|
*общ = |
: |
= |
. 1 • |
|
(min |
(*1“2 |
|
Обычно принимают |
d \= d 2= d и D\ — |
||
==D\=D, поэтому |
|
|
1общ= (D[d)2.
Вариатор работает при частоте враще ния 5—15 с-1, поэтому желательно его размещать за электродвигателем, вво дя клиноременную или цепную бесшум ную передачу. Коэффициент полезного действия вариатора около 0,9. Лента вариатора делается стальной с дере вянными колодками.
Скорости движения механизмов можно регулировать, применяя храпо вые передачи. Они просты, надежны, и могут давать большие передаточные числа. В этом случае регулирование скорости движения сводится к измене нию передаточного числа в результате зацепления собачкой различного коли чества зубьев храпового колеса. На рис. 7.12, д число зубьев, входящих в зацепление с собачкой храповика, из меняется гладким сектором 4, вводи мым между храповым колесом 2 и со бачкой 3. Гладкий сектор свободно крепится на оси храпового колеса и имеет штангу 1. Изменяя положение последней, в зацепление можно вво дить то или иное количество зубьев храпового колеса, регулируя переда точное число. Если на протяжении хо да собачки открыть'один зуб, то храпо вое колесо повернется тоже на один зуб, если открыть два зуба, то на два и т. д. На рис. 7.12, в изображена хра повая передача, в которой количество зубьев храпового колеса /, входящих в зацепление с собачкой 2, изменяется свободно сидящим на его оси гладким диском 3. Собачка одновременно сколь зит по храповому колесу и диску. Она зацепляется с колесом только в том случае, когда попадает в вырез глад кого диска.
8. ВСПОМОГАТЕЛЬНОЕ |
И ДОПОЛНИТЕЛЬНОЕ |
ОБОРУДОВАНИЕ |
|||||||||||
В данной главе описано |
вспомога |
нии, |
превышает затраты |
на топливо. |
|||||||||
тельное оборудование термических це |
Для борьбы с окислением и обезуглеро |
||||||||||||
хов, используемое для получения конт |
живанием |
применяют нагрев в чугун |
|||||||||||
ролируемых атмосфер и вакуума, и |
ной стружке, слабо науглероживающих |
||||||||||||
дополнительное, |
применяемое |
после |
средах, в свинцовых и соляных ваннах. |
||||||||||
операций |
термической |
|
обработки |
Иногда при нагреве деталей использу |
|||||||||
(травильные |
установки, |
дробеструй |
ют защитные покрытия стеклообразны |
||||||||||
ные аппараты, установки для наклепа, |
ми материалами: базальтом, андеци- |
||||||||||||
моечные машины, правильные прессы и |
том, габбором, трахитом и др. Наибо |
||||||||||||
машины, устройства для зачистки по |
лее |
распространенными |
покрытиями |
||||||||||
роков и вырезки образцов). |
|
|
|
являются силикатные эмали, представ |
|||||||||
При нагреве металлов и сплавов в |
ляющие собой сплавы окислов, получа |
||||||||||||
электрических и пламенных печах по |
емых из смеси песка, мела, соды, гли |
||||||||||||
верхностные слои деталей в результа |
нозема и других недорогих компонен |
||||||||||||
те воздействия атмосферы печи окисля |
тов. При нагреве деталей эмали оплав |
||||||||||||
ются и обезуглероживаются. Это ока |
ляются, |
образуя |
газонепроницаемую |
||||||||||
зывает |
отрицательное |
влияние |
на |
пленку, прочно сцепленную с метал |
|||||||||
качество деталей, вызывает |
необходи |
лом. |
|
|
|
|
|
||||||
мость увеличения припусков и удаления |
Лучшим способом борьбы с окали |
||||||||||||
поверхностного |
слоя металла, |
что, |
в |
ной и обезуглероживанием при опера |
|||||||||
свою очередь, приводит к значитель |
циях термической |
обработки является |
|||||||||||
ным потерям металла и к увеличению |
применение контролируемых атмосфер |
||||||||||||
себестоимости |
продукции. Часто |
стои |
или |
вакуума. |
Однако |
подавляющее |
|||||||
мость металла, теряемого при окисле |
большинство печей пока не имеют кон |
тролируемых атмосфер, поэтому нагре |
Контролируемые |
атмосферы |
применя |
||
ваемый металл покрывается окалиной, |
ются также при |
газовой цементации, |
|||
которую приходится удалять. Это осо |
газовом цианировании и как специаль |
||||
бенно нежелательно для ленты и ли |
ные — при азотировании, газовом хро |
||||
стового материала, проходящих холод |
мировании и т. п. |
|
|
||
ный прокат, |
холодную |
штамповку, |
Степень окисления, обезуглерожи |
||
а также для |
прутков, |
проволоки и |
вания при данной температуре зависит |
||
труб, предназначенных к волочению и |
от состава газовой фазы, типа нагрева |
||||
калибровке. Окалина затрудняет про |
емого сплава, адсорбционных и диф |
||||
цесс пластической деформации метал |
фузионных процессов, происходящих в |
||||
ла, обусловливает увеличение расхода |
поверхностных слоях деталей. Толщина |
||||
валков, фильтров и образование неудо |
пленки окислов и величина |
науглеро- |
|||
влетворительной поверхности металла. |
женного слоя при нагреве |
в течение |
Даже |
в том |
случае, |
когда |
детали |
в |
времени т подчиняются параболической |
||||||||||
дальнейшем |
проходят |
механическую |
зависимости %2= k т, а |
с повышением |
||||||||||||
обработку, их |
необходимо |
предвари |
температуры — экспоненциальной |
|||||||||||||
тельно очищать от окалины, так как |
|
|
|
|
|
|
|
|
||||||||
вследствие высокой |
твердости ее уда |
- ^ |
= |
Лехр( - - | г ) |
|
(8.1) |
||||||||||
ление в процессе |
резания |
приводит к |
|
|
|
|
|
|
|
|
||||||
большому расходу режущего инстру |
где А — постоянная величина; Q — теп |
|||||||||||||||
мента и снижению производительности |
лота активации; R — газовая постоян |
|||||||||||||||
станков. При удалении часто вскрыва |
ная; Т — температура, К. |
|
|
|||||||||||||
ются |
поверхностные |
пороки металла |
К числу наиболее энергично окисля |
|||||||||||||
(трещины, волосовины, плены, закаты |
ющих железо и сталь газов принадле |
|||||||||||||||
и т. п.). |
|
|
|
|
|
|
|
жат кислород, водяные пары, углекис |
||||||||
Детали от окалины очищают в тер |
лота и сернистый ангидрид. Кислород, |
|||||||||||||||
мических цехах. |
Это весьма трудоем |
углекислота, |
водород |
могут |
вызвать |
|||||||||||
кий и тяжелый процесс. Окалина с из |
обезуглероживание, а |
окись углерода, |
||||||||||||||
делий и полуфабрикатов удаляется в |
метан |
и |
другие |
углеводороды — на |
||||||||||||
результате травления в водных раст |
углероживание. |
Нейтральными явля |
||||||||||||||
ворах кислот, восстановления окислов, |
ются газы: сухой азот, аргон, гелий. |
|||||||||||||||
дробеструйной |
очистки, |
гидропеско- |
При |
выборе |
состава контролируе |
|||||||||||
очистки. Для очистки деталей после их |
мой атмосферы |
пользуются |
кривыми |
|||||||||||||
закалки в масле |
применяют моечные |
равновесия взаимодействия |
металла е |
|||||||||||||
машины. Большое внимание в терми |
газовой |
|
средой, |
по |
которым |
можно |
||||||||||
ческом цехе уделяется цеховому конт |
определить составы газовых |
сред, не |
||||||||||||||
ролю качества продукции. Для отрезки |
взаимодействующих с металлом. Кри |
|||||||||||||||
темплетов и образцов используют дис |
вые равновесия не учитывают |
кинети |
||||||||||||||
ковые пилы, |
станки, автогенные аппа |
ку реакции и влияние легирующих |
||||||||||||||
раты, а для зачистки поверхности изде |
элементов на установление равновесия. |
|||||||||||||||
лий — шлифовальные круги. В резуль |
В контролируемой атмосфере могут на |
|||||||||||||||
тате термической |
обработки детали и |
ходиться |
газы, |
взаимодействующие |
||||||||||||
полуфабрикаты |
могут |
покоробиться, |
между собой, а протекающие процессы |
|||||||||||||
поэтому в термическом |
цехе осущест |
не будут равновесными. Однако равно |
||||||||||||||
вляют также правку деталей, труб, сор |
весные кривые позволяют |
определять |
||||||||||||||
тового проката и листов. Для этого ис |
направления |
взаимодействия |
газов с |
|||||||||||||
пользуются правильные прессы, много |
поверхностью металла. |
|
|
|||||||||||||
валковые и растяжные машины. |
|
|
|
|
|
|
|
|
|
|||||||
|
8.1. |
|
ВЫБОР СОСТАВА |
|
8.1.1. Выбор состава контролируемых |
|||||||||||
|
КОНТРОЛИРУЕМЫХ АТМОСФЕР |
|
|
|
|
атмосфер |
|
|
||||||||
|
И СХЕМЫ УСТАНОВОК |
|
Принцип выбора состава контроли |
|||||||||||||
|
ДЛЯ ИХ ПОЛУЧЕНИЯ |
|
||||||||||||||
При нагреве в печах с контролируе |
руемой |
атмосферы сводится |
к тому, |
|||||||||||||
чтобы отношение объемов газов-восста |
||||||||||||||||
мыми атмосферами |
определенных |
со |
новителей к |
объему |
газов-окислите |
|||||||||||
ставов металл не обезуглероживается и |
лей при данных температурных услови |
|||||||||||||||
не окисляется или только слабо туск |
ях было равно константам равновесия |
|||||||||||||||
неет. В первом случае нагрев называ |
или превышало их. Рассмотрим дейст |
|||||||||||||||
ется |
светлым, |
во |
втором — чистым. |
вие газов на железо и сталь. |
|
Рис. 8.1. Кривые равновесия газов над поверх |
Рис. 8.2. Кривые равновесия газов над поверх |
ностью стали: |
ностью стали с различным содержанием угле |
а — смесь Н2—Н20 и СО-С(Э2; б — смесь СО—Н20 и |
рода: |
СО-Н2 |
а — смесь СО—С02; б — смесь СН«—Н2 |
К и с л о р о д . |
При |
температурах |
термообработки |
кислород окисляет |
|
сталь и другие сплавы |
даже в случае |
очень малых концентраций. Так, при температуре 900 °С и содержании 1 см3 кислорода в 1 км3 газов (что соответ ствует давлению упругости кислорода 10-2° Па) уже создаются условия для окисления стали. Поэтому контролиру емые атмосферы не должны содержать свободного кислорода.
Д в у о к и с ь у г л е р о д а и в о д я н ы е па р ы. При взаимодействии газов с металлом важно не абсолютное количество газов-окислителей (СОг и Н20 ), а соотношение газов: С02/С0 и Н20/Н 2. Окисление железа усиливает ся при появлении в окалине вюстита FeO. Если температуры превышают 570 °С, будут протекать такие простей шие реакции окисления железа:
Fe + |
C02 ^ F e O + |
CO, |
||
|
|
Рсо |
|
(8.2) |
|
*' = |
/.со |
■ |
|
|
|
|||
Fe + |
Н20 =** FeO + |
Н2, |
||
|
|
Рн.О |
|
(8.3) |
|
* • - |
„ |
• |
|
|
|
|||
На рис. 8.1, а показаны |
зависимости |
кривых равновесия этих реакций над поверхностью стали от температуры. В атмосфере СО, С02 (кривая 2) окис ление активно развивается при высо ких температурах, а в атмосфере Н2, Н20 (кривая /) — при низких. Поэто му в атмосфере Н2, Н20.окисление происходит в период охлаждения.
В применяемых контролируемых атмосферах чаще всего находятся обе смеси: СО—С02 и Н2—Н20. Указанные газы взаимодействуют между собой по реакции водяного газа:
С02 + Н2 ^ СО + Н20,
Р с о Р н 2о
3 р со2Рн2
На рис. 8.1, б дана кривая равнове сия реакции (8.4). Ниже приведены числовые значения константы равнове сия &3 и равновесное содержание С02 и Н20, %, при Р = 0,1 МПа в зависи мости от температуры:
t, °с |
600- |
700 |
800 |
900 |
^3 |
0,41 |
0,65 |
0.94 |
1.28 |
со2 |
23.70 |
20,40 |
17,85 |
15,88 |
Н20 |
13,34 |
15,39 |
17,13 |
18,66 |
t, °с |
1000 |
1100 |
1200 |
|
*3 |
1,66 |
2,07 |
2,51 |
|
со2 |
14,25 |
13,05 |
12,10 |
|
Н20 |
20,00 |
21,10 |
22,13 |
|
При расчете состава атмосфер СО— —СОг, Нг—Н20, N2 необходимо равно весное содержание С02 умножить на
■Рсо+сог. а Н20 на Ря2+я2о• Например, если применяется атмосфера, содержа щая 10 % СО, 6 % С02, 15 % Н2, 2,3 % НгО, 66,7 N2, то при температуре 800 °С
равновесное содержание |
С02— |
17,85 |
(0,10+0,06) =2,86 %, а |
Н20 — |
17,13 |
(0,15+0,023) =2,96 %. По кривым рис. 8.1, б находим, что в момент впуска га за в печь равновесное содержание С02—35,7X0,16 = 5,71 %; Н20 —34,ЗХ Х 0,173=5,94 %. Таким образом, ука занная атмосфера является окисли тельной в момент впуска газа в печь (так как равновесное содержание С02—5,71 % меньше заданного 6,0 %) и восстановительной в период проте кания реакции водяного газа. Необхо димо снизить содержание С02 в газе до 5,7 %.
Помимо окисления, атмосфера Н2— Н20 может вызывать обезуглерожива ние стали, а атмосфера СО—С 02 обез углероживание или науглероживание.
Газы с углеродом стали взаимодей ствуют по реакциям:
Fe(C) + |
2Н2 ть Fe |
+ |
СН4) |
||
|
ри |
|
|
(8.5) |
|
|
к, = р -^ -; |
|
|
||
|
■'см. |
|
|
|
|
Fe(C) -f- |
СОо |
Fe |
-f- |
2СО» |
|
|
'со |
|
|
(8.6) |
|
|
3со, |
|
|
||
|
|
|
|
||
Fe (С) + |
Н20 =Ft Fe + |
СО + |
Н2, |
||
|
Р с о |
+ Р а . |
|
|
(8.7) |
k6 |
|
|
|
||
|
Рн2о |
|
|
|
|
Кривые равновесия |
реакций |
(8.5) и |
(8.6) для стали с различным содержа нием углерода приведены на рис. 8.2, а
и б. |
обезуглероживания |
|
Во избежание |
||
необходимо, чтобы |
СО |
|
сн4 . |
къ\ |
|
н2 |
со2 |
|
со-н2 |
|
|
Н20 |
к*. |
|
|
|
|
Увеличение содержания |
водорода и |
|
двуокиси углерода |
способствует обез |
углероживанию стали, а повышение со держания СО — науглероживанию.
Обезуглероживающее действие во дорода можно нейтрализовать, введя в
газ метан СН4. Для низкоуглеродистой стали (С ^ 0 ,2 %) при 900 °С и 99,5 % Н2 в атмосферу достаточно ввести толь ко 0,5 % СН4. С увеличением содержа ния углерода количество метана, не обходимого для предупреждения обез углероживания, повышается. При нали чии влаги концентрация СН4 должна быть резко увеличена. Так, если в газе содержится 0,6 % паров воды (при 900 °С), для сталей с 0,2 и 0,3 % С кон центрацию СН4 надо повысить соот ветственно до 2,5 и 8,5 %. Таким обра зом, нейтрализовать действие влажно го водорода трудно, особенно при на греве средне- и высокоуглеродистых сталей. Чтобы газ был нейтральным по отношению к высокоуглеродистой ста ли, надо удалять из него пары воды и углекислый газ.
С е р н и с т ы й а н г и д р и д окис ляет сталь. Кроме того, сернистые га зы могут вызвать переход серы в ме талл, особенно при нагреве меди, нике ля и их сплавов. Поэтому сернистые газы необходимо удалять.
Аз от . Чистый молекулярный азот не реагирует со сталью, но достаточно следов влаги, чтобы металл начал обезуглероживаться. Азот с 2 % Н20, имеющий точку росы +18 °С, сильно обезуглероживает сталь. Даже при 0,05 % Н20 (точка росы —30 °С) про исходит обезуглероживание высокоуг леродистой стали. Сухой азот е 0,1 % 0 2 обезуглероживает сталь сильнее, чем воздух.
Из рассмотренных газов нейтраль ным в большинстве сплавов является сухой азот, а для низкоуглеродистых сталей (когда допустимо некоторое обезуглероживание) еще и сухой водо род.
Большое количество азота получа ется при производстве жидкого кисло рода. Однако он всегда содержит 1— 2 % 0 2 и поэтому без очистки не может быть использован как контролируемая атмосфера. В малых установках кисло род удаляется при пропускании азота через раскаленный уголь (f=900— 1000 °С). В установках большой произ водительности прибегают к гидрирова нию кислорода водородом, получаемым путем диссоциации аммиака. Однако указанные методы удаления кислорода являются дорогостоящими.
В промышленности в качестве конт ролируемой атмосферы экономичнее использовать продукты сгорания про мышленных газов, диссоциированного аммиака, генераторного газа, удаляя из состава атмосферы газы-окислители Н20, С02 и S02 и уравновешивая оставшееся количество окисляющих и обезуглероживающих газов соотноше ниями СО/С02; Н2/Н20; СН4/Н2. При светлом отжиге низкоуглеродистых ста лей необходимо соблюдать условие Н2О/Н2^0,1, а при нагреве среднеуг леродистых и высокоуглеродистых ста лей предельное содержание влаги в га зе должно составлять 0,035 %, что со ответствует температуре точки росы —35 °С.
Контролируемые атмосферы с кон центрацией водорода выше 20 % взры воопасны. Низкоуглеродистая сталь
в атмосфере, содержащей 20 % |
Н2 и |
2 % влаги (точка росы +18 °С), |
начи |
нает окисляться только при температу рах ниже 370 °С. При уменьшении тем пературы одновременно снижается и скорость реакции. Б этом случае, вос пользовавшись восстановительным действием СО, можно избежать окисле-