
- •ПРЕДИСЛОВИЕ
- •ВВЕДЕНИЕ
- •1. КЛАССИФИКАЦИЯ И ОСНОВНЫЕ ЭЛЕМЕНТЫ НАГРЕВАТЕЛЬНЫХ УСТРОЙСТВ
- •4. ПЕЧИ-ВАННЫ
- •5. НАГРЕВАТЕЛЬНЫЕ УСТАНОВКИ
- •5.9.1. Расчет непосредственного электронагрева
- •5.9.2. Расчет индукционного нагрева
- •6. ОБОРУДОВАНИЕ ДЛЯ ОХЛАЖДЕНИЯ
- •8.1.2. Удаление окисляющих газов из контролируемых атмосфер
- •8.1.4. Управление составом атмосферы
- •8.3.1. Травление окалины
- •8.3.4. Гидропескоочистка
- •9. ЦЕХОВЫЙ КОНТРОЛЬ
- •КАЧЕСТВА ТЕРМООБРАБОТКИ
- •10. УСТРОЙСТВО КОММУНИКАЦИЙ ТЕРМИЧЕСКОГО ЦЕХА
- •12. ЭКСПЛУАТАЦИЯ ОБОРУДОВАНИЯ ТЕРМИЧЕСКИХ ЦЕХОВ
- •ОГЛАВЛЕНИЕ
кое травление. Способ восстановления |
протравленного |
металла |
(до 50 ч при |
|||||||||||||||||||
окислов несколько дороже по сравне |
20° С, |
1,5—3 ч |
при |
125—150° С) |
или |
|||||||||||||||||
нию с описанными, но при его исполь |
кратковременную |
выдержку |
(30—15 |
|||||||||||||||||||
зовании |
сокращается время |
процесса, |
мин при |
250—300° С), |
используя для |
|||||||||||||||||
ликвидируются |
потери |
металла, улуч |
нагрева вентиляторные печи или ваку |
|||||||||||||||||||
шаются |
условия труда. |
|
|
|
|
умные сушила. |
|
|
|
|
|
|
|
|
||||||||
|
|
|
|
|
|
|
|
|
|
|
При травлении часть металла ра |
|||||||||||
|
8.3.1. Травление окалины |
|
створяется в кислоте, потери могут |
|||||||||||||||||||
Химическое |
травление |
металлов |
достигать 2—3 %. Для снижения по |
|||||||||||||||||||
терь металла, уменьшения травильной |
||||||||||||||||||||||
обычно производят в водных растворах |
хрупкости и расхода кислоты, улучше |
|||||||||||||||||||||
10—20 %-ной серной или 20 %-ной со |
ния условий труда в травильные ван |
|||||||||||||||||||||
ляной кислоты при температуре 40— |
ны |
добавляют |
специальные |
присадки |
||||||||||||||||||
80° С. Для удаления окалины |
с поко |
(ингибиторы) |
органического |
проис |
||||||||||||||||||
вок и литых деталей чаще применяют |
хождения, |
содержащие |
|
в |
составе |
|||||||||||||||||
10—12 %-ные водные растворы серной |
азот, серу, кислород. Защитное дейст |
|||||||||||||||||||||
кислоты, |
учитывая, |
что она |
дешева, |
вие ингибиторов связано с их адсорб |
||||||||||||||||||
доступна по сравнению с другими ки |
цией на поверхности чистого металла |
|||||||||||||||||||||
слотами, |
относительно |
меньше расхо |
и |
торможением |
анодного |
|
процесса |
|||||||||||||||
дуется и позволяет регулировать интен |
растворения |
железа. |
Наиболее |
рас |
||||||||||||||||||
сивность травления, не загрязняет ат |
пространенными |
являются: для |
раст |
|||||||||||||||||||
мосферу цеха. |
|
|
|
|
поверх |
воров |
серной кислоты |
ЧМ |
(тяжелые |
|||||||||||||
Окалина, |
покрывающая |
|
фракции |
хинолиновых |
оснований), |
|||||||||||||||||
ность сталей с особыми физическими |
ПБ-5 (продукт конденсации бензила- |
|||||||||||||||||||||
свойствами |
(нержавеющих, |
окалино |
мина), |
каталин |
(алкилбензилпириди- |
|||||||||||||||||
стойких и др.), трудно растворима, по |
нийхлорид); |
для |
растворов |
соляной |
||||||||||||||||||
этому при их травлении используют бо |
кислоты БА-6 (продукт конденсации |
|||||||||||||||||||||
лее концентрированные |
растворы |
или |
бензиламина |
с |
альдегидом), |
катапин, |
||||||||||||||||
смесь соляной и азотной кислот. Ско |
ПБ-5 и др. Присадки, адсорбируясь на |
|||||||||||||||||||||
рость |
растворения |
окалины |
нержаве |
поверхности |
металла, |
снижают |
поло* |
|||||||||||||||
ющей стали азотной кислотой макси |
жительный |
потенциал |
и |
облегчают |
||||||||||||||||||
мальна |
при |
концентрации |
последней |
адсорбцию органических |
катионов. |
|||||||||||||||||
6—8 %; растворы с большим содержа |
|
Ингибиторы |
добавляются |
в |
коли |
|||||||||||||||||
нием |
кислоты |
сильно |
разъедают ме |
чествах 0,1—0,2 % от объема травиль |
||||||||||||||||||
талл. |
|
|
|
|
|
|
|
|
сво |
ного раствора. При этом потери ме |
||||||||||||
Механизм процесса травления |
талла снижаются до 1—1,5 %, на 25— |
|||||||||||||||||||||
дится |
к |
последовательному |
растворе |
35 % |
сокращается |
расход |
кислоты, |
|||||||||||||||
нию |
окислов под |
действием |
кислот. |
уменьшается |
выделение |
ее |
паров и |
|||||||||||||||
На конечной стадии окислы растворя |
устраняется опасность перетравить ме |
|||||||||||||||||||||
ются по реакциям: |
|
|
|
|
|
талл. Срок |
действия |
присадок 100— |
||||||||||||||
|
F e0+ H 2S04= F e S 0 4+ H 20; |
|
150 ч, возможная температура нагрева |
|||||||||||||||||||
|
FeO + |
2НС1 = |
FeCl2 + |
Н20. |
|
травильной |
ванны |
60—70 °С. Продол |
||||||||||||||
|
|
жительность травления зависит от сос |
||||||||||||||||||||
Под |
действием |
растворов |
серной |
тава металла, характера |
и |
структуры |
||||||||||||||||
кислоты |
значительная |
часть |
|
окалины |
окалины и обычно равна 30—60 мин. |
|||||||||||||||||
отрывается |
от |
поверхности |
металла |
В случае травления в серной кислоте |
||||||||||||||||||
водородом, образующимся в результа |
легированных |
сталей |
процесс удале |
|||||||||||||||||||
те реакции железа с кислотой, прони |
ния окалины ускоряется, если в ванну |
|||||||||||||||||||||
кающей через трещины й поры в ока |
ввести 3—5 % |
NaCl. При этом, вслед |
||||||||||||||||||||
лине: |
^ |
|
|
|
FeS04 + |
Н2. |
|
ствие образования хлорид-ионов, |
рез |
|||||||||||||
|
Fe + H2S04 = |
|
ко уменьшаются скорость растворения |
|||||||||||||||||||
Водород, переходя из атомарного со |
чистого |
металла |
и |
количество погло |
||||||||||||||||||
стояния в молекулярное, создает зна |
щенного |
металлом |
водорода. |
|
|
|||||||||||||||||
чительное давление, под действием ко |
|
В процессе |
травления |
концентра |
||||||||||||||||||
торого и отрывается окалина. Вместе |
цию железа в растворе постоянно |
|||||||||||||||||||||
с тем водород, проникая в металл, рез |
контролируют и если она достигает |
|||||||||||||||||||||
ко снижает его Пластические свойства |
10—15 %, то раствор заменяют новым. |
|||||||||||||||||||||
и вызывает так называемую травиль |
|
При травлении в растворах серной |
||||||||||||||||||||
ную хрупкость. Для удаления водоро |
кислоты |
горячекатаной |
полосы в них |
|||||||||||||||||||
да применяют |
Длительную |
выдержку |
непрерывно увеличивается |
концентра |
ция сернокислого железа, в результате |
растворах серной кислоты с окисли |
||||||||||||||||||||||
чего |
активность |
процесса уменьшает |
тельными добавками |
азотной кислоты, |
|||||||||||||||||||
ся и железо |
в |
значительной |
степени |
хромового |
ангидрида |
или |
хромпика. |
||||||||||||||||
растворяется. Поэтому |
при |
непрерыв |
При травлении в смеси серной и азот |
||||||||||||||||||||
ном процессе травления тонкой ленты |
ной |
кислот |
выделяются |
токсичные |
|||||||||||||||||||
применяют растворы соляной кислоты, |
окислы азота. Поэтому для труднора |
||||||||||||||||||||||
что позволяет улучшить качество по |
створимых медных сплавов лучше при |
||||||||||||||||||||||
верхности, уменьшить время травления |
менять |
электрохимическое |
|
анодное |
|||||||||||||||||||
и увеличить скорость движения поло |
травление, используя |
протяжные ван |
|||||||||||||||||||||
сы до 250 мм/мин и выше. Травление |
ны и агрегаты. |
|
|
|
|
|
|
|
|
|
|||||||||||||
в растворах соляной кислоты протека |
Для титановых сплавов лучшие ре |
||||||||||||||||||||||
ет главным образом вследствие хими |
зультаты удаления окалины дает ще |
||||||||||||||||||||||
ческого |
растворения |
окислов |
железа. |
лочно-кислотное травление. В этом |
|||||||||||||||||||
При нагреве травильного раствора вы |
случае |
металл |
сначала |
обрабатывает |
|||||||||||||||||||
ше 50—40 °С хлористый водород уле |
ся в 80—70 %-ном расплаве едких ще |
||||||||||||||||||||||
тучивается, что ведет к значительным |
лочей (NaOH, КОН) с добавкой окис |
||||||||||||||||||||||
потерям кислоты. С повышением кон |
лителей (NaN03, KN03) при темпера |
||||||||||||||||||||||
центрации последней до 20—25 % |
турах |
250—400 °С |
в |
течение |
|
20—40 |
|||||||||||||||||
процесс травления улучшается. |
|
(нер |
мин. Затем для удаления образующих |
||||||||||||||||||||
Высоколегированные |
стали |
ся титанатов проводят травление в го |
|||||||||||||||||||||
жавеющие, жаростойкие и др.) |
|
травят |
рячем 15—30 %-ном водном растворе |
||||||||||||||||||||
в растворах азотной кислоты с добав |
серной |
кислоты с |
|
выдержкой |
|
10—15 |
|||||||||||||||||
лением |
фторидов и хлоридов |
(напри |
мин. При использовании такого трав |
||||||||||||||||||||
мер, 2—3 % HF). Часто перед травле |
ления получается высокое качество по |
||||||||||||||||||||||
нием окалину предварительно разрых |
верхности, |
наблюдается |
резкое умень |
||||||||||||||||||||
ляют в растворе 8%-ной HN03 или в |
шение содержания |
кислорода |
и водо |
||||||||||||||||||||
других составах. |
|
|
|
|
|
рода в результате удаления газонасы |
|||||||||||||||||
На современных машиностроитель |
щенного слоя, расход кислоты незначи |
||||||||||||||||||||||
ных и металлургических заводах хими |
телен. |
|
|
|
|
|
|
|
|
|
|
|
|||||||||||
ческое травление заготовок и деталей |
Электрохимическое травление в тер |
||||||||||||||||||||||
чаще производят в 10—12 %-ном раст |
мических цехах чаще применяется как |
||||||||||||||||||||||
воре серной |
кислоты, |
имеющем темпе |
подготовительная |
операция |
перед по |
||||||||||||||||||
ратуру 60—80 °С. Травление длится |
крытием |
(омеднением, |
|
хромировани |
|||||||||||||||||||
30—45 мин. Затем детали промывают |
ем). Такое травление по сравнению с |
||||||||||||||||||||||
в воде (60—70 °С) в течение 5—10 мин |
химическим позволяет уменьшить дли |
||||||||||||||||||||||
и нейтрализуют в известковой ванне |
тельность |
процесса, |
травильную |
хруп |
|||||||||||||||||||
или в растворе 0,5 %-ной NaOH при |
кость, сохранить размеры деталей, до |
||||||||||||||||||||||
90—95 °С в течение 5—10 мин. |
|
ванна |
стичь большей чистоты поверхности и |
||||||||||||||||||||
Наиболее |
употребительная |
|
снизить расход кислоты. При травле |
||||||||||||||||||||
для |
травления |
нержавеющих |
жаро |
нии |
сталей с |
особыми |
|
физическими |
|||||||||||||||
стойких сталей |
и нихромов содержит |
свойствами можно ограничиться более |
|||||||||||||||||||||
4? % НС1 и 5 % HN03. Травление про |
слабыми растворами |
кислот. Недоста |
|||||||||||||||||||||
изводится |
при |
температуре |
40—50°С |
ток электрохимического травления за |
|||||||||||||||||||
с последующим кратковременным (3— |
ключается в необходимости |
использо |
|||||||||||||||||||||
5 мин) |
чистовым травлением |
|
в 5 %- |
вания тока низкого напряжения.гЭлек- |
|||||||||||||||||||
ном растворе азотной кислоты. Про |
трохимическое травление |
чаще |
произ |
||||||||||||||||||||
шедшие отжиг высокохромистые стали |
водится в |
сернокислой |
ванне, |
|
питае |
||||||||||||||||||
предварительно травят |
в |
растворе с |
мой |
постоянным |
током |
|
напряжением |
||||||||||||||||
15 %-ной НС1 при температуре |
60 °С. |
4—10 В. Обрабатываемые детали слу |
|||||||||||||||||||||
Травление |
проволоки |
|
марок |
1X13 и |
жат катодом или анодом. В первом |
||||||||||||||||||
2X13 особенно эффективно в растворе |
случае |
травление |
|
называется |
|
катод |
|||||||||||||||||
20 %-ной НС1 с присадкой. |
|
|
|
ным, |
во втором — анодным. |
|
|
|
|||||||||||||||
Медь и ее сплавы травятся в 15 %- |
Катодное травление производится в |
||||||||||||||||||||||
ных водных растворах серной кислоты |
электролите, |
состоящем |
|
из |
раствора |
||||||||||||||||||
при |
температуре 60—70 °С |
в |
течение |
10—15 %-ной H2S 04. Окалина разрых |
|||||||||||||||||||
нескольких |
секунд. Механизм |
процес |
ляется и отбывается в результате вос |
||||||||||||||||||||
са травления сводится к растворению |
становления окислов-желез а выделяю |
||||||||||||||||||||||
окислов. |
Труднорастворимые |
медные |
щимся |
водородом. Благодаря |
проник |
||||||||||||||||||
сплавы, содержащие |
окислы |
алюми |
новению |
электрического |
тока |
через |
|||||||||||||||||
ния, никеля, свинца, травятся в водных |
поры |
|
окалины |
происходит |
разряд |
Рис. 8.19. Травильные баки
ионов водорода под окалиной. Приме няемые плотности тока при катодном травлении колеблются в пределах 5— 10 А/дм2 поверхности детали при на пряжении 4—8 В. Для ускорения про цесса травления температуру раствора повышают до 40—50 °С. Время трав ления по сравнению с химическим трав лением уменьшается в три раза и со ставляет 10—15 мин. Для изделий ме ди и медных сплавов катодное травле ние не дает положительных результа тов.
Анодное травление производится в слабых растворах кислот или даже в растворах токопроводящих солей, на пример в слабо подкисленном раство ре сульфата железа. При этом окалина не только растворяется, но и отрыва ется выделяющимся на аноде кислоро дом. Чтобы травление прошло успеш но, окалина должна быть достаточно пористой. При плотной окалине лучше прибегать к катодному травлению или к предварительному химическому трав лению в серной кислоте.
В случае электрохимического трав ления должен быть создан контакт де талей с источником тока. Если обраба тываются небольшие детали, многие технологические операции выполняют
ся вручную. |
травление, при |
Электрохимическое |
|
котором используются |
вспомогатель |
ные ^ т о д ы из свинца |
или графита, |
соединяемые с внешним источником то ка, называется биполярным. Детали в ванну помещаются между вспомогате льными электродами. Электропровод ность металла намного выше электро проводности электролита, поэтому бо льшинство силовых линий тока прохо дит через детали.
Основным оборудованием для всех видов травления являются специаль
ные баки. Наибольшее распростране ние получили деревянные и бетонные
травильные баки. |
Д е р е в я н н ы е |
б а к и (рис. 8.19, а) |
делают из сосно |
вых брусьев 3 толщиной 130 мм, кото рые соединяют в шпунт, плотно приго няя друг к другу и стягивая болтами из бронзы или кислотостойкой стали. Вну три баки покрывают листовым свинцом 2 толщиной 4—6 мм и зашивают дос ками 1 толщиной 40—60 мм для пре дохранения свинца от механического повреждения. Отдельные листы свин ца свариваются с помощью ацетилено вой горелки. Длина баков должна со ответствовать размерам травимых из делий. Наиболее употребительные раз меры травильных баков: 3,5X2,0Х X I,7 м и 2,5X1,8X1,0 м. При травле нии труб и сортового металла длина баков может достигать 8 м, а при не прерывном травлении горячекатаной полосы 50 м и более. Так как свинец является дефицитным металлом, его заменяют специальной резиной, пласт массами или битуминозными обмазка ми. Резину укладывают в три слоя об щей толщиной 6—7 мм: внутренний слой делают из твердой резины (эбо нита), хорошо сопротивляющейся сер ной и соляной кислотам, а наружные— из мягкой, имеющей повышенную устойчивость против ударов. Если стен ки бака изготовляют из железа, трех слойная резина примыкает непосредст венно к внутренним стенкам бака и плотно соединяется с ними вулканиза цией. Резина не устойчива к азотной кислоте.
Универсальным заменителем свин ца является винипласт, продукт терми ческой пластификации полихлорвини ла. Выпускается он в виде труб, фа сонных изделий и листов толщиной до 20 мм, обладает химической устойчи-
Рис. 8.20. Травильная установка со стационарными травильными баками
востью к большинству кислот и щело чей и может подвергаться сварке го рячим воздухом. Применение винипла ста ограничено, так как он имеет ма
лую теплостойкость под |
нагрузкой |
(до 50 °С). |
травильные |
Используются также |
б а к и из к и с л о т о с т о й к и х бе
т о н о в 1 |
и кирпича с толщиной стен |
|
ки |
3, равной 200—230 мм (рисГ 8.19, |
|
б). |
Между |
кирпичом и бетоном, для |
устранения теплового расширения кир пича при нагреве ванны делают про кладку толщиной 25 мм из пластично го цемента 2 или же из резины. Если стенки бака железные, его внутри об кладывают двумя-тремя слоями толя. Срок службы такого бака достигает 1—1,5 года.
Хорошие результаты дает облицов ка внутренних стенок бака плитами
толщиной 16—20 |
мм из |
плавленого |
камня — диабаза. |
Плитки |
укладыва |
ются на прокладку из битума и скреп ляются замазкой из диабаза на жид ком стекле. Снаружи железные баки окрашиваются кислотостойкой крас кой. Отработанный кислотный раствор удаляется из баков при помощи сифо на или через отверстие в дне по свин цовым или винипластовым трубопро водам. Перед спуском в канализацию раствор необходимо нейтрализовать в специальном колодце известью и раз бавить водой.
Травильный раствор подогревается острым паром. Металл для травления укладывается в корзины или крепится на подвесах, крючках,, гребенках, ко торые изготовляются из высокохроми стых сталей, медных сплавов или де рева. Хорошие результаты по стойко сти в кислотах дает монель-металл (НМЖМц 28—2,5—1,5). Подвески и корзины выбираются в соответствии с конструкцией обрабатываемых дета
лей. Травильные баки оборудуются продольными бортовыми отсосами для удаления паров кислоты, при этом ре комендуется применять сдув со сторо ны, противоположной отсосу, что дает больший эффект. Травильные ванны, промывочные и нейтрализационные ба ки располагают преимущественно в один-два ряда. Корзины транспортиру ются с помощью кранов, балочек, электроталей. При использовании электри ческих кранов и балочек необходимо, чтобы электродвигатели не располага лись над ваннами, так как они будут разъедаться парами кислот и быстро выходить из строя.
В травильной установке, показан ной на рис. 8.20, лебедка 1, приводя щая в движение подъемную таль, вы несена из травильного помещения. Для транспортировки изделий над тра вильными ваннами часто применяют пневматические подъемники. В уста новке два травильных бака 4 с раство ром кислоты, промывной бак 3 и бак 2 для нейтрализации расположены в од ну линию. Примерная производитель ность установки при времени травле нии 30 мин составляет 3—4 т/ч. Бак 6 для питания травильных ванн кислотой находится за пределами помещения'на высоте 2—3 м, кислота поступает в ванны самотеком через мерный бачок 5. В ванну сначала наливается кисло та, а затем вода. Кислоту в ванну луч ше подавать при помощи сжатого воз духа.
Травильное отделение изолируется от других помещений термического це ха и оборудуется мощной притбчно-вы- тяжной вентиляцией для устранения загрязненного воздуха. Испарения от ванн удаляются с помощью бортовых отсосов. Эта вентиляция выделяется в отдельную систему. Обслуживающий
персонал 'снабжается соответствующей спецодеждой.
Травильные установки служат для создания движения деталей в травиль ном растворе, что в два-три раза уско ряет процесс удаления окалины. При меняемые при травлении установки можно разделить на три основные группы: полумеханизированные, кон вейерные и барабанные.
Наиболее широко применяют п о- л у м е х а н и з и р о в а н н ы е у с т а н о в к и , показанные на рис. 8.21. Тра вильная установка кранового типа (рис. 8.21, а) представляет собой вер тикальный шток 5 с прикрепленными вверху четырьмя или шестью горизон тальными балками 6, к концам кото рых подвешиваются корзины 2 с дета лями. Шток имеет поршець и хвосто вик, они движутся соответственно в двух цилиндрах 4 и 3 (минимальный ход штока равен 1,3 м). Верхний ци линдр 4 под действием пара заставляет шток и корзины с изделиями совер шать вертикальные колебательные дви жения на высоту 300 мм с частотой 30—40 раз в минуту. Нижний цилиндр 3 под действием сжатого воздуха из влекает корзины из баков и перемеща ет их в другие баки 1. Корзины вокруг оси штока поворачиваются вручную. Поршень опускается вниз под действи ем массы крана и корзин. Для качания корзин и извлечения их из ванн доста точно одного верхнего цилиндра. Необ ходимое рабочее давление пара 0,6— 0,7 МПа. Отработанный пар использу ется для подогрева травильных и про мывных ванн, которые размещаются вокруг штока установки, причем одно место остается свободным для загруз ки и выгрузки корзин. Установки изго товляются с диаметрами паровых ци линдров 300, 560, 800 мм. Наибольшая нагрузка на коромысле в них соответ ственно равна 450, 900, 1800 кг, сред няя производительность при времени травления 30 мин составляет 1, 2, 4 т/ч. В установках из трех ванн пер вая &анна с раствором кислоты исполь зуется для травления, вторая — для нейтрализации, третья — с горячей во дой для промывки. В установках из пяти ванн в первой ванне находится проточная вода, в двух следующих — травильный раствор, в четвертой — нейтрализационный раствор и в пя той — горячая вода. При травлении листов время пребывания листа в каж
дом баке составляет 4—6 мин (в зави симости от слоя окалины).
Широко распространена на заводах качающаяся травильная установка, изображенная на рис. 8.21,6. Она со стоит из двух рядом расположенных травильных ванн 7, в которых помеща ются укрепленные на балках 3 корзины с травимым металлом, и свободно по ложенных в развилке 4 качающихся рычагов 2. Последние приводятся в движение при помощи кривошипного механизма 7 и зубчатой передачи 6 от двигателя 5. При погружении правой корзины левая корзина поднимается вверх, и наоборот. Движение корзин в баке соответствует движению скалок весов. Число качаний в минуту равно 30, мощность двигателя машин 12 кВт. Наиболее часто применяются ванны, имеющие размеры 3,0ХК5Х2,0 м. Производительность двух кислотных ванн равна 6—10 т/ч в зависимости от травимого материала.
В травильной установке Тейлора (рис. 8.21, б) качание корзин в трави льных ваннах совершается балочкой, приводимой в колебательное движение при помощи паровых или пневматичес ких цилиндров. Травильные ванны 5, 6 и промывные 7, 8 располагаются ря дом, а подвески 2 с деталями движут ся по монорельсу. Монорельсовый путь над ваннами разрезается и его учас ток 3 совершает колебательное движе ние приводом через рычаг 4 от парово го цилиндра 9. Благодаря этому под вески 2 с металлом, периодически покачиваясь, погружаются в ванну. По сле травления разрезная часть моноре льсового пути поднимается на первона чальный уровень, и корзины передви гаются на стационарный участок для разгрузки. Корзины от ванны к ванне транспортируются с помощью горизон тального парового цилиндра 1 посред ством каната и блоков. Высота подъ ема корзин 1900 мм, ход поршня па рового цилиндра 1740 мм, число ходов 15—25 в мин. Диаметр вертикального парового цилиндра равен 420 мм при длине 2000 мм, а диаметр цилиндра, управляющего горизонтальным пере мещением корзин, составляет 200 мм при длине 2600 мм.
В травильных ваннах можно при вести в движение раствор, а металл уложить неподвижно. В этом случае ванна имеет два неодинаковых сооб щающихся между собой отделения: в
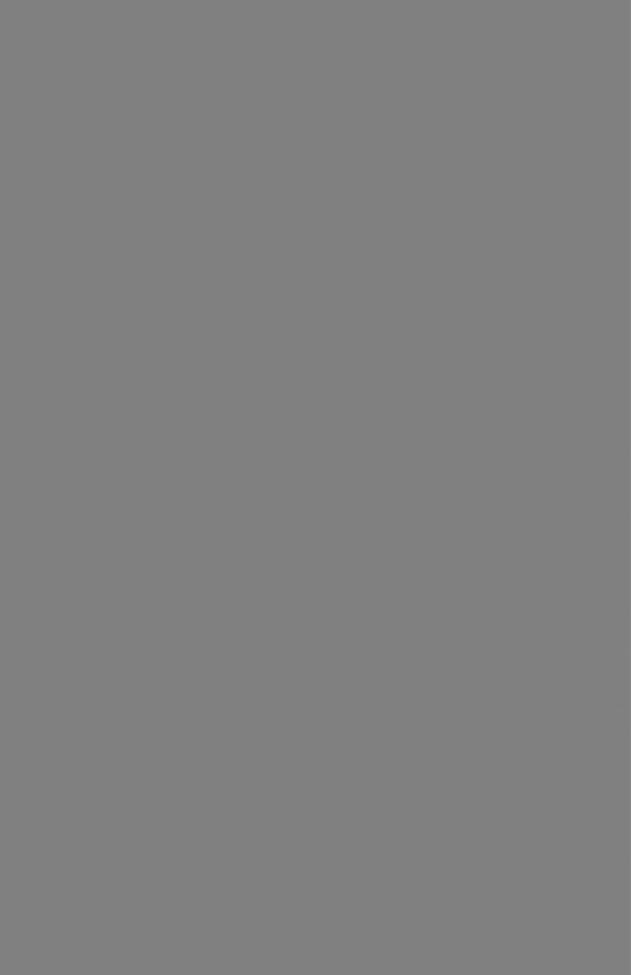
А-А
большом помещается на стойках кор зина с травимым металлом, в малом ходит поршень, приводящий в движе ние травильный раствор. Поршень со вершает 20—25 ходов в минуту и при водится в движение через кривошип ный механизм двигателем мощностью 8—10 кВт. Производительность ванны, имеющей полезные размеры 3,0Х1,5Х Х2,0 м, равна 1—2 т/ч. Трубы и сор товой металл травят в баках длиной 8 м и более.
К о н в е й е р н ы е т р а в и л ь н ы е у с т а н о в к и применяются при боль шом количестве деталей, которые тра вятся по одному режиму. Это длинные ванны 4 (рис. 8.22), детали в них про ходят на подвесном конвейере 2, пред ставляющем собой двутавровую бал ку 5, по нижней полке которой дви жется цепь из роликов. К последней прикрепляются подвески 1 или корзи ны с деталями. Установки имеют вы сокую производительность, дают хоро шие результаты травления, но занима ют "Много места. Если размеры трави льного бака составляют 18X1,5X1,8 м, установка имеет два промывных бака длиной по 9 м, ее производительность при травлении коленчатых валов в рас творе 8— %-ной H2S 04 в течение 30 мин равна 2 т/ч. Если размеры тра вильного 0ака составляют 22X2X1,8 м, производительность установки при травлении в течение 45 мин мелких де
талей в корзинах составляет 3,5 т/ч, а при времени травления 30 мин дости гает 5 т/ч.
Травильные установки обычно вы носятся из основного цеха в изолиро ванное помещение, а конвейер пропус кается в цех, где детали загружаются и разгружаются. Часто в потоке кон вейера устанавливают коридорную печь для сушки деталей.
Иногда травильную конвейерную установку располагают в основном це хе. В этом случае она должна быть за крытого типа и иметь гидравлические затворы. Такая установка (рис. 8.23) состоит из травильной ванны 7 длиной 10—16 м с расположенными у ее тор цов короткими баками 1, заполненны ми водой. Ванна закрыта герметичным кожухом 5 из кислотостойкой стали, наклонные торцевые стенки которого опускаются в водяные баки, создавая гидравлические затворы. Детали через баки транспортируются конвейером, состоящим из двух цепей Галля <5, к которым подвешены гребенки 9 с уло женными на них деталями. Конвейер приводится в движение от двигателя через приводное цепное колесо 3 и на правляется рядом цепных звездочек 4. Ванна снабжается двумя люками 6 длят чистки и заливки травильного раство ра и сливной .трубой 10. Водяные за творы имеют трубы 2 и 11 для подвода и отвода воды. Если длина ванны рав-
|
| \ |
у к |
i X |
|
|
|
|
|
|
|
|
||
|
|
|
------------- ---------------- ^ |
- |
|
|
|
P a cm tb p //e SOu |
^ |
|
|
||
/д/Mvaj/ / |
т о |
|
|
|
|
< I |
|
/ о о о о |
|
|
S000 , ^Холодная |
||
вода / |
11 |
|
|
|
Ю |
вода |
|
|
|
|
|
Рис. 8.23. Конвейерная травильная установка с водяными затворами
на 10 м, ширина 2,3 м, расстояние меж ду гребенками 600 мм, производитель ность установки при травлении перед них осей автомобиля в течение 25 мин составляет 3—3,5 т/ч. Если же длина травильной ванны 15 м, производите льность достигает 5 т/ч. При травлении ленты ее протягивают через травиль ные и промывные ванны с помощью ба рабанов или роликов (как это делается в агрегатах с протяжными печами). Для непрерывного травления применя ют горизонтальные и башенные агре гаты. Горизонтальный агрегат имеет до пяти травильных ванн общей длиной более 125 м, объем раствора в них со ставляет 450—500 м3. Скорость движе ния полосы в такой установке достига ет 380 м/мин. Травильные ванны гум мированы кислотостойкой резиной и футерованы кислотостойкой плиткой.
Мелкие детали сложной конфигура ции можно хорошо и быстро травить во
вращающихся |
б а р а б а н н ы х |
ус |
т а н о в к а х , |
осуществляя одновре |
|
менно пескоструйную очистку |
(рис. |
8.24). Детали для очистки доставляют ся конвейером в корзинах, из которых они ссыпаются через загрузочную во ронку 3 в переднюю часть барабана 2, вращающегося с частотой 0,3 с-1. Де тали в барабане помещаются в сталь ной песок и поливаются раствором 4—
6 %-ной |
H2S 04. |
Последний |
подается |
насосом |
1 из бака 13, находящегося |
||
под барабаном. |
Кислотный |
раствор |
разрыхляет окалину, которая очищает-
4 5 6 7 8 9 Ш
а |
!2 |
Рис. 8.24. Травильно-очистной барабан
ся с поверхности детали стальным пес ком. Отделившаяся окалина уносится вместе с кислотным раствором в бак 13, из которого она периодически уда ляется. Барабан изготовлен из листо вой стали и обложен внутри вулкани зированной резиной толщиной 15 мм. Он приводится во вращение двигате лем 4 через редуктор 5 и зубчатый обод 6. После того как детали очистятся от окалины, вращение барабана переклю чают в обратную сторону. Детали вме сте с песком с помощью конуса 7 на правляются во вторую часть барабана, внутренняя поверхность 8 которой име ет отверстия. Стальной песок высыпа ется через отверстия вниз, а детали по ступают в непрерывно вращающийся с частотой 0,15 с-1 моечно-нейтрализаци онный барабан 10. Здесь кислота на деталях нейтрализуется горячим Ще лочным раствором, подаваемым через ряд трубок 9 насосом 11 из бака 12. Пройдя моечный барабан 10, детали направляются в барабанную сушилку и далее на контроль. Стальной песок возвращают обратно в первую секцию барабана 2, переключая его вращение. Барабан загружают следующей парти ей деталей. Установка позволяет одно временно загрузить в травильный ба рабан 1,0—1,4 т деталей. При времени травления 15—20 мин производитель ность установки составляет 3—4 т/ч.
Электрохимическое травление Мо жет осуществляться в ваннах периоди ческого действия и в конвейерных уста новках. Конвейерная установка катод ного травления при скорости движения конвейера 0,6—0,8 м/мин и времени травления 25—30 мин имеет произво дительность 2—2,5 т/ч. Температура
.^травильной ванны равна 50—60 °С. По даваемый для питания катодной тра вильной ванны ток имеет напряжение 6 В, силу 4000 А и плотность 0,8 А/см2. Ванны для анодного обезжиривания и
снятия слоя свинца снабжены само стоятельным питанием от отдельных динамомашин (напряжение тока 6 В и сила 1500 А).
8.3.2. Удаление окалины путем восстановления окислов
Борьба с окалиной путем восстанов ления окислов металлов ведется при помощи энергичных восстановителей. В качестве последнего чаще применя ется гидрид натрия. Процесс восста новления окислов идет по следующим реакциям:
Fe30 4 + 4NaH = 3Fe + 4NaOH; Fe20 3 + 3NaH = 2Fe + 3NaOH; FeO + NaH = Fe + NaOH; Cr03 + NaH = 2CrO + NaOH; CuO + NaH = Cu + NaOH.
Гидрид натрия хорошо восстанав ливает магнитную окись железа и бо льшинство окислов легированных эле ментов, которые очень трудно поддают ся травлению в кислотах. В качестве растворителя гидрида натрия исполь зуется расплав едкой щелочи. Продук тами реакции являются восстановлен ный металл и едкая щелочь (NaOH), которая компенсирует унос щелочи с деталями. Для образования расплава щелочи температура нагрева ванны поддерживается равной 370—400 °С, а содержание гидрида натрия в растворе щелочи 1,5—2 %. Процесс восстанов ления ведется в электродных ваннах (рис. 8.25). Электроды 1 располагают ся вдоль задней боковой стенки ванны и отделяются от рабочего пространства последней железной решеткой 2. Для уменьшения потерь тепла целесообраз но внешние стенки ванны 6 изолиро вать малотеплопроводным материалом.
Необходимый для восстановления гидрид натрия чаще всего получают непосредственно в ванне. С этой целью вдоль ее передней стенки сверху уста навливают специальный генератор, ко торый представляет железную короб ку 5, перевернутую вверх, края ее опу щены в расплав щелочи. Коробка ввер ху имеет герметично закрывающееся отверстие 4 для загрузки металличес кого натрия и ряд трубок 3, по кото рым в расплав щелочи подается водо род. Металлический натрий вследствие низкой температуры плавления (около 100 °С) расплавляется и растекается в
Рис. 8.25. Ванна для восстановления окалины гидридом натрия
генераторе по поверхности щелочи. Подводимый по трубкам водород барботируется через слой расплавленной щелочи и вступает в реакцию с метал лическим натрием, в результате чего образуется гидрид натрия
Na + ^ - H 2 = NaH.
Гидрид натрия растворяется в распла вленной щелочи и равномерно распре деляется по ванне под влиянием силь ных конвекционных потоков, вызван ных электромагнитным перемешива нием при электродном нагреве.
Перед началом работы из ванны должна быть удалена влага, которая разрушает гидрид натрия. Это может быть достигнуто по реакции
NaH + Н20 = NaOH + Н2,
а также в. результате введения в ванну окиси натрия или металлического на трия.
После восстановления окалины го рячие детали сразу погружаются в бак с холодной водой, образующийся пар срывает продукты восстановления. За тем детали промываются водой из брандспойта и еще раз в баке с горя чей водой. Промытые детали быстро высыхают на воздухе. Расход материа лов на 1 т обрабатываемого металла составляет: металлического натрия 3— 5 кг, водорода 1,2—2 м3. С деталями уносится 0,3—0,5 % расплава.
Стоимость восстановления окалины гидридом натрия на 40 % выше по сравнению со стоимостью травления в кислотах, но эксплуатационные расхо
ды значительно ниже и поэтому в ко нечном итоге стоимость обработки 1 т металла тем и другим способом при мерно одинакова. Однако при восста новлении окалины гидридом натрия резко сокращаются потери металла, повышаются скорость процесса и про изводительность, улучшаются качест во поверхности, условия труда, не об разуются отходы, требующие нейтра лизации. Этот способ эффективен при обработке высоколегированных ста лей, кислотное травление которых про текает очень медленно.
При работе с гидридными щелоч ными расплавами необходимо соблю дать определенные правила безопасно сти. Так, чтобы предотвратить возгора ние металлического натрия, его надо держать под слоем керосина. Особенно опасно попадание в металлический на трий влаги, так как это приводит к его бурному воспламенению, иногда даже к взрыву. Чтобы исключить взрыв во дорода, необходимо предотвратить об разование в генераторе смеси водорода с воздухом. До загрузки в генератор металлического натрия весь воздух из него должен быть вытеснен водородом. Обслуживающий персонал следует снабдить специальными комбинезона ми, рукавицами и защитными очками, что позволит предохранить кожу от по ражения щелочью.
Применяемые гидридные щелочные ванны имеют разные размеры; объем ванн достигает 80 м3 (150 т расплава). Время выдержки деталей в ванне за висит от состава и характера окалины
иколеблется в пределах 5—20 мин.
8.3.3. Удаление окалины
вдробеструйных установках
Вдробеструйных установках дета ли от окалины очищаются струей чу гунной или стальной дроби. Струя соз дается сжатым воздухом давлением
0,3—0,5 МПа (пневматическая дробе струйная очистка) или быстровращающимися лопаточными колесами (меха ническая очистка дробеметами).
При пневматической дробеструйной очистке в установках может использо ваться как дробь, так и кварцевый пе сок. Однако в последнем случае обра зуется большое количество пыли, до ходящее до 5—10 % от массы очи щаемых деталей. Попадая в легкие
обслуживающего персонала, кварцевая пыль вызывает профессиональную бо лезнь — силикоз. Поэтому указанный способ применяется в исключительных случаях. При дробеструйной очистке давление сжатого воздуха должно со ставлять 0,5—0,6 МПа. Чугунная дробь изготовляется литьем жидкого чугуна в воду при распылении струи чугуна сжатым воздухом с последующей от сортировкой на ситах. Дробь должна иметь структуру белого чугуна с твер достью 500 НВ, ее размеры находятся в пределах 0,5—2 мм. Расход чугунной дроби составляет лишь 0,05—0,1 % от массы деталей. При очистке дробью получается более чистая поверхность детали, достигается большая произво дительность аппаратов и обеспечива ются лучшие условия труда, чем при очистке песком.
Для защиты окружающей атмосфе ры от пыли дробеструйные установки снабжаются закрытымикожухами с усиленной вытяжной вентиляцией. По санитарным нормам предельно допус тимая концентрация пыли не должна превышать 2 мг/м3. Транспортировка дроби в современных установках пол ностью механизирована.
Основной частью пневматической установки является дробеструйный ап парат, который может быть нагнетате льным и гравитационным. Простейший однокамерный нагнетательный дробе струйный аппарат (рис. 8.26, а) пред ставляет собой цилиндр 4, имеющий вверху воронку для дроби, герметичес ки закрывающуюся крышкой 5. Внизу цилиндр заканчивается воронкой, от верстие из которой ведет в смеситель ную камеру 2. Дробь подается пово ротной заслонкой 3. В смесительную камеру через кран 1 подводится сжа тый воздух, который захватывает дробь и транспортирует ее по гибкому шлан гу 7 и соплу 6 на детали. Дробь нахо дится под давлением сжатого воздуха вплоть до истечения из сопла, что по вышает эффективность действия абра зивной струи. В аппарате описанной однокамерной конструкции сжатый воздух необходимо временно отклю чать при его пополнении дробью.
Чтобы обеспечить непрерывность работы, аппараты нагнетательной си стемы делают двухкамерными с авто матическими устройствами для подачи дроби из загрузочной воронки в верх нюю промежуточную камеру, а из
Рис. 8.26. Дробеструйные пневматические аппараты
нее — в нижнюю рабочую камеру 8 (рис, 8.26,6). В последней все время поддерживается давление сжатого воз духа, поступающего в камеру по тру бе 9. Средняя камера 6 находится по переменно то под давлением сжатого воздуха, подводимого по трубе 3 через регулирующий клапан 2, то под атмо сферным давлением. Когда камера 6 находится под давлением сжатого воз духа, ее нижняя воронка 7 открывает ся и пропускает дробь в рабочую ка меру 8. В момент создания в верхней камере атмосферного давления ворон ка 7 под действием сжатого воздуха закрывается, а верхняя воронка 5 от крывается. При этом верхняя камера загружается дробью, поступающей из загрузочной воронки 4. Регулирующий клапан 2 управляется кулачковым ме ханизмом, который приводится в дей ствие храповой передачей 1.
В^равитационном аппаратедробь подается в смесительную камеру из открытой загрузочной воронки и на правляется на очищаемые детали под действием силы тяжести и инжекции струи сжатого воздуха, что позволяет получить струю дроби достаточной мо щности. Производительность дробе струйных аппаратов зависит от диа метра сопла. Рабочие сопла делают диаметром от 4 до 14 мм. Сопла изго
товляют из белого чугуна, высокохро мистого и сверхтвердых сплавов. Зави симость расхода свободного воздуха, эффективной мощности компрессора и количества выбрасываемой соплом дроби от диаметра сопла при давлении воздуха 0,4—0,6 МПа показана ниже.
Диаметр сопла, мм |
4 |
6 |
8 |
Расход свободного |
воздуха, |
1,5 |
3 |
м3/мин |
0,75 |
||
Эффективная мощность |
7.0 |
15 |
|
компрессора, кВт |
3,50 |
||
Количество выбрасываемой |
650 |
1200 |
|
дроби, кг/ч |
250 |
||
Диаметр сопла, мм |
10 |
12 |
14 |
Расход свободного |
воздуха, |
|
|
м3/мин |
4,5 |
6,5 |
9 |
Эффективная мощность |
|
|
|
компрессора, кВт |
25 |
35,0 |
45 |
Количество выбрасываемой |
|
|
|
дроби, кг/ч |
1600 |
2500 |
3000 |
При очистке изделий от окалины с
помощью быстровращающегося лопа точного колеса используется установка, показанная на рис. 8.27. В этом случае применяется только чугунная дробь, которая подается из воронки 1 само теком на лопатку внутреннего распре делительного колеса 5. Через его щели дробь попадает на рабочие лопатки 2 основного колеса 3 и под действием центробежной силы выбрасывается с большой скоростью в виде расходяще-
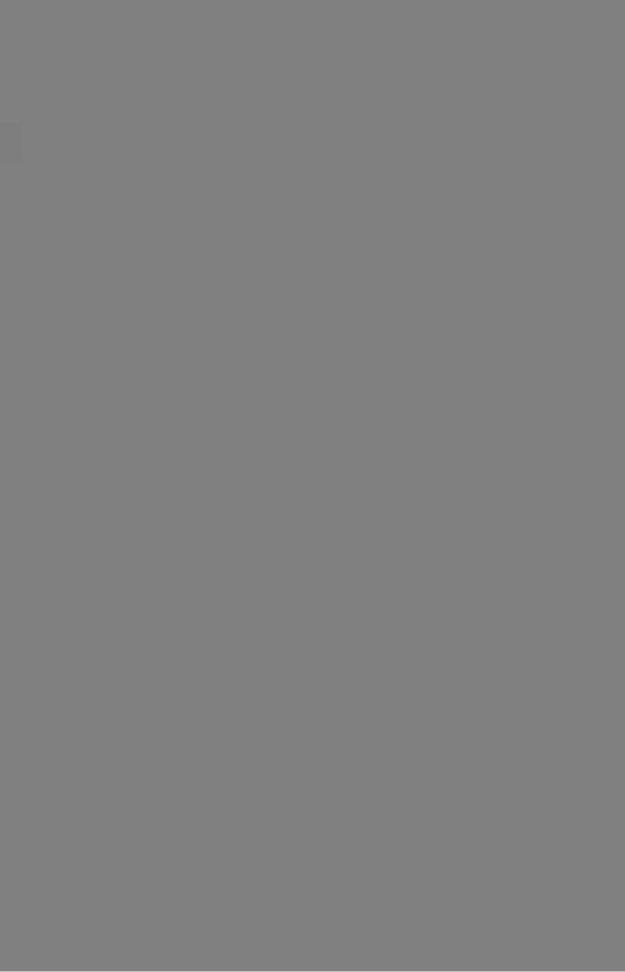

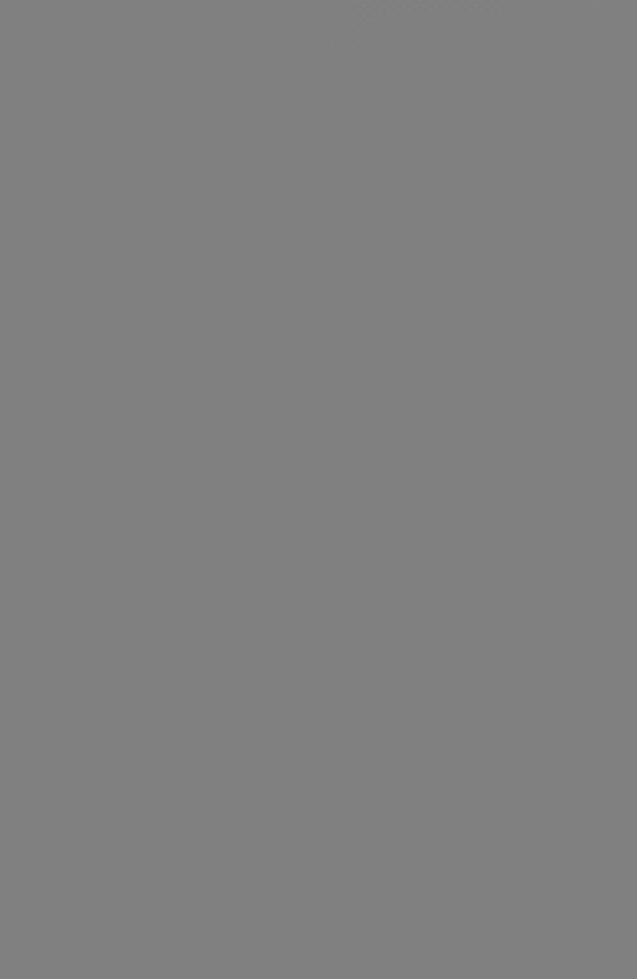
Рис. 8.31. Ленточный дробеметнын барабан
|
|
|
длиной 1,0—1,5 м. Он периодически за |
||||||||||
|
|
|
гружается деталями и дробью пример |
||||||||||
|
|
|
но на 1/3 его диаметра и приводится во |
||||||||||
|
|
|
вращение |
через |
передачу |
от электро |
|||||||
|
|
|
двигателя. В ряде конструкций бара |
||||||||||
|
|
|
банов дробь для очистки деталей пода |
||||||||||
|
|
|
|
ется через цапфы. Характеристика вра |
|||||||||
|
|
|
|
щающихся дробеструйных столов и ба |
|||||||||
|
|
|
|
рабанов приведена в табл. 8.5. |
|
||||||||
|
|
|
|
Оригинальна |
конструкция ленточ |
||||||||
|
|
|
|
ных дробеметных |
барабанов. Ленточ |
||||||||
|
|
|
|
ный барабан |
(рис. 8.31) |
имеет камеру |
|||||||
|
|
|
|
для очистки |
деталей, цилиндрическая |
||||||||
|
|
|
|
часть которой образуется движущимся |
|||||||||
|
|
|
|
на трех парах |
звездочек 2 полотном |
||||||||
|
|
|
|
пластинчатого конвейера 1. Торцы ба |
|||||||||
|
|
|
|
рабана составляют |
два |
диска |
3. Пе |
||||||
|
|
|
|
редняя сторона камеры барабана за |
|||||||||
|
|
|
|
крывается крышкой 4. Над барабаном |
|||||||||
|
|
|
|
устанавливается дробеметное лопаточ |
|||||||||
|
|
|
|
ное колесо 5, бросающее дробь на за |
|||||||||
|
|
|
|
груженные в барабан детали. Отрабо |
|||||||||
Рис. 8.30. Дробеметнын вращающийся стол |
танная дробь высыпается через зазоры |
||||||||||||
конвейера и шнеком 6 подается в ба |
|||||||||||||
|
|
|
|
||||||||||
|
|
|
|
рабанное |
сито, |
откуда |
|
поднимается |
|||||
дробеструйных |
столов с пневматичес |
ковшовым конвейером в воздушный се |
|||||||||||
кой очисткой, только в первых вместо |
паратор, |
из |
которого |
металлическая |
|||||||||
сопел установлены одна или две дробе- |
пыль вытягивается эксгаустером. Очи |
||||||||||||
метные турбинки 2 |
(рис. 8.30). Чаще |
щенная от пыли дробь подается через |
|||||||||||
используют рабочий стол 4 диаметром |
бункер в дробеметное колесо. |
колесо |
|||||||||||
2,4 м, его частота |
вращения |
равна |
Дробеметное |
лопаточное |
|||||||||
0,01—0,02 с-1. Отработанная дробь по |
диаметром 500 мм имеет электродвига |
||||||||||||
дается шнеком 5 на ковшовый конвей |
тель мощностью 12 кВт, элеватор, сито |
||||||||||||
ер 3. Он поднимает ее в сепаратор, из |
и шнек приводятся в движение двига |
||||||||||||
которого дробь снова поступает в дро- |
телем мощностью 2,2 кВт. Детали за |
||||||||||||
беметное колесо. Суммарная мощность |
гружаются в барабан скиповым подъ |
||||||||||||
установки 16—19 кВт; габариты 3,5Х |
емником |
с |
|
двигателем |
мощностью |
||||||||
Х2;8Х5,0 м, масса 4,5 т. Для большей |
3,2 кВт. После очистки детали из бара |
||||||||||||
равномерности очистки стол снабжает |
бана выгружаются ленточным конвейе |
||||||||||||
ся четырьмя-восьмью вращающимися |
ром. Для этого |
он |
переключается на |
||||||||||
вокруг своих |
осей |
дополнительными |
обратный ход. Скорость движения кон |
||||||||||
столиками 1 диаметром 0,6—0,9 м, на |
вейера около 5 м/мин. Вместимость ба |
||||||||||||
которые укладываются детали. |
предна |
рабана |
0,45 |
м3, |
продолжительность |
||||||||
Дробеструйные |
барабаны |
очистки 12—15 мин. Масса всей уста |
|||||||||||
значены для очистки от окалины мел |
новки Ю т. Вместимость выпускаемых |
||||||||||||
ких деталей. Барабан представляет со |
ленточных дробеметных барабанов со |
||||||||||||
бой цилиндр |
диаметром 0,8—1,2 м и |
ставляет 0,3—2 т деталей. |
|