
- •1.7. Первый закон термодинамики
- •1.9.2. Цикл Карно
- •2.1. Понятие о процессе парообразования
- •4.1. Основные понятия о тепловой обработке
- •4.2. Классификация способов тепловой обработки
- •4.5.3. Массообмен
- •4.9.2. Обеспечение применения ЭВМ
- •4.9.3. Принципы моделирования
- •6.2. Причины движения жидкости
- •5.3.1. Аэро- и гидродинамическое сопротивление каналов и трубопроводов
- •РАЗДЕЛ 4. ТЕПЛОГЕНЕРИРУЮЩИЕ УСТАНОВКИ
- •7.1. Классификация тепловых генераторов
- •7.2. Принципы использования тепловых генераторов для сушильных установок
- •8.2. Понятие о двигателях внешнего сгорания
- •9.1.1. Кинетика сушки влажных материалов
- •9.2. Система: материал — сушильная установка
- •9.2.1. Разработка математической модели системы: материал — сушильная установка
- •9.4. Принципы теплового и аэродинамического расчета сушильных установок
- •9.4.1. Расчет материального баланса
- •РАЗДЕЛ 7. ОБЖИГ МАТЕРИАЛОВ И ИЗДЕЛИЙ
- •10.5. Система: материал — обжиговая установка
- •11.2.2. Шахтные печи, работающие на природном газе
- •11.2.3. Печи кипящего слоя
- •11.3. Печи для обжига искусственных заполнителей бетона
- •13.2. Установки периодического действия
- •13.2.1. Камеры ямного типа
- •13.2.3. Пакетные установки
- •13.3.2. Вертикальные пропарочные камеры
- •РАЗДЕЛ 9. ПРИНЦИПЫ АВТОМАТИЗАЦИИ ТЕПЛОВЫХ УСТАНОВОК
- •14.1. Основные понятия о системе автоматического регулирования
Здесь рассмотрены теоретические основы усадки и деформации при обжиге таких изделий, как керамиче ских камней, плиток, кирпича, нарушение структуры ко торых приводит к растрескиванию, короблению и дру гим видам брака. Для кусковых материалов типа извест няка, гипсового камня и т. п. такого анализа не тре буется, ибо растрескивание и нарушение их структуры на конечные свойства материала не влияет.
10.5. Система: материал — обжиговая установка
Для анализа взаимодействия обжиговой установки о материалом составим структурную блок-схему. Прин цип составления такой блок-схемы рассмотрен ранее. В обжиговой установке в отличие от сушильной прохо дит много процессов, поэтому структурную блок-схему целесообразно представить в виде совокупности блоков, каждый из которых имитирует какую-то группу процес сов. Составление таких структурных моделей является основой для подготовки исследований кибернетическим методом.
На этом этапе целесообразно включить все факторы, предположительно влияющие на качество материала. Далее путем ранжирования факторов оставляют для анализа две или три основные блок-схемы, определяю щие качество изделий или оптимальные условия ведения процесса.
Выполнение поставленной задачи будет одним из возможных вариантов построения имитационой модели, которая в этом случае будет представлять некоторую комплексную программу ЭВМ, описывающую поведение компонентов системы и их взаимозависимость. Таким образом, совокупность взаимосвязанных блоков и даль нейшее объединение математических моделей отдель ных технологических переделов в единую модель для имитации всей технологии обжига позволяет провести исследование системы: материал — обжиговая уста новка.
Рассматривая эту сложную систему, необходимо от метить, что каждое воздействие на материал в процес се обжига носит вероятностный характер. Выходные па раметры каждого отдельного участка нельзя определить
по набору входных параметров, характеризующих мате* риал, и по управляемому воздействию параметров, ха рактеризующих теплоноситель. Такая ситуация обычна для сложных технологических систем. Эта сложность обусловлена физическими процессами, зависимыми от течения химических реакций.
В свою очередь, химические реакции зависят от со провождающих их физических процессов. Такая слож ная физико-химическая система может быть решена двумя методами: методом системного анализа с деталь ным изучением взаимосвязанных внешних и внутренних процессов (внутри материала), а также стохастическим моделированием (стохастический от греч. stochastikos, в буквальном смысле вероятностный, случайный метод).
При стохастическом моделировании предполагается, что выходные параметры для каждого конкретного про цесса связаны случайным образом, но коррелированы (взаимосвязаны) с входными параметрами и управляю щими воздействиями. Следовательно, для изучения та кой сложной системы, как взаимодействие материала с обжиговой установкой, необходимо составить структур ные блок-схемы отдельных участков технологической системы; с учетом теплового моделирования по ним вы полнить модельную тепловую установку для проведе ния необходимых исследований; по полученным данным составить имитационную математическую модель иско мой системы.
Таким образом, любую обжиговую установку целе сообразно представить в виде структурных блок-схем технологических участков, где идут отдельные процес сы. В этом случае (см. рис. 10.1 и 10.3) первым был бы участок удаления физико-химической влаги, вторым — участок модификационных превращений кварца, треть им — участок выделения химически связанной влаги и т. д.
Для упрощения разделим обжиговый агрегат на бо лее крупные участки (зоны) и покажем описанный вы ше принцип анализа (естественно, точность в этом слу чае резко снижается). Такими зонами будут: нагрева ния, обжига и охлаждения.
Построение структурной блок-схемы зон нагревания, обжига и охлаждения начнем с перечня параметров, отражающих свойства материала на отдельных переде лах, а также параметров, воздействующих на материал
по переделам с выяснением выходных параметров для каждой блок-схемы.
Для блока № 1 — зоны нагревания |
(рис. 10.13)—■ |
|
входными параметрами, характеризующими |
материал, |
|
будут плотность р0, теплопроводность Х.0> |
теплоемкость |
|
с0, влагосодержание UQ, температура Т0 и |
прочностная |
характеристика R0. Все эти параметры — входные, конт ролируемые, но нерегулируемые. Обозначим их Хь
На материал воздействуют отходящие газы, поступа ющие из зоны обжига, с контролируемыми и регулируе мыми параметрами Н\\ температура продуктов горения Гпг, их влагосодержание йпг, скорость движения по зоне нагревания о„г, концентрация оксида углерода и паров воды соответственно Ссо’ и Сн,о-
Воздействие на материал параметров Н\ и их изме нение повлечет за собой изменение входных парамет ров Н2: коэффициентов теплоотдачи конвективного ак и лучистого ал, массоотдачи р, времени нагрева t. Из менение этих параметров повлечет за собой изменение начала и скорости течения всех ранее рассмотренных хи мических реакций и изменение возникающих напряжен ного состояния о и деформаций е.
Воздействия параметров на блок № 1 (зона нагре вания) приведут к изменению свойств материала и па раметров отработанных газов, которые выходят из этой зоны. К этим параметрам, обозначаемым Уь отно
сим: плотность рь |
теплопроводность Я,ь теплоемкость |
|||
Си температуру Т\. |
Параметрами |
выбрасываемых |
из |
|
зоны отработанных |
газов У2 будут: температура |
Той |
||
влагосодержание йог. |
|
контро |
||
Для блока № 2 |
— зоны обжига — входными |
|||
лируемыми, но нерегулируемыми |
параметрами |
Х2, ха |
рактеризующими материал, будут выходные параметры
материала |
У1 из зоны нагревания; обозначим их на |
рис. 10.13: |
У]—(Х2). Этими параметрами являются рь |
Я,[, С\, Т\.
Входные контролируемые и регулируемые параметры Н' 1 в зоне обжига: массовый расход газа Gr, массовый расход первичного воздуха, подаваемого на горение га за Gai, масса нагретого воздуха GB2. поступающего из зоны охлаждения.
Контролируемые и регулируемые параметры Н'2, зависящие от расхода газа и воздуха, конструктивных особенностей печи: действительная температура горения
газа Гд, окислительная или восстановительная среда, определяемая концентрацией кислорода в продуктах горения СО2, скорость движения продуктов горения по зоне v'„, их температура /2, деформация г\.
Выходные |
параметры |
Y\ |
для |
материала |
из зоны |
||||
обжига: |
плотность |
р2, |
теплопроводность |
Х2, |
теплоем |
||||
кость со, температура Т2 и деформация е2. |
Выходными |
||||||||
параметрами |
продуктов |
горения |
У'2 являются |
входные |
|||||
параметры в |
зону |
нагревания, |
а |
имено: |
Гпг, |
dnr, аПг, |
|||
Geo, и |
СнаоПолученные данные |
представим |
на блок- |
||||||
схеме № 2. |
|
|
|
охлаждения — входными |
|||||
Для |
блока № 3 — зоны |
||||||||
контролируемыми, |
но |
нерегулируемыми |
параметрами |
*з, характеризующими материал, являются выходные параметры материала Y \ из зоны обжига: р2, Я2, с2, Г2, е2; обозначим их на рис. 10.13: Y \—(Х3).
Входными контролируемыми и регулируемыми пара метрами Н' 1 в зоне охлаждения является массовый рас ход наружного воздуха GB-
Контролируемыми и регулируемыми параметрами Н"2, зависящими от массового расхода наружного воз духа, будут: скорость воздуха пв, время охлаждения изделий /3, напряженное состояние изделий аз, а выход ными параметрами для материала Y"\ из зоны охлаж
дения — плотность рз, |
теплопроводность Х3, |
теплоем |
кость с3, температура Г3 и качество готовой |
продук |
|
ции /Сп. |
готовой продукции |
включает |
Показатель качества |
прочностную характеристику /?3, морозостойкость, тре щипостойкость и т. д.
Для блок-схемы № 3 выходными параметрами воз духа в зоне охлаждения Y"2 являются: масса нагретого воздуха, поступающего в зону обжига Gb2 и масса на гретого воздуха GBO, отбираемого из зоны охлаждения. Кроме того, соединим пунктирной линией выходные па раметры из зоны обжига У'ДГпг, dnr, ^пг, Geo, и Сн,о)> являющиеся входными Н\ для зоны нагревания. Также пунктирной линией соединим выходной параметр из зо ны охлаждения Yf,2{Gb2), являющийся входным Н'\ для
зоны обжига.
Для того чтобы не перегружать блок-схемы отдель ными периодами тепловой обработки, не рассматрива лись параметры взаимодействия зон с окружающей сре дой. Весь аэродинамический режим печи представлен
только одним результирующим параметром — создавае мой скоростью работающих в печи газов. И, самое глав ное, применение стохастического моделирования осво бождает от необходимости детального изучения сложно го процесса физико-химических превращений, на кото рое понадобились бы многие годы. В этом случае все физико-химические процессы представлены в виде не которой случайной коррелируемой функции Н\ входных параметров обжиговой установки.
Составление схемы технологического процесса обжи га изделий называют структурным моделированием тех нологии. Оно предназначено для полного анализа теп ловой обработки: определения оптимальных условий ве дения тепловой обработки с точки зрения технологии и экономики процесса, решения задач по контролю и ре гулированию хода процесса и управления им с помо щью ЭВМ.
ВОПРОСЫ ДЛЯ САМОСТОЯТЕЛЬНОЙ РАБОТЫ
1.Что такое обжиг? При производстве каких материалов его применяют?
2.Расскажите о принципах работы промышленной печи.
3. В чем суть внешнего и внутреннего тепло- и массообмена при разных периодах обжига?
4.Как возникает градиент давления при обжиге?
5.Объясните причины возникновения усадки при обжиге.
6.Постройте структурные блок-схемы различных зон печи.
ГЛАВА 11. ОБЖИГОВЫЕ УСТАНОВКИ
Промышленная печь в технологии строительных ма териалов и изделий представляет собой установку, в ко торой в результате воздействия относительно высоких температур на сырье и физико-химических превращений ему придают требуемые свойства. Процесс обжига в про мышленных печах является в большинстве случаев конеч ным при получении строительных материалов и изделий.
Промышленные печи можно классифицировать по различным признакам: по режиму работы — периодиче ского и непрерывного действия; по конструкции рабочей камеры — шахтные, туннельные, кольцевые, вращающие ся и др.; по применяемому источнику теплоты — пламен ные и электрические; по технологическому признаку — установки для обжига гипса, извести, искусственных за
полнителей бетона, сформованных изделий и др. Ниже рассматриваются печи, классифицируемые по последне му признаку.
11.1. Установки для обжига гипса
Простейшей и наиболее распространенной установкой для обжига или, как принято называть, для варки гип са является гипсоварочный котел. В настоящее время гипсоварочные котлы выпускают вместимостью 3 и
15м3.
Котел (рис. 11.1) представляет собой стальной бара
бан 4, снабженный стальной крышкой 7. В крышке два отверстия: первое 10 предназначено для загрузки гип
сового порошка с помощью шнека-питателя 9, |
другое |
6 — для отвода паров воды, выделяющихся при |
варке. |
Котел снабжен четырьмя нагревательными трубами 11 и двумя (верхней и нижней) мешалками 13 с приводным валом 8. Для выгрузки готовой продукции в нижней части установлена течка 15, снабженная открывающим ся шибером 14. Топливо (газ) 2 подается в горелку топки, эжектирует воздух 1 на горение. Газ горит в топ ке 3.
Продукты горения омывают сборное чугунное дни ще 16, проходят через каналы 12, выполненные в обму ровке, и обогревают стенки котла. Далее продукты го рения проходят через нагревательные трубы 11, посту пают в дымовую трубу 5 и удаляются в атмосферу.
Для более полного использования теплоты дымовые газы целесообразно не выбрасывать в атмосферу, а на правлять в установки для помола гипсового камня. По мол гипсового камня при обогреве отработанным тепло носителем требует меньшей затраты энергии, ибо дроб ление в этом случае идет не влажного, а подсушенного гипсового камня.
Обжиг гипсового порошка в котле осуществляется следующим образом. Включается топка и прогревается котел до температуры 390—400 К. В нагретый котел, предварительно включив перемешивающее устройство, постепенно загружают гипсовый порошок. Постепенно гипсовый порошок прогревается до температуры варки 410—420 К, при этом очень интенсивно проходит реак ция дегидратации. Вся подводимая тепловая энергия расходуется на испарение влаги. Необходимо следить за
изменением температуры, |
так как повышение ее до |
450 К приводит к полному |
обезвоживанию и резкому |
снижению качества продукции. В случае повышения тем пературы снижают количество газа, подаваемого на го рение.
Продолжительность варки в котлах малой вмести мости составляет 1—2 ч, в котлах большой вместимос ти — 2—3 ч. По окончании варки топка выключается, от крывается шибер и готовый материал через течку 15 направляют в бункера для его выдерживания (иногда называемого томлением). Выдерживание в бункерах при водит к усреднению гипса, так как частицы, в которых
реакция прошла не полностью за счет теплоты, содержа щейся в нем, переходят в полуводный гипс.
Расход условного топлива на варку гипса составляет 50—60 кг/1т готовой продукции, или 5—6 % массы го товой продукции.
Для обжига гипсового камня применяют также вра щающиеся печи непрерывного действия. Так условно называют обычные сушильные барабаны при использо вании их для варки гипса. Принцип действия и конструк тивные особенности барабанной сушилки показаны на рис. 9.8.
В таких печах (барабанную сушилку для этих целей будем называть вращающейся печью) гипсовый камень обжигают в виде кусков размером 10—40 мм. Тепловой агент готовится в тепловом генераторе, где и разбавля ется в смесительной камере до температуры 1070— 1200 К и по прямотоку подается во вращающуюся печь так, как показано на рис. 9.8. Как и в печи для сушки кусковых материалов, внутри печи установлены лопаст ные мешалки.
Загрузка печи гипсовым камнем производится на 12—15 % площади поперечного сечения печи. Сырье, передвигаясь по уклону печи, а также в результате ее вращения, постепенно дегидратируется до полуводного гипса. Часто центральные слои кусков не успевают де гидратироваться и поэтому качество обожженного гип са, полученного во вращающихся печах, значительно хуже получаемого в варочных котлах.
Тепло- и массообмен во вращающихся печах проис ходит через поверхность гипсового камня, соприкасаю щуюся с теплоносителем, а в варочных котлах тепло- и массообмен порошка происходит за счет кондуктивного нагрева через стенку. Расход условного топлива на об жиг (варку) гипса близок к расходу топлива варочных котлов и составляет также 5—6 % массы готовой про дукции. Однако производительность этих печей значи тельно выше производительности варочных котлов.
Разработана технология обжига гипса в кипящем слое или в пневматической установке. Рассмотрим пнев матическую установку для совместного помола и обжи га гипса (рис. 11.2). Принцип ее работы заключается в следующем. Гипсовый камень, предварительно раздроб ленный до фракций 30—50 мм, загружается через гер метизированную течку 4 и попадает в шахту мельницы
6
Рис. 11.2. Схема пневматической установки для совместного помола и обжига гипсового порошка
3, где подвергается помолу. В эту же шахту из теплово го генератора 1 подается предварительно подготовлен ный теплоноситель (газ) 2.
Теплоноситель подготовляется следующим образом: топливо сжигается в топке теплового генератора, затем продукты горения разбавляются наружным воздухом до 1000—1100 К. Поток теплоносителя захватывает размо лотые частицы гипсового камня и транспортирует их через трубу 5 к вентилятору 8. На пути движения газы проходят двойную или тройную очистку в циклонах 6, далее вторичную очистку в батарейном циклоне 7, за тем вентилятором выбрасываются в атмосферу.
Согласно исследованиям, для создания движения ма териала через трубу 5 необходима скорость несколько большая, чем скорость витания частиц. Тогда скорость движения частиц материала можно определить из фор мулы
уч= ут—vB, |
|
(11.1) |
где v 4 — скорость движения частиц материала |
по трубе 5; |
v T — не* |
обходимая скорость движения теплоносителя; |
ув — скорость вита |
|
ния частиц данного диаметра. |
|
|
Скорость витания частиц d — \ мм составляет около |
||
1,5 м/с; частиц d = 2 мм 3 м/с. Скорость обжига |
частиц |
гипса диаметром 3 мм по экспериментальным данным 6—7 с. Если длина трубы 5 установки (см. рис. 11.2) от шахтной мельницы до циклона 6 составляет, напри
мер, 7 м, то для движения частицы диаметром 3 мм (чтобы полностью прошла реакция обжига) требуется
пролететь 7 м за |
7 с, т. е. |
ее скорость должна быть |
||||
1 м/с. |
Скорость |
витания |
такой |
частицы |
составляет |
|
3 м/с. Следовательно, по формуле |
(11.1), можно опреде |
|||||
лить необходимую |
скорость |
теплоносителя |
в трубе 5: |
|||
vT = v4+ vB, или ит= 1 + 3 = 4 |
м/с. |
то легко |
подсчитать |
|||
Если |
знать диаметр трубы |
5, |
количество теплоносителя, расходующегося в установ ке за 1 ч. Соотношение между массой материала, нахо дящегося в газовом потоке, и массой теплоносителя оп ределяют по практическим данным. Это соотношение характеризует условия, при которых двуводный гипс можно превратить (обжечь) в полуводный за очень ко роткое время (6—7 с). Такое соотношение называют кон
центрацией |
материала |
в газовой |
среде и |
обозначают |
буквой М, |
кг/кг. Для |
гипсового |
порошка |
М = 0,5— |
—0,7 кг/кг. |
|
|
|
|
Для заданной часовой производительности G4 расход |
||||
массы теплоносителя G4T составит, кг/ч, |
|
|||
|
G4T = G4/M. |
|
(11.2) |
Так как такие установки в промышленности не при меняются, то удельный расход условного топлива пока определяют по расчету, и он составляет 4—5 % массы готовой продукции.
Печи для обжига гипса в кипящем слое ничем кроме температуры теплоносителя, не превышающей 1000— 1100 К, не отличаются от печей для обжига извести в кипящем слое (последние рассматриваются далее).
11.2. Известеобжигательные печи
Из печей непрерывного действия для обжига извес ти наибольшее применение нашли шахтные и вращаю щиеся печи.
11.2.1.Шахтные печи, работающие на твердом топливе
Простейшей шахтной печью является пересыпная из вестеобжигательная печь. Конструкция этой печи (рис. 11.3, а) выполнена из кирпича. Шахта печи устанавли вается на опоре—железобетонной плите, размещенной на железобетонных колоннах. Кладка шахты — многослой-
Рис. 11.3. Схема шахтной известеобжигательной печи
а — схем а |
конструкции; б — распределение |
температур |
в печи; |
/ — темпе* |
|||||
ратура |
печных газов; |
2 — температура |
материала; |
3 — смотровые |
отверстия; |
||||
h u h 2 |
hi — соответственно зоны: |
нагревания, обжига, |
охлаждения; А — вы* |
||||||
грузочное |
устройство; |
В — загрузочное |
устройство; |
С — подача воздуха; D — |
|||||
|
|
|
отбор |
дымовых |
газов |
|
|
|
ная. Внутренний слой выложен из .огнеупора, в качестве облицовочного слоя применен шамотный легковес или красный кирпич.
Между кирпичной кладкой и сварным металлическим кожухом, в который одета конструкция шахты печи, предусмотрена шамотная или трепельная засыпка, ком пенсирующая температурное расширение. По высоте печи в несколько рядов устроены смотровые отверстия, закрываемые заглушками; они предназначены для раз мещения контрольно-измерительных приборов и для на блюдения за работой печи.
Печь оборудована герметичными загрузочным и раз грузочным устройствами (рис. 11.4, а, б). После розжи-
10 11 о
Рис. 11.4. Схемы герметичных загрузочного (а) и выгрузочного (б) устройств шахтной известеобжигательной печи
га (пуска) печи через загрузочное устройство загружа ется шихта, состоящая из известкового камня и кусков короткопламенного топлива; загрузка шихты осуществ
ляется скиповым |
подъемником в бункер 2 |
(см. рис. |
11.4, а). Верхний |
затвор 3 открыт. Нижний |
затвор 5 |
поднят вверх, т. е. закрыт. Порция шихты пересыпается в промежуточную емкость 4, после чего верхний затвор 3 закрывается. Открывается (опускается) нижний за твор 5, и шихта из емкости 4 попадает на отбойную пли ту 8 и распределяется по печи 6. После подачи порции шихты нижний затвор 5 закрывается штангой 1, и про цесс загрузки повторяется.
Для интенсификации работы печи повышают газо проницаемость столба (слоя) шихты. С этой целью в печь загружают фракционированный материал (одина ковые или близкие по размеру куски камня или топ лива). В печи раздельно можно обжигать фракции 20—» 40; 40—60 и 60—80 мм и даже до 200 мм. Фракции меньше 20 мм в шахтной печи обжигать нецелесообраз но, ибо сопротивление такого слоя шихты движению теплоносителя резко возрастает, и процесс обжига зна чительно затрудняется или становится невозможным. Шихта загружается почти на всю высоту шахты, остав ляется около 1000 мм свободного пространства перед от бором отработанных газов 7 (в показанной на рис.
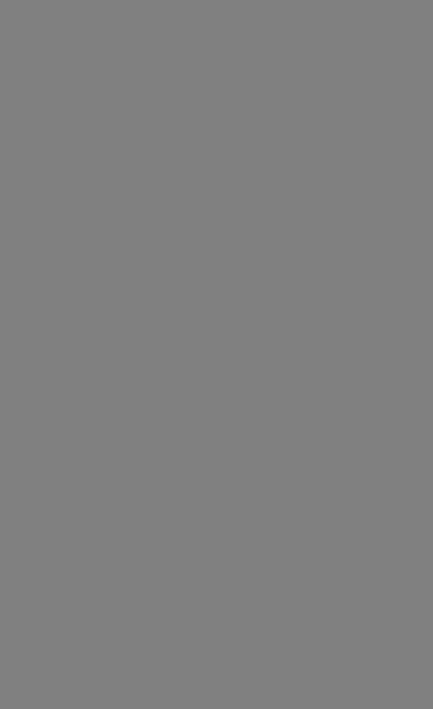