
- •ОБЩИЕ СВЕДЕНИЯ О БУРЕНИИ СКВАЖИН
- •ЛИТОМЕХАНИКА В БУРЕНИИ
- •2.1. ОБЩИЕ ПОЛОЖЕНИЯ
- •2.2. МЕХАНИЧЕСКИЕ И АБРАЗИВНЫЕ СВОЙСТВА ГОРНЫХ ПОРОД
- •3.1. ГИДРОМЕХАНИЧЕСКИЕ СВОЙСТВА И МОДЕЛИ ЖИДКОСТЕЙ
- •1 + ргдг ’
- •3.5. МЕСТНЫЕ ГИДРАВЛИЧЕСКИЕ СОПРОТИВЛЕНИЯ
- •4.1. ШАРОШЕЧНЫЕ ДОЛОТА
- •4.2. ЛОПАСТНЫЕ ДОЛОТА
- •4.3. ФРЕЗЕРНЫЕ ДОЛОТА
- •4.5. АЛМАЗНЫЕ ДОЛОТА
- •4.6. ШАРОШЕЧНЫЕ БУРИЛЬНЫЕ ГОЛОВКИ
- •4.11. КАЛИБРУЮЩЕ-ЦЕНТРИРУЮЩИЙ ИНСТРУМЕНТ
- •5.9. ОБРАТНЫЕ КЛАПАНЫ ДЛЯ БУРИЛЬНЫХ ТРУБ
- •5.10. ОПОРНО-ЦЕНТРИРУЮЩИЕ ЭЛЕМЕНТЫ
- •6.2. УСТОЙЧИВОСТЬ БУРИЛЬНОЙ КОЛОННЫ
- •6.3. НАПРЯЖЕНИЯ И НАГРУЗКИ
- •7.2. ЗАБОЙНЫЕ ДВИГАТЕЛИ
- •Турбобур с редуктором-вставкой
- •7.3. ЮТОРНОЕ БУРЕНИЕ
- •8.4. РАЦИОНАЛЬНАЯ ОТРАБОТКА ДОЛОТ
- •8.5. ПРОЕКТИРОВАНИЕ РЕЖИМОВ БУРЕНИЯ
- •8.6. ОГРАНИЧЕНИЯ НА ПОКАЗАТЕЛИ СВОЙСТВ БУРОВЫХ РАСТВОРОВ
- •Определение скорости осаждения частиц выбуренной породы в буровых растворах
- •9.3. ОПТИМИЗАЦИЯ РЕЖИМОВ ТУРБИННОГО БУРЕНИЯ
- •VHro..
- •10.1. ЦЕДИ И ЗАДАЧИ НАПРАВЛЕННОГО БУРЕНИЯ СКВАЖИН
- •10.3. ФАКТОРЫ, ОПРЕДЕЛЯЮЩИЕ ТРАЕКТОРИЮ ЗАБОЯ СКВАЖИНЫ
- •ПРИЛОЖЕНИЕ
- •СПИСОК ЛИТЕРАТУРЫ
- •ОГЛАВЛЕНИЕ
нике серии 128 ООО. В случае необходимости нижний конец корпуса шпинделя может быть оборудован стабилизатором, при этом на нижний конец вала устанавливается удлинитель, который центрируется внутри стабилизатора резинометалли ческой радиальной опорой.
При сборке турбинных секций предусмотрена возмож ность установки стабилизаторов между турбинными секция ми или между турбинной секцией и шпинделем. Для этого на нижнем переводнике турбинной секции на резьбе закрепля ется стабилизатор, а на нижнем конце вала — удлинитель соответствующей длины так, чтобы не изменять ранее отре гулированные присоединительные размеры утопания и выле тов полумуфт.
Наличие полых валов турбинных секций и шпинделя поз воляет осуществлять следующие операции:
поддерживать в насадках долота перепад давления 6 — 9 МПа без дополнительного нагружения буровых насосов;
проводить замеры пространственного положения ствола скважины в непосредственной близости от долота без подъ ема бурильной колонны на дневную поверхность;
на основании проведенных замеров корректировать осе вую нагрузку на долото для управления процессом набора, сброса или стабилизации угла искривления ствола скважины; прокачивать через полость валов, минуя турбину, разного
рода наполнители; спускать в аварийных случаях в полость вала приборы для
определения места прихвата ПО-50 по ТУ 39-020 —75 и торпе ды, например, ТШ-35, ТШ-43, ТШ-50 по ТУ 25-04-2726-75, ТУ 25-04-2702-75 или ТДШ-25-1, ТДШ-50-2 по ТУ 39/5-137-
73и ТУ 39/5-138-73; продавливать буровой раствор и выравнивать его свойства
через полый вал с последующим сбросом гидромониторного узла (такая операция позволяет во много раз сократить время для проведения указанных работ).
В табл. 7.5 приведены технические характеристики турбо буров с полым валом (при плотности жидкости 1000 кг/м3).
Турбобур с редуктором-вставкой
Турбобуры с редуктором-вставкой типа РМ предназначены для эффективного использования шарошеч ных долот с маслонаполненными опорами при технологичес ки необходимом расходе бурового раствора и уменьшенным
373
Тип |
Число |
Расход |
Крутящий |
Перепад |
|
турбинной |
турбинных |
жидкости, |
момент, |
Н м |
давления, |
секции |
секций |
л/с |
предельный |
при |
МПа |
ЗТСША-195ТЛ |
1 |
24 |
4826 |
2413 |
2,7 |
ЗТСШ1-195 |
1 |
40 |
4806 |
2403 |
3,6 |
А7ТШ |
1 |
30 |
3650 |
1825 |
3 |
П р и м е ч а н и е . N.^ |
— максимальная мощность турбобура; плот |
||||
ность жидкости 1000 кг/м3. |
|
|
|
|
по сравнению с другими гидравлическими двигателями пере падом давлений.
Маслонаполненный редуктор-вставка применяется в соче тании с турбинными секциями и шпинделем серийно выпус каемых турбобуров. Редуктор-вставка устанавливается между шпинделем и турбинными секциями, снабжен планетарной передачей и системой маслозащиты передачи и опор.
Планетарная передача двухрядная, зубчатая, с косозубым зацеплением Новикова. Система маслозащиты имеет уплот нения торцового типа. Выходной вал с помощью шлицевой муфты соединен с валом шпинделя, а входной вал с помо щью полумуфты — с турбинными секциями.
Редуктор-вставка представляет собой автономный узел, который может быть заменен непосредственно на буровой. Энергетические характеристики турбобура с редукторомвставкой и разными типами турбин приведены в табл. 7.6.
При испытаниях турбобуров средняя наработка на отказ маслонаполненного редуктора составила 100—115 ч, а при бурении скважин с высокими забойными температурами (свыше 150 °С) — около 40 ч.
Шпиндель с лабиринтным дисковым уплотнением
В настоящее время нашли промышленное применение и подготовлены для серийного производства шпиндели типа ШФД (табл. 7.7) с лабиринтным дисковым уплотнением (см. рис. 7.3). Они предназначены для использо вания с турбинными секциями серийных турбобуров при ча стоте вращения вала до 25 с-1 и обеспечивают увеличение наработки на отказ и межремонтного периода турбобура в 1,5—2,5 раза по сравнению с тем, когда используются шпин дели серийно выпускаемых конструкций. Увеличение нара ботки на отказ достигается за счет частичной изоляции кар-
Шифр |
Наруж |
Масса, |
Внутренний |
Наружный |
Общая |
Число |
||
ный |
радиаль |
|||||||
шпинделя |
диаметр, |
кг |
диаметр |
диаметр вала, длина, |
ных |
|||
корпуса, му |
мм |
|
мм |
|||||
|
мм |
|
|
|
|
|
опор |
|
ШФД-240 |
240 |
1310 |
205 |
115 |
|
4650 |
3 |
|
ШФД-195 |
195 |
910 |
165 |
105 |
|
4600 |
3 |
|
|
|
|
|
|
|
|
Т а б л и ц а 7.8 |
|
Шифр |
|
|
Присоединительная резьба по РТМ 26-02-15 —72 |
|||||
|
к турбинной |
|
|
|
верхней |
нижней |
||
подшипников |
к долоту |
корпуса |
|
|||||
ТУ 37.006.04281 |
секции |
|
|
части вала |
части вала |
|||
128723 |
|
РКТ-208 |
3-147 |
РКТ-218 |
|
МК-116 |
3-133 |
|
128721К |
|
|
3-171 |
3-117 |
РКТ-177 |
|
МК-105 |
3-117 |
тера осевой опоры от поступления бурового раствора, со держащего твердую абразивную фазу. Такая изоляция обес печивается оборудованием верхней части вала шпинделя "расходным" лабиринтным уплотнением и установкой между лабиринтным уплотнением и уплотнениями картера осевой опоры дренажной втулки, отверстия которой сообщаются с пространством скважины.
Уплотнители картера осевой опоры выполнены из элас тичного материала, укреплены на валу и контактируют с це ментированным металлическим диском, закрепленным в кор пусе, при этом число пар уплотнитель —диск равно восьми.
Для соединения с верхнерасположенными турбинными секциями вал шпинделя оборудован в верхней части конусно шлицевой полумуфтой, которая одновременно служит для сжатия пакета деталей, набранных на валу. Для центрации вала используются резинометаллические радиальные опоры, одна из которых установлена между полумуфтой и лаби ринтным уплотнением, а две другие — в нижней части вала. Лабиринтное уплотнение состоит из набора парных дисков ротора и статора и рассчитано на работу с перепадом давле ний в насадках долота до 7 МПа. В картере осевой опоры между двумя блоками уплотнителей установлен упорно радиальный шариковый подшипник серии 128 000.
По результатам сравнительных испытаний, проведенных в ПО "Куйбышевнефть", шпиндель ШФД-195 имеет наиболь шую наработку на отказ - (183 ч) из всех негерметизированных конструкций новых шпинделей турбобуров, разрабо танных ВНИИБТ. Конструктивные характеристики шпинде лей приведены в табл. 7.8.
Герметизированный маслонаполненный шпиндель
В настоящее время нашли промышленное применение и подготовлены для серийного производства гер метизированные маслонаполненные шпиндели типа ШГД (рис. 7.5). Шпиндели предназначены для использования с турбинными секциями серийных турбобуров при частотах вращения вала до 15 с"*1 и обеспечивают увеличение наработки на отказ и межремонтного периода турбобура в 2—4 раза по сравнению с использованием шпинделей серийно выпускаемых турбобуров.
Увеличение наработки на отказ в шпинделях ШГД дости гается полной герметизацией картера осевой опоры от по ступления бурового раствора, содержащего твердую абразив ную фазу, причем картер осевой опоры заполнен смазкой. Надежная герметизация картера осевой опоры обеспечивает ся тем, что на герметизирующие уплотнения не действует пе репад давлений, срабатываемый в насадках долота. Это стало возможным при использовании "расходного" лабиринтного уплотнения, аналогичного применяемому в шпинделях ШФД. Лабиринтное уплотнение установлено в верхней части вала над герметизирующими элементами. Раствор, прошедший через лабиринтное уплотнение, сбрасывается в затрубное пространство через отверстия в корпусе, расположенные над герметизирующим элементом. Герметизирующие элементы, выполненные из эластичного материала, закреплены на валу и контактируют с цементированным металлическим диском, закрепленным в корпусе.
Вал центрируется относительно корпуса тремя резиноме таллическими радиальными опорами, одна из которых уста новлена в верхней части вала, две другие — в нижней. Полумуфта закрепляется на валу малоконусной резьбой с внут ренним упорным торцом и одновременно своим наружным торцом сжимает пакет деталей, набранных на валу. С верх нерасположенными турбинными секциями полумуфта соеди няется конусно-шлицевым соединением, имеющим такие же присоединительные размеры, как и полумуфта серийно вы пускаемого турбобура. Лабиринтное уплотнение состоит из набора парных дисков ротора и статора и рассчитано на ра боту с перепадом давлений в насадках долота до 7 МПа. Для предотвращения попадания шлама в лабиринтные диски сле дует поддерживать перепад давлений в насадках долота не менее 2 МПа.
Рис. 7.5. Герметизированный мас лонаполненный шпиндель
Герметизирующие уп лотнители установлены над картером осевой опоры и под ним и объединены для удобства монтажа и де монтажа в отдельные бло ки. По принятой класси фикации герметизирую щие элементы состоят из двух частей: одна из них установлена в среде буро вого раствора, другая — в среде смазки. При этом между этими частями об разуется буферная зона, которая через регулирую щий клапан соединена с картером осевой опоры.
Назначение клапана комплексное:
поддержание заданного начального давления смаз ки в картере осевой опо ры как во время заправки, так и в процессе работы, когда происходит увеличе ние объема смазки вслед ствие ее разогрева;
создание встречного дви жения смазки буровому раствору в пределах бу ферной зоны между двумя уплотнителями и продавливание смазки между тор цами уплотнителя и антифрикциона;
возможность секционирования герметизирующих эле ментов с одновременным исключением воздушных пробок между герметизирующими элементами за счет перетока смазки через клапан;
Шифр
шпинделя
ШГД-240 ШГД-195
Шифр
шпинделя
ШГД-240
ШГД-195
Наружный |
|
Внутрен |
Наружный |
Общая |
Число |
Число |
Общий |
Число |
||
Масса, |
ний диа |
диаметр |
уплотни |
|
объем |
|||||
диаметр, |
метр |
длина, |
радиаль |
|
лубри |
|||||
кг |
вала, |
телей |
смазки, |
|||||||
мм |
корпуса, |
мм |
ных опор |
каторов |
||||||
|
мм |
картера |
|
дм3 |
||||||
|
|
мм |
|
|
|
|
||||
|
|
|
|
|
|
|
|
|
||
240 |
2200 |
205 |
115/130 |
7700 |
3 |
8 |
|
36 |
3 |
|
195 |
1450 |
165 |
105/115 |
7650 |
3 |
8 |
|
24 |
3 |
|
|
|
|
|
|
|
П р о д о л ж е н и е |
т а б л . 7.9 |
|||
Шифр |
|
|
Присоединительная резьба по РТМ 26-02-15 —72 |
|
нижней части |
|||||
подшипника по к турбинной |
к долоту |
|
корпуса |
верхней части |
||||||
ТУ 37.006.04281 |
секции |
|
вала |
|
|
вала |
||||
3-147 |
|
РКТ218 |
|
|
||||||
128723 |
|
РКТ208 |
|
МК116 |
|
|
3-133 |
|||
128721К |
|
3-171 |
3-117 |
|
РКТ177 |
СПМК105 |
|
|
3-117 |
равномерное распределение давления по всем образован ным буферным зонам;
вывод остатков воздуха при заправке шпинделей смазкой. Клапан установлен в диске, закрепляемом в корпусе.
Наряду |
с применением шарикового подшипника типа |
128 700 по |
ТУ 37.006.042 —81 предусмотрено использование |
опоры скольжения.
В качестве смазки может использоваться индустриальное масло и нигрол.
Конструкция шпинделя допускает производство доза правки или полной смены смазки на буровой, для чего верх няя и нижняя части картера снабжены заправочными втул ками.
Внастоящее время ведутся работы по использованию сма зок, обладающих высокоэффективными тормозящими свой ствами. С внедрением таких смазок применение герметизи рованных шпинделей станет еще более эффективным, так как тормозное устройство станет наиболее компактным из всех известных.
Врезультате сравнительных испытаний новых шпинделей турбобуров шпиндель ШГД-195 признан наиболее надежной и долговечной конструкцией. Его средняя наработка на отказ составила 294 ч.
Конструктивные характеристики шпинделей ШГД приве дены в табл. 7.9.
Турбины современных турбобуров
Турбина турбобура представляет собой пре образователь гидравлической энергии потока жидкости в ме ханическую энергию вращения вала.
Турбина современного турбобура — многоступенчатая, осевого типа и состоит из систем статоров и роторов. Как правило, система статоров связана с корпусом, а система ро торов — с валом турбобура (рис. 7.6).
При постоянном значении расхода бурового раствора че рез турбину развиваемый ею крутящий момент определяется
по формуле Эйлера |
|
М = Qpr(clu - CjJz, |
(7.1) |
где О — расход жидкости; р — плотность жидкости; г — средний радиус турбины; clu, с2и ~ проекции абсолютной скорости потока жидкости, протекающего соответственно
Рис. 7.6. Принцип действия турбины турбобура (пара статор - |
ротор): |
||
1, |
5 |
— наружный обод ротора и статора; 2, 3 — лопатка ротора |
и статора; |
4, |
6 |
— внутренний обод статора и ротора |
|
через статор и ротор на направление окружной скорости турбины; z — число ступеней турбины.
Эффективный перепад давления на турбине определяется по формуле
Рэ = pu2z, |
(7.2) |
где и — окружная скорость турбины на среднем диаметре. Развиваемый турбиной крутящий момент зависит от ре
жима ее работы, т.е. от частоты вращения ротора турбины. Для большинства современных турбин эта зависимость ли нейна и определяется уравнением
М = МТ(1 - —), |
(7.3) |
Лх |
|
где Мт — тормозной (предельный) крутящий момент; л — частота вращения ротора; пх — частота вращения ротора на холостом режиме (предельная).
Совокупность зависимостей крутящего момента, перепада давления, мощности и КПД от частоты вращения называется энергетической характеристикой турбины. Энергетическая характеристика представлена на рис. 7.7. Как видно из гра фиков, характеристика турбины турбобура — сериесная. Однако это не означает, что турбобур может работать на всех режимах — от холостого до тормозного. Известно, что при увеличении осевой нагрузки частота вращения вала тур бобура вначале уменьшается, затем турбобур начинает неус тойчиво работать, а потом резко останавливается — "срывается". Частота вращения при этом, как правило, быва ет не ниже 0,4 лх.
“Срыв" турбобура объясняется многими факторами, ос новными из которых являются нелинейный рост момента сопротивления на долоте и в пяте турбобура при увеличении осевой нагрузки и снижении частоты вращения, низкочас тотные колебания момента сопротивления из-за вибраций и неравномерностей подачи бурового инструмента, перемежае мость разбуриваемых горных пород по твердости. Все эти факторы приводят к тому, что устойчивая работа турбобура возможна только с определенным, как правило, не менее чем двукратным запасом крутящего момента, т.е. на режимах, располагающихся правее от режима максимальной мощ ности.
Эти режимы в большинстве случаев характеризуются так же и максимальным значением механической скорости про-
M;N;p;y\
Рис. 7.7. Энергетическая характеристика турби ны турбобура:
М — крутящий момент; Мт — тормозной мо мент; N — мощность; Мэ - максимальная мощ ность; р — перепад дав ления; л — частота вра щения; пэ, лх, л0 - частота вращения соот ветственно на экстре мальном, холостом и оптимальном режимах;
Л - КПД; Ло “ макси мальный КПД
ходки. Поэтому условно режим максимальной мощности можно считать рабочим режимом турбобура.
Следует отметить, что чем глубже забой скважины, чем больше искривлен ее ствол, чем более моментоемкое долото используется при бурении, чем выше вибрации бу рильного инструмента и чем больше перемежаемость гор ных пород, тем ближе к холостому режиму должен распола гаться рекомендуемый рабочий режим турбобура и тем, сле довательно, ниже должна быть частота вращения холостого хода.
Для расчета характеристики турбины могут исполь зоваться преобразованные формулы, определяющие крутя щий момент и перепад давления на режиме максимальной мощности:
М = 2пОрг2т , |
|
|
|
|
|
. |
|
(7.4) |
|
р=4тс2рг2—, |
|
|
|
|
|
|
|
(7.5) |
|
л |
|
|
|
|
|
|
|
|
|
где р — перепад давления на турбине; т| — КПД. |
|
|
|||||||
|
|
|
|
|
Т а б л и ц а |
7.10 |
|||
Технические характеристики турбин, выпускаемых отечественной |
|
|
|||||||
промышленностью |
|
|
|
|
|
|
|
||
|
|
|
|
Часто |
Пере |
Мак- |
|
|
|
|
|
|
|
си- |
|
|
|||
|
Диа- |
|
Тор |
та |
пад |
Мак- |
|||
|
Расход |
маль- |
|||||||
|
моз |
враще |
давле |
си- |
|||||
|
метр |
ный, |
|||||||
|
раст |
ной |
ния |
ния |
маль- |
||||
Тип турбины |
турбо- |
МПа |
|||||||
вора, |
мо |
холос |
рабо |
ный |
|||||
|
бура, |
пере |
|||||||
|
л/с |
мент, |
того |
чий, |
кпд, |
||||
|
М М |
|
Н-м |
хода, |
МПа |
пад |
|
% |
|
|
|
|
давле |
|
|||||
|
|
|
|
с 1 |
|
|
|
||
|
|
|
|
|
ния |
|
|
||
30/16,5-240 |
240 |
40 |
24,58 |
17,3 |
0,0262 |
|
|
||
0,0262 |
63,8 |
||||||||
A9KCA |
240 |
40 |
22,02 |
14,0 |
0,0252 |
0,0324 |
40,4 |
||
26/16,5-196 |
195 |
28 |
8,07 |
13,9 |
0,0113 |
0,0113 |
55,3 |
||
А7Н4С |
195 |
28 |
12,59 |
18,5 |
0,0287 |
0,0363 |
40,5 |
||
24/18-195ТА |
195 |
28 |
4,74 |
8,2 |
0,0048 |
0,0048 |
47,4 |
||
24/18-195ТПК |
195 |
28 |
5,63 |
8,1 |
0,0057 |
0,0057 |
42,3 |
||
А7ПЗ |
195 |
28 |
16,77 |
18,3 |
0,0320 |
0,0363 |
38,2 |
||
А7П36К |
195 |
28 |
17,69 |
19,8 |
0,0259 |
0,0296 |
52,8 |
||
21/16,5-195АТА |
195 |
28 |
16,32 |
23,2 |
0,0263 |
0,0341 |
70,6 |
||
ТД-195АТА |
195 |
28 |
16,92 |
29,2 |
0,0395 |
0,0433 |
65,6 |
||
T195K |
195 |
28 |
9,50 |
13,8 |
0,0139 |
0,0139 |
50,8 |
||
28/16-172 |
172 |
24 |
8,22 |
20,5 |
0,0239 |
0,0239 |
44,2 |
||
А6КЗС |
164 |
20 |
6,22 |
18,1 |
0,0194 |
0,0232 |
39,8 |
||
П р и м е ч а н и е . |
Число ступеней |
— 1. Плотность |
бурового |
рас |
|||||
твора — 1000 кг/м3 (техническая вода). |
|
|
|
|
|
При пересчете параметров характеристики турбины на другие значения расхода, плотности жидкости и числа ее сту пеней следует пользоваться выражениями
п ~ Q; М ~ Q2; р ~ О2; N ~ О3; Л inv Q;
п inv р; М ~ р; р ~ р; N ~ р; л inv р; |
(7.6) |
п inv z; М ~ z; р ~ z; N ~ z; п inv z,
где N —мощность турбины.
Турбины турбобуров изготавливаются из малолегирован ной стали преимущественно цельнолитыми в земляные фор мы и составными, когда лопаточный венец выплавляется точ ным литьем по моделям. Выпускаются также лопаточные венцы, изготовленные из пластмассы. Стойкость пластмас совых венцов, как правило, намного ниже стойкости сталь ных.
Характеристики турбин определяются экспериментально при испытаниях на специальном турбинном стенде. В табл. 7.10 даны основные параметры стендовых энергетических характеристик серийных и некоторых опытных турбин тур бобуров, выпускаемых промышленностью.
Турбобуры зарубежных фирм За рубежом производством, прокатом и об
служиванием турбобуров в настоящее |
время занимают |
ся фирмы "Neyrfor", турбобуры которой |
выпускает фир |
ма "Nerpic", и "Turboservice", контролируемая фирмой “Eastman". Однако в эксплуатации у многих мелких субпод рядчиков, владеющих 1—5 турбобурами, сохраняются маши ны, выпущенные более 15 лет назад фирмами "Eastman", “Salzgitter" и "Trauzel".
За исключением отдельных случаев в конструкциях фирмы “Neyrfor" используется многоступенчатая шаровая опора ка чения, очень напоминающая наш отечественный прототип, турбобуры зарубежных фирм содержат в качестве осевой опоры многорядную резинометаллическую пяту, а их ради альные опоры выполнены в виде двух втулок, одна из кото рых — стальная — закреплена на валу, а другая — эластич
ная —в корпусе.
В табл. 7.11 представлены технические характеристики турбобуров фирмы "Neyrfor". Следует отметить, что из
Число Тип ступе
ней
турби
ны
TF5" |
101 |
TF 77," |
110 |
TFST 7'/." |
53 |
TFST 107;’ |
80 |
TF 47." |
— |
TFI5" |
135 |
T2FI5" |
240 |
TFI 7V." |
154 |
TFAI 7 7 4" |
236 |
T3AI 77." |
308 |
T2AI 97." |
172 |
T3AJ 97 2" |
246 |
|
|
|
|
|
|
Мак- |
|
На |
|
|
|
|
|
си- |
|
|
|
|
|
Вра |
маль- |
||
руж |
|
|
|
|
|||
|
|
Расход |
Часто |
щаю |
ный |
||
ный |
Длина, |
Масса, |
|||||
та вра |
щий |
пере |
|||||
диа |
мм |
кг |
(вода), |
щения, |
мо |
пад |
|
метр, |
|
|
л/с |
с"1 |
мент, |
дав |
|
мм |
|
|
|
||||
|
|
|
|
Н-м |
ления, |
||
|
|
|
|
|
|
МПа |
|
Для направленного бурения |
|
|
|
||||
127 |
6590 |
550 |
10 |
17,17 |
204 |
4,0 |
|
189 |
8380 |
1420 |
30 |
12,5 |
ИЗО |
5,0 |
|
189 |
4940 |
740 |
30 |
12,5 |
560 |
2,5 |
|
260 |
7600 |
2300 |
50 |
10,33 |
2110 |
4,7 |
|
Для вертикального бурения |
|
|
|
||||
120 |
— |
— |
— |
— |
— |
- |
|
127 |
9070 |
755 |
10 |
17,17 |
‘ 269 |
5,3 |
|
127 |
15240 |
1255 |
10 |
17,17 |
538 |
9,7 |
|
189 |
11260 |
1855 |
30 |
14,83 |
1920 |
10,1 |
|
189 |
15500 |
2645 |
30 |
14,83 |
2940 |
14,6 |
|
189 |
19740 |
3435 |
30 |
14,83 |
3930 |
19,1 |
|
242 |
15575 |
4450 |
41,6 |
12,05 |
3685 |
11,0 |
|
242 |
21045 |
6050 |
41,6 |
12,05 |
5521 |
15,7 |
12 типов турбобуров для направленного бурения предназна чены 4 типоразмера с диаметрами корпуса 127, 189 и 260 мм.
Отличительной особенностью турбобуров фирмы "Neyrfor" является наличие лабиринтного уплотнения выход ного вала, выполненного в виде 8 ступеней дисков ротора и статора. Лабиринтное уплотнение установлено над нижней радиальной опорой под отверстиями в валу, через которые буровой раствор подается к долоту.
Корпус турбобура при необходимости может быть отцен трирован (турбобуры T3AI 774", T2FI 5м, T2AI 774и, T2AI 972", TFI 5", T3AI 972".
В табл. 7.12 приведены технические характеристики тур бобуров фирмы "Eastman”. Для направленного бурения пред назначено 5 типоразмеров турбобуров с диаметром корпуса 130 и 171 мм. Всего фирма имеет 12 типоразмеров турбобура. Турбобуры фирмы "Easman" шпиндельные; полумуфта, со единяющая валы турбинной секции и шпинделя, передает вращающий момент несколькими шлицами (шпонками), а осевое усилие — плоским торцом. Лопатки турбины выпол нены коническими с расширением к периферии, при этом роторы не имеют ободов.
|
|
|
|
|
|
Макси |
|
|
Наруж |
Расход |
Частота |
Вращаю |
маль |
|
Число |
ный |
||||
Тип |
ный |
(вода), |
враще |
щий |
перепад |
|
турбины |
диаметр, |
л/с |
ния, с -1 |
момент, |
дав |
|
|
|
мм |
|
|
Н-м |
ления, |
|
|
|
|
|
|
МПа |
|
|
Для направленного бурения |
325 |
3,0 |
||
б1/»" |
60 |
130 |
18,9 |
15,67 |
||
б1/!" |
90 |
130 |
18,9 |
15,67 |
485 |
4,4 |
63/ " |
50 |
171 |
31,5 |
16,67 |
475 |
2,4 |
67" |
64 |
171 |
31,5 |
16,67 |
600 |
3,4 |
6VJ" |
76 |
171 |
31,5 |
16,67 |
720 |
4,0 |
|
|
Для вертикального бурения |
310 |
2,9 |
||
б1/-" |
50 |
130 |
20,5 |
16,97 |
||
57" |
100 |
130 |
20,5 |
16,97 |
620 |
5,4 |
' в |
125 |
130 |
18,9 |
15,67 |
680 |
5,8 |
^бУо”/ 8 |
||||||
5У«”J |
150 |
130 |
20,5 |
16,97 |
925 |
7.8 |
/ в |
200 |
130 |
20,5 |
16,97 |
1235 |
10,3 |
5УоМ |
||||||
67" |
125 |
171 |
31,5 |
16,67 |
1172 |
6,3 |
6V4”-7V ;' |
100 |
|
34,7 |
18,23 |
1150 |
6,2 |
Т а б л и ц а 7.13
Краткие технические характеристики турбобуров фирмы ‘Turboservise"
|
|
Число |
|
|
|
Вра |
|
|
Расход |
Частота |
Давле |
щаю |
|
Тип |
ступеней |
щий мо |
||||
и тип |
(вода), |
враще |
ние, |
мент, |
||
(диаметр, мм) |
турби |
л/с |
ния, с"1 |
МПа |
Н-м |
|
|
|
ны, шт. |
33.3 |
16 |
2.4 |
814 |
V w V ? Z |
61N |
|||||
(от 254 до |
193,7) |
110N |
35,0 |
12,0 |
4.7 |
1589 |
|
|
115Р |
32.5 |
14,7 |
6.7 |
1638 |
|
|
150N |
33.3 |
11.5 |
5.3 |
1962 |
|
|
165Р |
30 |
13.6 |
7.6 |
1726 |
|
|
180N |
31.7 |
11 |
6.3 |
2119 |
|
|
200N |
30.8 |
10,1 |
6.7 |
2237 |
|
|
215Р |
16,7 |
12,1 |
8.2 |
2168 |
L, М |
|
|
|
24.3 |
4.0 |
294 |
(от 127 до |
142,9) |
40N |
17.5 |
20.3 |
7.1 |
510 |
|
|
140N |
12.5 |
16.3 |
8.5 |
618 |
|
|
240N |
10 |
21,5 |
2,75 |
990 |
Y (95,2) |
|
100N |
10 |
|||
|
|
200N |
8 |
17,2 |
3.5 |
1265 |
В табл. 7.13 и 7.14 приведены технические характеристики турбобуров фирмы “Turboservice". Общее число типоразме ров турбобуров достигает 25, при этом для направленного бурения предназначено 4 типоразмера турбобуров. Турбобу ры оснащаются турбинами двух типов (N нормальные,

|
|
|
|
|
|
|
Макси |
Мак- |
|
|
Число |
Наруж |
|
|
|
маль |
си- |
||
|
|
Расход |
Частота |
маль- |
|||||
|
|
ный |
|||||||
Тип |
ступе |
ный |
Длина, |
Масса, |
ный |
||||
(вода), |
враще |
вра |
|||||||
ней тур |
диа |
мм |
кг |
пере |
|||||
|
л/с |
ния, с~1 |
щаю |
||||||
|
бины |
метр, |
|
пад |
|||||
|
|
|
|
щий |
|||||
|
|
мм |
|
|
|
|
давле |
||
|
|
|
|
|
|
момент, |
|||
|
|
|
|
|
|
|
Нм |
ний, |
|
|
|
|
|
|
|
|
МПа |
||
|
|
|
|
|
|
|
|
||
|
|
|
Для направленного бурения |
|
|
|
|||
678" |
116 |
168 |
8371 |
1092 |
25 |
15,53 |
865 |
4,8 |
|
77а" |
115 |
190 |
8565 |
1320 |
30 |
11,87 |
1242 |
4,7 |
|
8” |
100 |
203 |
8900 |
1600 |
45 |
12,83 |
1995 |
6,2 |
|
9" |
120 |
228 |
9025 |
1935 |
55 |
12,87 |
3548 |
7,7 |
|
IQ |
100 |
254 |
8925 |
2365 |
65 |
13,17 |
4799 |
9,7 |
|
|
|
|
Для вертикального бурения |
|
|
|
|||
S'' |
240 |
127 |
13795 |
1006 |
17 |
14,67 |
543 |
9,6 |
|
67fl" |
226 |
168 |
15240 |
2035 |
25 |
13,53 |
1686 |
9,4 |
|
7У2" |
241 |
190 |
15872 |
2521 |
30 |
11,87 |
2583 |
9,8 |
|
8" |
197 |
203 |
15890 |
3145 |
38 |
10,25 |
2810 |
8,8 |
|
9" |
215 |
228 |
14825 |
3873 |
45 |
10,53 |
4246 |
9,5 |
|
10" |
200 |
254 |
15900 |
4336 |
45 |
9,17 |
4601 |
9,3 |
Регулирование характеристики турбобура
Как было показано выше, турбины турбобу ров при прокачивании через их лопаточный аппарат посто янного расхода жидкости развивают крутящий момент, пря мо пропорциональный частоте вращения ротора. Эта зави симость для всех типов турбин описывается известным урав нением Эйлера (7.1), из которого вытекает связь крутящего момента на турбине с частотой вращения ее ротора (на экс тремальном режиме). Поскольку при заданном значении рас хода бурового раствора и ограниченном числе ступеней (как правило, 300—330) турбина должна обеспечивать определен ный тормозной крутящий момент, необходимый для устой чивой работы турбобура; частота вращения вала при холос том режиме также не может быть ниже вполне определенной величины. Расчеты показывают, что при О = 30 л/с, М г = = 4000 Н-м, z = 300 значение пх не может быть ниже 18 с’ 1.
С целью снижения частоты вращения вала турбобура, в первую очередь на холостом режиме, при сохранении преж них значений крутящего момента, т.е. для увеличения отно шения Мт/п х, применяют различные способы регулирования
характеристики турбобура. Рассмотрим основные из них, которые используются в опытных конструкциях турбобу ров.
Клапанное регулирование. Наиболее эффективное регули рование характеристики турбобура, т.е. максимальное сни жение л при том же значении М, достигается при регулиро вании расхода жидкости, протекающей через лопатки тур бин, с помощью клапанного устройства. При этом в зависи мости от схемы забойного двигателя клапан устанавливается в бурильных трубах (при обычном турбобуре) или в полом валу турбобура. Последний вариант представляется наиболее целесообразным, так как часть бурового раствора при этом не сбрасывается в кольцевое пространство скважины над турбобуром, а суммируясь с основным потоком, поступает непосредственно на долото.
Клапанное регулирование применяется только при исполь зовании турбины с уменьшающимся к тормозному режиму перепадом давления. При этом открытие клапана осуществ ляется автоматически, за счет изменения перепада давления на трубине, в зависимости от режима работы. На тормозном режиме клапан полностью закрыт и вся жидкость поступает на лопатки турбины. По мере разгона турбобура перепад давления увеличивается и через клапан сбрасывается все больше жидкости. Максимальное открытие клапана соответ ствует холостому режиму работы турбобура.
Клапанное регулирование позволяет получить нелинейную, прогнутую к началу (в М — п координатах) моментную ха рактеристику, что имеет большое практическое значение, так как при этом уменьшается минимально устойчивая частота вращения вала турбобура.
Частоту вращения на холостом режиме можно определить
по формуле |
|
л' = лх / Va, |
(7.7) |
где лх — частота вращения вала турбобура без клапана на холостом режиме.
Как видно из формулы (7.7), возможность максимального снижения л определяется значением а, которое для реальных турбин с уменьшающимся к тормозному режиму перепадом давления, например для А7НЧС, составляет 1,95.
Регулирование с помощью ступеней гидродинамического торможения. С целью снижения частоты вращения вала тур бобура на холостом режиме применяют ступени гидродина
мического торможения (ГГ). Ступени ГГ представляют собой плоскую решетку, профили статора и ротора которой на клонены к плоскости, перпендикулярной оси вала турбобура под одним углом. При вращении такой решетки в среде по тока бурового раствора на роторе ступени ГТ возникает кру тящий момент, пропорциональный частоте вращения и на правленный в сторону, противоположную движению вала. Важной особенностью гидродинамического торможения явля ется то, что при п = 0 крутящий момент на ступенях ГТ не возникает и, следовательно, тормозной момент турбины не уменьшается.
Результирующая частота вращения вала турбобура опреде ляется по формуле
л1=л/(1+((4), |
(7.8) |
где л,, л — частота вращения вала турбобура соответственно при использовании ступеней ГТ и без ступеней ГТ; z lt z — число ступеней соответственно ГТ и турбины; ср — коэффи циент, определяющий эффективность гидротормоза, ф =
=0,9+1,25.
Для современных конструкций плоских гидродинамичес
ких решеток торможения коэффициент ф = 0,9+1,0. Перепад давления на ступенях гидроторможения практиче
ски не зависит от режима работы |
турбобура и определяется |
по эмпирической формуле |
|
Р = | 0 2pz, |
(7.9) |
где р — перепад давления, МПа; | |
— коэффициент гидравли |
ческого сопротивления одной ступени гидроторможения. О —расход бурового раствора, м3/с; р — плотность бурово го раствора, кг/см3; z — число ступеней гидротормоза.
Для турбобуров диаметрами 240 и 195 мм, значение £ со ставляет 0,003 и 0,0065 соответственно.
Регулирование путем сочетания турбин разного типа.
Этот способ заключается в сборке на одном валу турбобура разнотипных турбин, работающих при одинаковом расходе бурового раствора. Его следует применять в случае, когда в наличии имеются два типа турбин и более, каждый из кото рых в отдельности не удовлетворяет требованиям технологии
бурения.
Следует отметить, что применение комбинации двух (и более) типов турбин, либо турбины и гидротормоза, собран
ных на одном валу, энергетически менее выгодно, чем ис пользование одного (оптимального) типа турбины при том же числе ступеней, так как в каждом конкретном случае перепад давления на турбине оптимального типа будет ниже, чем та кой же, получающийся при сочетании турбин двух типов и более. Однако такую турбину для каждого конкретного слу чая бурения нужно специально спроектировать и изготовить. А наличие, например, двух типов турбин — тихоходной и быстроходной, либо турбины и гидротормоза позволяет опе ративно получать вполне приемлемую характеристику турбо бура и в случае необходимости изменять ее.
Так как характеристики турбин разные, то суммарный крутящий момент турбобура образуется в результате сложе ния моментов, развиваемых каждым типом турбин:
Mz ='ZMi, |
- |
(7.10) |
где М, — крутящий момент, развиваемый турбиной /-го типа. Суммарный перепад давления
Pr =ZPi . |
(7.Н) |
где р, — перепад давления на турбине /-го типа.
Результирующая частота вращения на холостом режиме определяется из выражения
nz — HM jZj |
(7.12) |
где nz — результирующая частота вращения вала турбобура на холостом режиме; AfT/ — тормозной момент турбины /-го типа; лХ| — частота вращения турбины /-го типа на холостом режиме.
В частности, если используются два типа турбин, то пара метры результирующей энергетической характеристики оп ределяются по формулам:
тормозной момент
Mz = MnZi + M T2Z2; |
(7.13) |
перепад давления
частота вращения на холостом режиме |
|
|
nz = Mf^Z\ + AfT2Z2 |
(7.15) |
|
Mjl - Z , + - |
M.т2 |
|
ЛХ1 |
* 2 |
|
Л , 2 |
|
где Мх1, р,, лх1, z, — соответственно тормозной момент од ной ступени, перепад давления на одной ступени, частота вращения на холостом режиме, число ступеней турбины 1-го типа соответственно; Мт2, р2, лх2, z2 — то же, для турбины 2-го типа.
Регулирование с помощью перетоков жидкости в турбине.
Исследованиями установлено, что при увеличении радиально го зазора между ротором и статором турбины с уменьшаю щимся к тормозному режиму перепадом давления в отличие от турбин нормального типа возрастает прогиб линии мо ментов. Это объясняется тем, что зазор выполняет функцию нерегулируемого гидросопротивления, а рабочий поток жид кости через турбину разделяется на два, один из которых поступает на лопатки турбины, а другой — в зазор. В ре зультате изменения перепада давления на лопатках, который определяется режимом работы турбин, соотношение между двумя потоками меняется. Это явление было использовано при разработке новых турбин высокоциркулятивного типа с увеличенным радиальным зазором. Эти турбины, имеющие шифр А7ПЗ, имеют нелинейную моментную характеристику. Отношение Мх/л х у них в 1,35 раза выше, чем у обычных турбин. Кроме того, как уже отмечалось, прогиб линии мо ментов позволяет снизить минимально устойчивую частоту вращения.
Эффективность применения ступеней ГТ с такими турби нами значительно возрастает, что также объясняется наличи ем прогиба у линии момента этой турбины.
Проектирование характеристики турбобура
Для эффективного применения турбобура не обходимо правильно спроектировать его энергетическую ха рактеристику. При этом следует руководствоваться следую щими общими положениями.
1. Надежный контроль за режимом работы турбобура в процессе бурения возможен при режиме, когда механическая скорость проходки максимальная. Как правило, этот режим совпадает с экстремальным режимом работы турбобура или
располагается в непосредственной близости в правой зоне кривой мощности. Таким образом, все расчеты характерис тики турбобура имеет смысл вести для экстремального ре жима работы или режимов, близких к нему.
2.Следует помнить, что при недоиспользовании крутящего момента турбобура долота отрабатываются на излишне вы соких частотах вращения. Это приводит к недобору проход ки за рейс долота, и поэтому запас крутящего момента не должен быть излишне большим.
3.При турбинном бурении гидравлическая мощность, ко торую можно сработать в гидромониторных насадках долота, всегда намного меньше той, которую можно использовать при роторном способе бурения. Поэтому турбинное бурение предпочтительнее применять в разрезах, сложенных доста точно крепкими породами.
При бурении в мягких и пластичных породах необходимо
впервую очередь думать об очистке вооружения долота, что обеспечивается правильным и несимметричным расположе нием промывочных каналов долота. Вполне удовлетворитель ная очистка вооружения шарошек достигается при сработке
вдолоте перепада давления 5 МПа.
4.При турбинном бурении целесообразно использовать осевые нагрузки на долото, составляющие 60 —80 % тех, ко торые имеют место при роторном способе бурения анало гичных разрезов.
5.Использование одной и той же энергетической характе ристики турбобура в разных по буримости разрезах, напри мер в кварцитах и мягких глинистых сланцах, заведомо ста вит турбинный способ бурения в невыгодные условия. По этому тип сборки турбобура в каждом конкретном случае должен соответствовать физико-механическим свойствам про ходимых пород, гидравлической программе бурения и воз можностям применяемого бурового оборудования. Формиро вание необходимой характеристики осуществляется за счет ис пользования различного соотношения турбин и решеток ГТ.
Проектирование характеристики турбобура следует начи нать с определения так называемого удельного крутящего момента на долоте ш, выражающего функциональную связь между осевой нагрузкой на долото и крутящим моментом, необходимым для вращения долота:
т = M/G; |
(7.16) |
где т — удельный момент, м; М — крутящий момент, |
Н-м; |
G — осевая нагрузка на долото, Н. |
|
Удельные моменты для различных районов бурения и ти поразмеров долот определены в результате испытаний турбо- и электробуров и приводятся во многих источниках.
После определения т находят требуемый крутящий мо мент турбобура на экстремальном режиме:
М = mG. |
(7.17) |
При этом нагрузка на долото G выбирается исходя из ти поразмера долота, физико-механических свойств разбурива емых пород и других факторов.
Зная величину М, можно определить тормозной момент турбобура:
МТ = 2М. |
(7.18) |
Расход бурового раствора определяется исходя из воз можностей насосной группы буровой установки и имеюще гося бурильного инструмента. На рис. 7.8 показаны совме щенные характеристики бурового насоса (кривая 1) и гидрав лического тракта манифольд — бурильная колонна с доло том — скважина (кривая 2) без учета турбобура. Гидравличе ская характеристика насоса строится по паспортным данным, а для манифольда, бурильной колонны, долота и кольцевого пространства скважины определяется расчетным путем или экспериментально.
Рис. 7.8. Совмещенные гидравлические харак теристики
Точка пересечения кривых 1 и 2 определяет предельные возможности данного бурового насоса. Расход бурового рас твора Отах, соответствующий этой точке, является предель ным (не оптимальным) при бурении данной скважины ро торным способом. Для создания необходимой эффективной характеристики турбобура рекомендуется использовать зна чения расхода О, составляющие 60 —80 % Отах. Выбран ное значение О в большинстве случаев не должно превышать 0,07 л/с на 1 см2 площади забоя скважины.
Если в распоряжении проектировщика не имеется специ альных типов турбин, то они выбираются из серийных, вы пускаемых машиностроительными заводами. Пересчет пара метров характеристики турбобура со стендовых данных производится по формулам (7.6).
При практических расчетах допускается не учитывать по тери крутящего момента турбобура в шпинделе-и радильных опорах секций, так как серийный турбобур обычно работает в зоне, близкой к разгрузке осевой опоры, где эти потери не очень значительны.
Потери давления в проточных |
каналах турбобура (без уче |
||
та турбины) при расходе воды 20 |
л/с приведены ниже. |
|
|
Диаметр турбобура, мм.................................................. |
164; 172 |
195 |
240 |
Потери давления, МПа.................................................... |
0,7 |
0,4 |
0,2 |
Работа турбобура считается устойчивой до тех пор, пока обеспечивается как минимум двойной запас тормозного мо мента по сравнению с рабочим, хотя этот вопрос изучен в недостаточной степени. Регулирование рабочей частоты вра щения осуществляется изложенными выше способами. Расче ты ведутся по формулам (7.1) — (7.15).
Конечная цель расчетов заключается в определении числа ступеней турбины и ступеней ГТ (если это необходимо), обеспечивающих необходимые значения крутящего момента и частоты вращения при заданных расходах и плотности бу рового раствора. Разумеется, это число должно округляться для того, чтобы соответствовать целому количеству турбин ных секций.
Расчет характеристики турбобура целесообразно вести для нескольких вариантов использования имеющихся турбин и ступеней ГТ. Затем выбирается тот вариант, который обес печивает заданные параметры характеристики при мень шем перепаде давления на турбобуре, или тот, который дает возможность обходиться меньшим числом турбинных сек ций.
Испытания турбобуров
Испытания турбобуров в зависимости от по ставленных целей можно разделить на три последовательно проводимых этапа:
I — стендовые испытания небольшого комплекта турбин (не более шести ступеней);
II — стендовые испытания турбобуров;
III — промышленные испытания турбобуров.
Первый этап проводят на специализированных лаборатор ных стендах в течение 2 —3 дней в целях проверки энергети ческих характеристик турбин. В качестве бурового раствора, как правило, используют техническую воду. Лопастные аппа раты турбин могут быть выполнены как из алюминиевых сплавов, так и из сталей.
Второй этап проводят в целях проверки выходной энерге тической характеристики турбобура на стендах в условиях эксплуатации, приближенных к реальным. В качестве бурово го раствора можно применять глинистый раствор.
Третий этап проводится в целях определения технико экономических показателей и проверки показателей надеж ности.
7.2.2. ВИНТОБУРЫ. БУРЕНИЕ ВИНТОВЫМИ ЗАБОЙНЫМИ ДВИГАТЕЛЯМИ
История создания винтовых двигателей
Начиная с 40-х годов в б. СССР основным техническим средством для бурения нефтяных и газовых скважин являлись многоступенчатые турбобуры.
Именно широкое распространение турбинного способа бурения обеспечило ускоренное разбуривание нефтегазонос ных площадей Урало-Поволжья и Западной Сибири и тем самым позволило получать высокие темпы роста добычи нефти и газа.
Однако с увеличением средних глубин скважин и по мере совершенствования породоразрушающего инструмента и технологии роторного способа бурения в отечественной неф тяной промышленности с каждым годом росла тенденция отставания проходки за рейс долота — показателя, опреде ляющего технико-экономические показатели бурения.
Несмотря на определенные усовершенствования техники и технологии турбинного бурения показатели работы долот на протяжении ряда лет улучшались весьма незначительно. Хотя в 70-е годы началось разбуривание месторождений Западной Сибири, отличающихся благоприятными условиями бурения (мягкие породы, относительно неглубокие скважины), сред няя проходка за рейс по эксплуатационному бурению суще ственно отставала от аналогичного показателя в нефтяной промышленности США в 3—4 раза. Так, в 1981 —1982 гг. средняя проходка за долбление в США составила 350 м, в то время как в нашей стране этот показатель не превышал
90м.
Существенное отставание в проходке за долбление было
связано с тем, что в те годы отечественная практика бурения базировалась на высокоскоростном режиме бурения с при менением многоступенчатых безредукторныэс турбобуров, характеристики которых не позволяли получать частоту вращения менее 400 —500 об/мин с обеспечением необходи мых крутящих моментов и приемлемого уровня давления на сосов и, как следствие, эффективно использовать революци онные усовершенствования шарошечных долот (с прецизи онными маслонаполненными опорами и твердосплавным во оружением).
В связи с этим перед специалистами и организаторами бу рения в нашей стране встал вопрос о создании техники для низкооборотного бурения.
Перед отечественной нефтяной промышленностью встала дилемма: либо переходить к роторному бурению, либо со здать низкооборотный забойный двигатель.
К этому времени имелись определенные успехи роторного бурения глубоких скважин в ряде районов (Северный Кавказ, Западная Украина и др.). Однако технически, экономически и психологически нефтяная промышленность не была готова к развитию роторного бурения. За многие годы государствен ной поддержки турбинного бурения существенно отстала от мирового уровня техника роторного бурения: не имелось бу рильных труб и буровых установок высокого технического уровня.
Переход на роторный способ бурения в основных регио нах страны снизил бы темпы развития отрасли, так как промышленность не располагала необходимыми средствами для строительства новых заводов и эксплуатационных баз или закупки за рубежом новых технологий.
Таким образом определился доминирующий способ буре
ния на базе низкооборотных забойных двигателей — винто вые двигатели.
Решение проблемы создания забойного гидравлического двигателя с характеристиками, отвечающими требованиям новых конструкции долот, было найдено в переходе от ди намических машин, каким являются турбобуры, к объемным.
Первым работоспособным, нашедшим промышленное применение, оказался гидродвигатель, представляющий собой обращенный насос Муано1, относящийся к планетарно роторному типу гидромашин.
Работы по созданию опытных образцов винтовых забой ных двигателей (ВЗД) начались практически в США и нашей стране в середине 60-х годов.
Американские специалисты фирмы "Smith Tool" разрабо тали ВЗД (на западе их называют PDM-positive displacement motors) для наклонно направленного бурения как альтернати ву турбобурам, а в нашей стране, родине турбинного буре ния — как техническое средство для привода низкооборот ных долот.
Многолетние поисковые научно-исследовательские работы во ВНИИБТ по совершенствованию забойных гидравличе ских двигателей привели в 1966 г. к появлению предложенного М.Т. Гусманом, С.С. Никомаровым, Н.Д. Деркачем, Ю.В. За харовым и В.Н. Меныпениным нового типа ВЗД, рабочие органы которого впервые в мировой практике выполнены на базе многозаходного винтового героторного механизма, вы полняющего функцию планетарного редуктора.
Впоследующие годы во ВНИИБТ и его Пермском филиале Д.Ф. Балденко, Ю.В. Вадецким, М.Т. Гусманом, Ю.В. Захаро вым, А.М. Кочиевым, С.С. Никомаровым и другими исследо вателями были созданы основы теории рабочего процесса, конструирования и технологии изготовления, разработана технология бурения винтовыми двигателями.
Врезультате многолетнего опыта бурения с использовани ем гидравлических забойных двигателей (турбобуров и ВЗД) сложился комплекс технических требований к современному
забойному двигателю.
1. Характеристики двигателя должны обеспечивать: высокий уровень крутящего момента (3 кН-м и более для
долот диаметрами 215 —243 мм); частоту вращения выходного вала в диапазоне 100—200 и
XR . Moineau (1887 —1948) — французский инженер, изобретатель одно винтовых гидравлических и пневматических машин.
500 —800 об/мин соответственно для шарошечных и алмаз ных долот;
высокий КПД двигателя для эффективного использования гидравлической мощности насосов;
пропорциональную зависимость между расходом бурового раствора и частотой вращения, а также между крутящим моментом и перепадом давления с целью эффективного управления режимом бурения.
2.Рабочие органы и другие узлы двигателя должны быть выполнены в износо- и термостойком исполнении, обеспе чивающем использование бурового раствора любой плот ности и вязкости, в том числе с содержанием тампони рующих материалов.
3.Конструктивная компоновка двигателя и проектные запасы прочности его узлов должны обеспечивать:
стойкость двигателя, достаточную для стабильной работы с современными шарошечными и алмазными долотами;
возможность искривления корпуса двигателя при наклонно направленном бурении;
возможность установки на корпусе двигателя опорноцентрирутощих элементов при проводке наклонно направлен ных и горизонтальных скважин.
4. Диаметральные и осевые размеры двигателя должны обеспечивать:
проведение буровых работ долотами различного диаметра, включая малогабаритные;
эффективную проводку наклонно направленных и гори зонтальных скважин;
использование стандартного ловильного инструмента. Анализ конструкций и характеристик забойных гидравли
ческих двигателей различного типа показывает, что ни один из них не отвечает в полной мере всем перечисленным тре бованиям; в большей степени указанным требованиям соответстуют ВЗД с многозаходными винтами.
Принцип действия ВЗД
Винтовые двигатели относятся к объемным роторным гидравлическим машинам.
Согласно общей теории винтовых роторных гидравличес ких машин элементами рабочих органов (РО) являются:
1) статор двигателя с полостями, примыкающими по кон цам к камерам высокого и низкого давления;
398
Рис. 7.0. Упрощенная схема двигателя:
I —корпус; 2 — ротор; 3 — вал; 4 , 5 — осе вой и радиальный подшипники; 6 — долото
2)ротор-винт, носящий назва ние ведущего, через который кру тящий момент передается исполни тельному механизму;
3)замыкатели-винты, носящие название ведомых, назначение ко торых уплотнять двигатель, т.е. препятствовать перетеканию жид кости из камеры высокого давле ния в камеру низкого давления.
В одновинтовых гидромашинах используются механизмы, в кото рых замыкатель образуется лишь двумя деталями, находящимися в постоянном взаимодействии, — статором и ротором.
Упрощенная схема двигателя показана на рис. 7.9.
При циркуляции жидкости через РО в результате действия перепада давления на роторе двигателя со здается крутящий момент, причем винтовые поверхности РО, взаимно замыкаясь, разобщают области вы сокого и низкого давления. Следо вательно, по принципу действия винтовые двигатели аналогично поршневым, у которых имеется винтообразный поршень, непре
рывно перемещающийся в цилинд ре вдоль оси двигаталя.
Для создания в РО двигателя по лостей, теоретически разобщенных от областей высокого и низкого давления (шлюзов), необходимо и достаточно выполнение четырех условий (рис. 7.10):
1) число зубьев z, наружного элемента (статора) должно быть на единицу больше числа зубьев z2 внутреннего элемента (ротора):
Рис. 7.10. Рабочие органы ВЗД на продольном и поперечном разрезах
Zj = z2 + 1;
2) отношение шагов винтовых поверхностей наружного элемента (статора) Т и внутреннего элемента (ротора) t долж но быть пропорционально отношению числа зубьев: T/t =
Zj/z2,
3)длина рабочего органа I должна быть не менее шага винтовой поверхности наружного элемента: I > Т;
4)профили зубьев наружного и внутреннего элементов должны быть взаимоогибаемы и находиться в непрерывном контакте между собой в любой фазе движения.
Отличительным параметров ВЗД, во многом определяю щим его выходные характеристики, является число зубьев РО, называемое кинематическим отношением i:
i= z2 : z,.
Кратность действия, зависящая от кинематического отно шения РО, равна числу заходов внутреннего элемента z и оп ределяет рабочий объем ВЗД:
V=z2ST,
где S — площадь живого сечения РО.
Кратность действия является основным параметром ВЗД что наглядно иллюстрируется теоретическими кривыми (рис. 7.11), полученными во ВНИИБТ в 1972 г. и в дальнейшем по всеместно используемыми при обоснований выбора рабочего органа ВЗД.
Отечественные ВЗД имеют многозаходные РО. Зарубеж ные компании производят двигатели как с однозаходным ро тором, так и с многозаходными РО.
Рис. 7.11. Зависимость момента и частоты вращения ВЗД от кинематического отношения рабочих элементов
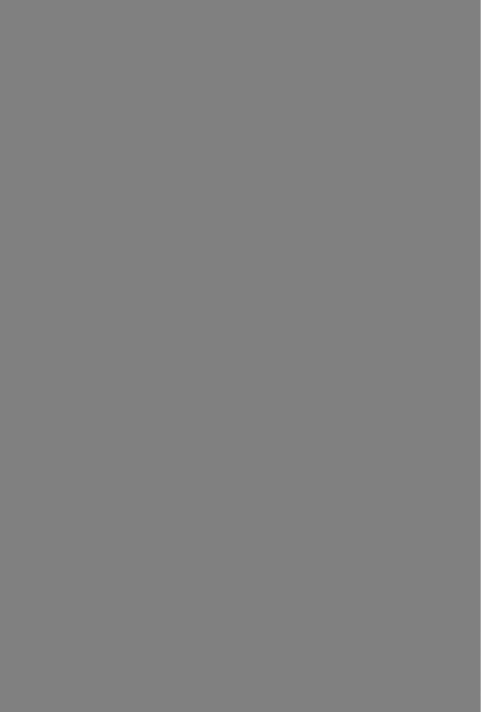
Рис. 7.12. Винтовой забойный двигатель ДЗ-172:
1 — статор; 2 — ротор; 3 — гибкий вал; 4, 5 —
корпусные подшипники; 6 — корпус; |
7 — вал; 8, |
9 — осевая и радиальная опоры; 1 0 |
— намолот- |
ный переводник |
|
номном переводнике непосредственно над двигателем или между трубами бурильной колонны.
Силовая секция включает в себя статор 1, ротор 2, соеди нение ротора и выходного вала 3 и корпусные переводники 4 и 5.
Шпиндельная секция состоит из корпуса 6, вала 7 с осе выми 8 и радиальными 9 опорами, наддолотного переводни ка 10.
Двигатели для наклонно направленного и горизонтального бурения. Эта серия представлена двигателями с наружными диаметрами от 60 до 172 мм и предназначена для бурения на клонно направленных (с большой интенсивностью искривле ния) и горизонтальных скважин.
Обладая конструктивными особенностями и рациональ ным критерием эффективности М/п, двигатели этой серии в отличие от турбобуров эффективно используются в различ ных технологиях наклонно направленного и горизонтального бурения, в том числе при зарезке и бурении вторых (дополнительных) стволов через окно в эксплуатационной колонне.
При использовании ВЗД в горизонтальном бурении реали зуются их преимущества по сравнению с турбобурами, в ча стности меньшая зависимость от диаметра, а также повы шенный удельный момент двигателя. Это позволяет сконст руировать силовую секцию длиной 1 —2 м с наружным диа метром, существенно меньшим, чем у турбобура для анало гичных целей.
В результате проведенных в 90-х годах НИОКР ВНИИБТ создана новая серия забойных двигателей типа ДГ диаметром 60—172 мм (табл. 7.17) для проводки новых горизонтальных скважин и бурения дополнительных стволов.
При проектировании этой серии двигателей использовался 25-летний опыт конструирования ВЗД общего назначения и в то же время учитывались требования технологии горизон тального бурения.
Основные особенности двигателей серии ДГ: уменьшенная длина, достигаемая сокращением как сило
вой, так и шпиндельной секции, причем силовая секция, как правило, выполняется двухшаговой, что обеспечивает необ ходимую мощность и ресурс РО;
уменьшенный наружный диаметр (108 мм против 120 мм; 155 мм против 172 мм), что при сохранении оптимальных характеристик ВЗД обеспечивает надежную проходимость двигателя с опорно-центрирующими элементами в стволе
404
скважины и улучшенную гидродинамическую ситуацию в затрубном пространстве;
многообразие механизмов искривления корпуса (жесткий искривленный, регулируемый переводники, корпусные шар ниры с одной или двумя ступенями свободы), что позволяет использовать различные технологии проводки скважин;
возможность размещения на корпусе двигателя опорноцентрирующих элементов;
усовершенствованное соединение ротора и вала шпинделя, гарантирующее надежную работу с большими углами пере коса.
Технические характеристики серии ДГ представлены в табл. 7.17.
Двигатели для ремонта скважин. Двигатели, применяемые в ремонте нефтяных и газовых скважин, выпускаются под шифром Д с наружным диаметром 108 мм и менее (см. табл. 7.17).
Диапазон наружных диаметров, конструкции двигателей, а также их характеристики позволяют использовать эти маши ны для всевозможных буровых работ, встречающихся в ре монте скважин.
ВЗД используются при разбуривании цементных мостов, песчаных и гидратных пробок, фрезеровании труб, кабелей электропогружных насосов и прочих предметов. Эти двига-
Т а б л и ц а 7.17
Винтовые забойные двигатели для бурения скважин дополнительных стволов и капитального ремонта (новая серия - разработки 00-х годов)
Обо |
Диа- |
О б |
Шаг |
Чис |
Расход |
Крутящий |
Часто |
Пере |
||
щая |
ста |
ло |
жидко |
та вра |
пад |
|||||
значение |
метр, |
дли |
то |
ша |
сти, |
момент, |
ще |
давле |
||
двигателя |
мм |
на, |
ра, |
Н-м |
ния, |
ния, |
||||
гов |
л/с |
|||||||||
|
|
мм |
мм |
|
|
с"1 |
МПа |
|||
|
|
|
|
|
|
|||||
Д48 |
48 |
1850 |
200 |
3 |
0,5-1,5 |
60 -80 |
4,1-6,7 |
4,0-5,0 |
||
ДГ60 |
60 |
2550 |
225 |
3 |
1 -2 |
70 |
-100 |
3,0-6,0 |
4,5-5,5 |
|
Д95 |
95 |
2855 |
630 |
2 |
6 -1 0 |
600 - 900 |
2,0-3,3 |
4,5-6,0 |
||
Д295 |
95 |
3580 |
630 |
3 |
6 -1 0 |
800 |
-1200 |
2,0-3,3 |
6,0-9,0 |
|
Д595 |
95 |
3580 |
945 |
2 |
6 -1 0 |
900 |
-1400 |
1,3-2,2 |
4,5-6,0 |
|
ДГ95 |
95 |
2680 |
630 |
2 |
6 -1 0 |
600 - 900 |
2,0-3,3 |
4,5-6,0 |
||
А108 |
108 |
2930 |
640 |
2 |
6 -1 2 |
800 |
-1300 |
1,3-2,5 |
3,5-5,5 |
|
Д2108 |
108 |
3690 |
640 |
3 |
6 -1 2 |
1200-1800 |
1,3-2,5 |
5,0-7,5 |
||
Д5108 |
108 |
3690 |
880 |
2 |
6 -1 2 |
1300-1900 |
0,8-1,6 |
3,5-5,5 |
||
ДГ108 |
108 |
2600 |
640 |
2 |
6 -1 2 |
800-1300 |
1,3-2,5 |
3,5-5,5 |
||
ДК-108-1 |
108 |
5000 |
975 |
1,5 |
' 3 - 6 |
2000 -2700 |
0,3-0,65 |
5,5-7,5 |
||
ДК-108-Н |
108 |
3000 |
640 |
2 |
6 -1 2 |
800-1300 |
1,3-2,5 |
3,5-5,5 |
||
ДК-108-Ш |
108 |
3000 |
625 |
2 |
6 -1 2 |
500 |
- 800 |
1,9-3,8 |
3,0-5,0 |
|
ДГ155 |
155 |
4330 |
680 |
3 |
24 -30 |
3500 |
- 4000 |
2,2-2,7 |
6,5-7,5 |
тели могут производить бурение как внутри насосно компрессорных труб, так и внутри эксплуатационной колон ны.
При проведении капитального ремонта внутри колонн может использоваться также двигатель Д1-127.
По своей конструкции ВЗД для ремонта скважин принци пиально не отличаются от двигателей общего назначения.
Наибольший интерес представляет многофункциональный двигатель ДК-108, разработанный ВНИИБТ по заказу ОАО "Газпром".
Особенность созданного двигателя — широкий диапазон его энергетических параметров, обеспечивающийся наличием в его комплекте трех модификаций рабочих органов с раз личными рабочими объемами, что позволяет использовать эти машины для самых разнообразных видов ремонтно восстановительных работ при капитальном ремонте скважин.
Элементы конструкций двигателей и их компоновок
Несмотря на многообразие типоразмеров винтовых двигателей их рабочие органы имеют общие осо бенности:
РО выполняются по одной кинематической схеме: непо движный статор и находящийся внутри него планетарно дви жущийся ротор;
направление винтовой поверхноста РО —левое, что обес печивает заворачивание реактивным моментом корпусных резьб ВЗД и резьб бурильных труб;
в зависимости от заданных характеристик двигателя РО выполняются как с однозаходным, так и многозаходным ро торами;
роторы изготавливаются из нержавеющей или легирован ной стали с износостойким покрытием, а обкладка стато ра — из эластомера (преимущественно резины), обладающего сопротивляемостью абразивному изнашиванию и работоспо собностью в среде бурового раствора.
Вотечественных двигателях первого поколения (Д1-172, Д2-172, Д2-172 м), выпускаемых в 70-х годах, РО имели не значительную длину, не превышающую 1 —1,5 шага винтовой поверхности статора.
Вдвигателях второго поколения, выпускаемых с начала 80-х годов, длина РО составляет 2 —3 шага статора.
Наиболее перспективна монолитная конструкция РО, обеспечивающая простоту и малодетальность машин.
Рабочие органы ВЗД комплектуются с натягом. Величина натяга зависит от диаметральных и осевых размеров РО, свойств промывочной жидкости и материала обкладки стато ра и оказывает существенное влияние на характеристики и долговечность двигателя.
Все отечественные винтовые двигатели, начиная с первых образцов, выпускаются в шпиндельном исполнении.
Под термином “ш п и н д е л ь " подразумевается авто номный узел двигателя с выходным валом с осевыми и ради альными подшипниками.
В большинстве случаев шпиндель может быть отсоединен без демонтажа силовой секции, при необходимости и на бу ровой.
Шпиндели отечественных ВЗД выполняются немаслонаполненными. Все узлы трения смазываются и охлаждаются буровым раствором. Отказ от использования маслонаполнен ных и герметизированных шпинделей объясняется как тра диционным подходом конструирования забойных двигате лей, так и практической целесообразностью иметь гидрома шину, обладающую примерно равным ресурсом отдельных узлов.
Шпиндель — один из главных узлов двигателя. Он переда ет осевую нагрузку на породоразрушающий инструмент, вос принимает реакцию забоя и гидравлическую осевую нагрузку, действующую в РО, а также радиальные нагрузки от долот и шарнирного соединения (гибкого вала).
В ряде случаев при использовании породоразрушающих инструментов с насадками (гидромониторное бурение) шпин дель должен выполнять функции уплотнения выходного вала, позволяя создавать необходимый перепад давления в насад ках долота.
Наиболее распространенная конструкция шпинделя вклю чает монолитный полый вал, соединенный посредством над долотного переводника в нижней части с долотом, а с помо щью муфты в верхней части — с шарниром.
Для восприятия осевых нагрузок используются как ради ально-упорные, так и упорные подшипники. Подшипники выполняются многорядными и сохраняют свою работоспо собность при выработке зазора (люфта) до 5 —7 мм.
В отечественных двигателях применяются радиально упорные подшипники качения:
с коническими дорожками качения (серия 128700), исполь-
зуемые в двигателях с наружными диаметрами 105, 108, 195 и
240мм;
стороидными дорожками качения (серия 296000), исполь
зуемые в двигателях с наружными диаметрами 85, 88 и
127мм;
стороидными дорожками качения и резиновым компен сатором типа ШШО (серия 538900), используемые в некото рых модификациях двигателей диаметром 172 мм;
скомбинированными дорожками качения, используемые в двигателях Д-48, Д1-54, ДГ-95, ДГ-108 (для увеличения нагру зочной способности при одновременном упрощении конст рукции тороидные дорожки для шаров этих опор располо жены непосредственно на валу).
Детали подшипников качения выполняются из специаль ной подшипниковой стали 55СМА или 55СМА5ФА (ТУ 14-1-
3189 —81) с пределом текучести 1100 МПа и ударной вязкос тью а = 800 кДж/м2. Твердость колец, контактирующих с шарами — 45 —47 HRC, а шаров — 58 —62 HRC.
Внекоторых моделях ВЗД используются непроточные многорядные подшипники скольжения (подпятник — диск). Выбор типа осевых подшипников зависит от условий эксплу атации ВЗД.
Многолетние стендовые и промысловые испытания под твердили преимущества упорных подшипников скольжения при эксплуатации двигателей в абразивной среде и при высо ких нагрузках. Недостаток подшипников скольжения — по вышенные механические потери, особенно при невысоких частотах вращения.
Вподпятниках используется резина марки ИРП-1226, а ра бочие поверхности контактирующих с ними дисков выпол
няются из цементируемой стали, закаленной |
до твердости |
45-48 HRC. |
шпинделя в |
Р а д и а л ь н ы е п о д ш и п н и к и |
большинстве случаев представлены парой трения скольжения резина — металл. Неподвижный элемент выполняется в виде резинометаллической детали, на рабочей эластичной поверх ности которой выполнены профильные канавки. Ответная деталь —металлическая, ее рабочая поверхность подвержена упрочнению.
В двигателях для наклонно направленного и горизонталь ного бурения радиальные подшипники выполняются в виде пары трения металл — металл. Однако из-за повышенных радиальных нагрузок, присущих ВЗД этого класса (вследствие действия отклоняющей силы на долоте), данный узел является
408
одним из самых недолговечных, определяющих межремонт ный период двигателя в целом.
Соединение ротора ВЗД и вала шпинделя представляет со бой один из основных узлов двигателя, определяющих долго вечность и надежность гидромашины в целом.
Механизм, соединяющий планетарно движущийся ротор с концентрично вращающимся валом, работает в тяжелых ус ловиях. Помимо передачи крутящего момента и осевой силы, этот узел должен воспринимать сложную систему сил в РО, характеризующуюся непостоянной ориентацией ротора.
В отличие от известных в технике соединений, передаю щих вращение между двумя насосными концентрическими вращающимися валами, рассматриваемое соединение в ВЗД является связующим звеном с ротором, совершающим плане тарное движение, причем за один оборот выходнрго вала ро тор z, поворачивается вокруг своей оси, соответственно со вершая z, циклов переменных напряжений.
Это обусловливает повышенные требования к цикличес кой прочности соединения, особенно при использовании многозаходных ВЗД.
Своеобразные условия работы соединения и невозмож ность использования готового технического решения обусло вили многообразие компоновок этого узла. Принципиально могут быть использованы четыре типа соединений на базе:
деформации одного или нескольких элементов конструк ции;
обеспечения свободы перемещения ротора за счет введе ния элементов с относительно большим люфтом;
шарнирных соединений; гибкого вала.
Первый и второй типы соединения ввиду существенных удельных нагрузок в ВЗД не нашли применения.
Ш а р н и р н ы е с о е д и н е н и я . Шарнирные со единения ВЗД прошли эволюцию от пальцевых шарниров (аналогичных автомобильным) до специальных конструкций, наиболее приспособленных для передачи динамических осе вой нагрузки и крутящего момента.
В первом поколении отечественных ВЗД применялись двухшарнирные соединения зубчатого типа с центральным шаром. Оно использовалось для передачи крутящих момен тов до 7000 Н-м при частоте вращения до 200 об/мин. Экс центриситет соединения доходил до 5 мм.
Шарнирные соединения ВЗД работают, как правило, в среде абразивных жидкостей. Поэтому надежная герметиза
ция шарниров является одним из основных направлений по вышения их работоспособности. Проблема герметизации ос ложняется тем, что полости, которые требуется изолировать, вращаются вокруг смещенных осей в условиях вибрации и значительного гидростатического давления. Поэтому гермети зирующие элементы должны быть гибкими и прочными при циклической нагрузке, а устройство для герметизации в це лом простым и надежным.
Сначала в шарнирах использовались простейшие резино вые уплотнения, в дальнейшем стали применять уплотнения сильфонного и манжетного типов (рис. 7.13).
Г и б к и е в а л ы . Существенный шаг, оказавший вли яние на подходы к конструированию ВЗД в целом, был сде лан в середине 70-х годов, когда ВНИИБТ выполнил комплекс научно-исследовательских работ и впервые в практике про ектирования ВЗД предложил конструкцию гибкого вала, за щищенную патентами.
К началу 90-х годов в большинстве типоразмеров ВЗД выпускаемых в России, для соединения ротора и выходного вала применяются гибкие валы. В двигателях с наружным ди аметром 88 мм и более гибкий вал размещается в расточке ротора, а в малогабаритных двигателях — ниже ротора.
В большинстве случаев гибкий вал ВЗД представляет собой металлический стержень круглого сечения с утолщенными концами. На концах выполняются присоединительные эле менты: гладкий конус или коническая резьба. Иногда гибкий вал выполняется полым со сквозным цилиндрическим кана лом для подвода рабочей жидкости высокого давления непо средственно к долоту. Для повышения циклической прочнос ти в месте перехода от заделки к рабочей части вала имеется конус с углом 5—15° или галтель.
Типичные конструкции гибких валов приведены на рис. 7.14.
Преимущества использования гибких валов заключаются в простоте конструкции и высокой технологичности, большом сроке службы, соизмеримом с ресурсом корпусных деталей
Рис. 7.13. Уплотнения для ВЗД
410
Рис. 7.14. Гибкий вал ВЗД
двигателя, а также в возможности реализации различных компоновок двигателей.
Опыт эксплуатации двигателей в наклонно направленном и горизонтальном бурении выявил недостаточную стойкость гибких валов при углах перекоса секций более 1°30'. В связи с этим в последних конструкциях двигатели типа ДГ стали оснащать шарнирно-торсионными соединениями.
Характеристики ВЗД
Характеристики ВЗД необходимы для выбора оптимальных параметров режима бурения и поддержания их в процессе долбления, а также для определения путей даль нейшего совершенствования конструкций ВЗД и технологии бурения с их использованием.
В последнее время внимание к характеристикам ВЗД все более повышается. Это связано с внедрением регулируемых приводов буровых насосов, для эффективного использования которых знание характеристик гидромашины становится не пременным условием; распространением новых технологий (наклонно направленное и горизонтальное бурение, бурение с использованием непрерывных труб), особенно чувствитель ных к изменению режимов работы ВЗД.
Современные программы бурения ведущих зарубежных фирм предусматривают стендовые испытания каждого гидро двигателя с целью получения их фактических характеристик. Несмотря на дополнительные затраты, это позволяет наибо лее эффективно использовать ВЗД, в частности, косвенно по давлению на стояке контролировать нагрузку на долото, что в конечном счете приводит к улучшению технико-эконо мических показателей процесса бурения.
В России стендовые испытания также стали проводить за воды —изготовители двигателей.
В общем случае различают с т а т и ч е с к и е и д и |
|
н а м и ч е с к и е |
характеристики ВЗД. |
Статические характеристики отражают зависимость между |
|
переменными гидродвигателя в установившихся режимах. |
|
Динамические |
характеристики определяют соответствую |
щие зависимости в неустановившихся режимах и обусловли ваются инерционностью происходящих процессов. К дина мическим относятся и пусковые характеристики гидродвига теля.
Статические характеристики ВЗД можно условно класси фицировать как стендовые и нагрузочные. Стендовые харак теристики (как функции от крутящего момента) определяют ся в результате испытаний гидродвигателя. Нагрузочные ха рактеристики (как функции от осевой нагрузки) чаще всего рассчитываются по стендовым для конкретных условий буре ния.
Типичные стендовые характеристики винтового двигателя представлены на рис. 7.15. По мере роста момента М перепад давления р увеличивается практически линейно, а частота вращения п снижается вначале незначительно, а при прибли жении к тормозному режиму — резко. Кривые мощности N и общего КПД ц имеют экстремальный характер.
Различают четыре основных режима: холостой (М = 0); оптимальный (максимального КПД); экстремальный (макси мальной мощности) и тормозной (л = 0).
п, об/мин


р, МПа
10г 2,0
М, кН м
Рис. 7.17. Влияние натяга в рабочих элементах на характеристику ВЗД: 1 — зазор 0,15 мм; 2, 3, 4 — натяг соответственно 0,15 и 0,3 мм
утечек при уменьшении натяга (увеличении зазора) снижают ся частота вращения и перепад давления в холостом режиме. При уменьшении 8 частота вращения в номинальном режиме (для двигателя Д1-195 номинальный крутящий момент принят равным 4 кН-м) существенно снижается (в 2 —3 раза при за зоре 0,6 мм по сравнению с натягом 0,3 —0,6 мм). Перепад давления в номинальном режиме мало зависит от натяга. При уменьшении натяга снижается амплитуда поперечных колеба ний корпуса двигателя и динамические нагрузки в РО и опо рах шпинделя.
По мере износа РО, что равносильно снижению натяга или появлению зазора в паре, рекомендуется в процессе бурения увеличивать расход жидкости.
Влияние расхода жидкости. Расход жидкости О является одним из параметров режима бурения. Чаще всего возмож ный диапазон изменения О определяется исходя из техноло гии бурения скважины и задается конструктору ВЗД вместе с другими исходными данными.
Стендовые испытания ВЗД различных типоразмеров пока-
зывают, что с увеличением расхода (рцс. 7.18) повышаются как тормозной момент и перепад давления, так и мощность, крутящий момент, частота вращения и перепад давления в экстремальном режиме; КПД гидродвигателя при увеличении Q в допустимом диапазоне изменяется незначительно.
Нижний предел расхода жидкости ограничивается нагру зочной способностью или устойчивостью работы двигателя. Верхний предел допустимого расхода жидкости ограничива ется тремя факторами:
высокими инерционными нагрузками при увеличении час тоты вращения;
КПД двигателя: при заданном натяге с определенного рас хода жидкости происходит снижение объемного т|. Это объ ясняется тем, что с увеличением частоты вращения и перепа да давления на длине линии контакта образуется односторон ний зазор, приводящий к разгерметизации РО и росту уте чек. Кроме того, с увеличением расхода растут и гидравличе ские потери в двигателе;
износом РО из-за повышенных контактных напряжений и
Рис. 7.18. Влияние расхода бурового раствора на характеристику ВЗД (рабочий режим)
скоростей скольжения в рабочей паре, а также скорости жидкости в каналах РО.
В случае, если ограничения по расходу не удовлетворяют требованиям гидравлической программы бурения, использу ется способ разделения потока жидкости через полый ро тор двигателя с помощью регулятора расхода.
7.2.3. ТУРБОВИНТОВЫЕ ГИДРАВЛИЧЕСКИЕ ДВИГАТЕЛИ
В последние годы отечественный парк забой ных гидравлических двигателей пополнился новым представи телем —турбовинтовым двигателем (ТВД).
Впервые схема турбовинтового агрегата была предложена в 1970 г. авторским коллективом ВНИИБТ в составе М.Т. Гу смана, Д.Ф. Балденко, А.М. Кочнева и С.С. Никомарова.
Турбовинтовые двигатели ТВД органично сочетают высо кую стойкость, свойственную турбобурам, и оптимальную энергетическую характеристику (высокий уровень отношения М/п при незначительном падении частоты вращения при на грузке двигателя), характерную для ВЗД.
Турбовинтовой двигатель можно отнести к редукторным турбобурам, в котором винтовая пара выполняет функции не только редуктора, но и стабилизирующего элемента при пе регрузках долота.
Несмотря на большую металлоемкость и сложность кон струкции, турбовинтовые двигатели в ряде случаев успешно конкурируют с ВЗД.
Это объясняется прежде всего их существенно большим ресурсом, что особенно привлекательно при использовании современных высокопроизводительных долот.
Двигательные секции ТВД конструктивно могут выпол няться в двух вариантах:
винтовая пара монтируется над турбинной секцией; винтовая пара монтируется между турбинной и шпиндель
ной секциями.
В первом варианте упрощается конструкция двигателя — проектируется лишь один узел соединения планетарного ро
тора.
Второй вариант менее предпочтителен, так как требует двух узлов соединения ротора.
2 7 - 1 1 2 5
Народу с гидравлическими машинами исполь зуют и электрические — электробуры. Электробур — это электрическая забойная машина, своеобразный электродвига тель, смонтированный в трубном корпусе малого диаметра и предназначенный для привода долота на забое скважины.
Современный электробур представляет собой, как прави ло, асинхронный маслонаполненный двигатель с короткоза мкнутым ротором.
Конструкция промышленного электробура была разрабо тана в СССР в 1937—1940 гг. группой инженеров (А.П. Ост ровский, Н.В. Александров, Ф.Н. Фоменко, А.Л. Ильский, Н.Г. Григорян и др.). Последующие опытно-конструкторские работы позволили значительно модернизировать электробур по сравнению с первыми образцами: была создана безредукторная машина, мощность на валу электробура была увели чена в 2 —3 раза (от 70 до 120—230 кВт) и народу с этим уменьшен наружный диаметр. Серийное производство элект робуров в СССР налажено с 1956 г.
В СССР до 1960 г. с помощью электробура было пройдено около 500 тыс. м скважин на нефть и газ. В настоящее время в роде районов страны этим способом ежегодно бурят 200250 тыс. м. Хотя указанный объем многократно уступает объему турбинного бурения в нашей стране, принципиальная схема подачи электрической энергии к забою скважины и использование погружного электрического двигателя для при вода долота имеют неоспоримые преимущества, однако кон структивные трудности, невысокие эксплуатационно технические показатели и большая стоимость машины на данном этапе пока сдерживают применение этого вида тех ники в бурении.
Размерный род электробуров предусматривает их выпуск с наружными диаметрами корпуса 164, 170, 185, 215, 240, 250 и 290 мм. Наиболее распространен электробур диаметром 170 мм. В обозначении электробура первое число — его на ружный диаметр, второе — число полюсов обмотки статора (например, Э215-10). Может добавляться буква "М", обозна чающая модернизированную модель, и 11Р" для редукторных турбобуров. Обозначение электродвигателя содержит сведе ния о наружном диаметре корпуса, общей длине магнитопровода с длиной немагнитопроводных пакетов и о числе полю сов. Например, маркировка МАГИ-17-658/6 расшифровывавется следующим образом: МАП — мотор асинхронный по-
418
гружной; 1 — для электробура; 17 — наружный диаметр корпуса в см; 658 — общая длина магнитопровода и немаг нитных пакетов статора в см; 6 — число полюсов.
Выпускаемый промышленностью электробур включает трехфазный асинхронный маслонаполненный двигатель А и маслонаполненный шпиндель Б на подшипниках качения (рис. 7.19).
В трубном корпусе электробура размещены пакеты маг нитопроводной стали статора 6; они разделены пакетами не магнитопроводной стали в местах расположения радиальных шариковых опор ротора. Пакеты ротора 7 с алюминиевой обмоткой насажены на полом валу двигателя 5. Ротор распо ложен в статоре с зазором 0,5 —0,6 мм на сторону. Внутрен няя полость двигателя заполнена сухим изоляционным мас лом. От внешней среды внутренняя полость двигателя изоли рована верхним 4 и нижним 8 сальниками. В сальники пода ется машинное масло. Для компенсации утечек масла через сальники и поддержания некоторого избыточного давления внутри двигателя, препятствующего попаданию промывочной жидкости внутрь, в верхней части электробура в лубрикаторной головке размещены лубрикаторы двигателя 3 и сальника 2. Внутри верхнего переводника проходит кабельный ввод от контактного стержня 1 до обмотки статора. Для восприятия веса вала в нижней его части над нижним сальником установ лен упорный шариковый подшипник.
Снизу к двигателю присоединяется шпиндель. В шпинделе находится многорядная осевая опора на шариковых подшип никах 10. Полый вал центрируется в корпусе с помощью ро ликовых и шариковых подшипников. Вал шпинделя соединен с валом двигателя посредством соединительной зубчатой муфты 9; в месте соединения валов находится шарнирное уплотнение для изоляции внутреннего пространства от про мывочной жидкости, поступающей к забою по внутреннему каналу в валу двигателя и шпинделя. Осевые нагрузки на по родоразрушающий инструмент полностью воспринимаются осевой опорой шпинделя и на вал двигателя не передаются. В нижней части шпинделя помещено сильниковое уплотнение 12. Шпиндель заполнен густым машинным маслом и оснащен лубрикатором 11. Избыточное давление лубрикатор создает за счет усилия сжатой пружины, которая давит на поршень. Под поршнем находится резерв масла, восполняющий его потери из шпинделя.
Асинхронные двигатели для электробуров имеют жесткую характеристику, т.е. диапазон изменения их частоты враще-
27* |
410 |
|
Рис. 7.19. Принципиальная схема электро |
/ а у — |
бура |
|
Рис. 7.20. Характеристика двигателя МАП1Д-25-617/10
ifift n rm
ния довольно ограничен. Ее изменение зависит от скольже ния ротора относительно поля статора:
п = лп( 1 - S),
где л — частота вращения ротора двигателя; лп — частота вращения магнитного поля статора, лп = 60//р,; / — частота тока; р — число пар полюсов (двигатели выпускают 10-, 8- и
6-полюсными); 5 — скольжение, при нормальной нагрузке скольжение 5 = 8+12 %.
Вращающий момент (Н м) асинхронного двигателя элект робура может быть подсчитан по формуле
М= - 2nf
mipU\ Y
пR2
+ {xl + c lx ’2)2
R' +C' T
где ш, — число фаз обмотки статора; Ux — напряжение на зажимах двигателя, В; R2 — приведенное омическое сопро тивление ротора, Ом; Rx — омическое сопротивление фазы обмотки статора, Ом; х{ — индуктивное сопротивление об мотки статора, Ом; х2 — приведенное индуктивное сопро тивление ротора, Ом; сх — коэффициент, зависящий от на пряжения на клеммах двигателя.
Как следует из формулы, вращающий момент .двигателя прямо пропорционален квадрату напряжения на его вводе. Снижение напряжения приводит к заметному падению вра щающего момента. В связи с этим необходимо учитывать потери напряжения в токоподводе от поверхности к двигате лю, а падение напряжения при кратковременных перегруз ках двигателя рекомендуется компенсировать некоторым повышением напряжения на вводе двигателя на 5 —10 % от номинального. Номинальное напряжение на клеммах элект робуров составляет 1000—1200 В в зависимости от типа дви гателя.
Характер зависимости вращающего момента двигателя МАП1Д-25-617/10 от частоты вращения вала двигателя приве ден на рис. 7.20.
На графике вращающего момента правая ветвь от точки максимума является областью устойчивой работы (рабочая область), левая — областью неустойчивой работы. При запу ске двигателя заметно снижается вращающий момент (зона провала) в процессе выхода на режим. В зоне провала вра щающий момент может падать до 60 % от номинального. Но так как двигатель запускают с малой нагрузкой, а маховой момент вращающихся деталей и инструмента мал, даже при уменьшенном моменте двигатель быстро увеличивает частоту
вращения вала.
Коэффициент полезного действия двигателя при номи нальной нагрузке составляет 66 —68 %. Поскольку механичес кие потери в шпинделе на опорах качения сравнительно не
велики, характеристику электробура можно принимать цо характеристике двигателя.
Электроэнергия к забойному двигателю подводится по секционированному кабелю, помещенному внутри бурильной колонны.
Токоподвод может осуществляться по трехили двухжиль ному кабелю. В последнем случае в качестве третьего провода используется бурильная колонна. Эта система питания носит название "два провода — земля" (сокращенно ДПЗ).
Система ДПЗ позволяет увеличить площадь сечения про ходного канала в бурильной колонне и таким образом спо собствует снижению потерь напора при циркуляции промы вочной жидкости по бурильной колонне. _
Каждую кабельную секцию помещают в отдельной бу рильной трубе, и ее концы закрепляют в трубе на опорах с втулками, обеспечивающими некоторое свободное провора чивание кабеля при соединении труб. Секции соединяют в единую цепочку с помощью контактных элементов — кон тактного стержня на верхнем конце и контактной муфты на нижнем. Контактный стержень защищен от механических повреждений защитным стаканом. Соединение контактных элементов происходит автоматически при свинчивании бу рильных труб, при этом контактный стержень входит в муф ту с некоторым натягом, обеспечивающим герметичность со единения от проникновения бурового раствора.
Для монтирования секций электрокабеля используют спе циальные бурильные трубы типа ЭБШ с гладкопроходным сечением. Они выпускаются диаметрами 140 и 114 мм с вы саженными наружу концами. Трубы изготовляют из стали групп прочности Д и Е.
Кабельный подвод электробура — одно из наиболее сла бых звеньев системы. Вследствие загрязнения и недостаточ ной герметичности соединений секций омическое сопротив ление изоляции снижается. Если при спуске инструмента на блюдается резкое падение сопротивления (первоначальное сопротивление собственно электробура 50 МОм), то спуск инструмента прекращают и выбраковывают трубы с низким сопротивлением в изоляции кабеля. В процессе работы в со единениях с недостаточной герметичностью происходят про бои. Пробои и разрывы электрической цепи могут происхо дить также вследствие поломки медных контактов в муфте и излома кабеля в местах его сращивания с контактными со единениями.
Для бурения с электробуром буровую установку оснащают
дополнительным электрооборудованием: распределительным устройством высокого напряжения, трансформатором, стан цией управления электробуром. На пульте бурильщика уста навливают дополнительные электрические контрольные при боры (вольтметр, амперметр) для контроля нагрузки электро бура, кнопки управления контактной системой, подающей напряжение на электробур, органы управления режимом ра боты автоматического регулятора. Автоматический регулятор управляет подачей инструмента в зависимости от загрузки двигателя и буримости горных пород.
Обладая всеми достоинствами, присущими забойным дви гателям (облегчение условий работы бурильной колонны, су щественное снижение износа бурильных труб в скважине, исключение затрат мощности на их холостое вращение и т.п.), электробур имеет неоспоримые преимущества по срав нению с гидравлическими забойными машинами:
режим работы электробура не зависит от расхода промы вочной жидкости, который в данном случае можно выбирать только по условию полной и своевременной очистки забоя от шлама;
режим работы электробура практически не зависит от свойств циркулирующего бурового раствора, что позволяет применять его при использовании утяжеленных растворов, газообразных агентов и при продувке;
токоподвод с поверхности к электробуру является каналом связи, позволяющим использовать забойные системы кон троля режима работы породоразрушающего инструмента и непрерывно следить за направлением ствола скважины;
при работе с электробуром открывается возможность ав томатизировать процесс бурения по данным забойных дат чиков для оптимального использования мощности двигателя;
поскольку электробур представляет собой маслонаполнен ный двигатель, все детали которого работают в среде, изоли рованной от бурового раствора, он меньше подвержен абра зивному износу и его рабочая характеристика остается прак тически неизменной в течение всего срока работы.
К недостаткам электробура относятся: высокая стоимость забойного двигателя, опасность потери дорогостоящей ма шины вследствие прихвата в скважине, ограниченный срок межремонтной работы вследствие недостаточной износо стойкости уплотнительных сальников электробура и недоста точной надежности системы токоподвода.
Перспективы развития буровых работ с применением эле ктробуров связаны с существенным повышением ресурса