
1286
.pdf
Рис. 3. Проект охранно-патрульного робота
Разработанные методологические основы дизайна наземных транспортных роботов апробировались в проекте охранно-патрульного робота совместно с ОАО «Ижевский радиозавод». Проект данного робота представлен на рис. 3.
Список литературы
1.Антипина Е.В., Ившин К.С. Особенности классификации в ди- зайн-проектировании робототехники // Молодые ученые – ускорению научно-технического прогресса в XXI веке: материалы II Всерос. науч.-техн. конф. / ИжГТУ им. М.Т. Калашникова. – Ижевск, 2013. –
С. 1006–1010.
2.Антипина Е.В., Ившин К.С. Робот как дизайн-продукт // Современные техника и технологии: материалы XIX Междунар. науч.-практ.
конф. – Т. 3; НИТПУ. – Томск, 2013. – С. 276–277.
3.Антипина Е.В., Ившин К.С. Разработка системы методов инжиниринга в дизайне роботов специального назначения // Технические университеты: интеграция с европейскими и мировыми системами образования: материалы VI Междунар. конф. / ИжГТУ им. М.Т. Калаш-
никова. – Ижевск, 2014. – С. 208–211.
4.Мосоров А.М., Мосорова Н.Н. Теория дизайна. Проблемы онтологического и методологического знания. – Екатеринбург: Солярис, 2004. – 412 с.
5.Барташевич А.А. Основы художественного конструирования: учебник для втузов. – Минск: Выш. шк., 1984. – 224 с.
6.Художественное проектирование / Б.В. Нешумов [и др.]. – М.: Просвещение, 1979. – 175 с.
51

Об авторах
Ившин Константин Сергеевич (Ижевск, Россия) – кандидат тех-
нических наук, профессор кафедры «Дизайн», Удмуртский государственный университет (УдГУ), (426034, г. Ижевск, ул. Университетская, 1; e-mail: ivshic@mail.com).
Антипина Елена Валерьевна (Ижевск, Россия) – аспирантка, ассистент кафедры «Дизайн», Удмуртский государственный университет
(УдГУ), (426034, г. Ижевск, ул. Университетская, 1; e-mail: antipinaelena@gmail.com).
52

УДК [621.431.73: 629.33]: 004.94
СОВЕРШЕНСТВОВАНИЕ ТЕХНИЧЕСКОГО ДИАГНОСТИРОВАНИЯ АВТОМОБИЛЬНЫХ ДВИГАТЕЛЕЙ НА ОСНОВЕ МЕТОДОВ ИМИТАЦИОННОГО МОДЕЛИРОВАНИЯ
А.А. Козин, Р.Н. Хмелев
Тульский государственный университет, Россия
Повышающиеся требования к характеристикам автомобильных двигателей ведут к усложнению конструкции ДВС и его систем управления. При этом роль технического диагностирования, являющегося основным компонентом технического обслуживания и ремонта автомобилей, постоянно возрастает. Предложенная математическая имитационная модель позволяет получить обширный статистический материал по изменению показателей рабочих процессов автомобильных двигателей при возникновении неисправностей.
Ключевые слова: имитационное моделирование, методы диагностирования, автомобильный двигатель, неисправность.
На сегодня процедура технического диагностирования включает в себя: поиск характера и причин неисправностей с использованием диагностических параметров, прямые и косвенные измерения, наблюдения, вычисления, логическую обработку результатов, приведение в действие органов управления и силовые воздействия на компоненты автотранспортного средства (АТС), использование нормативов и сведений о конструкции и функционировании АТС. Процедура технического диагностирования может чередоваться с частичной разборкой АТС, ремонтом или заменой компонентов [1].
Повышающиеся требования к двигателю внутреннего сгорания (ДВС) неизбежно ведут к усложнению конструкций двигателей и систем управления [2]. Как результат возрастает роль технического диагностирования, которое является важным компонентом обслуживания и ремонта АТС.
Стремительное развитие вычислительной техники привело к появлению доступных для эксплуатации комплексов технического диагно-
53
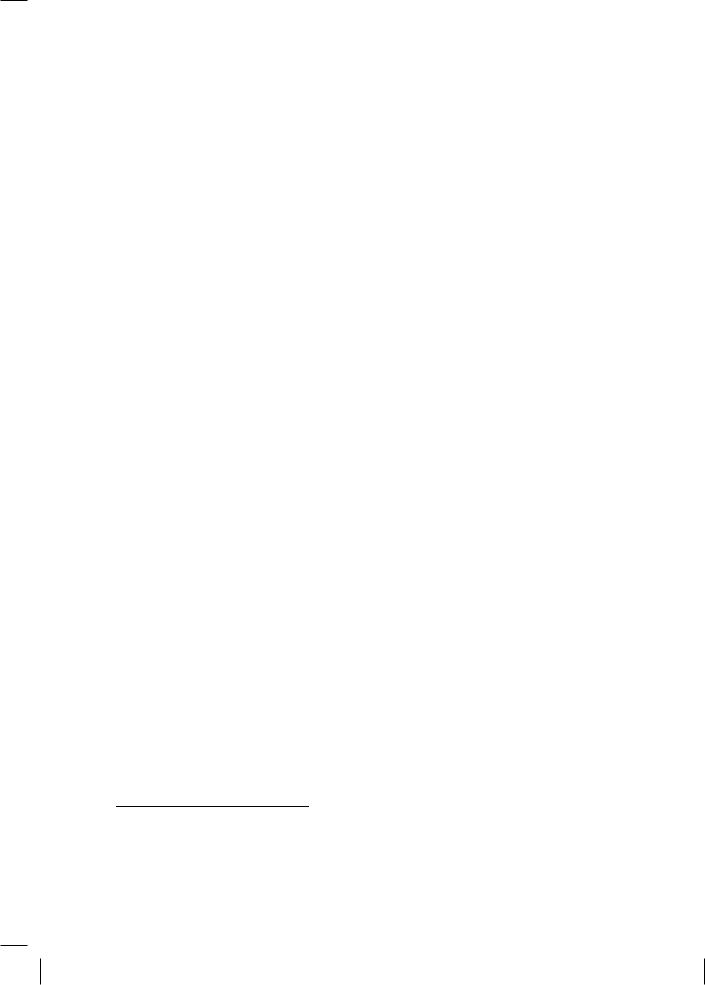
стирования, которые регистрируют показатели изменения рабочих процессов двигателя за один рабочий цикл: давление в цилиндрах, давление топлива и т.п. Создателей привлекает возможность получения большого количества информации об узлах и механизмах ДВС при использовании минимального числа измерительных датчиков [3]. В то же время существует проблема – сложность выявления конкретных причин, приводящих к изменениям сигналов. Различные дефекты идентично влияют на диагностические параметры, что является основной причиной, снижающей эффективность практического использования такого рода систем. Измерение сигналов в условиях эксплуатации всегда вносит погрешности и искажения.
Совершенствование технического диагностирования ДВС является актуальной задачей вследствие увеличения объема производств, расширения модельных рядов ДВС, усложнения элементов конструкции, различий условий эксплуатации. Кроме того, существующие методы диагностирования автомобильных двигателей не дают возможности распознать неисправности на ранней стадии развития дефекта [4].
Современный этап теоретических исследований в автомобилестроении характеризуется широким использованием математических моделей, сложность которых постоянно возрастает. Введение в процесс диагностирования методов имитационного моделирования способно значительно снизить материальные затраты и трудоемкость по сравнению с традиционными методами диагностики. Известны работы [3–5], посвященные совершенствованию процесса диагностирования ДВС на основе методов имитационного моделирования. В данных работах не учитываются особенности функционирования ДВС в установившихся и переходных режимах в составе АТС.
Разработанная авторами математическая модель [6] является усовершенствованным вариантом программного комплекса «Имитационная динамическая модель автомобиля»1 и позволяет получить обширный статистический материал по изменению показателей рабочих процессов как агрегатов автомобиля, так и автомобиля «в целом» при возникновении неисправностей или отказов в установившихся и переходных режимах. Полученная информация может быть использована для установления закономерностей влияния показателей рабочих процессов на диагностические параметры при возникновении неисправностей или отказов.
1 Свидетельство о государственной регистрации программы для ЭВМ № 2014617074. Программный комплекс «Имитационная динамическая модель автомобиля» / М.В. Малиованов, А.Е. Радько, Р.Н. Хмелев. 10.06.2014.
54

Вмодели задается перечень основных конструктивных и эксплуатационных параметров, соответствующих исправному состоянию автомобильного двигателя. Посредством изменения данных параметров можно имитировать следующие неисправности автомобильного ДВС для каждого цилиндра:
– негерметичность цилиндропоршневой группы;
– негерметичность впускных клапанов;
– негерметичность выпускных клапанов;
– пропуски воспламенения;
– отсутствие топливоподачи;
– нарушение угла опережения зажигания;
– нарушение фаз газораспределения.
Вкачестве характеристик работы автомобильного ДВС анализируется изменение показателей рабочего процесса (давления и температуры в цилиндре), эффективных показателей ДВС (эффективной мощности, крутящего момента, удельного эффективного расхода топлива), стабильности работы по цилиндрам и неравномерности частоты вращения коленчатого вала, времени разгона автомобиля до заданной скорости и других характеристик.
На рис. 1 и 2 приведены результаты имитационного моделирования процесса возникновения неисправностей в работе автомобильного двигателя. Изображены (см. рис. 1) графики давлений рабочего цикла при наличии негерметичности впускного клапана (зазор 3 % от площади проходного сечения). Рис. 2 отображает графики температур рабочего цикла цилиндра исправного двигателя и результаты имитационного моделирования пропусков воспламенения на холостом ходу.
Рис. 1. Графики давлений рабочего цикла исправного двигателя и при негерметичности впускного клапана (зазор 3 %)
55

Рис. 2. Графики температур рабочего цикла 1-го цилиндра исправного двигателя и при наличии пропусков воспламенения
Таким образом, предложенная имитационная модель позволяет получить обширный статистический материал по изменению показателей работы автомобильных двигателей при возникновении неисправностей, а также установить закономерности влияния показателей рабочих процессов на диагностические параметры при возникновении неисправностей или отказов.
Список литературы
1.Мороз С.М. Методы обеспечения работоспособного технического состояния автотранспортных средств: учебник. – М.: Изд-во МАДИ, 2015. – 204 с.
2.Александров А.В. Методические основы разработки диагностического комплекса для оценки технического состояния автомобильных двигателей: автореф. …. канд. техн. наук. – М., 2013. – 20 с.
3.Коньков А.Ю. Диагностирование технического состояния дизеля в эксплуатации на основе идентификации быстропротекающих рабочих процессов: автореф. … д-ра техн. наук. – Хабаровск, 2010. – 35 с.
4.Таричко В.И. Методические основы совершенствования технического диагностирования двигателей внутреннего сгорания: автореф.
…канд. техн. наук. – М., 2013. – 19 с.
5.Обозов А.А. Разработка теоретических основ и средств повышения эффективности систем технического диагностирования мало-
56

оборотных дизелей: автореф. … канд. техн. наук. – Брянск, 2010. – 38 с.
6. Козин А.А., Хмелев Р.Н. Имитационное моделирование неисправностей автомобильных двигателей. Альтернативные источники энергии в транспортно-технологическом комплексе: проблемы и перспективы рационального использования: сб. науч. тр. по материалам ежегодных конференций. – Воронеж, 2015. – Т. 2, вып. 2 (3). –
С. 440–444.
Об авторах
Козин Андрей Андреевич (Тула, Россия) – аспирант кафедры «Автомобили и автомобильное хозяйство», Тульский государственный университет» (300012, г. Тула, пр. Ленина, 92; e-mail: 79066231038@ yandex.ru).
Хмелев Роман Николаевич (Пермь, Россия) – доктор технических наук, доцент, профессор кафедры «Автомобили и автомобильное хозяйство», Тульский государственный университет (300012, г. Тула,
пр. Ленина, 92; e-mail: aiah@yandex.ru).
57
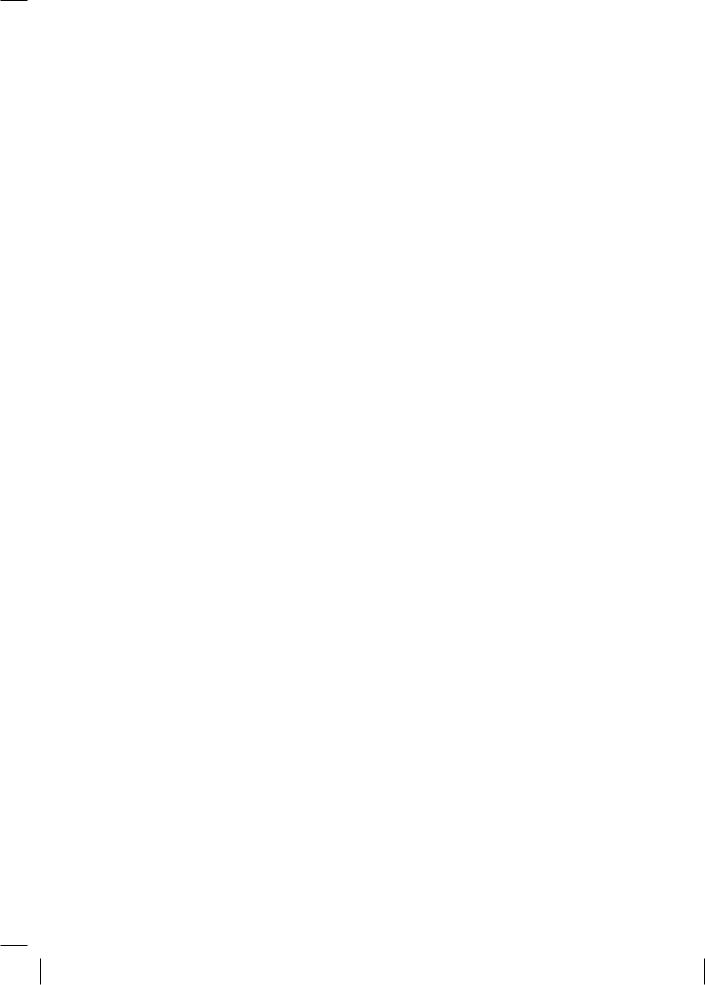
УДК 622.73
КВОПРОСУ ЗАВИСАНИЯ КАМНЯ
ВЗЕВАХ ЩЕКОВЫХ ДРОБИЛОК
В.И. Коноплев, В.М. Макаров
Тульский государственный университет, Россия
Представлен механизм, обеспечивающий предотвращение зависания камня в щековых дробилках. Механизм облегчает выгрузку кускового материала путем его ворошения.
Ключевыеслова: дробилка, истечениематериала, зависание, ворошение.
Щековые дробилки являются основным технологическим оборудованием предприятий, производящих щебень [1, 2]. Однако процесс дробления кускового материала в щековых дробилках иногда сопровождается его зависанием в камере дробления. Это оказывает негативное влияние на их производительность. Для ее повышения за счет сокращения времени простоя предлагается оснащать щековые дробилки соответствующим устройством для устранения зависания камня в зевах [3]. Данной проблеме посвящен ряд работ [4–6].
Дробилки с простым движением щеки характеризуются малой величиной хода сжатия в верхней части камеры дробления. Из-за этого возможно возникновение расклинивания и удержания нескольких камней между двумя стенками дробилки и неподвижной щекой. Также возможно образование зазора между камнями и поверхностью подвижной щеки. Причем величина зазора обычно равна или немного большего хода сжатия. При этом нарушаются условия дробления, и дробилка начинает работать вхолостую. В результате возникает явление «зависания» камней, когда они теряют возможность самостоятельно продвигаться вниз под действием силы тяжести.
Устройство щековой дробилки представлено на рисунке. Щековая дробилка (рисунок, а) включает следующие основные элементы: станина 6, подвижная щека 3, подвешенная на оси 4, две продольные стенки 5, шатун 1, шарнирно соединенный верхней головкой с приводным эксцентриковым валом 2. Нижняя часть шатуна 1 шарнирно связана с двумя распорными плитами 18, одна из которых противополож-
58

ным концом связана с нижней частью подвижной щеки 3, другая – с регулировочным устройством. Камера дробления образуется рабочими поверхностями станины 6, подвижной щеки 3 и двух боковых стенок 5. В пазе 17, выполненном в днище 16 дробилки, расположен рабочий орган, предназначенный для ворошения застревающих кусков дробимого материала. Рабочий орган представляет собой плиту 8, имеющую рифленую рабочую часть, связанную с помощью гайки 10 и винта 11 с приводом 14 (рисунок, б). Гайка 10, расположенная в направляющих 15 рамы 12, винт 11 (рисунок, в) и привод 14 смонтированы под днищем 16 дробилки. Конечные выключатели 9 и 13 ограничивают ход плиты 8. Торцевая поверхность плиты 8 со стороны, противоположной гайке 10, имеет скос 7, выполненный под углом, который равен углу наклона днища 16 дробилки.
.
Рис. Механизм, устраняющий зависание камня в зевах щековых дробилок: а – общий вид; б – привод; в – винтовое устройство
59
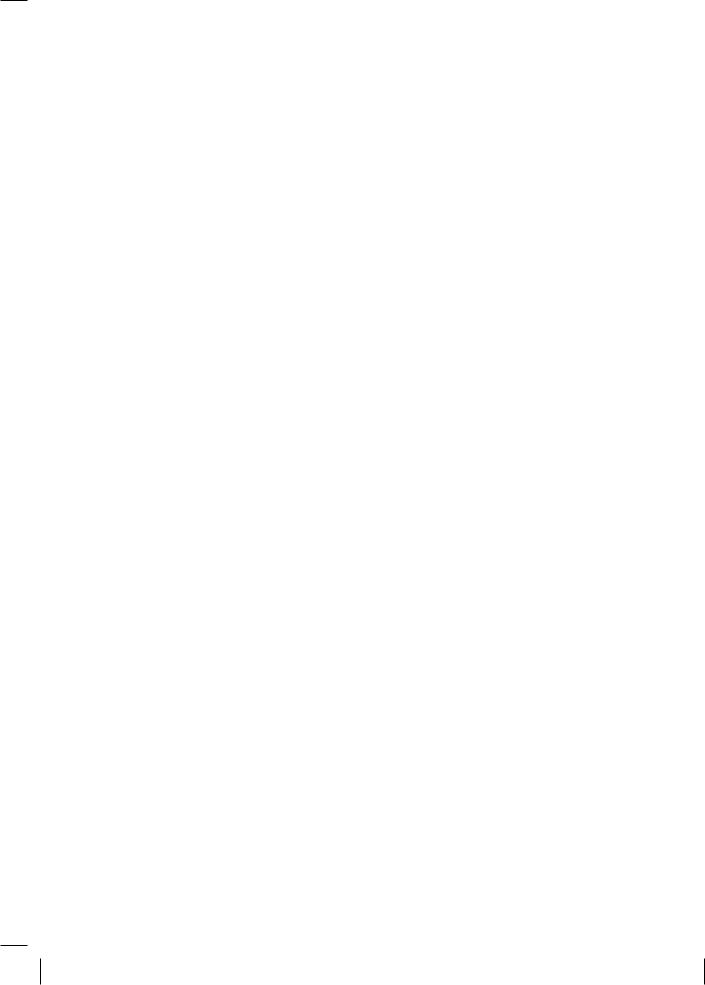
Механизм работает по следующему алгоритму. После включения привода щековой дробилки эксцентриковый вал 2 начинает вращаться. При этом шатун 1 начинает вертикальное возвратно-поступательное движение. При его движении вверх начинают перемещаться распорные плиты 18, оказывая давление на заднюю стенку подвижной плиты 3. При этом плита 3 совершает рабочий ход в виде колебательных движений относительно оси 4.
Далее включается питатель загрузки дробилки. Порода начинает дробиться в рабочей камере и под действием силы тяжести перемещаться через выходную щель на днище 16. В рабочем положении плита 8 должна находиться в крайнем нижнем положении. При этом ее скос 7 располагается в пазе 17 заподлицо с днищем 16. Если в дробилке зависают крупные куски, то необходимо отключить питатель загрузки дробилки и включить реверсивный привод 14. При этом плита 8 с помощью винта 11 и гайки 10 перемещается вверх до крайнего верхнее положения, настраиваемое выключателем 9. Плита 8 дробит и выгружает зависшие в камере куски породы, приподнимая и поворачивая их. Когда зависание будет устранено, плита 8 перемещается вниз по направляющим 15 рамы 12 вдоль паза 17 до совмещения ее скоса 7 с плоскостью днища 16. При этом ее крайнее нижнее положение настраивается выключателем 13. В результате взаимодействия рабочего органа 6 с кусковым материалом происходят его ворошение, дробление и выгрузка.
Из-за склонности кускового материала к зависанию в замкнутом объеме его дробление и выгрузка обычно затруднены. Если для ликвидации зависания кусков в камере использовать ручные операции, то это негативно сказывается на времени и, соответственно, эффективности дробления. Представленный механизм повышает эффективность процесса ворошения зависших кусков материала, их дробления и выгрузки.
Список литературы
1.Бауман В.А., Клушанцев Б.В., Мартынов В.Д. Механическое оборудование предприятий строительных материалов, изделий и конструкций: учеб. для вузов. – М.: Машиностроение, 1975. – 351 с.
2.Коноплев В.И., Анцев В.Ю., Реков П.К. Устройство для выгрузки кускового материала из бункера // Строительные и дорожные маши-
ны. – 2015. – № 1. – С. 34–36.
60