
1274
.pdf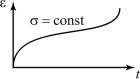
3) изменение зазоров в сопряженных деталях, что может привести к заклиниванию.
Для выяснения теплового режима проводятся расчеты на нагрев (червячные передачи, подшипники скольжения). При этом составляют уравнение теплового
баланса, приравнивая тепловыделение в единицу времени теплоотдаче, и определяют среднюю температуру при работе машин.
Виброустойчивость. Вибрация вызывает дополнительные динамические нагрузки, которые приводят к преждевременному усталостному разрушению деталей. Вибрация ухудшает качество работы машины. Особенно опасными являются резонансные колебания, при которых частота внешних колебаний совпадает с частотой собственных колебаний системы.
1.2.2. Критерии надежности
Надежность – свойство сохранять во времени способность к выполнению заданных функций в заданных режимах в течение заданного времени.
Основными критериями надежности являются безотказ-
ность, долговечность, ремонтопригодность и сохраняемость.
Безотказность – свойство изделия сохранять работоспособность в течение заданного времени без вынужденных перерывов. Понятие «безотказность» неразрывно связано с понятиями «отказ» и «наработка».
Отказ – событие, заключающееся в полной или частичной утрате работоспособности.
Наработка – продолжительность работы изделия (в часах, километрах, числах циклов).
21
elib.pstu.ru

Основные показатели безотказности – вероятность отказов Q(t), вероятность безотказной работы P(t) и интенсивность отказов λ(t).
Вероятность отказа определяется по формуле
Q (t ) = |
n (t ) |
, |
(1.14) |
||
|
|
||||
|
|
|
N |
|
|
где N – число принятых к испытанию изделий; n – |
число от- |
||||
казавших изделий за время t . |
|
||||
Вероятность безотказной работы изделия определя- |
|||||
ют как |
|
||||
P (t ) = 1 − |
n (t ) |
= 1 − Q (t ). |
(1.15) |
||
|
|||||
|
N |
|
Изменение Q(t) и P(t) во времени представлено на рис. 1.11.
Пример: по результатам испытания в одинаковых условиях партии изделий из N = 1000 шт. после наработки 5000 ч наблюдали отказы n = 100 шт. изделий. Вероятность безотказной работы этих изделий определяется по формуле
P (5000) = 1 − n = 1 − 100 = 0,9.
N |
1000 |
Вероятность безотказной работы сложного изделия равна произведению вероятностей безотказной работы отдельных его элементов,
P (t ) = P |
(t ) P |
(t ) … |
P (t ). |
|
(1.16) |
|
1 |
2 |
|
n |
|
|
|
|
|
|
Интенсивность |
отка- |
||
|
|
зов λ(t) |
– отношение числа |
|||
|
|
изделий, отказавших в еди- |
||||
|
|
ницу времени, к числу изде- |
||||
|
|
лий |
(N – |
n), |
исправно |
рабо- |
|
|
тающих |
в |
данный момент |
||
Рис. 1.11 |
|
времени. |
|
|
|
|
|
|
|
|
|
|
22
elib.pstu.ru

Если к началу произвольно выбранного отрезка времени ∆t из строя вышли n(t) изделий, а в течение периода ∆t зарегистрировано ∆n(t) отказов, то интенсивность отказов
(1.17)
Вероятность безотказной работы можно оценить по
интенсивности отказов:
P (t ) = 1 − λ (t ) t. |
(1.18) |
На рис. 1.12 приведен вид функции интенсивности отказов.
Из рис. 1.12 видно, что наработка изделия разделена на три периода. Период I относится к приработке изделия, пери-
од II называется периодом |
|
|
нормальной эксплуатации, в |
|
|
периоде III начинают появ- |
|
|
ляться интенсивные отказы. |
|
|
Долговечность – |
свой- |
|
ство изделия сохранять рабо- |
|
|
тоспособность до наступле- |
Рис. 1.12 |
|
ния предельного состояния. |
|
|
Основные показатели долговечности – |
средний и гамма- |
|
процентный ресурс. |
|
|
Средний ресурс – |
математическое |
ожидание ресурса |
в часах работы, километрах пробега, миллионах оборотов.
Гамма-процентный ресурс – суммарная наработка,
в течение которой изделие не достигает предельного состояния с вероятностью γ, выраженной в процентах.
Дополнительные показатели долговечности: наработка, технический ресурс, назначенный ресурс, срок службы.
23
elib.pstu.ru
Технический ресурс – суммарная наработка изделия от начала эксплуатации до перехода в предельное состояние (в часах, километрах пробега и др.).
Назначенный ресурс – суммарная наработка, при которой прекращается эксплуатация изделия независимо от его состояния.
Срок службы– календарная продолжительность эксплуатации изделия от начала до перехода в предельное состояние (включает наработку изделия и время простоев).
Ремонтопригодность – свойство изделия, заключающееся в приспособлении к поддержанию и восстановлению работоспособности путем технического обслуживания и ремонта.
Числовой показатель ремонтопригодности – вероят-
ность восстановления в заданное время и среднее время восстановления.
Под вероятностью восстановления понимают вероят-
ность того, что время восстановления работоспособного состояния изделия не превысит заданное значение.
Сохраняемость – свойства изделий сохранять эксплуатационные показатели на время хранения. Числовой показатель – средний срок сохраняемости.
1.2.3. Критерии экономичности
Экономичность – это минимальная стоимость затрат на проектирование, изготовление и эксплуатацию изделий.
Основными критериями экономичности являются произ-
водительность; энергоемкость; материалоемкость; технологичность; стандартизация; унификация и взаимозаменяемость; транспортабельность; удобство и безопасность обслуживания; эстетичность; экологичность; эргономичность.
В качестве примеров критериев экономичности рассмотрим критерии технологичности, стандартизации, унификации, взаимозаменяемости и эргономичности.
24
elib.pstu.ru
Под технологичностью машин и их деталей понимаются такие конструктивные формы, способы и приемы изготовления, материалы деталей, которые обеспечивают минимальный вес и размеры, минимальные затраты на производство и эксплуатацию.
Стандартизация – установление обязательных норм, правил, параметров, технических и начальных характеристик, которым должно соответствовать изделие.
Унификация – целесообразное сокращение номенклатуры однотипных деталей и сборочных единиц.
Взаимозаменяемыми называются такие детали, которые могут занимать свои места в машинах без дополнительной доработки и полностью выполнять свои функции. При этом упрощается изготовление, понижается себестоимость. Взаимозаменяемость обеспечивается системой допусков и посадок, нормализованной стандартами.
Эргономичность – соответствие машины антропометрическим и физиологическим характеристикам человека.
Контрольные вопросы
1.Какое различие между механизмом и машиной?
2.Чем отличается ведущее звено механизма от ве-
домого?
3.В чем состоит различие между деталью и сборочной единицей (узлом) машины?
4.Какие детали относят к деталям общемашиностроительного применения?
5.Приведите примеры деталей соединений и механических передач.
6.Приведите примеры деталей и узлов, обслуживающих механические передачи.
25
elib.pstu.ru
7.Какие передачи относятся к передачам трением,
акакие – зацеплением?
8.Какие передачи относятся к передачам гибкой связью?
9.Что понимают под качеством изделия и под критериями качества?
10.Объясните понятия основных критериев работоспособности деталей машин: прочность, жесткость, износостойкость, теплостойкость, вибростойкость.
11.Что следует понимать под безотказностью, отказом и долговечностью деталей машин?
12.В чем различие между техническим и назначенным ресурсом?
26
elib.pstu.ru
ТЕМА 2. ОБЩИЕ СВЕДЕНИЯ О ПРОЕКТИРОВАНИИ.
ВЫБОР ДОПУСКАЕМЫХ НАПРЯЖЕНИЙ
2.1. ОБЩИЕ СВЕДЕНИЯ О ПРОЕКТИРОВАНИИ
Цель проектирования – определение формы, размеров и материалов деталей, сборка которых в определенной последовательности обеспечит создание изделия с требуемыми функциональными и эксплуатационными свойствами.
Результатом проектирования является информационная модель будущего изделия в виде конструкторской документации.
Конструкторская документация – текстовые и графи-
ческие документы с данными, необходимыми для разработки, изготовления, контроля и эксплуатации изделия.
Проектировочный (предварительный, упрощенный) расчет – это определение основных размеров детали при выбранном материале. Производится по формулам, соответствующим главному критерию работоспособности (например, прочности, жесткости и др.). Этот расчет применяют в тех случаях, когда размеры конструкции заранее не известны.
Проверочный расчет (уточненный) – это определение фактических характеристик главного критерия работоспособности детали или определение наибольшей допустимой нагрузки на деталь по допускаемым значениям критерия работоспособности. Расчет проводят, когда форма и размеры детали известны из проектировочного расчета или приняты конструктивно, когда определена технология изготовления детали.
27
elib.pstu.ru
Расчетная или эквивалентная нагрузка – такой уровень нагрузки (сила, крутящий момент, мощность), который по своему действию на изделие равносилен действию всех основных и дополнительных нагрузок.
Проектирование состоит из следующих этапов:
1.Техническое задание. Включает в себя назначение изделия, область применения, условия эксплуатации и технические требования. Техническое задание составляется совместно заказчиком и исполнителем, затем происходит окончательное оформление документа.
2.Техническое предложение. Это конструкторский доку-
мент, в котором содержится обоснование технической и техни- ко-экономической целесообразности разработки изделия. Разрабатывается анализ вариантов возможных решений, достижений науки и техники, патентных материалов, возможностей машиностроительных заводов и смежных отраслей.
3.Эскизный проект (содержит общий вид и сборочные чертежи в эскизной проработке) включает этапы:
– оценка нагрузок и напряжений, определяющих харак-
терные отказы и главный критерий работоспособности.
– выбор материала конструкции, оценка его механиче-
ских характеристик, определение допускаемых значений критериев работоспособности.
– составление приближенной математической модели, предварительное определение размеров конструкции, эскизная компоновка и проверочные расчеты по критериям работоспособности.
4.Технический проект. Составление уточненной математической модели, окончательная проработка конструкции, проверочные расчеты по всему комплексу критериев и оптимизация конструкции.
5.Рабочий проект. Окончательное оформление рабочих чертежей, составление рабочей документации, технологических карт, проведение заводских испытаний опытного образца
игосударственные испытания, выпуск головной партии.
28
elib.pstu.ru
2.2. ВЫБОР ДОПУСКАЕМЫХ НАПРЯЖЕНИЙ И КОЭФФИЦИЕНТОВ ЗАПАСА ПРОЧНОСТИ
При расчете деталей на прочность и жесткость размеры их должны быть такими, чтобы в них не произошли разрушения и не появились деформации, превышающие допустимые.
Под допускаемыми напряжениями понимают такие максимальные значения рабочих напряжений, которые могут быть допущены в опасном сечении детали при условии обеспечения необходимой надежности и долговечности. Таким образом, задача расчета конструкции на прочность сводится к определению таких размеров деталей, при которых обеспечивается работоспособность конструкции в течение всего срока службы:
|
|
σ пред |
τ пред |
|
|||||
|
[σ ]= |
|
|
|
, [τ =] |
|
|
, |
(2.1) |
|
[S |
σ |
] |
[S ] |
|||||
|
|
|
|
|
|
τ |
|
||
где [σ ], [τ |
] – допускаемые нормальные и касательные на- |
||||||||
пряжения, |
σ пред , τ пред – |
предельные напряжения, |
[Sσ ], [Sτ ] – |
допускаемые или нормативные коэффициенты запаса проч-
ности по нормальным и касательным напряжениям.
При статических нагрузках в качестве σ пред и τ пред принимают пределы текучести σ Т или τ Т для пластичных материаловипределыпрочности σ B или τ B дляхрупкихматериалов.
При переменных нагрузках в качестве σ пред или τ пред принимают пределы выносливости (усталости) σ R или τ R , например, при симметричном цикле σ −1 или τ −1 соответст-
венно. Для определения пределов выносливости реальных деталей используются коэффициенты снижения пределов выносливости Kσ Д и Kτ Д ,
29
elib.pstu.ru
|
|
|
|
K |
|
|
= |
|
σ –1 |
|
|
, |
K |
|
= |
|
τ |
–1 |
, |
(2.2) |
||||||||
|
|
|
|
|
|
σ |
|
|
|
|
|
|
|
|
|
|
||||||||||||
|
|
|
|
|
σ Д |
|
|
–1 Д |
|
|
|
τ |
Д |
τ |
–1 Д |
|
||||||||||||
где σ |
–1 ,τ |
–1 |
– |
пределы выносливости лабораторных образцов, |
||||||||||||||||||||||||
σ –1 Д ,τ |
–1 Д |
– |
пределы выносливости реальных деталей. |
|
||||||||||||||||||||||||
|
Значения Kσ Д , |
Kτ Д |
|
определяются следующим образом: |
||||||||||||||||||||||||
|
|
|
|
Kσ Д = |
|
|
K |
σ |
|
|
+ |
1 |
|
|
− |
|
|
1 |
|
|
|
|
||||||
|
|
|
|
|
|
|
|
|
|
|
|
|
|
|
1 |
|
|
|
, |
|
||||||||
|
|
|
|
|
K |
|
|
|
|
|
K |
|
|
|
|
|
|
|
||||||||||
|
|
|
|
|
|
|
|
d σ |
|
|
|
|
|
Fσ |
|
|
|
|
K |
|
||||||||
|
|
|
|
|
|
|
|
|
|
|
|
|
|
|
|
|
|
νσ |
(2.3) |
|||||||||
|
|
|
|
|
|
|
K |
|
|
|
|
|
1 |
|
|
|
|
|
1 |
|
|
|
||||||
|
|
|
|
|
|
τ |
|
|
|
|
|
|
|
|
|
|
|
|
||||||||||
|
|
|
|
Kτ Д = |
|
|
|
|
+ |
|
|
|
−1 |
|
|
|
, |
|
|
|
||||||||
|
|
|
|
|
|
|
|
|
KFτ |
|
|
|
|
|
|
|||||||||||||
|
|
|
|
|
Kd τ |
|
|
|
|
|
|
|
Kντ |
|
||||||||||||||
где Kσ , Kτ |
– |
эффективные коэффициенты концентрации на- |
||||||||||||||||||||||||||
пряжений ( Kσ >1, Kτ |
|
>1 ), |
Kd σ |
, Kdτ |
– |
|
коэффициенты влияния |
|||||||||||||||||||||
абсолютных размеров поперечного сечения (Kd σ <1, Kdτ |
<1) , |
|||||||||||||||||||||||||||
KF σ , KFτ – |
коэффициенты влияния шероховатости поверхно- |
|||||||||||||||||||||||||||
сти ( KF σ ≤ |
1, |
KFτ ≤ 1) , Kν σ |
, Kντ |
|
– |
коэффициенты влияния по- |
||||||||||||||||||||||
верхностногоупрочнения( |
K |
νσ |
>1, |
K |
|
>1 ). |
|
|||||||||||||||||||||
|
|
|
|
|
|
|
|
|
|
|
|
|
|
|
|
|
|
|
|
ντ |
|
|
|
|
|
|
Значения коэффициентов Kd , KF , Kν определяются
отношениями пределов выносливости образцов при наличии соответствующих факторов влияния к пределам выносливости стандартных образцов или при помощи справочных таблиц и графиков.
Для выбора допускаемых (нормативных) коэффициентов запаса прочности используются два метода: табличный и дифференциальный.
Табличный метод предполагает использование специализированных таблиц коэффициентов запаса прочности, составленных для отдельных деталей и узлов машин.
Дифференциальный метод заключается в том, что до-
пускаемые коэффициенты запаса прочности определяют по формуле
30
elib.pstu.ru