
1274
.pdf
ТЕМА 7. ОБЩИЕ СВЕДЕНИЯ О ЗАКЛЕПОЧНЫХ, КЛЕММОВЫХ, ПАЯНЫХ,
КЛЕЕВЫХ И ШТИФТОВЫХ СОЕДИНЕНИЯХ
7.1. ЗАКЛЕПОЧНЫЕ СОЕДИНЕНИЯ
Заклепочные соединения (рис. 7.1) являются неразъем-
ными соединениями.
Рис. 7.1
Достоинства заклепочных соединений (в сравнении со сварными соединениями): возможность соединения деталей из несвариваемых материалов, надежная работа при ударных и вибрационных нагрузках.
Недостатки заклепочных соединений: трудоемкость и невысокая технологичность; ослабление деталей отверстиями и в связи с этим повышенный расход металла; трудность автоматизации процесса склепывания; высокий уровень шума при работе с пневмоинструментом, используемым для деформирования заклепок; коэффициенты линейного расширения материала заклепок и соединяемых деталей должны быть равными или близкими друг к другу.
Заклепочное соединение образуют деформированием заклепки, свободно установленной в отверстия соединяемых деталей (рис. 7.2). Пластически деформируя, заклепку осаживают, заполняя зазор между стержнем заклепки и стенками отверстия, и формируют замыкающую головку. Закладную головку выполняют на заклепке заранее.
101
elib.pstu.ru

Рис. 7.2
Основные типы заклепок представлены на рис. 7.3: где а, б, в – сплошные стержневые заклепки: а – с полукруглой головкой; б – плоской (трапецеидальной) головкой; в– потайной головкой; г– пустотелые (для мягких тканей); д– полупустотелые (для снижения силы расклепывания и повышения сопротивлению усталости соединения из композиционных материалов – стеклотекстолитов, углепластиков).
Рис. 7.3
По расположению заклепок (рис. 7.4) соединения подразделяют на однорядные (а) и многорядные (б).
Рис. 7.4
102
elib.pstu.ru
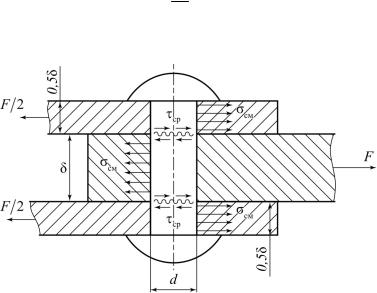
Проверку прочности телазаклепки (рис. 7.5) выполняют: по напряжениям среза:
τ ср = |
4F |
≤ τ[ ср ], |
(7.1) |
|
|||
|
π d 2iср |
|
и по напряжениям смятия
σ см= |
F ≤ σ[ |
см ], |
(7.2) |
|
δ d |
|
|
где iср – число поверхностей среза.
Рис. 7.5
Соединяемые детали проверяют на прочность в сечениях, ослабленных отверстиями под заклепки. Для рассмотрения условия прочности вырежем из листа участок, равный по ширине одному шагу t (рис. 7.6). При толщине листа δ и нагружении растягивающей силой F имеем следующие напряжения растяжения в листе на ширине t:
103
elib.pstu.ru
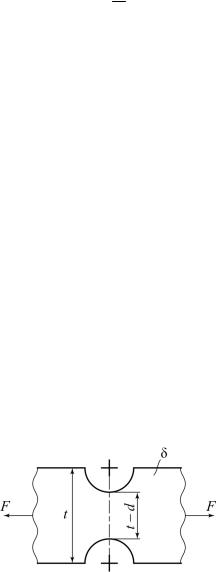
σt = F , (7.3)
p tδ
анапряжения растяжения в листе в сечении, ослабленном отверстием диаметра d,
σ p= |
F |
|
|
|
. |
(7.4) |
|
(t − d )δ |
|||
Условие прочности листа: |
|
||
σ р≤ |
σ[ р ], |
(7.5) |
где [σ р ] – допускаемое напряжение на растяжение.
Отношение σ tр /σ р обозначают ϕ и называют коэффициентом прочности соединяемых деталей заклепочного шва:
ϕ = |
σ |
tp |
= |
t − d |
. |
(7.6) |
σ |
|
|
||||
|
p |
t |
|
Коэффициент ϕ показывает, насколько уменьшается
прочность листов при соединении заклепками. Среднее значение ϕ = 0,85 соответствует уменьшению прочности листов
при образовании заклепочного соединения на 15 %. Повысить коэффициент прочности заклепочного шва
можно, уменьшив d. Для этого применяют многорядные швы (с большим числом заклепок меньшего диаметра).
Рис. 7.6
104
elib.pstu.ru

Смятие стенок отверстия нарушает работоспособность соединения и может привести к последующему прорезанию заклепкой соединяемых деталей (рис. 7.7), следы которого показаны волнистыми линями.
Рис. 7.7
Для предотвращения прорезания должно выполняться условие прочности по допускаемым напряжениям среза τ ср для материала деталей,
τ ср = |
|
F |
|
|
|
≤ τ[ ср ]. |
(7.7) |
|
|
d |
|
||||
|
2 t1 |
− |
|
|
δ |
|
|
|
|
|
|||||
|
|
|
2 |
|
|
|
Допускаемые напряжения на срез и смятие детали обычно принимают:
[τ ср ]= 0, 2σ B , σ[ см=] (0,…4 0,σ 5) B ,
где σ B – временное сопротивление материала детали.
Основным видом разрушения заклепочных соединений при переменных режимах нагружения является возникнове-
105
elib.pstu.ru

ние усталостных трещин. В общем машиностроении переменный характер нагружения учитывают понижением допускаемых напряжений. Например, при редких знакопеременных нагрузках допускаемые напряжения понижают, умножая их на коэффициент:
γ = |
1 |
≤ 1, |
(7.8) |
|
a − b Fmin
Fmax
где Fmin и Fmax – наименьшая и наибольшая по абсолютному
значению действующие на заклепки силы, взятые со своими знаками; а, b – коэффициенты: а = 1 и b = 0, 3 для соединения элементов из низкоуглеродистых сталей; а = 1, 2 и b = 0,8 – для соединений из среднеуглеродистых сталей.
7.2. КЛЕММОВЫЕ СОЕДИНЕНИЯ
Клеммовые соединения применяют для закрепления деталей на валах и осях, цилиндрических колоннах, кронштейнах и т.д.
Конструктивно эти соединения обычно имеют охватываемую деталь (вал) и охватывающую деталь – утолщенную часть рычага или кронштейна с отверстием внутри, которую называют клеммой (ступицей). Сжатие сопряженных поверхностей ступицы и вала выполняют за счет винтов (болтов), когда в одной из половин ступицы нарезают внутреннюю резьбу. При соединении деталей с помощью клемм используют силы трения, которые возникают от затяжки болтов. Эти силы позволяют нагружать соединение моментом и осевой силой.
За счет сил трения, которые возникают на сопряженных поверхностях ступицы и вала после затяжки болтов
106
elib.pstu.ru
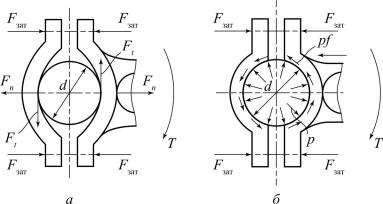
(винтов), клеммовое соединение способно воспринимать осевую сдвигающую силу Fa, вращающий момент Т, совместное действие вращающего момента Т и осевой силы Fa.
Достоинства клеммовых соединений: простота монтажа и демонтажа, самопредохранение от перегрузки, возможность перестановки и регулировки взаимного расположения деталей как в осевом, так и окружном направлениях.
Недостатки клеммовых соединений: малая нагрузочная способность (не рекомендуют применять для передачи больших нагрузок), увеличенное количество деталей.
Взависимости от выполнения соединения при расчете можно рассмотреть два предельных случая (рис. 7.8, а, б).
Впервом случае (рис. 7.8, а) клемма обладает большой жесткостью, а посадка деталей выполнена с большим зазором. При этом контакт деталей происходит по линии, а условия прочности соединения имеют вид:
Ft d = Fn fd ≥ T ; 2Fn f ≥ Fa , |
(7.9) |
где Fn – реакция в месте контакта, f – коэффициент трения.
Рис. 7.8
107
elib.pstu.ru
Из условия равновесия каждой половины клеммы следует, что
Fn = 2Fзат , |
(7.10) |
где Fзат – сила затяжки болтов.
После подстановки (7.10) в (7.9) условия прочности соединения будут иметь вид:
2Fзат fd ≥ T ; 4Fзат f ≥ Fa . |
(7.11) |
Во втором случае (рис. 7.8, б) клемма достаточно гибкая, форма сопрягаемых деталей строго цилиндрическая, зазор в соединении близок к нулю. В этом случае давление p распределено равномерно по поверхности соприкосновения деталей, а условия прочности соединения выражаются в виде:
pfπdb |
d |
≥ T ; pfπdb≥ Fa , |
(7.12) |
|
|||
2 |
|
|
где b – длина образующей цилиндрической контактной поверхности.
По аналогии с формулой (7.10) из условия равновесия полуклеммы получим
p = |
2Fзат |
. |
(7.13) |
|
|||
|
db |
|
После подстановки (7.13) в (7.12) условия прочности соединения будут иметь вид:
πFзат fd ≥ T ; π2Fзат f ≥ Fa . |
(7.14) |
Таким образом, нагрузочные способности для двух предельных случаев относятся как 2/π [ср. формулы (7.11) и (7.14)]. Первый случай является самым неблагоприятным, а второй – наиболее рациональным с точки зрения требуемой затяжки болтов.
108
elib.pstu.ru

Практически выполняемые клеммовые соединения рассматриваются как средние между двумя рассмотренными выше крайними случаями:
2,5Fзат fd ≥ |
T ; |
5Fзат f ≥ Fa |
(7.15) |
||||||
или для z болтов, расположенных с одной стороны вала: |
|||||||||
F |
= |
KT |
|
; |
F |
= |
KFa |
, |
(7.16) |
|
|
|
|||||||
зат |
|
2,5zfd |
зат |
|
5zf |
|
|||
|
|
|
|
|
где K – коэффициент запаса, K = 1,3…1,8.
При совместном действии T и Fa сдвигающей силой на поверхности контакта будет равнодействующая осевой Fa и окружной Ft сил, Ft = 2T/d. Для такого случая
|
= |
K |
F 2 |
+ F 2 |
|
|
F |
|
t |
a |
. |
(7.17) |
|
|
|
|
||||
зат |
|
|
5zf |
|
||
|
|
|
|
7.3. ПАЯНЫЕ СОЕДИНЕНИЯ
Паяные соединения – это неразъемные соединения, образуемые силами молекулярного взаимодействия между соединяемыми деталями и присадочным материалом, называемым припоем.
Припой – сплав (на основе меди, олова, серебра) или чистый металл, вводимый в расплавленном состоянии в зазор между соединяемыми деталями.
По конструкции паяные соединения подобны сварным (рис. 7.9), где а – соединение встык, б – внахлестку, в – с одной накладкой, г – вскос, д – втавр, е – телескопическое соединение.
Пайка позволяет соединять не только однородные, но и разнородные материалы: черные и цветные металлы, сплавы, керамику, стекло и др.
109
elib.pstu.ru
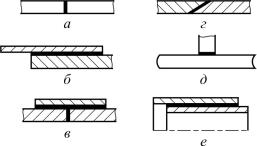
Рис. 7.9
При пайке поверхности деталей очищают от окислов
иобезжиривают с целью получения хорошей смачиваемости припоем и качественного заполнения им зазоров. Нагрев припоя и деталей в зависимости от их размеров осуществляют паяльником, газовой горелкой, электронагревом, в термических печах и др. Для уменьшения вредного влияния окисления поверхностей деталей при пайке применяют флюсы, атакже паяют в вакууме или в среде нейтральных газов. Расплавленный припой растекается по нагретым поверхностям стыка деталей
ипри охлаждении затвердевает, прочносоединяя детали.
Размер зазора принимают 0,03…0,2 мм в зависимости от припоя (легкоплавкий или тугоплавкий) и материала деталей.
Достоинства паяных соединений: возможность соединения разнородных материалов, стойкость против коррозии, возможность соединения тонкостенных деталей, герметичность, малая концентрация напряжений вследствие высокой пластичности припоя, возможность получения соединений деталей в скрытых и труднодоступных местах конструкции.
Недостатки паяных соединений: сравнительно невысокая прочность (по сравнению со сваркой), необходимость малых и равномерно распределенных зазоров между соединяемыми деталями, что требует их точной механической обработки и качественной сборки, а также предварительной обработки поверхностей перед пайкой.
110
elib.pstu.ru