
ПРОЕКТИРОВАНИЕ ЭФФЕКТИВНЫХ ТЕХНОЛОГИЧЕСКИХ ПРОЦЕССОВ ИЗГОТОВЛЕНИЯ И СБОРКИ ИЗДЕЛИЙ
.pdf
К3.0 Р0 ,
Для массового типа производства коэффициент закрепления операций составляет К3.0 1, для крупносерийного типа производства –
2 < К3.0 10, для серийного типа производства – 10 < К3.0 20, для мелкосерийного типа производства – 20 < К3.0 40, для единичного
производстваК3.0 > 40.
В связи с тем, что при разработке технологического процесса число выполняемых операций и количество рабочих мест обычно неизвестно, тип производства с достаточной точностью можно установить из соотношения между трудоемкостью выполнения операций и тактом изготовления изделия.
Коэффициент закрепления операций К3.0 определяется по формуле
К3.0 |
|
, |
|
||
|
шт.ср |
|
где τ – такт выпуска, мин; шт.ср |
– среднее время на выполнение |
характерных операций по маршруту изготовления, мин. Такт выпуска определяется по формуле
F 60 з.н Fднkсм см60 з.н ,
N N
где F – годовой фонд времени работы станка, час; ηз.н – нормативный коэффициент загрузки оборудования (в серийном производстве ηз.н 0,8); N – годовая программа выпуска деталей, шт.; Fдн – годовой фонд времени работы станка, дни; kсм – коэффициент сменности; τсм – продолжительность рабочей смены, ч.
После определения типа производства определяют форму организации технологического процесса. Согласно ГОСТ 14.312-74 существуют две формы организации технологических процессов, а именно групповая и поточная.
При групповой форме производства запуск деталей производится партиями с определенной периодичностью, что является ос-
21
elib.pstu.ru

новным признаком серийного производства (мелкосерийного, серийного, крупносерийного).
Размер производственной партии может быть определен по формуле
n N a ,
Fдн
где a – периодичность запуска, дни (рекомендуемая периодичность запуска составляет 3, 6, 12 или 24 дней); Fдн – годовой действительный фонд времени работы станка, дни.
Корректировка размера производственной партии состоит в определении расчетного числа рабочих смен С, необходимых для обработки всей партии изделий на основных рабочих местах
СТшт.кал.срn ,
Тсм з.н
где Тшт.кал.ср – среднее штучно-калькуляционное время по основ-
ным операциям, мин; n – количество заготовок в производственной партии, шт.; Тсм – действительный фонд времени работы оборудования в течение одной рабочей смены, мин.
Расчетное число смен округляется до ближайшего целого числа Спр, затем определяется число деталей в партии, необходимое для загрузки оборудования на основных операциях в течение целого числа смен
n Fсм з.нСпр , пр Тшт.кал.ср
где Fсм – действительный фонд времени работы оборудования в
смену, как правило, его принимают равным 476 мин.; Поточная форма организации технологических процессов в
свою очередь подразделяется на однономенклатурную и многономенклатурную поточную линии.
Однономенклатурную поточную линии целесообразно организовывать при двухсменной работе при загрузке линии не менее чем на 60 %:
22
elib.pstu.ru
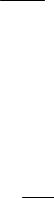
з N шт.ср 0,6,
Fg 60
где з – нормативный коэффициент загрузки однономенклатурной
поточной линии при двухсменной работе; N – годовая программа выпуска изделий, шт.; τшт.ср – среднее штучное время, мин; Fg – действительный годовой фонд времени работы оборудования поточной линии, ч.
Такт выпуска на однономенклатурной поточной линии составляет
в 60NFg .
Если коэффициент загрузки однономенклатурной поточной линии ηз составляет менее 0,6, то следует применять многономенклатурную поточную линию, либо групповую форму организации технологического процесса.
7.4. Анализ существующего (базового) технологического процесса
Разработке нового технологического процесса должен предшествовать анализ существующего на предприятии или отрасли аналога технологического процесса. Анализ производится с целью изыскания возможностей совершенствования технологического процесса, повышения производительности и обеспечения качества обработки.
Анализ аналога технологического процесса механической обработки включает следующий примерный перечень вопросов:
–целесообразность вида и метода получения исходной заготовки для заданных условий производства;
–правильность выбора черновых и чистовых баз;
–целесообразность применяемых методов обработки;
–правильность последовательности выполнения операций для достижения заданной точности поверхностей изделия;
23
elib.pstu.ru
–соответствие технологических возможностей применяемого оборудования требованиям точности и шероховатости поверхностей на операциях технологического процесса;
–степень концентрации операций;
–обоснованность назначенных параметров режима обработки;
–обоснованность оснащенности операций технологической оснасткой;
–производительность обработки;
–фактическое качество обработки.
Аналогично осуществляют анализ существующего технологического процесса сборки изделия.
Результаты анализа существующего технологического процесса должны быть изложены в пояснительной записке. Недопустимо
заменять анализ существующего технологического процесса описанием этого технологического процесса.
На основании анализа существующего технологического процесса предлагаются возможные варианты по изменению технологического процесса с целью его совершенствования и оптимизации.
7.5. Назначение стадий обработки [1.24, 1.25,1.43, 1.46, 1.47]
Технологический процесс механической обработки – это совокупность операций, выполняемых в определенной последовательности.
Несмотря на разнообразие форм деталей машин и множество методов механической обработки, существуют общие положения, которыми руководствуются при разработке технологического процесса.
Разрабатывают схему (последовательность операций) технологического процесса обработки.
Технологический процесс условно делят на стадии, каждая из которых преследует определенную цель. Многолетняя практика показала, что технологический процесс механической обработки целесообразно делить на соответствующие стадии:
–обдирочная обработка;
–черновая обработка;
24
elib.pstu.ru
–получистовая обработка;
–чистовая обработка;
–тонкая отделочная (финишная) обработка.
Таким образом, каждую поверхность заготовки обрабаты-
вают несколько раз на разных операциях. При этом каждая предшествующая операция подготавливает поверхность к обработке на последующей операции. Точность размеров и взаимного расположения поверхностей при этом последовательно повышается.
7.6. Выбор технологических баз [1.17, 1.41, 1.47]
Правильный выбор баз (черновых и чистовых), а также способов установки и закрепления заготовки на станке при ее обработке является одним из наиболее важных вопросов при разработке технологического процесса изготовления детали [1,41]. От этого зависит точность и качество обработки.
В пояснительной записке должен быть обоснован выбор технологических баз.
При выборе баз следует руководствоваться следующими соображениями:
–необходимо по возможности реализовывать принцип совмещения баз (технологической, измерительной и конструкторской). При этом наилучшие по точности результаты будут достигнуты в случае, когда технологической и измерительной базой служит основная сборочная база, то есть поверхности, которые определяют положение деталей в сборочной единице (например, центральное отверстие и торец зубчатого колеса);
–следует соблюдать принцип постоянства баз, то есть в ходе обработки на основных технологических операциях необходимо использовать в качестве технологических баз одни и те же поверхности,
втомчислеискусственные базы, например, центровые отверстия;
–в случае, если постоянство баз не может быть обеспечено, в качестве новой технологической базы используют обработанные поверхности. Если при этом базовая поверхность не является изме-
25
elib.pstu.ru
рительной, то необходимо выполнить проверочный расчет допуска на обрабатываемый размер;
–технологическая база должна обеспечивать достаточную устойчивость и жесткость заготовки, что достигается соответствующими размерамибазовых поверхностей иих взаимнымрасположением;
–технологическую базу следует выбирать с учетом простоты и дешевизны зажимного приспособления, удобства установки детали
иее закрепления.
Выбранные в качестве технологических баз поверхности должны быть обработаны на первых операциях.
При выборе черновой технологической базы руководствуются следующим:
–для заготовок, у которых обрабатывают не все поверхности, в качестве черновой базы принимают поверхности, остающиеся необработанными. В этом случае обеспечивается более точное взаимное положение обработанных и необработанных поверхностей;
–для заготовок, у которых все поверхности обрабатываются, за черновую базу принимают поверхности, имеющие наименьшие припуски.
Черновые базовые поверхности должны быть по возможности гладкими, не должны иметь штамповочных или литейных уклонов, на них не должно быть литников, прибылей, плоскостей разъема моделей, штампов и форм.
Обычно на первой операции (или на одной из первых операций) целесообразно обработать ту поверхность, которая в дальнейшем будет служить чистовой технологической базой, то есть наи-
более важной с точки зренияустановки и закрепления заготовки. Для установки исходной заготовки на станке, при отсутствии у
нее явной технологической базы, используют скрытые базы, например, геометрическую ось вала, и создают искусственные (вспомогательные) базы, например, центровые отверстия при обработке деталей типа вал.
При реализации автоматического метода получения точности размеров черновая установочная база принимается только для одного установа. Повторное использование этой черновой базы мо-
26
elib.pstu.ru
жет нарушить взаимное расположение обрабатываемых поверхностей. Однако для заготовок, получаемых точными методами литья или штамповки, это правило не является обязательным.
Чистовой технологической базой должна служить та поверхность (или сочетание поверхностей) заготовки (детали), относительно которой на чертеже координировано положение обрабатываемой поверхности (совмещение конструкторской, технологической и измерительной базы).
Точность, форма и размеры чистовой технологической базы должны обеспечивать хорошую устойчивость заготовки на установочных элементах приспособления, простоту и надежность закрепления заготовки.
7.7.Термическая обработка и ее место
втехнологическом процессе
Термическая обработка (ТО) преследует три основные цели:
–улучшить обрабатываемость материала и уменьшить внутренние остаточные напряжения – отжиг;
–улучшить микроструктуру стали, уменьшить внутренние остаточные напряжения, улучшить механические свойства стали и подготовитьк последующейтермическойобработке– нормализация;
–улучшить физико-механические свойства материала в соответствии с техническими условиями чертежа – закалка и/или хими- ко-термическая обработка (цементация, азотирование, цианирование, алитирование и т.п.).
Отжигу подвергают исходные литые, кованные и штампованные заготовки. Нормализацию, как правило, проводят после обдирки или черновой обработки.
Покупной стандартизованный прокат (круглый пруток, квадрат, шестигранник, периодический прокат, труба и т.д.) на предприятииизготовителе изделия не повергают ни отжигу, ни нормализации, так как эти операции производят централизовано на заводе-изготовителе проката для поставки обезличенному потребителю.
Закалка (объемная или местная) повышает твердость, прочность и износоустойчивость материала заготовки, но сопровождается изменением формы и размеров, поэтому ее производят перед
27
elib.pstu.ru
чистовыми и отделочными операциями технологического процесса изготовления детали, когда обрабатываемые поверхности заготовки имеют небольшой припуск.
При местной закалке отдельных поверхностей после химикотермической обработки (ХТО), например, при закалке рабочих поверхностей зубьев зубчатых колес после цементации, в технологическом процессе должны быть предусмотрены операции защиты не закаливаемых поверхностей и поверхностей, не подвергающихся химико-термической обработке от поверхностного насыщения углеродом или азотом.
Кроме того, в технологическом процессе могут быть предусмотреныоперации нанесениязащитныхгальванических покрытий.
Врезультате ТО или ХТО форма и размеры заготовки изменятся. В связи с этим необходимо увеличивать припуск на поверхности с искаженной формой и измененными размерами.
Обычно объемную закалку с последующим отпуском производят непосредственно передчистовымиилиотделочнымиоперациями.
Вряде случаев применяют местную закалку путем местного нагрева токами высокой частоты (ТВЧ) и закалке с последующим отпуском отдельных поверхностей детали, например, эвольвентные поверхности зубьев зубчатых колес подвергают нагреву ТВЧ с закалкой и последующим отпуском. Вид ТО или ХТО и требования по механическим свойствам (твердости, вязкости, категории прочности
ит.д.) материала указывают в технических условиях на рабочем чертеже детали. В случае местной ТО или ХТО в картах маршрутного описания ТП должны быть предусмотрены операции защиты поверхностей, которые не должны подвергаться ТО или ХТО.
7.8. Выбор вида и метода получения исходной заготовки [1.47, 4.1–4.10]
В этом разделе курсового проекта необходимо провести краткий анализ метода получения заготовки существующего технологического процесса изготовления детали, его преимущества и недостатки, сведения о точностииэкономичностиполучения заготовки.
28
elib.pstu.ru
На основании анализа конфигурации детали, ее назначения, технических условий изготовления, программы выпуска и условий производства следует выбрать рациональный метод получения исходной заготовки, обеспечивающий минимальную себестоимость изготовления.
При этом необходимо стремиться к максимальному приближению формы и размеров исходной заготовки к размерам детали. Это уменьшает расход материала и снижает трудоемкость механической обработки.
При выборе метода получения исходной заготовки для разрабатываемого технологического процесса изготовления изделия возможны следующие варианты:
–метод получения исходной заготовки принимают аналогичным существующему;
–метод получения исходной заготовки изменяют, но это не вызывает существенных изменений технологического процесса механической обработки;
–метод получения исходной заготовки изменяют, и в результате этого существенно изменяется ряд операций последующей механической обработки.
В первом случае необходимо со ссылкой на специальную литературу обосновать оптимальность существующего метода получения исходной заготовки. Расчет себестоимости получения заготовки в этом случае производить нецелесообразно.
Во втором случае выбор нового метода получения исходной заготовки необходимо обосновать экономическим расчетом, для чего необходимо определить себестоимость получения заготовки в сравниваемых вариантах и показать преимущества предлагаемого способа по сравнению с существующим способом получения исходной заготовки. Себестоимость заготовки определяют в соответствии с указаниями, приведенными в работах [1.47].
В третьем случае, когда изменение способа получения заготовки существенно изменяет технологический процесс изготовления детали, оценка экономической эффективности должна производиться путем сравнения себестоимости изготовления изделия по
29
elib.pstu.ru
сопоставляемым вариантам. При этом учитывают как себестоимость получения исходной заготовки, так и себестоимость последующей механической, термической, химико-термической и др. обработки.
Сизд = Сзаг + Собр
Себестоимость получения исходной заготовки Сзаг и себестоимость последующих видов обработки (механической, термической, химико-термической и др.) Собр определяют согласно указаниям работ [1.47].
Степень совершенства предлагаемого метода получения исходной заготовки необходимо оценить коэффициентом использования материала.
7.9. Содержание и последовательность технологических операций и выбор средств технологического оснащения
[1.1–1.13, 1.14, 1.24, 1.25, 1.43, 1.46–1.48]
Выбор обработки отдельных поверхностей детали и последовательность выполнения операций выбирают исходя из требований рабочего чертежа и с учетом размеров, массы изделия, вида и способа получения исходной заготовки.
Вначале по заданным рабочим чертежом точности и шероховатости обрабатываемой поверхности намечают способ ее окончательной обработки. При этом следует руководствоваться справочными таблицами экономической точности и шероховатости обработки. Затем по известным свойствам исходной заготовки выбирают способ первичной (черновой) обработки поверхности. Зная способы окончательной и первичной обработки, намечают промежуточные способы обработки, при этом каждый последующий способ должен быть точнее предыдущего.
После того, как намечена последовательность обработки отдельных поверхностей, составляют маршрут обработки заготовки, выбирая из большого числа возможных вариантов решения оптимальный.
30
elib.pstu.ru