
Свариваемость материалов
..pdf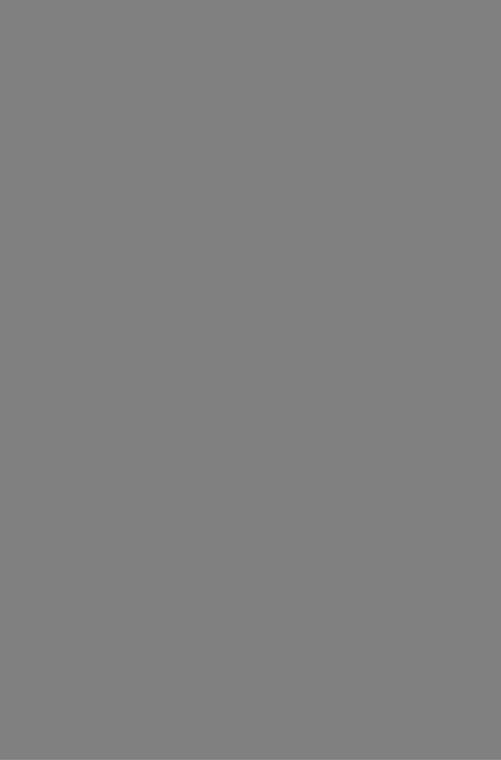
5 % фтористого натрия. Сварку осуществляют на постоянном токе обратной полярности. Для уменьшения разупрочнения хромомолибденованадиевых сталей в околошовной зоне реко мендуется Использовать режимы с малой погонной энергией. В связи с этим для сварки используется проволока диаметром 3 мм при силе тока 350—400 А, напряжении дуги 30—32 В и повышенных скоростях сварки (40—50 м/ч). Сварка хромомо либденовых сталей может осуществляться проволоками 0 4 и 5 мм при силе тока 520—600 и 620—650 А и напряжении 30— 32 и 32—34 В соответственно. Для сварки хромомолибденовых
сталей |
используется проволока марок Св-08МХ и Св-08ХМ, |
а для |
сварки хромомолибденованадиевых сталей — проволока |
Св-08ХМФА.
12.3.4. Электроконтактная сварка
Контактная стыковая сварка непрерывным оплавлением явля ется основным технологическим процессом при изготовлении элементов поверхностей нагрева котлов. Сварку труб диамет ром 30—40 Мм осуществляют на автоматизированных машинах ЦСТ-200 и ЦСТ-200М. Привод механизма оплавления и осадки у машин раздельный. При оплавлении передвижение подвиж ной плиты машины осуществляется кулачковым механизмом с электроприводом, постоянного тока, что обеспечивает плавное регулирование скорости оплавления. Программа, задаваемая кулачком, построена таким образом, что скорость оплавления непосредственно перед осадкой резко возрастает. Это способ ствует повышению качества сварных соединений. Машина ЦСТ-200М позволяет, кроме того, осуществлять сварку с подо гревом, что используется при изготовлении поверхностей на грева из сталей 12Х2МФСР и 12Х2МФБ. Характеристики ма шины следующие: первичное напряжение 380 В, номинальная мощность 200 кВ "А, ПВ 20%, номинальное свариваемое сече ние 900 мм2, максимальный ход подачи 30 мм, усилие осадки 90 Кн, зажатия 180 Кн.
Необходимое качество сварки труб достигается при выпол нении следующих рекомендаций. Установочная длина каждой трубы должна составлять 0,8—1,0 наружного диаметра трубы, но не менее 30 мм. Сварку необходимо производить при мини мально возможном вторичном напряжении (5,5—6,5 В), ис ключающем возникновение коротких замыканий при оплавле нии. Припуск на оплавление выбирают в зависимости от тол щины стенки трубы:
б, мм . . . . . . . |
3 |
4 |
5 |
7 |
Припуск, мм |
8 |
12 |
14 |
19 |
Длительность оплавления принимается из расчета обес печения средней скорости оплавления 0,75—1,25 мм/с. Конеч
ная скорость оплавления должна возрастать в 3—4 раза по сравнению со средней. Общий припуск на осадку должен со ставлять (1,0—1,5)6, а припуск на осадку под током — 0,5—0,8 общего припуска на осадку. Скорость осадки рекомендуется для труб из стали 12Х1МФ и 15Х1М1Ф не менее 30 мм/с, а для труб из стали 12Х2МФСР — не менее 60 мм/с.
Для уменьшения внутреннего грата в некоторых случаях во время сварки продувают трубы азотом или азотоводородной смесью с избыточным давлением около 0,1 МПа. При этом в связи с охлаждающим действием газа на зону стыка режимы сварки труб поверхностей нагрева следует корректировать с увеличением времени сварки и припуска на оплавление. По сле сварки грат может удаляться с помощью специальных сна рядов, которые закладываются в змеевик и под действием сжа того воздуха разрушают грат. Диаметр снарядов составляет обычно 0,9 от внутреннего диаметра трубы. После пробивки стыка снаряд удерживается снарядоулавливателем.
Стыки труб из сталей 12Х1МФ и 15Х1М1Ф мало восприим чивы к закалке и термической обработке после сварки их можно можно не подвергать. Кратковременному отпуску сле дует подвергать стыки труб из стали 12Х2МФСР (750±Ю °С в течение 10—20 мин).
12.3.5. Свойства сварных соединений
Эксплуатационная надежность сварных соединений определя ется их длительной прочностью и стабильностью механических свойств во времени.
При нормальной температуре механические свойства свар ных соединений находятся на уровне соответствующих свойств
свариваемых сталей. Значения |
этих свойств |
приведены |
в табл. 12.4. |
(105 ч и более) |
сварных со |
Опыт длительной эксплуатации |
единений хромомолибденовых сталей при 510 °С указывает на достаточную стабильность свойств при нормальной темпера туре. Временное сопротивление и ударная вязкость практиче ски не изменяются. Твердость начинает снижаться после 105 ч со 180 HV до 150—160 HV (3-105 ч эксплуатации). Временное сопротивление и ударная вязкость сварных соединений хромомолибденованадиевых сталей после работы при 565 °С в тече ние 105 ч также остаются на исходном уровне. Твердость сни жается с 200—240 HV до 160—180 HV [3].
При температуре 450—570 °С свойства сварных соединений н в первую очередь их длительная прочность несколько усту пают свариваемым сталям. Это обусловлено разупрочнением сталей в околошовной зоне под действием термического цикла сварки в результате дополнительного высокотемпературного
ТАБЛИЦА 12.4
МЕХАНИЧЕСКИЕ СВОЙСТВА СВАРНЫХ СОЕДИНЕНИЙ ПРИ 20 °С ПОСЛЕ ОТПУСКА
Марка стали |
Способ сварки |
ав |
а0.2 |
|
|
кси, |
||
|
|
|
|
|||||
|
|
|
|
МПа |
|
% |
Дж/сма |
|
|
|
|
|
|
|
|||
15ХМ |
Ручная |
дуговая |
450—500 |
220—300 |
15—22 |
30—55 |
140—200 |
|
|
электродами |
|
|
|
|
|
||
|
ЦУ-2ХМ- * |
|
|
20-22 |
|
|
||
20ХМЛ |
Полуавтоматиче |
420—450 |
240—280 |
55 -6 0 |
140—200 |
|||
|
ская |
|
дуговая в |
|
|
|
|
|
|
среде |
С02 прово |
|
|
|
|
|
|
|
локой |
|
|
|
|
|
|
|
|
Св-08ХГСМА |
|
|
|
|
|
||
12Х1МФ, |
Ручная |
дуговая |
500—580 |
350—450 |
15—18 |
70—75 |
130—160 |
|
15Х1М1Ф |
электродами ЦЛ-20 |
450—500 |
300—320 |
22—26 |
70—76 |
160—200 |
||
15Х1М1Ф* |
Автоматическая |
|||||||
|
дуговая под флю |
|
|
|
|
|
||
|
сом |
проволокой |
|
|
|
|
|
|
|
Св-08ХМФА |
|
|
|
|
|
||
* Свойства |
металла |
шва. |
|
|
|
|
|
отпуска и неполной перекристаллизации. Снижение длительной прочности сварных соединений по сравнению с основным метал лом зависит от характера термического цикла сварки, степени упрочнения -сталей термической обработкой и структурной ста бильности стали.
Длительная прочность хромомолибденовых сталей и их сварных соединений находится примерно на одном уровне (табл. 12.5). Это объясняется тем, что вследствие малой про-
|
|
|
|
|
|
ТА БЛИЦА 12.5 |
|
ДЛИТЕЛЬНАЯ ПРОЧНОСТЬ СВАРНЫХ СОЕДИНЕНИЙ ЗА 105 Ч |
|||||||
|
|
|
[2, |
4] |
|
|
|
|
|
|
|
|
Темпера |
Длительная проч |
|
|
|
|
|
|
ность за 10е ч, МПа |
||
Марка стали |
Способ сварки |
|
тура |
|
|
||
|
испыта |
|
сварное |
||||
|
|
|
|
|
ния, °С |
|
|
|
|
|
|
|
сталь |
соедине |
|
|
|
|
|
|
|
|
ние |
15ХМ |
Ручная |
дуговая |
электродами |
450 |
265 |
264 |
|
|
ЦУ-2ХМ |
|
|
|
550 |
63 |
59 |
20ХМЛ |
Полуавтоматическая |
дуговая |
475 |
274 |
226 |
||
|
в среде |
С02 |
проволокой |
550 |
59 |
58 |
|
12Х1МФ, |
Св-08ХГСМА |
электродами |
565 |
83 |
64 |
||
Ручная дуговая |
|||||||
15Х1М1Ф |
ЦЛ-20 |
|
дуговая под |
|
88 |
74 |
|
15Х1М1Ф |
Автоматическая |
|
88 |
78 |
флюсом проволокой Св-08ХМФА
каливаемости и нерегламентируемой скорости охлаждения при нормализации стали этой группы упрочняются в процессе тер мической обработки незначительно, а следовательно, и мало склонны к разупрочнению при сварке.
Хромомолибденованадиевые стали разупрочняются при сварке в большей степени, так как сталь 15Х1М1Ф, например, охлаждается при нормализации принудительно со скорстью около 1000 °С/ч, а трубы из стали 12Х1МФ проходят закалку.
Если коэффициент жаропрочности сварных соединений (т. е. отношение длительной прочности сварного соединения к дли тельной прочности основного металла) для нормализованной и отпущенной стали 15Х1М1Ф при ручной автоматической сварке равен 0,84—0,88, то для закаленной и отпущенной стали 12Х1М1Ф (толстостенные паропроводные трубы) он равен 0,77. Коэффициент жаропрочности сварных соединений хромомолиб денованадиевых сталей на уровне единицы можно обеспечить, используя после сварки в качестве термической обработки нор мализацию с отпуском. Однако в этом случае необходимо при менять такие сварочные материалы, которые обеспечивают термическую прорабатываемость швов на уровне свариваемой стали. Термическая же обработка должна быть не местной, а общей для всей сварной конструкции. Например, автоматйческая сварка стали 15Х1М1Ф под флюсом АН-22 проволокой Св-14Х1М1ФА с последующей нормализацией и отпуском обес печивает длительную прочность сварных соединений при 565 °С за 10s ч условного испытания, равную 88 МПа, а электрошлаковой проволокой Св-08ХМФ — 82 МПа [5].
Что касается кратковременных механических свойств свар ных соединении при рабочих температурах, то они не ^уступают соответствующим свойствам свариваемых сталей.
Раздел 4 ВЫСОКОЛЕГИРОВАННЫЕ СТАЛИ
—■ ■ И СПЛАВЫ
Гл ава 13. МАРТЕНСИТНЫЕ СТАЛИ (Зубченко А. С.)
13.1. Состав и свойства сталей
13.1.1. Назначение и марки сталей
В большинстве случаев высокохромистые мартенситные стали имеют повы шенное содержание углерода, некоторые из них дополнительно легированы никелем (табл. 13.1). Углерод, никель и другие аустенитообразующие эле менты расширяют область у и способствуют практически полному у-И 1 (Л1)- превращению в процессе охлаждения. Применение для закаленной стали отжига при температурах ниже точки Аз способствует отпуску структур за
калки и возможности получения весьма благоприятного сочетания механи ческих свойств — одновременно высоких значений прочности, пластичности и ударной вязкости. Ферритообразующие элементы (Mo, W, V, Nb) вводят для повышения жаропрочности сталей. Если обычные 12 %-ные хромистые стали имеют достаточно высокие механические свойства при температурах до 500 °С, то сложнолегированные на этой основе стали обладают высокими характеристиками до 650 °С и используются для изготовления рабочих и направляющих лопаток, дисков паровых турбин и газотурбинных установок различного назначения (табл. 13.2).
13.1.2. Структура сталей, легированных хромом
Железо образует |
с хромом |
непрерывный ряд сь(6)-твердых растворов |
||
с объемноцентрированной кубической |
решеткой |
(рис. 13.1). У сплавов с вы |
||
соким содержанием |
железа |
имеется |
замкнутая |
область у-твердых раство- |
|
|
0 |
5 |
10 Сг,% |
Рис. 13.1. Структурная диаграмма же- |
Рис. 13.2. Влияние хрома на положе- |
|||
лезо — хром |
|
ние критических точек фазовых пре |
||
|
|
вращений в сплавах с железом |
||
ров. На диаграмме Fe — Сг |
область |
у ограничена справа двумя линиями, |
||
замыкающими гетерогенный |
участок |
а»(6)+у. Хром |
|
оказывает сильное |
влияние на положение критических точек, отмечающих у-мх-превращение. Вначале увеличение содержания хрома приводит к понижению точки Лз. При концентрации до 8 % хром может быть отнесен к элементам, способ
ствующим устойчивости аустенита и расширению |
его температурной |
об |
ласти (рис. 13.2). Большие концентрации хрома |
повышают точку |
Лз. |
У сплавов с у-мх-превращением легирование хромом значительно снижает также критические скорости охлаждения. В результате этого при низком
содержании углерода легирование |
до |
12 % Сг приводит |
к формированию |
|||
в стали однофазной |
мартенситной |
структуры даже |
при |
весьма |
замедлен |
|
ном охлаждении от |
800 °С, например |
со скоростью |
менее |
I °С/с. |
|
При содержании хрома более 12 % в процессе нагрева у сплавов не возможно полное превращение а->-у. В соответствии с образующейся после
охлаждения |
структурой |
такие |
сплавы |
относят к |
мартенсисно-ферритному |
|
или ферритномУ классу. |
|
|
|
|
||
Связывая |
углерод в карбиды, ферритообразующие элементы способствуют |
|||||
в процессе охлаждения формированию в структуре |
II— 12 %-ных хромистых |
|||||
сталей |
наряду с мартенситом |
некоторого количества 6-феррита. В связи |
||||
с этим |
рассматриваемые |
в этом |
разделе |
некоторые |
марки высоколегирован- |

МАРТЕНСИТНЫХ СТАЛЕЙ |
|
|
|
|
|||
|
|
|
% (по массе) |
|
|
|
|
р |
Сг |
|
Ni |
Мо |
Y |
|
прочие |
<0,030 |
10.0— |
11,5 |
|
0,6-0,8 |
0,25—0,40 |
W |
0,7—1,1 |
<0,030 |
11.0— |
13,0-0,4—0,8 |
0,5-0,7 |
0,15—0,30 |
|||
<0,030 |
10.0— |
11,5 |
0,5—1,0 |
0,8—1,1 |
0,20—0,40 |
Nb 0,20—0,45 |
|
<0,030 |
10,5—12,0 |
1,50—1,80 |
0,35—0,50 |
0,18—0,30 |
W |
1,60—2,00 |
|
<0,025 |
10.0— |
12,0 |
0,60 |
0i60—0,90 |
0,15—0,30 |
W |
1,70—2,20 |
<0,025 |
12.0— |
13,5 |
2,8—3,2 |
0,8—1,1 |
|
Си |
0,8—1,0 |
<0,025 |
12.0— |
13,5 2,80—3,20 |
|
|
Си 0,80—1,10 |
Для высокохромистых сталей температура начала мартен ситного превращения не превышает 360 °С, а окончания 240 °С. С увеличением содержания углерода точки Тм.„ и Тм.к еще бо лее понижаются, что приводит к возрастанию твердости мартен сита и его хрупкости. Учитывая это, а также необходимость обеспечения сварным соединениям высокой пластичности и
|
|
|
|
|
ТАБЛИЦА 13.2 |
|
НАЗНАЧЕНИЕ ВЫСОКОХРОМИСТЫХ МАРТЕНСИТНЫХ СТАЛЕЙ |
||||||
|
|
|
|
|
|
Максималь |
Сталь, марка |
Примеры использования |
ная темпе |
||||
ратура эк |
||||||
|
|
|
|
|
|
сплуатации, |
|
|
|
|
|
|
0 С |
15ХПМФ, 15X11МФ-Ш, |
Корпуса цилиндров паровых и |
550-580 |
||||
15Х12ВНМФ, 15Х12ВНМФ-Ш, |
газовых турбин, горячие опоры |
500 |
||||
18Х11МНФБ-Ш, |
каркасов, рабочие и |
направ |
|
|||
13Х11Н2В2МФ, |
ляющие лопатки |
и бандажные |
|
|||
13Х11Н2В2МФ-Ш |
ленты |
диафрагм, |
диски и р о -' |
|
||
|
торы газовых турбин и ком |
|
||||
|
прессоров [6, |
7] |
|
|
|
|
12Х11В2МФ |
Поверхности |
нагрева |
котлов, |
550 |
||
|
трубопроводы |
|
|
|
|
|
10Х12НД |
Ободы диафрагм |
паровых тур |
350 |
|||
|
бин [6], детали рабочих колес |
|
||||
|
гидротурбин |
|
|
|
|
|
06Х12НЗД |
Ободы и другие Детали диа |
350 |
||||
06Х12НЗД |
фрагм |
паровых турбин |
[6] |
350 |
||
Детали |
рабочих |
колес |
гидро |
|||
06Х12НЗД |
турбин |
|
|
|
|
|
Корпуса главных циркуляцион |
350 |
|||||
|
ных насосов АЭС |
|
|
|
МЕХАНИЧЕСКИЕ СВОЙСТВА ВЫСОКО ХРОМИСТЫХ МАРТЕНСИТНЫХ СТАЛЕЙ
|
«0.2. |
°в. |
\ . К |
У. % |
к с и , |
Сталь, марка |
МПа |
МПа |
|
МДж/м2 |
|
|
|
|
|
|
|
|
|
|
не менее |
|
|
15Х11МФ |
490 |
690 |
15 |
55 |
0,6 |
15Х12ВНМФ |
590 |
740 |
15 |
45 |
0,6 |
18Х11МНФБ |
590—735 |
740 |
15 |
50 |
0,6 |
13Х11Н2В2МФ |
735 |
880 |
15 |
55 |
0,9 |
12X11В2МФ |
392 |
588 |
18 |
— |
— |
10Х12НД |
500 |
650 |
14 |
30 |
0,3 |
06X12НЗД |
500—700 |
700 |
14 |
30 |
0,5 |
ударной вязкости для. безопасной эксплуатации ответственных энергетических установок, содержание углерода в хромистых мартенситных сталях ограничивают до 0,20 %.
13.2.2. Выбор теплового режима сварки
Предотвращение образования холодных трещин является од ной из задач при сварке И —12 %-ных хромистых сталей. В связи с этим применяют предварительный и сопутствующий подогрев до 200—450 °С. Температура подогрева тем выше, чем
|
ОСОБЕННОСТИ ТЕПЛОВОГО РЕЖИМА СВАРКИ |
ТАБЛИЦА 13.4 |
||||
|
|
|||||
|
МАРТЕНСИТНЫХ СТАЛЕЙ |
|
|
|||
Сталь марка |
т, °с, |
Время пролежи- |
Термическая обработка |
|||
подогрева, |
вания до терми |
|||||
|
|
ческой обработки, |
ч |
|
|
|
15ХЫМФ, |
300 |
Не |
допускается |
Отпуск при 700—720 °С (без ох |
||
15Х12ВНМФ, |
|
|
|
лаждения |
ниже |
температуры |
18Х11МНФБ, |
|
|
|
подогрева). При толщине более |
||
13X11Н2В2МФ |
|
|
|
30 мм перед термообработкой |
||
|
|
|
|
рекомендуется |
«подстужива- |
|
|
|
|
|
ние» до 100 °С |
|
|
12Х11В2МФ |
250—300 |
|
72 |
Отпуск при 715—745 °С (пред |
||
|
|
|
|
варительный, и |
735—765 X |
|
|
>100 |
|
|
(окончательный) |
|
|
10Х12НД |
Не |
допускается |
Отпуск при 650 °С (с предвари |
|||
|
>200 |
|
|
тельным |
«подстуживанием») |
|
06Х12НЗД |
|
То же |
Отпуск при 610—630 °С (пред |
|||
|
|
|
|
варительный) и |
625—650 °С |
|
|
|
|
|
(окончательный) |
|
выше склонность стали к закалке. В то же время температура подогрева не должна быть чрезмерно высокой, так как это мо жет привести к отпускной хрупкости вследствие снижения ско-
- Кфх(%ъ+ % N ) + % Г1+4*%k\+о 4*%Ti + 1,5*%V+0,5*%W+0,9* % N D -0,6» %С0-
рнс. 1Э.З. Структурная диаграмма низкоуглероднстых нержавеющих сталей, предложенная Я. М. Потаком и Е. А. Сагалевич