
Аэрокосмическая техника высокие технологии и инновации – 2016
..pdf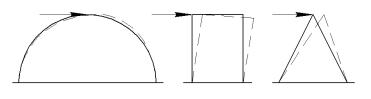
Рис. 5. Характер деформации выступов
Представляет большой интерес рассмотрение этой задачи для ременных передач. Здесь материал рабочего ремня при наложении нагрузки упруго деформируется и заполняет микронеровности поверхности шкива. Волнистость поверхности увеличивает площадь контакта и коэффициент трения, уменьшает износ ремня. Также необходимо учитывать условия заполняемости впадин конкретным материалом ремня и соотносить условия контактирования с прочностью ремня для того, чтобы при достижении критического тягового усилия не допустить его разрушения.
С этой целью была разработана технология обработки поверхностей ППД осциллирующим инструментом [3].
Рассмотрим траекторию и относительную скорость скольжения инструмента по поверхности детали. Расстояние точки контакта инструмента от выбранной точки отсчета в любой момент времени t равно
X S0 Nд t Asin 2 Nи.дв.хt Ф0 ,
где S0 – подача по станку; Nи. дв.х – частота осцилляции точки контакта, Nи. дв.х = Nи; Φ0 – начальный угол поворота инструмента.
Из анализа математической модели видно, что, изменяя соотношение частот вращения детали и инструмента, а также подач и амплитуд осцилляции, можно управлять траекторией и скоростью перемещения точки контакта инструмента по обрабатываемой поверхности, обеспечивая максимальное выглаживание микронеровностей или создавая требуемый микрорельеф поверхностей.
С применением пакета MathCAD проведены исследования характеристик процесса обработки инструментом со скользящим контактом для разных сочетаний величин подач и амплитуды осцилляции, разных значений частот вращения инструмента
61
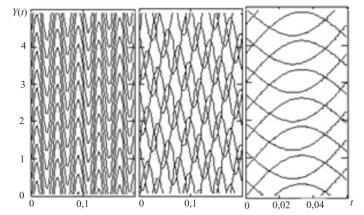
идетали. Проведены расчеты относительной скорости скольжения инструмента по обрабатываемой поверхности детали и траектории перемещения точки контакта (рис. 6).
Изменение режимов обработки осциллирующим инструментом со скользящим контактом позволяет в широких пределах варьировать параметры траектории перемещения точки контакта
иобеспечивать получение поверхности с различной микрогеометрией, а также изменять температуру в зоне контактного взаимодействия, что, в свою очередь, позволяет управлять свойствами материала поверхностного слоя обрабатываемой детали.
Рис. 6. Расчетные траектории перемещения точки контакта инструмента по обрабатываемой поверхности
для различных режимов обработки
Управление параметрами микропрофиля деталей представляется перспективным для более глубокого изучения. Задачей дальнейших исследований является поиск методов и режимов обработки, позволяющих получить максимально приближенный к оптимальному микрорельеф.
Список литературы
1.Демкин Н.Б., Рыжов Э.В. Качество поверхности и контакт деталей машин. – М.: Машиностроение, 1981. – 244 с.
2.Джонсон К. Механика контактного взаимодействия: пер.
сангл. – М.: Мир, 1989. – 510 с. – ISBN 5-03-000994-9.
62
3.Обработка деталей поверхностным пластическим деформированием: моногр. / М.Е. Попов [и др.]; под. ред. С.А. Зайдеса. – Иркутск: Изд-во ИрГТУ, 2014. – 560 с.
4.Попов М.Е., Аваниш А. Финишная обработка прецизионных поверхностей осциллирующим инструментом // Вестник ДГТУ. – 2002. – № 1. – С. 40–50.
УДК 621.1(075.8):004.4
АНАЛИЗ НОМЕНКЛАТУРЫ ОБРАБАТЫВАЕМЫХ ДЕТАЛЕЙ МЕТОДАМИ КЛАСТЕРНОГО И ФРАКТАЛЬНОГО АНАЛИЗА
М.Е. Попов, А.М. Попов, А.Е. Чеберкус
Донской государственный технический университет, Ростов-на-Дону, Россия
mepop@yandex.ru
Представлены результаты исследования методов оценки геометрической сложности, классификации и группирования деталей машин в интегрированных системах подготовки производства.
Ключевые слова: детали машин, сложность деталей машин, классификация, группирование, кластерный анализ, фрактальный подход.
Задачи технологической подготовки производства (ТПП) включают разработку технологических процессов и выбор соответствующего им технологического оборудования для изготовления конкретных деталей заданной формы и размеров. Каждая конкретная задача ТПП характеризуется номенклатурой (ассортиментом, семейством) деталей, подлежащих обработке [1].
Существуют три общих метода объединения деталей в семейства:
1)метод визуального контроля;
2)метод анализа технологических маршрутов;
3)метод классификации и кодирования деталей. Наибольшее применение на практике находит последний
метод. Он самый сложный из названных, но дает самый лучший
63
результат. Преобладающий недостатком метода анализа технологических маршрутов является, то, что он исходит из неизменности ранее определенных технологических маршрутов для изготовления отдельных деталей, что в определенной мере ограничивает творческий подход к образованию семейств деталей, обсуждая и варьируя полученные в каждом случае производственные процессы. Метод визуального контроля является наименее точным.
Группирование деталей методом классификации и кодирования характеризуется изучением конкретных конструктивных и (или) технологических характеристик деталей и приписыванием им кодовых чисел и шифров, образующих по определенному порядку код изучаемых деталей, служит для распределения их на определенные семейства либо по конструктивным, либо по технологическим признакам.
Классификация объектов, в данном случае деталей, позволяет ускорить их поиск по заданным признакам, так как сравнение кодового обозначения с кодами других деталей производится быстрее, чем прямое сравнение заданных на чертеже признаков. Кроме того, классификация удобна для механизированного и автоматизированного решения задач ТПП [2].
При классификации деталей по конструктивным признакам в основу положены конструктивные характеристики (геометрическая форма, наименование, выполняемая функция и т.д.). Геометрическая форма детали является наиболее объективным и стабильным признаком при ее описании, она характеризует непосредственно деталь, независимо от ее функции и принадлежности к другим изделиям, поэтому имеет главное значение.
Данная система позволяет произвести предварительную, главным образом конструкторскую, классификацию объектов производства с присвоением им определенного номера чертежа. Но эта система не обеспечивает получения необходимых данных для более полной характеристики деталей с учетом их технологических особенностей. Поэтому наряду с системами конструкторской классификации в настоящее время разработаны технологические классификаторы.
Одновременно с системами классификации и кодирования особое внимание заслуживают методы кластерного анализа, исключающие некоторые недостатки описанных систем.
64
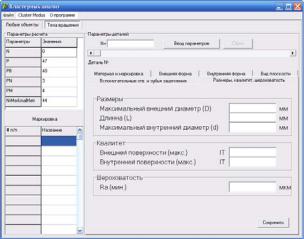
Кластерный анализ – совокупность математических методов, предназначенных для формирования относительно «отдаленных» друг от друга групп «близких» между собой объектов по информации о расстояниях или связях (мерах близости) между ними.
Задачей представленной работы является разработка и исследование подсистемы автоматизированной технологической подготовки для классификации различных технологических объектов (деталей, станков, инструментов и т.п.) с помощью ЭВМ. Разработанная программа (CLUSTAN), реализованная на программном языке Delphi 7, реализует математические методы кластерного анализа и представляет собой готовый инструмент для применения при решении задач группирования и классификации, исследование точного «поведения» которого при применении в практических условиях еще остается важной проблемой (рисунок).
Рис. Интерфейс программы CLUSTAN
В последнее время для оценки геометрической сложности различных объектов все шире применяют фрактальный подход [3, 4]. Понятие фракталов привлекалось для выражения в упрощенном виде неправильного очертания предметов. Исследование фрактальности сводится к математическому выражению критериев, описывающих реальные конфигурации. Свойство выглядеть
65
в любом сколь угодно мелком масштабе приблизительно одинаково называется масштабной инвариантностью, множества, которые им обладают, – фракталами.
Фрактальная размерность чувствительна ко всякого рода несовершенствам реальных объектов, позволяя различать и индивидуализировать то, что прежде было безлико и неразличимо.
Фракталы – это математические модели сложных структур, пространственные изображения которых представляются в виде сломанных, морщинистых и нечетких форм. Фракталы в данной статье рассматриваются как математические абстракции, которые обладают некоторыми характерными свойствами. Такие фрактальные структуры имеют широкое применение не только в естественной, но и в искусственной среде [3, 4].
Развитие ЭВМ и средств мультимедиатехнологий привело к возможности эффективной реализации сложных рекурсивных процедур построения объектов фрактальной геометрии и последующей компьютерной визуализации этих объектов.
Определение стратегий и возможных направлений процесса конструкторского проектирования должно рассматриваться в соответствии с иерархической формулой: материалы → технологии → формы. Современное состояние научно-технической базы существенно расширяет возможности формообразования, особенно в аспекте реализации фрактальных форм. Можно привести современные примеры машин и сооружений, сочетающих функциональность, технологичность, экологичность и образное решение с интересным дизайнерским решением, отражающим фрактальные формы, причем сознательно и целенаправленно.
Список литературы
1.Ильин А.И. Планирование на предприятии: учеб. пособие. – 7-е изд., испр. и доп. – Минск: Новое знание, 2006. – 668 с.
2.Давыдов А.Н., Судов Е.В., Якунина О.В. Применение расширенной идеологии IDEF для анализа и реинжиниринга биз- нес-процессов в производственных и организационных системах // Проблемы продвижения продукции на внешний рынок. – 1997. – Спец. вып. – С. 23–27.
3.Мандельброт Б. Фрактальная геометрия природы. – М.: Ин-т компьютерных исслед., 2002. – 856 с.
66
4. Шредер М. Фракталы, хаос, степенные законы. – М.; Ижевск: НИЦ «Регулярная и хаотическая динамика», 2001. – 527 с.
УДК 621.9.015
ДИАГНОСТИРОВАНИЕ И МОДЕЛИРОВАНИЕ ФИЗИЧЕСКИХ ПАРАМЕТРОВ ПРОЦЕССА РЕЗАНИЯ ПРИ СВЕРЛЕНИИ КОМПОЗИЦИОННЫХ МАТЕРИАЛОВ
В.Ф. Макаров, И.И. Койнов
Пермский национальный исследовательский политехнический университет, Пермь, Россия
makarovv@pstu.ru, 111igoresha111@mail.ru
Проведены исследования зависимостей влияния физических параметров процесса резания (силы, виброскорости, шума, температуры) от режимов резания. Описана методика математического планирования. Представлены математические модели зависимостей, выводы и заключение по применению компьютерного стенда диагностики процесса резания для выбора оптимальных режимов резания при обработке композиционного материала марки ВКУ-39.
Ключевые слова: композиционный материал, диагностика, исследование, влияние, физические параметры, оптимальные режимы резания, сверление.
Развитие авиационной и ракетно-космической техники неразрывно связано с разработкой новых конструктивных решений, прогрессивных инновационных технологий, совершенствованием существующих или созданием композиционных материалов, обладающих уникальными свойствами – при малом весе достаточно большой прочностью.
Широкое применение новых композиционных материалов на основе стеклопластиков и углепластиков сдерживается из-за проблем, связанных с механической обработкой прежде всего при сверлении отверстий. Это обусловлено низкой стойкостью режущих инструментов, обеспечением требуемого качества об-
67
работанной поверхности и точности размеров обрабатываемых деталей при сверлении, фрезеровании, точении. Основные дефекты поверхности композиционного материала при воздействии режущего инструмента следующие: неравномерная повышенная шероховатость; вырывы и сколы на торцах; расслоение и вырыв волокна (деламинация), ворсистость; трещины в матрице материала; отклонение сверх допуска формы и взаимного расположения поверхностей.
Основным направлением диагностирования является анализ и сведение к минимуму вибрации, шума, сил и температуры резания. Управляющими факторами такого снижения могут служить режимы резания и геометрия режущих инструментов.
В Пермском национальном исследовательском политехническом университете на кафедре «Инновационные технологии машиностроения» для решения поставленной выше задачи разработан комплексный компьютерный центр диагностики процесса сверления композиционного материала.
Условия испытаний: исследования процесса сверления композиционного материала проводились на универсальном фрезерном станке модели JET JMD-1452 TS DRO. Обрабатывались образцы 80×27×6 мм из углепластика ВКУ-39 по ТУК 55/13-615 АО ПМ «Машиностроитель». Каждый опыт повторялся от 2 до 3 раз в зависимости от величины разброса получаемых данных. Инструмент – спиральное сверло фирмы TIZ (Ø = 2,0 мм; угол в плане 2φ = 118°; материал Р6М5К5; износостойкое покрытие TIN предотвращает налипание обрабатываемого материала). Обработка образцов производилась без СОЖ, так как не допускается по техническим условиям.
Методика установления зависимости физических параметров процесса резания (сила, виброскорость, шум, температура) предусматривает применение метода математического планирования экспериментов [1, 2]. Для описания этой зависимости физических параметров процесса резания от независимых переменных скорости резания V, м/мин, и подачи S, мм/об, выбираем эксперимент 22. Исследуемыми параметрами являются: сила резания, виброскорость, шум резания, температура резания.
На примере радиальной составляющей силы резания Py проверка значимости коэффициентов bi проходила с помощью кри-
68
терия Стьюдента [tкр = 2,3](8; 0,05). Для данной модели значения критериев следующие: t0 = 69,82, t1 = 26,07, t2 = 4,91, t12 = 0,22.
Если ti > tкр, то гипотеза отвергается и коэффициент bi признается значимым [3]. В данном случае незначимым коэффициентом яв-
ляется b12.
Построенные математические модели, отражающие зависимость основных физических параметров процесса резания от режимов резания, являются значимыми, адекватными и пригодными для дальнейших исследований процесса резания композиционных материалов [3].
Для радиальной составляющей силы резания
Fрасч = 0,048 < Fкр (8; 0,05) = 5,3.
Для виброскорости
Fрасч =4,532 < Fкр (8; 0,05) = 5,3.
Для шума резания
Fрасч = 4,735 < Fкр (8; 0,05) = 5,3.
Для температуры
Fрасч = 2,289 < Fкр (8; 0,05) = 5,3.
Таким образом, были построены математические модели физических параметров процесса резания:
– для радиальной составляющей силы резания Py, Н,
P |
9,807 e4,117 |
S 0,195 |
|
601,903 S 0,195 |
; |
V 0,785 |
|
V 0,785 |
|||
y |
|
|
|
– для виброскорости, м/с,
В e2,424 V0,298 S1,266 11,291V0,298 S1,266 ;
– для шума резания, дБ,
Ш e5,258 V 0,12 S 0,397 85, 627V 0,12 S 0,397 ;
– для температуры резания, °С,
T e3,388 V 0,021 S 0,082 29, 607V 0,021 S 0,082 .
Выводы:
1. Применение компьютерного стенда диагностики позволяет сократить трудоемкость и материалоемкость стойкостных испытаний.
69
2.Установлено, что при сверлении отверстий Ø2 мм в углепластике ВКУ-39 с увеличением скорости резания V от 6,3 до 28,6 м/мин уменьшается радиальная составляющая силы резания
Py от 97 до 24 H; увеличивается виброскорость В (с 0,36 до 2,4 м/с); шум резания Ш (от 30 до 56 дБ); температура Т (с 24,0 до
27,3 °С).
3.C увеличением подачи S от 0,045 до 0,142 мм/об увели-
чивается радиальная составляющая силы резания Py (от 24 до 97 H); виброскорость В (0,36 до 2,4 м/с); шум резания Ш (от 30 до
56 дБ); температура Т (24,0 до 27,3 °С).
4.Получены математические модели зависимости в диапазоне скорости резания V от 6,3 до 28,6 м/мин и подачи S от 0,045 до 0,142 мм/об, которые позволяют определять оптимальные режимы сверления композиционного материала марки ВКУ-39 по ТУК 55/13-615 АО ПМ «Машиностроитель».
5.Применяя разработанный стенд, появилась возможность: а) управлять процессом резания на станках с помощью ди-
агностики; б) выбирать наиболее рациональную геометрию и марку ма-
териала; в) назначать наиболее оптимальные режимы резания;
г) предупреждать возможную поломку инструмента и дорогостоящее оборудование.
6. С точки зрения оптимизации процесса резания, чем меньше вибрация, шум, сила резания, тем более благоприятные условия наблюдаются в зоне резания и тем выше стойкость режущих инструментов, производительность и меньше себестоимость обработки.
В результате анализа результатов проведенных экспериментов установлено, что для повышения эффективности работы станка, повышения стойкости сверл необходимо минимизировать значения вибрации, шума и силы резания. При этих условиях оптимальным режимом резания является режим со значениями
V = 28,6 м/мин, S = 0,045 мм/об.
При |
этом |
Py min 2, 429 Н; |
Вmin = 0,623 |
м/см/с; |
Шmin 38,95 дБ ; Tmin 24,6 °С.
70