
Аэрокосмическая техника высокие технологии и инновации – 2016
..pdfисследовательского политехнического университета. Аэрокосми-
ческаятехника. – 2014. – №36. – С. 119–130.
3. Бербек А.М. Теоретическое обоснование создания ракетного двигателя на порошкообразном металлическом горючем и воде в качестве окислителя: дис. ... канд. техн. наук. – Пермь, 2012. – 134 с.
4.Математическое моделирование воспламенения и горения частиц алюминия за ударными волнами, учитывающее кинетику процессов и особенности накопления окисла / В.И. Малинин, Е.И. Коломин, И.С. Антипин, В.Л. Рылов // Химическая фи-
зика. – 2001. – Т. 20, № 6. – С. 75–83.
5.Демидов С.С., Малинин В.И., Бульбович Р.В. Моделирование воспламенения порошка алюминия, распределенного в газовом потоке с высоким содержанием кислорода // Вестник Пермского национального исследовательского политехнического университета. Аэрокосмическая техника. – 2016. – № 46. – С. 73–86.
УДК 621.92
ИСПОЛЬЗОВАНИЕ МЕТОДА ЭЛЕМЕНТАРНЫХ ПОВЕРХНОСТЕЙ ПРИ МОДЕЛИРОВАНИИ ПРОЦЕССА ПРОФИЛЬНОГО ГЛУБИННОГО ШЛИФОВАНИЯ
В.Ф. Макаров, С.П. Никитин
Пермский национальный исследовательский политехнический университет, Пермь, Россия
makarovv@pstu.ru
Представлена методика прогноза качества обработки при глубинном профильном шлифовании на многоосевом станке поверхностей сложной формы. Приведены элементарные поверхности и математические модели контакта шлифовального круга с элементарными поверхностями, позволяющие прогнозировать съем материала, износ шлифовального круга и шероховатость по каждой элементарной поверхности на основе режимов резания, характеристики круга, динамики упругих, тепловых и рабочих процессов в технологической системе. Данная методика позволяет управлять процессом глубинного профильного шлифования для достижения заданных параметров
31
качества лопаток газотурбинных двигателей и повышения производительности обработки.
Ключевые слова: технология обработки, глубинное шлифование, многоосевая обработка, динамическая система станка, динамические характеристики.
Глубинное шлифование применяется главным образом для окончательной обработки плоских и сложнофасонных поверхностей хвостовиков и полок рабочих и сопловых лопаток турбин газотурбинных двигателей (ГТД) [1, 2]. Для повышения точности, гибкости и производительности обработка осуществляется на многоосевых обрабатывающих центрах с ЧПУ. При этом возникают проблемы с размерной точностью сложного профиля лопатки, а также с дефектами поверхностного слоя в виде прижогов и трещинообразования на ряде поверхностей [1–3]. Для обеспечения заданной размерной точности и качества поверхностного слоя при обработке лопаток ГТД приходится реализовывать множество проходов [1], что снижает производительность глубинного шлифования.
При глубинном профильном шлифовании контура сложной формы одновременно формируется несколько различных поверхностей, отличающихся условиями формообразования. Наблюдаются варьирование режимов резания, припусков, пятна контакта шлифовального круга с заготовкой и т.д. Это приводит к различию сил резания, действующих на зерно; упругих и динамических деформаций; величины съема; температур в зоне контакта, которые определяют размерную точность и качество поверхностного слоя [1–3]. Исходя из этого возникает проблема выбора режимов шлифования и характеристик круга для обеспечения приемлемых размерной точности и качества поверхностного слоя при шлифовании сложного профиля. Для решения этой проблемы предлагается использовать математическое моделирование динамики процесса профильного глубинного шлифования.
Обработку сложных поверхностей лопаток можно представить как композицию элементарных поверхностей и простых схем профильного шлифования: плоского шлифования периферией круга, плоского шлифования торцом круга и профильного шлифования методом копирования (таблица). Набор элементар-
32
ных поверхностей должен позволять отображать любой реальный профиль сложной поверхности с необходимой точностью.
Кинематическое различие реализуемых схем шлифования элементарных поверхностей сводится к вариации пятна контакта шлифовального круга и заготовки [1]. Поэтому необходимо оценить различие параметров качества обработки выделенных элементарных поверхностей при разных схемах шлифования, определяющих разные условия контакта шлифовального круга и заготовки. Основными характеристиками контакта являются среднее
число режущих зерен на единице поверхности круга nз , средняя глубина среза единичным зерном zз и площадь пятна контакта шлифовального круга с заготовкой. Пятно контакта шлифовального круга с заготовкой определяет эквивалентный диаметр DЭ и длину зоны контакта шлифовального круга с заготовкой lк [2, 4].
Для обеспечения заданных значений качества, размерной точности и производительности при глубинном профильном шлифовании лопаток газотурбинных двигателей на многоосевых станках необходимо обеспечить устойчивость процесса, ограничение силы и температуры шлифования, равные показатели по съему, слою микронеровностей и износу круга по каждой элементарной поверхности за счет выбора оптимальных режимов резания и характеристик круга. Поэтому требуется оценить: а) устойчивость процесса шлифования; б) величину съема материала при обработке элементарной поверхности ( r и вероятность съема материала p(м)); в) толщину слоя микронеровностей H или шероховатость элементарной поверхности Ra; г) критерий износа шлифовального круга Rз [4]. Эти показатели взаимосвязаны и определяются кинематикой и динамикой взаимодействия шлифовального круга и заготовки.
Для изучения устойчивости процесса глубинного шлифования предлагается использовать математическое моделирование [5]. В условиях неустойчивости выполнение обработки или достижение заданных параметров качества невозможны. Математическое моделирование позволяет добиться устойчивости процесса глубинного шлифования за счет изменения параметров обработки, в том числе конструктивных параметров технологической системы, при сохранении максимально возможной производительности.
33
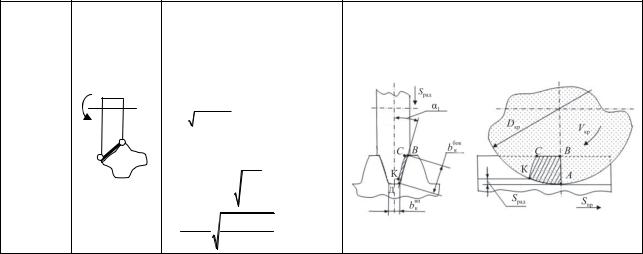
34
|
|
|
Пример выделения элементарных поверхностей при глубинном |
||||||
|
|
|
шлифовании сложного профиля на многоосевом станке с ЧПУ |
||||||
Элемен- |
|
|
|
|
|
|
|
|
|
тарная |
Эскиз |
|
Схема шлифования |
Пятно контакта |
|||||
поверх- |
|
и параметры контакта |
|||||||
|
|
|
|
||||||
ность |
|
|
|
|
|
|
|
|
|
|
|
|
|
|
|
|
|
|
|
1 |
2 |
|
|
|
|
3 |
|
4 |
|
Наклонная |
|
|
Профильное шлифование |
|
|||||
поверх- |
|
|
наклонной поверхности. |
|
|||||
ность |
|
|
lк |
Sрад Dкр , |
|
|
|
||
|
|
2 |
b |
bбок , |
|
|
|
||
|
|
|
|
|
|||||
|
1 |
|
к |
к |
|
|
|
||
|
|
tф |
Sрад sin i , |
|
|
|
|||
|
|
|
|
|
|
||||
|
|
|
aбок Sпр L |
tф |
|
|
|||
|
|
|
z |
|
60Vкр |
|
Dкр |
|
|
|
|
|
|
|
|
|
Sпр L Sрад sin i 60Vкр Dкр
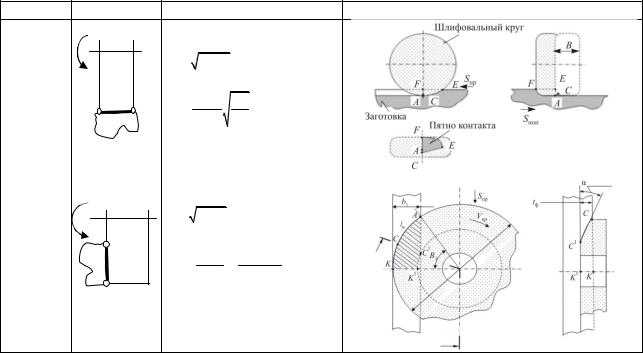
Окончание таблицы
1 |
2 |
3 |
4 |
Плоскость |
|
Плоское шлифование перифе- |
|
|
|
рией круга выступа. |
|
|
|
|
|
|
lк |
Dкр tф , |
|
|
|
bк 1,1Sпоп , |
|
|
2 |
3 |
az |
Sпр L |
tф |
|
|
60Vкр |
Dкр |
|
|
|
|
35
Торец |
|
Плоское шлифование |
||||
|
|
торцом круга. |
||||
|
|
l |
к |
|
b D |
, |
|
|
|||||
|
|
|
|
1 кр |
||
4 |
|
bк tф , |
|
|
a |
z |
az max |
|
Sпр L |
|
|
|
2 |
|
2 60Vкр |
|
|
5 |
|
|
|
|
||
sin sin 1 |
|
|
||||
|
|
|
При обеспечении устойчивости процесса необходимо на основе математического моделирования [5] получить статические и динамические характеристики, которые будут определять взаимные смещения шлифовального круга и заготовки A0 , текущую
глубину резания tф , колебания силы шлифования P и температур в зоне резания i .
Предложенные модели для расчета параметров контакта могут быть использованы при исследовании особенностей динамики тепловых процессов при глубинном шлифовании лопаток. Это позволит изучать влияние условий профильного глубинного шлифования на тепловые процессы в зоне обработки, на относительные смещения шлифовального круга и заготовки из-за динамических явлений и задавать оптимальные режимы резания и характеристику круга.
Список литературы
1.Макаров В.Ф. Современные методы высокоэффективной абразивной обработки жаропрочных сталей и сплавов: учеб. по-
собие. – СПб.: Лань, 2013. – 320 с.
2.Полетаев В.А., Волков Д.И. Глубинное шлифование лопаток турбин: библиотека технолога. – М.: Машиностроение, 2009. – 272 с.
3.Старков В.К. Шлифование высокопористыми кругами. – М.: Машиностроение, 2007. – 688 с.
4.Новоселов Ю.К. Динамика формообразования поверхностей при абразивной обработке. – Саратов: Изд-во Сарат. ун-та, 1972. – 232 с.
5.Никитин С.П. Моделирование процесса резания при шлифовании с учетом взаимодействия упругой и тепловой сис-
тем // Вестник УГАТУ. – 2009. – Т. 12, № 4 (33). – С. 61–65.
36
УДК 621.9
ОРГАНИЗАЦИЯ КОМПЛЕКСНОГО ПОДХОДА ДЛЯ ЭФФЕКТИВНОГО ВЫПОЛНЕНИЯ СБОРОЧНЫХ ОПЕРАЦИЙ ВЫСОКОТОЧНЫХ ИЗДЕЛИЙ АВИАЦИОННО-КОСМИЧЕСКОЙ ПРОМЫШЛЕННОСТИ
А.В. Назарьев, П.Ю. Бочкарев
Саратовский государственный технический университет имени Ю.А. Гагарина, Саратов, Россия
alex121989@mail.ru, bpy@sstu.ru
Рассматривается организация комплексного подхода (комплекса проектных процедур), обеспечивающего эффективное выполнение сборочных операций на основе связи между технологической подготовкой обрабатывающего и сборочного производств высокоточных изделий авиационно-космической промышленности.
Ключевые слова: сборочное производство, комплекс проектных процедур технологической подготовки производства, высокоточные изделия, конфигурационное пространство.
В настоящее время проблема совершенствования машиностроительных производств, в том числе авиационно-космической промышленности, приобретает первостепенное значение, так как развитие данных отраслей происходило стихийно, что в итоге привело к значительному расходу материальных, энергетических
итрудовых ресурсов, отрицательно влияющих на состояние окружающей среды и т.п. Особенно ярко это проявляется при изготовлении высокоточных узлов, поскольку данные изделия характеризуются жесткими, постоянно возрастающими требованиями к качеству изготовления. Обеспечение данных требований существующими методами связано в основном с чрезмерными проблемами, решение которых достигается в большинстве случаев затратными способами в виде многочисленных переборок, доработок
иуточнения конструкции, поскольку эти требования в серийном производстве находятся на грани максимально технологически достижимых. Кроме того, значительные трудности, особенно на этапе сборочного производства, связаны с влиянием непознанных
37
инеуправляемых причин, вызывающим непрогнозируемый разброс заданных эксплуатационных характеристик [1, 2].
Именно поэтому необходимо проведение исследований по созданию комплексного подхода к решению существующих задач в авиационно-космическкой промышленности, особенно сборки высокоточных изделий, так как основными особенностями эффективного функционирования предприятий авиационнокосмической промышленности являются сжатые сроки и высокое качество технологической подготовки производства (ТПП) [2].
На сегодняшний день наблюдаются разрозненные решения отдельных задач этой проблемы, отсутствует наиболее приближенная к реальным требованиям концепция системы в целом [1].
Предлагается комплексный подход (комплекс проектных процедур), который основывается на установлении связи между технологической подготовкой обрабатывающего и сборочного производств с учетом требований, заложенных при проектировании изделия. Подход позволит в зависимости от складывающейся производственной ситуации выбирать оптимальные технологические процессы обработки элементов, учитывающие требование последующей сборки. Это, в свою очередь, позволит снизить трудоемкость, время и себестоимость изготовления, повысить качество и точность высокоточных изделий, сократить время и трудоемкость при технологической подготовке производства. Комплекс проектных процедур включает в себя анализ требований к сборке высокоточных изделий и возможных технологических процессов обработки деталей, входящих в высокоточные изделия, и выбор на основе анализа рациональных технологических процессов. В общем виде структура комплекса приведена на рисунке.
Анализ исходных данных и выбор рациональных технологических процессов в системе автоматизированного планирования технологических процессов (САПЛ-ТП) [3] происходит в несколько этапов.
Первоначально проводятся конструкторский размерный анализ сборочного изделия и деталей, задействованных в сборке,
итехнологический размерный анализ множества возможных вариантов технологических процессов, разработанных в САПЛ-ТП.
38
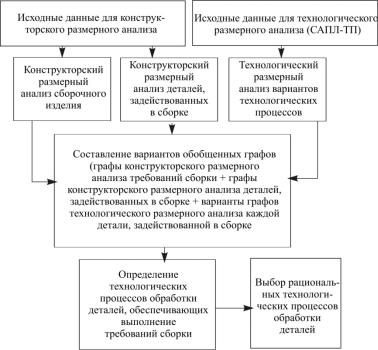
Исходными данными для проведения конструкторского размерного анализа являются конструкторская документация на сборочное изделие и детали, задействованные в сборке, и полученные на основе обработки конструкторской документации базы данных. На основе исходных данных проводится конструкторский размерный анализ сборочного изделия и деталей, участвующих в сборке. Для автоматизации данного этапа применена математическая модель представления и анализа деталей и сборок (в том числе и высокоточных) с использованием понятия конфигурационного пространства [4].
Рис. Структура комплекса проектных процедур в общем виде
Одним из подходов, позволяющих автоматизировать ТПП, является САПЛ-ТП, обеспечивающая параллельное проектирование технологических процессов для заданной группы деталей в рассматриваемый период с учетом реально складывающейся производственной ситуации [3].
39
Для технологического размерного анализа исходными данными является множество вариантов технологических процессов изготовления деталей, задействованных в сборке, полученное в САПЛ-ТП. Технологический размерный анализ сводится к построению графов возможных технологических процессов изготовления деталей. Для автоматизации расчета технологических размерных цепей используется подход, исходными данными для которого являются граф технологического процесса и размерные цепи [5].
На заключительном этапе выбирается множество технологических процессов изготовления деталей, удовлетворяющих требованиям сборки, из которых определяется вариант рационального технологического процесса с учетом складывающейся производственной ситуации.
Таким образом, представлена структура и проанализированы возможные решения реализации комплекса проектных процедур, обеспечивающего эффективное выполнение сборочных операций на основе связи между ТПП обрабатывающего и сборочного производств высокоточных изделий с учетом требований, заложенных при проектировании изделия.
Список литературы
1.Семенов А.Н. Проблемы теоретического обеспечения сборки высокотехнологичных изделий // Инструмент и техноло-
гии. – 2004. – № 21–22. – С. 122–124.
2.Базров Б.М. Основы технологии машиностроения: учеб. – М.: Машиностроение, 2005. – 736 с.
3.Бочкарев П.Ю. Системное представление планирования технологических процессов механообработки // Технология ма-
шиностроения. – 2002. – № 1. – С. 10–14.
4.Гаер М.А., Журавлев Д.А., Яценко О.В. Конфигурационные пространства поверхностей деталей и сборок // Вестник ИрГТУ. – 2011. – № 10 (57). – С. 32–36.
5.Мухолзоев А.В. Алгоритм модуля автоматизированного расчета технологических размерных цепей // Вестник ЮУрГУ.
Сер.: Машиностроение. – 2015. – Т. 15, № 3. – С. 48–55.
40