
Механика композитных материалов 4 1980
..pdfкромка инструмента 7 касается образца биоткани, размером ЮХЗОХ Х70 мм. Биоткань выделена из мышц задних конечностей кролика. На тросике 9 подвешивали груз 8, имитирующий усилие резания, прикла дываемое хирургом к ультразвуковому инструменту. Далее проводили балансировку моста и выверяли амплитуду и частоту ультразвуковых колебаний. Измерение амплитуды проводили оптическим методом с ис пользованием горизонтального микроскопа МГ (разрешающая способ ность 2 мкм). Частоту контролировали электронным частотомером
43-33. После освобождения тележки 5 от стопора 15 начинался процесс резания.
В первой серии опытов определяли зависимость скорости резания от усилия резания. Проводили измерение средней скорости движения инст румента в биоткани в зависимости от массы грузов, имитирующих на ла бораторной установке усилие резания, прикладываемое хирургом к ре жущему инструменту. Масса грузов в основном изменялась в пределах 0,1,..., 1,5 кг, что приближенно соответствует применяемому в клинике диапазону усилий хирурга при ультразвуковом оперативном методе на мягких биотканях кисти. Экспериментальные результаты представлены на рис. 1. В тех же координатах построена теоретическая кривая 1, отра жающая функциональную зависимость (1) при следующих значениях акустических параметров: Л = 20 мкм, f = 26,5 кГц, /Со = 0,04. Сила со противления биоткани /о = 1,8 кгс также измерена экспериментально. Сравнивая кривые 1 и 2, нетрудно заметить, что они имеют идентичный вид. Экспериментально определенная величина максимальной скорости резания приближенно совпадает с теоретически рассчитанной V= =70 мм/с. Расхождение теоретических расчетов с данными измерений не превышает 20%, что свидетельствует об удовлетворительном согласии теоретических и экспериментальных результатов. Отличие эксперимен тальной кривой 2 от теоретической 1 (см. рис. 1), выходящее за пределы ошибок измерений, наблюдалось при усилиях резания, меньших 0,2 кгс. Оно может быть вызвано, на наш взгляд, нескомпенсированными силами трения, имеющимися в лабораторной установке, и силой трения инстру мента о поверхность биоткани, которая не учитывалась при проведении теоретических расчетов. Эта сила измерена экспериментально и состав ляет 15± 5 гс. При малых усилиях резания она начинает играть все возрастающую роль в процессе резания.
Экспериментальное подтверждение аналитических расчетов свиде тельствует о правильности примененного теоретического подхода к расчету скорости ультразвукового разделения мягких биотканей. Это позволяет использовать зависимости (1) и (2) как для нахождения опти мальных параметров процесса резания, так и для определения его мак симальной производительности, которая достигается, как предсказывает теория, при равенстве усилия резания силе сопротивления биоткани: h=fo= 1,8 кгс.
Во второй серии опытов определяли влияние амплитуды ультразвуко вых колебаний режущей кромки инструмента на скорость резания мяг кой биоткани. Изменением величины тока подмагничивания магнитостриктора регулировали амплитуду ультразвуковых колебаний, которая менялась в пределах 1 0 ,..., 40 мкм. На рис. 4 прямая 1 построена на основании теоретически выведенной зависимости (2), устанавливающей линейную связь скорости резания с амплитудой ультразвуковых колеба ний. Прямая 2 проведена наилучшим образом с помощью метода наи меньших квадратов через экспериментальные точки. Из рис. 4 видно, что с увеличением амплитуды, например, в три раза, максимально достижи мая скорость увеличивается также в три раза. Экспериментально опре деленная величина, соответствующая данной амплитуде, несколько меньше.
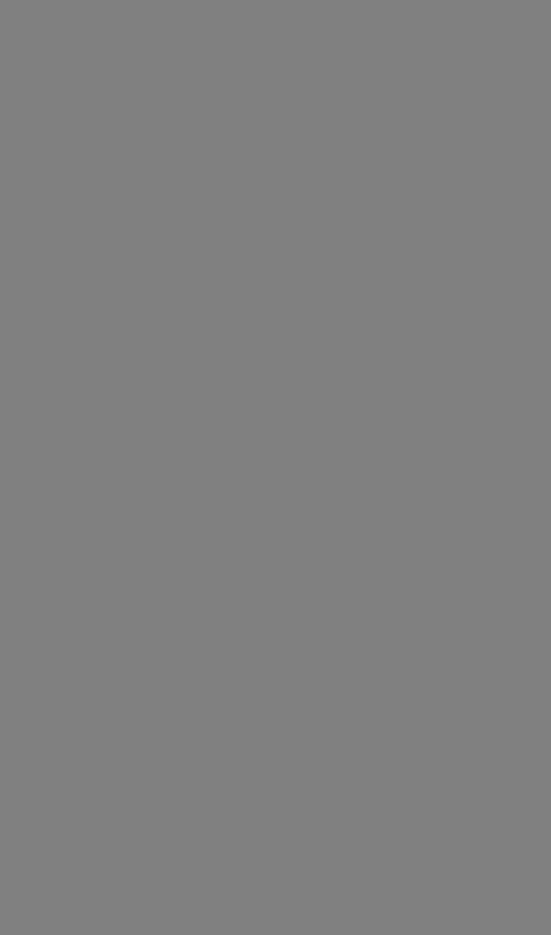
ему необходимо на границе раздела тканей (точки b, d, е, рис. 5) скачко образно изменять усилие резания.
Из графиков 1—3 рис. 5 видно, что теоретически максимальная ско рость резания одинакова для различных биотканей и определяется только акустическими параметрами процесса ультразвукового резания: Vmax= -^tL>i\o- Достигнуть эту скорость можно, приложив к режущему ин струменту усилие, равное силе сопротивления резанию данного вида био ткани. Экспериментально измеренные максимальные скорости ультра звукового резания для кожной, жировой и мышечной тканей оказались приближенно одинаковыми и равными 64 ± 5 мм/с (Л = 20 мкм, /=26,5 кГц, Ко=0,04). Достигалась эта скорость при различных усилиях резания, соответственно равных /0К= 3,2 кгс, /ож = 0,16 кгс и /0М=1,8 кгс. Совпадение максимальных скоростей резания биотканей свидетельст вует о независимости этой скорости от механических свойств биоткани и о справедливости теоретически выведенной зависимости (2). Описанное явление, как подсказывает теория, должно наблюдаться для любых био логических тканей, у которых сила сопротивления резанию много меньше амплитудного значения силы ультразвуковых колебаний, т. е. Гх<сЛш2т .
Проведенный анализ, в частности, показывает, что для поддержания максимальной производительности процесса резания при переходе режу щего ультразвукового инструмента от одного вида биоткани к другому хирургу необходимо определенным образом изменять усилие резания.
Отметим, что ультразвуковая резка мягких биотканей может осу ществляться при любых усилиях резания, в том числе и меньших силы сопротивления биоткани. Обычное же резание происходит только при усилиях резания, больших силы сопротивления биоткани. Если увели чить усилие резания сверх силы сопротивления биоткани, то производи тельность процесса ультразвукового резания начинает падать. Кроме того, в этом случае ультразвуковой метод становится невыгодным, так как может осуществляться обычное безультразвуковое резание.
Таким образом, для достижения максимальной производительности ультразвукового резания мягких биотканей хирург должен приклады вать к режущему инструменту усилие, равное силе сопротивления реза нию данного вида биоткани. При меньших усилиях также происходит резание, но с меньшей скоростью. Для повышения производительности резания необходимо увеличивать амплитуду и частоту ультразвуковых колебаний, а также инерционные свойства инструмента путем относи тельного увеличения массы его колеблющейся части.
Авторы выражают признательность Г. А. Николаеву за помощь в ра боте.
СП И С О К Л И Т Е Р А Т У Р Ы
1.Поляков В. А., Николаев Г. А., Лощилов В. И., Петров В. И. Ультразвуковая сварка костей и резка живых биологических тканей. М., 1973. 136 с.
2.Набибеков М. К., Плющенков Б. Д., Саркисов И. 10. Исследование процесса
ультразвукового резания мягких биологических тканей. — Механика композитных мате
риалов, 1980, № 3, с. 519— 524.
3. Лощилов В. И., Веденков В. Г., Волков С. М., Трофимов А А. Ультразвуковые установки, применяемые для резки и сварки биологических тканей. В кн.: Ультра звук в хирургии. М., 1973, с. 40— 44.
Всесоюзный научно-исследовательский институт |
Поступило в редакцию 08.05.79 |
медицинского приборостроения, Москва |
|
Институт прикладной математики АН СССР, Москва |
|
Институт медико-биологических проблем Министерства здравоохранения СССР, Москва
МЕХАНИКА КОМПОЗИТНЫХ МАТЕРИАЛОВ, 1980, № 4, с. 708—712
УДК 620.179:678
Г. Мартинчек
О П Р Е Д Е Л Е Н И Е Д И Н А М И Ч Е С К И Х В Я З К О У П Р У Г И Х Х А Р А К Т Е Р И С Т И К М Е Т О Д О М М Е Х А Н И Ч Е С К О Г О И М П Е Д А Н С А
В основе метода механического импеданса лежит определение изме нения функции механического импеданса в точке возбуждения гармо нических колебаний. Изменение частотной зависимости этой функции выражается наличием резонансных и антирезонансных экстремумов, ко ординаты которых при данных краевых условиях зависят от вязкоупру гих характеристик материала тела, подвергнутого колебаниям. Измене ния функции механического импеданса в достаточно широком частот ном диапазоне дают возможность определять динамические параметры материала, в частности его комплексный модуль [1].
Механический импеданс в точке возбуждения гармонических колеба ний системы определяется как отношение силы к скорости движения в месте возбуждения. При проведении измерений целесообразно устано вить нормативный механический импеданс, который определяется [2] как отношение синусоидально изменяющейся силы F и ускорения а в точке возбуждения колеблющегося тела на единицу его массы m :
где Z*n — комплексная безразмерная функция.
Схема испытания по методу механического импеданса зависит от вида материала и от способа его нагружения. Так, например, при испы тании призматических или цилиндрических тел постоянного сечения це лесообразно применять вынужденные продольные и крутильные колеба ния, точка возбуждения которых расположена на одном конце тела, тогда как другой его конец свободен. Теоретический анализ такой схемы, разработка методики и применение в случае связных грунтов и термопластов, приведены в [3, 4]. В случае консольного элемента, вы годнее использовать гармонические изгибные колебания, вызываемые переменной силой, приложенной к свободному концу тела. Эта методика
вприменении к битумным материалам описана в работах [5, 6].
Вданной работе подробно рассматривается элемент со свободными концами длиной 21, изгибные колебания которого вызваны гармониче ской переменной силой Р, приложенной в середине пролета. В ходе экс периментов с применением метода механического импеданса определяли динамические вязкоупругие характеристики — комплексный модуль упругости
£*ш,т = о/е = £о),т (1 + £б),
где £со, г — вещественная часть комплексного модуля; б — параметр за тухания. Исходя из дифференциального уравнения изгибного ко л ебан ия
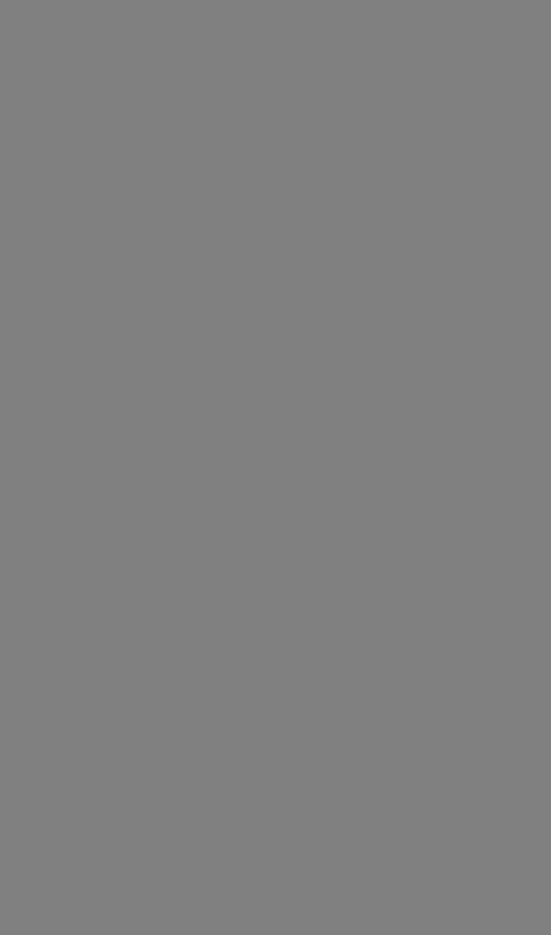
Вещественная часть комплексного модуля Е а>т определяется по из меренным значениям антирезонансных и резонансных частот и соответ ствующего частотного параметра nl согласно выражению
„4я2/2/4р
ш,г |
(n /)V 2 ’ |
где г — радиус инерции сечения образца вдоль оси, перпендикулярной к плоскости колебания; р — плотность; f — частота, Гц.
Методы механического импеданса требуют автоматизированного процесса измерения. Современная измерительная техника позволяет за писывать значения амплитуды силы при постоянной амплитуде ускоре ния колебаний в широком частотном диапазоне. Блок-схема эксперимен тального оборудования приведена на рис. 2. Синусоидальный сигнал от автоматического управляющего генератора подается на вибратор, коле бания которого передаются через преобразователь силы на образец. Да лее сигнал подается на вольтметр и фиксируется самописцем. Получен ная кривая представляет собой функцию, пропорциональную \Z*n\. Сигнал акселерометра, закрепленного на образце в точке возбуждения колебаний, поступает в систему сервовключения для обеспечения посто янной амплитуды ускорения колебаний во всем частотном диапазоне.
Вольтметры 3, 4, регистрирующий прибор 5, преобразователь силы импедансной головки 7 изготовлены фирмой «Брюэль-Кьер» (Дания); акселерометр 9, усилитель мощности 1 изготовлены предприятием «МЕТРА МЕСС-унд Фреквенцтехник» (Радебойл, ГДР), вибратор 6 и генератор 2 — предприятием «ВЕБ-Мессэлектроник» (Дрезден, ГДР).
Рассмотрим результаты измерений, проведенных методом механиче ского импеданса на термопластах. Измерения проводились при разных температурах материала — от —25 до 85° С. На рис. 3 в двойном лога рифмическом масштабе представлены изотермы значений комплексного модуля в зависимости от частоты для полиамида, представляющие собой в измеряемом частотном диапазоне (до 5000 Гц) прямые. Комп лексный модуль |£*| в зависимости от частоты можно выразить отно шением
Е* |= A {T )fBiT).
Рис. 2. Блок-схема экспериментального устройства: 1 — усилитель ЛВ102; 2 — авто матический генератор СГ201; 3, 4 — вольтметры 2409; 5 — регистрирующий прибор 2305; 6 — вибратор ЕСЕ211; 7 — преобразователь силы 8001; 8 — образец; 9 — ак селерометр КД91.
Рис. 3. Зависимости комплексного модуля от частоты при разных температурах для полиамида.
На рис. 4 представлены функции А (7), В(Т), вычисленные по ре зультатам измерений, полученных в эксперименте.
По изменению изотерм можно установить изохромы, т. е. линии зависимости комплексного модуля \Е*\ от температуры 7 для постоян ного значения частоты /, Гц. На рис. 5 изображены изохромы для поли амида при / = 100 и 5000 Гц. Здесь также показано изменение средних значений параметра затухания б в зависимости от температуры 7. Зави симость б от частоты в измеряемом диапазоне была невыраженной, его значения колебались в пределах от 6 = 0,037 при 7 = -2 5 ° С до 6 = 0,139 при 7=55^-85° С.
Комплексный модуль |£*| имеет значения 890 МПа при f = 100 Гц и Г=85°С и 4820 МПа при / = 5000 Гц и Т = —25° С. Отношение для изо термы 7 = 20° С равно |£*|20>с= 2850-/0-018.
Подобные изменения получены и для других термопластов. Для полнметилметакрилата значения б колеблются от 6 = 0,05 при 7 = — 25°С
до 6= 0,120 |
при 7 = 85°С, комплексного модуля — от |£*|=3100 МПа |
||
при /=Ю0 |
Гц и Т = 85°С до |
|£*|=7400 МПа |
при / = 5000 Гц и |
Г=-25°С . |
Отношение для |
изотермы Т = 20° С |
равно |£*|2о°с = |
=4625 * /°.°45.
Как показали измерения образцов из поливинилхлорида, параметр
затухания сохраняет низкие |
значения |
(6 = 0,05-4-0,07) вплоть до темпе |
ратуры 7 = 45° С, затем величина его |
быстро нарастает и при 7 = 85° С |
|
5=0,65-4-0,80. Комплексный |
модуль |
|£*| имеет значения от 300 до |
4400 МПа. При 7 = 20°С |£*|20°с = 3350-/0'0175.
Применение температурно-временной аналогии [7] основано на гипо тезе термореологически-линейного материала, т. е. материала, при изме нении температуры которого изменяется только положение функции вязкоупругих свойств на шкале времени или частот, но не общая форма ее.
Полученные изотермы указывают на то, что вязкоупругая реакция испытываемых материалов термореологически линейна только в грубом приближении. Однако с точки зрения практических нужд, целесооб разно принять эту гипотезу и применить принцип суперпозиции времени нтемпературы, причем это, по нашему мнению, имеет смысл только в отношении комплексного модуля.
Рис. 4. Зависимости функций А(Т) и В(Т) |
от температуры. |
5. Зависимости комплексного модуля и параметра |
затухании 6 от температуры |
при разных частотах. |
|
Рис. 6. Обобщенная изотерма для полиамида.
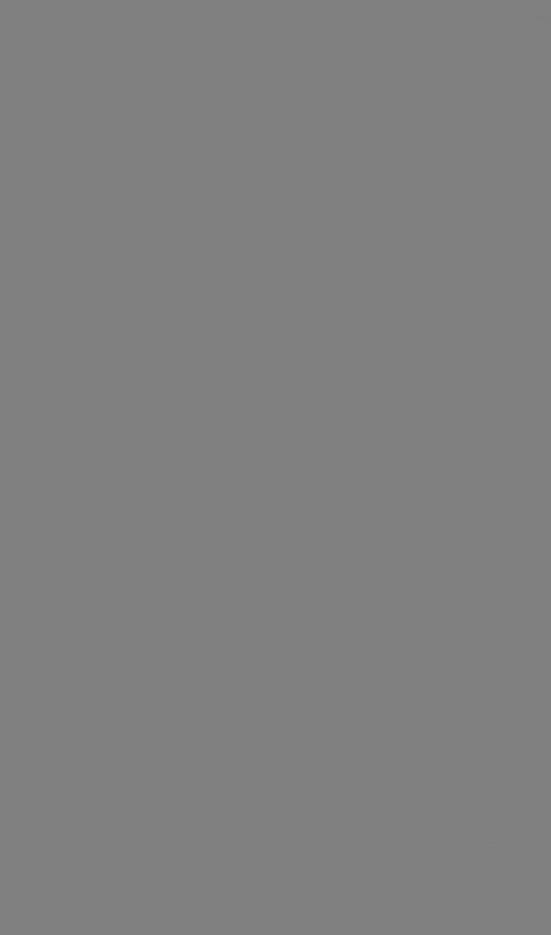
МЕХАНИКА КОМПОЗИТНЫХ МАТЕРИАЛОВ, 1980, № 4, с. 713—721
УДК 539.3:678.01
А.А. Аскадский, Т. В. Тодадзе
КВОПРОСУ О ПРОГНОЗИРОВАНИИ РЕЛАКСАЦИОННЫХ СВОЙСТВ ПОЛИМЕРОВ
Для прогнозирования релаксационных свойств полимеров обычно применяют принцип температурно-временной аналогии. Если прогноз требуется осуществить в широком интервале температур и деформаций, необходимо провести большое количество экспериментов по определе нию кривых релаксации напряжения и ползучести. Для полной оценки релаксационного поведения полимерного материала сначала проводят эксперименты по релаксации напряжения (ползучести) во всем возмож ном интервале деформаций (или напряжений) при одной выбранной температуре, затем ту же процедуру проделывают при другой темпе ратуре и т. д. В случае твердых полимерных материалов возможный интервал деформаций (или напряжений) определяется способностью материала при данной температуре не размягчаться и не разрушаться при действии механической нагрузки. Возможный интервал температур сверху ограничен температурой стеклования. Естественно, что такой эксперимент требует большой затраты времени, и он может быть осу ществлен только для некоторых представителей полимеров [1—3].
Для ускорения возможности прогнозирования релаксационного по ведения полимерных материалов можно использовать сканирующие ме тоды измерения, с помощью которых, как будет показано ниже, пара метры релаксационных характеристик могут быть определены с доста точной точностью.
Если сканирование осуществляется по температуре, то в условиях ползучести при постоянном напряжении (a = const) определяется серия термомеханических кривых (зависимостей деформации е от темпера туры Т), каждая из которых соответствует определенной величине о. В общем случае вид термомеханических кривых бывает двояким. Если твердый полимер при нагревании переходит из стеклообразного состоя ния непосредственно в вязкотекучее, термомеханические кривые имеют вид, схематически изображенный на рис. 1—а. Если же сначала осу ществляется переход из стеклообразного состояния в высокоэластичес кое, характер термомеханических кривых таков, как это схематически
показано на рис. 1—б.
В первом случае для описания термомеханических кривых (в обла сти главного перехода) можно воспользоваться обобщенным уравне нием Максвелла. При переходе от одной температуры испытания к дру
гой это уравнение согласно [4] |
принимает вид: |
|
do |
р dz |
о |
dt |
dt |
( 1) |
тойт |
где t — время; Е — модуль упругости; то — время релаксации при температуре приведения, равной То; Яг — фактор сдвига. В условиях термомеханических испытаний при а = const dofdt = 0 и тогда
de о
(2)
dt Хойт
Рис. 1. Схематическое изображение термомеханических кривых, характеризующих пе реход из твердого состояния в вязкотекучее (а) и в высокоэластическое (б). Каж дая кривая определена при постоянном напряжении ст.
Рис. 2. Кривые нензотермической релаксации напряжения в условиях одноосного сжатия. Сплошная кривая проведена по точкам максимумов (пояснения в тексте).
Проведенные нами опыты показали, что в случае ползучести ряда твердых стеклообразных полимеров в широком интервале напряжений и температур зависимость а т от Т — Т0 хорошо описывается соотно шением
1g a T = B ( T - T 0)”\ |
(3) |
Учитывая, что термомеханические испытания наиболее часто прово дятся при линейном росте температуры со временем T = T 0 + $t, где (3 — скорость роста температуры, Г0 — начальная температура опыта (она же может быть выбрана за температуру приведения), из (2) и (3) имеем:
t
Es(t) =-^— J е-2,зB m mdt. |
(4) |
То о |
|
После интегрирования (4) и перехода от времени t к температуре Т получаем уравнение термомеханической кривой, описывающее переход из твердого (стеклообразного) состояния в вязкотекучее.
Если требуется описать переход из твердого (стеклообразного) со стояния в высокоэластическое, можно воспользоваться обобщенным уравнением Кельвина—Фойгта—Мейера:
a = £ ,i8+ £ ,i0 o a r -^ -, |
(5) |
где Е\ — модуль высокоэластичности; 0О — время запаздывания при температуре приведения; ат — фактор сдвига. При условии, что темпе ратурная зависимость ат описывается выражением (3), на основе (5) можно записать:
|
de |
|
e |
|
1 |
|
|
|
|
|
--------i------- |
|
|
|
dt |
|
|
)Qo e 2,3D {T-T0) |
|
|
или |
|
|
|
|
t |
|
|
|
|
( % |
|
||
|
|
|
0 |
|
||
e |
|
— exp |
|
1 |
J e-2,3B(POm^ ^J |
(6) |