
Физико-химические основы литейных процессов
..pdf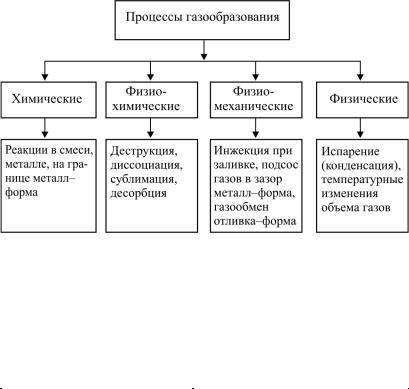
Рис. 13. Классификация процессов газообразования в литейной форме
Таблица 1 2
Ориентировочная количественная оценка различных процессов газообразования в литейной форме (% от общего объема газов)
Процесс |
|
Вид форм |
|
|
Сырые |
Сухие |
Оболочковые |
||
|
||||
Испарение влаги: |
|
|
|
|
свободной |
50–60 |
8–12 |
3–5 |
|
входящей в состав минералов |
0,5–8 |
15–25 |
0,5–2 |
|
Горение |
2–3 |
5–8 |
2–10 |
|
Сублимация |
30–40 |
45–65 |
80–90 |
|
Разложение материалов-примесей |
1–5 |
1–5 |
1–2 |
|
Диссоциация газов |
6–10 |
8–12 |
10–15 |
|
Расширение воздуха |
До 0,5 |
До 1 |
До 0,5 |
81
8.3. Механизм образования объемных газовых раковин
По своему виду и механизму образования объемные газовые раковины отличаются от поверхностных газовых раковин. Механизм образования объемных газовых раковин может считаться состоящим из пяти этапов:
1)образование газов в форме;
2)перемещение газов к поверхности формы;
3)переход газов в жидкий металл;
4)перемещение газов в жидком металле;
5)выделение газов из жидкого металла.
При рассмотрении этого механизма следует иметь в виду, что газовые раковины в отливках могут образоваться как за счет формы, так и за счет металла. Однако строго отделить раковины, получающиеся за счет металла, от раковин, получающихся за счет формы, не представляется во многих случаях возможным.
Расчет газового режима литейной формы показал, что в форме создаются условия, вызывающие перемещение газов от поверхности формы к ее периферии. Следует иметь в виду, что проникновение газов из формы в отливку наиболее опасно в начальный момент времени заливки формы жидким металлом, когда слой жидкого металла очень незначителен и может быть равным нулю; опасность образования газовых раковин уменьшается при увеличении газопроницаемости и уменьшении газотворности.
8.4. Поверхностные газовые раковины
Объемные газовые раковины выделяются из формы, проникают в тело отливки и застревают в ее затвердевшем поверхностном слое при своем выделении из тела отливки. Поверхностные газовые раковины также выделяются из формы, но не проникают в тело отливки, а застревают в ее затвердевшем поверхностном слое. Таким образом, объемные газовые раковины
82
застревают в теле отливки при выделении из него, а поверхностные газовые раковины застревают в нем при своем образовании. Из этого определения вытекает и ряд следствий:
1.Поверхностные газовые раковины могут появиться только после образования затвердевшего поверхностного слоя металла отливки.
2.По времени поверхностные газовые раковины образуются позднее, чем объемные.
3.Поверхностные газовые раковины могут образоваться только в металле с повышенной разностью температур начала и конца затвердевания. Только в этом случае можно ожидать появления на поверхности отливки слоя повышенной вязкости при наличии очень тонкой затвердевшей корки, которая пробивается газовым пузырьком.
4.Возможность пробивания этой корочки газовым пузырьком создается только за счет его большой пробивной способности. Такая способность создается за счет развития процессов, близких к «микровзрывным». Этот процесс возможен только при наличии процессов внезапного газообразования.
5.Внезапное образование газа наиболее вероятно в том случае, если процесс происходит при вполне определенной температуре. Если выделение газов происходит в интервале температур, то процесс протекает менее бурно и возможность пробивания затвердевшей корки резко снижается. Поэтому появление поверхностных газовых раковин часто не удается связать с увеличением содержания воды в смесях. Это может сказаться главным образом на объемных газовых раковинах.
6.К числу процессов выделения газов, протекающих при вполне определенной температуре, можно отнести процессы выделения конституционной воды из глинистых минералов.
7.Наличие конституционной воды характерно для водных минералов, в том числе для глинистых. Поэтому появление поверхностных газовых раковин часто удается связать с увеличением содержания глины в смесях. Кроме того, на практике от-
83
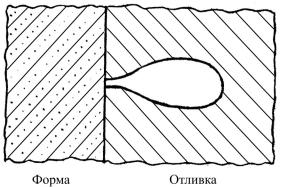
мечалось, что наличие глины некоторых месторождений связано с увеличением опасности появления поверхностных газовых раковин.
8.Поверхностные газовые раковины могут различаться по своему составу. Можно предполагать возможность растворения газов в металле в тех случаях, когда металл газами не насыщен. Этим можно объяснить связь между увеличением опасности образования поверхностных газовых раковин и обработкой жидкого металла разнымидобавками, снижающимисодержаниегазавметалле.
9.Опасность образования поверхностных газовых раковин увеличивается при повышении температуры заливки, опасность образования объемных газовых раковин уменьшается при повышении температуры. Поэтому существенно важно различать обе разновидности. Характерным для поверхностных раковин является вид в направлении, перпендикулярном к поверхности отливки: поверхностные газовые раковины имеют вид взрывной камеры (рис. 14).
Рис. 14. Схема образования поверхностных газовых раковин (ситовидной пористости)
Такой вид связан с процессом их образования: газы пробивают тонкий слой затвердевшей корки и, попав в менее плотную среду, расширяются. С поверхности они часто полностью закры-
84
ваются, например при очистке поверхности дробью. Но они могут вскрыться после удаления очень тонкого поверхностного слоя, например, даже после тепловой обработки.
Из представленного разбора процесса образования поверхностных газовых раковин могут быть сделаны важнейшие рекомендации по уменьшению их образования:
1.Уменьшение содержания глины в смеси. При этом не все глины ведут себя одинаково.
2.Заливка при более низкой температуре. Но при этом увеличивается опасность образования объемных газовых раковин.
3.Применение металла, содержащего меньшее количество газов.
85
9.ПРИЛОЖЕНИЕ ЗАКОНОВ ФИЗИЧЕСКОЙ ХИМИИ
КНЕКОТОРЫМ ЛИТЕЙНЫМ ПРОЦЕССАМ.
СВЯЗЬ ДИСЦИПЛИНЫ С ИСТОРИЕЙ РАЗВИТИЯ МЕТАЛЛУРГИИ И ЛИТЕЙНОГО ПРОИЗВОДСТВА
9.1. Выплавка металла
Археологические материалы свидетельствуют, что для изготовления орудий и оружия человек прежде всего стал употреблять медь, хотя золото он, очевидно, знал еще раньше [10, с.36]. Первые медные орудия (кирка, кинжал и небольшой топор), похожие на каменные, относятся еще к энеолиту, т.е. переходному периоду от каменного века к бронзовому (от IV до III тыс. до н.э.).
Обработка самородной меди привела первобытных людей к важным наблюдениям. Во-первых, в результате ударов каменного молота медь становилась более твердой и поэтому пригодной для производства орудий. Тем самым были выработаны приемы холодной обработки металла. Во-вторых, занимаясь обработкой меди, человек открыл возможность плавки металла. Кусок самородной меди или найденной руды, содержащей металл, попавший в огонь костра или в очажную яму, позволил человеку обнаружить новые и несвойственные камню особенности: от сильного нагревания происходило неполное восстановление металла, который расплавлялся и, остывая, приобретал новый вид. При использовании более высокой температуры качество выплавляемого металла улучшалось. Занимаясь обработкой самородной меди, человек открыл возможность плавления металла. К этому времени уже была известна гончарная печь, температура пламени в которой значительно выше, чем в кост-
86
ре. Используя такую печь, люди смогли начать систематическую выплавку меди. При плавке меди нельзя было не заметить черные, коричневые и красновато-коричневые куски важнейшей оловянной руды – кассиарита, или оловянного камня (SnO2). Это, а также наблюдения над свойствами медных руд, содержащих незначительные (до 2 %) примеси олова, привели к важному открытию: прибавление к меди олова придает металлу лучшие качества. Так был изобретен первый искусственный сплав – бронза. Бронза обладает значительными преимуществами перед медью. Она имеет более низкую температуру плавления, примерно 700–900 ºС, более высокие литейные качества, а при охлаждении обладает значительной прочностью и твердостью. Если медное орудие в основном ковалось, то бронзовое отливалось, что имело большое значение, так как это открыло возможность массового производства орудий и оружия.
Крупнейшим достижением человечества, вызвавшим бурный рост производительных сил, явилось получение и применение железа. В отличие от меди и олова железо в древности добывалось повсюду из озерных, болотистых, луговых и других руд, которые в настоящее время уже не имеют большого практического значения. Одним из величайших изобретений человечества был сыродутный процесс получения железа. При этом процессе восстановление железа из руды достигается при температуре 900 ºС. Для получения железа сыродутным способом руда дробилась и затем обжигалась на открытом огне; после этого в ямах или небольших глиняных печах производилось восстановление металла. Для восстановления металла в горн добавлялся древесный уголь и нагнетался воздух. В результате процесса на дне глиняной печи образовывалась так называемая крица – комок пористого тестообразного и сильно загрязненного железа весом от 1 до 8 кг. Ее необходимо было затем подвергать многократной горячей проковке, после чего из нее изготовляли различные орудия труда и оружие. Кричное железо, которое получалось в результате сыродутного процесса, отличалось
87
мягкостью. Однако еще в древности был открыт способ получения более твердого металла. Для этого применяли сваривание, а также закалку железных изделий или их цементацию. Способ получения сварного железа, а также методы поверхностной закалки, по-видимому, были впервые применены в 1400 г. до н.э.
вАрмении, в небольшом местечке Шохдох-Карадаг, расположенном к северо-востоку от горы Арарат. Стремление иметь прочные орудия труда и оружие привело к открытию производства стали. Уже в античном мире, начиная с первой половины I тыс. до н.э., сталь широко употреблялась для изготовления изделий.
Хотя сыродутный процесс давал мягкое железо высокого качества, но крайне низкая степень извлечения железа из руды (не больше 50 %) и очень незначительная производительность не удовлетворяли увеличивающегося спроса на металл. Стремление устранить эти недостатки привело к увеличению высоты самого горна, в результате чего сыродутный горн превратился
вдомницу, и к усилению дутья путем применения водяного колеса для приведения в действие воздуходувных мехов. Эти два технических усовершенствования изменили и самый процесс, который происходил в горне. Температура в верхней части горна понизилась до 750–900 ºС, и поэтому железная руда восстанавливалась раньше, чем образовывался шлак. Благодаря этому уменьшились потери железа в шлаке, а само железо сильнее науглероживалось. В результате в нижней части печи, где температура под влиянием дутья повышалась до 1350 ºС, вместо твердого железа получался жидкий чугун. Сперва чугун получался случайно вследствие отклонения сыродутного процесса от нормального хода. Он был хрупок, не поддавался ковке и поэтому рассматривался как брак, вызванный расстроенным ходом сыродутного процесса. Однако с течением времени его начали применять для производства отливок, а несколько позже негодный для литья чугун пускали вместе с рудой во вторичную переплавку. При этом обнаруживалось, что передел чу-
88
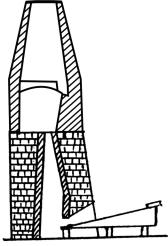
гуна в мягкое (сварное) железо во второй плавке требует меньшего расхода топлива и руды, а железо получается лучшего качества. Поэтому впоследствии сыродутный процесс стал постепенно вытесняться двухступенчатым способом получения стали: сначала получали чугун, потом при вторичной переплавке в горне – сталь. Первая стадия называется доменным процессом, а печь, где производится этот чугун, – доменной печью. Вторая стадия получила название кричного передела.
Первые доменные печи, появление которых в Западной Европе относится к середине XIV в., по своим размерам мало отличались от домниц, но постепенно конструкция их совершенствуется. Доменная печь XV–XVI вв. (рис. 15) имела примерно следующие размеры: высота ее доходила до 4,5 м, а внутренний диаметр был равен примерно 1,8 м. Меха приводились в движение уже водяным колесом. В такой доменной печи производили 1,6 т чугуна в сутки, например в России с 1637 года недалеко от Тулы.
Рис. 15. Схема доменной печи XV–XVI вв.
89
Вмануфактурный период литейное производство становится на новую ступень. Изменения в методах литейного дела были связаны с широким применением огнестрельного оружия, литьем колоколов и художественных изделий. Наряду с ранее уже применявшейся для литья бронзой начали использовать
ичугун, получаемый в больших количествах. Вековой опыт литейщиков многих стран позволил уже в этот период освоить производство отливок по разъемным формам, а также тонкостенных и пустотелых отливок.
9.2.Развитие техники металлургии
Всвязи с катастрофическим истреблением леса уже в середине XVII века были начаты поиски заменителей древесного угля. Однако попытки использовать каменный уголь для получения чугуна были заранее обречены на неудачу, так как в то время не были изучены условия и температурные режимы коксования, а также были неизвестны марки коксующихся углей. Только
в1735 г. английский инженер-металлург, владелец железоделательного завода Кольбрундель Авраам Дерби-сын (1711–1763), опираясь на опыт своих предшественников, разрешил проблему применения минерального топлива в доменном производстве, использовав для доменной плавки не просто каменный уголь, а специально переработанный кокс. Использование кокса потребовало увеличения количества воздуха, подаваемого в доменную печь. В дальнейшем техника подачи воздуха в домну продолжала совершенствоваться, росла мощность двигателей, приводивших в движение воздуходувные устройства. Благодаря применению новых систем воздуходувок, приводимых в действие паровыми машинами, появилась возможность значительно увеличить размеры доменных печей и ускорить процесс доменной плавки, что, в свою очередь, привело к резкому повышению выплавки чугуна. Дальнейший рост производительности домен-
90