
Физико-химические основы литейных процессов
..pdf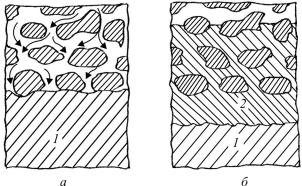
Рис. 6. Проникновение твердых окислов в поры формовочной смеси до начала окисления металла (а) и после его окончания (б):
1 – металл; 2 – окислы
4.2. Влияние состава сплава и температурного режима формы
Основное влияние на процесс образования окисной пленки оказывает обезуглероживание поверхности отливки, которое связано с начальным содержанием углерода в расплаве, температурой и продолжительностью выдержки при данной температуре. Только после достижения на поверхности отливки некоторого предельного (критического) содержания углерода структура окисной пленки обеспечивает легкое отделение пригара от отливки. В зависимости от температуры и продолжительности выдержки общее содержание углерода существенно снижается. Достаточно быстрое выгорание углерода происходит не только из жидкого, но и из твердого чугуна (при 1100 ºС), что свидетельствует о большой скорости диффузии углерода при температуре, близкой к температуре плавления. Легкоотделимый пригар был получен лишь после выдержки при 1500 ºС в течение 10 мин, то есть после того, как общее содержание углерода в металлическом образце снизилось примерно до 2 %. Очевид-
41
но, что такое содержание углерода может быть получено при любой более низкой температуре, но при соответствующем увеличении выдержки.
Сравнение химического состава лекгоотделимого пригара, полученного на отливках из стали 30Л, и трудноотделимого, полученного на чугунных отливках, показывает существенное различие, в первую очередь, в содержании закиси железа (табл. 8).
Таблица 8
Состав пригарных корок на чугунных и стальных отливках
Сплав |
Температура |
Толщина |
Характер |
Содержаниеокислов, % |
||
стенки |
|
|
|
|||
заливки, ºС |
пригара |
FeO |
Fe2O3 |
MnO |
||
|
|
отливки, ºС |
|
|
|
|
ЧугунС420 |
1350 |
10 |
Трудно- |
1,83 |
1,21 |
0,03 |
|
|
40 |
отделимый |
2,2 |
2,01 |
0,03 |
|
|
70 |
|
3,04 |
1,26 |
0,05 |
|
|
100 |
|
3,26 |
1,43 |
0,04 |
|
1550 |
10 |
|
2,4 |
1,55 |
0,02 |
|
|
40 |
|
3,91 |
1,31 |
0,04 |
|
|
70 |
|
3,62 |
1,93 |
0,02 |
|
|
100 |
|
4,08 |
1,75 |
0,06 |
Сталь30Л |
1550 |
10 |
Легко- |
11,7 |
3,03 |
0,35 |
|
|
40 |
отделимый |
12,09 |
2,39 |
0,34 |
|
|
70 |
|
12,52 |
2,33 |
0,44 |
Как видно из приведенных данных, при контакте чугуна со смесью в образовавшемся пригаре содержание закиси железа в 3–4 раза меньше, чем при контакте со сталью, на порядок ниже и содержание MnO. При заливке формы чугуном толщина стенок отливки и температура заливки оказывают незначительное влияние на содержание окислов железа в пригаре. Экспериментально подтверждено, что толщина химического пригара в реальных условиях практически не зависит от температуры заливки.
42
4.3. Влияние состава формовочных смесей
Возможность формирования легкоотделимого пригара за счет изменения состава сплава и температуры заливки весьма ограничена, так как последние определяются требованиями к эксплуатационным свойствам готовой детали и литейной технологии. Управлять процессами образования химического пригара можно, лишь изменяя состав формовочных смесей. Необходимо также учитывать, что первоначально формовочные материалы выбирают, исходя из условий предотвращения образования металлизированного пригара. Влияние литейной формы и ее материалов проявляется в той степени, в какой они способствуют образованию и сохранению окисной пленки требуемой структуры на границе раздела металл – форма.
В литейной форме продукты окисления отливки или взаимодействия окислов металла с формовочными материалами не остаются в зоне реакции, а под действием капиллярных сил проникают в толщу формы, определяя тем самым толщину химического пригара. Установлено, что химический пригар, появившийся в процессе взаимодействия углеродистой стали со смесями на основе различных наполнителей, состоит из зерен песка, сцементированного железистым стеклом; каких-либо соединений, кроме файялита, в заметном количестве в нем не обнаружено, хотя термодинамически образование их возможно, например герцинита (FeAl2O4). Во всех случаях слой пригара отделен от металла окалиной, прочность которой и определяет силы связи пригара с отливкой.
Глубина проникновения окислов, образующихся на поверхности стали 110Г13Л, характеризуется следующими данными (рис. 7).
43
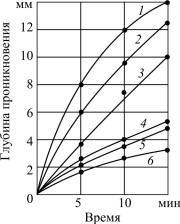
Рис. 7. Влияние продолжительности выдержки стали 110Г13Л при 1400 ºС на глубину проникновения окислов в формовочные смеси на основе: 1 – кварца; 2 – циркона; 3 – хромомагнезита; 4 – силлиманита; 5 – корунда; 6 – оливинита
Видно, что наибольшая глубина проникновения наблюдается при использовании смеси на основе кварцевого песка, наименьшая – на основе оливинита, корунда и дистенсиллиманита.
4.4. Термический пригар
Рассмотрим отношение к нагреву наиболее распространенных формовочных смесей с точки зрения вероятности образования термического пригара. В песчано-глинистых смесях содержатся, как правило, достаточно тугоплавкие компоненты; взаимодействие между ними (без участия окислов железа) происходит медленно и не приводит к образованию заметного количества жидкой фазы, способной цементировать зерна песка. Еще менее вероятно возникновение термического пригара при использовании песчано-смоляных смесей, так как для последних применяют безглинистые пески, а образовавшийся при нагреве
44
слой углеродистого вещества (кокса) на поверхности зерен песка препятствует их спеканию.
Иначе обстоит дело при использовании жидкостекольных смесей. В высушенных смесях зерна песка связаны силикатом натрия, имеющим температуру плавления ≈ 800 ºС. Следовательно, при заливке металла в слое формы, прогретом до 800 ºС, будет происходить расплавление обволакивающих зерна песка пленок силиката натрия и последующее растворение двуокиси кремния песка в расплаве. Если адгезия расплава силикатов к металлу или покрывающим его окислам будет большой, возможно образование достаточно толстого слоя термического пригара, отделяемость которого будет зависеть от свойств и структуры окисных пленок.
4.5. Методы предотвращения химического пригара
В железоуглеродистых сплавах переход от трудноотделимого пригара к легкоотделимому происходит скачкообразно при уменьшении концентрации углерода до 2–2,5 %. На чугунных отливках при использовании обычных смесей на основе кварцевого песка невозможно получить легкоотделимый пригар. Для обеспечения необходимой чистоты поверхности тонкостенного литья из чугуна в смесь можно добавлять углеродосодержащие материалы, предотвращающие окисление железа. Для получения толстостенной чугунной отливки без пригара обязательным условием является изоляция окислов от материала формы. Наилучшим с этой точки зрения противопригарным материалом является графит, плохо смачиваемый и железом, и окислами железа.
Формы для получения отливок из углеродистых, а тем более легированных сталей окрашивать углеродосодержащими покрытиями не рекомендуется из-за опасности науглероживания отливок. При выборе противопригарных материалов для
45
отливок из углеродистых и легированных сталей необходимо учитывать как характер образующихся окислов в результате взаимодействия формы с металлом, так и скорость отвода их из зоны контакта металла с формой. Оптимальным будет случай максимального образования вюстита (образующийся между стальной отливкой и химическим пригаром окисный слой) на поверхности отливки при минимальном проникновении образовавшихся окислов в поры формы. Наилучшим противопригарным материалом для красок при производстве литья из углеродистой стали является корунд. Действительно, в контакте с корундом углеродистая сталь окисляется достаточно полно при значительном содержании FeO в продуктах окисления. В то же время скорость отвода продуктов окисления от поверхности металла в случае использования корундовой смеси минимальна.
46
5. МЕХАНИЗМЫ ОБРАЗОВАНИЯ ПРИГАРА
5.1. Пригар как комплексное явление
Чаще всего на отливке одновременно образуется пригар двух или трех видов. Проникший в поры литейной формы металл, окисляясь, вступает в химическое взаимодействие с компонентами формовочной смеси, которые, в свою очередь, под воздействием теплоты взаимодействуют друг с другом и образуют легкоплавкие соединения. В результате на отливке появляется так называемый комплексный пригар. Нужно отметить, что определяющим является первый этап процесса (образование металлизированного пригара), а его второй этап можно рассматривать как неизбежное явление, сопутствующее охлаждению отливки. В то же время возможно образование химического пригара и без предварительного проникновения металла. В зарубежной литературе обычно рассматривается лишь межзеренное проникновение, то есть металлизированный пригар, и собственно «пригар», под которым понимают химический пригар, а термический не учитывается как имеющий малое практическое значение.
Большинство исследователей рассматривают металлизированный пригар как результат проникновения залитого металла в поры формовочной смеси под действием давления, превышающего капиллярное противодавление. В большинстве случаев это давление создается за счет статического давления жидкого металла, однако иногда возможно возникновение повышенного локального давления, что объясняет появление металлизированного пригара на отливках небольшой высоты. Высокая газотворная способность или низкая газопроницаемость смеси может привести к взрывам при заливке формы металлом и к образованию поверхностных дефектов (ужимин, металлизированного пригара).
47
Возможность образования пригара на низких отливках связывается со взрывным характером испарения влаги при заливке формы металлом и с возникновением при этом динамического удара жидкого металла.
Величина критического давления или давления проникновения Рк зависит от свойств расплава и формы. Смачиваемость формовочных материалов зависит от природы последних, состава литейного сплава и газовой среды, в которой происходит контакт жидкого металла с формой. Например, краевой угол смачивания чугуном в зависимости от состава смеси равен 108–144 ºС. Поверхностное натяжение чугуна колеблется также в широких пределах. Еще в большей мере изменяются поверхностные свойства стали, которая в отличие от чугуна склонна к насыщению кислородом. По данным С.И. Попеля и Б.В. Царевского, при увеличении концентрации кислорода в железе от 0,004 до 0,07 % σ уменьшается от 1710 до 1235 мН/м, а краевой угол смачивания корунда – от 141 до 90 º.
Приведенные данные свидетельствуют, что пористость обычно используемых формовочных и стержневых смесей и величина пор в них недостаточно малы, чтобы обеспечить высокое Рк, поэтому в практике литейного производства часто улучшают капиллярные свойства формы. Например, для улучшения качества поверхности литья широко применяют мелкие пески
идобавки к смесям тонкодисперсных материалов, главным образом маршалита (пылевидный кварц). Оптимальное содержание маршалита в смеси на основе кварцевого песка 30–50 %, именно при таком его содержании наблюдается минимальный металлизированный пригар и смесь сохраняет достаточную газопроницаемость. Однако для крупных отливок рекомендуется применять крупный песок, так как использование мелких песков
ипылевидных добавок, хотя и уменьшает опасность образования пригара, но может привести к другим дефектам, связанным с пониженной огнеупорностью смеси.
48
Для улучшения капиллярных свойств смесей также можно увеличивать плотность набивки, например, повышая давление прессования, пропитывая поверхность формы растворами сульфитной барды, этилсиликата, жидкого стекла, формовочными красками с малой плотностью и др. При производстве крупного литья эти методы либо неприемлемы, либо малоэффективны, поэтому для предотвращения образования металлизированного пригара чаще всего используют противопригарное покрытие – облицовочные смеси, пасты и краски, обеспечивающие Нк, заведомо большую, чем высота отливки. Однако и в этом случае образования металлизированного пригара наблюдается достаточно часто.
Выше рассматривался процесс проникновения металла в поры смеси по всей плоскости контакта отливки с формой. В практике литейного производства известны случаи образования местного пригара, образование металлизированного пригара на отливках, высота которых менее критической, а также образования легкоотделимого от отливки металлизированного пригара. Эти явления могут происходить в результате разрушения плотного поверхностного слоя формы потоком жидкого металла (эрозия формы), образования трещин в форме и т.п. В зарубежной литературе четко различают межзеренное проникновение (по всей плоскости контакта металла с формой) и просечку (проникновение через трещины в поверхностном слое). В первом случае образуется сплошной металлокерамический слой пригара, во втором – металлические гребешки. Просечки яв-
ляются частым случаем металлизированного пригара, когда через образовавшиеся дефекты поверхности формы жидкий металл проникает в глубь формы и распространяется параллельно поверхности формы. При прогреве литейной формы выше температуры затвердевания сплава в результате распространения расплава вдоль поверхности формы гребешки могут превратиться в слой сплошного металлизированного пригара, связанного с отливкой отдельными перемычками. Образование просечек, ме-
49
стного пригара, пригара на низких отливках связано с реакцией формовочных смесей и покрытий на быстрый нагрев формы во времязаливки.
Эрозия формы зависит от влажности и пористости смеси, зернистости песка, прочности поверхностного слоя формы, массы отливки, температуры заливки и т.д. Лучшим способом уменьшения эрозии формы многие исследователи считают применение поверхностных покрытий, однако и сами покрытия в процессе заливки формы подвергаются эрозионному воздействию металла. Свойства слоя краски при комнатной температуре существенно отличаются от ее свойств при высоких температурах. Закономерной связи между эрозией под воздействием жидкого металла и осыпаемостью при комнатной температуре не обнаружено.
Эрозионная стойкость противопригарных красок определяется прежде всего свойствами связующих материалов, основные требования к которым сводятся к необходимости обеспечения достаточной прочности и хорошего сцепления покрытия с поверхностью формы. Известно, что деструкция декстрина,
сульфитно-спиртовой барды, |
патоки начинается при 200 ºС, |
а при 400 ºС потери массы |
связующего достигают 70–80 %. |
Следовательно, нужно ожидать, что противопригарные покрытия с такими связующими будут обладать низкой эрозионной стойкостью, не обеспечат предотвращения пригара и могут явиться причиной образования засоров в отливках. С точки зрения эрозионной стойкости более надежны противопригарные покрытия с неорганическими связующими. Хорошей прочностью обладают краски, в которых связующим является жидкое стекло, однако они весьма склонны к образованию крупных трещин и отслаиванию от поверхности формы. Иногда применяют краски на основе алюмофосфатных и алюмохромфосфатных связующих. Они обладают лучшими противопригарными свойствами, чем краски с бентонитом и ССБ.
50