
Физико-химические основы литейных процессов
..pdf
за счет теплоты, подводимой из центральной части отливки. В последнем случае поверхность формы прогреется до температуры поверхностных слоев отливки и может начаться проникновение металла в поры формы, поэтому понятно стремление литейщиков определить и обеспечить условия сохранения образовавшейся в начальный момент твердой корки. Основным критерием, характеризующим температурные условия на поверхности контакта металл–форма, является температура поверхности tп. Температура на поверхности формы определяется многими факторами: теплофизическими свойствами формовочных смесей и металла, толщиной отливки, температурой заливки и другими. И.Б. Куманин установил, что глубина проникновения расплава в поры формы обратно пропорциональна коэффициенту теплоаккумулирующей способности смеси bф, и предложил использовать формовочные смеси, обладающие высокой теплоаккумулирующей способностью, для предотвращения образования металлизированного пригара. В частности, лучшие противопригарные свойства смесей на основе хромитовых и хромомагнезитовых песков связывают с большей их теплоаккумулирующей способностью по сравнению со смесями на основе кварцевого песка. Увеличение bф смесей значительно сокращает продолжительность контакта жидкого металла с формой (табл. 10).
Таблица 1 0
Влияние bФ на продолжительность контакта жидкого металла с формой
Песок |
bф, |
Продолжительность контатта |
||||
(с) при толщине отливки (мм) |
||||||
(основа смеси) |
Вт с1/ 2 м2 °С |
|||||
50 |
150 |
300 |
600 |
|||
|
|
|||||
Кварцевый |
1260 |
43 |
141 |
442 |
– |
|
Дистен-силлиманитовый |
1470 |
34 |
115 |
306 |
972 |
|
Цирконовый |
1820 |
26 |
83 |
199 |
594 |
|
Рутиловый (TiO2) |
1960 |
23 |
68 |
159 |
472 |
|
Хромомагнезитовый |
2100 |
19 |
58 |
142 |
391 |
|
Хромитовый |
2240 |
9 |
25 |
57 |
135 |
71
Литейная форма в тепловом отношении представляет собой анизотропное тепло, тепловые свойства которого заметно изменяются в направлении потока теплоты. Каждый элементарный слой в сечении формы имеет свою определенную температуру, которой соответствуют вполне определенные истинные значения теплофизических констант. При экспериментальном определении любого теплофизического параметра удается лишь найти некоторое среднее эффективное значение коэффициента, зависящее не только от неравномерности распределения температуры, но и от прочих процессов, протекающих в форме (испарения влаги, горения связующих и т.п.). Теплофизические коэффициенты нельзя рассматривать как постоянные характеристики данной формовочной смеси. Значения коэффициентов зависят от типа расплава и его температуры, толщины отливки, начальной температуры формы и других. Кроме того, тепловые свойства формовочной смеси на одной основе (кварцевом песке, хромомагнезите и т.д.) будут изменяться при изменении влажности, размеров зерен песка, природы связующего и других параметров. Влияние плотности набивки и размеров зерен песка на теплопроводность смесей очень велико и сопоставимо с максимально возможным изменением за счет природы песка.
Таким образом, влияние теплофизических свойств на образование металлизированного пригара очевидно, однако рассматриватьегонеобходимо сучетом влияниядругихсвойств формы.
7.4. Термостойкость синтетических смол
Само понятие термостойкости смесей возникло в связи
споявлением связующих – синтетических смол, которые подвергаются при нагреве деструкции со значительной потерей массы. О термостойкости смесей можно судить прежде всего
спомощью методов термического анализа самой затвердевающей связующей композиции – полимера. Весь процесс деструк-
72
ции проходит в интервале температур 20–1500 ºС. Он разделяется на три стадии. Первая стадия примерно соответствует интервалу температур 20–200 ºС, причем ее верхняя граница может изменяться на 60–70 ºС в зависимости от состава полимера.
Вэтот период происходит удаление связанной воды и свободных летучих компонентов смол и катализаторов (ацетон, формальдегид, фенол). Общие потери массы составляют 10–12 %. Вторая стадия, соответствующая интервалу температур 200–700 ºС, является наиболее сложной по типу протекающих реакций и наиболее важной с точки зрения технологических свойств смесей.
Вэтой области развивается и в основном завершается процесс карбонизации полимера; содержание углерода в связующих повышается до 80–90 %. У смол со средней и высокой термостойкостью карбонизация завершается при 700–800 ºС. Кокс, который при этом образуется, является полукоксом, поскольку структура его не вполне упорядочена и содержит значительное количество атомов О и Н. Такой кокс представляет собой полимерное сочетание конденсированных ароматических углеродных слоев (ядерная часть структуры) и связывающих их боковых углеродных цепочек (периферийная часть). На третьей стадии (выше 700 ºС) угольная структура кокса непрерывно меняется. Если процесс протекает в окислительной среде, кокс полностью газифицируется. В восстановительной или нейтральной атмосфере увеличиваются размеры ароматических слоев и возрастает доля углерода, упорядоченного в слои за счет периферийной, неупорядоченной части молекул; одновременно удаляется кислород и водород. Считают, что этот процесс представляет собой постепенный переход от структуры кокса к более устойчивой форме – графиту с образованием различных переходных форм углерода.
Термостойкость складывается из периода деструкции и периода существования кокса, который некоторое время сохраняет функции связующего: σ адг в конце карбонизации равна 10–30 % от начального значения.
73
7.5. Особенности проявления прочности в нагретом состоянии смесей с неорганическими и органическими добавками
Разупрочнение нагретых смесей с неорганическими добавками связано главным образом с процессом расплав-
ления. Отсюда следующие выводы:
1.Чем ниже температура плавления неорганической добавки, тем раньше начинается разупрочнение. К добавкам с температурой плавления наиболее низкой относится жидкое стекло, наиболее высокой – огнеупорная глина. Среднее положение занимает бентонит. Но, как было указано, температура размягчения повышается с увеличением скорости нагрева смеси.
2.Так же, как и прочность смесей при нагреве с последующим охлаждением, нарастание прочности смесей на кварцевой основе в нагретом состоянии замедляется в интервале его модификационных изменений.
3.Температура размягчения смеси и снижение ее прочности зависят не только от температур размягчения чистых окислов, но и от возможного химического взаимодействия их с окислами зерновой части смеси. Поэтому необходимо соблюдать осторожность при изготовлении формы из зерен разного состава. В частности, это относится к формам и стержням из составов на разной неорганической основе. При этом качество смеси может ухудшаться постепенно, по мере увеличения числа заливок.
4.При введении в смесь небольшого количества органической добавки дополнительно к изменяющейся неорганической добавке наблюдается снижение прочности, но не температуры размягчения.
Разупрочнение смесей с органическими добавками связаноглавнымобразомспроцессами сгорания. Отсюдавыводы:
1.Процесс разупрочнения смесей с органическими добавками начинается при более низких температурах, чем процессы
74
размягчения неорганических добавок; в большинстве случаев эта температура не превышает 400 ºС. Значительной прочностью при высоких температурах обладают коксующиеся добавки.
2. При одновременном введении в смесь большого количества неорганических добавок температура разупрочнения смеси определяется температурой их размягчения, а не температурой сгорания органических добавок.
7.6. Прочность в нагретом состоянии, наблюдаемая на практике
Форма и стержень в нагретом состоянии могут иметь нулевую прочность без ущерба для качества отливок в случаях:
1)всестороннего сжатия стержня;
2)образования достаточно прочной корки на поверхности отливки к моменту потери прочности формой под воздействием тепла жидкого металла;
3)отсутствия размывающего действия стенок формы протекающим металлом.
Практически нулевой прочностью может обладать форма из чистого кварцевого песка при использовании выгорающей пенополистироловой модели. В большинстве случаев предел прочности смеси при сжатии в нагретом состоянии (около 1200 ºС) составляет 0,5–1,5 кг/см2. При более низкой прочности увеличивается опасность размыва формы металлом, а при более высокой – опасность образования горячих трещин в отливках.
75
8.ГАЗЫ В ФОРМЕ
8.1.Газовая среда литейной формы
Впервый момент заливки полость формы и поры смеси заполнены воздухом. Однако сразу после заполнения формы металлом в результате теплового воздействия в форме начинаются процессы испарения, диссоциации, возгонки (переход вещества из твердого состояния в газообразное, минуя жидкую фазу; то же, что сублимация), горения и т.п., в результате чего состав газовой среды формы существенно изменяется. Образующиеся газы вытесняют газы, ранее заполнявшие поры (азот и кислород); газы, возникающие при более высокой температуре (например, при диссоциации карбонатов, дегидратации гидратов), вытесняют газы, образовавшиеся при более низкой температуре и перед этим вытеснившие или разбавившие воздух.
Природа газов и последовательность их выделения из формовочной смеси по мере прогрева формы определяются прежде всего составом смеси. Жидкостекольные смеси, состоящие из кварцевого песка и жидкого стекла и отвержденные углекислым газом или феррохромовым шлаком (нефелиновым шламом), имеют влажность 4–6 %. Из 100 г продутой углекислым газом смеси при нагреве до 200 ºС выделяется 26–44 см3 СО2. В порах формы из этой смеси, заполненной металлом, основным компонентом газовой среды будет водяной пар (≈ 99 %); то же наблюдается и в практически сухой песчано-глинистой форме при остаточной влажности 0,2 % (рис. 12).
76
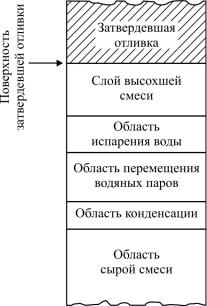
Рис. 12. Схема образования в форме областей испарения и конденсации
При нагреве смесей, содержащих растворимые в воде органические связующие (например, ССБ) или добавки, будут выделяться такие газы, как водород, углеводороды, продукты сгорания углеродной составляющей СО и СО2 и другие. Все это изменит первоначальный состав газовой среды литейной формы. Однако нужно учитывать то обстоятельство, что зона, охваченная интенсивным образованием паров воды, всегда будет шире (ее границей будет изотерма 100 ºС) зоны возгонки или горения органических материалов. Следовательно, и в этом случае в составе газовой среды будет преобладать водяной пар.
Роль реакции окисления железа кислородом незначительна, так как запасы свободного кислорода в порах формы невелики; гораздо большее значение имеют реакции окисления железа
77
углекислым газом и особенно водяным паром. Основная доля углекислого газа в форме образуется в результате реакции
С |
тв |
+ 2Н |
О→ СО+ 2Н |
2 |
. |
|
2 |
2 |
|
Твердый углерод Ств либо уже присутствует в исходном
составе смеси (графит, уголь, кокс), либо появляется в связи с частичным коксованием органических связующих при высокой температуре. В условиях литейной формы интенсивное окисление (горение) углерода, добавленного в смесь в виде графита, начинается при 450 ºС, и в интервале 800–1050 ºС при изменении концентрации водяного пара от 0 до 100 % происходит реакция между углеродом и водяным паром
С+ Н2О = СО+ Н2 .
Следовательно, основным окислительным газом по отношению к железоуглеродистым сплавам являются пары воды.
После начала взаимодействия окислительных газов с металлом отливки в газовой среде формы происходят значительные изменения в сторону увеличения количества восстановительных газов. Эти изменения находят отражение в составе газов, отбираемых из формы во время охлаждения отливки. Именно восстановительный характер отходящих газов свидетельствует о том, что в зоне взаимодействия металла с формой существует окислительная газовая среда.
Следует подчеркнуть, что пары воды в литейной форме могут играть не только роль окислительного газа. Известно, что они повышают реакционную способность окислов, интексифицируют процессы кристаллизации и спекания окислов при высокой температуре. Активирующее действие паров воды осуществляется путем химической адсорбции их на поверхности окисла. В результате внедрения гидроксильных групп в решетку окисла происходит поляризация атомов, ослабление сил связи вповерхностных слоях кристалла. Чем сильнее нарушена стехио-
78
метрия кристаллической решетки, тем выше реакционная способность вещества. Следовательно, пары воды могут не только окислять компоненты сплава, но и оказывать влияние на взаимодействие окислов с формовочными материалами.
Совершенно иная картина наблюдается в литейной форме (или ее части), изготовленной из безводных смесей с синтетическими смолами в качестве связующих (смолой ПК-104, фенолофурановыми смолами и др.). Кроме незначительного количества воздуха, находящегося в порах смеси в начальным момент заливки, газы, выделяющиеся из этих смесей, являются по отношению к основным компонентам литейных сплавов восстановительными. В качестве примера в табл. 11 приведен состав газов, выделившихся при нагреве смеси со смолой ОФ-1.
Таблица 1 1
Состав газов, выделяющихся при нагреве смеси со смолой ОФ-1
Температурный ин- |
|
|
Состав газов, % |
|
||
тервал отбора газов, ºС |
Н2 |
СО |
|
CnH2n+2 |
RO2 |
CnHm |
200–1100 |
49 |
22 |
|
14 |
14,2 |
0,8 |
200–1500 |
27,2 |
60,4 |
|
4,6 |
3,3 |
0,5 |
1100–1500 |
3,6 |
56 |
|
33,7 |
6,5 |
0 |
Объем выделяющихся из смеси газов более чем в 300 раз превышает объем кислорода, присутствующего в порах смеси; очевидно, что при таком соотношении компонентов газовой среды окисляющее действие кислорода практически не проявляется.
Состав газов сильно изменяется при повышении температуры, однако эти количественные изменения не меняют характер газовой среды, и по отношению к расплаву она остается восстановительной. Тем не менее на отливках есть окисная пленка.
79
8.2. Процессы газообразования
Исследования атмосферы литейной формы можно условно разделить на физико-механические и физико-химические. Первыми изучаются кинетика газового давления в форме, фильтрация газов и связанные с этой группой вопросы образования раковин в отливках. Исследователей данного направления больше интересуют вопросы количества выделяемых газов (независимо от состава) и кинетики их перераспределения по литейной форме. В работах второго направления решаются вопросы, связанные с качеством атмосферы литейной формы, химическим составом и химическим взаимодействием как с материалом формы, так и отливки. Больше внимания уделяется химической стороне вопроса, получению отливок без пригара, плен и других дефектов.
На рис. 13 представлена классификация процессов газообразования в литейной форме. (Десорбция – извлечение поглащенного вещества). Эти процессы, протекая практически одновременно, имеют различную природу. Как справедливо считает Я.И. Медведев, они «сливаются друг с другом, что затрудняет исследование каждого процесса в отдельности. Поэтому при изучении газового режима литейной формы сталкиваются с обобщенным процессом образования газов, который является результатом одновременного протекания индивидуальных процессов».
Мощность определенных процессов газообразования, а следовательно, и состав образующейся атмосферы литейной формы зависят от состава и массы формовочной смеси, времени от начала заливки металла, температуры прогрева формы и некоторых других факторов. В табл. 12 приведена ориентировочная мощность различных процессов газообразования в зависимости от вида форм.
80