
Процессы обработки заготовок. Часть 2. Составление рациональных техно
.pdf
|
|
|
|
на днище поршня |
|
|
|||
40 |
Зенкерование |
отвер- |
|
|
|
|
|
|
|
|
стий под |
поршневой |
|
|
|
|
|
|
|
|
палец, снятие фасок, |
|
|
|
|
|
|
||
|
подрезание торцов бо- |
Центровое |
отвер- |
Специаль- |
|||||
|
бышек, растачивание |
стие в бобышке на |
ный агрегат- |
||||||
|
канавок под стопор- |
днище поршня |
и |
ный станок |
|||||
|
ные кольца |
|
|
торец юбки порш- |
|
|
|||
50 |
Сверление |
отверстий |
ня |
|
|
|
|
|
|
|
для отвода масла |
|
|
|
|
|
|
||
60 |
Фрезерование |
проре- |
|
|
|
|
|
|
|
|
зей на юбке |
|
|
|
|
|
|
|
|
70 |
Чистовое и тонкое |
Торец юбки, внут- |
Горизон- |
||||||
|
растачивания отвер- |
ренний поясок от- |
тальный |
||||||
|
стий под поршневой |
крытого конца юб- |
двусторон- |
||||||
|
палец |
|
|
ки поршня и цен- |
ний |
расточ- |
|||
|
|
|
|
тровое отверстие в |
ной станок |
||||
|
|
|
|
бобышке на днище |
|
|
|||
|
|
|
|
поршня |
|
|
|
|
|
80 |
Тонкое копирное об- |
Внутренний |
поя- |
Прецизион- |
|||||
|
тачивание юбки порш- |
сок открытого кон- |
ный |
гидро- |
|||||
|
ня |
|
|
ца юбки поршня и |
копироваль- |
||||
|
|
|
|
отверстие |
в |
бо- |
ный станок |
||
|
|
|
|
бышке |
на |
днище |
|
|
|
|
|
|
|
поршня |
|
|
|
|
|
|
|
|
|
|
Окончание табл. 2.28 |
||||
|
|
|
|
|
|
|
|
|
|
Номер |
Краткое содержание |
Технологическая |
Оборудова- |
||||||
опера- |
|||||||||
ции |
операции |
|
база |
|
|
|
ние |
||
|
|
|
|
|
|
|
|
|
|
90 |
Отрезание центровой |
Внутренний |
поя- |
Токарный |
|||||
|
бобышки |
|
|
сок |
открытого |
станок |
|||
|
|
|
|
конца юбки порш- |
|
|
|||
|
|
|
|
ня и отверстие под |
|
|
|||
|
|
|
|
поршневой палец |
|
|
121
100 |
Подгонка поршня по |
Наружная поверх- |
Полуавтомат |
|
|
массе с погрешностью |
ность и торец юб- |
для |
подгон- |
|
2 грамма |
ки |
ки поршня |
|
|
|
|
по |
массе |
|
|
|
(весу) |
|
110 |
Лужение (анодирова- |
– |
|
|
|
ние) |
|
|
|
120 |
Контроль и сортиров- |
– |
Контроль- |
|
|
ка поршней на группы |
|
ный |
сорти- |
|
|
|
ровочный |
|
|
|
|
автомат |
Отсортированные на 4–5 групп поршни маркируют номером размерной группы, а затем при сборке комплектуют по этому признаку (селективная сборка). Сортировочный допуск дает возможность обеспечить зазор между поршнем и цилиндром в пределах, который практически достигается при точности обработки заготовок этих сопрягаемых деталей по 3 квалитету точности.
2.7.3. Технологические маршруты обработки поршневых колец
Поршневые кольца предназначены для уплотнения зазора между стенками цилиндра (гильзы) и поршнем в целях предотвращения проникновения газов из камеры сгорания в картер (компрессионные кольца) и смазочного масла из картера в камеру сгорания (маслосъемные кольца). В двигателях тракторов на поршень устанавливаются обычно 2–3 компрессионных
и1–2 маслосъемных кольца. Поршневые кольца должны плотно
ис равномерным распределением удельного давления прилегать к стенкам цилиндра по всей окружности. Для этого поршневые кольца выполняют с наружным диаметром в свободном состоянии больше, чем диаметр цилиндра (гильзы) и делают прорези. На рис. 2.14 приведены виды поршневых колец и их профили в радиальном сечении.
122

Рис. 2.14. Виды поршневых колец и их профили в радиальном сечении
Компрессионные кольца (рис. 2.14, а) имеют в радиальном сечении прямоугольную форму, на внешней образующей которой делают фаску под углом 30°. Эти кольца работают в условиях высоких температур и полусухого трения, особенно кольцо, расположенное у камеры сгорания. Верхнее компрессорное кольцо, работающее в наиболее тяжелых условиях, подвергается пористому хромированию с последующим лужением слоем олова толщиной 0,005–0,01 мм. Толщина хромового покрытия
0,1–0,2 мм, глубина пор 0,04–0,06 мм.
Маслосъемные кольца (рис. 2.14, б) более разнообразны по конструкции, однако их назначение (отвод излишков масла) и расположение на поршне не требует придания им особых газоуплотняющих и теплоотводящих свойств. Наиболее распространенная конструкция этих колец представляет собой кольца с радиальными углублениями по торцовой поверхности, предназначенными для перепуска масла во внутреннюю полость поршня. В поршневых кольцах для предохранения их от заклинивания при расширении от нагрева в прорези (замке кольца) предусматривают зазор 0,2–0,6 мм.
Для изготовления поршневых колец применяют высококачественные перлитные чугуны, легированные хромом, молибденом, вольфрамом или ванадием, а также модифицированный
123
чугун. Наряду с чугунными (литыми) поршневыми кольцами в ряде конструкций двигателей применяют стальные и металлокерамические маслосъемные кольца.
Точность обработки по высоте кольца выдерживают в пределах 7–8 квалитетов, шероховатость поверхности торцов Ra 1,25 мкм. Допуск на ширину прорези в замке в сжатом состоянии кольца 0,1–0,2 мм. Отклонение от параллельности торцовых поверхностей допускается в пределах допуска на высоту кольца. Отклонение от соосности наружной внутренних поверхностей не более 0,1 мм. Шероховатость внешней боковой поверхности кольца Ra 2,5 мкм.
Коробление торцовых поверхностей не должно превышать 0,05–0,07 мм. Местный радиальный зазор (просвет) между испытываемым кольцом и зеркалом гильзы (калибром) не должен превышать 0,02 мм. Упругость поршневого кольца проверяется его сжатием до получения в замке зазора, соответствующего зазору кольца в цилиндре. Технологический маршрут обработки компрессионного поршневого кольца представлен в табл. 2.29.
|
|
|
|
|
Таблица 2.29 |
|
Технологический маршрут |
|
|
||
|
компрессионного поршневого кольца |
||||
|
|
|
|
|
|
Номер |
Краткое содер- |
|
Технологическая |
|
Оборудование |
операции |
жание операции |
|
база |
|
|
05 |
Черновое шлифо- |
Наружная и внут- |
Специальный |
||
|
вание внутренней |
ренняя поверхно- |
бесцентрово- |
||
|
и наружной по- |
сти |
|
шлифовальный |
|
|
верхностей |
|
|
|
автомат |
|
|
|
Окончание табл. 2.29 |
||
|
|
|
|
|
|
Номер |
Краткое содер- |
Технологическая |
|
Оборудование |
|
операции |
жание операции |
база |
|
|
|
10 |
Черновое (обди- |
Торцы кольца |
Специальный |
||
|
рочное) шлифова- |
|
двусторонний |
||
|
ние торцов |
|
шлифовальный |
||
|
|
|
|
автомат |
|
20 |
Искусственное |
– |
Электропечь |
124
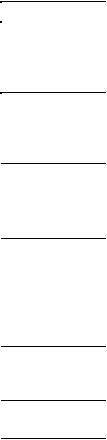
|
старение |
|
|
|
|
|
|
30 |
Получистовое |
|
Торцы кольца |
Специальный |
|||
|
шлифование |
тор- |
|
двусторонний |
|||
|
цов |
|
|
|
шлифовальный |
||
|
|
|
|
|
автомат |
|
|
40 |
Черновое |
обтачи- |
|
Специальный |
|||
|
вание по копиру |
|
копировальный |
||||
|
|
|
|
Торцы и внут- |
токарный полу- |
||
|
|
|
|
автомат |
|
||
|
|
|
ренняя поверх- |
Горизонтально- |
|||
50 |
Фрезерование |
|
|||||
|
(вырезание) замка |
ность кольца |
фрезерный |
ста- |
|||
|
|
|
|
нок |
|
||
60 |
Фрезерование |
(ка- |
|
|
|||
|
либрование) замка |
|
|
|
|||
70 |
Растачивание |
|
Торцы и наруж- |
Прецизионный |
|||
|
внутренней по- |
ная поверхность |
токарный |
ста- |
|||
|
верхности |
|
|
кольца |
нок |
|
|
80 |
Чистовое |
обтачи- |
|
|
|
||
|
вание колец по на- |
Торцы и внут- |
|
|
|||
|
ружному диаметру |
|
|
||||
|
|
|
|
ренняя поверх- |
|
|
|
90 |
Окончательное |
Горизонтально- |
|||||
ность кольца |
|||||||
|
фрезерование |
(ка- |
|
фрезерный |
ста- |
||
|
либрование) замка |
|
нок |
|
|||
100 |
Контроль |
|
|
– |
Контрольный |
||
|
|
|
|
|
автомат |
|
П р и м е ч а н и е. Обработку поршневых колец на операциях 30–90 производят партиями по 30–50 колец, закрепленных в приспособлении (на оправке или в стакане) в сжатом состоянии.
Верхнее компрессионное кольцо подвергается также хромированию и лужению.
При изготовлении маслосъемных колец после растачивания дополнительно выполняются операции по протачиванию канавок и фрезерованию прорезей для отвода масла.
125
2.7.4. Технологические маршруты обработки гильз цилиндров
Различают сухие и мокрые гильзы. Сухие (короткие) гильзы из материала повышенной износостойкости устанавливают в верхней части цилиндра двигателя и прилегают всей своей наружной поверхностью к цилиндру блока двигателя. Сухие гильзы применяют, в основном, в блоках двухтактных двигателей. Мокрые гильзы сопрягаются с блоком лишь по посадочным пояскам и по торцу буртов, а наружная поверхность между поясками может оставаться необработанной. Блоки тракторных и автомобильных двигателей имеют мокрые гильзы. Гильзы изготавливают из серых чугунов СЧ 20, СЧ 30 и из специальных чугунов с легирующими добавками.
Повышение износостойкости зеркала гильзы в ряде случаев достигается ее хромированием (толщина хрома 0,05–0,1 мм).
Для повышения износостойкости автотракторных гильз поверхность зеркала гильзы подвергают закалке с нагревом токами высокой частоты до твердости HRC 40–50 на глубину не менее 1,5 мм.
Заготовки гильз изготовляются литьем в земляные, оболочковые формы или центробежным литьем. Припуски на механическую обработку составляют 1,5–2,5 мм на сторону. Отливки очищают от песка и пригоревшей земли и подвергают отжигу.
Основной объем работ по механической обработке гильз приходится на токарные и расточные операции. При обработке необходимо учитывать, что гильза представляет собой тонкостенный цилиндр, легко деформируемый под действием усилий зажима и сил резания.
Основные технические требования к механической обработке заключаются в следующем. Точность изготовления отверстия автотракторных гильз обеспечивается в пределах 6–8 квалитетов.
Для получения точного сопряжения с поршнем гильзы в пределах допуска сортируют на группы с более жестким допуском в пределах 10–20 мкм. Допустимое отклонение формы отверстия на всей гильзе должно быть в пределах допуска груп-
пы (10–20 мкм).
126

Рис. 2.15. Гильза цилиндров двигателя ЯМЗ-238НБ
Допуски на диаметры наружных поверхностей (посадочные пояски) обычно назначаются по 6 квалитету точности. Биение посадочных поясков относительно внутренней поверхности
должно быть |
не более |
0,1 |
мм, а их |
шероховатость Rz |
= |
= 10–20 мкм. |
|
|
|
|
|
Шероховатость зеркала цилиндра |
тракторного двигате- |
||||
ля составляет |
Ra 0,32 |
мкм, |
автомобильного двигателя |
– |
|
Ra 0,16 мкм. |
|
|
|
|
|
Вобработанном виде гильза должна быть подвергнута гидравлическому испытанию под давлением 0,4 МПа.
Для получения заданной шероховатости поверхности гильза на заключительных операциях обработки подвергается шлифованию поясков и бурта и многократному хонингованию зеркала цилиндра (черновое, получистовое, чистовое, тонкое).
Вкачестве примера на рис. 2.15 показана гильза тракторного двигателя ЯМЗ-238НБ, а в табл. 2.30 приведен технологический маршрут механической обработки этой гильзы.
127
Таблица 2.30
Технологический маршрут обработки гильзы цилиндров двигателя
Номер |
Наименование |
Технологи- |
Оборудование |
||||
операции |
и содержание операции |
ческая база |
|
|
|||
05 |
Токарная: |
|
|
Центровое |
|
Токарный |
гид- |
|
черновое |
обтачивание |
отверстие |
|
рокопироваль- |
||
|
наружной поверхности |
(центровая |
|
ный станок с |
|||
|
гильзы по копиру, под- |
разжимная |
|
многорезцовым |
|||
|
резание бурта и обоих |
оправка) |
|
суппортом 1722 |
|||
|
торцов |
|
|
|
|
|
|
10 |
Расточная: |
|
Наружная |
|
Вертикально- |
||
|
черновое |
растачивание |
поверхность |
радиальный |
|||
|
отверстия гильзы |
гильзы |
|
4-шпиндельный |
|||
|
|
|
|
|
|
станок РП-209 |
|
20 |
Токарная: |
|
|
Центровое |
|
Токарный |
мно- |
|
получистовое |
обтачи- |
отверстие |
|
горезцовый |
|
|
|
вание поясков и бурта |
(центровая |
|
полуавто- |
|
||
|
|
|
|
разжимная |
|
мат 1А630 |
|
|
|
|
|
оправка) |
|
|
|
30 |
Расточная: |
|
Поверхность |
Вертикально- |
|||
|
чистовое растачивание |
поясков |
и |
расточной |
|
||
|
отверстия гильзы |
торец со сто- |
4-шпиндельный |
||||
|
|
|
|
роны бурта |
|
станок РП-209 |
|
40 |
Термическая обработка |
– |
|
Установка ТВЧ |
|||
|
(закалка ТВЧ) |
|
|
|
|
|
|
50 |
Токарная: |
|
|
Центровое |
|
Токарный |
мно- |
|
обтачивание |
поясков, |
отверстие |
|
горезцовый |
по- |
|
|
протачивание |
канавок |
(центровая |
|
луавтомат |
|
|
|
и снятие фасок |
|
разжимная |
|
1А730 |
|
|
|
|
оправка) |
|
|
|
||
|
|
|
|
|
|
|
|
|
|
|
|
Окончание табл. 2.30 |
|||
|
|
|
|
||||
Номер |
Наименование |
Технологи- |
Оборудование |
||||
операции |
и содержание операции |
ческая база |
|
|
128
60 |
Гидравлическое испы- |
– |
Гидравлический |
|
тание водой под давле- |
|
стенд |
|
нием 0,4 МПа в тече- |
|
|
|
ние 2 минут |
|
|
70 |
Хонинговальная: |
Поверхность |
Вертикальный |
|
черновое хонингование |
поясков |
хонинговаль- |
|
зеркала гильзы |
и торец со |
ный 4-х шпин- |
|
|
стороны |
дельный станок |
|
|
бурта |
|
80 |
Хонинговальная: |
Поверхность |
Вертикальный |
|
получистовое хонинго- |
поясков |
хонинговаль- |
|
вание |
и торец со |
ный 4-х шпин- |
|
зеркала гильзы |
стороны |
дельный станок |
|
|
бурта |
|
90 |
Токарная: |
Центровое |
Отделочно-об- |
|
чистовое обтачивание |
отв. (раз- |
точной двух |
|
поясков и бурта |
жимная оп- |
шпиндельный |
|
|
равка) |
станок 2А715 |
100 |
Токарная: |
Центровое |
Отделочно-об- |
|
чистовое подрезание |
отверстие |
точной 4-шпин- |
|
торца бурта |
(центровая |
дельный ста- |
|
|
разжимная |
нок 2705 |
|
|
оправка) |
|
110 |
Хоинговальная: |
Поверхность |
Вертикальный |
|
чистовое хонингование |
поясков и |
хонинговаль- |
|
зеркала гильзы |
торец со сто- |
ный 4-х шпин- |
|
|
роны бурта |
дельный станок |
Для контроля гильз цилиндров применяются пневматические и индикаторные приспособления.
Контролируются диаметры и форма отверстия, толщина бурта, торцовое и радиальное биения. На специальных устройствах производится автоматический контроль внутреннего диаметра гильз и их сортировка по размеру на группы.
129

2.8. Технологический маршрут обработки лопаток паровых и газовых турбин
Количество лопаток на одну турбину составляет 1500–3000 штук. Поэтому даже при мелкосерийном производстве турбин производство лопаток будет крупносерийным или массовым.
Лопатки турбин представляют собой детали пониженной жесткости с криволинейными, точными поверхностями, требующими сложной механической обработки.
Основными технологическими задачами при производстве лопаток являются:
получение установочных поверхностей лопатки (замка)
свысокой точностью;
достижение правильного положения пера лопатки относительно замка;
обеспечение точной формы и низкой шероховатости криволинейных поверхностей пера лопатки для уменьшения потерь на трение пара или газа о поверхность вращающейся лопатки.
На рис. 2.16 показаны лопатки паровых (рис. 2.16, а) и газовых турбин (рис. 2.16, б).
аб
Рис. 2.16. Лопатки турбин: а – паровых; б – газовых
Лопатки турбин делятся на направляющие (неподвижные) и рабочие (вращающиеся вместе с ротором). Главные части лопаток – это замок 1 и рабочая часть 2, называемая пером. Выпуклую поверхность пера называют «спинка», а вогнутую – «корыто». Лопатки паровых турбин применяются с длиной пера 200–1000 мм и более, для газовых турбин – 30–600 мм.
130