
Методические указания к лабораторным работам «Технология машиностроения» и «Управление качеством изделий» (120
..pdf
|
|
Таблица 4 |
Распределение действительных размеров изделий |
||
|
|
|
Интервал |
Абсолютная |
Относительная |
размеров, мм |
частота m, шт. |
частота m/n |
7,91–7,93 |
1 |
0,02 |
7,93–7,95 |
2 |
0,04 |
7,95–7,97 |
5 |
0,10 |
7,97–7,99 |
11 |
0,22 |
7,99–8,01 |
14 |
0,28 |
8,01–8,03 |
10 |
0,20 |
8,03–8,05 |
4 |
0,08 |
8,05–8,07 |
2 |
0,04 |
8,07–8,09 |
1 |
0,02 |
|
m = n = 50 |
m/n = 1,0 |
|
|
|
Полагая, что распределение размеров соответствует нормальному закону распределения, определяем погрешность обработки (поле рассеяния действительных размеров) заготовок по правилу «шести сигм»
= 6
иквалитет точности.
Ввыводах даем заключение о соответствии формы кривой распределения размеров кривой нормального распределения, выявляем причины несоответствия этих кривых. Делаем вывод о точности данного метода обработки и даем рекомендации повышения точности обработки. Результаты выполненной работы заносим в бланк отчета (Приложение 1).
Контрольные вопросы
1.Приведите примеры комплексных кривых распределения.
2.Покажите форму кривой распределения размеров поверхностей заготовок, если в процессе обработки произошло нарушение настроечного размера.
3.В каких случаях имеет место асимметричная форма кривой распределения размеров обрабатываемых поверхностей?
4.Как проявится на кривой распределения размеров влияние размерного износа режущего инструмента?
5.Как по кривой распределения найти вероятное количество годных деталей, если поле допуска ýже поля рассеяния?
11
Работа №2
ИССЛЕДОВАНИЕ ДЕФОРМАЦИЙ ЗАГОТОВОК ПРИ ЗАКРЕПЛЕНИИ
Цель работы – исследование влияния силы закрепления нежесткой заготовки на погрешность формы.
Содержание работы
1.Определить погрешность формы внутренней поверхности тонкостенного кольца, закрепляемого в трехкулачковом патроне, расчетно-аналитическим и экспериментальным методами.
2.Определить достижимые квалитет и степень точности поверхностей кольца при данном способе закрепления заготовки.
3.Выявить и сопоставить степень влияния технологических факторов на погрешность формы кольца.
Порядок выполнения работы
Студенту выдают стальное кольцо и задают силу Q = = 1000…1500 Н, обеспечивающую надежное закрепление кольца при оптимальных параметрах режима резания. Размеры кольца D, d, b измеряем штангенциркулем (рис. 3). Размеры h, Rcр и момент инерции J поперечного сечения кольца определяем по формулам
h |
D d |
; |
R |
D d ; |
J bh3 мм4. |
|
|||||
2 |
|
ср |
4 |
12 |
|
|
|
Результаты заносим в бланк отчета (Приложение 2).
1. Определение погрешности формы расчетно-аналитичес- ким методом
При закреплении кольца в трехкулачковом патроне по наружной поверхности в местах приложения зажимного усилия Q (под
кулачками) возникают прогибы кольца 1, а между кулачками – его выпучивание 0 (рис. 4).
12
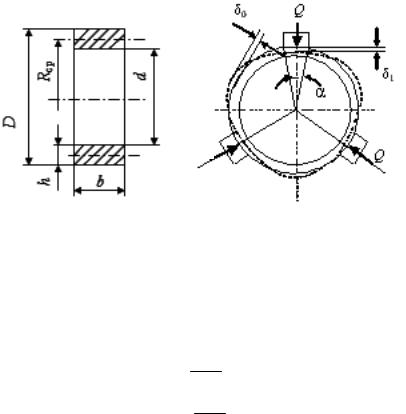
Q
Рис. 3. Эскиз кольца: |
Рис. 4. Схема деформации кольца |
D – наружный диаметр; d – диаметр |
под влиянием силзакрепления: |
отверстия; b – ширина; h – толщина; |
Q – сила закрепления; δ1 – прогиб |
Rср – средний радиус |
кольца; δ0 – выпучивание кольца; |
|
α– уголконтактакулачкаикольца |
Величины 1 и 0 определяем по следующим формулам:
QR3
δ1 k1 EJср ;
QR3
δ0 k0 EJcр ,
где k0, k1, kΣ – коэффициенты, зависящие от ширины охватываю-
щей части кулачков (угла контакта кулачка с поверхностью заготовки); Q – сила закрепления, Н; Rcр – средний радиус, мм; Е – модуль упругости материала кольца (для стали Е = 2 105 Н / мм2); J – момент инерции поперечного сечения кольца относительно нейтральной оси, мм4. Значения коэффициентов k0, k1, kΣ приведены в табл. 5.
|
|
|
Таблица 5 |
|
Значения коэффициентов k0, k1 и kΣ для угла контакта |
||||
|
|
|
|
|
Угол контакта , град |
k0 |
k1 |
kΣ |
|
0 |
– 0,0140 |
0,0160 |
0,0300 |
|
30 |
– 0,0095 |
0,0095 |
0,0180 |
|
50 |
– 0,0035 |
0,0020 |
0,0055 |
|
13

Расчетную величину погрешности формы определяем по формуле
ф δ1 δ0 .
Результаты расчета заносим в бланк отчета (см. приложение 2).
2. Определение погрешности формы кольца измерением
Для определения погрешности формы кольца 1 от силы закрепления Q используем экспериментальную установку (рис. 5). Самоцентрирующий трехкулачковый патрон 2 с комплектом сменных кулачков размещен на неподвижной опоре. В одном из кулачков установлена гидравлическая месдоза 3. При закреплении кольца силу Q контролируем по манометру 4 месдозы 3. Давление, соответствующее этой силе Q, находим по тарировочному графику.
Рис. 5. Экспериментальная установка:
1 – кольцо; 2 – самоцентрирующий трехкулачковый патрон; 3 – гидравлическая месдоза; 4 – манометр; 5 – нутромер; 6 – индикатор
Измерение деформации кольца под кулачками 1 и между ними 0 выполняем с помощью нутромера 5 индикаторного типа с
ценой деления 0,01 мм при заданной силе Q. За величину деформации кольца принимаем среднее значение трех измерений. Значение деформации поперечного сечения кольца соответствует 1/3
14
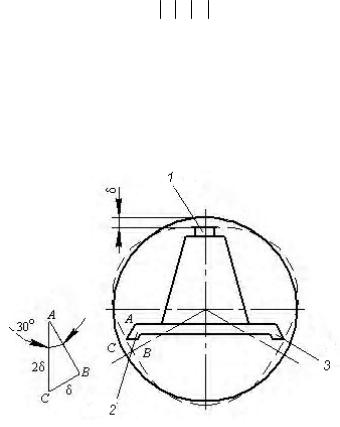
показания индикатора 6. Это объясняется тем, что индикатор 6 нутромера 5 показывает сумму двух перемещений: мерительного наконечника и ножек корпуса нутромера. Если мерительный наконечник 1 (рис. 6) перемещается на величину деформации кольца,
равную , то ножки корпуса нутромера перемещаются на величину 2 . Следовательно, общее перемещение составляет
+ 2 = 3 ,
адеформация кольца равна 1/3 показания индикатора. Результаты измерений заносят в бланк отчета. Фактическую погрешность формы определяем по формуле
ф δ1 δ0 .
По результатам работы находим относительную погрешность расчетного метода
|
ф |
ф |
100 %. |
|
|
||
|
|
|
|
|
ф |
|
|
Производим замену кулачков следующим комплектом и полностью повторяем эксперимент.
Рис. 6. Схема измерения погрешности формы кольца:
1 – мерительный наконечник; 2 и 3 – ножки корпуса нутромера
15
По результатам расчета и эксперимента строим график зависимости ф f ( ).
Контрольные вопросы
1.Приведите схемы установки тонкостенного кольца без искажения его формы при закреплении.
2.Какой квалитет точности диаметра отверстия кольца можно получить по условиям выполненного исследования, если погрешность формы обработанного отверстия принять равной половине допуска на диаметр?
3.Какова должна быть сила закрепления кольца по условиям данного исследования, если необходимо обеспечить диаметр отверстия кольца по 8-му квалитету точности с погрешностью формы отверстия не более 1/3 допуска размера диаметра?
4.Приведите примеры технологических методов обработки, не требующих закрепления заготовки.
16
Работа № 3
ИССЛЕДОВАНИЕ ПОГРЕШНОСТИ НАСТРОЙКИ СТАНКА НА РАЗМЕР
Цель работы – исследование погрешности установки режущего инструмента на заданный размер.
Содержание работы
1.Исследовать погрешность установки (регулирования) резца на размер по лимбу, индикатору, жесткому упору, эталонной детали и щупу.
2.Определить погрешности настройки станка для выполнения чистовой обработки.
Порядок выполнения работы
Погрешность настройки определяется как поле рассеяния положений инструмента при обработке нескольких партий заготовок, т. е. при многократной установке инструмента на размер. Погрешность настройки равна допуску на настроечный размер или разности наибольшего и наименьшего настроечных размеров. Эта величина включает в себя несколько составляющих. Одной из существенных составляющих является погрешность установки (регулирования) инструмента на размер.
1. Исследование погрешности установки ( регулирования)
резца на размер
Погрешность установки инструмента по каждому исследуемому методу определяем контрольным индикатором 1 с ценой деления 0,001 мм, размещенным на направляющей станка (рис. 7).
Установку инструмента в заданное положение проводим 10 раз. При первом измерении шкалу контрольного индикатора устанавливаем на нуль. При последующих измерениях фиксируем показания
17
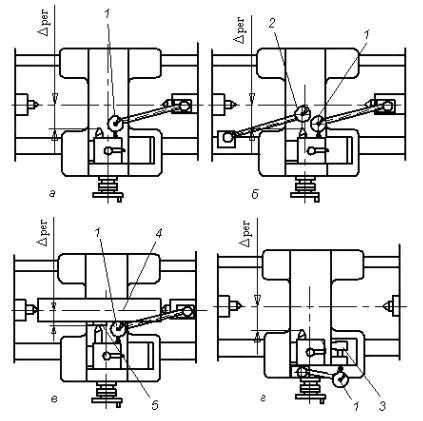
индикатора с учетом знака отклонения от нулевого положения. Погрешность установки (регулирования) инструмента на размер при малом количестве измерений характеризуется размахом значений полученных величин:
рег max min ,
где max – наибольшее (положительное) отклонение; min – наименьшее (отрицательное) отклонение.
Рис. 7. Схема настройки инструмента на размер:
а – по лимбу; б – по индикатору; в – по эталонной детали и щупу; г – по жесткому упору; 1 – контрольный индикатор; 2 – рабочий индикатор; 3 – упор; 4 – эталонная деталь; 5 – щуп
18
Погрешность установки резца по лимбу (рис. 7, а). Приступая к работе, любое, желательно кратное пяти, деление лимба принимаем за начало отсчета, предварительно выбрав зазор в винтовой паре. Контрольный индикатор 1 вводим в контакт с поперечным суппортом. Шкалу индикатора устанавливаем на нуль. Отводим поперечный суппорт «на себя» и затем снова устанавливаем суппорт по принятому делению лимба в заданное положение. Смещения суппорта от заданного положения фиксируем в бланке отчета c учетом знака (Приложение3).
Погрешность установки резца по индикатору (рис. 7, б). На-
строечный (рабочий) индикатор 2 с ценой деления 0,01 мм устанавливаем на станине станка. При первом подводе инструмента к рабочему индикатору 2 шкалы обоих индикаторов устанавливаем на нуль. После отводим суппорт «на себя» и затем снова устанавливаем инструмент, осуществляя контроль по рабочему индикатору, в первоначальное положение. Смещение от первоначального положения фиксируем по контрольному индикатору 1 и результат записываем в бланк отчета (см. приложение 3).
Погрешность установки резца на размер по эталонной детали с применением щупа (рис. 7, в). При выполнении иссле-
дования к установленной в центрах эталонной детали 4 подводим инструмент. Между ним и эталонной деталью помещаем щуп 5, толщину которого выбираем в пределах 0,05…0,30 мм. Критерием правильности установки резца служит незначительное усилие («закусывание») щупа при его протягивании. Отклонение от первоначального положения суппорта измеряем контрольным индикатором 1 и записываем в бланк отчета (см. приложение 3).
Погрешность установки резца по жесткому упору (рис. 7, г).
Поперечный суппорт подводим к упору 3, закрепленному на каретке продольного суппорта. При этом шкалу контрольного индикатора устанавливаем на нуль. При последующих перемещениях суппорта измеряем его смещение относительно первоначального положения по контрольному индикатору 1. Результаты записываем в бланк отчета (см. приложение 3).
По результатам экспериментов определяем погрешности настройки инструмента для рассмотренных методов установки резца
на размер по: лимбу – л, индикатору – ин, эталонной детали и щупу – эт и жесткому упору – уп.
19
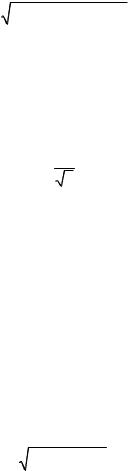
2. Расчет погрешности настройки станка для выполнения чистовой обработки
При настройке методом пробных ходов и измерений (МИПР) погрешность настройки н, отнесенная к диаметру обрабатываемой заготовки, составляет
н 2K |
изм2 расч2 |
рег2 , |
где K = 1,0…1,2 – коэффициент, учитывающий отклонение закона распределения составляющих погрешностей от нормального зако-
на; изм – погрешность измерения пробных заготовок (при измерении микрометром 1-го класса точности изм = 0,007…0,009 мм);
расч – погрешность вычисления средней арифметической величины размера пробных заготовок
расч σn ,
где – среднее квадратичное отклонение, характеризующее точность данного метода обработки; n – число пробных заготовок (обычно принимают n = 5…10 шт.). Если значение неизвестно, то приближенно принимают
σ 16 T ,
где Т – допуск на выдерживаемый размер (задается преподавателем в пределах 0,1…0,2 мм).
Кроме этих погрешностей на погрешность настройки оказывают влияние погрешности установочных мер, температурных деформаций, базирования и т. д.
При настройке по эталонной детали погрешность настройки определяют по формуле
н 2K |
изг2 .эт рег2 , |
где изг.эт – погрешность изготовления эталонной детали (прини-
маем в пределах 0,005…0,015 мм); рег – погрешность установки
принимать по результатам эксперимента.
Заполняем бланк отчета (см. приложение 3) и делаем выводы о выполненной работе.
20