
- •Рис. 1. Укрупнённая схема связей службы ОУП с другими службами предприятия
- •Бюро запуска осуществляет запуск в производство деталей и узлов заданной номенклатуры изделий на плановый период с учётом опережения их запуска;
- •Производственно-диспетчерские бюро (ПДБ) цехов составляют месячные производственные программы для производственных участков цеха;
- •Склады ПДО осуществляют хранение материалов, заготовок, узлов, комплектующих деталей, потребность в которых чаще всего возникает при нарушениях нормального хода производства на предприятии.
- •Рис. 3. Пример матричной структуры службы оперативного управления
- •3.2. Базовые системы оперативно-производственного планирования, их характерные черты и особенности
- •4.2. Календарно-плановые нормативы, применяемые в ОПП: их содержание и методика расчёта
- •Методика расчёта нормативного размера партии деталей

49
|
nmin |
tпз |
, |
|
tш т |
||
|
|
|
|
где n min − минимальный размер партии деталей; |
|||
t п з |
− норма подготовительно-заключительного времени по ведущей |
||
операции; |
|
|
|
t ш т |
− норма штучного времени по ведущей операции с учётом |
||
выполнения норм; |
|
|
α − коэффициент допустимых потерь на переналадку оборудования. В зависимости от типа и масштаба производства α = 0,005 ÷ 0,15.
С помощью этой формулы, как правило, определяется размер партии для деталей с наиболее трудоёмкими переналадками оборудования. При этом расчётный размер партии корректируется с учётом определённых производственных условий и устанавливается равным или кратным величине месячной программы выпуска по данной детали. Затем по установленным размерам партии определяется периодичность деталей по определённым формулам.
Методика расчёта нормативного размера партии деталей
1. Определяется ведущая операция производственного процесса. Ведущей операцией следует считать ту, у которой отношение
подготовительно-заключительного к штучному времени является максимальным:
|
|
|
tпз |
→ max. |
||||
|
|
|
|
|
||||
|
|
|
tш т |
|
|
|
||
2. Рассчитывается минимальный размер партии деталей (n min ) по |
||||||||
ведущей операции: |
|
|
|
|
|
|
|
|
n |
|
= |
tп.з |
÷ |
100 |
≈ n , |
||
|
min |
|
|
tш т |
|
|
|
|
|
|
|
|
|
|
|
где − процент допустимых потерь на переналадку оборудования, %.

50
3. Определяется периодичность запуска-выпуска партий деталей в
обработку (R з в ): |
|
|
R з в = |
n |
, |
|
||
|
N с.д |
где n − величина партии деталей, равная её минимальной величине, округлённой до ближайшего целого числа, шт.
Nс.д. − среднесуточная потребность в данной детали, шт/дн.
Для упрощения ОПП целесообразно унифицировать полученные значения периодичности запуска.
Рекомендуются следующие унифицированные величины периодичности изготовления деталей: 3 месяца, 1 месяц, 10 рабочих дней, 5 рабочих дней, 2,5 рабочих дня (R униф ).
При этом размер партии устанавливается исходя из нормативной (унифицированной) периодичности запуска (выпуска), принятой на соответствующем производственном участке, т.е. n = Nс.д. ∙ R униф .
Вслучае если для обработки деталей применяется оборудование, не требующее значительного времени на наладку, отправным критерием при установлении нормативной величины партии должна служить непрерывность выполнения каждой операции − не менее смены. При этом для наиболее производительной операции технологического процесса размер партии будет как минимум равен сменной или полусменной выработке деталей при высокой производительности соответствующего оборудования.
Продолжительность обработки партии деталей в данном случае рекомендуется определять по наиболее трудоёмким операциям, для того чтобы избежать чрезмерного увеличения длительности производственного цикла.
Врезультате последующей корректировки размера партии её величину приводят в соответствие с потребностью в деталях для выполнения программы выпуска.
Для обеспечения периодического изготовления деталей необходимо стремиться к тому, чтобы установленный размер партии укладывался в

51
объёме производственного задания целое число раз или был кратен этой величине.
Тактом выпуска (ч) называется период времени между выпуском двух смежных деталей с поточной линии. Такт выпуска измеряется в днях, неделях, часах, минутах.
Ритм выпуска (R) – промежуток времени между выпуском двух смежных транспортных (передаточных) партий с поточной линии.
Зависимость между величиной партии и периодом её повторений в производстве (R) выражается так:
R = n T ,
N
где N – программа запуска (выпуска) за планируемый период Т(дн).
Длительность производственного цикла (Т)
Производственным циклом изготовления детали называется календарное время, в течение которого она изготавливается, начиная от запуска исходного сырья или материала на 1-ю операцию и кончая выпуском готовой продукции.
Длительность производственного цикла складывается:
-из технологического времени, т.е. времени, непосредственно затрачиваемого на изготовление продукции;
-времени межоперационной межцеховой транспортировки изделия;
-времени межоперационного и окончательного контроля;
-времени межоперационного пролёживания изделия в ожидании освобождения оборудования.
В серийном производстве Т определяется по партиям или серии. Различают: Т цикла операции; Т цикла в пределах цеха; Т цикла по
предприятию в целом.
Общая длительность производственного цикла изделия определяется циклом ведущей детали.
52
Длительность цикла сборки узла, в который входит ведущая деталь, определяется длительностью общей сборки изделия, начиная от времени поступления в сборку ведущего узла.
Расчёт длительности производственного цикла необходим для определения сроков запуска изделий в обработку при заданных сроках его выпуска, расчётов времени опережения, определения размеров производственных заделов, размеров оборотных средств в незавершённом производстве.
Календарным опережением называется величина календарного времени от запланированной даты выпуска серий изделий до запуска деталей или узлов на определённой стадии производства.
По опережениям можно определить, за сколько дней до выпуска готового изделия должна быть запущена в обработку партия данных деталей на каждой технологической стадии производства. Величина опережения может быть выражена в днях, в изделиях или в порядковых номерах изделий, которые присваиваются также комплектам заготовок, узлов.
Величина опережения слагается из длительности производственного цикла и резервного времени, обеспечивающего своевременное начало работ на последующей фазе процесса при возникновении каких-либо перебоев.
Опережение может рассчитываться как по запуску детали по каждому цеху, так и по выпуску её цехом.
Опережение рассчитываются по отдельным цехам и деталям изделия.
Время опережения на запуск (Ч зап ) определяется как сумма длительности изготовления детали (изделия) во всех цехах, включая и цех для которого рассчитывается время опережения, а также резервное время во всех цехах, т.е. время опережения на запуск заготовительного цеха относительно сборочного равно длительности цикла изготовления детали (изделия).
Время опережения на выпуск (Ч вып ) рассчитывается как сумма длительности изготовления детали (изделия) во всех цехах, следующих за цехом, для которого рассчитывается время опережения, и резервного

53
времени во всех цехах (включая цех, для которого рассчитывается время опережения).
Графически расчёт времени опережения представлен на рис. 6
Ч зап. заг. ц.
Ч вып.заг.ц.
t з аг |
|
t р.з. |
|
Ч зап. обр.ц. |
|
|
|||
|
|
|
|
|
t обраб |
|
|
|
|
Ч вып. обр.ц. |
|||
|
|
|
|
|||||
|
tрезерв |
|
|
|
|
Ч зап. узл. сб. |
||
|
|
|
|
|
||||
|
|
|
||||||
|
|
|
||||||
|
|
|
||||||
|
|
резервн. |
|
|
|
|
|
|
|
|
t р |
|
|
|
|
|
|
|
|
|
t |
уз.сб. |
|
t у.с. р. |
||
|
|
|
|
|
||||
|
|
|
|
|
|
|
||
|
|
|
|
|
|
|
|
|
|
|
|
|
|
|
|
|
|
Ч вып.узл.сб
t общ.сб.
Т цикла изготовления изделий
Рис. 6. Расчёт времени опережения по изделию,
где Ч зап. i – время опережения на запуск в i-м цехе; Ч вып.i – время опережения на выпуск в i-м цехе; t p.i – резервное время в i-м цехе.
Расчёты опережения запуска-выпуска необходимы для того, чтобы определить частные сроки запуска и выпуска деталей, что необходимо для своевременного комплектного обеспечения любого цеха заготовками и деталями и своевременного выпуска продукции.
Ввиду того, что в каждом цехе возможны отключения от нормального хода производства по разным причинам (поломка оборудования, невыход рабочего и др.), вследствие чего удлиняется производственный цикл, то необходимо предусматривать страховые сроки в межцеховом опережении, в результате чего образуются страховые запасы деталей.

54
Заделами называются заготовки, полуфабрикаты и детали в процессе их обработки, готовые детали и узлы, находящиеся на всех стадиях производственного процесса.
Заделы необходимы для обеспечения непрерывности производственного процесса и ритмичного выпуска продукции.
Общий размер производственного задела складывается из внутрицеховых и межцеховых заделов.
Внутрицеховые заделы бывают:
-технологический; -транспортный;
-страховой;
-межоперационный оборотный.
К технологическим ( Z т ех ) относятся заделы на рабочих местах, размер которых на каждом рабочем месте равен установленной партии, то есть числу деталей, подлежащих одновременно обработке в соответствии с технологическим процессом:
m ex Cобщ Р ,
где Z m ex − величина технологического задела, шт.;
Собщ − общее число рабочих мест на участке (цехе);
Р − размер транспортной (передаточной партии).
Транспортный задел ( Zт рансп) включает в себя узлы и детали, находящиеся в процессе транспортировки между рабочими местами. Размер его устанавливают по-разному. При передаче деталей с операции на операцию транспортными партиями задел равен величине транспортной партии:
Zт ранс (Собщ 1) P ,
где Zт ранс − величина транспортного задела, шт.
Межоперационный оборотный задел ( Z м о ) - задел, возникающий при перерывах в работе одних рабочих мест при продолжающейся работе других.

55
Z |
м о |
T Ci |
|
T Ci 1 , |
|
|
ti |
|
ti 1 |
|
|
|
max |
|
где Z м о − максимальная величина межоперационного оборотного
max
задела, шт.
−длительность i и (i+1) операций, мин.;
Ci ; Сi 1 − количество рабочих мест на i и (i+1) операциях;
T − расчётный период времени, при котором количество работающих станков на смежных операциях остаётся неизменным, мин.
Страховые (резервные) заделы ( Zст рах) создаются для обеспечения рабочих мест заготовками, полуфабрикатами или готовыми деталями на случай перерывов в подаче их от питающих рабочих мест, со складов, из цехов.
Zст рах = 4 – 5% сменного задания.
Поскольку правильное размещение заделов по отдельным стадиям производственного цикла играет решающую роль в обеспечении ритмичной работы, то расчёт величины разделов ведётся отдельно по его составляющим.
В ОПП чаще всего используется классификация заделов в зависимости от места образования. По этому признаку различают заделы цикловые и складские.
Цикловые заделы включают партии узлов, деталей или заготовок, запущенных в производство, но ещё незаконченных обработкой на той или иной технологической стадии и находящихся в цехах на производственных участках, то есть цикловой задел состоит из технологического задела (т.е. задела на рабочих местах) и транспортного задела.
Расчёт циклового задела производится на основе нормативной величины партий деталей, длительности производственного цикла и планового задания по изготовлению данной детали и состоит в определении количества партий одноименных деталей, которые должны находится в процессе обработки в каждый данный момент времени. Средняя величина нормативного циклового задела ( Zц ) определяется

56
Zц = Tц Nср.сб. ,
где Т ц − длительность производственного цикла изготовления детали; − среднесуточная потребность сборки в этих деталях.
Складской задел состоит из оборотных заделов (складские запасы заготовок, деталей, используемых для повседневного питания цехов) и страховых заделов, создаваемых для ликвидации возможных перебоев в производстве. Складские заделы деталей представляют собой переменную величину.
Минимальный складской задел устанавливается с учётом некоторого резерва на случай возможного опоздания изготовления очередной партии.
Эта часть складского задела соответствует страховому заделу. Она устанавливается на основе опытных данных.
Максимальный складской задел ( Z max ) равен сумме страховой и оборотной части в момент поступления очередной партии деталей.
Z max = ni Zст рахi ,
где ni − размер партии изготовления i детали.
Средний размер складского задела необходимо рассчитывать для равномерного расходования деталей для питания, дальнейших технологических стадий производства он определяется:
Z |
|
= |
|
ni |
Zст рах . |
|
ср.скл |
2 |
|||||
|
|
i |
||||
|
|
|
|
|||
Заделы, находящиеся на |
1-е |
|
число планового периода (месяца, |
квартала) в производстве на межцеховых и внутрицеховых складах,
называются переходящими заделами.
Переходящие заделы включают внутрицеховые или цикловые заделы и складские оборотные заделы. (В серийном производстве переходный задел выражается целыми партиями).
Переходящий задел складских готовых деталей перед сборкой состоит из 2 частей − оборотной и страховой.
Оборотная часть переходящего складского задела ( Zср.скл ) определяется при помощи календарного графика изготовления партий деталей. Для этого количество дней от 1-го числа предстоящего месяца до поступления

57
на склад ближайшей партии деталей ( В ) умножается на среднесуточную потребность сборки в этих деталях ( Nср.сб ):
Zоб В Nср.сб. .
Использование расчётных формул для определения величины переходящих заделов способствует обоснованности ОПП, но не является гарантией точности самого расчёта. Только при составлении календарных планов запуска – выпуска деталей можно наиболее точно определить величину переходящих заделов.
Вэтом случае величина переходящего оборотного задела устанавливается путём сопоставления календарных сроков запускавыпуска партий деталей и самих размеров партий в 2 смежных цехах.
Впереходящем цикловом заделе будут все партии деталей, которые, согласно графику, допущены в обработку и ещё находятся в производстве на начало планируемого периода.
Несмотря на элементарную форму определения заделов, эти расчёты целесообразно проводить с помощью персональных компьютеров, так как номенклатура деталей на предприятии может достигать нескольких тысяч позиций.
Расчёты переходящих нормативных заделов ведутся раздельно по каждой плановой позиции деталей, изготовляемых партиями, и носят единовременный характер. Они, как правило, проводятся 1 раз в год на производственную программу планируемого года за 10−15 дней до его начала с последующей корректировкой только при резких изменениях программы или фактического хода производства.
Страховая часть переходящего складского задела устанавливается в днях и определяется на основе опытных данных предприятия. Она создаётся в целях компенсации всякого рода перебоев в ходе производства
идля обеспечения непрерывности сборки и выпуска изделий.
58
Таблица 4.2
Примерные нормы страхового задела на складе
(дни потребления)
Перио- |
Условные |
Длительность производственного цикла |
|||||
дичность |
обозначения |
|
|
|
|
|
|
1 − 3 |
4 − 6 |
|
7 − 10 |
11−15 |
Более 15 |
||
запуска |
|
|
|
|
|
|
|
|
|
|
Страховой задел |
|
|||
|
|
|
|
|
|||
|
|
|
|
|
|
|
|
2,5 дн. |
М/8 |
1 |
2 |
|
2 |
3 |
3 |
|
|
|
|
|
|
|
|
5 дн. |
М/4 |
1 − 2 |
1 − 2 |
|
2 |
3 |
3 |
|
|
|
|
|
|
|
|
10 дн. |
М/2 |
1 − 2 |
2 − 3 |
|
3 |
3 − 4 |
4 |
|
|
|
|
|
|
|
|
1 месяц |
М/ |
1 − 2 |
2 − 3 |
|
3 |
3 − 4 |
4 |
|
|
|
|
|
|
|
|
Приведённые в данном разделе календарно-плановые нормативы используются в качестве базы оперативно-производственного планирования на предприятиях.
Вопросы и задания для самоконтроля
1.Дайте понятие оперативно-производственного планирования (ОПП).
2.Перечислите основные этапы ОПП.
3.Чем обусловлена определённая последовательность этапов ОПП?
4.Какова роль и значение календарно-плановых нормативов в ОПП?
5.Перечислите календарно-плановые нормативы, используемые в ОПП.
6.Что такое серия изделий?
7.Что такое партия изделий?
8.Какие условия необходимо соблюдать при расчёте партии изделий?
9.Дайте понятие партии деталей.
10.Что понимается под оптимальной партией деталей?
11.Какова методика расчёта размера партии деталей?
12.Как определить периодичность запука-выпуска деталей?
13.Дайте понятие унифицированного ряда периодичности запускавыпуска деталей.
14.Какова методика расчёта длительности производственного цикла?
15.Что такое время опережения?
16.Перечислите виды времени опережения и дайте методику их расчёта.
59
17.Какова практическая значимость времени опережения?
18.Какова роль и значение заделов в ОПП?
19.Перечислите виды заделов и охарактеризуйте их.
20.Что такое цикловые заделы?
21.Дайте расчёт нормативной величины циклового задела.
22.Что такое складские заделы, их структура?
23.Какова методика расчёта уровней запасов в складских заделах?
24.Дайте понятие задела.
25.Какова методика расчёта переходящего задела?
5.Организация оперативного планирования в индивидуальном
производстве
Как известно, индивидуальное производство характеризуется изготовлением различных изделий поштучно или небольшими сериями.
Повторяемость выпуска изделий либо отсутствует, либо нерегулярна и не оказывает влияния на существенные особенности ведения производственного процесса.
Главная задача ОПП в индивидуальном производстве заключается в обеспечении своевременного выполнения разнообразных заказов изготовления изделий, предусмотренных договорами, заключёнными с заказчиками, и равномерной загрузки всех участков и звеньев производства при наиболее коротких производственных циклах изготовления продукции.
Характерной чертой ОПП индивидуального производства является тесная связь календарно-плановых расчётов производства с планированием технической подготовки выполнения каждого заказа.
Календарно-плановые расчёты в индивидуальном производстве охватывают весь процесс изготовления изделия. Эти расчёты выполняются в порядке, обратном ходу технологического процесса, то есть установленные сроки окончания выполнения заказа определяют необходимые сроки запуска изделий в производство.
В процессе расчётов определяются:
- длительность производственного цикла изготовления изделий;
60
-строят цикловые графики по отдельным изделиям (заказам);
-определяют календарные опережения в работе цехов;
-составляют сводный календарный график выполнения заказов, принятых к производству по плану предприятия;
-уточняют календарные опережения в работе цехов, которые практически устанавливают планируемый ход выполнения заказов;
-проводят «объёмные» расчёты загрузки производственных площадей и оборудования с целью выравнивания загрузки по отдельным периодам;
-осуществляют корректировку сводного графика с целью выравнивания загрузки по отдельным плановым периодам.
Определение длительности производственного цикла изготовления изделия Тц − важный календарно-плановый расчет, так как Тц берется в основу других расчетов. Обычно определение длительности цикла начинается с построения циклового графика (циклограммы) общей сборки изделия. Отправным пунктом является дата сдачи изделия заказчику, от нее строится «главная линия» последовательно связанных между собой сборочных процессов. Затем определяется, длительность выполнения наиболее трудоемких процессов в механообрабатывающих и заготовительных цехах. Между смежными цехами предусматривается резервное время, учитывающее возможные задержки в работе, а также время на оформление документов. При изготовлении сложных технических изделий вместо цикловых графиков могут строиться сетевые, которые также позволяют определитьТц .
По цикловому графику определяются опережения запуска деталей и сборочных единиц в производство, сроки подачи на сборку ведущих деталей, узлов, комплектующих изделий.
Календарные графики разрабатываются в начале по отдельным заказам (упрощенный пример такого графика приведен в табл. 5.1), а затем на основании их составляется общий объемно-календарный график по всему портфелю заказов на данный плановый период и по каждому цеху. При этом необходимо обеспечить такую загрузку всех звеньев производства, чтобы она соответствовала их пропускной способности и была равномерной на протяжении планового периода. Для решения этой задачи производятся
61
объемно-календарные расчеты и строятся соответствующие графики, в которых отражаются взаимная увязка выполнения заказов и загрузка оборудования, площадей, рабочих (табл. 5.1).
Таблица 5.1
Упрощённый календарный график подготовки производства и выполнения заказа
|
|
|
Объем |
|
|
|
|
|
|
|
|
|
|
|
|
|
|
|
|
|
|
|
|
|
|
|
|
|
|
|
|
|
|
|
|
Наименова- |
Исполни- |
работ, |
Январь |
Февраль |
Март |
|
Апрель |
|
|
Май |
|
Июнь |
|||||||||||||||||||||||
ние работы |
тель |
чел. |
|
|
|
|
|
|
|
|
|
|
|
|
|
|
|
|
|
|
|
|
|
|
|
|
|
|
|
|
|
|
|
|
|
|
|
|
дней |
|
|
|
|
|
|
|
|
|
|
|
|
|
|
|
|
|
|
|
|
|
|
|
|
|
|
|
|
|
|
|
|
|
|
|
|
|
I |
II |
|
III |
I |
II |
|
III |
I |
II |
|
III |
I |
|
II |
III |
|
I |
|
II |
III |
|
I |
II |
III |
||||||
|
|
|
|
|
|
|
|
|
|
|
|
|
|
|
|
|
|
|
|
|
|
|
|
|
|
|
|
|
|
|
|
|
|
|
|
Разработка |
Отдел |
|
|
|
|
|
|
|
|
|
|
|
|
|
|
|
|
|
|
|
|
|
|
|
|
|
|
|
|
|
|
|
|
|
|
чертежей |
главного |
430 |
|
|
|
|
|
|
|
|
|
|
|
|
|
|
|
|
|
|
|
|
|
|
|
|
|
|
|
|
|
|
|
|
|
|
_____ |
|
|
|
|
|
|
|
|
|
|
|
|
|
|
|
|
|
|
|
|
|
|
|
|
|
|
|
|||||||
деталей |
|
конструк- |
|
|
|
|
|
|
|
|
|
|
|
|
|
|
|
|
|
|
|
|
|
|
|
|
|
|
|
|
|
||||
|
|
|
|
|
|
|
|
|
|
|
|
|
|
|
|
|
|
|
|
|
|
|
|
|
|
|
|
|
|
|
|
|
|
||
(январь) |
|
тора |
|
|
|
|
|
|
|
|
|
|
|
|
|
|
|
|
|
|
|
|
|
|
|
|
|
|
|
|
|
|
|
|
|
Разработка |
Отдел |
|
|
|
|
|
|
|
|
|
|
|
|
|
|
|
|
|
|
|
|
|
|
|
|
|
|
|
|
|
|
|
|
|
|
сборочных |
главного |
|
|
|
|
|
|
|
|
|
|
|
|
|
|
|
|
|
|
|
|
|
|
|
|
|
|
|
|
|
|
|
|
|
|
чертежей (III |
конструк- |
140 |
|
|
|
|
|
|
|
|
|
|
|
|
|
|
|
|
|
|
|
|
|
|
|
|
|
|
|
|
|
|
|
|
|
|
|
|
|
_________ |
|
|
|
|
|
|
|
|
|
|
|
|
|
|
|
|
|
|
|
|
|
|
|||||||||
декада января, |
тора |
|
|
|
|
|
|
|
|
|
|
|
|
|
|
|
|
|
|
|
|
|
|
|
|
|
|
||||||||
февраль) |
|
|
|
|
|
|
|
|
|
|
|
|
|
|
|
|
|
|
|
|
|
|
|
|
|
|
|
|
|
|
|
|
|
|
|
Разработка |
Отдел |
|
|
|
|
|
|
|
|
|
|
|
|
|
|
|
|
|
|
|
|
|
|
|
|
|
|
|
|
|
|
|
|
|
|
технологии |
главного |
|
|
|
|
|
|
|
|
|
|
|
|
|
|
|
|
|
|
|
|
|
|
|
|
|
|
|
|
|
|
|
|
|
|
(III |
декада |
техноло-га |
154 |
|
|
|
|
|
|
|
|
|
|
|
|
|
|
|
|
|
|
|
|
|
|
|
|
|
|
|
|
|
|
|
|
|
|
|
|
|
|
|
|
|
________ |
|
|
|
|
|
|
|
|
|
|
|
|
|
|
|
|
|
|||||||||
февраля, март) |
|
|
|
|
|
|
|
|
|
|
|
|
|
|
|
|
|
|
|
|
|
|
|
|
|
|
|
|
|||||||
Проектиро- |
|
|
|
|
|
|
|
|
|
|
|
|
|
|
|
|
|
|
|
|
|
|
|
|
|
|
|
|
|
|
|
|
|
|
|
вание |
|
|
|
|
|
|
|
|
|
|
|
|
|
|
|
|
|
|
|
|
|
|
|
|
|
|
|
|
|
|
|
|
|
|
|
оснастки (II и |
Отдел |
232 |
|
|
|
|
|
|
|
|
|
|
|
|
|
|
|
|
|
|
|
|
|
|
|
|
|
|
|
|
|
|
|
|
|
|
|
|
|
|
|
|
|
|
|
|
|
|
|
___ |
|
|
|
|
|
|
|
|
|
|
|
|
|
|
|
||||||
III декады |
главного |
|
|
|
|
|
|
|
|
|
|
|
|
|
|
|
|
|
|
|
|
|
|
|
|
|
|
|
|
|
|
||||
марта, I декада |
технолога |
|
|
|
|
|
|
|
|
|
|
|
|
|
|
|
|
|
|
|
|
|
|
|
|
|
|
|
|
|
|
|
|
|
|
апреля) |
|
|
|
|
|
|
|
|
|
|
|
|
|
|
|
|
|
|
|
|
|
|
|
|
|
|
|
|
|
|
|
|
|
|
|
Изготовление |
Цех |
|
|
|
|
|
|
|
|
|
|
|
|
|
|
|
|
|
|
|
|
|
|
|
|
|
|
|
|
|
|
|
|
|
|
оснастки (II и |
оснастки |
|
|
|
|
|
|
|
|
|
|
|
|
|
|
|
|
|
|
|
|
|
|
|
|
|
|
|
|
|
|
|
|
|
|
III декады |
|
160 |
|
|
|
|
|
|
|
|
|
|
|
|
|
|
|
|
|
|
|
|
|
|
|
|
|
|
|
|
|
|
|
|
|
|
|
|
|
|
|
|
|
|
|
|
|
|
|
|
|
|
|
|
|
_____ |
|
|
|
|
|
|
|
|
|
|
|||||
апреля, I |
|
|
|
|
|
|
|
|
|
|
|
|
|
|
|
|
|
|
|
|
|
|
|
|
|
|
|
|
|
|
|
||||
декада мая) |
|
|
|
|
|
|
|
|
|
|
|
|
|
|
|
|
|
|
|
|
|
|
|
|
|
|
|
|
|
|
|
|
|
|
|
Изготовле-ние |
|
|
|
|
|
|
|
|
|
|
|
|
|
|
|
|
|
|
|
|
|
|
|
|
|
|
|
|
|
|
|
|
|
|
|
деталей (II и |
Цехи 1, 3, |
775 |
|
|
|
|
|
|
|
|
|
|
|
|
|
|
|
|
|
|
|
|
|
|
|
|
|
|
|
|
|
|
|
|
|
|
|
|
|
|
|
|
|
|
|
|
|
|
|
|
|
|
|
|
|
|
|
|
|
___ |
|
|
|
|
|
|
|||||
III декады мая) |
5 |
|
|
|
|
|
|
|
|
|
|
|
|
|
|
|
|
|
|
|
|
|
|
|
|
|
|
|
|
|
|
|
|||
|
|
|
|
|
|
|
|
|
|
|
|
|
|
|
|
|
|
|
|
|
|
|
|
|
|
|
|
|
|
|
|
|
|||
Сборка и |
Сбороч- |
|
|
|
|
|
|
|
|
|
|
|
|
|
|
|
|
|
|
|
|
|
|
|
|
|
|
|
|
|
|
|
|
|
|
испытания |
ный цех |
750 |
|
|
|
|
|
|
|
|
|
|
|
|
|
|
|
|
|
|
|
|
|
|
|
|
|
|
|
|
|
|
|
|
|
|
|
|
|
|
|
|
|
|
|
|
|
|
|
|
|
|
|
|
|
|
|
|
|
|
|
|
|
_____ |
|
||||||
изделия |
|
|
|
|
|
|
|
|
|
|
|
|
|
|
|
|
|
|
|
|
|
|
|
|
|
|
|
|
|
|
|
|
|||
|
|
|
|
|
|
|
|
|
|
|
|
|
|
|
|
|
|
|
|
|
|
|
|
|
|
|
|
|
|
|
|
|
|
|
|
(июнь) |
|
|
|
|
|
|
|
|
|
|
|
|
|
|
|
|
|
|
|
|
|
|
|
|
|
|
|
|
|
|
|
|
|
|
|
В тех случаях, когда пропускная способность недостаточна для параллельной работы над различными изделиями, проводятся мероприятия по расшивке «узких мест» или же делается корректировка сроков выполнения заказов путем сдвига начальных стадий на более раннее время.
62
5.1. Особенности межцехового и внутрицехового ОПП в индивидуальном производстве
К характерным особенностям оперативного планирования в индивидуальном производстве относятся:
−тесная связь подготовки производства изделия (конструкторской, технологической, материально-технической) с планом его изготовления; как правило, система оперативного планирования охватывает весь процесс от подготовки производства до сдачи продукции заказчику;
−сложность обеспечения выполнения всех заказов в установленные сроки при постоянной наиболее полной загрузке оборудования, площадей, рабочих;
−отсутствие (или неполнота) в момент разработки оперативных планов необходимой достаточно технически и экономически обоснованной информации: норм времени, расхода материалов, продолжительности выполнения этапов подготовки производства и т.п.
Особенности межцехового ОПП в индивидуальном производстве
сводятся к следующему:
−распределение годовой производственной программы внутри планового периода осуществляется в соответствии с портфелем заказов, очерёдностью их поступления, сроками их окончания с загрузкой производства;
−отсутствие стабильных КПН на длительный период ввиду неповторяемости заказов. Нормативный характер, в известной мере, имеют цикловые графики и объёмно-календарные расчёты по аналогичным заказам;
−закрепление номенклатуры за производственными подразделениями переменное и зависит от загрузки оборудования, определяемой в результате объёмных расчётов, специализации производственных единиц;
−при ОПП используется позаказная и реже − комплектно-узловая система ОПП;
63
− календарное распределение заданий осуществляется по установленным срокам сдачи (комплектования) по каждому заказу с учётом календарных операций в работе цехов.
Выбор системы и методов оперативно-календарного планирования предопределён особенностями индивидуального производства. Обычно планово-учётной единицей являются заказ, комплект деталей на заказ или же при изготовлении изделий сложных в конструктивно-технологическом отношении с длительными циклами сборки – узловой комплект.
Выбор позаказной или комплектно-узловой системам ОПП определяется длительностью производственного цикла сборки изделий.
Если цикл относительно невелик (в пределах одного месяца), то применяется позаказная система ОПП, при которой все необходимое для сборки комплектуется до начала сборочных работ.
Если цикл сборки превышает месяц, то применяется комплектноузловая система ОПП, при которой всё необходимое для сборки
комплектуется |
в соответствии с последовательностью выполнения |
сборочных работ. |
|
В этом случае на сборку последовательно и в установленные сроки подаются узлы и комплектующие детали.
Для унифицированных и стандартных деталей, применяемых в различных заказах, целесообразно использование подетально-складской системы, при которой рассчитывают три уровня складских запасов − минимальный, максимальный запас в точке заказа.
Минимальный (страховой) запас создаётся для бесперебойного обеспечения производства в случае каких-либо нарушений, приводящих к задержке изготовления очередной партии деталей.
Максимальный запас образуется в тот момент, когда на склад поступает очередная партия изготовленных деталей.
Запас в точке заказа образуется в момент, когда, кроме минимального в запас деталей на складе включается величина, равная суточной потребности в деталях, умноженная на длительность цикла изготовления партии этих деталей.
64
Порядок прохождения заказа
Процесс выполнения заказа состоит из следующих этапов: оформление заказа, подготовка производства заказа, изготовление изделий, входящих в заказ.
Заказ, если он соответствует специализации предприятия и есть основания для его приёма к исполнению (решение вышестоящей организации, прямые производственные связи, план предприятия), регистрируется в Журнале портфеля заказов и на него выписывается так называемый Запросный лист, в который вносятся все данные, связанные с проработкой заказа в различных подразделениях предприятия (табл. 5.2). Затем составляются сметная калькуляция на подготовку производства и изготовление заказа и проект договора. После согласования с заказчиком договора заказу присваивается определённый шифр, который сообщается всем подразделениям-соисполнителям и бухгалтерии, оформляется карта заказа, разрабатываются календарные графики прохождения заказа через различные стадии его подготовки и выполнения.
Внутрицеховое оперативное планирование в условиях индивидуального производства характеризуется тем, что установление заданий для производственных участков по каждой позиции номенклатуры осуществляется путём выборки из оперативного задания цеху с учётом технологических маршрутов и распределением их по цехам. Причём, если цеху в задании регламентированы сроки по ведущим деталям и узлам, то внутри цеха сроки по остальным видам деталей распределяются самостоятельно.
Внутрицеховое планирование в условиях индивидуального производства осуществляется в несколько этапов:
-конкретизация производственной программы цеха и поверка её обеспеченности технической документацией, технологической оснасткой и т.д.;
-разработка производственных программ и графика сдачи продукции участкам цеха;
-составление сменно-суточных заданий, графиков загрузки рабочих мест
иочерёдности выполнения работ участками и рабочими местами и проведение мероприятий по их выполнению;

65
- проведение оперативного учёта состояния производства и хода выполнения производственных заданий.
Таблица 5.2
Оперограмма прохождения запросного листа
Наименование работы |
|
Бюро |
|
|
|
|
|
|
Исполнитель |
|
|
|
|
|
|
|||||
|
|
|
|
|
|
|
|
|
|
|
|
|
|
|
|
|
|
|
|
|
|
заказов |
|
|
|
|
|
|
Отдел труда и з/п |
|
Отдел материаль- но-тех. снабжения |
Производственнодиспетчерский |
Плановоэкономический отдел |
||||||||
|
|
|
|
|
Отдел гл. конструктора |
Отдел гл. технолога |
|
|||||||||||||
|
|
|
|
|
|
|
|
|
|
|
|
|
|
|
|
|
|
|
|
|
Регистрация заказа и |
|
|
|
|
|
|
|
|
|
|
|
|
|
|
|
|
|
|
|
|
|
. |
|
|
|
|
|
|
|
|
|
|
|
|
|
|
|
|
|
|
|
оформление запросного |
|
|
|
|
|
|
|
|
|
|
|
|
|
|
|
|
|
|
|
|
|
|
|
|
|
|
|
|
|
|
|
|
|
|
|
|
|
|
|
|
|
листа |
|
|
|
|
|
|
|
|
|
|
|
|
|
|
|
|
|
|
|
|
|
|
|
|
|
|
|
|
|
|
|
|
|
|
|
|
|
|
|
|
|
|
|
|
|
|
|
|
|
|
|
|
|
|
|
|
|
|
|
|
|
|
Укрупнённый расчёт |
|
|
|
|
|
|
|
|
|
|
|
|
|
|
|
|
|
|
|
|
объёмов и сроков |
|
|
|
|
|
|
|
|
|
|
|
|
|
|
|
|
|
|
|
|
|
|
|
|
|
|
|
|
|
|
|
|
|
|
|
|
|
|
|
|
|
проведения |
|
|
|
|
|
|
|
|
|
|
|
|
|
|
|
|
|
|
|
|
|
|
|
|
|
|
|
|
|
|
|
|
|
|
|
|
|
|
|
|
|
конструкторской |
|
|
|
|
|
|
|
|
|
|
|
|
|
|
|
|
|
|
|
|
|
|
|
|
|
|
|
|
|
|
|
|
|
|
|
|
|
|
|
|
|
подготовки |
|
|
|
|
|
|
|
|
|
|
|
|
|
|
|
|
|
|
|
|
|
|
|
|
|
|
|
|
|
|
|
|
|
|
|
|
|
|
|
|
|
|
|
|
|
|
|
|
|
|
|
|
|
|
|
|
|
|
|
|
|
|
Укрупнённый расчёт |
|
|
|
|
|
|
|
|
|
|
|
|
|
|
|
|
|
|
|
|
объёмов и сроков |
|
|
|
|
|
|
|
|
|
|
|
|
|
|
|
|
|
|
|
|
технологической |
|
|
|
|
|
|
|
|
|
|
|
|
|
|
|
|
|
|
|
|
подготовки |
|
|
|
|
|
|
|
|
|
|
|
|
|
|
|
|
|
|
|
|
|
|
|
|
|
|
|
|
|
|
|
|
|
|
|
|
|
|
|
|
|
|
|
|
|
|
|
|
|
|
|
|
|
|
|
|
|
|
|
|
|
|
Расчёт потребного |
|
|
|
|
|
|
|
|
|
|
|
|
|
|
|
|
|
|
|
|
количества материалов, |
|
|
|
|
|
|
|
|
|
|
|
|
|
|
|
|
|
|
|
|
|
|
|
|
|
|
|
|
|
|
|
|
|
|
|
|
|
|
|
|
|
полуфабрикатов и сроков |
|
|
|
|
|
|
|
|
|
|
|
|
|
|
|
|
|
|
|
|
|
|
|
|
|
|
|
|
|
|
|
|
|
|
|
|
|
|
|
|
|
их поставки |
|
|
|
|
|
|
|
|
|
|
|
|
|
|
|
|
|
|
|
|
|
|
|
|
|
|
|
|
|
|
|
|
|
|
|
|
|
|
|
|
|
|
|
|
|
|
|
|
|
|
|
|
|
|
|
|
|
|
|
|
|
|
Определение трудоёмкости |
|
|
|
|
|
|
|
|
|
|
|
|
|
|
|
|
|
|
|
|
выполнения заказа |
|
|
|
|
|
|
|
|
|
|
|
|
|
|
|
|
|
|
|
|
|
|
|
|
|
|
|
|
|
|
|
|
|
|
|
|
|
|
|
|
|
Разработка |
|
|
|
|
|
|
|
|
|
|
|
|
|
|
|
|
|
|
|
|
ориентировочного плана- |
|
|
|
|
|
|
|
|
|
|
|
|
|
|
|
|
|
|
|
|
графика изготовления |
|
|
|
|
|
|
|
|
|
|
|
|
|
|
|
|
|
|
|
|
заказа |
|
|
|
|
|
|
|
|
|
|
|
|
|
|
|
|
|
|
|
|
|
|
|
|
|
|
|
|
|
|
|
|
|
|
|
|
|
|
|
|
|
Составление плановой |
|
|
|
|
|
|
|
|
|
|
|
|
|
|
|
|
|
|
|
|
калькуляции |
|
|
|
|
|
|
|
|
|
|
|
|
|
|
|
|
|
|
|
|
|
|
|
|
|
|
|
|
|
|
|
|
|
|
|
|
|
|
|
|
|
Оформление результатов |
|
|
|
|
|
|
|
|
|
|
|
|
|
|
|
|
|
|
|
|
проработки заказа |
|
|
|
|
|
|
|
|
|
|
|
|
|
|
|
|
|
|
|
|
|
|
|
|
|
|
|
|
|
|
|
|
|
|
|
|
|
|
|
|
|
- Запросный лист
66
Дальнейшая конкретизация производственной программы становится необходимой при комплектно-групповых системах межцехового планирования, когда программа цеху устанавливается в укрупнённых планово-учётных единица – комплектах.
В индивидуальном производстве основным плановым периодом, на который составляется и задается цеху производственная программа, является месяц. Состав месячной программы определяется методом подбора по портфелю заказов. Из отдельных календарных плановграфиков выбираются номенклатура и сроки работ, соответствующие договорным срокам, учитываются пропускная способность цеха и опережение по запуску-выпуску.
Планово-учетными единицами в сборочных цехах являются изделия или сборочные единицы (узлы) соответствующего наименования. В обрабатывающих и заготовительных цехах — комплект деталей этого цеха на определенный заказ.
Если продолжительность сборочного цикла велика (больше одного месяца), детали в сборочный цех рекомендуется подавать несколькими очередями в виде узловых комплектов применительно к различным этапам выполнения сборочных работ (чтобы не было длительного пролеживания материальных ценностей на протяжении сборочного цикла). В этом случае планово-учетной единицей является узловой комплект, включающий все детали, необходимые для сборки конструктивных узлов на определенном этапе цикла сборки.
Таким образом, в индивидуальном производстве основными системами оперативно-календарного планирования являются позаказная и комплектно-узловая. Кроме того, унифицированные и нормализованные детали изготовляются по системе планирования на склад.
Цех, получив производственную программу, распределяет ее по участкам, при этом проводятся объемные расчеты пропускной способности оборудования (по группам однотипных станков), уточняется потребность в рабочей силе.

67
5.2. Разработка производственных программ цехам и участкам
При предметной форме специализации участков планирование их работы не представляет трудностей. Номенклатура деталей, подлежащих изготовлению в данном месяце, выбирается из месячной оперативной программы цеха.
Для технологически специализированных участков часто не удается оформить месячное задание в подетальном разрезе из-за сложности технологического маршрута изготовления деталей. В этих случаях месячное задание выдается участкам в комплектном или же в трудовом выражении, а календарное подетальное планирование осуществляется по более коротким отрезкам времени (неделям, суткам).
В индивидуальном производстве применяется и сменно-суточное планирование. При этом задания могут разрабатываться как для участков, так и для отдельных рабочих мест. В них уточняется задание на данную смену или сутки по номенклатуре, количеству, срокам, рабочим местам. Уточнения производятся по данным о фактическом выполнении работ за предыдущие сутки. При этом учитываются такие обстоятельства, как ремонт станков, вышедших из строя и т. п.
Наименование |
Количество |
Месячный |
группы |
единиц |
полезный фонд |
оборудования |
|
рабочего |
|
|
времени |
|
|
группы |
|
|
оборудования, |
|
|
ч |
Токарная |
10 |
3840 |
Фрезерная |
6 |
2280 |
Рис. 7. Фрагмент графика загрузки оборудования механического цеха выполнением заказов
(числитель — номер заказа, знаменатель − трудоемкость, станко-ч)
68
Оперативное планирование тесно связано с учетом выработки и движения деталей (изделий) в процессе обработки. Обычно учет осуществляют с помощью нарядов. В наряде указывается содержание работы (номера заказа, детали, количество деталей), условия ее выполнения (разряд работы, норма времени, расценка за единицу), данные о фактическом выполнении. Наряд скрепляется подписями мастера (работа выдана) и контролера (работа принята). По закрытым нарядам судят о продвижении отдельных заказов. В настоящее время на многих предприятиях учет выполненной работы ведется с помощью персональных компьютеров.
Вопросы и задания для самоконтроля
1.Дайте характеристику индивидуального типа организации производства.
2.Какова отличительная особенность ОПП в индивидуальном типе организации производства?
3.Дайте характеристику системы ОПП, применяемые в индивидуальном производстве.
4.Каковы характерные черты ОПП в индивидуальном производстве?
5.Какие календарно-плановые нормативы, используемые в ОПП индивидуального производства?
6.Каковы особенности межцехового ОПП в индивидуальном производстве?
7.Как осуществляется разработка производственной программы цехам и участкам в индивидуальном типе организации производства?
8.Перечислите особенности внутрицехового ОПП в индивидуальном типе организации производства.
69
6. Оперативное планирование в серийном производстве
6.1. Особенности оперативного планирования в серийном производстве
В серийном производстве номенклатура изготовляемых изделий более или менее стабильна и регулярно повторяется в программе выпуска; число выполняемых в цехах детале-операций значительно превышает количество рабочих мест, требующихся для изготовления заданной продукции, что предопределяет необходимость изготовления изделий (деталей) на рабочих местах партиями в порядке чередования с другими изделиями (деталями), изготовляемыми на тех же рабочих местах.
Важнейшей задачей оперативного планирования в этих условиях является установление и обеспечение периодичности изготовления изделий в соответствии с заданием годового плана. В связи с этим ведущее место в оперативном планировании серийного производства принадлежит определению размера партий выпуска изделий, величины партии деталей и периодичности их запуска в обработку. Исходя из установленного размера партии запуска деталей строятся календарные планы-графики работы оборудования, регламентирующие сроки запуска партий в обработку, а также очередность и сроки их прохождения по операциям технологического процесса. Графики различаются степенью детализации и устойчивости.
Стабильность производственной программы, повторяемость изделий в программе выпуска, освоенный технологический процесс позволяют придать календарно-плановым расчетам в условиях серийного производства нормативный характер.
Серийное производство, как указывалось выше, имеет несколько разновидностей (в зависимости от масштабов выпуска изделий, их трудоемкости, степени регулярности повторения в программе выпуска), тяготеющих по своему характеру либо к индивидуальному (мелкосерийное), либо к массовому (крупносерийное) производству. Повышение уровня серийности достигается благодаря унификации дета-
70
лей и узлов, типизации технологических процессов, что является предпосылкой предметной специализации цехов и участков, орга - низации переменно-поточных линий.
6.2. Расчёты календарно-плановых нормативов в серийном производстве
Расчеты календарно-плановых нормативов в серийном производстве включают: определение размера партий изготовления изделий; определение нормативного размера партии деталей и периодичности их изготовления; определение продолжительности производственных циклов обработки партии деталей и календарно-плановых опережений; построение календарных планов-графиков работы производственных участков; расчет заделов.
Партией изделий называется количество единовременно запускаемых на сборку или выпускаемых готовых машин.
Втех случаях, когда при относительно небольшой трудоёмкости объем выпуска отдельных изделий невелик, т. е. исчисляется несколькими штуками, размер партий изделий устанавливают равным годовому заданию. Если же количество одноименных изделий, планируемых к выпуску по годовой программе завода, достаточно велико, то его следует дробить на несколько партий, приурочивая их изготовление к различным кварталам и месяцам на протяжении года. При этом возникает задача определения экономически целесообразного размера партии. Она совпадает, по существу, с задачей распределения годового объема производства каждого вида изделий по месяцам и с требованием наиболее удобного сочетания месячных заданий по разным изделиям для достижения равномерной загрузки парка оборудования и рационального использования трудовых ресурсов. (Подробнее см. раздел 4.2).
Впрактике предприятий эти вопросы зачастую решаются методом эмпирического подбора с проведением некоторых проверочных расчетов, показывающих приемлемость либо нецелесообразность намеченного
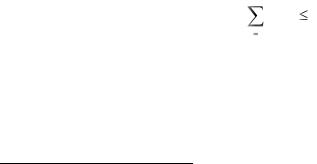
71
варианта календарного плана производства с точки зрения использования оборудования и исходя из других соображений.
Предварительно должна быть произведена классификация номенклатуры выпускаемой продукции по признакам повторяемости: выделены изделия, изготовляемые регулярно в течение каждого месяца планируемого года: изделия с ежеквартальным повторением их производства и, наконец, изделия, производство которых повторяется нерегулярно.
Наиболее целесообразное решение задачи календарного распределения выпуска изделий по месяцам предполагает построение оптимального календарного плана производства с применением математических методов, в частности линейного программирования. Трудоемкость расчетов по оптимизации размеров партий изделий в связи с календарным распределением их выпуска и построением помесячных номенклатурных сочетаний разных изделий требует применения электронно-вычислительных машин.
Формализация задачи равномерного распределения выпуска продукции и равномерной загрузки оборудования может быть показана на следующем схематическом примере1 (следует иметь в виду, что речь идет не о всей продукции, а лишь о той ее части, выпуск которой не распределяется равномерно по месяцам). При решении задачи следует учитывать ряд ограничительных условий:
− выпуск деталей, запланированный в каждом периоде, должен обеспечивать полную (с учётом некоторого допустимого отклонения) загрузку каждой j-й группы оборудования, т.е.
и
tij xik Fjk jk,
i 1
где tij − суммарное необходимое время для изготовления одной штуки i-го изделия по j-му виду оборудования; i = 1,2,3…u, j =
1,2,3…m;
1 См. К. Г. Татевосов. Основы оперативно-производственного планирования на машиностроительном предприятии. М. : Машиностроение, 1965.
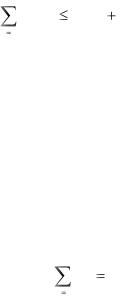
|
|
|
|
72 |
|
|
хik |
− количество штук i-го изделия, планируемое к выпуску в k-м |
|||||
месяце; k = 1.2…р; |
|
|
|
|
||
Fjk |
− |
используемый |
фонд времени |
j-го вида оборудования, за |
||
вычетом времени, необходимого для |
изготовления |
продукции |
||||
равномерно распределяемой по месяцам планируемого периода; |
||||||
jk – заданное допустимое отклонение от равномерности загрузки |
||||||
оборудования в k-м месяце. |
|
|
|
|||
− |
необходимо обеспечить равномерное распределение выпуска в |
|||||
стоимостном выражении |
|
|
|
|
||
|
|
|
и |
|
|
|
|
|
|
Ц i xik |
ПТ .ik |
ПТ .ik , |
|
|
|
|
i 1 |
|
|
|
где Ц i − оптовая цена i-го изделия; |
|
|
||||
ПТ .k |
− |
планируемый |
в k-м |
месяце |
объём выпуска |
товарной |
продукции в оптовых ценах (за вычетом продукции, равномерно распределяемой по месяцам);
− заданное допустимое отклонение от равномерности выпуска в оптовых ценах в k-м месяце.
И наконец третье ограничение описывается следующим равенством:
p
xik N В ,
k 1
где NВ − программа выпуска i-го изделия в плановом периоде. Оптимум в данном примере выражает стремление к максимальной
концентрации выпуска по каждому изделию в одном месяце при соблюдении сформулированных выше ограничений.
Партией деталей называется количество единовременно запускаемых в обработку деталей с однократной затратой подготовительно-заключительного времени.
Определение нормативного размера партии деталей служит следующим задачам:
- регламентации периодичности переналадок оборудования и изготовления одноименных деталей в течение планового периода по отдельным производственным звеньям (участкам, цехам);

73
-расчету нормативной длительности производственных циклов и календарных опережений в работе последовательных производственных звеньев;
-построению календарных планов, определяющих сроки запуска деталей в обработку, их выпуска и комплектования для обеспечения сборки;
-определению нормативного среднего уровня незавершенного производства и величины переходящих заделов на конец планового периода.
В заводских условиях наиболее распространен метод определения целесообразного размера партий путем подбора. Сначала определяют минимально допустимый размер партии, а затем этот размер корректируют, руководствуясь конкретными производственными условиями.
Минимальный размер партии определяется двумя способами в зависимости от характера оборудования, на котором обрабатываются данные детали. Если на производственном участке применяется оборудование, требующее значительного времени на наладку (агрегатные станки, автоматы и полуавтоматы), то в качестве отправного критерия при установлении нормативной величины партии следует принимать такое соотношение между подготовительно-заключительным временем
ивременем обработки партии деталей на ведущих операциях технологического процесса, которое соответствует допустимому проценту потерь на наладку. Ведущей операцией, по которой должен производиться расчет минимального размера партии, следует считать операцию с наибольшим отношением подготовительно-заготовительного времени к штучному времени. Этот расчет производится по формуле
пmin |
tп.з |
|
100 , |
tшт |
|
||
|
об |
где
tш т
об
tп.з − норма подготовительно-заключительного времени;
−норма штучного времени с учётом выполнения норм;
−процент допустимых потерь на переналадку оборудования.

74
Примерные значения процента потерь на наладку в зависимости от себестоимости одной детали и числа операций, закрепленных за рабочим местом, приведены в табл. 6.21.
|
|
|
Таблица 6.2 |
Примерные значения процента потерь на наладку |
|||
|
|
|
|
Себестоимость одной |
Число операций, закреплённых за рабочим |
||
детали, руб. |
|
местом |
|
|
|
|
|
|
до 10 |
от 10 до 20 |
свыше 20 |
|
|
|
|
До 0,2 |
2 |
3 |
5 |
|
|
|
|
0,2 – 1,5 |
3 |
4 |
6 |
|
|
|
|
1,5 – 2,0 |
4 |
5 |
8 |
|
|
|
|
2,0 – 5,0 |
5 |
6 |
9 |
|
|
|
|
Свыше 5,0 |
6 |
8 |
12 |
|
|
|
|
Если на производственном участке применяется оборудование, не требующее значительного времени на наладку, то отправным критерием при установлении нормативной величины партии должна служить непрерывность выполнения каждой операции по меньшей мере в течение смены. Для наиболее производительной операции технологического процесса размер партии должен быть как минимум равен сменной выработке либо (при высокой производительности соответствующего оборудования) полусменной выработке деталей. При этом следует определять продолжительность обработки партии по наиболее трудоемким операциям с тем, чтобы избегать чрезмерного увеличения длительности производственного цикла.
Последующая корректировка минимального размера партии должна привести ее величину в соответствие с потребностью в деталях для выполнения плана производства. Для обеспечения периодического изготовления деталей необходимо, чтобы установленный размер партии
1 Министерство станкостроительной и инструментальной промышленности СССР. «Разработка календарно-плановых нормативов на машиностроительных заводах». НИИ информации по машиностроению. М., 1966.

75
укладывался в объем задания целое число раз или был кратен этой величине.
Такой способ установления нормативной величины партии мо жет применяться в условиях устойчивого серийного производства средних и крупных масштабов.
Периодичность запуска-выпуска деталей в обработку Rз.в опре-
деляется как отношение принятого размера партии п к среднесуточной потребности в данной детали в штуках Nс.д :
Rз.в |
n |
. |
|
||
|
N с.д |
Для упрощения оперативного планирования и регулирования хода производства, а также для создания условий ритмичной работы на каждом производственном участке целесообразно унифицировать полученные значения периодичностей запуска Rз.в и изготовления разных деталей, сведя их к двум-трем вариантам, или же принимать единую периодичность для всех деталей, обрабатываемых на данном участке.
Для укрупненных расчетов можно пользоваться готовыми нормативными таблицами, которые построены путем обобщения большого количества практических данных. Для этого в основу кладутся не непосредственно размеры партий в штуках, а унифицированные периодичности запуска-выпуска.
Рекомендуются следующие унифицированные величины периодичности изготовления деталей: три месяца (ЗМ), один месяц (М), 10 рабочих дней (М/2), 5 рабочих дней (М/4), 2,5 рабочих дня
(М/8).
Размер партий устанавливается при этом исходя из нормативной периодичности запуска-выпуска партий на соответствующем производственном участке, т. е.:
nRз.в. Nс.д. .
Вусловиях мелкосерийного и серийного производства при изго-
товлении изделий небольшими партиями размер партии деталей

76
устанавливается, как правило, соответствующим размеру партии изделий с учетом количества деталей, идущих на одно изделие.
Особенности определения продолжительности производственных циклов в серийном производстве в отличие от индивидуального состоят в следующем:
а) продолжительность цикла устанавливается как длительно действующий расчетный норматив, используемый при оперативном планировании;
б) длительность циклов определяется, как правило, не в отношении
изготовляемой партии |
изделий в целом, а по каждому узлу, |
||||
группе |
деталей |
или |
конкретному |
наименованию |
детали, |
комплектующей соответствующее изделие |
или ряд изделий; |
|
в) установление длительности производственного цикла основывается на расчетной величине нормативного размера партии изготовления деталей (сборки узлов, производства заготовок определённой разновидности), принятой для данного цеха или организационного
подразделения (участка, отделения).
Нормативная продолжительность (в часах) производственного цикла партии деталей рассчитывается по формуле
|
m |
t |
к |
|
t |
м о |
|
|
|
|
, |
|
T (n |
|
m |
|
)K |
|
t |
|
|||
|
|
|
|
|
пар |
e |
|||||
|
ц |
csq |
sq |
|
|
||||||
|
1 |
|
|
|
|
||||||
где n − нормативный размер партии деталей, шт.; |
|||||||||||
m |
− количество операций |
технологического процесса обработки |
|||||||||
партии; |
|
|
|
|
|
|
|
|
|
|
|
tк |
− полная норма времени на операцию, час; |
|
|
|
|||||||
c − число рабочих мест, параллельно занятых выполнением операции; |
|||||||||||
s |
− число рабочих смен в сутках; |
|
|
|
|
|
|
|
|||
q − длительность рабочей смены, час; |
|
|
|
|
|
|
|
||||
t м о − межоперационное время, час; |
|
|
|
|
|
|
|
||||
tе |
− время естественных процессов, час; |
|
|
|
|
Kпар − коэффициент параллельности.
При очень крупных партиях деталей и значительной трудоемкости отдельных операций наиболее длительные из них могут, в виде

77
исключения, выполняться параллельно на двух или большем числе рабочих мест (станков). В этом случае партия деталей фактически делится при выполнении данной операции на несколько частичных партий, обрабатываемых соответствующими станками-дублёрами, а штучное время по этой операции учитывается в формуле с корректировкой на число станков-дублёров.
Нормы среднего межоперационного времени устанавливаются с учетом особенностей производственных участков и характера обрабатываемых деталей. Для этого используется обработка обширных данных статистических наблюдений методом множественной корреляции.
Наиболее точно длительность производственного цикла обработки партии деталей может быть установлена на основании планов-графиков работы производственных участков, которые представляют собой расписание прохождения партий деталей по всем рабочим местам соответственно технологическим процессам. При наличии таких графиков длительность производственного цикла и его структура для каждой партии деталей устанавливается в органическом сочетании с процессами изготовления других партий, обрабатываемых на том же производственном участке, с учетом пропускной способности рабочих мест1.
На основе длительности производственного цикла, рассчитанной по отдельным цехам или производственным участкам, в которых осуществляется обработка соответствующих деталей, устанавливаются планово-календарные опережения.
Планово-календарные опережения используются для определения заданий по запуску в производство партий узлов, деталей и заготовок, сообразно с запланированными сроками монтажной сборки, и выпуска планируемых партий изделий.
В табл. 6.3 представлена схема расчета опережений по детали А-2435- 12, входящей в количестве двух штук в узел А-2435-00. Этот узел входит в изделие А, ежедневный выпуск которого составляет 1 штуку.
1 Подробнее о пооперационных планах-графиках см. ниже, в этом разделе.
78
Таблица 6.3
Схема расчёта опережений и заделов
|
|
|
|
Номера технологических операций |
|
|
1 |
|
|
2 |
|
3 |
|
4 |
|
5 |
|
6 |
|||||||
Монтажная |
сборка |
|
|
|
|
|
|
|
|
|
|
|
|
|
|
|
|
|
|
|
|
|
|
|
|
|
|
Продолжительность операционного |
|
|
2 |
|
|
2 |
|
2 |
|
2 |
|
2 |
|
2 |
|||||||||
|
|
|
|
|
|
|
|
|
|
|
|
||||||||||||||
|
|
|
|
цикла, дн. |
|
|
|
|
|
|
|
|
|
|
|
|
|
|
|
|
|
|
|
|
|
|
|
|
|
|
|
|
|
|
|
|
|
|
|
|
|
|
|
|
|
|
|
|
|
|
|
|
|
|
|
Опережение нарастающим итогом, дн. |
|
|
|
|
|
|
|
|
|
|
|
|
6 |
|
4 |
|
2 |
||||
|
|
|
|
|
|
|
|
|
|
|
|
|
|
|
|
|
|
|
|
|
|
|
|
|
|
|
|
|
|
Опережение нарастающим итогом, шт |
|
|
|
|
|
|
|
|
|
|
|
|
12 |
|
8 |
|
4 |
||||
|
|
|
|
|
|
|
|
|
|
|
|
|
|
|
|
|
|
|
|
|
|
|
|
|
|
|
|
|
|
|
|
|
|
|
|
|
|
|
|
|
|
|
|
|
|
|
|
|
|||
|
|
Номера технологических операций |
|
1 |
|
2 |
|
3 |
|
|
4 |
|
|
5 |
|
6 |
|
7 |
|||||||
сборка |
|
|
|
|
|
|
|
|
|
|
|
|
|
|
|
|
|
|
|
|
|
|
|||
|
|
|
Продолжительность |
|
2 |
|
2 |
|
1 |
|
|
1 |
|
|
2 |
|
1 |
|
2 |
||||||
|
|
|
операционного цикла, дн. |
|
|
|
|
|
|
|
|
|
|
|
|
|
|
|
|
|
|
|
|
|
|
|
|
|
|
|
|
|
|
|
|
|
|
|
|
|
|
|
|
|
|
|
|
|
|
|
|
|
|
|
|
|
|
|
|
|
|
|
|
|
|
|
|
|
|
|
|
|
|
|
|||
Узловая |
|
Опережение нарастающим итогом, |
|
|
|
|
|
|
|
|
|
12 |
|
|
11 |
|
9 |
|
8 |
||||||
|
|
|
дн. |
|
|
|
|
|
|
|
|
|
|
|
|
|
|
|
|
|
|
|
|
|
|
|
|
|
|
|
|
|
|
|
|
|
|
|
|
|
|
|
|
|
|
|
|
|
|
|
|
|
|
|
|
|
|
|
|
|
|
|
|
|
|
|
|
|
|
|
|
|
|
|
|||
|
|
Опережение нарастающим итогом, |
|
|
|
|
|
|
|
|
|
24 |
|
|
22 |
|
18 |
|
16 |
||||||
|
|
|
|
шт. |
|
|
|
|
|
|
|
|
|
|
|
|
|
|
|
|
|
|
|
|
|
|
|
|
|
|
|
|
|
|
|
|
|
|
|
|
|
|
|
|
|
|
|||||
|
|
|
|
|
|
|
|
|
|
|
|
|
|
|
|
|
|
|
|||||||
Механическая |
|
|
|
Номера технологических операций |
|
|
|
|
1 |
|
|
|
2 |
|
3 |
|
4 |
||||||||
сборка |
|
|
|
|
|
|
|
|
|
|
|
|
|
|
|
|
|
||||||||
|
|
Опережение нарастающим итогом, |
шт. |
|
|
|
|
32 |
|
|
30 |
|
28 |
|
26 |
||||||||||
|
|
|
|
Продолжительность операционного цикла, |
|
1 |
|
|
|
1 |
|
1 |
|
1 |
|||||||||||
|
|
|
|
дн. |
|
|
|
|
|
|
|
|
|
|
|
|
|
|
|
|
|
|
|
|
|
|
|
|
|
Опережение нарастающим итогом, дн. |
|
|
|
|
16 |
|
|
15 |
|
14 |
|
13 |
|||||||||
|
|
|
|
|
|
|
|
|
|
|
|
|
|
|
|
|
|
|
|
|
|
||||
|
|
|
|
|
|
|
|
|
|
|
|
|
|
|
|
|
|
|
|
|
|
|
|
|
|
|
|
|
|
|
|
|
|
|
|
|
|
|
|
|
|
|
|
|
|
|
|
||||
Изготовление |
|
|
|
Номера технологических операций |
|
1 |
|
|
2 |
|
|
|
|
|
|
|
|
|
|
|
|
|
|||
заготовки |
|
|
|
|
|
|
|
|
|
|
|
|
|
|
|
|
|
|
|
|
|
|
|||
|
|
Опережение нарастающим итогом |
|
|
40 |
|
|
36 |
|
|
|
|
|
|
|
|
|
|
|
|
|
||||
|
|
|
|
Продолжительность операционного |
|
2 |
|
|
2 |
|
|
|
|
|
|
|
|
|
|
|
|
|
|||
|
|
|
|
цикла, дн. |
|
|
|
|
|
|
|
|
|
|
|
|
|
|
|
|
|
|
|
|
|
|
|
|
Опережение нарастающим итогом, дн. |
|
20 |
|
|
18 |
|
|
|
|
|
|
|
|
|
|
|
|
|
||||
|
|
|
|
|
|
|
|
|
|
|
|
|
|
|
|
|
|
|
|
|
|
|
|
|
|
|
|
|
|
|
|
|
|
|
|
|
|
|
|
|
|
|
|
|
|
|
|
|
|
|
|
Как видно из табл. 6.3, узел, в который входит деталь, поступает на общую сборку на четвертую операцию с опережением в 6 дней до выпуска изделия. Деталь включается в узловую сборку на четвертой операции с опережением в 12 дней до выпуска изделия. С учетом механической обработки и изготовления заготовки опережение в запуске детали составляет 20 дней.
Для обеспечения непрерывности работы на предприятии, участках и рабочих местах в серийном производстве создаются заделы.

79
Заделы в серийном производстве принято различать по месту их образования на две взаимосвязанные разновидности:
-цикловые заделы, которые включают партии узлов, деталей или заготовок, запущенные в производство, но еще не законченные обработкой на той или иной технологической стадии и находящиеся в цехах на производственных участках;
-складские межцеховые заделы в составе уже изготовленных заготовок, деталей или узлов, ожидающие дальнейшей обработки на последующей стадии производства или постепенно потребляемые в порядке комплектования узловой либо монтажной сборки.
При расчетах заделов в серийном производстве устанавливаются, как правило, следующие планово-нормативные показатели:
-средний размер заделов;
-переходящий нормативный размер заделов на конец (и на начало) планового периода при установлении подетальных оперативных производственных заданий цехам и производственным участкам и при
определении календарных сроков запуска очередных партий деталей в обработку.
Расчёт цикловых заделов выражается в определении количества партий одноименных деталей, которые должны находиться в процессе обработки в каждый данный момент времени.
Средняя величина нормативного циклового задела Z4 устанавливается по формуле
Zц Tw Nс.д.сб ,
где Т ц − длительность производственного цикла изготовления;
N с.д.сб − среднесуточная потребность сборки в этих деталях.
При наличии календарных графиков работы производственных участков нормативный уровень цикловых заделов на любую дату определяется непосредственно из графика.
Складские заделы деталей представляют собой переменную величину и состоят из оборотного и страхового заделов. Минимальный складской задел устанавливается с учетом необходимости некоторого резерва на случай возможного опоздания изготовления очередной партии. Эта часть

80
складского задела называется страховым заделом. Она устанавливается на основе опытных данных относительно фактических отклонений в сроках изготовления партий деталей от строгой нормативной периодичности их обработки в условиях данного цеха или производственного участка.
Максимальный складской задел (Zmax) представляет собой сумму страховой и оборотной части в момент поступления очередной партии деталей, т. е.
Zmax ni Zст р ,
где Zст р − страховой задел i-й детали;
ni − размер партии ее изготовления,
Переходящий складской задел заготовок перед обрабатывающими цехами при непрерывности потребления определяется так же, как и переходящий задел деталей перед сборкой.
При производстве заготовок и обработке деталей партиями размер переходящего задела зависит от размера партии в заготовительных и обрабатывающих цехах, а также от сроков запуска-выпуска этих партий. Если размер партии заготовок превышает размер партии в механической обработке, то величина переходящего задела на складе заготовок устанавливается исходя из срока выпуска последней партии заготовок в истекшем месяце и также срока запуска деталей в обработку. Она рассчитывается как разность между размером последней партии заготовок, выпущенной перед первым числом, и количеством деталей, поданных на обработку за то же время.
6.3. Построение календарных планов-графиков работы участков серийного производства
Построение календарных планов-графиков работы участков серийного производства деталей осуществляется различными методами в зависимости от условий, характеризующих работу различных производственных участков, а именно:
- от количества детале-операций, закреплённых в среднем за одним станком;
81
- от степени устойчивости номенклатуры изготавливаемых деталей и периодичности их обработки, которая определяется, в первую очередь, характером организации сборочных процессов (непрерывная сборка и выпуск изделий, строго периодическая сборка и выпуск изделий партиями, повторяющийся выпуск партий изделий с нерегулярной периодичностью).
Всоответствии с этими условиями различают следующие варианты построения календарных планов-графиков работы производственных участков:
− планы-графики работы переменно-поточных линий,
регламентирующие периодичность запуска деталей в обработку и соответственно сроки переналадки линии с одного объекта на другой;
− пооперационный стандартный план-график для производственных участков, обрабатывающих детали партиями для непрерывной сборки изделий при небольшом числе детале-операций, обрабатываемых на одном рабочем месте (до 5 − 6 детале-операций);
− стандартный план-график запуска-выпуска партий деталей с
периодической повторяемостью применительно к непрерывной или строго периодической строго периодической сборке готовых изделий и при условии, что за каждым рабочим местом закреплено более 6 деталеопераций;.
− календарный план-график сроков подачи деталей на сборку и их запуска на первую операцию применительно к серийному производству без строгой периодичности выпуска изделий.
Воснову построения планов-графиков работы производственных участков должны быть положены следующие данные:
а) технологические маршруты обработки деталей с указанием выполняемых операций, применяемого оборудования и норм времени на обработку одной детали (с учетом планового процента выполнения норм);
б) закрепление детале-операций за станками;
в) размеры месячного производственного задания по детали каждого наименования, нормативные значения размеров партий и периодичности их запуска в обработку.
82
6.4. Системы межцехового планирования и разработка производственных программ цеха
В условиях серийного производства в зависимости от особенностей его отдельных разновидностей находят применение следующие системы планирования: групповая, или система планирования по цикловым комплектам, система планирования по комплектовочным номерам и система планирования по заделам (удачной разновидностью которой является система непрерывного оперативного планирования, впервые применённая на Новочеркасском электровозостроительном заводе).
Сущность и особенность каждой из указанных систем приведены в разделе 3.
Вместе с тем необходимо подробнее остановиться на системе непрерывного оперативного производственного планирования, которая принципиально отличается от остальных систем, применяемых в серийном производстве.
6.4.1. Система непрерывного оперативно-производственного планирования (НОПП)
Особенность системы НОПП заключается в том, что она предусматривает создание постоянной насыщенности всех стадий производственного процесса заделами полуфабрикатов, деталей и узлов разной степени готовности и строгое соблюдение установленного расчетного уровня неснижаемой части этих заделов по каждой детали (заготовке) применительно к каждому цеху.
Эта система нашла успешное применение и развитие на Новочеркасском электровозостроительном заводе (НЭВЗ) и используется (подвергаясь различным модификациям) на многих машиностроительных предприятиях.
Система НОПП предусматривает следующие основные элементы:
1. Устанавливается ведущее изделие — условный представитель, т. е. изделие, которое преобладает в производственной программе завода и постоянно изготовляется на протяжении всех месяцев планируемого периода примерно в одинаковых количествах. Все остальные детали и

83
изделия как бы условно комплектуют это изделие. На этой основе производится расчет условного комплекта деталей на изделие-представитель. Пример определения условного количества деталей «А» на изделиепредставитель электровоз ВЛ-60 приведен в табл. 6.4
Таблица 6.4
Определение состава условного изделия
Наименова- |
Наименование |
Квартальный |
Количество |
Квартальный |
Условное |
|||
ние детали |
изделий |
план |
деталей на |
план |
количество |
|||
(чертёж) № |
|
выпуска |
изделие, |
выпуска |
|
деталей, |
||
|
|
изделий, шт. |
шт. |
деталей, шт. |
|
шт. |
|
|
«А» № |
ВЛ-60 |
100 |
2 |
200 |
|
|
|
|
181400 |
ВЛ-8 |
40 |
10 |
400 |
900 |
|
9 |
|
|
ВЛ-23 |
25 |
4 |
100 |
|
|
|
|
|
100 |
|
||||||
|
|
|
||||||
|
На сторону |
|
|
200 |
|
|
||
|
|
|
|
|
|
|
При изменении программы должна быть произведена корректировка
условного комплекта. |
|
|
|
Следующий важный этап оперативного |
планирования |
по |
этой |
системе − расчет необходимых опережений |
по каждой |
детали |
по |
всем технологическим переделам и определение на этой основе неснижаемого размера заделов, который должен насытить весь производственный поток.
Методика расчёта опережений и заделов приведена в разделе 4.
Расчет произведен исходя из данных о длительности операционных циклов в днях и суточной потребности в деталях. Так, если длительность шестой операции монтажной сборки составляет 2 дня, а дневная потребность
вдеталях 2 штуки, то задел на этой операции должен быть равен 4 деталям. Рассчитанная таким образом нормальная насыщенность производственного потока заделом по этой детали должна составлять 40 шт. и ниже этого количества задел снижаться не может без риска нарушить бесперебойность процесса.
При системе НОПП этот задел в 40 шт. для упрощения как бы «снимается» с учета, поскольку он является обязательным и неснижаемым. Это дает возможность устанавливать единый календарный график-задание
вусловных машино-комплектах для всех цехов (см. рис. 8), не дифференцируя задания согласно календарным опережениям.

84
Октябрь
1 |
2 |
3 |
4 |
5 |
6 |
8 |
9 |
10 |
11 |
12 |
13 |
15 |
16 |
17 |
18 |
19 |
20 |
22 |
23 |
24 |
25 |
26 |
27 |
29 |
31 |
|
|
|
|
|
|
|
|
|
|
|
|
|
|
|
|
|
|
|
|
|
|
|
|
|
|
789 |
790 |
792 |
793 |
795 |
796 |
798 |
799 |
801 |
802 |
803 |
805 |
806 |
807 |
809 |
810 |
812 |
813 |
814 |
816 |
817 |
818 |
820 |
821 |
823 |
825 |
|
|
|
|
|
|
|
|
|
|
|
|
|
|
|
|
|
|
|
|
|
|
|
|
|
|
Ноябрь
1 |
2 |
3 |
5 |
6 |
9 |
10 |
12 |
13 |
14 |
15 |
16 |
17 |
19 |
20 |
21 |
22 |
23 |
24 |
26 |
27 |
28 |
29 |
30 |
|
|
|
|
|
|
|
|
|
|
|
|
|
|
|
|
|
|
|
|
|
|
|
|
|
|
826 |
827 |
829 |
830 |
832 |
833 |
835 |
836 |
838 |
839 |
841 |
842 |
843 |
845 |
846 |
848 |
849 |
851 |
852 |
854 |
855 |
857 |
858 |
850 |
|
|
|
|
|
|
|
|
|
|
|
|
|
|
|
|
|
|
|
|
|
|
|
|
|
|
Декабрь
1 |
3 |
4 |
6 |
7 |
8 |
10 |
11 |
12 |
13 |
14 |
15 |
17 |
18 |
19 |
20 |
21 |
22 |
24 |
25 |
26 |
27 |
28 |
29 |
30 |
|
|
|
|
|
|
|
|
|
|
|
|
|
|
|
|
|
|
|
|
|
|
|
|
|
|
|
|
|
861 |
862 |
864 |
865 |
867 |
868 |
870 |
871 |
872 |
874 |
875 |
877 |
878 |
880 |
881 |
883 |
884 |
885 |
887 |
888 |
890 |
891 |
893 |
894 |
896 |
|
|
|
|
|
|
|
|
|
|
|
|
|
|
|
|
|
|
|
|
|
|
|
|
|
|
|
|
|
Рис. 8. Единый график выпуска изделий

85
Оперативный учет хода комплектации по каждой детали осуществляется следующим образом: на определенную дату путем инвентаризации устанавливается фактический задел, из него вычитается нормативный. Разность показывает, какое количество деталей может пойти на комплектацию выпуска. Путем деления этого количества на количество данных деталей, идущих на один условный машино-комплект, определяется номер изделия, обеспеченный данной деталью.
Для оперативного учета хода комплектации используются различного рода картотеки, в частности,— по опыту НЭВЗа — удобным вариантом является «картотека пропорциональности». Картотека представляет собой шкаф, разделенный по горизонтали на три секции, каждая из которых отводится соответствующему месяцу квартала. Секции разделены по вертикали на ячейки по числу рабочих дней в месяце. Над каждой ячейкой указаны календарная дата и номер изделия, подлежащий выпуску в этот день по графику. В ячейках секций раскладываются учетные карточки, заведенные на каждую деталь. Они помещаются в тех секциях, которые соответствуют номеру изделия, укомплектованному данной деталью. По мере изготовления деталей они перемещаются в ячейку соответствующего номера. Все карточки, находящиеся в ячейках влево от сегодняшнего дня, относятся к отстающим деталям. Таким образом, размещение карточек деталей в картотеке дает отсортированную информацию о состоянии производства на каждый день.
Для того чтобы ежедневно иметь информацию о выполнении каждым цехом плана по комплектации выпуска изделий, используется график по образцу, приведенному на рис. 91. На основании данных картотеки пропорциональности для каждого цеха определяется, по какой номер цех полностью укомплектовал своей продукцией выпуск конечных изделий. Об этом свидетельствует стрелка на графике (см. рис. 9), устанавливаемая против соответствующего дня и номер изделия. Отставание от графика оценивается в условных единицах «наименованиях-днях». Наименованиедень соответствует отставанию одной детали на один день.
1 В соответствии с практикой НЭВЗа подобные графики получили название «графиков пропорциональности».
86
Условиями применения этой системы оперативного планирования являются значительный объем и достаточная устойчивость выпуска продукции, что дает возможность не подвергать частой корректировке расчет условного комплекта и экономически оправдывает неснижаемый уровень задела по каждой детали по каждому технологическому переделу.
При дальнейшем увеличении объема выпуска, в условиях поточной сборки изделий и партионного изготовления деталей, что характерно для крупносерийного производства, согласованная работа производственных звеньев достигается путем установления и постоянного соблюдения четкой периодичности изготовления заготовок, деталей и узлов партиями по стандартным календарным расписаниям.
6.4.2. Внутрицеховое планирование в серийном производстве
Конкретные формы и методы организации внутрицехового оперативного планирования зависят от особенностей серийного производства в данном цехе (степени устойчивости условий работы, регулярности повторения партий и др.).
Вцехах крупносерийного производства производственные задания участкам доводятся в виде пооперационных планов-графиков, регламентирующих размер партий, очередность их запуска и сроки прохождения по операциям технологического процесса. Эти графики уточняют нормативные календарные графики соответственно фактическому состоянию производства на участке к началу планового периода. На их основе могут быть составлены календарные планы-графики для каждого рабочего места.
Вусловиях серийного производства исходными данными для составления заданий участкам служат планы-графики запуска и выпуска
групповых комплектов при системе планирования по цикловым

87
|
|
ГРАФИК ПРОПОРЦИОНАЛЬНОСТИ НА |
|
|
|
|
|
|
|
|
|
|
|
|
|
|
|
|
|
|
|
|
|
|
|
˙ |
0 |
|
2 |
|
|
|
|
|
|
|
|||||||||||||||||
|
|
|
|
|
|
|
|
|
|
|
|
|
|
|
|
|
|
|
|
|
|
|
|
|
|
|
|
|
|
|
|
|
|
|
|
|
|
|
|
|
|
|
|
|
|
|
|
|
|
|
|
|
|
Месяц |
|
|
|
|
|
|
|
|
|
|
|
|
|
|
|
|
|
|
ФЕВРАЛЬ |
|
|
|
|
|
|
|
|
|
|
|
|
|
|
|
|
|
|
|
|
|
|
|
Показатель |
|
|||||||||
число |
1 |
|
2 |
3 |
5 |
6 |
7 |
8 |
|
9 |
10 |
12 |
|
13 |
14 |
15 |
|
|
|
16 |
17 |
19 |
|
20 |
|
|
21 |
22 |
|
|
23 |
24 |
26 |
27 |
|
28 |
|
|
|
|
отставания |
|
|||||||||||
номер |
518 |
519 |
520 |
521 |
522 |
523 |
524 |
525 |
526 |
527 |
|
528 |
529 |
530 |
|
|
531 |
532 |
533 |
|
534 |
|
535 |
536 |
|
537 |
538 |
539 |
540 |
|
541 |
|
|
|
в наим-днях |
|
|||||||||||||||||
электровоза |
|
|
|
|
|
|
|
|
|
|
|
|
|
|
|
|
|||||||||||||||||||||||||||||||||||||
|
|
|
|
|
|
|
|
|
|
|
|
|
|
|
|
|
|
|
|
|
|
|
|
|
|
|
|
|
|
|
|
|
|
|
|
|
|
|
|
|
|
|
|
|
|
|
|
|
|
|
|
|
|
ЦЕХИ: |
|
|
|
|
|
|
|
|
|
|
|
|
|
|
|
|
|
|
|
|
|
|
|
|
|
|
|
|
|
|
|
|
|
|
|
|
|
|
|
|
|
|
|
|
|
|
|
|
|
|
|
|
|
сталелитейный |
|
_____________________________________________________________________________________________ |
|
|
|
|
|
|
|
|
|
|
|
|
|
|
|
|
|
|
˙ |
˙ |
˙ |
3 |
|
7 |
|||||||||||||||||||||||||||
|
|
|
|
|
|
|
|
|
|
|
|
|
|
|
|
|
|
|
|
|
|
|
|
|
|
|
|
|
|
|
|
|
|
|
|
|
|
|
|
|
|
|
|
|
|
|
|
||||||
чугунолитейный |
|
_______________________________________________________________________ |
|
|
|
|
|
|
|
|
|
|
|
|
|
|
|
|
|
|
|
|
|
|
|
|
|
|
|
˙ |
˙ |
2 |
1 |
|
9 |
||||||||||||||||||
|
|
|
|
|
|
|
|
|
|
|
|
|
|
|
|
|
|
|
|
|
|
|
|
|
|
|
|
|
|
|
|
|
|
|
|
|
|
|
|
|
|
|
|
|
|
|
|
|
|
|
|
||
крепёжный |
|
____________ |
|
|
|
|
|
|
|
|
|
|
|
|
|
|
|
|
|
|
|
|
|
|
|
|
|
|
|
|
|
|
|
|
|
|
|
|
|
|
|
|
|
|
˙ |
5 |
5 |
9 |
|
1 |
|||
|
|
|
|
|
|
|
|
|
|
|
|
|
|
|
|
|
|
|
|
|
|
|
|
|
|
|
|
|
|
|
|
|
|
|
|
|
|
|
|
|
|
|
|
|
|
|
|
|
|
|
|||
кузнечный |
|
____________ |
|
|
|
|
|
|
|
|
|
|
|
|
|
|
|
|
|
|
|
|
|
|
|
|
|
|
|
|
|
|
|
|
|
|
|
|
|
|
|
|
|
|
˙ |
2 |
0 |
6 |
|
8 |
|||
|
|
|
|
|
|
|
|
|
|
|
|
|
|
|
|
|
|
|
|
|
|
|
|
|
|
|
|
|
|
|
|
|
|
|
|
|
|
|
|
|
|
|
|
|
|
|
|
|
|
|
|||
модельный |
|
____________ |
|
|
|
|
|
|
|
|
|
|
|
|
|
|
|
|
|
|
|
|
|
|
|
|
|
|
|
|
|
|
|
|
|
|
|
|
|
|
|
|
|
|
˙ |
˙ |
4 |
6 |
|
9 |
|||
|
|
|
|
|
|
|
|
|
|
|
|
|
|
|
|
|
|
|
|
|
|
|
|
|
|
|
|
|
|
|
|
|
|
|
|
|
|
|
|
|
|
|
|
|
|
|
|
|
|
|
|
|
|
обмоточный |
|
_______________________________________ |
|
|
|
|
|
|
|
|
|
|
|
|
|
|
|
|
|
|
|
|
|
|
|
|
|
|
|
|
|
|
|
|
|
|
|
|
|
|
|
1 |
3 |
1 |
|
0 |
|||||||
|
|
|
|
|
|
|
|
|
|
|
|
|
|
|
|
|
|
|
|
|
|
|
|
|
|
|
|
|
|
|
|
|
|
|
|
|
|
|
|
|
|
|
|
|
|
|
|
|
|
|
|
|
|
кузовной |
|
_____________________________________________________________________________________________ |
|
|
|
|
|
|
|
|
|
|
|
|
|
|
|
|
|
|
˙ |
˙ |
5 |
6 |
|
1 |
|||||||||||||||||||||||||||
|
|
|
|
|
|
|
|
|
|
|
|
|
|
|
|
|
|
|
|
|
|
|
|
|
|
|
|
|
|
|
|
|
|
|
|||||||||||||||||||
тележечный |
|
_____________________________________________________________________________ |
|
|
|
|
|
|
|
|
|
|
|
|
|
|
|
|
|
|
|
|
|
|
|
|
|
|
2 |
4 |
|
2 |
|||||||||||||||||||||
|
|
|
|
|
|
|
|
|
|
|
|
|
|
|
|
|
|
|
|
|
|
|
|
|
|
|
|
|
|
|
|
|
|
|
|
|
|
|
|
|
|
|
|
|
|||||||||
аппаратный |
|
_______________________________________ |
|
|
|
|
|
|
|
|
|
|
|
|
|
|
|
|
|
|
|
|
|
|
|
|
|
|
|
|
|
|
|
|
|
|
|
|
˙ |
|
6 |
5 |
|
4 |
|||||||||
|
|
|
|
|
|
|
|
|
|
|
|
|
|
|
|
|
|
|
|
|
|
|
|
|
|
|
|
|
|
|
|
|
|
|
|
|
|
|
|
|
|
|
|
|
|
|
|
|
|
|
|
|
|
пантографный |
|
_____________________________________________________________________________________________________________ |
|
|
|
|
|
|
|
|
|
|
|
˙ |
˙ |
1 |
3 |
|
8 |
||||||||||||||||||||||||||||||||||
|
|
|
|
|
|
|
|
|
|
|
|
|
|
|
|
|
|
|
|
|
|
|
|
|
|
|
|
|
|
|
|
|
|
|
|
|
|
|
|
|
|
|
|
|
|
|
|
|
|
||||
машинный-53 |
|
____________ |
|
|
|
|
|
|
|
|
|
|
|
|
|
|
|
|
|
|
|
|
|
|
|
|
|
|
|
|
|
|
|
|
|
|
|
|
|
|
|
|
|
|
1 |
0 |
6 |
8 |
|
9 |
|||
|
|
|
|
|
|
|
|
|
|
|
|
|
|
|
|
|
|
|
|
|
|
|
|
|
|
|
|
|
|
|
|
|
|
|
|
|
|
|
|
|
|
|
|
|
|
|
|
|
|
|
|
|
|
машинный-54 |
|
_______________________________________ |
|
|
|
|
|
|
|
|
|
|
|
|
|
|
|
|
|
|
|
|
|
|
|
|
|
|
|
|
|
|
|
|
|
|
|
|
˙ |
˙ |
˙ |
9 |
|
9 |
|||||||||
|
|
|
|
|
|
|
|
|
|
|
|
|
|
|
|
|
|
|
|
|
|
|
|
|
|
|
|
|
|
|
|
|
|
|
|
|
|
|
|
|
|
|
|
|
|
|
|
|
|
||||
Сборочный |
|
|
___________ |
|
|
|
|
|
|
|
|
|
|
|
|
|
|
|
|
|
|
|
|
|
|
|
|
|
|
|
|
|
|
|
|
|
|
|
|
|
|
|
|
|
|
|
|
|
|
|
|
||
|
|
|
|
|
|
|
|
|
|
|
|
|
|
|
|
|
|
|
|
|
|
|
|
|
|
|
|
|
|
|
|
|
|
|
|
|
|
|
|
|
|
|
|
|
|
|
|
|
|
|
|
|
|
ОКиК |
|
_______________________________________ |
|
|
|
|
|
|
|
|
|
|
|
|
|
|
|
|
|
|
|
|
|
|
|
|
|
|
|
|
|
|
|
|
|
|
|
|
˙ |
˙ |
˙ |
˙ |
˙ |
||||||||||
|
|
|
|
|
|
|
|
|
|
|
|
|
|
|
|
|
|
|
|
|
|
|
|
|
|
|
|
|
|
|
|
|
|
|
|
|
|
|
|
|
|
|
|
|
|
|
|
|
|
||||
ОТС |
|
____________ |
|
|
|
|
|
|
|
|
|
|
|
|
|
|
|
|
|
|
|
|
|
|
|
|
|
|
|
|
|
|
|
|
|
|
|
|
|
|
|
|
|
|
|
|
|
|
|
|
|||
|
|
|
|
|
|
|
|
|
|
|
|
|
|
|
|
|
|
|
|
|
|
|
|
|
|
|
|
|
|
|
|
|
|
|
|
|
|
|
|
|
|
|
|
|
|
|
|
|
|
|
|
|
|
ИТОГО |
|
|
|
|
|
|
|
|
|
|
|
|
|
|
|
|
|
|
|
|
|
|
|
|
|
|
|
|
|
|
|
|
|
|
|
|
|
|
|
|
|
|
|
|
|
|
|
2 |
2 |
0 |
7 |
|
7 |
Рисунок 9. - График пропорциональности
88
комплектам или установленные сроки выпуска машинокомплектов при системе планирования по комплектовочным номерам. Планы работы участков представляют собой календарные планы запуска-выпуска партий деталей, закрепленных за данным производственным участком и входящих в групповые комплекты или машинокомплекты, предусмотренные месячным планом.
На производственных участках разрабатываются подетальнопооперационные графики обработки деталей, и в них же обычно делается отметка о выполнении операций. Доведение заданий до рабочих может быть оформлено в виде выписки из таких подетально-пооперационных графиков. Для повышения качества работы и сокращения ее трудоемкости разработка подетально-пооперационных планов-графиков и заданий для отдельных рабочих мест должна быть механизирована.
При системе планирования по заделам, в частности на Новочеркасском электровозостроительном заводе, во внутрицеховом планировании применяются участковые картотеки, в которых отражается движение деталей по операциям и укомплектованность выпуска деталями, обрабатываемыми на участке.
Для текущей корректировки хода производства и доведения заданий до исполнителей на каждые предстоящие сутки в цехах серийного производства разрабатываются сменно-суточные планы. Они являются также основой для проведения всей работы по оперативной подготовке производства. В условиях крупносерийного производства сменные задания составляются преимущественно в виде сменного задания-рапорта (Приложение 1. Форма 5). При их составлении необходимо следить, чтобы строго выдерживался регламент изготовления деталей, предусмотренный пооперационными стандарт-планами.
6.5. Оперативный учёт выработки и движения деталей
Оперативный учёт выработки и движения деталей осуществляется при помощи маршрутных листов. Маршрутный лист (Приложение 2. Форма 6) выписывается на партию деталей и сопровождает её по всем операциям
89
технологического процесса вплоть до сдачи готовых деталей на склад. В маршрутном листе фиксируются результаты приёмки деталей ОТК и отражается баланс количества деталей на каждой операции. Применение маршрутной системы обеспечивает:
−контроль за соблюдением технологической дисциплины;
−контроль за сохранностью партий деталей в производстве;
−учёт движения деталей в производстве;
−уменьшение числа первичных документов и простоту их оформления. Выписку маршрутных листов целесообразно производить
централизованно в производственно-диспетчерском отделе (ПДО) завода. Это позволяет создать благоприятные условия для организации их механизированной подготовки и обеспечивать контроль со стороны ПДО завода за запуском партий в производство. Оперограмма движения маршрутного листа, показывающая его роль в улучшении оперативной подготовки производства, показана в приложении 3.
Маршрутные листы хранятся на участке в соответствующих ячейках распределительно-контрольной доски или картотеки. С её помощью планировщик всегда имеет представление о подготовленном портфеле работ и о работах, выполняемых на каждом рабочем месте.
Сменное задание-рапорт является как плановым, так и учётным документом и используется в следующих целях:
-составление сменного задания и учёт его выполнения участком;
-оперативная подготовка всего необходимого для выполнения сменного задания;
-учёт результатов количественной и качественной приёмки ОТК выработки рабочих;
-начисление рабочим заработной платы в соответствии с количеством
икачеством выполненных работ.
Вопросы и задания для самоконтроля
1. Дайте характеристику серийного типа организации производства.
90
2.Охарактеризуйте базовые ОПП, применяемые в серийном производстве.
3.Какие календарно-плановые нормативы используются в ОПП серийного производства?
4.Каковы особенности межцехового ОПП на предприятиях серийного типа организации производства?
5.Назовите виды календарных планов-графиков, используемые в межцеховом ОПП серийного производства.
6.Как осуществляется разработка производственных программ цехов на предприятиях серийного типа организации производства?
7.Определите сущность системы непрерывного оперативнопроизводственного планирования (НОПП).
8.Какие планово-учётные единицы применяются в НОПП?
9.Назовите основные элементы системы НОПП.
10.Какова роль единого сквозного графика сдачи продукции в системе НОПП?
11.Раскройте возможности картотеки пропорциональности в системе НОПП.
12.Каково назначение графика пропорциональности в системе НОПП?
13.Раскройте преимущества системы НОПП.
14.Каковы особенности внутрицехового ОПП в серийном производстве?
15.Как осуществляется оперативный учёт на предприятии серийного типа организации производства?
7.Оперативное планирование в массовом производстве
7.1. Особенности оперативного планирования в массовом производстве
Массовое производство характеризуется изготовлением ограниченной и устойчивой в течение длительного периода номенклатуры изделий, относительно постоянным суточным темпом выпуска готовой продукции, узкой специализацией рабочих мест.
91
Массовое производство организуется по поточному методу характеризующемуся строгой ритмичностью в работе всех производственных подразделений.
Поэтому основное требование, которое предъявляется к оперативнопроизводственному планированию в массовом производстве, – обеспечить непрерывность и ритмичность всех элементов процесса.
Движение предметов труда по операциям организуется на основе предварительных тщательных расчётов плана работ по каждой поточномассовой линии. Основные вопросы регламентации движения предметов рассмотрены при изучении поточного производства.
ОПП массового производства отличается рядом особенностей:
−календарно-плановые расчёты массового производства тесно связаны
сорганизационными мероприятиями по обеспечению беспеременной и ритмичной работы на всех операциях производственного процесса применительно к единой расчётной величине – такту выпуска предприятия;
−значительная часть календарно-плановых нормативов массового производства имеет весьма устойчивый характер и непосредственно
закладывается в основу планового регламента работы участков и линий;
−работа по текущему планированию в этих условиях сводится лишь к корректировке фактического хода производства применительно к нормативному распорядку.
Указанные особенности ОПП массового производства создают условия для применения централизованной системы ОПП и управления производством, имеющей в этих условиях значительные преимущества (чёткость, гибкость, действенность, сокращение звеньев управления и сокращение расходов на его содержание).
В свою очередь, централизация ОПП в массовом производстве позволяет широко и наиболее успешно применять механизацию и автоматизацию планово-расчётных и учётно-контрольных функций, использовать персональные компьютеры. ОПП в массовом производстве базируется на календарно-плановых нормативах:
−расчёт такта и ритма выпуска деталей изделий;
92
−нормальные графики работы участков и линий;
−нормативы внутрилинейных или цикловых заделов (межоперационные, транспортный, технологический и страховой);
−нормативы межлинейных и межцеховых заделов.
На основе календарно-плановых нормативов и в соответствии с заданием вышестоящих организаций и хоздоговорами составляются годовые, квартальные и месячные подетальные (поузловые и поиздельные для сборочных цехов) производственные программы и планы-графики на короткие отрезки времени по заводу, цехам и участкам.
Методы и формы ОП массового производства, учитывающие особенности конкретного предприятия, основываются на 3 основных моментах:
1)наличие заранее разработанной технической документации (точно регламентирующей технологию);
2)наличие расходных подетальных и пооперационных норм затрат труда и материалов на продукцию, отпускающую предприятием;
3)система календарно-плановых нормативов.
Важным условием непрерывного и ритмичного выпуска продукции на предприятии массового производства и организации на нём ОПП является наличие необходимых заделов на тех операциях, где это вызвано производственной необходимостью. Аналогично рассмотрению вопросов в условиях индивидуального и серийного производства, рассмотрим организацию ОПП в массовом производстве.
7.2. Межцеховое оперативно-производственное планирование
Задачей межцехового оперативного планирования в условиях массового производства является обеспечение установленного ритма главного конвейера и всех поточных линий, строгой согласованности в их работе, что требует большой точности в расчёте заданий цехам.
В условиях массового производства применяется подетальная система планирование по такту (ритму).
93
Суть подетальной системы планирования по такту выпуска состоит в том, что общая потребность в деталях каждого наименования по каждому цеху рассчитывается как суммарная потребность в данной детали цеха – потребителя с учётом поставок на сторону и количества, необходимого для доведения заделов по всем последующим цехам до нормативного уровня. По большинству деталей суммарная потребность в подавляющей части определяется программой выпуска готовой продукции, т.е. потребностью сборки, которая в условиях массового производства подчинена определённому такту.
7.2.1.Порядок разработки цеховых программ
Вмассовом производстве слаженный ход работы всех звеньев производства достигается путем выравнивания их производительности применительно к единой расчетной величине — такту-ритму выпуска готовых изделий.
Для данного типа производства характерна система планирования по ритму выпуска. При планировании по ритму выпуска основной плановоучетной единицей в производственных заданиях механосборочным и
выпускающим цехам является агрегат или готовая машина; механическим и заготовительным цехам соответственно — деталь или заготовка. Механосборочные, механические и заготовительные цехи получают подетальные расшифровки производственных заданий, в которых определяется количество деталей каждого наименования, подлежащее получению и изготовлению цехом для обеспечения планируемого выпуска агрегатов или изделий. Производственные задания цехам разрабатываются в целом на год с разбивкой по кварталам. Объём задания по каждой детали определяется в штуках.
Производственная программа цехам обычно устанавливается на квартал с помесячной разбивкой по системе подетального планирования. Использование этой системы позволяет установить цехам задание по выпуску и запуску по отдельным деталям (по каждой поточной линии и производственному участку внутри цехов), а плановые расчёты

94
осуществлять так, чтобы межцеховые производственные заделы были на уровне установленных норм.
Причём расчёты производственных программ цехам проводятся в порядке, обратном ходу производственного процесса, начиная с выпускающих цехов, т.е. определив программу выпускающих цехов, которые совпадают с программой предприятия, рассчитывают задания для обрабатывающих, а затем для заготовительных цехов.
Программа выпуска какого-либо изделия цеха равна программе запуска этого изделия в последующем цехе и изменению его остатков в межцеховом заделе против установленной по нему нормы.
В основе расчёта заданий цехам лежит годовой план завода по сборке машин, сдаче деталей в запасные части и по кооперации, технические спецификации и действующие технологические маршруты изготовления деталей и узлов. Программное задание по выпуску деталей каждого наименования N вi рассчитывается по каждому цеху i так, чтобы оно обеспечивало потребность в этой детали в последующем технологическому маршруту (i +1) цехе для запуска её в обработку поставки на сторону N кi и необходимого пополнения межцехового задела:
Nвi N зi 1 N лi (Zнм ц Zфм ц ) ,
где Zнм ц − нормативный уровень межцехового задела по данной детали между цехом i и (i+1) на начало планового периода;
Z фм ц − фактический уровень межцехового задела между цехами i и
Программа по запуску каждой детали N зi определяется исходя из потребности выпуска и необходимого пополнения внутрицехового задела до нормы.
|
N зi Nв1 (Z yвц Z adw ) , |
где Z вц |
− нормативный уровень циклового задела по данной детали в i |
н |
|
цехе на начало планового периода;
− фактический уровень циклового задела по данной детали в i цехе.
Пример расчета задания по деталям приведен в табл. 7.1

95
Разработка годовых заданий цехам с поквартальной разбивкой сопровождается проведением объемных расчетов, т. е. расчетов загрузки и пропускной способности оборудования. Объемный расчет основывается на установлении дневной пропускной способности каждого станка поточной линии в количестве деталей, закрепленных за линией 1. Для определения баланса загрузки и пропускной способности достаточно сравнить эту пропускную способность со среднедневным плановым заданием по годовой программе, выраженным в штуках деталей. Это задание рассчитывается путем деления программного задания в штуках деталей на количество рабочих дней в плановом периоде. Такой расчет обнаруживает, с одной стороны, соответствие производственной программы пропускной способности каждой линии, а с другой − указывает те станки и операции в линии, по которым могут возникнуть затруднения, связанные с выполнением программы («узкие» места). Для ликвидации выявленных «узких мест» требуется разработка и проведение организационных и технических мероприятий.
На машиностроительных предприятиях массового производства разработка цеховых производственных программ осуществляется на персональных компьютерах. При этом каждому цеху устанавливаются три программы:
1.Программа получения, составляемая в разрезе цехов-поставщиков, включает данные: цех-поставщик, шифр изделия, номер детали, номер узла, их количество к получению. Эта программа является вместе с тем программой изготовления деталей для цеха-поставщика.
2.Программа по изготовлению, составляемая по участкам цеха,
содержит |
данные: |
участок-изготовитель, |
шифр |
изделия, |
но |
мер детали, |
их количество, намечаемое к |
изготовлению за |
месяц. |
При необходимости по программе изготовления производят проверочные расчеты загрузки оборудования.
3. Программа по сдаче, составляемая в разрезе цехов-потребителей, содержит данные: участок-сдатчик детали, шифр изделия, номер деталей,
1 Пропускная способность каждого станка определяется отношением дневного фонда времени работы станка и штучной нормы обработки детали с учётом планового коэффициента выполнения норм.
96
их количество к сдаче «цеху-потребителю» шифр последнего, количество сдачи в запасные части и по кооперации, общее количество к сдаче. Эта программа является вместе с тем программой получения для соответствующего цеха-потребителя.
Таблица 7.1
Ведомость расчёта выпуска и запуска деталей по машине АТ-82 на июнь 2005 года по сборочному, механическому и кузнечному цехам (программа выпуска машины 10 000 шт.)
|
|
|
|
|
1 |
|
|
|
|
|
|
|
Расчёт подачи деталей в сборочный цех |
|
|
|
|
|
|||||||||||||
|
|
|
Наименование деталей |
Количествона машину |
|
машины |
|
|
|
|
|
|
|
число |
|
|
Требуется |
|
|
|
|
|
(гр. 7+гр. 8) |
||||||||
|
Номер |
|
|
|
|
|
|
|
|
|
|
|
(гр. 5 – гр.6) |
|
|
|
|
|
|||||||||||||
|
|
|
|
|
|
Требуется |
|
|
Норматив- |
|
|
Фактичес- |
|
|
на |
|
Отсев |
|
Требуется |
||||||||||||
|
детали |
|
|
|
|
|
на |
|
|
ный уровень |
|
кий уровень |
|
изменение |
|
дета- |
|
|
на запуск |
||||||||||||
|
|
|
|
|
|
|
выпускае- |
|
|
циклового |
|
|
циклового |
|
циклово- |
|
лей в |
|
в сбороч- |
||||||||||||
|
|
|
|
|
|
|
мые |
|
|
|
|
задела |
|
|
задела на 1-е |
|
го задела |
|
цехе |
|
|
ном цехе |
|||||||||
|
|
|
|
|
|
|
|
|
|
|
|
|
|
|
|
|
|
|
|
|
|
|
|
|
|
|
|
|
|
|
|
1 |
|
2 |
|
3 |
4 |
|
|
|
|
5 |
|
|
6 |
|
|
|
7 |
|
|
8 |
|
|
|
|
9 |
|
|||||
|
AI-017 |
|
Вал |
1 |
10000 |
|
|
|
1000 |
|
|
600 |
|
|
|
+400 |
|
|
- |
|
|
|
10400 |
|
|||||||
|
AI-020 |
|
Кулачок |
4 |
40000 |
|
|
|
5000 |
|
|
3500 |
|
|
|
+1500 |
|
|
- |
|
|
|
41500 |
|
|||||||
|
|
|
|
|
|
|
|
|
|
|
|
|
|
|
|
|
|
|
|||||||||||||
|
|
|
|
|
|
|
|
|
Расчёт запуска-выпуска деталей по механическому цеху |
|
|
||||||||||||||||||||
|
|
|
|
|
|
|
|
|
|
|
|
|
|
|
|
|
|
|
|
|
|
|
|
||||||||
|
номер детали |
Наименование деталей |
|
Количество на 1 машину |
|
Нормативный уровень межцехового заделе на складе готовых изделий |
|
Фактический уровень межцехового задела на 1 число на складе готовых деталей |
|
Требуется на изменение межцехового задела (гр. 10 – гр.11) |
На запасные части и по кооперации |
|
Выпуск механического цеха (гр. 9+гр.12+гр.13) |
|
Нормативный уровень циклового задела |
|
Фактический уровень цехового задела на 1-е число |
|
Требуется на изменение циклового задела (гр.15 – гр.16) |
|
Отсев деталей в цехе |
Запуск в механическую обработку (гр.14 + гр.17. + гр.18) |
|
||||||||
|
|
|
|
|
|
|
|
|
|
|
|
|
|
|
|
|
|
|
|
|
|
|
|
|
|
|
|
|
|||
|
1 |
2 |
|
3 |
|
10 |
|
11 |
|
|
|
12 |
13 |
|
|
14 |
|
15 |
|
|
16 |
|
17 |
|
|
18 |
19 |
|
|||
|
|
|
|
|
|
|
|
|
|
|
|
|
|
|
|
|
|
|
|
|
|
|
|
|
|
|
|
||||
|
AI- |
|
Вал |
|
1 |
|
800 |
|
1000 |
|
|
-200 |
- |
|
|
10200 |
|
1800 |
|
600 |
|
+1200 |
|
|
100 |
11500 |
|
||||
|
017 |
|
|
|
|
|
|
|
|
|
|
|
|
|
|
|
|
|
|
|
|
|
|
|
|
|
|
|
|
|
|
|
|
|
|
|
|
|
|
|
|
|
|
|
|
|
|
|
|
|
|
|
|
|
|
|
|
|
|||||
|
AI- |
|
кулачок |
|
4 |
|
6000 |
|
5000 |
|
|
+1000 |
4000 |
|
46500 |
|
4500 |
|
3000 |
|
+1500 |
|
|
1000 |
49000 |
|
|||||
|
020 |
|
|
|
|
|
|
|
|
|
|
|
|
|
|
|
|
|
|
|
|
|
|
|
|
|
|
|
|
|
|
|
|
|
|
|
|
|
|
|
|
|
|
|
|
|
|
|
|
|
|
|
|
|
|
|
|
|
|
|
|
|
|
97
Продолжение таблицы 7.1
|
|
|
|
Расчёт запуска-выпуска деталей по кузнечному цеху |
|
|||||||
|
|
|
|
|
|
|
|
|
|
|
|
|
номер детали |
Наименование деталей |
Количество на 1 машину |
Нормативный уровень межцехового заделе на складе заготовок |
Фактический уровень межцехового задела на складе заготовок |
Требуется на изменение цехового задела (гр.20-гр.21) |
Выпуск поковок по плану кооперации |
Выпуск кузнечного цеха (гр. 19+гр.22+гр.23) |
Нормативный уровень циклового задела |
Фактический уровень цехового задела на 1-е число |
Требуется на изменение циклового задела (гр.15 – гр.16) |
Отсев деталей в цехе |
Запуск в штамповку (гр.24 + гр.27. + гр.28) |
|
|
|
|
|
|
|
|
|
|
|
|
|
1 |
2 |
3 |
20 |
21 |
22 |
23 |
24 |
25 |
26 |
27 |
28 |
29 |
|
|
|
|
|
|
|
|
|
|
|
|
|
AI-117 |
Вал |
1 |
2000 |
3000 |
-1000 |
- |
10500 |
400 |
400 |
- |
- |
10500 |
|
|
|
|
|
|
|
|
|
|
|
|
|
AI-120 |
кулачок |
4 |
10000 |
10000 |
- |
2000 |
51000 |
2500 |
1500 |
+1000 |
- |
52000 |
|
|
|
|
|
|
|
|
|
|
|
|
|
|
|
|
|
|
|
|
|
|
|
|
|
|
Все три вида подетальных месячных программ (получения, изготовления и сдачи) составляются на основе одних и тех же исходных данных.
К ним относятся цеховая спецификация, план сдачи основных изделий по видам изделий и их модификациям, план сдачи запасных частей и изделий по кооперации, корректив, учитывающий фактическое выполнение плана за прошлый период, и корректив по выравниванию заделов. Составление таких программ всем цехам осуществляется централизованно и одновременно. Это обеспечивает полную взаимосвязанность цеховых программ и исключает ошибки.
Существенное значение при системе планирования по ритму выпуска имеет вопрос о порядке корректировки квартальных заданий годового плана с учетом фактического состояния заделов по данным инвентаризации. Кроме того, потребность в коррективе квартальных заданий годового плана может возникнуть и в результате дополнительных заданий заводу в течение года, изза сверх-лимитного брака и т. д.
Порядок внесения коррективов с учетом фактического состояния заделов определяется установленными на заводе сроками инвентаризации. Так, на ряде заводов инвентаризация проводится на I.XII и на I.VI каждого года. Соответственно с этим первый квартал годового плана устанавливается с

98
учетом фактического состояния заделов, а в план третьего квартала вносятся соответствующие коррективы. Коррективы к программе по результатам инвентаризационной проверки фактического состояния заделов устанавливаются путем сравнения фактических остатков по инвентаризации с теми нормативами, которые были положены в основу расчёта годового плана. При наличии небольшого расхождения, которое не может повлиять на выполнение программы, корректировка не производится. При значительном же расхождении производится перерасчёт плана выпуска детали по цеху, в котором обнаружено это расхождение, и соответственно пересчитывается программа сдачи этой детали по всем предшествующим переделам (цехам) по
технологическому маршруту. |
|
|
|
|
|
|
|
||
Корректив к |
программе |
сообщается |
цехам |
по |
следующей форме |
||||
(табл. 7.2): |
|
|
|
|
|
|
|
|
|
|
|
|
|
|
|
|
|
|
Таблица 7.2 |
|
|
Пересчёт плана выпуска детали цеха |
|||||||
|
|
|
|
|
|
|
|
|
|
№ |
№ детали |
Было задано |
Задаётся на |
|
В том числе по месяцам |
Примечание |
|||
п.п |
или узлов |
на квартал |
квартал |
|
1 |
|
2 |
3 |
|
1 |
1521332 |
15500 |
15900 |
|
5250 |
|
5300 |
5350 |
|
|
|
|
|
|
|
|
|
|
|
и т.д.
Помимо корректировки годового плана, устанавливаются суточные и часовые графики сдачи основной продукции. Пример такого графика приведён в табл. 7.3
Таблица 7.3
График сборки и сдачи агрегатов цехом коробок скоростей на март 2005 г.
|
План |
Суточный |
Всего |
Всего |
Всего |
Всего |
Наименование агрегатов и машин |
на |
темп |
с 2 по |
с 8 по |
с 16 |
с 23 |
|
март |
|
7 вкл. |
14 |
по 21 |
по 31 |
|
|
|
|
вкл. |
вкл. |
вкл. |
Всего собрать узлов 164А |
15048 |
684 |
3420 |
3420 |
3420 |
4788 |
В том числе: |
|
|
|
|
|
|
Сдать в цех сборки и испытания |
9284 |
422 |
2110 |
2110 |
2110 |
2954 |
автомобилей |
|
|
|
|
|
|
Вэтих графиках находит выражение корректировка программы по данным
овыполнении плана за предыдущий месяц. В конце месяца проводится
99
проверка остатков агрегатов на главной сборке и в цехе-изготовителе; сопоставление фактической величины с нормальной находит отражение в графике.
Подетально программы корректируются только при больших расхождениях. В основном стремятся такую корректировку делать только один раз в полгода.
Кроме коррективов, связанных с изменением заводской программы, цехам могут выдаваться «талоны отклонений», которые представляют собой коррективы на фактический брак и потери в производстве (см. форму 7).
Форма 7 Талон отклонений №_________ о нарушениях сроков подачи
Из цеха: термического
В цех: МСЦ 7 за 15/IV – 2006 г.
Вами нарушены сроки подачи по деталям
Номер детали |
План подачи за |
Фактически |
Отставание с |
Примечание |
|
сутки |
подано за сутки |
начала месяца |
|
485-4211260 |
140 |
96 |
44 |
|
Таким образом, особенности межцехового оперативного планирования в условиях массового производства заключается в следующем:
-операционные программы цехам составлены на квартал;
-номенклатура цеховых программ заполняется в подетальном выражении, то есть без специального комплектования;
-количественно задания рассчитываются по нормам задела и распределяются в виде ежедневного равномерного или ступенчатонарастающего выпуска.
7.3. Внутрицеховое оперативное планирование
Внутрицеховое оперативно-производственное планирование является завершающим этапом внутризаводского планирования. Задача внутрицехового ОПП заключается в доведении заданий до непосредственных исполнителей и обеспечении их всем необходимым для ритмичного выполнения планов.
100
В массово-поточном производстве, все основные параметры которого закладываются при проектировании поточных линий, задача внутрицехового ОПП ограничена главным образом поддержанием этих параметров.
Поэтому внутрицеховое планирование в условиях жёсткого закрепления деталей за поточными линиями, а операция – за каждым рабочим местом характеризуется тем, что:
-количество задания линиям устанавливают непосредственно из оперативной программы цеха;
-цеховой календарный план служит непосредственным документом, исходя из заданий которого осуществляется календарное распределение заданий в виде ежедневного плана запуска и выпуска продукции.
Внутрицеховое планирование в |
массовом производстве сводится к |
|
проектированию мер |
по ликвидации |
отклонений от графиков выпуска |
заготовок и деталей, |
сборки узлов и машин. |
Оперативный учёт хода производства осуществляется при помощи суточных план-карт, которые ведутся производственно-диспетчерским аппаратом цеха (см. табл. 7.4).
Таблица 7.4
Суточная план-карта на 28.05.2006 г.
|
План подачи |
|
Подано |
|
Результат |
|||
Номер |
по |
Отклонение |
1-я |
2-я |
3-я |
|
|
|
детали |
стандартным |
|
смена |
смена |
смена |
Сутки |
+ |
- |
|
|
|||||||
|
срокам |
|
|
|
|
|
|
|
01-15- |
286 |
- |
96 |
95 |
95 |
286 |
- |
- |
473 |
|
|
|
|
|
|
|
|
Кроме того, по решающим звеньям производственного процесса и по отстающим объектам ведется оперативный учет выполнения часового графика, позволяющий непрерывно следить за темпом выполнения производственного задания.
Важное прогрессивное значение имеет широкое использование автоматического первичного учета с помощью системы датчиков и дистанционной передачи соответствующей информации для централизованного наблюдения.
101
Так, в цехах массового производства ряда предприятий применяются специальные установки для автоматического учета работы конвейерных
линий и состояния их обеспеченности |
деталями |
и узлами, широко |
используются диспетчерские установки |
для автоматического учета работы |
металлорежущих станков и их простоев и другие технические средства диспетчерского управления производством.
Вопросы и задания для самоконтроля
1.Дайте характеристику массового типа организации производства.
2.Определите особенности организации ОПП в массовом производстве.
3.Охарактеризуйте базовые системы ОПП, применяемые в массовом производстве.
4.Покажите особенности межцехового ОПП в массовом производстве.
5.Какие календарно-плановые нормативы, применяемые в ОПП в массового производства?
6.Сколько и каких программ одновременно получает цех на предприятии массового типа организации производства?
7.Каков порядок разработки цеховых программ в массовом производстве?
8.Какие особенности имеет внутрицеховое ОПП в массовом производстве?
9.Как организован оперативный учёт и контроль в массовом производстве?
102
8. Организация производственного диспетчирования
8.1. Сущность и задачи диспетчерского руководства производством
Работа по составлению производственных программ и календарных планов-графиков является I-м этапом ОУП. Другой не менее важный этап
– диспетчирование − состоит в организации их выполнения и оперативном руководстве ходом производства, что необходимо для своевременного устранения предотвращения отклонений от нормального хода производства.
Причины отклонений могут быть весьма разнообразные: нарушение сроков поставок материалов, заготовок; отсутствие технической документации; брак продукции, простои оборудования и др.
Возможность быстрого и эффективного преодоления отклонений от нормального хода производства в большей степени зависит от оперативной информации о состоянии производства, а также от степени централизации и непрерывности руководства им.
Современной системой оперативного руководства производством, сочетающей в себе эти качества, является диспетчирование.
Диспетчирование представляет собой централизованный контроль и непрерывное оперативное руководство текущим ходом производства как в масштабе завода, так и в масштабе его внутренних подразделений.
Диспетчирование, являющееся органической частью оперативного планирования производства, включает:
−непрерывный учет и текущую информацию о фактическом ходе
работ |
по выполнению установленного |
графика |
|
производства и |
сменносуточных заданий; |
|
|
|
|
− |
принятие оперативных мер по предупреждению и устранению |
|||
отклонений от плана и перебоев в ходе производства; |
|
|
||
− |
выявление и анализ причин отклонений |
от |
установленных |
плановых заданий и календарных графиков производства и принятие оперативных мер по ликвидации этих причин;
103
−координацию текущей работы взаимосвязанных звеньев производства в целях обеспечения ритмичного хода работы по установленному графику;
−организационное руководство оперативной подготовкой всего необходимого для выполнения сменно-суточных заданий и календарных графиков производства.
Таким образом, диспетчирование представляет собой централизованный непрерывный контроль и оперативное регулирование хода производства с целью обеспечения равномерного и комплектного выполнения плана выпуска продукции.
Важнейшая задача диспетчирования состоит в том, чтобы, используя методы оперативного распорядительства, обеспечить выполнение и перевыполнение производственной программы завода при ритмичной работе рабочих мест, участков и равномерном выпуске продукции.
Диспетчирование должно носить предупредительный характер и заключаться в заблаговременном выявлении и своевременном устранении намечающихся отклонений от планов графиков и текущих заданий.
Система диспетчерского руководства является действенным средством обеспечения ритмичной работы при следующих основных условиях:
- диспетчирование должно опираться на четкую организацию оперативного планирования производства, непосредственным продолжением которого оно является;
- диспетчерское руководство предполагает непрерывность контроля и наблюдения за ходом производства, для чего необходима своевременная и точная оперативная информация о фактическом выполнении плановграфиков изготовления и выпуска продукции и обо всех неполадках, возникающих в текущей работе. При этом создание специальной системы оперативной информации основывается на применении современных технических средств, обеспечивающих автоматизацию получения, переработки и передачи информации;
- диспетчирование предполагает обязательное быстрое и четкое выполнение распоряжений диспетчерского руководства, что позволит успешно ликвидировать возникающие неполадки и координировать работу
104
всех звеньев производства; для этого диспетчерский персонал должен быть наделен достаточными полномочиями, дающими возможность осуществлять текущее распорядительство и маневрирование имеющимися на производстве резервами (страховыми запасами материалов, заделами заготовок и деталей, резервным оборудованием и т. п.) и применять другие средства, необходимые для устранения перебоев и регулирования хода производства;
-диспетчерская служба должна базироваться на четкой ответственности
ипреемственности оперативного руководства производством.
Вразных типах производства конкретное содержание диспетчерского руководства имеет ряд существенных особенностей.
Непрерывный, систематический контроль за состоянием всех элементов производства и за фактическим ходом работы по выполнению плана отличается в разных типах производства и при различных системах оперативного планирования прежде всего составом объектов наблюдений
идиспетчерского контроля.
Виндивидуальном производстве основным объектом диспетчерского контроля заходом производства являются сроки выполнения важнейших работ по отдельным заказам. Диспетчерский контроль осуществляется в этих условиях применительно к разработанным цикловым планам-графикам выполнения заказов. Он предусматривает систематическую проверку своевременности запуска и выпуска заготовок, деталей и узлов по отдельным этапам их изготовления, а также своевременности комплектования деталей и узлов для окончательного монтажа и выпуска готовой машины в установленные планом сроки.
Важнейшим условием бесперебойного выполнения производственных заданий в этих условиях является своевременная и комплектная техническая подготовка, а также сопровождающая ее оперативная подготовка всего необходимого для выполнения заказа. Диспетчерское руководство производством должно осуществлять текущую увязку работы органов технической подготовки, участвующих в последовательных стадиях разработки заказов, а также руководить комплектованием технологического оснащения и необходимых материалов.
105
Удобным вспомогательным документом для осуществления текущего контроля за ходом подготовки производства и изготовления отдельных заказов является график, приведенный в табл. 8.1.
Подобный график составляется с помощью вычислительных машин на основании сводного графика подготовки и изготовления изделий
Таблица 8.1
График для контроля за ходом подготовки производства и изготовления отдельных заказов
|
|
|
Позиция по |
|
Дата в порядке |
Наименование этапа подготовки |
Номер |
графику |
|
и изготовления изделий |
подготовки и |
|||
возрастания |
заказа |
|||
(или наименование отдела и цеха) |
изготовления |
|||
|
|
|||
|
|
|
изделий |
|
|
Отдел главного конструктора |
24 134 |
1 |
|
20/11 |
Изготовление моделей |
24 970 |
29 |
|
|
Изготовление оснастки |
26 812 |
30 |
|
|
Литейный цех |
24 915 |
3 |
|
|
и т.д. |
|
|
|
|
|
|
|
Вусловиях серийного производства главным объектом диспетчерского наблюдения и контроля являются установленные по плану сроки запуска и выпуска партий заготовок и деталей на всех участках производства, состояние складских заделов заготовок и деталей и степень комплектной обеспеченности сборочных работ в соответствии с графиком.
Взависимости от характера серийного производства и, в частности, от степени его устойчивости диспетчерский контроль может осуществляться либо применительно к стандартным графикам (расписаниям) межцеховых подач по отдельным цехам и планам-графикам работ производственных участков, либо применительно к установленным на очередной месяц срокам комплектования узлов, обработки деталей и производства заготовок. Так, при использовании системы планирования по заделам основными объектами диспетчерского контроля являются степень укомплектованности изделий, которая устанавливается на основании данных картотеки пропорциональности, и показатель отставания в сутко-позициях, определяемый из графика пропорциональности.
106
Вусловиях серийного производства важной задачей оперативной подготовки производства является обеспечение ритмичного чередования запуска партий деталей в обработку и их выпуска по установленному календарному графику. Для этого необходима, в первую очередь, четкая организация переналадки оборудования, особенно на тех участках, которые оснащены высокопроизводительными агрегатами и где применяется сложное технологическое оснащение. Работа наладчиков оборудования проводится под контролем диспетчеров, которые должны добиваться строгого соблюдения установленных графиков переналадок.
Вусловиях массового производства диспетчерское наблюдение и контроль должны быть в первую очередь направлены на проверку соблюдения установленного такта работы и нормы заделов на всех стадиях производственного процесса. Такого рода контроль осуществляется, как правило, с помощью суточных и часовых графиков работы.
Наряду со специфическими для каждого типа производства объектами диспетчерского контроля существуют и такие объекты диспетчерского наблюдения, которые свойственны любому типу производства. К ним относятся: контроль за наличием необходимых материалов, бесперебойностью работы оборудования и выполнением внеплановых срочных заказов или заданий.
Диспетчерский контроль хода производства осуществляется, как правило по следующим направлениям:
− контроль выполнения плановых заданий;
−контроль межцеховых передач заготовок, деталей, узлов и состояния заделов в производстве;
−контроль оперативной подготовки производства для обеспечения выполнения сменно-суточных заданий и графиков производства;
−контроль за работой производственных участков;
− оперативный учет и регулирование хода производства.
Диспетчер должен обеспечивать систематическую проверку наличия в производственных цехах требуемых материалов и заготовок. При этом подача всего необходимого на производственные участки и к отдельным рабочим местам средствами внутрицехового транспорта должна
107
осуществляться под наблюдением диспетчера и в ряде случаев по его прямому распоряжению.
Таким образом, при любом типе производства неизменными объектами диспетчерского контроля остается выпуск предприятием товарной продукции и обеспечения производства всем необходимым.
Текущий контроль и регулирование хода производства осуществляемые диспетчерской службой, направлены в основном на выполнение производственной программы и календарных плановграфиков в пределах суток.
8.2.Методы работы диспетчерской службы завода
Вся текущая работа по диспетчерскому руководству производством в общезаводском масштабе лежит на персонале центрального диспетчерского бюро (сменные диспетчеры и операторы), находящегося в подчинении главного диспетчера завода.
Для обеспечения непрерывности оперативного руководства производством должен быть организован четкий порядок дежурства диспетчеров и строгая преемственность в их работе, что достигается ответственной сдачей и приемкой смен. В зависимости от условий работы предприятий в практике организации диспетчерской службы применяется двоякий режим дежурств диспетчеров: круглосуточный и посменный. Наиболее эффективной для обеспечения преемственности в условиях многосменной работы является суточная система диспетчерского дежурства.
Сдавая дежурство, диспетчер отчитывается о выполнении суточного задания по выпуску готовых машин, а также важнейших агрегатов, узлов и деталей, выполнении распоряжений главного диспетчера или начальника производства о ликвидации отставаний или «узких» мест, возникших в его дежурство. Эти сведения оформляются рапортом (отчетом) сменного диспетчера.
Приступая к дежурству, диспетчер должен проверить состояние работы по выполнению графика производства и выпуска продукции, обеспеченность
108
выполнения суточного плана необходимыми материалами, ознакомиться с оперативным отчетом диспетчера предыдущей смены, обратить особое внимание на реализацию мер по ликвидации отставания от графика, устранению неполадок в ходе производства. Принятие дежурства диспетчер оформляет подписью в журнале.
Впроцессе дежурства диспетчер завода получает оперативную информацию о ходе производства и его обеспечении.
Таким образом, в общем виде оперативный контроль за ходом производства осуществляется диспетчером завода по четырем основным направлениям:
1)контроль выполнения номенклатурного плана завода и плана отгрузки продукции;
2)контроль заделов на межцеховых складах, а также межцеховых передач заготовок, деталей, узлов;
3)контроль оперативной подготовки производства;
4)наблюдение за работой отстающих участков и цехов.
Впроцессе своей работы диспетчерский аппарат завода теснейшим образом связан со всеми производственными и вспомогательными цехами, а также другими службами и отделами завода.
Для повышения четкости оперативного контроля и регулирования хода производства важное значение имеет соблюдение определенного расписания в работе диспетчерского персонала в течение дежурства.
Важным элементом работы диспетчерского аппарата завода являются диспетчерские совещания, на которых разбираются несогласованные взаимные претензии цехов, решаются вопросы координации работы всех производственных звеньев и ликвидации неполадок и отклонений от графика. Эти совещания проводятся в строго установленные сроки, его участники не отвлекаются от своих рабочих мест, что достигается применением диспетчерских коммутаторов. Последние являются важным средством технического оснащения диспетчерской службы.
Впроцессе дежурства диспетчер с помощью оператора ведет диспетчерский журнал (форма 8) и картотеку сроков. В журнал заносятся все распоряжения руководства завода и самого диспетчера, которые должны
109
быть выполнены в течение суток. В журнале также фиксируются взаимные требования цехов.
|
|
|
|
|
|
|
Форма 8 |
||
|
|
|
Диспетчерский журнал |
|
|
|
|||
|
|
|
|
|
|
|
|
|
|
|
|
Смена |
Распоряжение |
Содержание |
Сроки |
|
Отметка |
||
п№.п |
Дата |
|
|
распоряжения |
исполнения |
|
об |
||
кем дано |
кому дано |
||||||||
|
|
|
исполне |
||||||
|
|
|
|
|
|
||||
|
|
|
|
|
|
|
|
||
|
|
|
|
|
|
|
|
нии |
|
|
|
|
|
|
|
|
|
|
|
1 |
5/IX |
2 |
Главный |
Начальник |
Собрать узлы |
6/IX |
|
Сдано |
|
|
|
|
диспетчер |
сборочного |
МК-2, 2 шт. |
|
|
I6/IX в |
|
|
|
|
|
цеха |
|
|
|
12 час. 2 |
|
|
|
|
|
|
|
|
|
шт. |
Существенное значение в работе общезаводской диспетчерской службы имеют контроль и регулирование межцеховых заделов заготовок, деталей и узлов, сосредоточенных в промежуточных складах.
Подчиненные производственно-диспетчерскому отделу межцеховые производственные склады позволяют ему строго контролировать межцеховую кооперацию, обеспечивать точный учет выпуска продукции каждым цехом и регулировать подачу заготовок и деталей на дальнейшие стадии обработки.
Производственные склады обеспечивают:
-контроль своевременности подач заготовок и поступления готовых деталей из цехов;
-контроль комплектности складских заделов;
-правильную организацию хранения заделов и систематический контроль их размера (в сопоставлении с нормативным);
-организацию комплектования и своевременную подачу комплектов заготовок и деталей в соответствующие цехи.
Работники складов, руководствуясь графиками, контролируя ход производства, сигнализируют о возникающих задержках в поступлении заготовок и деталей и отпускают цехам-потребителям лишь те заготовки и детали, которые необходимы для осуществления планового запуска на соответствующие стадии производства.
Особенно важное значение для диспетчерского контроля и обеспечения равномерного выпуска продукции имеет правильная организация оперативной работы склада готовых деталей и комплектующих изделий.
110
Для обеспечения бесперебойной работы сборочных цехов необходимо организовать предварительное комплектование деталей и покупных изделий в соответствии со сменно-суточными заданиями на очередные сутки. Работа по комплектованию производится на основе комплектовочных ведомостей.
Для своевременного комплектования сборки диспетчерская служба завода должна ликвидировать отставание и «дефицитность» отдельных деталей, а также обеспечивать постоянное поддержание заделов на установленном плановом уровне. Для систематического наблюдения за наличием деталей на складе ведется ежедневный учет поступления и выдачи деталей каждого наименования и размера с выявлением текущих остатков.
Описанный порядок работы по складу готовых деталей применяется также и на складе заготовок. Особенностью работы этого склада является то, что он выполняет функцию не комплектования, а питания обрабатывающих цехов заготовками в соответствии с установленными опережениями в работе цехов.
8.3. Техническое оснащение диспетчерской службы
Высокий темп современного производства, требование быстроты реакции на малейшие отклонения от графиков, необходимость немедленной локализации и устранения перебоев делают обязательным применение в практике диспетчирования комплекса средств технического оснащения. Использование этих средств значительно облегчает задачи и поднимает на более высокий качественный уровень оперативный контроль и регулирование производства.
В практике диспетчирования на машиностроительных предприятиях применяются следующие виды технического оснащения:
A. Административно-производственная связь, включающая: специальную телефонную связь; телеграфную и фототелеграфную связь; радиосвязь.
Б. Поисковая, вызывная и производственная сигнализация.
111
В. Средства отображения процессов производства и управления, куда входят: диспетчерские пульты, промышленное телевидение, контрольные доски-графики и картотеки, звукозаписывающая аппаратура.
Специальная диспетчерская телефонная связь отличается от обычной телефонной тем, что в ней применяются коммутаторы, позволяющие подключить к диспетчерскому пункту ряд абонентских точек и вести одновременные переговоры с ними. Для этого используются диспетчерские коммутаторы (общезаводские или цеховые). Диспетчерские коммутаторы обычно рассчитаны на 40, 60, 70 и более абонентских точек. Общезаводской коммутатор позволяет:
- диспетчеру и оператору вести независимо друг от друга одновременные разговоры с несколькими абонентами;
- диспетчеру разговаривать не только с помощью микротелефонной трубки, но и посредством настольного микрофона и репродуктора (громкоговорящий прием);
- проводить диспетчерские совещания с любым количеством участников (в пределах емкости коммутатора) и вести циркулярную передачу сообщений, т. е. передавать их одновременно в несколько пунктов.
Задачи разработки оптимальных планов производства, начиная от перспективных и включая сменно-суточные, оперативного учета и диспетчерского регулирования хода производства, находят наиболее эффективное решение в условиях автоматизированных систем управления производством (АСУП). АСУП охватывает и связывает между собой все функции управления и планирования производства на основе совершенствования организационных методов управления, использования экономико-математических методов и быстродействующей вычислительной техники, а также современных средств накопления, обработки, отображения и передачи информации.
Внедрение АСУП требует упорядочения информационной базы, отработки документации и документооборота, создания нормативного хозяйства. Нормативная и другая относительно постоянная производственная информация, соответствующим образом зашифрованная, хранится в ВЦ в картотеке нормативно-справочной информации на электронных носителях.
112
Если в процессе плановых расчетов возникает необходимость использовать промежуточные или окончательные результаты одного расчета в других, должен быть обеспечен вывод этих результатов на электронные носители, которые также поступают в картотеку ВЦ. Таким образом, обеспечивается увязка информационных потоков подсистем, т. е. документальное и нормативное единство и связь результативных и исходных данных в комплексе плановых расчетов.
Математическое обеспечение АСУП включает разработку методов и алгоритмов решения задач, рабочих нестандартных программ.
На такой основе АСУП в части оперативного планирования позволяет:
а) использовать компьютерную технику для расчета формирования
производственной |
программы |
и |
построения |
номенклатурно- |
календарного плана, |
расчета |
календарно-плановых |
нормативов и |
разработки цеховых оперативных программ, построения календарных планов-участков;
б) автоматизировать процесс обработки отчетных данных, формировать и получать аналитическую информацию, непрерывно отображающую фактический ход производственного процесса;
в) корректировать оперативные программы и календарные графики и осуществлять научное прогнозирование выполнения работ в установленные сроки;
г) накапливать систематизированные статистические данные о фактической длительности циклов, трудоемкости работ для разработки укрупненных нормативно-справочных материалов.
Автоматизация и механизация работ по планированию, учету и регулированию резко повышает качество плановых расчетов, позволяя осуществлять выбор наиболее целесообразных решений, намного сокращает трудоемкость и повышает эффективность управления в целом.
Вопросы и задания для самоконтроля
1.Покажите значение диспетчирования в ОУП.
2.Раскройте сущность диспетчирования.
113
3.Почему диспетчирование должно носить предупредительный характер?
4.Каковы задачи диспетчирования на предприятии?
5.Каковы особенности диспетчирования в зависимости от типа организации производства?
6.Кто осуществляет текущую работу по диспетчерскому руководству производством?
7.По каким основным направлениям осуществляется оперативный контроль за ходом производства диспетчером предприятия?
8.Для чего проводятся диспетчерские совещания?
9.Какие документы заполняет диспетчер в процессе дежурства?
10.Что включает в себя техническое оснащение диспетчерской службы?
9. Современные методы, применяемые в оперативном управлении производством
9.1. Некоторые особенности оперативного управления производством в условиях АСУП
До сих пор мы рассматривали традиционные методы ОУП в различных типах производства. Применение этих методов является необходимой предпосылкой организации равномерной и эффективной работы предприятия. Однако передовые предприятия стремятся к дальнейшему совершенствованию ОУП. Для этого они широко используют в плановоэкономических расчетах математические методы, ЭВМ, создают автоматизированные системы управления производством (АСУП). Основным элементом в АСУП является оперативное планирование и регулирование хода производства.
Опыт передовых предприятий свидетельствует о том, что внедрение АСУП наиболее прогрессивный путь совершенствования ОУП.
Задачи разработки оптимальных планов производства, начиная от перспективных и включая сменно-суточные планы, оперативный учет и диспетчерское регулирование хода производства, находят наиболее эффективное решение в условиях АСУП.
114
АСУП охватывает и связывает между собой все функции управления, в т.ч. планирования на основе совершенствования организационных методов управления, использования математических методов и ЭВМ, а также современных средств накопления, обработки, отображения и передачи информации.
Впрактике предприятий при применении традиционных методов планирования вариантные расчеты плана, требующие быстрого пересчета технико-экономических показателей, подчас не выполняются из-за большой трудоемкости расчетов и отсутствия реальных возможностей проведения такой работы плановыми органами. Использование экономикоматематических методов и ЭВМ делает реальным решение подобных задач.
Вчастности, использование экономико-математических методов и персональных компьютеров позволяет определить оптимальный размер партий деталей. В настоящее время на большинстве предприятий этот вопрос решается путем эмпирического подбора. Поскольку расчеты по оптимизации величины партий деталей в зависимости от факторов, на нее влияющих, весьма трудоемки. Применение математических методов и ЭВМ позволяет в короткие сроки обоснованно решить данную задачу и охватить весь комплекс параметров, влияющих на основные технико-экономический показатели работы с учетом фактора времени.
Последнее особенно важно, т.к. нередко поиск оптимального решения той или иной задачи вручную не может быть проведен ввиду того, что займет много времени, в результате чего снижается оперативность планирования.
Применение АСУП в части ОУП позволяет:
-использовать ЭВМ для расчета формирования производственной программы и построения номенклатурно-календарного плана, расчета календарных плановых нормативов и разработки цеховых операционных программ и календарных планов участков;
-автоматизировать процесс обработки отчетных данных, формировать и получать аналитическую информацию, непрерывно отображающую фактический ход производственного процесса;
115
-корректировать оперативные программы и календарные графики и осуществлять научное прогнозирование выполнения работы в установленные сроки.
-накапливать систематизированные статистические данные о фактической деятельности циклов, трудоемкости работ для разработки укрупненных нормативно-справочных материалов.
Выполнение всех этих операций при помощи персональных компьютеров создает условия, в которых планирование и регулирование хода производства действительно становятся непрерывными, централизованными и оперативными, т.е. удовлетворяют требованиям рационального организованного производственного процесса.
Автоматизация работ по планированию, учету и регулирования производства резко повышает качество плановых расчетов, позволяя осуществлять выбор наиболее целесообразных решений, намного сокращает трудоемкость и повышает эффективность управления в целом.
Дальнейшее улучшение действующих комплексов задач автоматизированной системы оперативного управления производством (АСОУП) возможно по направлениям:
− совершенствование состава задач в соответствии с требованиями к системам ОУП на этапе ускорения его интенсификации; − применение прогрессивных методов моделирования, в лучшем случае, методов решения оптимизационных задач;
− широкое использование функциональных и обеспечивающих пакетов прикладных программ и типовых проектных решений.
9.2. Экспертные системы в оперативном управлении производством
К числу современных методов, применяемых в ОУП относятся: экспертные системы и методы имитационного моделирования.
116
9.2.1. Понятие «экспертная система» и её классификация
Экспертные системы – это сложные программы, которые манипулируют знаниями в целях получения удовлетворительного и эффективного решения в узкой предметной области.
Основа экспертной системы — совокупность знаний,
сконструированная определенным образом в целях упрощения процесса принятия решений.
Характерным примером экспертной системы может быть экспертная система для оценки банковских операций с клиентами, которая способна принимать решения о предоставлении ссуд частным лицам на основе автоматизированной оценки кредита (при этом используются разнообразные базы данных о клиентах). Решения принимаются на основе стандартных процедур мышления (правил поведения) опытных специалистов (экспертов) по предоставлению таких ссуд, опыт которых преобразован в автоматические алгоритмы принятия решений.
В зависимости от способа организации (конструирования) знаний в экспертных системах они бывают:
классификационными, в которых реализуется вариантный подход (перебор возможных решений, мониторинг, диагностика, сравнение с аналогами), т. е. осуществляется поиск по определенным «продукционным правилам»;
синтезирующими, в которых реализуется генеративный подход «от цели к фактам» (синтез неопределенных решений, метод «обратной волны»). При этом используются особые минимальные информационные структуры – фреймы, способные описать тот или иной класс объектов (явлений, процессов). Фрейм состоит из имени фрейма и слотов. Слот – это незаполненная подструктура фрейма в виде сети. Слоты состоят из шпаций, содержащих текущие значения слотов;
комбинированными, в которых используются оба подхода (т.н. семантические сети). Именно этот класс экспертных систем наиболее пригоден для систем организационно-технологического управления.
117
Важным импульсом в создании и использовании этих систем послужило создание ЭВМ пятого поколения (интеллектуальных ЭВМ), созданных на базе особых логических теорий, новых языков логического программирования, представления и обработки знаний, новой архитектуры систем. Широко использована теория нечетких множеств. В результате прикладной специалист теперь может разрабатывать собственные прикладные программы. Система свободно распознает ошибки, противоречия и самостоятельно может их исправлять. Существуют возможности самообучения этих систем (накопления знаний, в т.ч. от эксперта к системе). С системой могут работать сразу несколько специалистов.
Втехническом отношении экспертные системы имеют лингвистические интерпретаторы, блоки знаний и блок коррекции базы данных, подсистемы диагностирования и контроля состояния технических объектов.
Всложных случаях (при нахождении объекта на грани «ухода» режима за рамки, определенные технологическим регламентом, например, при авариях) система может принимать решения автоматически без участия диспетчера. В обычных же условиях система функционирует в режиме «советчика», работая на профессиональном диалекте естественного языка. Окончательный выбор решения остается за человеком.
Использование экспертных систем по сравнению с обычными системами управления дает ощутимый прирост выпуска продукции.
Отечественные экспертные системы считаются одними из наиболее эффективных в мире.
118
9.3.Методы имитационного моделирования
9.3.1.Понятие математической имитации
Под имитацией понимается численный метод проведения экспериментов с моделью исследуемого объекта, описывающий его поведение в течение длительного времени.
Следует отметить, что в реальной экономике проведение любых экспериментов сопряжено с большими рисками, поэтому имитационное моделирование экспериментов является, по сути, единственной возможностью действовать в данном направлении.
Помимо модели технологической системы в имитационную модель системы управления включаются датчики случайных чисел с заданным законом распределением (функцией распределения). При этом чаще всего используется равномерное распределение или таблицы случайных чисел. Применяются и другие методы, учитывающие вероятностный характер наступления тех или иных событий.
Имитационное моделирование широко используется при составлении графиков производства, определения уровня запасов и процедур технического обслуживания, для планирования производственной мощности, потребностей в ресурсах и т.п.
Имитационное моделирование означает использование компьютера для выполнения экспериментов с моделью той или иной реальной системы. Такие компьютерные модели хорошо известны (учебная игра «Дельта», авиационные имитаторы, видеоигры и подобная анимация виртуальной реальности). Этот метод используется в тех случаях, когда не удаётся использовать методы математического анализа и математической оптимизации (в сложных проблемах и большой размерности задач). Очереди деталей хорошо поддаются имитационному моделированию.
Поскольку имитационное моделирование − это всякий раз эксперимент, то используется специальная математическая теория планирования эксперимента и обработки его результатов.
Процесс моделирования можно представить в виде блок-схемы (рис. 10)

119
начало
1. Формирование задачи
совершенствование модели
2. Построение имитационной модели
очередная интерация
3.Определение значений переменных и параметров
4.Моделирование (работа программы)
5.Оценка результатов
а) адекватность |
б) степень |
модели реальности |
достижения целей |
|
моделирования |
оценка
неудовлетворительна
6. Проведение нового исследования
Определение целей исследуемой системы; переменных, которые влияют на достижение цели
Определение параметров переменных; формирование правил принятия решений; определение распределения вероятности; выбор способа наращивания времени
Определение начальных условий; определение продолжительности
моделирования
полное достижение целей моделирования
завершение
исследования
Рис. 10. Блок-схема моделирования
9.3.2. Предпосылки, ограничения и перспективы использования имитационного моделирования в организационно-технологическом управлении (ОТУ)
Размерность ОТУ настолько велика, что потребовалось использовать и данный метод. Причем этот метод считается наилучшим в ряду других нетрадиционных методов оперативного управления (например,
120
фондоотдача основного технологического оборудования может возрасти до 2 раз).
Однако этот метод нельзя использовать в реальном масштабе времени при диспетчировании (т.к. для проведения эксперимента как раз требуется время), поэтому метод используется главным образом для сменносуточного, декадного, месячного планирования и при проектировании новых гибких производственных систем (ГПС)
Сочетание экспертных систем с имитационным моделированием позволяет получить качественно новую ступень в создании инструментальных средств проектирования ГПС и систем оперативного управления. При этом появляется возможность проведения целенаправленных (сознательных) экспериментов, а имитационная модель последовательно приближается к описываемому ею объекту. Именно объединение указанных методов представляется перспективой в создании новых управляющих систем.
Практика показывает, что внедрение математических методов и автоматизация оперативно-плановой работы особенно с помощью ЭВМ, оказываются эффективными лишь при условии, когда вычислительная техника сочетается с передовыми принципами и методами оперативного управления.
Вопросы и задания для самоконтроля
1.Какие современные методы оперативного управления используются на предприятии?
2.Какие возможности ОУП расширяются с использованием АСУП?
3.По каким направлениям возможно улучшение ОУП в автоматизированной системе оперативного управления производством?
4.Что такое экспертные системы?
5.Как могут быть классифицированы экспертные системы?
6.Дать понятие имитации.
7.Определите область использования имитационного моделирования в системе управления.
8.Какова блок-схема процесса моделирования?
121
9. Каковы возможности и ограничения использования имитационного моделирования?
Тесты для контроля результатов обучения
1. Что такое оперативное управление производством?
а) система обработки информации и принятие решений, в которой управление реализуется по принципу обработки связи;
б) комплекс органически взаимоувязанных элементов, подчинённых единому принципу обеспечения согласованного хода производства по равномерному изготовлению и выпуску заданной номенклатуры продукции при наилучшем использовании производственных ресурсов;
в) самостоятельный комплекс мероприятий, направленный на гибкую организацию производственного процесса и ритмичный выпуск продукции.
2. Какие фазы включает в себя оперативное управление?
а) планирование, контроль, анализ и диспетчирование;
б) планирование, учёт, контроль, анализ и регулирование хода производства;
в) контроль, мотивация, планирование и учёт хода производства.
3. Требования, предъявляемые к оперативному управлению:
а) гибкость, чёткость, своевременность, качество;
122
б) равномерность, ритмичность, сокращение перерывов в длительности производственного цикла, обеспечение загрузки оборудования, гибкость;
в) чёткость, обеспечение своевременной загрузки оборудования и рабочих, непрерывность планирования.
4. При обеспечении равномерности производственного процесса коэффициент равномерности:
а) возрастает; б) уменьшается;
в) остаётся неизменным в равные промежутки времени.
5. Если коэффициент дискретности стремится к «0», это означает, что:
а) перерывы в длительности производственного цикла не меняются;
б) перерывы в длительности производственного цикла уменьшаются;
в) перерывы в длительности производственного цикла возрастают.
6. Какой орган координирует работу по оперативному управлению производством на предприятии?
а) отдел оперативного управления; б) производственно-диспетчерский отдел;
в) производственно-технологический отдел.
7. Какие виды оперативного управления выделяют на предприятии?
а) цеховое оперативное управление и оперативное управление участков; б) общезаводское и цеховое оперативное управление;
123
в) межвузовское и внутрицеховое оперативное управление.
8. Сущность календарно-плановых расчётов, используемых в оперативном планировании:
а) система норм и нормативов, позволяющая спланировать обоснованную производственную программу цехов и участков, довести задания до конкретных исполнителей и разработать календарные планыграфики работы подразделений;
б) система норм и нормативов необходимая для организации производственного процесса на различных уровнях и позволяющая проверить обоснованность годовых заданий предприятия;
в) система расчётных показателей, необходимых для формирования производственной программы предприятия и его подразделений.
9. Какие типы организации производства существуют?
а) поточный, непоточный; б) индивидуальный, партионный и поточный;
в) индивидуальный, серийный, массовый.
10. Что такое тип организации производства?
а) комплексная характеристика особенностей организации и технического уровня предприятия, обусловленная степенью его специализации, сложностью и устойчивостью изготавливаемой номенклатуры продукции, размерами и повторяемостью их выпуска, а также масштабами производства;
б) комплексная характеристика организационно-технического уровня производства, обусловленная масштабами и повторяемостью
124
номенклатуры выпускаемой продукции, её качеством и уровнем квалификации рабочих;
в) организационно-техническая характеристика производства, обусловленная применяемым оборудованием, оснасткой, кадрами рабочих, изготавливающих продукцию.
11. Факторы, влияющие на тип организации производства:
а) степень специализации, масштаб и устойчивость номенклатуры выпускаемой продукции, степень повторяемости продукции;
б) масштаб и степень специализации выпускаемой продукции, применяемое оборудование и кадры рабочих, уровень организации производства;
в) повторяемость номенклатуры выпускаемой продукции, применяемое оборудование и оснастка, устойчивость номенклатуры продукции.
12. В каком типе организации производства целесообразно использовать специальное оборудование и оснастку?
а) индивидуальном; б) массовом;
в) массовом и серийном.
13. В каком типе организации производства себестоимость изготавливаемой продукции будет наименьшей?
а) серийном; б) индивидуальном; в) массовом.
125
14. Какие |
базовые |
системы |
оперативно-производственного |
планирования используются в индивидуальном типе организации производства?
а) позаказная, по комплектовочным номерам, «на склад»; б) позаказная, покомплектно-узловая, «на склад»; в) позаказная, по заделам, по комплектовочным номерам.
15. Какие |
базовые |
системы |
оперативно-производственного |
планирования используются в массовом производстве?
а) по цикловым комплектам, партионно-периодическая, «на склад»; б) по заделам, серийная по опережениям, по ритму выпуска; в) партионно-периодическая, по ритму выпуска.
16. Какие календарно-плановые нормативы используются в оперативном планировании индивидуального производства?
а) длительность производственного цикла, партия деталей, время опережения;
б) длительность производственного цикла, время опережения, заделы;
в) длительность производственного цикла, партия деталей, периодичность запуска-выпуска деталей.
17. Что такое «время опережения»?
а) календарный период времени между запуском и выпуском изделия в определённом цехе;
126
б) календарный период времени, который отделяет более ранние сроки начала работ от запланированной даты выпуска изделия;
в) календарный период времени между запуском двух смежных изделий в цехе.
18. Какие заделы используются в оперативном планировании?
а) технологический, межоперационный оборотный, страховой;
б) цикловой, складской, переходящий;
в) складской, страховой, оборотный.
19. Отличительная особенность оперативно-производственного планирования в индивидуальном типе организации производства?
а) портфель заказов является основой составления календарных графиков их выполнения;
б) планирование технической подготовки заказа включается в календарный график его выполнения;
в) календарный график составляется с учётом загрузки оборудования.
20. Виды календарных планов-графиков, используемых в межцеховом оперативно-производственном планировании серийного производства:
а) план-график работы участка; план-график запуска деталей на сборку; план-график выпуска деталей; стандартный план-график;
б) план-график работы переменно-поточных линий; пооперационный стандартный план-график; стандартный план-график запуска-выпуска
127
деталей; календарный план-график сроков подачи деталей на сборку и их запуска на первую операцию;
в) стандартный план-график запуска-выпуска деталей; план-график запуска деталей на первую операцию; план-график выпуска изделия.
21. Основные элементы системы непрерывного оперативнопроизводственного планирования:
а) единый сквозной график выпуска продукции, картотека пропорциональности; график пропорциональности;
б) нормативные заделы, условное изделие, условный сутко-комплект, единый сквозной график сдачи продукции;
в) условное изделие, график пропорциональности, картотека пропорциональности, «ключ» к картотеке пропорциональности.
22. Базовые системы оперативно-производственного планирования, применяемые в серийном производстве:
а) серийная по операциям; по заделам; по комплектовочным номерам; по цикловым заделам; «на склад»;
б) серийная по опережениям, «на склад», пооперационно-периодическая по цикловым комплектам, позаказная;
в) пооперационно-периодическая, по цикловым комплектам, по ритму выпуска, по комплектовочным номерам.
128
23. Что означает диспетчирование производства?
а) контроль, учёт и оперативное руководство ходом производства в цехах и на производственных участках;
б) централизованный контроль и непрерывное оперативное руководство текущим ходом производства как в масштабе предприятия, так и в масштабе его внутренних подразделений;
в) устранение отклонений от нормативного хода производства путём мероприятий по руководству оперативным ходом производства.
129
Библиографический список
1.Афитов Э. А., Новицкий Н. И., Цыганков В. Д. Организация вспомогательных цехов и обслуживающих хозяйств предприятия : учебное пособие по курсу «Организация и планирование производства. Управление предприятием». – Минск : МРТИ, 1992. – 60 с.
2.Батенин Е. В. Календарно-плановые расчеты в оперативном планировании производства. – М. : МИНХ, 1979. – 80 с.
3.Батенин Е. В. Организация диспетчерской работы на промышленном предприятии. – М. : МИНХ, 1980. – 84 с.
4. |
Бухалков М. И. Внутрифирменное |
|
планирование : |
учебник. |
– |
|
М. : ИНФРА-М, 2001. – 392 с. |
|
|
|
|
||
5. |
Гончаров В. Н., Колосов А. Н., Дибнис Г. И. Оперативное управление |
|||||
производством: Опыт |
разработки и |
совершенствование |
систем. |
– |
||
М. : Экономика, 1987. – 120 с. |
|
|
|
|
||
6. |
Васильев В. Н. Организация, управление и экономика гибкого |
|||||
интегрированного |
производства |
в |
машиностроении. |
– |
||
М. : Машиностроение, 1986. – 232 с. |
|
|
|
|
7.Ицкович Э. Л., Сорокин Л. Р. Оперативное управление непрерывным производством. – М.: Наука, 1989. – 281 с.
8.Карданская Н. Л., Чудаков А. Д. Системы управления производством: анализ и проектирование : учебное пособие. – М. : Русская Деловая литература, 1999. – 240 с.
9.Каминский Б. В., Лукашин А. Я. Знакомьтесь: новое в организации производства. – М. : Экономика, 1992. – 154 с.
10.Климов А. Н., Оленев И. Д., Соколицин С. Л. Организация и планирования производства на машиностроительном заводе. – Л. :
Машиностроение, 1979. – 640 с.
11.Курляндчик Р. И. Обеспечение ритмичности машиностроительного производства. – Л. : Машиностроение, 1989. – 152 с.
12.Лобов Ф. М. Оперативное управление производством. – Ростов-на-Дону :
Феникс, 2003. – 160 с.
130
13.Логистика : учебное пособие / под ред. Б. А. Аникина. – М. : ИНФРА-М,
1997. – 327 с.
14.Макаренко М. В., Махалина О. М. Производственный менеджмент. – М. : 2001. – 150 с.
15.Минаев Э. С., Агеева Н. Г., Аббата Дага А. Управление производством и операциями: 17-модульная программа для менеджеров «Управление развитием организации», Модуль 15. – М. : ИНФРА-М, 2000. – 256 с.
16.Никифоров А. Д., Ковшов А. Н., Назаров Ю. Ф. Процессы управления объектами машиностроения : учебное пособие. – М. : Высшая школа, 2001. –
455с.
17.Новицкий Н. И. Основы менеджмента: организация и планирование производства (задачи и лабораторные работы). – М. : Финансы и статистика,
1998. – 208 с.
18.Новицкий Н. И. Организация производства на предприятиях : учебнометодическое пособие. – М. : Финансы и статистика, 2001. – 392 с.
19.Организация производства и управление предприятием : учебник / под ред. О. Г. Туровца. – М. : ИНФРА-М, 2002. – 544 с.
20.Организация и планирование производства на машиностроительном предприятии : учебник / под ред. В. А. Летенко. – М. : Высшая школа, 1972. –
607с.
21.Организация, планирование и управление деятельностью промышленного предприятия : учебник / под ред. С. М. Бухало. – Киев : Выша школа, 1989. –
472с.
22. Оперативное управление в ГПС / В. Ф. Горнев и др. – М. : Машиностроение, 1990. – 203 с.
23. Оперативно-производственное планирование ГПС / под ред. Б. И. Черпакова. – М. : Высшая школа, 1989. – 412 с.
24.Оперативный контроль экономической деятельности предприятия / под ред. Б. М. Валуева – М. : Финансы и статистика, 1991. – 241 с.
25.Первозванский А. А. Курс теории автоматического управления. – М. :
Наука, 1986. – 298 с.
26.Поспелов Д. А. Ситуационное управление. Теория и практика. – М. :
Наука, 1986. – 158 с.
131
27.Рабочая тетрадь к учебнику «Управление организацией»: Раздел 7 «Управление производством» / М. А. Дьяченко, Н. А. Саломатин, А. В. Фель
– М. : ИНФРА-М, 2001. – 86 с.
28.Разумов И. М. Организация и планирование машиностроительного производства : учебник. – М. : Машиностроение, 1974. – 591 с.
29. Служба оперативного управления основным производством. –
Л. : Лениздат, 1989. – 97 с.
30.Соколицин С. А., Кузин Б. И. Организация и оперативное управление машиностроительным производством. – Л. : Машиностроение, 1988. – 527 с.
31.Татевосов К. Г. Основы оперативно-производственного планирования на машиностроительном предприятии. – Л. : Машиностроение, 1985. – 285 с.
32.Управление производством : учебник / под ред. Н. А. Саломатина. – М. :
ИНФРА-М, 2001. – 219 с.
33.Хан Д. Планирование и контроль: Концепция контроллинга : пер. с немец. / под ред. А. А. Турчака – М. : Финансы и статистика, 1997. – 800 с.
34.Чейз Ричард Б., Эквилайн Николас, Дж. Якобс, Роберт Ф. Производственный и операционный менеджмент, 8-е изд. : пер. с англ. М. :
Вильямс, 2001. – 704 с.
35.Шепеленко Г. И. Экономика, организация и планирование производства
на предприятии : учебное пособие. – Ростов-на -Дону : МарТ, 2001. – 544 с.
132
|
|
|
|
|
|
|
|
|
|
|
|
|
|
|
|
|
|
|
|
|
|
|
|
|
|
|
|
|
|
|
|
|
|
|
|
|
|
|
Приложение 1 |
||||||
|
|
|
|
|
|
|
|
|
|
|
|
|
|
|
|
|
|
|
|
|
|
|
|
|
|
|
|
|
|
|
|
|
|
|
|
|
|
|
|
|
|
|
Форма 5 |
||
|
|
|
|
|
|
|
|
|
|
|
|
|
|
|
|
|
Сменное задание – рапорт |
|
|
|
|
|
|
|
|
|
|
|
|
|
|
|
|
|
|
|
|
|
|||||||
|
|
|
|
|
|
|
|
|
|
|
|
|
|
|
|
|
|
|
|
|
|
|
|
|
|
|
|
|
|
|
|
|
|
|
|
|
|
|
|
|
|
|
|||
|
|
|
|
|
Год |
|
|
Месяц |
|
Фамилия мастера |
|
|
Цех |
|
|
Пролёт |
|
|
Смена |
|
|
|
Число |
|
|
|
|
|
Вид |
||||||||||||||||
|
|
|
|
|
|
|
|
|
|
|
|
|
|
|
|
|
|
|
|
|
|
|
|
|
|
|
|
|
|
|
|
|
|
|
|
|
|
|
|
|
|
оплаты |
|||
|
|
|
|
|
1971 |
|
|
|
5 |
|
|
|
Шумский |
|
|
|
1 |
|
|
|
2 |
|
|
|
1 |
|
|
|
|
|
8 |
|
|
|
|
|
|
05 |
|
||||||
|
|
|
Задание |
|
|
|
|
|
|
|
|
|
|
|
Нормативы |
|
|
|
|
выполненииоОтметка задания |
|
|
|
|
|
|
|
|
Приёмка ОТК |
|
|
|
|
|
|
|
|
||||||||
|
|
|
|
|
|
|
|
|
|
маршрутногоНомер листа |
|
|
|
|
|
|
|
|
|
|
|
|
|
|
|
|
|
|
|
|
|
|
|
|
|
|
|
|
|
|
|
||||
на,станкаНомеркотором производиласьработа |
|
деталейНомер |
Номер |
Наименование |
Выданов работу |
|
|
|
работыРазряд |
|
Время |
Расценок |
Время |
Расценок |
|
Всего |
|
Прописью |
|
счислетомВ1-го |
предъявления |
Количество |
|
.опл% |
|
Количество |
.опл% |
|
извещенияНомеро браке |
|
штампеоПодписьОТК |
||||||||||||||
|
|
|
|
|
Операция |
|
|
|
|
|
|
|
Подготовленное |
штучное |
|
|
|
Годных |
|
|
|
|
|
|
Брак |
|
|
|
|
|
|
|
|
||||||||||||
|
|
|
|
|
|
|
|
|
|
|
|
|
|
|
заключение |
|
|
|
|
|
|
|
|
|
|
|
|
|
|
|
|
|
|
|
|
|
|
|
|
|
|
||||
|
|
|
|
|
|
|
|
|
|
|
|
|
|
|
|
|
|
|
|
|
|
|
|
|
|
|
|
|
|
|
|
Исправим |
|
Оконч. |
|
|
|
|
|
|
|
||||
|
|
|
|
|
|
|
|
|
|
|
|
|
|
|
|
|
|
|
|
|
|
|
|
|
|
|
|
|
|
|
|
|
|
|
|
|
|
|
|
|
|
||||
1 |
|
2 |
|
3 |
4 |
5 |
|
6 |
|
7 |
|
8 |
|
9 |
|
|
10 |
|
11 |
|
12 |
13 |
|
14 |
|
15 |
|
16 |
|
17 |
18 |
|
19 |
|
20 |
|
21 |
|
|||||||
|
|
|
|
|
|
|
|
|
|
|
|
|
|
|
|
|
|
|
|
|
|
|
|
|
|
|
|
|
|
|
|
|
|
|
|
|
|
|
|
|
|
|
|||
|
|
|
|
|
|
|
|
|
|
|
|
|
|
|
|
|
|
|
|
|
|
|
|
|
|
|
|
|
|
|
|
|
|
|
|
Продолжение формы 5 |
|||||||||
|
|
|
|
|
|
|
|
|
|
|
|
|
СМЕННОЕ ЗАДАНИЕ – РАПОРТ № 208 |
|
|
|
|
|
|
|
|
|
|
|
Листов |
|
|
|
|
|
|
|
|||||||||||||
|
|
|
|
|
|
|
|
|
|
|
|
|
|
|
|
|
|
|
|
|
|
|
|
|
|
|
|
|
|
|
|
|
|
|
Лист № 1 |
|
|
|
|||||||
|
|
|
|
|
|
|
|
Исполнитель |
|
|
|
|
|
|
|
|
|
|
|
|
|
|
|
Нормированное время и зарплата |
|
||||||||||||||||||||
Шифр мастера |
|
|
|
Фамилия |
|
|
номер.Таб |
|
|
Категория |
|
|
Профессия |
|
Разряд |
|
|
|
|
|
|
|
|
наВремя годные детали |
|
|
Зарплатаза ,деталисдан. предго-1с . |
|
Зарплатаза годные |
,деталируб. |
|
|
|
За брак |
|
||||||||||
|
|
|
|
|
|
|
|
|
|
|
|
|
Шифр затрат |
|
|
|
|
|
|
|
|
|
|
|
|
||||||||||||||||||||
|
|
|
|
|
|
|
|
|
|
|
|
|
|
|
|
|
|
|
|
|
|
|
|
|
|
|
|
|
|
|
|
|
|
|
|
|
|
|
|
|
|
|
|||
|
|
|
|
|
|
|
|
|
|
|
|
|
|
|
|
|
|
|
|
|
|
|
|
|
|
|
|
|
|
|
|
|
|
|
|
|
|
|
|
|
|
|
|
||
|
|
|
|
|
|
|
|
|
|
|
|
|
|
|
|
|
|
|
|
|
|
|
|
|
|
|
|
|
|
|
|
|
|
|
|
|
|
|
|
|
|
Зарплата |
|
||
|
|
|
|
|
|
|
|
|
|
|
|
|
|
|
|
|
|
|
|
|
|
|
|
|
|
|
|
|
|
|
|
|
|
||||||||||||
04 |
|
|
|
Петрова |
|
4070 |
|
1 |
|
|
23 |
|
|
|
|
|
|
20010225 |
|
5,02 |
|
|
|
|
|
2,07 |
|
|
|
|
|
|
|
||||||||||||
|
|
|
|
|
|
|
|
|
|
|
|
|
|
|
|
|
|
|
|
|
|
|
|
|
|
|
|
|
|
|
|
|
|
|
|
||||||||||
22 |
|
|
|
23 |
|
|
24 |
|
|
25 |
|
26 |
|
27 |
|
|
|
|
|
28 |
|
|
|
|
29 |
|
|
|
30 |
31 |
|
|
|
|
32 |
|
|||||||||
|
|
|
|
|
|
|
|
|
|
|
|
|
|
|
|
|
|
|
|
|
|
|
|
|
|
|
|
|
|
|
|
|
|
|
|
|
|
|
|
|
|
|
|
|
|
133
|
|
|
|
|
|
|
|
|
|
|
|
|
|
|
|
|
|
|
|
|
|
|
|
|
|
|
|
|
|
|
|
Приложение 2 |
|
|
|
|
|
|
|
|
|
|
|
|
|
|
|
|
|
|
|
|
|
|
|
|
|
|
|
|
|
|
|
|
|
|
Форма 6 |
|
|
|
|
|
|
|
|
|
|
|
|
|
|
|
|
|
|
|
|
|
|
|
|
|
|
|
|
|
|
|
|
|
Лист 1 |
|
|
|
|
|
|
|
|
|
|
|
|
|
|
|
Маршрутный лист |
|
|
|
|
|
|
|
|
|
|
|
|
|
|||||
|
|
|
Маршрутный лист №144 |
|
|
Номер |
|
Цех/уч. |
|
|
Номер |
|
|
|
|
Наименование |
|
|
|
Шифр заказа |
|||||||||||||
|
|
|
|
|
|
|
|
|
|
|
|
|
задан |
|
|
|
|
детали |
|
|
|
|
|
|
|
|
|
|
|
|
|
||
|
|
|
Заготовка |
|
|
|
|
01 |
|
5/1 |
|
|
Зу 4390-031 |
|
|
|
|
Дроссель |
|
|
|
20011000 |
|||||||||||
|
Вид |
|
Марка мат. |
|
Размер |
|
|
Вес |
|
Шифр |
Маршрут |
|
Место хранения в цехе |
|
Кол. на прог. |
|
Выдано в |
|
|
Подпись ПДО |
|||||||||||||
|
|
|
|
|
|
|
|
|
|
|
|
гр. обра- |
|
|
|
|
|
|
|
|
|
|
|
|
|
работу |
|
|
|
||||
|
|
|
|
|
|
|
|
|
|
|
|
ботки |
|
|
|
|
|
|
|
|
|
|
|
|
|
|
|
|
|
|
|
||
Пруток |
|
СТ-45 |
|
Ǿ 50х66 |
|
0,25 |
|
|
|
|
10-10/3-10-5- |
|
11/2 |
|
|
|
|
|
6 |
|
|
6 |
|
|
|
|
|||||||
|
|
|
|
|
|
|
|
|
|
|
|
|
|
|
11-5-20-4-(5) |
|
|
Дата получения |
|
|
По номер |
|
Шесть |
|
|
|
|||||||
|
|
|
|
|
|
|
|
|
|
|
|
|
|
|
|
|
|
|
|
|
|
|
|
|
ст-ка |
|
(прописью) |
|
|
|
|||
|
|
|
|
|
|
|
|
|
|
|
|
|
|
|
|
|
|
|
1/IV |
|
|
|
|
|
|
|
|
|
|
|
|
|
|
|
Операция |
|
|
|
|
|
|
Норма |
|
|
|
|
Фамилия |
|
|
|
|
|
|
Принято |
|
|
|
|
|
Дата, подпись, |
|||||||
№ |
Наименование |
|
работыРазряд |
|
Тп.з |
Расцен. |
|
оборуШифр- |
дования |
|
исполнителя |
|
годных |
|
с 1-го |
|
.Исправ |
брак |
|
|
Номер извещения |
|
|
штамп |
|||||||||
|
|
|
|
|
|
|
|
подгот. |
|
|
|
|
|
|
|
предъ- |
|
|
.Окончат |
|
|
|
|
приёмщика |
|||||||||
|
|
|
|
|
|
|
|
|
|
|
|
|
|
|
|
|
|
|
|
|
|
|
|
|
|
|
|
|
|||||
|
|
|
|
|
|
|
|
i ш т |
Расцен. шт. |
|
|
|
|
|
|
|
|
|
явления |
|
|
|
|
|
|
|
|
|
|
|
|||
|
|
|
|
|
|
|
|
|
|
|
|
|
|
|
|
|
|
|
|
|
|
|
|
|
|
|
|
|
|
|
|
||
|
|
|
|
|
|
|
|
|
|
|
|
|
|
|
|
|
|
|
|
|
|
|
|
|
|
|
|
|
|
|
|||
1. |
Токарная |
|
|
3 |
|
12 |
8,26 |
|
|
|
01 |
|
|
|
|
|
|
|
|
|
|
|
|
|
|
|
|
|
|
|
|||
|
|
|
|
|
|
|
|
|
|
|
|
|
|
|
|
|
|
|
|
|
|
|
|
|
|
|
|
|
|
|
|
|
|
|
|
|
|
|
|
|
|
30 |
20,65 |
|
|
|
|
|
|
|
|
|
|
|
|
|
|
|
|
|
|
|
|
|
|
|
|
|
|
|
|
|
|
|
|
|
|
|
|
|
|
|
|
|
|
|
|
|
|
|
|
|
|
|
|
|
|
|
|
||
2. |
Разметка |
|
|
3 |
|
- |
|
- |
|
|
|
91 |
|
|
|
|
|
|
|
|
|
|
|
|
|
|
|
|
|
|
|
||
|
|
|
|
|
|
|
|
|
|
|
|
|
|
|
|
|
|
|
|
|
|
|
|
|
|
|
|
|
|
|
|
|
|
|
|
|
|
|
|
|
|
7 |
|
4,82 |
|
|
|
|
|
|
|
|
|
|
|
|
|
|
|
|
|
|
|
|
|
|
|
|
|
|
|
|
|
|
|
|
|
|
|
|
|
|
|
|
|
|
|
|
|
|
|
|
|
|
|
|
|
||||
3. |
Верт. фрез. |
|
3 |
|
12 |
8,26 |
|
|
|
12 |
|
|
|
|
|
|
|
|
|
|
|
|
|
|
|
|
|
|
|
||||
|
|
|
|
|
|
|
|
|
|
|
|
|
|
|
|
|
|
|
|
|
|
|
|
|
|
|
|
|
|
|
|
|
|
|
|
|
|
|
|
|
|
10 |
6,88 |
|
|
|
|
|
|
|
|
|
|
|
|
|
|
|
|
|
|
|
|
|
|
|
|
|
|
|
|
|
|
|
|
|
|
|
|
|
|
|
|
|
|
|
|
|
|
|
|
|
|
|
|
|
|
|
|||
4. |
Верт. сверл. |
|
3 |
|
8 |
|
4,83 |
|
|
|
21 |
|
|
|
|
|
|
|
|
|
|
|
|
|
|
|
|
|
|
|
|||
|
|
|
|
|
|
|
|
|
|
|
|
|
|
|
|
|
|
|
|
|
|
|
|
|
|
|
|
|
|
|
|
|
|
|
|
|
|
|
|
|
|
3 |
|
1,81 |
|
|
|
|
|
|
|
|
|
|
|
|
|
|
|
|
|
|
|
|
|
|
|
|
|
|
|
|
|
|
|
|
|
|
|
|
|
|
|
|
|
|
|
|
|
|
|
|
|
|
|
|
|
||||
5. |
Гор. фрез. |
|
3 |
|
10 |
6,88 |
|
|
|
10 |
|
|
|
|
|
|
|
|
|
|
|
|
|
|
|
|
|
|
|
||||
|
|
|
|
|
|
|
|
|
|
|
|
|
|
|
|
|
|
|
|
|
|
|
|
|
|
|
|
|
|
|
|
|
|
|
|
|
|
|
|
|
|
5 |
|
3,44 |
|
|
|
|
|
|
|
|
|
|
|
|
|
|
|
|
|
|
|
|
|
|
|
|
|
|
|
|
|
|
|
|
|
|
|
|
|
|
|
|
|
|
|
|
|
|
|
|
|
|
|
|
|
|
|
||
6. |
Разметка |
|
|
3 |
|
- |
|
- |
|
|
|
91 |
|
|
|
|
|
|
|
|
|
|
|
|
|
|
|
|
|
|
|
||
|
|
|
|
|
|
|
|
|
|
|
|
|
|
|
|
|
|
|
|
|
|
|
|
|
|
|
|
|
|
|
|
|
|
|
|
|
|
|
|
|
|
2 |
|
1,38 |
|
|
|
|
|
|
|
|
|
|
|
|
|
|
|
|
|
|
|
|
|
|
|
|
|
|
|
|
|
|
|
|
|
|
|
|
|
|
|
|
|
|
|
|
|
|
|
|
|
|
|
|
|
||||
7. |
Гор. фрез. |
|
3 |
|
12 |
8,26 |
|
|
|
10 |
|
|
|
|
|
|
|
|
|
|
|
|
|
|
|
|
|
|
|
||||
|
|
|
|
|
|
|
|
|
|
|
|
|
|
|
|
|
|
|
|
|
|
|
|
|
|
|
|
|
|
|
|
|
|
|
|
|
|
|
|
|
|
1 |
|
6,88 |
|
|
|
|
|
|
|
|
|
|
|
|
|
|
|
|
|
|
|
|
|
|
|
|
|
|
|
|
|
|
|
|
|
|
|
|
|
|
|
|
|
|
|
|
|
|
|
|
|
|
|
|
|
|
|
|
|

Талон № 1 на выдачу заготовок (литья) к маршрутному листу № 144
Цех № |
Шифр заказа |
Номер |
|
|
задания |
5/1 |
20011000 |
|
Деталь № |
|
Склад № |
ЗУ 4390 – 031 |
|
92 |
Наименование |
|
Место |
|
|
хранения |
Дроссель |
|
6/6 |
Размер, марка |
|
Отпущено шт. |
|
|
|
|
|
6 |
Дата |
|
Отпустил |
30/III |
|
Иванов |
------------------отреза Линия------------------
134
Форма 6 Лист 2
Талон № 2 на выдачу заготовок (литья) к маршрутному листу № 144
Цех № |
Шифр заказа |
кальк. гр. |
Номер |
|
|
|
задания |
5/1 |
20011000 |
|
|
Деталь № |
|
Склад № |
Номенкл. № |
ЗУ 4390 – 031 |
|
92 |
|
Наименование |
|
Марка, размер |
|
|
|
|
|
Дроссель |
|
|
|
Поставщик, |
Отпущено к-во |
Цена |
Сумма |
дата |
|
|
|
поступления |
|
|
|
|
|
|
|
Дата |
Отпустил |
|
Получил |
30/III |
Иванов |
|
Васильев |

135
Приложение 3 Таблица
Оперограмма движения маршрутного листа
|
|
|
|
|
|
|
|
|
Структурные подразделения и исполнители |
|
||||||||||
|
|
|
|
|
|
|
|
|
|
|
|
|
|
|
|
|
|
|
|
|
|
|
|
|
|
|
|
ПРБ |
|
|
|
|
|
|
|
|
|
||||
№ |
Наименование операций |
|
|
|
(планово- |
|
|
|
|
|
|
|
Склад |
|
||||||
|
ПДО |
распредели- |
ПланировРаспредели- |
|
||||||||||||||||
п/п |
|
|
Кладовая |
|||||||||||||||||
|
|
заготовок |
||||||||||||||||||
|
|
|
|
|
тельное |
|
|
щик |
тель |
|||||||||||
|
|
|
|
|
|
|
|
|
||||||||||||
|
|
|
|
|
|
|
|
|
|
|||||||||||
|
|
|
|
|
|
бюро) |
|
|
|
|
|
|
|
|
|
|||||
|
|
|
|
|
|
|
|
|
|
|
|
|
|
|
|
|
|
|
|
|
1 |
Передача маршрутного листа |
|
|
|
|
|
|
|
|
|
|
|
|
|
|
|
|
|
|
|
|
(1) с талонами на получение |
|
|
2 |
|
|
|
|
2 |
|
|
|
|
|
|
|
|
|
|
|
|
заготовок (2) и регистрация |
|
|
|
|
|
|
|
|
|
|
|
|
|
|
|
|
|||
|
|
1 |
|
|
1 |
|
|
|
|
|
|
|
|
|
|
|
|
|
||
|
|
2 |
|
|
2 |
|
|
|
|
|
|
|
|
|
|
|||||
|
поступления листа |
|
|
|
|
|
|
|
|
|
|
|
|
|
|
|
|
|||
|
|
|
|
|
|
|
|
|
|
|
|
|
|
|
|
|
|
|
|
|
|
|
|
|
|
|
|
|
|
|
|
|
|
|
|
|
|
|
|
|
|
|
|
|
|
|
|
|
|
|
|
|
|
|
|
|
|
|
|
|
|
|
2 |
Регистрация маршрутных |
|
|
|
|
|
|
|
|
|
|
|
|
|
|
|
|
|
|
|
|
листов в подетальных |
|
|
|
|
|
|
|
|
|
|
|
|
|
2 |
|
|
|
|
|
|
заданиях (дата, номер) (3) |
|
|
|
|
|
|
|
|
|
|
|
1 |
|
|
|
|
|
|
|
|
|
|
|
|
|
|
3 |
|
|
|
|
|
|
|
|
|
||||
|
|
|
|
|
|
|
|
|
|
2 |
|
|
|
|
||||||
|
|
|
|
|
|
|
|
|
|
|
|
|
|
|
|
|
||||
|
|
|
|
|
|
|
|
|
|
|
|
|
|
|
|
|
|
|
||
|
|
|
|
|
|
|
|
|
|
|
|
|
|
|
|
|
|
|
|
|
|
|
|
|
|
|
|
|
|
|
|
|
|
|
|
|
|
|
|
|
|
|
|
|
|
|
|
|
|
|
|
|
|
|
3 |
|
|
|
|
|
||
|
|
|
|
|
|
|
|
|
|
|
|
|
|
|
|
|
|
|
||
|
|
|
|
|
|
|
|
|
|
|
|
|
|
|
|
|
|
|
|
|
3 Передача двух экземпляров талонов для получения 2 заготовок
2

136
4 Комплектация заготовок на |
|
|
|
складе и заполнение талонов |
2 |
|
2 |
|
|
||
|
|
|
|
|
2 |
|
|
|
|
|
|
5Поступление партии деталей с одним экземпляром талона в участковую кладовую
2
6Отметка в талоне места хранения деталей в участковой кладовой, даты получения
заготовок, количества |
2 |
7 Передача талона для отметок в маршрутном листе места 1 2 хранения заготовок в кладовой
8Передача талона 2-го экземпляра на склад заготовок
для отметок о выдаче |
2 |
|

137
9 Отметка в подетальном задании о поступлении 1 заготовок на участок
3
138
Приложение 4
Распределение номенклатурного задания по месяцам планового периода
Наименование |
Годовое задание, |
Коэффициент |
|
|
|
|
|
|
|
|
|
|
|
|
|
|
|
|
|
|
|
Месяцы |
|
|
|
|
|
|
|
|
|
|
|
|
|
|
|
||||
изделий |
шт. |
трудоёмкости |
|
I |
|
II |
III |
|
IV |
|
|
V |
|
VI |
VII |
VIII |
IX |
|
X |
|
XI |
XII |
|||||||||||||||||||
А |
64 |
2 |
8 |
|
8 |
|
- |
|
- |
|
8 |
|
8 |
|
8 |
|
8 |
|
- |
|
- |
|
8 |
|
8 |
|
|||||||||||||||
|
|
|
|
|
|
|
|
|
|
|
|
|
|
|
|
|
|
|
|
|
|
|
|
|
|
|
|
|
|
|
|
|
|
|
|
|
|
|
|
|
|
|
|
|
16 |
|
16 |
|
|
|
|
|
|
|
|
|
16 |
|
16 |
|
16 |
|
16 |
|
|
|
|
|
|
|
16 |
|
16 |
|
|||||||||
Б |
40 |
4 |
5 |
|
5 |
|
|
|
|
|
|
|
|
|
5 |
|
5 |
|
5 |
|
5 |
|
|
|
|
|
|
|
5 |
|
5 |
|
|||||||||
|
|
|
|
|
|
|
|
|
|
|
|
|
|
|
|
|
|
|
|
|
|
|
|
|
|
|
|
|
|
|
|
|
|
|
|
|
|
|
|
|
|
|
|
|
20 |
|
20 |
|
|
|
|
|
|
|
|
|
20 |
|
20 |
|
20 |
|
20 |
|
|
|
|
|
|
|
20 |
|
20 |
|
|||||||||
В΄ |
12 |
4 |
- |
|
- |
|
6 |
|
6 |
|
- |
|
- |
|
- |
|
- |
|
- |
|
- |
|
- |
|
- |
|
|||||||||||||||
|
|
|
|
|
|
|
|
|
|
|
|
|
|
|
|
|
|
|
|
|
|
|
|
|
|
|
|
|
|
|
|
|
|
|
|
|
|
|
|
|
|
|
|
|
|
|
|
|
|
|
24 |
|
24 |
|
|
|
|
|
|
|
|
|
|
|
|
|
|
|
|
|
|
|
|
|
|
|
|
|
|
||||
В΄΄ |
10 |
3 |
- |
|
- |
|
5 |
|
5 |
|
- |
|
- |
|
- |
|
- |
|
- |
|
- |
|
- |
|
- |
|
|||||||||||||||
|
|
|
|
|
|
|
|
|
|
|
|
|
|
|
|
|
|
|
|
|
|
|
|
|
|
|
|
|
|
|
|
|
|
|
|
|
|
|
|
||
|
|
|
|
|
|
|
|
|
15 |
|
15 |
|
|
|
|
|
|
|
|
|
|
|
|
|
|
|
|
|
|
|
|
|
|
|
|
|
|
||||
Г΄ |
8 |
4 |
- |
|
- |
|
- |
|
- |
|
- |
|
- |
|
- |
|
- |
|
4 |
|
4 |
|
- |
|
- |
|
|||||||||||||||
|
|
|
|
|
|
|
|
|
|
|
|
|
|
|
|
|
|
|
|
|
|
|
|
|
|
|
|
|
|
|
|
|
|
|
|
|
|
|
|
|
|
|
|
|
|
|
|
|
|
|
|
|
|
|
|
|
|
|
|
|
|
|
|
|
|
|
|
|
|
|
|
16 |
|
16 |
|
|
|
|
|
|
|
||
Г΄΄ |
14 |
3 |
- |
|
- |
|
- |
|
- |
|
- |
|
- |
|
- |
|
- |
|
7 |
|
7 |
|
- |
|
- |
|
|||||||||||||||
|
|
|
|
|
|
|
|
|
|
|
|
|
|
|
|
|
|
|
|
|
|
|
|
|
|
|
|
|
|
|
|
|
|
|
|
|
|
|
|
||
|
|
|
|
|
|
|
|
|
|
|
|
|
|
|
|
|
|
|
|
|
|
|
|
|
|
|
|
|
|
21 |
21 |
|
|
|
|
|
|
||||
Д |
1258 |
1 |
96 |
|
91 |
|
102 |
103 |
94 |
|
107 |
115 |
103 |
110 |
105 |
106 |
120 |
||||||||||||||||||||||||
Итого в приведённых единицах |
|
132 |
127 |
141 |
142 |
130 |
143 |
151 |
139 |
147 |
142 |
142 |
156 |
||||||||||||||||||||||||||||
изделия «Д» |
|
|
|
|
|
|
|
|
|
|
|
|
|
|
|
|
|
|
|
|
|
|
|
|
|
|
|
|
|
|
|
|
|
|
|
|
|
|
|
|
|
Количество рабочих дней в |
|
21 |
|
20 |
|
22 |
|
22 |
|
20 |
|
22 |
|
23 |
|
21 |
|
22 |
|
22 |
|
21 |
|
23 |
|
||||||||||||||||
месяце……… |
|
|
|
|
|
|
|
|
|
|
|
|
|
|
|
|
|
|
|
|
|
|
|
|
|
|
|
|
|
|
|
|
|
|
|
|
|
|
|
|
|
Среднедневной выпуск …… |
|
6,29 |
6,36 |
6,4 |
6,46 |
6,48 |
6,5 |
6,57 |
6,64 |
6,68 |
6,72 |
6,76 |
6,8 |
Примечание: в числителе указано количество изделий в шт., в знаменателе – в приведённых единицах изделий «Д».
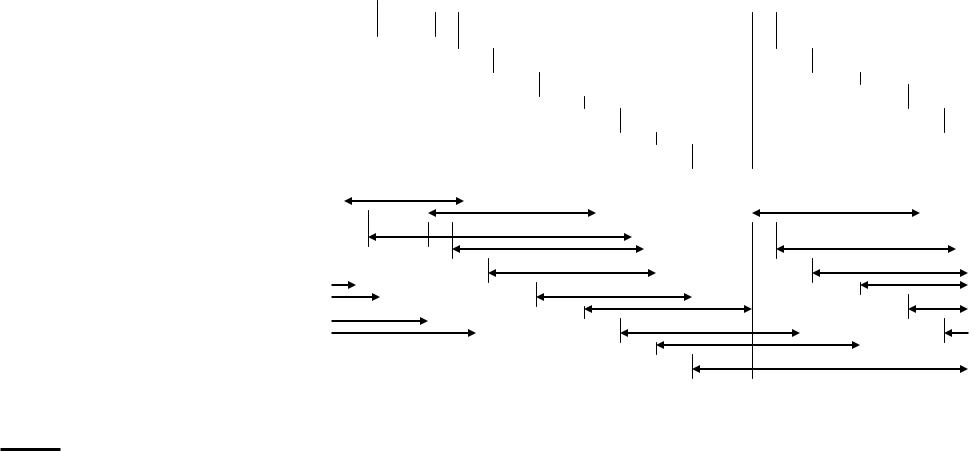
139
Приложение 5
I. Календарный график загрузки агрегатно-сверлильного станка
№ |
Наименование |
Номер |
Периодичность |
|
|
|
|
|
|
|
|
|
|
|
|
|
|
|
|
|
|
|
|
|
|
|
|
|
|
|
|
|
|
|
|
|
|
|
Рабочие дни |
|
|
|
|
|
|
|
|
|
|
|
|
|
|
|
|
|
|
|
|
|
|
|
||||||||||
п/п |
детали |
детали |
запуска |
1 |
|
|
|
2 |
|
3 |
|
4 |
|
5 |
|
6 |
|
|
|
7 |
8 |
9 |
10 |
11 |
12 |
13 |
14 |
15 |
16 |
17 |
18 |
|
|
19 |
20 |
21 |
22 |
23 |
|
|
24 |
|
||||||||||||||||||||||||||||||
|
|
|
|
выпуска |
|
|
|
|
|
|
|
|
|
|
|
|
|
|
|
|||||||||||||||||||||||||||||||||||||||||||||||||||||
|
|
|
|
|
|
|
|
|
|
|
|
|
|
|
|
|
|
|
|
|
|
|
|
|
|
|
|
|
|
|
|
|
|
|
|
|
|
|
|
|
|
|
|
|
|
|
|
|
|
|
|
|
|
|
|
|
|
|
|
|
|
|
|
|
|
|
|
|
|
|||
1. |
Шкив |
02-13 |
|
м |
|
|
|
|
|
|
|
|
|
|
|
|
|
|
|
|
|
|
|
|
|
|
|
|
|
|
|
|
|
|
|
|
|
|
|
|
|
|
|
|
|
|
|
|
|
|
|
|
|
|
|
|
|
|
|
|
|
|
|
|
|
|
|
|
|
|
||
|
|
|
|
|
|
|
|
|
|
|
|
|
|
|
|
|
|
|
|
|
|
|
|
|
|
|
|
|
|
|
|
|
|
|
|
|
|
|
|
|
|
|
|
|
|
|
|
|
|
|
|
|
|
|
|
|
|
|
|
|
|
|
|
|
|
|
||||||
2. |
Вилка |
02-35 |
|
м/2 |
|
|
|
|
|
|
|
|
|
|
|
|
|
|
|
|
|
|
|
|
|
|
|
|
|
|
|
|
|
|
|
|
|
|
|
|
|
|
|
|
|
|
|
|
|
|
|
|
|
|
|
|
|
|
|
|
|
|
|
|
|
|
|
|
|
|
||
|
|
|
|
|
|
|
|
|
|
|
|
|
|
|
|
|
|
|
|
|
|
|
|
|
|
|
|
|
|
|
|
|
|
|
|
|
|
|
|
|
|
|
|
|
|
|
|
|
|
|
|
|
|
|
|
|
|
|
|
|
|
|
|
|
|
|
||||||
3. |
Вилка |
02-36 |
|
м |
|
|
|
|
|
|
|
|
|
|
|
|
|
|
|
|
|
|
|
|
|
|
|
|
|
|
|
|
|
|
|
|
|
|
|
|
|
|
|
|
|
|
|
|
|
|
|
|
|
|
|
|
|
|
|
|
|
|
|
|
|
|
|
|
|
|
||
|
|
|
|
|
|
|
|
|
|
|
|
|
|
|
|
|
|
|
|
|
|
|
|
|
|
|
|
|
|
|
|
|
|
|
|
|
|
|
|
|
|
|
|
|
|
|
|
|
|
|
|
|
|
|
|
|
|
|
|
|
|
|
|
|
|
|
||||||
4. |
Рычаг |
02-40 |
|
м/2 |
|
|
|
|
|
|
|
|
|
|
|
|
|
|
|
|
|
|
|
|
|
|
|
|
|
|
|
|
|
|
|
|
|
|
|
|
|
|
|
|
|
|
|
|
|
|
|
|
|
|
|
|
|
|
|
|
|
|
|
|
|
|
|
|
|
|
||
|
|
|
|
|
|
|
|
|
|
|
|
|
|
|
|
|
|
|
|
|
|
|
|
|
|
|
|
|
|
|
|
|
|
|
|
|
|
|
|
|
|
|
|
|
|
|
|
|
|
|
|
|
|
|
|
|
|
|
|
|
|
|
|
|
|
|
||||||
5. |
Рычаг |
02-41 |
|
м/2 |
|
|
|
|
|
|
|
|
|
|
|
|
|
|
|
|
|
|
|
|
|
|
|
|
|
|
|
|
|
|
|
|
|
|
|
|
|
|
|
|
|
|
|
|
|
|
|
|
|
|
|
|
|
|
|
|
|
|
|
|
|
|
|
|
|
|
||
|
|
|
|
|
|
|
|
|
|
|
|
|
|
|
|
|
|
|
|
|
|
|
|
|
|
|
|
|
|
|
|
|
|
|
|
|
|
|
|
|
|
|
|
|
|
|
|
|
|
|
|
|
|
|
|
|
|
|
|
|
|
|
|
|
|
|
||||||
6. |
Рукоятка |
03-15 |
|
м/2 |
|
|
|
|
|
|
|
|
|
|
|
|
|
|
|
|
|
|
|
|
|
|
|
|
|
|
|
|
|
|
|
|
|
|
|
|
|
|
|
|
|
|
|
|
|
|
|
|
|
|
|
|
|
|
|
|
|
|
|
|
|
|
|
|
|
|
||
|
|
|
|
|
|
|
|
|
|
|
|
|
|
|
|
|
|
|
|
|
|
|
|
|
|
|
|
|
|
|
|
|
|
|
|
|
|
|
|
|
|
|
|
|
|
|
|
|
|
|
|
|
|
|
|
|
|
|
|
|
|
|
|
|
|
|
||||||
|
|
|
|
|
|
|
|
|
|
|
|
|
|
|
|
|
|
|
|
|
|
|
|
|
|
|
|
|
|
|
|
|
|
|
|
|
|
|
|
|
|
|
|
|
|
|
|
|
|
|
|
|
|
|
|
|
|
|
|
|
|
|
|
|
|
|
|
|
|
|
|
|
7. |
Вилка |
07-29 |
|
м/2 |
|
|
|
|
|
|
|
|
|
|
|
|
|
|
|
|
|
|
|
|
|
|
|
|
|
|
|
|
|
|
|
|
|
|
|
|
|
|
|
|
|
|
|
|
|
|
|
|
|
|
|
|
|
|
|
|
|
|
|
|
|
|
|
|
|
|
||
|
|
|
|
|
|
|
|
|
|
|
|
|
|
|
|
|
|
|
|
|
|
|
|
|
|
|
|
|
|
|
|
|
|
|
|
|
|
|
|
|
|
|
|
|
|
|
|
|
|
|
|
|
|
|
|
|
|
|
|
|
|
|
|
|
|
|
||||||
8. |
Вилка |
07-30 |
|
м/2 |
|
|
|
|
|
|
|
|
|
|
|
|
|
|
|
|
|
|
|
|
|
|
|
|
|
|
|
|
|
|
|
|
|
|
|
|
|
|
|
|
|
|
|
|
|
|
|
|
|
|
|
|
|
|
|
|
|
|
|
|
|
|
|
|
|
|
||
|
|
|
|
|
|
|
|
|
|
|
|
|
|
|
|
|
|
|
|
|
|
|
|
|
|
|
|
|
|
|
|
|
|
|
|
|
|
|
|
|
|
|
|
|
|
|
|
|
|
|
|
|
|
|
|
|
|
|
|
|
|
|
|
|
|
|
||||||
9. |
Вилка |
07-32 |
|
м |
|
|
|
|
|
|
|
|
|
|
|
|
|
|
|
|
|
|
|
|
|
|
|
|
|
|
|
|
|
|
|
|
|
|
|
|
|
|
|
|
|
|
|
|
|
|
|
|
|
|
|
|
|
|
|
|
|
|
|
|
|
|
|
|
|
|
||
|
|
|
|
|
|
|
|
|
|
|
|
|
|
|
|
|
|
|
|
|
|
|
|
|
|
|
|
|
|
|
|
|
|
|
|
|
|
|
|
|
|
|
|
|
|
|
|
|
|
|
|
|
|
|
|
|
|
|
|
|
|
|
|
|
|
|
||||||
10. |
Рычаг |
07-33 |
|
м |
|
|
|
|
|
|
|
|
|
|
|
|
|
|
|
|
|
|
|
|
|
|
|
|
|
|
|
|
|
|
|
|
|
|
|
|
|
|
|
|
|
|
|
|
|
|
|
|
|
|
|
|
|
|
|
|
|
|
|
|
|
|
|
|
|
|
||
|
|
|
|
|
|
|
|
|
|
|
|
|
|
|
|
|
|
|
|
|
|
|
|
|
|
|
|
|
|
|
|
|
|
|
|
|
|
|
|
|
|
|
|
|
|
|
|
|
|
|
|
|
|
|
|
|
|
|
|
|
|
|
|
|
|
|
||||||
|
|
II. |
Нормативный график запуска-выпуска партий деталей на участке |
|
|
|
|
|
|
|
|
|
|
|
|
|
|
|
|
|
|
|
||||||||||||||||||||||||||||||||||||||||||||||||||
1. |
Шкив |
02-13 |
|
м |
|
|
|
|
|
|
|
|
|
|
|
|
|
|
|
|
|
|
|
|
|
|
|
|
|
|
|
|
|
|
|
|
|
|
|
|
|
|
|
|
|
|
|
|
|
|
|
|
|
|
|
|
|
|
|
|
|
|
|
|
|
|
|
|
|
|
|
|
|
|
|
|
|
|
|
|
|
|
|
|
|
|
|
|
|
|
|
|
|
|
|
|
|
|
|
|
|
|
|
|
|
|
|
|
|
|
|
|
|
|
|
|
|
|
|
|
|
|
|
|
|
|
|
|
|
|
|
|
|
|
|
|
|
|
|
|
|
||||
2. |
Вилка |
02-35 |
|
м/2 |
|
|
|
|
|
|
|
|
|
|
|
|
|
|
|
|
|
|
|
|
|
|
|
|
|
|
|
|
|
|
|
|
|
|
|
|
|
|
|
|
|
|
|
|
|
|
|
|
|
|
|
|
|
|
|
|
|
|
|
|
|
|
|
|
|
|
|
|
|
|
|
|
|
|
|
|
|
|
|
|
|
|
|
|
|
|
|
|
|
|
|
|
|
|
|
|
|
|
|
|
|
|
|
|
|
|
|
|
|
|
|
|
|
|
|
|
|
|
|
|
|
|
|
|
|
|
|
|
|
|
|
|
|
|
|
|
|
||||
3. |
Вилка |
02-36 |
|
м |
|
|
|
|
|
|
|
|
|
|
|
|
|
|
|
|
|
|
|
|
|
|
|
|
|
|
|
|
|
|
|
|
|
|
|
|
|
|
|
|
|
|
|
|
|
|
|
|
|
|
|
|
|
|
|
|
|
|
|
|
|
|
|
|
|
|
|
|
|
|
|
|
|
|
|
|
|
|
|
|
|
|
|
|
|
|
|
|
|
|
|
|
|
|
|
|
|
|
|
|
|
|
|
|
|
|
|
|
|
|
|
|
|
|
|
|
|
|
|
|
|
|
|
|
|
|
|
|
|
|
|
|
|
|
|
|
|
||||
4. |
Рычаг |
02-40 |
|
м/2 |
|
|
|
|
|
|
|
|
|
|
|
|
|
|
|
|
|
|
|
|
|
|
|
|
|
|
|
|
|
|
|
|
|
|
|
|
|
|
|
|
|
|
|
|
|
|
|
|
|
|
|
|
|
|
|
|
|
|
|
|
|
|
|
|
|
|
|
|
|
|
|
|
|
|
|
|
|
|
|
|
|
|
|
|
|
|
|
|
|
|
|
|
|
|
|
|
|
|
|
|
|
|
|
|
|
|
|
|
|
|
|
|
|
|
|
|
|
|
|
|
|
|
|
|
|
|
|
|
|
|
|
|
|
|
|
|
|
||||
5. |
Рычаг |
02-41 |
|
м/2 |
|
|
|
|
|
|
|
|
|
|
|
|
|
|
|
|
|
|
|
|
|
|
|
|
|
|
|
|
|
|
|
|
|
|
|
|
|
|
|
|
|
|
|
|
|
|
|
|
|
|
|
|
|
|
|
|
|
|
|
|
|
|
|
|
|
|
|
|
|
|
|
|
|
|
|
|
|
|
|
|
|
|
|
|
|
|
|
|
|
|
|
|
|
|
|
|
|
|
|
|
|
|
|
|
|
|
|
|
|
|
|
|
|
|
|
|
|
|
|
|
|
|
|
|
|
|
|
|
|
|
|
|
|
|
|
|
|
||||
6. |
Рукоятка |
03-15 |
|
м/2 |
|
|
|
|
|
|
|
|
|
|
|
|
|
|
|
|
|
|
|
|
|
|
|
|
|
|
|
|
|
|
|
|
|
|
|
|
|
|
|
|
|
|
|
|
|
|
|
|
|
|
|
|
|
|
|
|
|
|
|
|
|
|
|
|
|
|
|
|
|
|
|
|
|
|
|
|
|
|
|
|
|
|
|
|
|
|
|
|
|
|
|
|
|
|
|
|
|
|
|
|
|
|
|
|
|
|
|
|
|
|
|
|
|
|
|
|
|
|
|
|
|
|
|
|
|
|
|
|
|
|
|
|
|
|
|
|
|
||||
|
|
|
|
|
|
|
|
|
|
|
|
|
|
|
|
|
|
|
|
|
|
|
|
|
|
|
|
|
|
|
|
|
|
|
|
|
|
|
|
|
|
|
|
|
|
|
|
|
|
|
|
|
|
|
|
|
|
|
|
|
|
|
|
|
|
|
|
|
|
|
|
|
7. |
Вилка |
07-29 |
|
м/2 |
|
|
|
|
|
|
|
|
|
|
|
|
|
|
|
|
|
|
|
|
|
|
|
|
|
|
|
|
|
|
|
|
|
|
|
|
|
|
|
|
|
|
|
|
|
|
|
|
|
|
|
|
|
|
|
|
|
|
|
|
|
|
|
|
|
|
|
|
|
|
|
|
|
|
|
|
|
|
|
|
|
|
|
|
|
|
|
|
|
|
|
|
|
|
|
|
|
|
|
|
|
|
|
|
|
|
|
|
|
|
|
|
|
|
|
|
|
|
|
|
|
|
|
|
|
|
|
|
|
|
|
|
|
|
|
|
|
||||
8. |
Вилка |
07-30 |
|
м/2 |
|
|
|
|
|
|
|
|
|
|
|
|
|
|
|
|
|
|
|
|
|
|
|
|
|
|
|
|
|
|
|
|
|
|
|
|
|
|
|
|
|
|
|
|
|
|
|
|
|
|
|
|
|
|
|
|
|
|
|
|
|
|
|
|
|
|
|
|
|
|
|
|
|
|
|
|
|
|
|
|
|
|
|
|
|
|
|
|
|
|
|
|
|
|
|
|
|
|
|
|
|
|
|
|
|
|
|
|
|
|
|
|
|
|
|
|
|
|
|
|
|
|
|
|
|
|
|
|
|
|
|
|
|
|
|
|
|
||||
9. |
Вилка |
07-32 |
|
м |
|
|
|
|
|
|
|
|
|
|
|
|
|
|
|
|
|
|
|
|
|
|
|
|
|
|
|
|
|
|
|
|
|
|
|
|
|
|
|
|
|
|
|
|
|
|
|
|
|
|
|
|
|
|
|
|
|
|
|
|
|
|
|
|
|
|
|
|
|
|
|
|
|
|
|
|
|
|
|
|
|
|
|
|
|
|
|
|
|
|
|
|
|
|
|
|
|
|
|
|
|
|
|
|
|
|
|
|
|
|
|
|
|
|
|
|
|
|
|
|
|
|
|
|
|
|
|
|
|
|
|
|
|
|
|
|
|
||||
10. |
Рычаг |
07-33 |
|
м |
|
|
|
|
|
|
|
|
|
|
|
|
|
|
|
|
|
|
|
|
|
|
|
|
|
|
|
|
|
|
|
|
|
|
|
|
|
|
|
|
|
|
|
|
|
|
|
|
|
|
|
|
|
|
|
|
|
|
|
|
|
|
|
|
|
|
|
|
|
|
|
|
|
|
|
|
|
|
|
|
|
|
|
|
|
|
|
|
|
|
|
|
|
|
|
|
|
|
|
|
|
|
|
|
|
|
|
|
|
|
|
|
|
|
|
|
|
|
|
|
|
|
|
|
|
|
|
|
|
|
|
|
|
|
|
|
|
м – месячная периодичность запуска-выпуска партий м/2 – полумесячная периодичность запуска-выпуска партий
Длительность цикла обработки партии деталей на первой операции (агрегатно-сверлильном станке) Длительность цикла обработки партии деталей на участке
Длительность цикла обработки партии деталей, переходящей на следующий месяц.
Рис. 11. План-график запуска-выпуска деталей