
Учебники / Акуленок М.В. Основы менеджмента риска
.pdf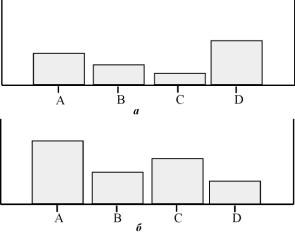
Результаты оценки мероприятий для преодоления рассматриваемых проблем (т.е. разработанных мероприятий для групп дефектов: A - трещин; B - царапин; C - раковин; D - деформаций) по возможным срокам реализации и по финансовым затратам показаны на рис.2.7.
Рис.2.7. Диаграммы анализа временных (а) и финансовых (б) затрат на мероприятия по соответствующим группам дефектов: A - трещинам; B - царапинам; C - раковинам; D - деформациям
2.4. Диаграмма «галстук-бабочка»
Диаграмма «галстук-бабочка» представляет собой схематичное описание и анализ путей развития опасного события от причин до последствий (рис.2.8). В данной диаграмме особое значение имеют барьеры (или управленческие действия), отражающие механизмы, препятствующие возникновению и эскалации риска. Для построения диаграммы «галстук-бабочка» могут быть использованы данные ПСД и других методов оценки риска (например, ETA, FTA и т.д.), которые были применены на предыдущих этапах исследования. Данная диаграмма особенно полезна в сложных ситуациях, так как она позволяет использовать количественные оценки.
31
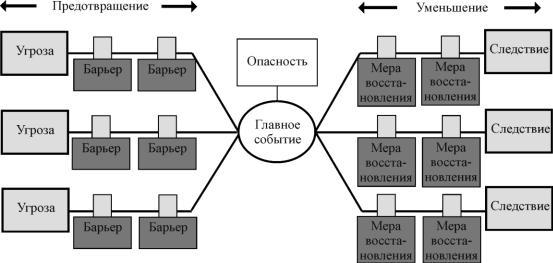
32
Рис.2.8. Вид диаграммы «галстук-бабочка»
Перечислим преимущества и недостатки данного метода. Преимущества:
простое, наглядное, графическое представление проблемы;
ориентация на средства управления и предупреждение эскалации проблемы;
возможность применения и к негативным, и к положительным рискам;
не требует наличия высококвалифицированных экспертов. Недостатки:
невозможность работать с совокупностью причин;
возможность чрезмерного упрощения сложной ситуации. Для построения диаграммы необходимы точные знания о ходе
развития событий от причин до последствий.
Порядок построения диаграммы включает следующие этапы:
1.Описание «центрального узла» (главного анализируемого
риска).
2.Составление перечня основных причин, их возможное количественное описание.
3.Идентификация механизмов развития событий от причин до «центрального узла».
4.Соединение причин и центрального события, иллюстрирующее пути эскалации.
5.Определение барьеров (преград) на пути развития причин.
6.Определение возможных последствий реализации главного анализируемого риска. Соединение последствий с «центральным узлом» линиями.
7.Определение барьеров на пути к последствиям главного
риска.
8.Устанавление вспомогательных управленческих действий. Пример диаграммы для анализа риска пропуска дефектного из-
делия на этапе выходного контроля приведен на рис.2.9.
33
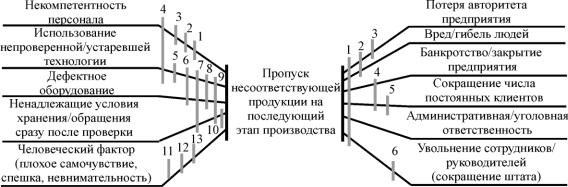
34
Рис.2.9. Пример диаграммы «галстук-бабочка».
Левая часть диаграммы, 1 - 13 - управленческие барьеры: |
10. |
Проведение аудита (внутренний/внешний) условий хра- |
|
1. |
Курсы повышения квалификации. |
|
нения. |
2. |
Разработка профильной образовательной программы, це- |
11. |
Создание рабочей обстановки (освещение, температура, |
|
левая подготовка. |
|
шум и т.д.) |
3. |
Предоставление специального материала/литературы для |
12. |
Перепроверка, повторный контроль (с уменьшенной вы- |
|
самообразования сотрудников (индивидуально). |
|
боркой). |
4. |
Посещение тематических выставок. |
13. |
Введение премии (поощрение). |
5. |
Изучение рынка и внедрение новых современных ме- |
|
|
|
тодов. |
Правая часть диаграммы, 1 - 6 - меры восстановления: |
|
6. Замена оборудования в течение гарантийного срока экс- |
1. Выходной контроль (увеличение выборки). |
||
|
плуатации. |
2. Отзыв готовой продукции. |
|
7. |
Амортизация основных средств на оборудование. |
3. Резервный финансовый фонд (неустойка/компенсация). |
|
8. Разработка плана-графика проведения поверок/калибровки, |
4. Продажа с большой скидкой (отклонение некритическое). |
||
|
назначение ответственного. |
5. Переоформление договора/дополнительного соглашения |
|
9. |
Приглашение специалиста для выявления конкретного |
|
(внесение новых условий). |
|
дефекта оборудования, устранения проблем. |
6. Предупреждение/выговор/штраф/понижение в должности |
2.5. Анализ видов и последствий отказов
Анализ видов и последствий отказов (англ. FMEA - Failure Mode and Effects Analysis), изначально разработанный и опубликованный воен- но-промышленным комплексом США в форме стандарта MIL-STD-1629, является сегодня настолько популярным, что в некоторых отраслях промышленности и даже на отдельных предприятиях разработаны и опубликованы специализированные стандарты, посвященные FMEA. Требования к проведению данного анализа внесены в ряд стандартов Международной электротехнической комиссии (например, серия МЭК 60300-2003 и МЭК 60812-1985), национальных стандартов (например, стандарты серий ГОСТ Р 27.002-89, ГОСТ Р 27.301-95 и ГОСТ Р 27.310-95), отраслевых (например, стандарты серии ГОСТ Р 51814), а также в стандарты ВВС США, аэрокосмической отрасли, полупроводниковой промышленности, автомобильной промышленности, корпораций Toyota и Ford Motors.
Метод FMEA позволяет исследовать цепочки событий с анализом последствий и возможных решений. Применим для отказов (несоответствий) различной природы. Однако требует больших объемов данных и знаний об объекте.
Метод FMEA дает возможность выявить дефекты, обусловливающие наибольший риск потребителя, определить их потенциальные причины, разработать предупреждающие и корректирующие действия, позволяющие предотвратить потенциальные затраты на исправление дефектов. Поэтому, как правило, метод FMEA применяется к новой разрабатываемой продукции или процессу, оценивая риски потребителя (при анализе продукции) и риски внутреннего потребителя (для процессов).
Разновидности метода FMEA представлены на рис.2.10.
АВПКО объекта |
АВПКО процесса |
|
|
|
|
Анализ воздействия |
Анализ воздействия |
Анализ воздействия опе- |
отказа элемента объ- |
операции на конеч- |
рации на технологический |
екта |
ный продукт |
процесс |
|
|
|
Критический отказ |
Критический отказ |
Критический отказ вызы- |
вызывает отказ объ- |
вызывает критиче- |
вает остановку технологи- |
екта и может привес- |
ский дефект про- |
ческого процесса, влияет |
ти к аварийному со- |
дукта |
на безопасность персонала |
стоянию |
|
и окружающей среды |
|
|
|
Рис.2.10. Разновидности анализа видов и последствий отказов
35
Метод FMEA дает возможность идентифицировать все виды отказов частей (элементов) системы, последствия и механизмы отказов, способы смягчения последствий, а также оценить общую критичность любого отказа. Под критичностью понимают совокупность признаков, характеризующих последствия отказа, при этом оценка критичности может быть количественная, качественная и смешанная.
Следует помнить, что данный вид исследования проводят для конкретных условий, конкретного этапа ЖЦП, ситуации и т.п. Это связано, в частности с трудоемкостью и дороговизной проведения таких исследований без соответствующей направленности (или спецификации). Кроме того, метод используют только для отдельных отказов, но не для их сочетания.
Главными целями метода FMEA являются обоснование, проверка достаточности, оценка эффективности и контроль за реализацией управленческих решений, направленных на совершенствование конструкции, технологии изготовления, правил эксплуатации, систем технического обслуживания ремонта объекта и обеспечивающих предупреждение возникновения и/или ослабления тяжести возможных последствий его отказа; достижение требуемых характеристик безопасности, экологичности, эффективности и надежности.
В ходе анализа могут решаться следующие задачи:
идентификация (выявление) возможных отказов;
изучение причин и последствий отказов;
качественная и количественная оценка последствий отказов;
формирование перечня критичных элементов (процессов);
оценка достаточности мер, средств и методов контроля, диагностики, а также обоснование необходимости новых действий;
разработка предложений по изменению конструкции и/или технологического процесса;
оценка достаточности мер, средств, обслуживания и профилак-
тики;
анализ правил эксплуатации;
анализ правил поведения в экстренных ситуациях;
анализ возможных ошибок персонала.
Технология FMEA включает следующие этапы:
решение о проведении анализа и планирование. Определение целей, спецификаций, разработка необходимых шкал (см. табл.2.3, 2.4);
построение компонентной, структурной, функциональной и потоковой моделей объекта анализа (в зависимости от объекта, цели и ситуации);
36
исследование моделей, при котором определяются:
-потенциальные дефекты для каждого элемента конструкции на основе компонентной модели объекта анализа;
-потенциальные причины дефектов с применением причинноследственного анализа;
-потенциальные последствия дефектов продукции для потребителя (или несоответствий процесса для внутренних потребителей) с использованием структурной и потоковой диаграмм; возможности контроля дефектов; вероятности обнаружения их;
-тяжесть последствий для потребителя;
-частота возникновения дефектов;
-интегральный параметр риска потребителя;
разработка корректирующих и предупреждающих действий по результатам анализа;
подготовка отчета (примерная форма приведена в Приложении 8). Метод FMEA получил развитие в виде FMECA, включающего ана-
лиз видов, последствий и критичности отказов.
Общая критичность i-го элемента объекта RPN рассчитывается как
RPN Si Oi Di ,
где Si - оценка тяжести последствий отказа (или дефекта) i-гo элемента; Oi - оценка частоты (вероятности) наступления потенциального отказа i-го элемента; Di - оценка вероятности необнаружения (или невыявления) отказа (дефекта) i-го элемента до его проявления у потребителя.
Значения показателей определяют по соответствующим таблицам (например, табл.2.3 - 2.5), при этом, как правило, все эти целочисленные показатели изменяются в диапазоне от 1 до 10.
|
|
Таблица 2.3 |
Пример количественной (балльной) оценки вероятности |
||
|
|
|
Ожидаемая частота |
Ассоциируемая вероятность |
Балл |
отказа |
отказа (пример) |
|
Частый отказ |
Р > 0,2 |
10 |
|
|
9 |
Вероятный отказ |
0,1 < Р < 0,2 |
8 |
|
|
7 |
Редкий отказ |
0,01 < Р < 0,09 |
6 |
|
|
5 |
Очень редкий отказ |
0,001 < Р < 0,01 |
4 |
|
|
3 |
Невероятный отказ |
Р < 0,001 |
2 |
|
|
1 |
|
|
37 |

Таблица 2.4
Пример ранжирования тяжести последствий отказов по МЭК 60812
Тяжесть |
Критерий |
Ранг |
последствий |
|
|
Отсутствует |
Нет последствий |
1 |
|
|
|
Очень не- |
Отделка (шумность) объекта не соответствует |
2 |
значитель- |
требованиям. Дефект замечают требовательные |
|
ная |
клиенты (менее 25 %) |
|
Незначи- |
Отделка (шумность) объекта не соответствует |
3 |
тельная |
требованиям. Дефект замечают 50 % клиентов |
|
Очень низ- |
Отделка (шумность) объекта не соответствует |
4 |
кая |
требованиям. Дефект замечают большинство |
|
|
клиентов (более 75 %) |
|
Низкая |
Транспортное средство работоспособно, но сис- |
5 |
|
тема комфорта/удобства работает на ослаблен- |
|
|
ном уровне, малоэффективна. Клиент испытыва- |
|
|
ет некоторую неудовлетворенность |
|
Умеренная |
Транспортное средство/узел работоспособны, |
6 |
|
но система комфорта/удобства неработоспособна. |
|
|
Клиент испытывает дискомфорт |
|
Высокая |
Транспортное средство/узел работоспособны, |
7 |
|
но на сниженном уровне эффективности. |
|
|
Клиент очень неудовлетворен |
|
Очень высо- |
Транспортное средство/узел неработоспособны |
8 |
кая |
(потеря основной функции) |
|
|
|
|
Опасная с |
Очень высокий уровень тяжести последствий, |
9 |
предупреж- |
когда потенциальный вид отказа влияет на безо- |
|
дением об |
пасность работы транспортного средства и/или |
|
опасности |
вызывает несоответствие обязательным требова- |
|
|
ниям безопасности с предупреждением об опас- |
|
|
ности |
|
Опасная без |
Очень высокий уровень тяжести последствий, |
10 |
предупреж- |
когда потенциальный вид отказа влияет на без- |
|
дения об |
опасность работы транспортного средства и/или |
|
опасности |
вызывает несоответствие обязательным требова- |
|
|
ниям без предупреждения об опасности |
|
38 |
|
|
Таблица 2.5
Пример оценки ненаблюдаемости отказа
Характеристика |
Критерий - возможность обнаружения вида |
Ранг |
обнаружения |
отказов на основе предусмотренных опера- |
|
|
ций контроля |
|
Практически |
Предусмотренный проектом контроль почти |
1 |
стопроцентно |
всегда обнаруживает потенциальную причи- |
|
|
ну/механизм и следующий вид отказа |
|
Очень хорошее |
Очень высокая вероятность, что предусмотрен- |
2 |
|
ный проектом контроль обнаружит потенци- |
|
|
альную причину/механизм и последующий вид |
|
|
отказа |
|
Хорошее |
Высокая вероятность, что предусмотренный |
3 |
|
проектом контроль обнаружит потенциальную |
|
|
причину/механизм и последующий вид отказа |
|
Умеренно хо- |
Умеренная вероятность, что предусмотренный |
4 |
рошее |
проектом контроль обнаружит потенциальную |
|
|
причину/механизм и последующий вид отказа |
|
Умеренное |
Умеренная вероятность, что предусмотренный |
5 |
|
проектом контроль обнаружит потенциальную |
|
|
причину/механизм и последующий вид отказа |
|
Слабое |
Низкая вероятность, что предусмотренный про- |
6 |
|
ектом контроль обнаружит потенциальную |
|
|
причину/механизм и последующий вид отказа |
|
Очень слабое |
Очень низкая вероятность, что предусмотрен- |
7 |
|
ный проектом контроль обнаружит потенци- |
|
|
альную причину/механизм и последующий вид |
|
|
отказа |
|
Плохое |
Маловероятно, что предусмотренный проектом |
8 |
|
контроль обнаружит потенциальную причи- |
|
|
ну/механизм и последующий вид отказа |
|
Очень плохое |
Почти невероятно, что предусмотренный про- |
9 |
|
ектом контроль обнаружит потенциальную |
|
|
причину/механизм и последующий вид отказа |
|
Практически |
Предусмотренный проектом контроль не мо- |
10 |
невозможно |
жет обнаружить потенциальную причи- |
|
|
ну/механизм и последующий вид отказа, или |
|
|
контроль не предусмотрен |
|
|
|
39 |
Контрольные вопросы
1.В каком нормативном документе представлены основные методы оценки рисков?
2.Какие методы могут быть применены для идентификации рисков?
3.Какие источники рисков присутствуют в процессах жизненного цикла продукции?
4.Что приводит к возникновению барьеров в процессе интервью?
5.В чем состоят отличия оценочного листа, опросного и чек-
листа?
6.Что влияет на установление критериев приемлемости риска?
7.Какие методы позволяют быстро провести ранжирование рисков?
8.Какой метод наиболее пригоден для анализа отказов при наличии статистических данных?
9.В чем заключается принципиальное отличие причинноследственной диаграммы от диаграммы «галстук-бабочка»?
10.На каком этапе жизненного цикла продукции наиболее полезно проведение АВПКО?
40