
Учебное пособие 800419
.pdfзаказов, выполнять их подбор с учетом сложившейся (или намеченной) специализации предприятия, находить наиболее прибыльные объекты производства.
Разработанная система управления прошла проверку при создании наукоемких изделий на предприятиях Воронежа, Казани, Москвы, при выполнении индивидуальных заказов малыми предприятиями (в основном мебельной отрасли). Полученные результаты подтвердили правомерность основных положений работы, на что имеются акты внедрения.
В качестве основных выводов по проделанной работе можно указать следующее:
1.Создана система экономического управления производством продукции научного опытного машиностроительного предприятия и малых предприятий, базирующаяся на выдвинутых в работе критериях и учитывающая в качестве приоритетного направления основной профиль фирмы по созданию новых образцов современных изделий, что позволило возродить и поднять объемы создания опытной продукции по трудоемкости до 52% к общему объему выполняемых работ.
2.За счет реализации предложенной системы удалось обеспечить выпуск через организации различных форм собственности опытных образцов, в основном за счет внутренних накоплений от реализации освоенной продукции, без прекращения выплат по ранее образовавшимся задолженностям.
3.Сформирована структура контроля этапов прохождения финансовых потоков, учитывающая изменения внешних и внутренних факторов и отличающаяся гибкостью воздействия на всех этапах контроля, что позволило в 3-5 раз ускорить создание новых образцов, не имеющих аналогов и для некоторых профилирующих изделий отмечено премией Правительства РФ.
4.Обоснована новая концепция по экономическому управлению производством продукции в условиях задолженности за прошлый период, в которой приоритеты смещены в сторону разработки принципиально новых образцов по основному профилю предприятия с финансированием разработок в основном за счет средств от реализации научно-обоснованных объемов востребованных изделий, созданных и освоенных в прошлый период, что позволило стабилизировать своевременную выплату средств трудовому коллективу и начать погашение внешних задолженностей.
101
5. Разработана система управления ускоренным созданием новых изделий с учетом вероятного риска получения отрицательного результата, вызывающего безвозвратные материальные потери, отличающиеся динамичным изменением объемов финансирования, вплоть до его полного прекращения, при вероятности отрицательного результата, и с повышением уровня коллективной материальной ответственности за результативность разработок по созданию новой техники. В результате достигнут объем финансирования новых изделий до 60-68% от общего и намечено повысить долю новых разработок до 80-85%.
Основным результатом работы является построение экономической системы управления для возрождения создания опытных образцов сложной техники, защищенных патентами разработчиков, обладающих приоритетами на мировом рынке и востребованных ведущими фирмами страны.
Литература
1.Абрамов О.В., Инберг С.П. Параметрический синтез настраиваемых технических систем. М.: 1985. 127 с.
2.Аверченков В.И. Автоматизация проектирования технологических процессов. Брянск: БИТМ, 1984. 84 с.
3.Автоматизация проектирования технологии в машиностроении / Б.Е. Челищев, И.В. Боброва, А. Гонсалес-Собатер; Под ред. акад. Н.Г.Бруевича. М.: Машиностроение, 1987. 264 с.
Воронежский государственный технический университет
УДК 621.9.047
В.П. Смоленцев, Е.В. Гончаров
ГИДРОАБРАЗИВНОЕ РАЗДЕЛЕНИЕ МЕТАЛЛОВ С НАЛОЖЕНИЕМ ЭЛЕКТРОИЧЕСКОГО ПОЛЯ
Рассматривается принцип образования шаржирования при гидроабразивном разделении материалов. Приведены практические исследования геометрической формы обработанной гидроабразивным разделением поверхности и образования шаржирования. Приведен способ устранения шаржирования.
102
Постоянно растущие требования потребителей к качеству и производительности процессов резки, появление новых материалов, большой сортамент и номенклатура разрезаемых изделий, многократность использования операции резки на стадиях изготовления деталей потребовали новых подходов к технологии резки, характеризующихся отсутствием непосредственного механического контакта инструмента с заготовкой.
Одним из методов, удовлетворяющих таким требованиям, является гидроабразивная резка металла. У способа имеются преимущества по сравнению с другими методами разделения материалов [1, стр.41-50]:
-отсутствует термическое влияние на разрезаемый материал, так как генерируемое в процессе резки тепло практически мгновенно уносится водой;
-высокое качество получаемых кромок, не требующих дополнительной обработки;
-имеется возможность разрезать пакеты, состоящие из нескольких слоев различных материалов;
-можно обрабатывать материалы с волнистой поверхностью
исложных контуров;
-небольшая ширина реза;
-имеется возможность начать резание материала в любой его точке;
-высокая скорость резания;
-высокая универсальность использования для любых металлов, различной толщины;
-высокая точность резки фасонных частей;
-полное отсутствие повреждения краев близко расположенных отверстий (толщина перемычки между отверстиями может быть 0,5 мм. и даже меньше);
-низкое тангенциальное усилие резания на деталь;
-отсутствует необходимость снятия заусенцев;
-высокая экономичность резания благодаря удалению малого объема материала и использования дешевых расходных материалов;
-отсутствие выделения пыли, дыма, токсичных паров;
-взрывобезопасность и пожаробезопасность процесса;
-очень быстрое и простое перепрограммирование.
103
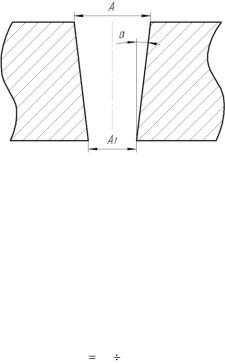
Несмотря на все преимущества у данного метода присутствует негативное остаточное явление – шаржирование. Абразив, застрявший в материале, ухудшает эксплуатационные свойства изделия, что может привести к выходу из строя узлов трения. Поэтому в некоторых случаях возникает необходимость после гидроабразивного разделении вязких металлов удалять вкрапления абразива.
Экспериментальные исследования проводились на установке для гидроабразивной резки модели PTV WJ3020E 1Z-D 37 с давлением рабочей среды 415МПа. Использовался абразив - гранатовый концентрат GMA 80, в качестве образцов применялся алюминиевый прокат толщиной 12 мм. Замеры паза, получаемого при разделении, показали, что форма реза представляет собой V образную форму, которая показана на рис. 1.
При этом замеры размеров А и А1 ширины паза при различных подачах и давлениях рабочей среды 415 МПа дали возможность найти зависимость изменения угла α от величины подачи инструмента, представленную на рис. 2.
Рис. 1 – Форма реза при нормальных условиях
Зависимость на рис. 2 показывает, что при увеличении подачи инструмента угол наклона разделенной кромки (α) увеличивается, при достижении критической скорости подачи форма среза сильно искажается (рис. 3), за счет недостатка времени обработки для обеспечения нормального режима резания, при этом образуется в нижней точке обработки утолщение, обусловленное задержкой абразива и его отводом с рабочей жидкостью в сторону противоположную направлению подачи сопла. В связи с этим погрешность разделенных деталей возрастает в 2-3 раза.
А1 |
(2 3) |
А2 . |
|
А3 |
А3 |
|
104
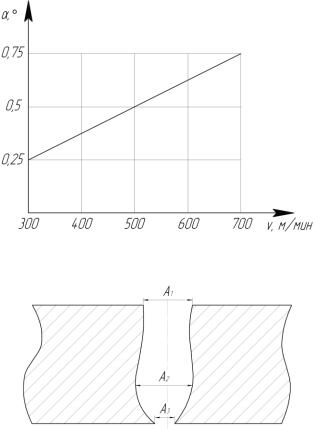
Рис. 2. Зависимость угла наклона разделенной кромки α от величины подачи инструмента v
Рис. 3. Форма реза при разделении с критической подачей
Была исследована глубина проникновения абразивных частиц в обрабатываемый материал. Проведенные исследования позволили установить зависимость количества застрявших частиц в зависимости от глубины их внедрения, представленную на рис. 4. Для этого была измерена глубина залегания ста абразивных частиц изометрической формы со средним размером зерен 0,25÷0,3 мм.
Из зависимости, представленной на рис. 4, видно, что абразив, проникающий менее чем на 70% своего среднего размера, удаляется потоком рабочей жидкости, сопровождающей процесс гидроабразивного разделения. Проникновение абразива на большую глубину практически не происходит из-за высокой концентрации в потоке рабочей суспензии.
105
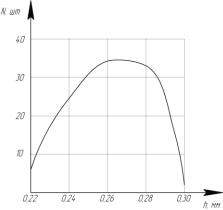
Рис. 4. Зависимость количества застрявших частиц от глубины их проникновения
Из теории шлифования известно, что при погружении абразивного вкрапления в материал менее чем на 1/3 своего среднего размера, абразив легко удаляется. Следовательно, для очистки разделенного гидроабразивным методом материала необходимо снять припуск такой толщины, чтобы на поверхности шаржированного материала не осталось абразива, углубленного в материал более чем на 1/3 своего среднего размера. Экспериментальные данные, приведенные выше, показали, что обычно глубина проникновения абразивных вкраплений в обрабатываемый материал при гидроабразивном разделении составляет не более среднего размера абразивных зерен. Проникновение на большую глубину маловероятно из-за того, что тангенциальная составляющая инерции абразива в струе жидкости мала и ее недостаточно для значительного углубления абразивных вкраплений в обрабатываемый материал. Особенно сильно это явление выражено при обработке вязких металлов, где съем припуска для удаления абразивных вкраплений наиболее желателен. Традиционные методы удаления шаржирования имеют высокую стоимость и малоэффективны. При обработке режущим инструментом вязкий металл вызывает выкрашивание режущей части, а твердые абразивные вкрапления быстро затупляют режущую кромку, что в совокупности приводит к быстрому выходу инструмента из строя. При обработке абразивным инструментом, вязкий металл быстро засаливает инструмент и тем самым приводит к необходимости частой и дорогой правки. К тому же траектория разделения материала
106
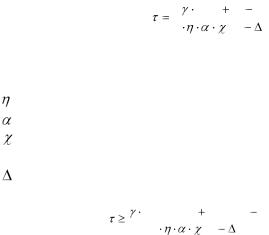
может иметь сложную форму, что не позволяет использовать для чистовой обработки большинство традиционных методов.
Для решения такой проблемы необходимо применять бесконтактные методы обработки, в частности электрохимическую и комбинированную обработку. Это позволяет растворить слой металла, достаточный для легкого отделения абразивных вкраплений, равный:
z≥0,7dmax, |
(1) |
где z – припуск на обработку;
dmax – максимальный размер используемого абразива при гидроабразивном разделении.
Время обработки находится из зависимости:
z(S0 |
z) S02 |
, |
(2) |
2 |
(U U ) |
|
|
|
|
где - плотность материала;
S0 – межэлектродный зазор, равный среднему расстоянию от со- пла-катода до плоскости разделения;
-выход по току;
-электрохимический эквивалент;
-удельная проводимость;
U – напряжение на электродах; U - потери напряжения.
Подставляя (1) в (2) получаем:
0,7dmax (S0 |
0,7dmax ) S02 . |
(3) |
|||
2 |
(U |
U ) |
|
||
|
При проведении экспериментов установлено, что расчет по зависимости (3) дает результат со сходимостью более 90%.
Авторами предложен новый способ разделения металлов с использованием абразивной среды и одновременного удаления части припуска анодной обработкой. Приведены зависимости, полученные экспериментальным путем, для определения:
-угла наклона разделенной кромки от величины подачи инструмента;
-количества застрявших частиц от глубины их проникнове-
ния.
107
Литература 1. Павлов Э. Гидроабразивная резка // Умное производство,
№1 (7), 2009.
2. Электрофизические и электрохимические методы обработки: В 2-х т. Т1/ Под ред. В.П. Смоленцева. – М.: Высш. шк., 1983. 247 с.
Воронежский государственный технический университет
УДК 621.09.047
Е.Ю. Кропоткина, О.В. Журавлева, В.П. Смоленцев
ТЕХНОЛОГИЯ АССИМЕТРИЧНОГО УПРОЧНЕНИЯ ВАЛОВ
Рассматриваются вопросы технологии ассиметричного обкатывания нежестких валов роликами, учитывающие комплексное влияние различных технологических факторов. Приведены конкретные рекомендации в виде расчетного алгоритма для выбора режимов ассиметричного упрочнения нежестких валов, изготовленных из разных материалов.
В работе проведено теоретическое моделирование процесса асимметричного упрочнения, которое базировалось на решении трѐх взаимосвязанных задач: задачи создания асимметричной эпюры силы обкатывания (выглаживания) в зависимости от условий обработки; задачи определения параметров области контакта и распределения остаточных напряжений, вызывающих изгиб вала; задачи управления изгибом.
Обкатывание и выглаживание являются наиболее простыми
иэффективными методами упрочнения и отделки поверхностного заключается в пластическом деформировании тонкого поверхностного слоя обрабатываемой детали движущимся инструментом, имеющим рабочий элемент в виде сферы, цилиндра, кругового тора
идругих форм. С точки зрения физики явлений, возникающих в процессе рассматриваемых методов обработки, основное отличие между обкатыванием и выглаживанием состоит в особенности контактного трения между рабочей поверхностью инструмента и деформируемой поверхностью детали. При обкатывании превалирует трение качения. Выглаживание осуществляется в условиях трения
108
скольжения. Обработка обоими методами чаще всего производится на станках токарной группы. Относительно частое применение этих методов в промышленности объясняется значительными преимуществами, которые можно объединить в две группы. К первой группе относятся преимущества, связанные с качеством обрабатываемого изделия: получение поверхности с шероховатостью до Ra 0,08 мкм; получение оптимальной величины относительной длины опорного профиля; образование в верхнем слое упрочненного слоя, благоприятных сжимающих напряжений; возможность ликвидации локальной концентрации остаточных напряжений; повышение усталостной прочности, износостойкости, коррозионной стойкости, хорошие адгезионные свойства; обеспечение равномерного нанесения гальванических покрытий; обеспечение прочности неподвижных соединений. Ко второй группе относятся преимущества, связанные с технологией обработки детали: возможность проведения обкатывания и выглаживания на универсальных станках с применением универсальной оснастки; малая потребляемая мощность; высокая производительность; экономичное использование обрабатываемого материала; возможность замены в определенных случаях термической или термохимической обработки на поверхностное пластическое деформирование (ППД). Известно, что обработка ППД сопровождается появлением в поверхностном слое деталей достаточно больших и благоприятных для эксплуатационных качеств детали остаточных напряжений сжатия. При создании в поверхностном слое несимметричной относительно оси детали эпюры остаточных напряжений с помощью обкатывания или выглаживания возможно возникновение деформаций изгиба. Однако для практического использования этого метода необходима методика по прогнозированию деформаций изгиба детали в зависимости от режимов и условий обработки
Созданием неравномерного напряжѐнно-деформированного состояния можно получить не только плоский, но и пространственный изгиб. Это достаточно просто можно осуществить, например, смещая центр вращения детали при закреплении на эксцентриситет eц1 у правого торца детали и на эксцентриситет eц2 у левого торца. Направление смещения эксцентриситетов относительно оси OY может быть под любым углом (рис. 1). При таком закреплении распределение силы обкатывания Р по периметру детали в каждом сечении, перпендикулярном оси детали, подчиняется закону эксцентриситета:
109
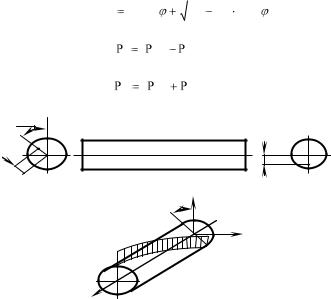
P Pa cos |
2 |
2 |
sin |
2 |
, |
(1) |
Pcp |
Pa |
|
|
|
где Pa - амплитуда изменения силы обкатывания:
a |
( max |
min ) / 2; |
Pср - средняя сила обкатывания:
ср |
( max |
min ) / 2; |
- угол поворота обрабатываемой детали.
φ
ец
е
у
φ
z
х
Рис.1. Схема приложения наибольшей силы обкатывания Рmax в общем случае асимметричного закрепления вала
При этом угол приложения максимальной силы давления инструмента изменяется в разных плоскостях, перпендикулярных оси OX балки. Изогнутая ось балки в этом случае является пространственной кривой. Это будет наиболее общий случай для рассматриваемой схемы закрепления.
Так как в процессе асимметричного деформирования сила давления инструмента меняет свое значение по периметру детали, то меняются и параметры области контакта инструмента и обрабатываемой заготовки.
При обкатывании и выглаживании в состоянии активного нагружения находится передняя часть поверхности контакта. Поэтому упругопластические деформации развиваются, главным образом, в областях материала, прилегающих к передней части контактной поверхности. Для задней поверхности касания характерно уменьшение контактной нагрузки от максимума в центральной части до нуля на контуре площадки. Поэтому в
110