
- •В.А. Жулай детали машин
- •190600 «Эксплуатация транспортно-технологических машин и комплексов»
- •Рецензенты:
- •Основные условные обозначения
- •Общие сведения о деталях машин и истории их развития
- •Краткий исторический обзор
- •Основные понятия и задачи курса деталей машин. Основные направления развития конструкций машин
- •Классификация деталей машин
- •Контрольные вопросы
- •2.2. Последовательность и этапы проектирования
- •Контрольные вопросы
- •2.3. Виды нагрузок, действующих на детали машин
- •Контрольные вопросы
- •2.4. Основные критерии работоспособности и расчета деталей машин
- •2.4.1. Прочность
- •Выбор запаса прочности и допускаемых напряжений
- •В основу положено уравнение линейного суммирования повреждений
- •Жесткость
- •Износостойкость
- •2.4.4. Теплостойкость
- •2.4.5. Виброустойчивость
- •2.4.6. Надежность
- •Контрольные вопросы
- •3. Соединения
- •3.1. Неразъемные соединения
- •3.1.1. Сварные соединения
- •3.1.2. Паяные и клеевые соединения
- •3.1.3. Соединения с натягом
- •3.1.4. Заклепочные соединения
- •Расчет на прочность элементов заклепочного шва
- •Расстояние между рядами заклепок
- •Условие прочности на срез:
- •Условие прочности на смятие:
- •Контрольные вопросы
- •3.2. Разъемные соединения
- •3.2.1. Резьбовые соединения
- •Силовые соотношения и расчет на прочность резьбовых соединений.
- •С учетом (3.28) формула (3.27) примет вид
- •3.2.2. Шпоночные соединения
- •3.2.3. Шлицевые и профильные соединения
- •3.2.4. Штифтовые соединения
- •Для односрезного соединения
- •Условие прочности на смятие:
- •3.2.5 Клеммовые соединения
- •Контрольные вопросы
- •4. Механические передачи
- •4.1. Общие сведения. Основные кинематические и энергетические соотношения
- •Кинематические и энергетические соотношения в передаточных механизмах
- •Контрольные вопросы
- •4.2. Фрикционные передачи и вариаторы
- •Создаваемый момент трения
- •Расчет на прочность фрикционной передачи
- •Фрикционные вариаторы
- •Контрольные вопросы
- •4.3. Ременные передачи
- •Кроме того, натяжения в ветвях f1 и f2 связаны с передаваемой окружной силой Ft условием:
- •Напряжение от окружного усилия, передаваемого ремнем:
- •Напряжения от изгиба ремня
- •4.4. Зубчатые передачи
- •Классификация зубчатых передач
- •4.4.1. Геометрия и кинематика цилиндрических прямозубых передач
- •4.4.2. Основы расчета на контактную прочность и изгиб
- •4.4.3. Косозубые и шевронные колеса. Особенности их расчета
- •4.4.4. Конические зубчатые передачи
- •В соответствии со схемами (см. Рис. 4.27, 4.28)
- •Основы расчета на контактную прочность и изгиб конической передачи
- •4.4.5. Планетарные передачи
- •4.4.6. Волновые передачи
- •4.4.7. Передачи Новикова
- •4.5. Червячная передача
- •Области применения червячных передач
- •Расчет па прочность червячной передачи
- •4.6. Передача винт-гайка
- •4.7. Рычажные механизмы
- •4.8. Цепная передача
- •Силы в цепной передаче
- •5. Валы и оси. Подшипники.
- •5.1. Валы и оси
- •Материалы
- •5.2. Подшипники
- •5.2.1. Подшипники скольжения
- •Материалы
- •5.2.2. Подшипники качения
- •Условные обозначения подшипников качения
- •Смазывание подшипников
- •Поля допусков отверстий под подшипники
- •5.2.3. Уплотняющие устройства
- •5.3. Общие сведения о редукторах
- •Схемы редукторов
- •Смазывание редукторов
- •Муфты. Упругие элементы. Смазочные материалы. Сапр
- •6.1. Муфты
- •Классификация муфт Муфты подразделяют:
- •Подбор муфт и проверка па прочность основных элементов
- •Фрикционная муфта
- •6.2. Пружины и рессоры
- •6.2.1. Основные понятия
- •6.2.2. Конструирование и расчет цилиндрических витых пружин
- •Шаг пружины сжатия в ненагруженном состоянии
- •Длина пружины в ненагруженном состоянии
- •6.3. Смазочные материалы
- •6.3.1. Смазочные масла
- •Классификация трансмиссионных масел
- •Соответствие классов вязкости и групп трансмиссионных масел по гост 17479.2-85 классификациям sae j306с и арi
- •6.3.2. Пластичные смазки
- •6.3.3 Твердые смазочные материалы
- •6.3.4. Твердые смазочные покрытия
- •6.3.5. Ротапринтная смазка
- •6.3.6. Магнитные смазочные материалы
- •6.3.7. Антифрикционные самосмазывающиеся материалы
- •6.4. Автоматизация проектирования узлов и деталей машин
- •6.4.1. Структура и функционирование сапр
- •6.4.2. Типовые процедуры и маршруты сапр
- •Заключение
- •Библиографический список
- •Жулай владимир алексеевич
- •190600 «Эксплуатация транспортно-технологических машин и комплексов»
- •3 94006 Воронеж, ул. 20-летия Октября, 84
3.2.2. Шпоночные соединения
Шпоночные соединения в основном служат для передачи крутящего момента с вала на расположенные на нем детали – шкивы, зубчатые колеса, муфты, маховики и пр. Иногда шпонки фиксируют эти детали, предотвращая осевые перемещения. Классификация шпоночных соединений приведена на рис. 3.30.
Рис. 3.30. Классификация шпоночных соединений
|
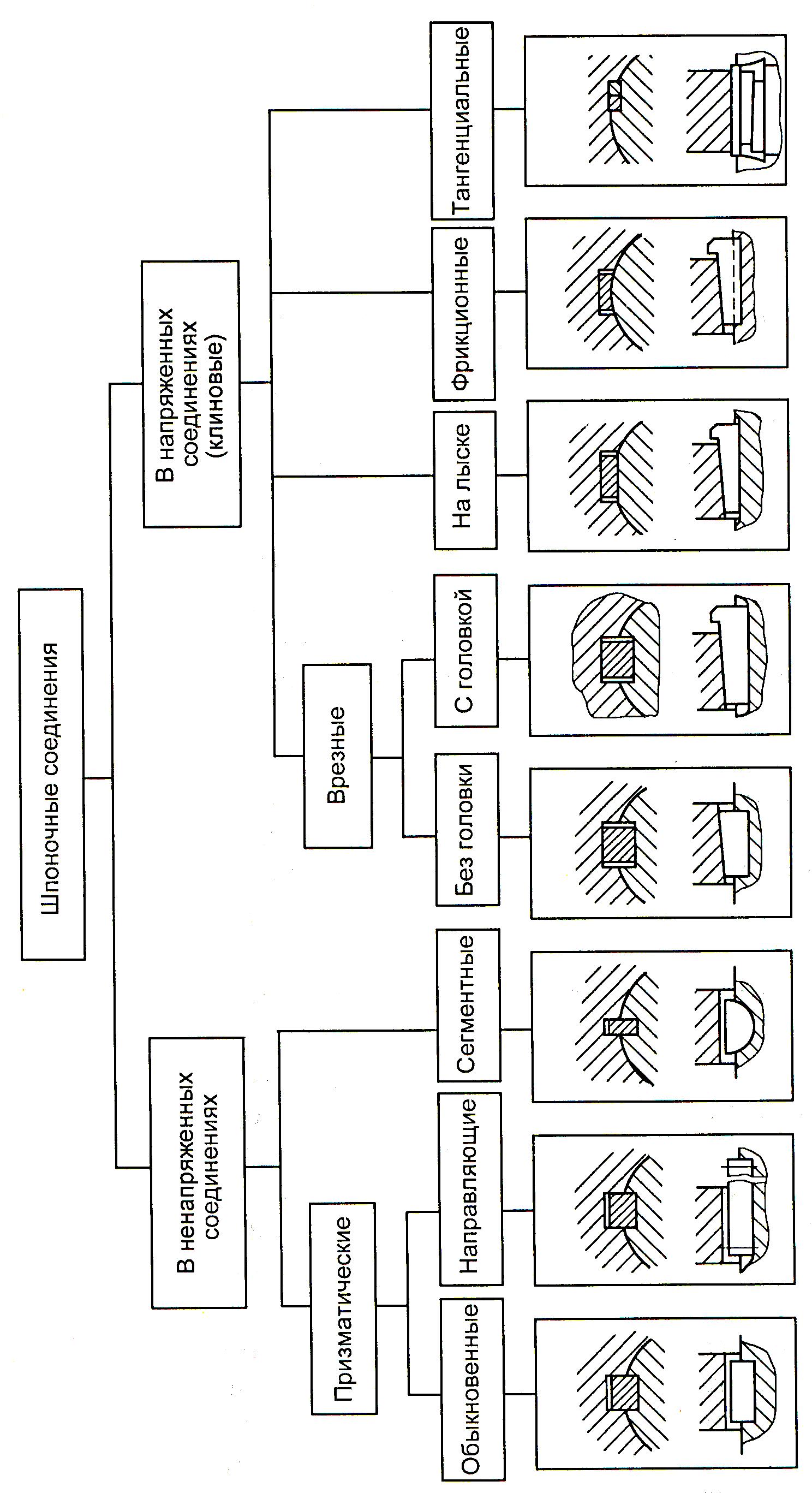
Наиболее ранние из шпоночных соединений, известные еще с XVII – XVIII вв. и примененные, в частности, на первых паровых машинах, – клиновые шпонки (рис. 3.31).
Рис. 3.31. Шпоночное соединение с клиновой шпонкой
Клиновые шпонки 2 забиваются в паз между канавками на валу 3 и ступице 1, образуя так называемое напряженное соединение. В таком соединении напряжения, вызванные забиванием клина, появляются до передачи крутящего момента. Сам крутящий момент передается такой шпонкой большей частью за счет сил трения, обусловленных радиальными силами, с которыми заклиненная шпонка действует на вал и ступицу. Эти же силы трения препятствуют осевому перемещению закрепленной на валу детали. Однако клиновая шпонка вызывает радиальное смещение деталей относительно вала, что нарушает точность соединения, способствует дисбалансу детали; из-за этих недостатков клиновые шпонки в современных, особенно быстроходных, машинах практически не используются.
Еще в XIX в. назрела необходимость перемещать детали, расположенные на валу: зубчатки, шкивы и т.д. – в осевом направлении, в том числе и на работающей машине. Это вызвало появление ненапряженных шпоночных соединений, вид одного из которых, созданных в XIX в., представлен на рис. 3.32. Это так называемая скользящая шпонка 3, образующая телескопическое соединение вала с деталью, позволяющее детали, в данном случае шкиву, передвигаться вдоль вала, передавая крутящий момент. Если шпонка неподвижна относительно вала, то она называется направляющей и закрепляется на валу винтами.
Достоинства шпоночных соединений – простота конструкции и сравнительной невысокая стоимость изготовления.
Недостатки шпоночных соединений – низкая несущая способность и снижение сопротивления усталости вала из-за ослабления сечений шпоночными пазами и концентрации напряжений в зоне шпоночной канавки.
Шпонки большей частью встречаются призматические, сегментные и цилиндрические.
Призматические шпонки различных исполнений представлены на рис. 3.33.
Рис. 3.32. Шпоночное соединение со скользящей шпонкой:
1 – вал; 2 – шкив; 3 – шпонка
Рис. 3.33. Шпоночные соединения с призматическими шпонками
Обозначения: h – высота шпонки; в – ширина шпонки; l – длина шпонки; d – диаметр вала; t1 – глубина паза на валу; t2 – глубина паз во втулке.
Исполнение 1 предусматривает шпонку с двумя закругленными торцами, исполнение 2 – с двумя плоскими, а исполнение 3 – с одним плоским торцом, а другим закругленным. Осевую нагрузку призматические шпонки не воспринимают. В зависимости от принятой базы обработки на рабочих чертежах нужно указывать размер для вала – t1 или (d – t1), а для втулки – (d + t2).
Сегментная шпонка (рис. 3.34) бывает без лыски с высотой h и с лыской – высотой h1. Соединения сегментной шпонкой технологичны, не требуют ручной подгонки. Они самоустанавливаются, что уменьшает перекос шпонки, удобны в сборке. При длинной ступице такие шпонки можно устанавливать по две на длине ступицы. Сегментная шпонка характеризуется двумя основными размерами: диаметром заготовки d1 и шириной b; длина шпонки близка к d1,. Сегментные шпонки находят применение в крупносерийном и массовом производстве, в частности автомобилестроении.
Рис. 3.34. Шпоночное соединение с сегментной шпонкой
Цилиндрические шпонки (рис. 3.35) применяют для закрепления деталей на конце вала.
Отверстия сверлят в собранном состоянии параллельно оси вала на стыке деталей. Диаметр отверстия под шпонку dшп = (0,13 ... 0,16) d, длина l = (3 ... 4) dшп. Обычно цилиндрические шпонки ставят с натягом, в частности Н7/r6, в количестве двух или трех, соответственно под углом 180 или 120° друг к другу.
Рис. 3.35. Шпоночное соединение с цилиндрической
шпонкой-штифтом
Шпонки изготовляются из прутков углеродистой или легированной стали с пределом прочности σв ≥ 500 МПа.
Главным критерием работоспособности шпоночных соединений является прочность на смятие.
Это обосновано тем, что шпонки выбираются по таблицам из стандартов в зависимости от диаметра вала. При этом размеры шпонок и пазов подобраны так, что прочность шпонок на срез обеспечивается, если выполняется условие прочности на смятие. Стандартные шпонки можно не проверять на срез.
Шпонка рассчитывается на смятие по формуле
,
(3.45)
где Т – передаваемый крутящий момент;
d – диаметр вала;
Асм = k lр – площадь смятия для призматических и сегментных шпонок;
k = (h – t1) – высота площадки смятия (k ≈ 0,4h);
lр – расчетная длина шпонки.
lр = (1 – b) l для шпонок исполнения 1; lр = l для исполнения 2; lр = (l – 0,5b) l для исполнения 3; lр = d1 для сегментных шпонок; для цилиндрических шпонок Aсм = dшпl.