
Учебное пособие 1754
.pdf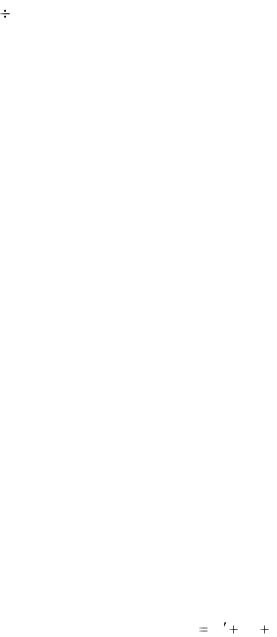
41
рекомендуется применение трубок с dвн больше 38 - 57 мм. Шаг труб S (расстояние между осями соседних труб) чаще всего выбирается равным (1,2 – 1,4) dн, но не
меньше dн |
6 мм. |
|
|
|
|
|
|
|
|
|
||
|
Рекомендации по выбору шага между трубами S по известному наружному |
|||||||||||
диаметру dн |
|
|
|
|
|
|
|
|
|
|
||
|
|
|
|
|
|
|
|
|
|
|
Таблица 8 |
|
|
|
|
|
|
|
|
|
|
|
|
|
|
|
dн, мм |
|
17 |
22 |
25 |
32 |
38 |
44,5 |
51 |
54 |
|
76 |
|
|
|
|
|
|
|
|
|
|
|
|
|
|
S, мм |
|
27 |
32 |
35 |
44 |
50 |
58 |
66 |
74 |
|
93 |
|
|
|
|
|
|
|
|
|
|
|
|
|
Наиболее целесообразным расположением считается размещение центров трубок на трубной решетке по вершинам равносторонних треугольников
(ромбическое). Размещение труб может быть выполнено и по концентрическим окружностям, отстоящим одна от другой на принятую величину шага между трубами. Зная общее количество труб (формула (75)), можно по приложению, табл.
П-2 определить диаметр окружности, на которой располагаются крайние трубы, D′,
м.
Необходимо учесть, что место части труб пучка может быть занято установкой анкерных связей или перегородками в трубном пространстве. Это может вызвать увеличение расстояния между трубами.
После выбора диаметра D′ определяют внутренний диаметр корпуса D по формуле
D D dн 2к , м |
(78) |
где К – кольцевой зазор между крайними трубами и корпусом, который принимается из конструктивных соображений 6 мм и больше.
Значение D, вычисленное по формуле (78) необходимо округлить до ближайшего стандартного значения диаметра. Основные параметры нормализованных конструкций теплообменников:
Поверхность теплообмена F, м2
5, 10, 15, 20, 30, 40, 50, 80, 100, 150, 200, 250, 300, 350, 400, 500, 600, 700, 800.

42
Диаметр кожуха D, мм
400, 500, 600, 700, 800, 900, 1000, 1200, 1400, 1600, 1800, 2000.
Длина труб l, мм
1000, 1250, 1500, 2000, 2500, 3000, 3500, 4000, 4500, 5000, 6000, 7000.
Диаметр корпуса многоходового теплообменного аппарата определяется с учетом размещения перегородок и производится обычно графическим путем. С
этой целью вычерчивают в определенном масштабе часть трубной доски и на ней размещают трубы с учетом мест для перегородок, анкерных связей, каркаса трубного пучка и т.д.
Длина труб пучка (расстояние между трубными решетками) определяется по формуле
lтр |
F |
, м , |
|
|
|||
d pnoZ |
|||
|
|
где no – число трубок в одном ходу; Z – число ходов.
Диаметр патрубков для теплоносителей определяются по формуле
G
0,5
dп 0,0188 Wп , м ,
(79)
(80)
где G – расход теплоносителя, кг/ч; - плотность теплоносителя при рабочей температуре, кг/м3; Wп – скорость теплоносителя в патрубке, м/с, которую выбирают в следующих пределах:
для паров Wп = 15 - 30 м/с;
для жидкостей Wп = 1 - 2 м/с;
для конденсатов Wп = 0,5 - 1 м/с;
для газов Wп = 20 - 40 м/с.
Остальные размеры теплообменного аппарата выбираются по результатам прочностного расчета.
43
Теплообменники «труба в трубе»
Две коаксиально расположенные трубы с двумя теплоносителями, один из которых течет по внутренней трубе, а второй по кольцевому каналу между трубами, образуют простую конструкцию теплообменника многоцелевого назначения. Подбором диаметров внутренней и наружной труб можно обеспечить обеим рабочим средам, участвующим в теплообмене, необходимую скорость для достижения высокой интенсивности теплообмена. Такие теплообменные аппараты применяются как жидкостные или газо-жидкостные. Большая часть газо-
жидкостных теплообменников этого типа имеет продольные ребра на внешней стороне внутренней трубы.
Аппараты такого типа могут быть соединены как последовательно, так и параллельно, обеспечивая любую необходимую теплопроизводительность и эффективность нагревания или охлаждения. Конструкция такого типа особенно целесообразна в тех случаях, когда одна или обе жидкости находятся под высоким давлением, при котором необходима большая толщина стенки кожуха, и обычные кожухотрубные теплообменники в этом случае становятся дорогими.
Теплообменные аппараты типа «труба в трубе» изготавливают жесткой конструкции (обозначаются ТТ), с сальником на одном конце трубы (обозначаются ТТ-с) или с сальниками на обоих концах трубы (обозначаются ТТ-р). Жесткая конструкция применяется в случае, когда разность температур наружной и внутренней труб невелика и когда не требуется механическая чистка труб.
Аппараты ТТ-с применяются в случаях, когда необходима компенсация температурных расширений. Аппараты ТТ-р применяются в случаях, когда при эксплуатации теплообменника требуется полный демонтаж внутренних труб.
Для расчета теплообменного аппарата типа «труба в трубе» исходные данные те же, что и для кожухотрубного теплообменника.
1. Выбираются диаметры труб аппарата с целью получения одинаково высоких скоростей движения теплоносителей:

44
а) для внутренней трубы выбирается скорость и определяется сечение одной секции
|
|
|
d 2 |
|
|
G |
|
, м2 ; |
|
|
|
||
fвн |
|
вн |
|
|
вн |
|
|
|
(81) |
||||
|
4 |
|
|
|
|
|
|
|
|||||
|
|
|
|
|
3600 внWвн |
|
|
|
|||||
б) для кольцевого сечения |
|
|
|
|
|
|
|
|
|
|
|
||
f |
|
|
|
|
|
D2 |
d 2 |
|
Gкольц |
|
, м2 |
(82) |
|
|
кольц |
4 |
|
вн |
н |
3600 кольцWкольц |
|
||||||
|
|
|
|
|
|
|
|
|
|||||
или, задаваясь диаметрами труб и зная расходы теплоносителей Gвн и Gкольц, |
|||||||||||||
определяют скорости их движения. Скорости Wвн и |
Wкольц выбираются для |
жидкостей в пределах от 0,8 до 2 м/с. Диаметры труб – внутренней не более 57
мм, наружной – не более 108 мм.
3. Определяются величины коэффициентов 1и К, Вт/(м2 ∙К).
4.Определяется поверхность теплообмена Fобщ = Q/(K∙ tср), м2.
5.Находят общую длину внутренней трубы по формуле
L |
Fобщ |
,м |
|
|
(83) |
||
|
dср |
||
|
|
||
5. При последовательном соединении теплообменных аппаратов «труба в |
|||
трубе» число секций находят по уравнению |
|
||
Z |
L / lтр |
(84) |
где lтр лежит в пределах от 1,5 до 6 м.
6. При параллельном соединении аппаратов в первую очередь по заданному расходу Gвн, выбранному диаметру dвн и принятой скорости Wвн определяют необходимое проходное сечение для движения теплоносителя:
f вн |
Gвн |
, м2 |
(85) |
|
3600 внWвн |
||||
|
|
|
а затем находится число параллельно включаемых аппаратов по формуле
n |
f |
вн |
|
4Gвн |
|
; |
(86) |
|
fвн |
|
3600 W |
d 2 |
|||
|
|
|
|
вн вн |
вн |
|

45
Секционные (элементные) теплообменники
Эти теплообменники состоят из нескольких последовательно соединенных элементов-секций, каждая из которых представляет собой трубный пучок с малым числом труб, помещенный в кожухе небольшого диаметра. Поверхность теплообмена одной секции применяемых элементных теплообменников составляет
0,75 - 30 м2, число труб – от 4 до 140.
Теплообменные аппараты типа ТЭ (теплообменник элементный) составляют из одноходовых теплообменных аппаратов типа ТН с диаметрами кожухов 159 и
273 мм, взятых без крышек и соединенных в блоки с помощью калачей.
Применяются для теплоносителей пар-жидкость, газ-жидкость. Используются как нагреватели и конденсаторы.
Расчет элементных теплообменников производится в следующей последовательности:
1.Определяется тепловая нагрузка аппарата Q по формулам (3) или (4).
2.Определяется средняя разность температур между теплоносителями в аппарате по формулам (70), (71) или (72).
3.Выбираются элементы конструкции аппарата, т.е. число и диаметр труб в элементе, длина труб, диаметр корпуса.
4.Определяются скорости теплоносителей: W = G/ f;
а) проходное сечение трубного пучка из «n» труб
f |
тр |
n |
dвн2 |
,м |
2 |
; |
(87) |
|
4 |
|
|
||||||
|
|
|
|
|
|
|
|
|
б) проходное сечение межтрубного пространства |
|
|||||||
fмт |
0,25 Dвн2 |
|
ndн2 ,м2 |
(88) |
5. Вычисляются эквивалентные диаметры труб и межтрубного пространства
|
D2 |
nd 2 |
|
||
dэ.тр dвн , м; dэ.мт |
вн |
н |
, м |
(89) |
|
Dвн |
ndн |
||||
|
|
|
6. Определяются величины коэффициентов 1 ; и К, Вт/(м2 ∙К).

46
7.Находится общая площадь поверхности теплообмена по формуле (1), F, м2.
8.Определяется поверхность теплообмена одного элемента аппарата
Fэл n dсрlтр , м2 |
(90) |
9. Определяется необходимое число элементов в теплообменном аппарате n=F/Fэл
Оросительные теплообменники
Оросительные теплообменники собирают из прямых горизонтальных труб и соединительных калачей (на сварке или на фланцах) в виде плоских змеевиков,
укрепляемых на специальных каркасах. Орошающая холодная вода подается из желоба или перфорированных труб на верхнюю трубу, стекает с нее на нижележащую трубу и, пройдя последовательно по поверхности всех труб, стекает в поддон. Вследствие частичного испарения охлаждающей воды ее расход всегда ниже, чем в охладителях другого типа. Оросительные теплообменники применяют главным образом в качестве холодильников для жидкостей и газов или как конденсаторы.
Расчет оросительных теплообменников производится в следующей последовательности:
1.Выбираются элементы конструкции аппарата: материал, длина и диаметр труб, число секций m (рекомендуется m = 4, 6 или 8), относительный шаг труб S/dн в пределах 1,2 - 2,0.
2.Определяется тепловая нагрузка аппарата Q по формулам (3) или (4).
3.Определяется количество орошающей воды по формуле
W = Wн + Wи, кг/ч, |
(91) |
||||
где Wн – количество нагреваемой воды, кг/ч, определяется по уравнению |
|||||
Wн |
0,96Q |
,кг / ч |
|
||
|
|
(92) |
|||
Cв tв |
tв |
||||
|
|
|
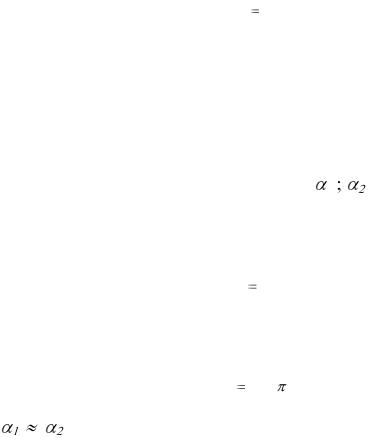
47
Здесь Св – средняя теплоемкость орошающей воды, кДж/(кг∙К); tв″ – конечная температура орошающей воды, оС;
tв′ - начальная температура орошающей воды, оС.
Wи – количество испарившейся воды, кг/ч, определяется по уравнению
Wи |
0,04Q |
,кг / ч |
(93) |
|
r |
||||
|
|
|
Здесь r – скрытая теплота парообразования орошающей воды при ее средней температуре, кДж/кг
4.Определяется средняя разность температур между теплоносителями при их перекрестном токе по формуле (73)
5. Определяются величины коэффициентов 1 |
и К, Вт/(м2 ∙К). |
6.Находится поверхность теплообмена всего аппарата F по формуле (1)
7.Определяется поверхность теплообмена одной секции
Fc F / m , м2 |
(94) |
8.Определяется количество последовательно включенных звеньев в одной секции
|
Z |
Fc / d plтр . |
(95) |
Если |
, то dp = 0,5(dвн + dн), |
м. Число звеньев Z должно быть целым |
|
числом. |
|
|
|
Погружные теплообменники
Теплообменные аппараты этого типа состоят из плоских или цилиндрических змеевиков, погруженных в сосуд с рабочей жидкостью. Один теплоноситель циркулирует в сосуде, другой вводится в трубу змеевика.
Вследствие малой скорости омывания жидкостью и низкой интенсивности теплообмена снаружи змеевика погруженные теплообменники являются недостаточно эффективными аппаратами, но вследствие простоты изготовления и возможности использования для этого любого коррозионностойкого материала
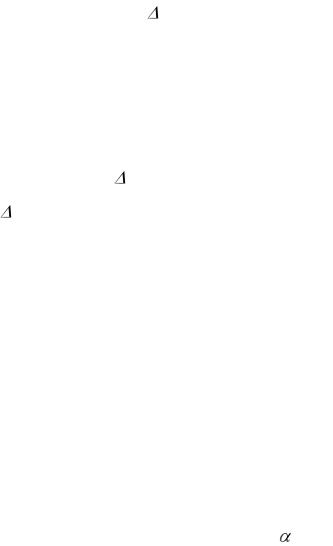
48
они получили широкое распространение. Их целесообразно использовать, когда жидкий теплоноситель снаружи змеевика находится в состоянии кипения или
имеет механические включения, а также представляет из себя агрессивную среду.
Ввиду сравнительно большого гидравлического сопротивления змеевиков скорость жидкостей в них принимают 0,3 - 0,8 м/с, а для газов при атмосферном
давлении 3 - 10 м/с.
Для паровых змеевиков для нагревания жидкостей начальная скорость пара в змеевике не должна превышать 30 м/с. Предельное наибольшее отношение l/dвн
(где l – длина каждого змеевика) в зависимости от абсолютного давления пара Р
при средней разности температур |
tср= 30 – 40 оС, составляет |
|
|
|
||||||||
|
|
|
|
|
|
|
|
|
|
|
Таблица 9 |
|
|
|
|
|
|
|
|
|
|
|
|
|
|
Р, ата |
5 |
|
4 |
|
3 |
|
2 |
1,5 |
1,25 |
0,8 |
|
0,5 |
|
|
|
|
|
|
|
|
|
|
|
|
|
(l/d)max |
275 |
|
250 |
|
225 |
|
200 |
175 |
150 |
125 |
|
100 |
|
|
|
|
|
|
|
|
|
|
|
||
При других значениях |
tср |
приведенные значения l/d следует умножить на |
||||||||||
коэффициент 6/ |
tср0,5. |
|
|
|
|
|
|
|
|
Расчет погружных теплообменников производится в следующем порядке:
1.Выбирается внутренний диаметр труб в пределах 32 - 76 мм.
2.Выбирается скорость движения теплоносителя по трубам и определяется число параллельно включенных рабочих секций m;
В практике аппаратостроения число секций обычно принимается равным 8,
10 или 12 для случая движения газа внутри труб.
3.Определяется тепловая нагрузка аппарата Q по формулам (3), (4) и (5).
4.Определяется средняя разность температур между теплоносителями по формулам (70), (71) или (72).
5. Определяются величины коэффициентов 1;и К, Вт/(м2 ∙К).
6.Находится поверхность теплообмена аппарата F по формуле (1).
7.Рассчитывается длина труб в секции по формуле

|
|
49 |
|
|
|
||
|
L |
|
|
F |
|
, м |
|
|
|
|
|
|
(96) |
||
|
|
|
d pm |
||||
|
|
|
|
|
|||
|
|
|
|
|
|
||
8. |
Принимая диаметр спирали DСП, м, определяет число витков в змеевике |
||||||
|
n |
|
|
L |
. |
|
|
|
|
|
|
|
(97) |
||
|
|
|
Dсп |
|
|||
|
|
|
|
|
|
||
|
|
|
|
|
|
|
|
9. |
Задаваясь шагом спирали hсп, м, определяем высоту секции |
|
|||||
|
h |
hсп n 1 , м |
(98) |
10. В случае необходимости определяются внутренний диаметр коллекторов
и диаметры патрубков.
Сравнительные характеристики рекуперативных аппаратов приведены в
табл. 9.
Таблица 10
аппаратов |
легкостьиПростота |
изготовления |
осуществленияВозможность |
противотокачистого |
трубахв |
высоких .межтрубв Простр |
ЛегкостьТруб |
.межтруб .простр |
иосмотрадляДоступность |
натеплообменаПоверхность |
мобъема.ед |
еднаметаллаРасход |
теплообменникаповерхности |
м/кг |
|
|
|
|
|
|
Достижение |
|
скоростей |
|
очистки |
|
|
3 |
|
|
2 |
|
|
|
|
|
|
|
|
|
2 |
|
|
||||
|
|
|
|
|
|
|
|
|
|
|
|
м/ |
|
|
|
Конструктивные |
|
|
|
|
|
|
|
|
|
|
|
|
|
|
|
|
|
|
|
|
|
|
|
|
|
|
|
|
|
|
|
признаки |
|
|
|
|
|
|
|
|
|
|
|
|
|
|
|
теплообменных |
|
|
|
|
|
|
|
|
|
|
|
|
|
|
|
|
|
|
|
|
|
|
|
|
|
|
|
|
|
|
|
Кожухотрубные |
|
|
|
|
- |
|
- |
+ |
- |
Х |
15-40 |
|
30-80 |
|
|
Одноходовые |
|
Х |
+ |
|
|
|
|
|
|
|
|
|
|
|
|
|
|
|
|
|
|
|
|
|
|
|
|
|
|
|
|
Многоходовые |
|
Х |
Х |
|
+ |
|
Х |
+ |
- |
Х |
15-40 |
|
30-80 |
|
|
|
|
|
|
|
|
|
|
|
|
|
|
|
|
|
|
Элементные |
|
Х |
+ |
|
+ |
|
Х |
+ |
- |
Х |
10-15 |
|
30-80 |
|
|
|
|
|
|
|
|
|
|
|
|
|
|
|
|
|
|
«труба в трубе» |
|
+ |
+ |
|
+ |
|
+ |
+ |
- |
Х |
4-15 |
|
175 |
|
|
|
|
|
|
|
|
|
|
|
|
|
|
|
|||
Погруженные |
|
+ |
- |
|
+ |
|
- |
- |
+ |
+ |
5-10 |
90-120 |
|||
|
|
|
|
|
|
|
|
|
|
|
|
|
|
|
|
Оросительные |
|
+ |
- |
|
+ |
|
не |
Х |
+ |
+ |
|
3-6 |
|
40-60 |
|
|
|
|
|
|
|
|
треб. |
|
|
|
|
|
|
|
|
|
|
|
|
|
|
|
|
|
|
|
|
|
|
|
|
50
В таблице 10 приняты следующие обозначения: + - аппарат соответствует требованиям; Х – частично соответствует; – - не соответствует.
6. ГИДРАВЛИЧЕСКОЕ СОПРОТИВЛЕНИЕ КАНАЛОВ ПОВЕРХНОСТЕЙ ТЕПЛООБМЕНА
Движение теплоносителей в теплообменных аппаратах происходит в условиях неизотермичности, т. е. с переменными физическими свойствами теплоносителей.
Как показано в теории подобия, в выражение, определяющее гидравлическое сопротивление в условиях неизотермичности, входят три безразмерных комплекса:
первым определяется коэффициент сопротивления при изотермическом движении,
вторым – влияние изменения вязкости в пристенном пограничном слое теплоносителя и третьим – влияние свободного движения (турбулизация потока).
К этому результату приходят, если сопротивление подсчитывается так же, как и при изотермическом движении, и по тем же самым формулам. Влияние же изменения температуры при этом учитывается лишь тем, что все расчетные величины – скорость, плотность и вязкость – относят к средней температуре теплоносителя. Коэффициент сопротивления в этом случае является функцией не только критерия Рейнольдса, но также критериев Грасгофа и Прандтля,
определяющих тепловое подобие.
Следовательно, при гидромеханическом расчете теплообменных аппаратов всегда необходимо знать коэффициенты сопротивления при изотермическом движении. Кроме того, моделью изотермического движения можно воспользоваться в тех случаях, когда температурное поле теплоносителя практически изменяется незначительно, например, при сравнительно небольших тепловых нагрузках и малых подогревах теплоносителя.
При изотермическом движении коэффициент гидравлического трения зависит от числа Re и от некоторой безразмерной величины, характеризующей пограничную геометрию потока. Под пограничной геометрией следует понимать